Page 13 of 73
AIR CONDITIONING
General
62
A Passenger compartment
B Engine compartment
C Exterior air
D To air mixing unit
E Scuttle panel grille
F Exterior or recirculated air
1 Compressor with variable capacity
2 Condenser
3 Dehydration canister
4 Pressure sensor
5 High pressure valve
6 Pressure relief valve
7 Evaporator
8 Low pressure valve
9 Heating/ventilation fan
10 Cooling fan
11 Engine radiator
12 High pressure fluid
13 Low pressure vapour
14 High pressure vapour
Consumables:
- Compressor oil
SANDEN SP 10: 135 cm3 ± 15
- Coolant
R134a: 650 g ± 35
- Compressor
SANDEN SD 7V 16
62-2
Page 34 of 73
c11010.0
AIR CONDITIONING
Fault finding charts
62
KANGOO
ALL TYPES
Check that the components which were removed are connected correctly.
Check that the system operates correctly.AFTER
REPAIR
yes
CHART 3
CONT
A
noChange the thermostat.
yes
yes
noEnd of fault finding.
noEnd of fault finding.
With the engine cold, remove the engine
coolant thermostat and check that it is not
jammed in the open position.
Is it correct?
Check that there is no unwanted intake of
cold air into the passenger compartment
(seals, grommets, cables ...).
Repair if necessary
Does the fault persist?
Check the air inlets (particle filter)
and outlets.
Partially blocked air inlets or outlets
reduce the flow of heated air
into the
passenger compartment.
Repair if necessary.
Does the fault persist?
The heater radiator must be blocked. Remove
the radiator and clean or change it
(only valid for vehicles which have been
driven without the particle filter).
62-23
Page 36 of 73
c11010.0
AIR CONDITIONING
Fault finding charts
62
KANGOO
ALL TYPES
Check that the system operates correctly.AFTER
REPAIR
yes
CHART 5TOO HOT
NOTES
noSee CHART 1.
noReadjust the cable
(to the right of the air distribution unit).
yes
yesSee CHART 11.
no
Before carrying out any work, check that the customer uses the air conditioning
correctly.
Non regulated air conditioning.
Visually check that moving the control
moves the mixing flap.
Does it move?
Check that the flap travel
is complete.
Is the travel complete?
Check the operation
of the recirculation flap.
Is it jammed in the recirculation position?
Check the operation
of the engine coolant thermostat.
Change the thermostat if necessary.
62-25
Page 49 of 73
yes
c11010.0
CONDITIONING
Fault finding charts
62
KANGOO
ALL TYPES
AFTER
REPAIR
CHART 14
CONT
noTop up the coolant circuit.
yes
noSee CHART 15.
Change the pressure sensor.
Check the cleanness of the
condenser wiring harness.
Clean or change the condenser.
If the fault persists, check the operation of
the cooling fan assembly at high speed
(ventilation and air conditioning
on maximum).
It should be:
- operating if high pressure≥ 20 bars
- stopped if high pressure≤ 15 bars
Is the operation of the fan assembly normal?
Check that the components which were removed are connected correctly.
Check that the system operates correctly.
A
With the vehicle stationary, engine running
at idle, air conditioning on maximum,
measure the pressure of the coolant circuit.
If the pressure is > 28 bars, there is :
- too much fluid,
- or the operation of the fan assembly is ab-
normal,
- or the condenser is clogged,
- or the engine heats up too much.
Is the pressure < 28 bars ?
