Page 113 of 801
YH4
GRAND
VITARA
3. Pipe clamp
1B-42 AIR CONDITIONING (OPTIONAL)
EXPANSION VALVE
INSPECTION
Refer to ªTroubleshooting Procedure Using Manifold Gauge Setº in
this section.
REMOVAL
1) Recover refrigerant by using recovery and recycling equipment.
Be sure to follow the instruction manual for the equipment. The
amount of compressor oil removed must be measured and the
same amount added to the system.
2) Remove front grill.
3) Disconnect suction pipe (1), and liquid pipe (2) from evaporator
(Cooling unit).
CAUTION:
As soon as above hose and pipe are disconnected, cap
opened fittings so that moisture and dust may not enter
cooling unit.
4) Disconnect suction pipe, and liquid pipe from suction hose (1)
and condenser outlet pipe (2).
5) Remove pipe clamp then remove suction pipe and liquid pipe.
6) Remove expansion valve (1).
INSTALLATION
1) Reverse removal sequence to install expansion valve.
2) Evacuate and charge system. Refer to ªEVACUATINGº and
ªCHARGINGº in this section.
Page 114 of 801
YH4
GRAND
VITARA
1. Evaporator thermistorTemperature
Resistance ( )
AIR CONDITIONING (OPTIONAL) 1B-43
A / C EVAPORATOR THERMISTOR
(EVAPORATOR TEMPERATURE SENSOR)
A thermistor is a temperature sensor to sense the temperature of
air discharged from evaporator. The electrical characteristic is
shown in the figure.
When temperature is lower than preset temperature, amplifier
makes magnet clutch turn off to prevent evaporator from frosting.
INSPECTION
Check resistance between A / C evaporator thermistor (1) termi-
nals.
If check results are as not specified, replace thermistor.
Sensor Temperature
Resistance
0C, 32F7.0 ± 7.7 k
25C, 77F2.1 ± 2.4 k
REMOVAL
Refer to ªCOOLING UNIT (EVAPORATOR)º in this section.
INSTALLATION
1) Reverse removal sequence to install thermistor.
2) Enable air bag system. Refer to ªENABLING AIR BAG SYS-
TEMº in Section 10B.
3) Evacuate and charge system. Refer to ªEVACUATINGº and
ªCHARGINGº in this section.
Page 115 of 801
YH4
GRAND
VITARA
1B-44 AIR CONDITIONING (OPTIONAL)
REFRIGERANT PIPES AND HOSES
INSPECTION
1) Use a leak tester to check hoses and pipes for any gas leakage.
2) Check each hose or pipe clamp for tightness.
Retighten or replace loose clamp as required, if any.
REMOVAL
1) Recover refrigerant by using recovery and recycling equipment.
Be sure to follow the instruction manual for the equipment.
The amount of compressor oil removed must be measured and
the same amount must be added to the system when reinstal-
ling.
2) Replace defective hose or pipe.
CAUTION:
As soon as the above hose or pipe is disconnected, cap
its opened fitting to prevent moisture and dust from en-
tering.
INSTALLATION
1) Reverse removal procedure to install refrigerant line.
2) Evacuate and charge system. Refer to ªEVACUATINGº and
ªCHARGINGº in this section.
INSPECTION OF IDLE SPEED WITH A / C ON
For G16 and J20 engines model, refer to Section 6E1.
For H25 engine model, refer to Section 6E2.
Page 116 of 801
YH4
GRAND
VITARA
1
1. Mode control switch coupler
2. A / C switch
3. Indicator lamp
AIR CONDITIONING (OPTIONAL) 1B-45
A / C SWITCH
REMOVAL
1) Disconnect negative (±) cable at battery.
2) If equipped with air bag system, disable air bag system.
Refer to ªDISABLING AIR BAG SYSTEMº in Section 10B.
3) Remove mode control switch (Refer to ªMODE CONTROL
SWITCHº in Section 1A).
INSPECTION
A / C Switch
Press A / C button and check if there is continuity between termi-
nals ªDº and ªGº.
With battery voltage (+) connected to terminal ªKº and (±) to termi-
nal ªDº, press A / C button and check if indicator lamp lights.
INSTALLATION
1) Install in reverse order of removal procedure.
2) If equipped with air bag system, enable air bag system.
Refer to ªENABLING AIR BAG SYSTEMº in Section 10B.
Page 117 of 801
YH4
GRAND
VITARA
1B-46 AIR CONDITIONING (OPTIONAL)
A / C CONTROLLER
REMOVAL
1) Disconnect negative (±) cable at battery.
