Page 13 of 667
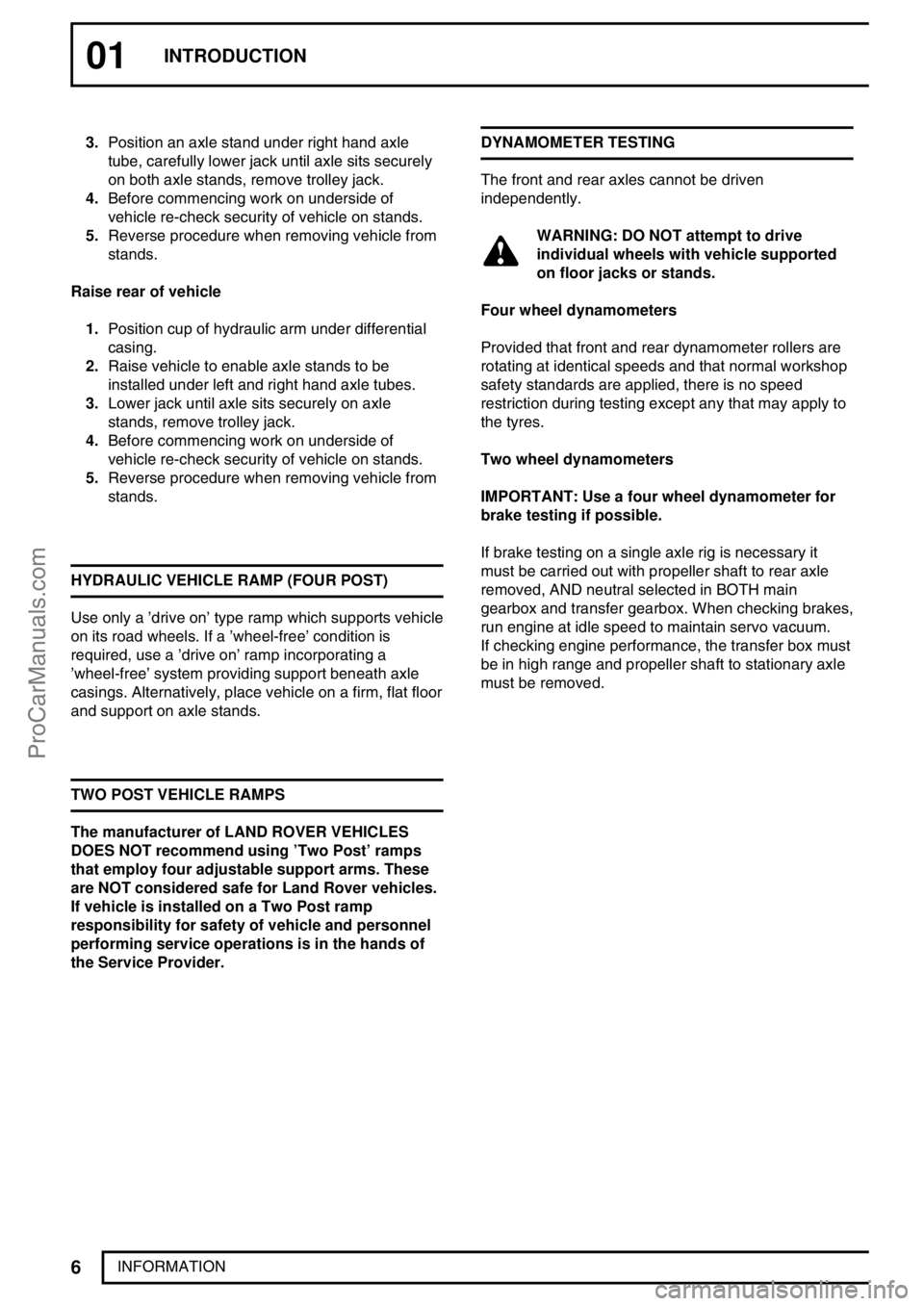
01INTRODUCTION
6
INFORMATION 3.Position an axle stand under right hand axle
tube, carefully lower jack until axle sits securely
on both axle stands, remove trolley jack.
4.Before commencing work on underside of
vehicle re-check security of vehicle on stands.
5.Reverse procedure when removing vehicle from
stands.
Raise rear of vehicle
1.Position cup of hydraulic arm under differential
casing.
2.Raise vehicle to enable axle stands to be
installed under left and right hand axle tubes.