62-38
Page 50 of 73
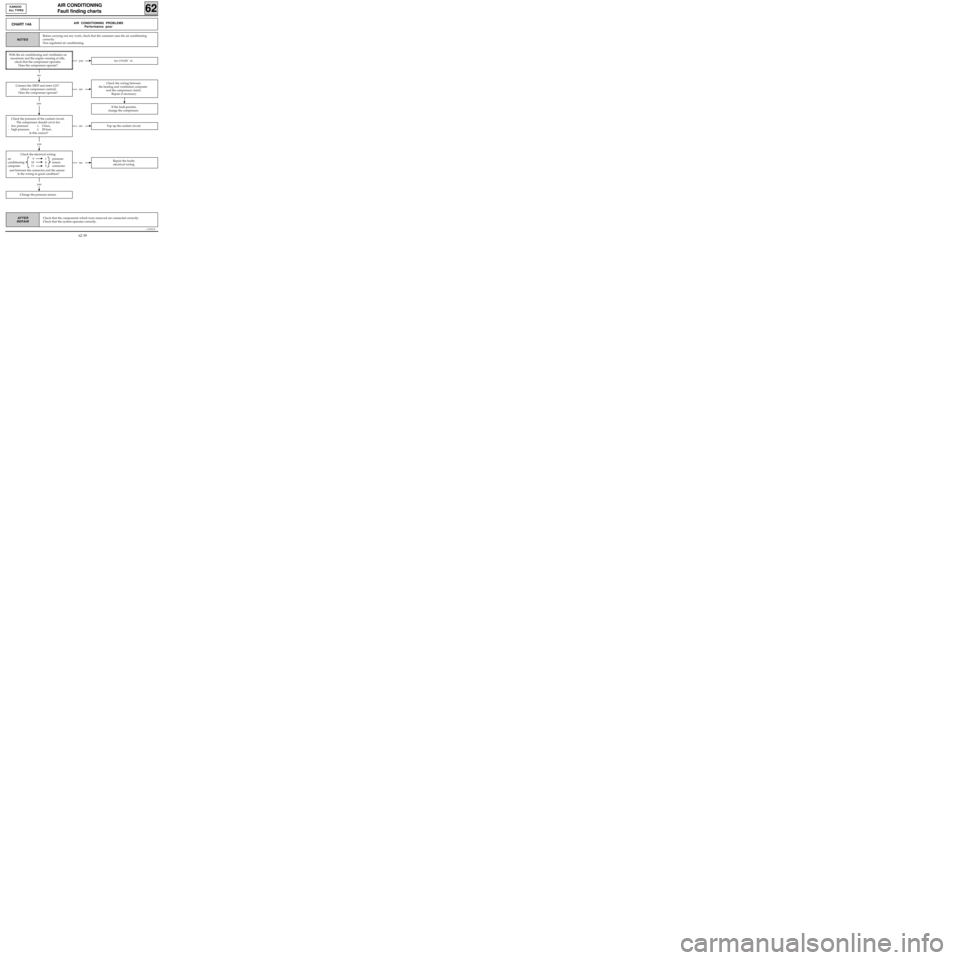
yes
Check the electrical wiring:
air 9 1 pressure
conditioning 10 4 sensor
computer 11 3 connector
and between the connector and the sensor.
Is the wiring in good condition?
c11010.0
AIR CONDITIONING
Fault finding charts
62
KANGOO
ALL TYPES
AFTER
REPAIR
CHART 14AAIR CONDITIONING PROBLEMS
Performance poor
NOTES
yesSee CHART 14.
no
no
If the fault persists,
change the compressor.
yes
noRepair the faulty
electrical wiring.
yes
noTop up the coolant circuit.
Change the pressure sensor.
Before carrying out any work, check that the customer uses the air conditioning
correctly.
Non regulated air conditioning.
With the air conditioning and ventilation on
maximum and the engine running at idle,
check that the compressor operates.
Does the compressor operate?
Connect the XR25 and enter G21*
(direct compressor control).
Does the compressor operate?
Check the pressure of the coolant circuit.
The compressor should cut in for:
- low pressure≥ 2 bars,
- high pressure≤ 28 bars.
Is this correct?
Check the wiring between
the heating and ventilation computer
and the compressor clutch.
Repair if necessary.
Check that the components which were removed are connected correctly.
Check that the system operates correctly.
62-39
Page 54 of 73
c11010.0
AIR CONDITIONING
Fault finding - Associated checks
62
KANGOO
ALL TYPES
COMMAND MODE G--*
To use this function, enter G on the XR25 keypad, then the number of the command selected followed by
an asterisk.