2) Disable air bag system, if equipped.
Refer to ªDISABLING AIR BAG SYSTEMº in Section 10B.
3) Open glove box, then remove screw.
4) Remove glove box.
5) Disconnect A / C controller coupler (2), evaporator thermistor
coupler (3).
6) Remove A / C controller (1) from heater unit (4).
INSPECTION
Refer to ªINSPECTION OF A / C CONTROLLER AND ITS CIR-
CUITº in this section.
INSTALLATION
1) Install in reverse order of removal procedure.
2) If equipped with air bag system, enable air bag system. Refer to
ªENABLING AIR BAG SYSTEMº in Section 10B.
Page 118 of 801
YH4
GRAND
VITARA
Pressure ABCD SWITCH
ON
(Continuity)
OFF
(No continuity)
AIR CONDITIONING (OPTIONAL) 1B-47
DUAL PRESSURE SWITCH
INSPECTION
1) Check dual pressure switch (1) on liquid pipe for continuity at
normal temperature (approx. 25C (77F)) when A / C system
has a proper charge of refrigerant and when A / C system (com-
pressor) is under operation. In each of these cases, switch
should show proper continuity.
2) Using a manifold gauge set, check switch for operation at speci-
fied pressure as shown, refer to ªPERFORMANCE DIAGNO-
SISº in this section.
Switch ON : above ªCº and below ªDº
Switch OFF : below ªAº or above ªBº
ªAº: Approx. 200 kPa (2.0 kg / cm
2)
ªBº: Approx. 3200 kPa (32 kg / cm
2)
ªCº: Approx. 230 kPa (2.3 kg / cm
2)
ªDº: Approx. 2800 kPa (28 kg / cm
2)
Tightening torque:
Dual pressure switch: 10 N
.m (1.0 kg-m, 7.5 lb-ft)
Page 120 of 801
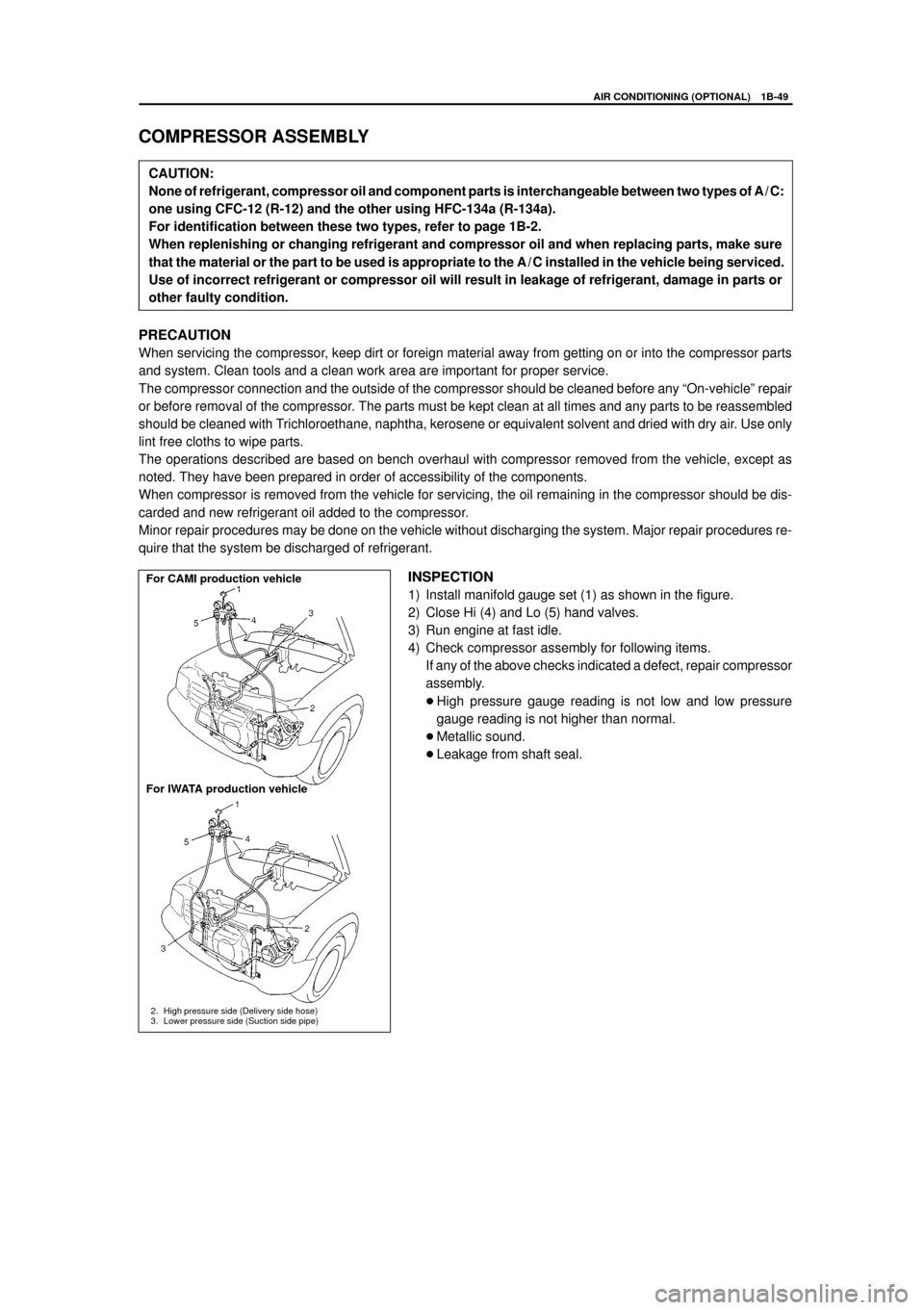
YH4
GRAND
VITARA
For CAMI production vehicle
For IWATA production vehicle
2. High pressure side (Delivery side hose)
3. Lower pressure side (Suction side pipe)
AIR CONDITIONING (OPTIONAL) 1B-49
COMPRESSOR ASSEMBLY
CAUTION:
None of refrigerant, compressor oil and component parts is interchangeable between two types of A / C:
one using CFC-12 (R-12) and the other using HFC-134a (R-134a).
For identification between these two types, refer to page 1B-2.
When replenishing or changing refrigerant and compressor oil and when replacing parts, make sure
that the material or the part to be used is appropriate to the A / C installed in the vehicle being serviced.
Use of incorrect refrigerant or compressor oil will result in leakage of refrigerant, damage in parts or
other faulty condition.
PRECAUTION
When servicing the compressor, keep dirt or foreign material away from getting on or into the compressor parts