3.Lower jack until axle sits securely on axle
stands, remove trolley jack.
4.Before commencing work on underside of
vehicle re-check security of vehicle on stands.
5.Reverse procedure when removing vehicle from
stands.
HYDRAULIC VEHICLE RAMP (FOUR POST)
Use only a’drive on’type ramp which supports vehicle
on its road wheels. If a’wheel-free’condition is
required, use a’drive on’ramp incorporating a
’wheel-free’system providing support beneath axle
casings. Alternatively, place vehicle on a firm, flat floor
and support on axle stands.
TWO POST VEHICLE RAMPS
The manufacturer of LAND ROVER VEHICLES
DOES NOT recommend using ’Two Post’ ramps
that employ four adjustable support arms. These
are NOT considered safe for Land Rover vehicles.
If vehicle is installed on a Two Post ramp
responsibility for safety of vehicle and personnel
performing service operations is in the hands of
the Service Provider.DYNAMOMETER TESTING
The front and rear axles cannot be driven
independently.
WARNING: DO NOT attempt to drive
individual wheels with vehicle supported
on floor jacks or stands.
Four wheel dynamometers
Provided that front and rear dynamometer rollers are
rotating at identical speeds and that normal workshop
safety standards are applied, there is no speed
restriction during testing except any that may apply to
the tyres.
Two wheel dynamometers
IMPORTANT: Use a four wheel dynamometer for
brake testing if possible.
If brake testing on a single axle rig is necessary it
must be carried out with propeller shaft to rear axle
removed, AND neutral selected in BOTH main
gearbox and transfer gearbox. When checking brakes,
run engine at idle speed to maintain servo vacuum.
If checking engine performance, the transfer box must
be in high range and propeller shaft to stationary axle
must be removed.
ProCarManuals.com
Page 50 of 667
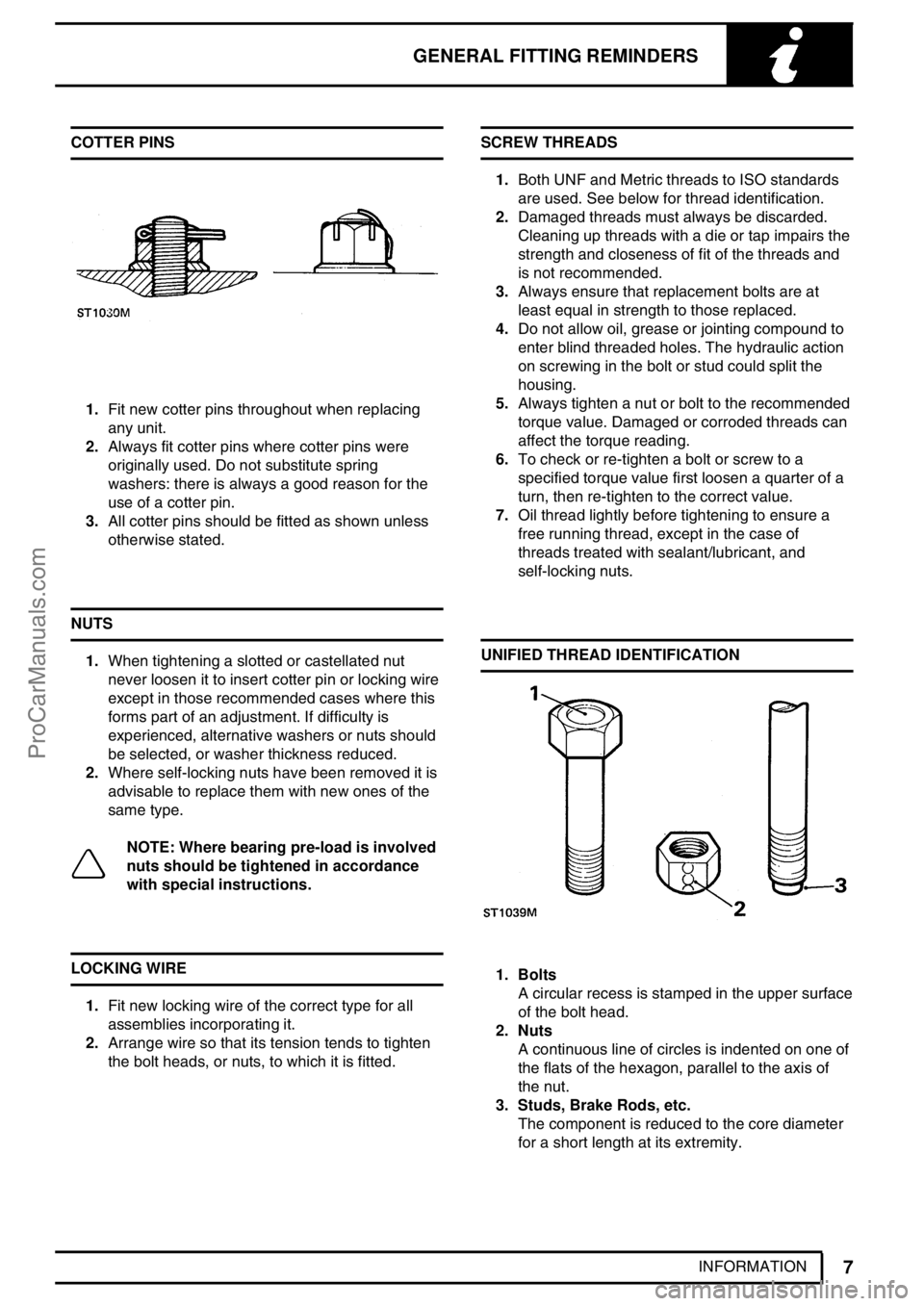
GENERAL FITTING REMINDERS
7
INFORMATION COTTER PINS
1.Fit new cotter pins throughout when replacing
any unit.
2.Always fit cotter pins where cotter pins were
originally used. Do not substitute spring