G21* : compressor clutch control
G22* : fan low speed control
G23* : fan high speed control
G24* : recirculation motor control
G13* : end of fault finding
COMMAND MODE #
# 08 : fan assembly speed
# 15 : engine speed
# 16 : pressure of coolant in the circuit
62-43
Page 62 of 73
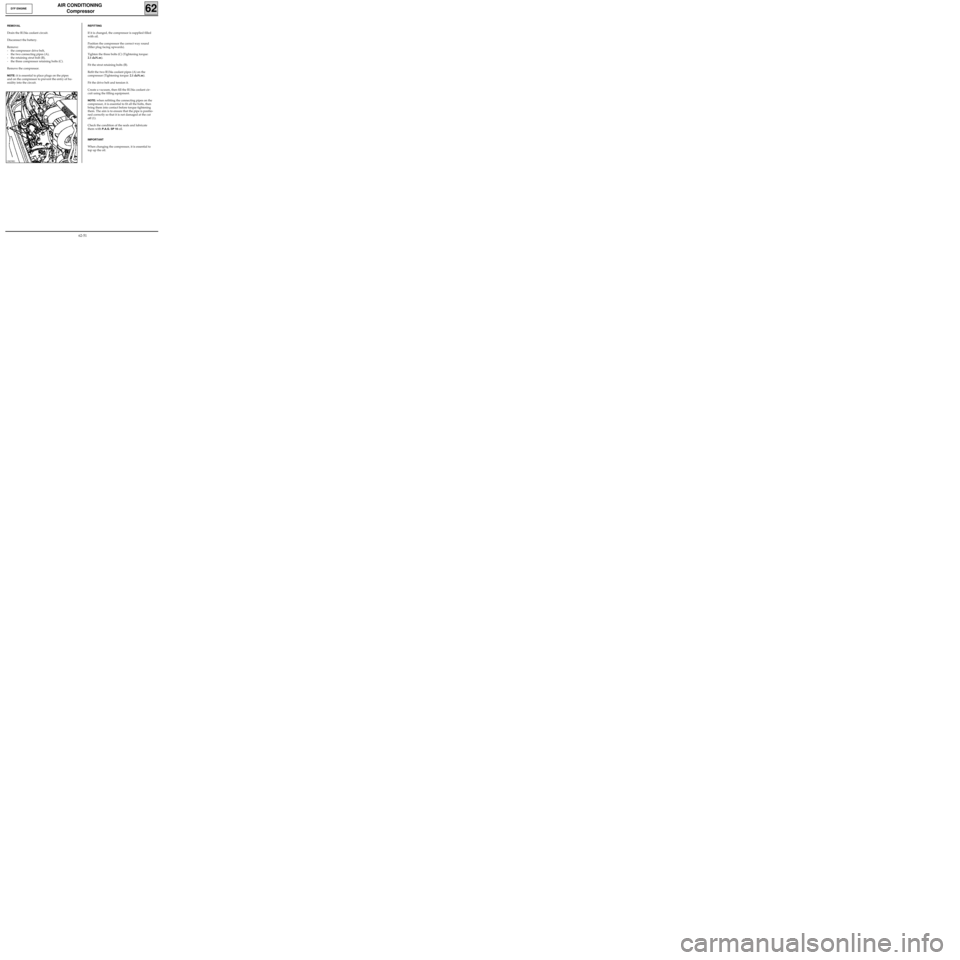
AIR CONDITIONING
Compressor
62D7F ENGINE
13829R1
REMOVAL
Drain the R134a coolant circuit.
Disconnect the battery.
Remove:
- the compressor drive belt,
- the two connecting pipes (A),
- the retaining strut bolt (B),
- the three compressor retaining bolts (C).
Remove the compressor.
NOTE: it is essential to place plugs on the pipes
and on the compressor to prevent the entry of hu-
midity into the circuit.
REFITTING
If it is changed, the compressor is supplied filled
with oil.
Position the compressor the correct way round
(filler plug facing upwards).
Tighten the three bolts (C) (Tightening torque:
2.1 daN.m).
Fit the strut retaining bolts (B).
Refit the two R134a coolant pipes (A) on the
compressor (Tightening torque:
2.1 daN.m).
Fit the drive belt and tension it.
Create a vacuum, then fill the R134a coolant cir-
cuit using the filling equipment.
NOTE: when refitting the connecting pipes on the
compressor, it is essential to fit all the bolts, then
bring them into contact before torque tightening
them. The aim is to ensure that the pipe is positio-
ned correctly so that it is not damaged at the cut
off (1).
Check the condition of the seals and lubricate
them with
P.A.G. SP 10 oil.
IMPORTANT
When changing the compressor, it is essential to
top up the oil.