and system. Clean tools and a clean work area are important for proper service.
The compressor connection and the outside of the compressor should be cleaned before any ªOn-vehicleº repair
or before removal of the compressor. The parts must be kept clean at all times and any parts to be reassembled
should be cleaned with Trichloroethane, naphtha, kerosene or equivalent solvent and dried with dry air. Use only
lint free cloths to wipe parts.
The operations described are based on bench overhaul with compressor removed from the vehicle, except as
noted. They have been prepared in order of accessibility of the components.
When compressor is removed from the vehicle for servicing, the oil remaining in the compressor should be dis-
carded and new refrigerant oil added to the compressor.
Minor repair procedures may be done on the vehicle without discharging the system. Major repair procedures re-
quire that the system be discharged of refrigerant.
INSPECTION
1) Install manifold gauge set (1) as shown in the figure.
2) Close Hi (4) and Lo (5) hand valves.
3) Run engine at fast idle.
4) Check compressor assembly for following items.
If any of the above checks indicated a defect, repair compressor
assembly.
High pressure gauge reading is not low and low pressure
gauge reading is not higher than normal.
Metallic sound.
Leakage from shaft seal.
Page 121 of 801
YH4
GRAND
VITARA
1B-50 AIR CONDITIONING (OPTIONAL)
REMOVAL
1) Run engine at idle with A / C ON for 10 minutes.
2) Disconnect negative (±) cable at battery.
3) Recover refrigerant from refrigeration system using recovery
and recycling equipment.
NOTE:
The amount of compressor oil at removed must be mea-
sured and the same amount must be poured when installing
the compressor.
4) Disconnect thermal protector lead wire.
5) Disconnect suction and discharge hoses from compressor as-
sembly.
NOTE:
Cap open fitting immediately to keep moisture out of sys-
tem.
6)For G16 engine:
Remove compressor drive belt by loosening compressor as-
sembly mounting bolts.
For J20 engine:
Remove generator belt. Refer to Section 6H.
For H25 engine:
Remove compressor drive belt by loosening tension pulley bolt.
7) Remove compressor with magnet clutch assembly from its
mount.
8) If compressor assembly is replaced. Drain oil from compressor
assembly, and measure its amount.