washers: there is always a good reason for the
use of a cotter pin.
3.All cotter pins should be fitted as shown unless
otherwise stated.
NUTS
1.When tightening a slotted or castellated nut
never loosen it to insert cotter pin or locking wire
except in those recommended cases where this
forms part of an adjustment. If difficulty is
experienced, alternative washers or nuts should
be selected, or washer thickness reduced.
2.Where self-locking nuts have been removed it is
advisable to replace them with new ones of the
same type.
NOTE: Where bearing pre-load is involved
nuts should be tightened in accordance
with special instructions.
LOCKING WIRE
1.Fit new locking wire of the correct type for all
assemblies incorporating it.
2.Arrange wire so that its tension tends to tighten
the bolt heads, or nuts, to which it is fitted.SCREW THREADS
1.Both UNF and Metric threads to ISO standards
are used. See below for thread identification.
2.Damaged threads must always be discarded.
Cleaning up threads with a die or tap impairs the
strength and closeness of fit of the threads and
is not recommended.
3.Always ensure that replacement bolts are at
least equal in strength to those replaced.
4.Do not allow oil, grease or jointing compound to
enter blind threaded holes. The hydraulic action
on screwing in the bolt or stud could split the
housing.
5.Always tighten a nut or bolt to the recommended
torque value. Damaged or corroded threads can
affect the torque reading.
6.To check or re-tighten a bolt or screw to a
specified torque value first loosen a quarter of a
turn, then re-tighten to the correct value.
7.Oil thread lightly before tightening to ensure a
free running thread, except in the case of
threads treated with sealant/lubricant, and
self-locking nuts.
UNIFIED THREAD IDENTIFICATION
1. Bolts
A circular recess is stamped in the upper surface
of the bolt head.
2. Nuts
A continuous line of circles is indented on one of
the flats of the hexagon, parallel to the axis of
the nut.
3. Studs, Brake Rods, etc.
The component is reduced to the core diameter
for a short length at its extremity.