62-51
Page 63 of 73
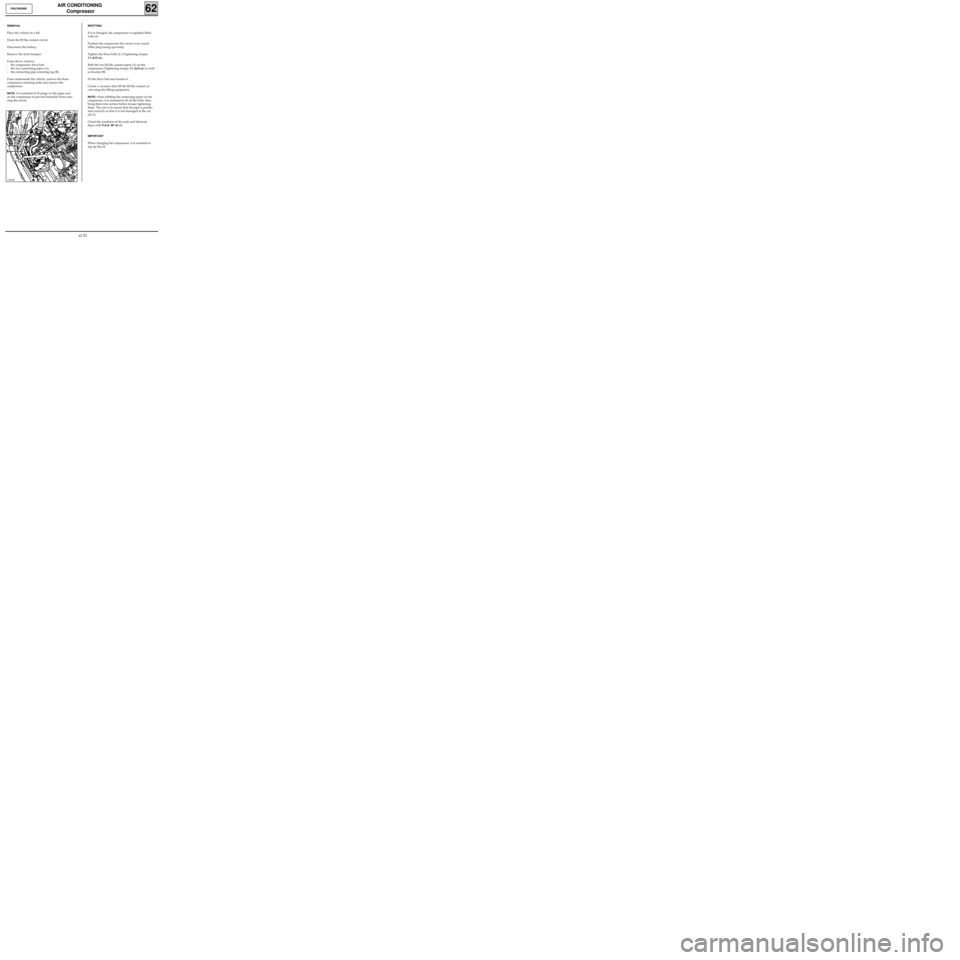
AIR CONDITIONING
Compressor
62F8Q ENGINE
REMOVAL
Place the vehicle on a lift.
Drain the R134a coolant circuit.
Disconnect the battery.
Remove the front bumper.
From above, remove:
- the compressor drive belt,
- the two connecting pipes (A),
- the connecting pipe retaining lug (B).
From underneath the vehicle, remove the three
compressor retaining bolts and remove the
compressor.
NOTE: it is essential to fit plugs on the pipes and
on the compressor to prevent humidity from ente-
ring the circuit.
13947R
REFITTING
If it is changed, the compressor is supplied filled
with oil.
Position the compressor the correct way round
(filler plug facing upwards).
Tighten the three bolts (C) (Tightening torque:
2.1 daN.m).
Refit the two R134a coolant pipes (A) on the
compressor (Tightening torque:
2.1 daN.m) as well
as bracket (B).
Fit the drive belt and tension it.
Create a vacuum, then fill the R134a coolant cir-
cuit using the filling equipment.
NOTE: when refitting the connecting pipes on the
compressor, it is essential to fit all the bolts, then
bring them into contact before torque tightening
them. The aim is to ensure that the pipe is positio-
ned correctly so that it is not damaged at the cut
off (1).
Check the condition of the seals and lubricate
them with
P.A.G. SP 10 oil.
IMPORTANT
When changing the compressor, it is essential to
top up the oil.
62-52