ProCarManuals.com
Page 596 of 667
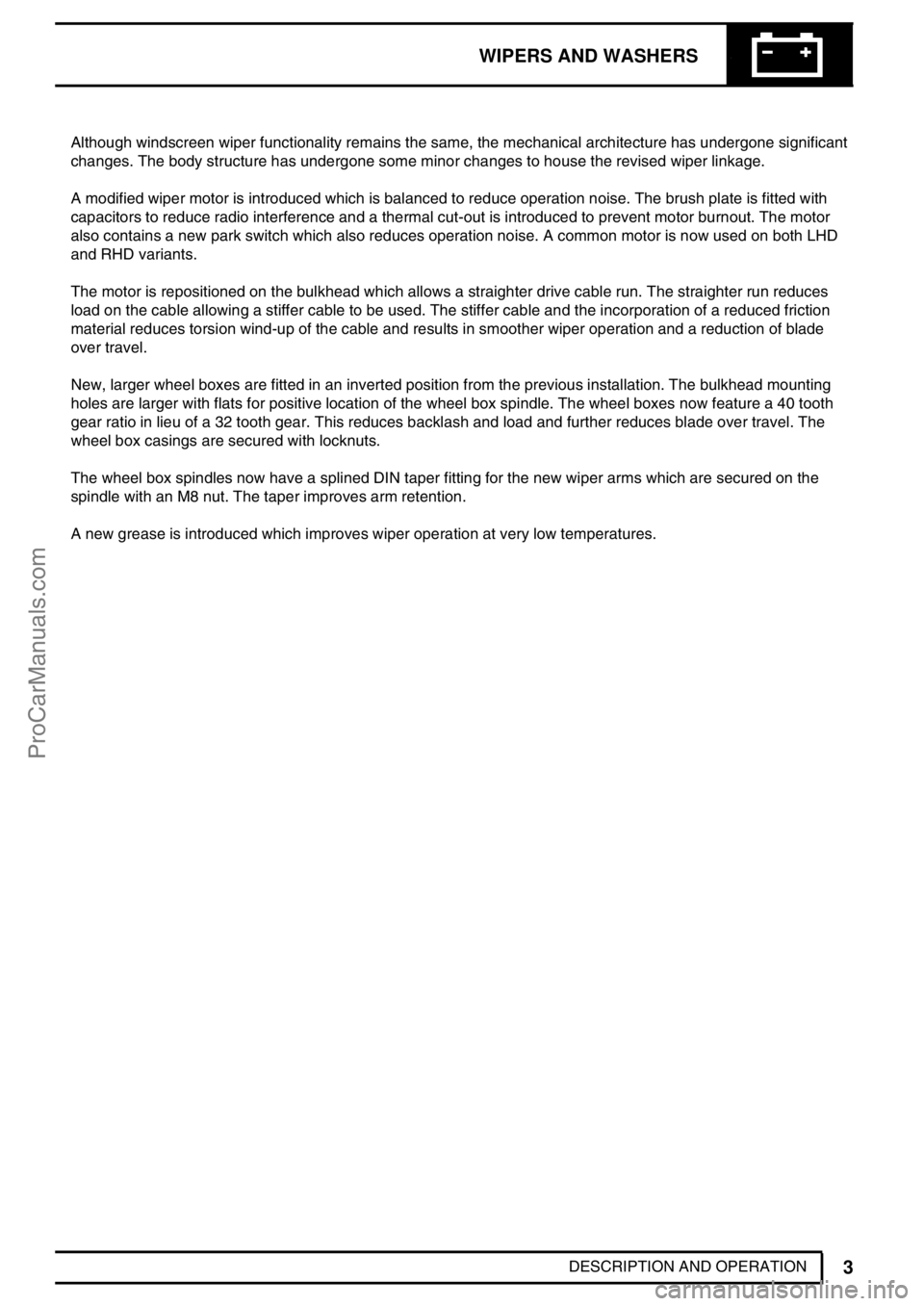
WIPERS AND WASHERS
3
DESCRIPTION AND OPERATION Although windscreen wiper functionality remains the same, the mechanical architecture has undergone significant
changes. The body structure has undergone some minor changes to house the revised wiper linkage.
A modified wiper motor is introduced which is balanced to reduce operation noise. The brush plate is fitted with
capacitors to reduce radio interference and a thermal cut-out is introduced to prevent motor burnout. The motor
also contains a new park switch which also reduces operation noise. A common motor is now used on both LHD
and RHD variants.
The motor is repositioned on the bulkhead which allows a straighter drive cable run. The straighter run reduces
load on the cable allowing a stiffer cable to be used. The stiffer cable and the incorporation of a reduced friction
material reduces torsion wind-up of the cable and results in smoother wiper operation and a reduction of blade
over travel.
New, larger wheel boxes are fitted in an inverted position from the previous installation. The bulkhead mounting
holes are larger with flats for positive location of the wheel box spindle. The wheel boxes now feature a 40 tooth
gear ratio in lieu of a 32 tooth gear. This reduces backlash and load and further reduces blade over travel. The
wheel box casings are secured with locknuts.
The wheel box spindles now have a splined DIN taper fitting for the new wiper arms which are secured on the
spindle with an M8 nut. The taper improves arm retention.
A new grease is introduced which improves wiper operation at very low temperatures.
ProCarManuals.com