Page 70 of 396
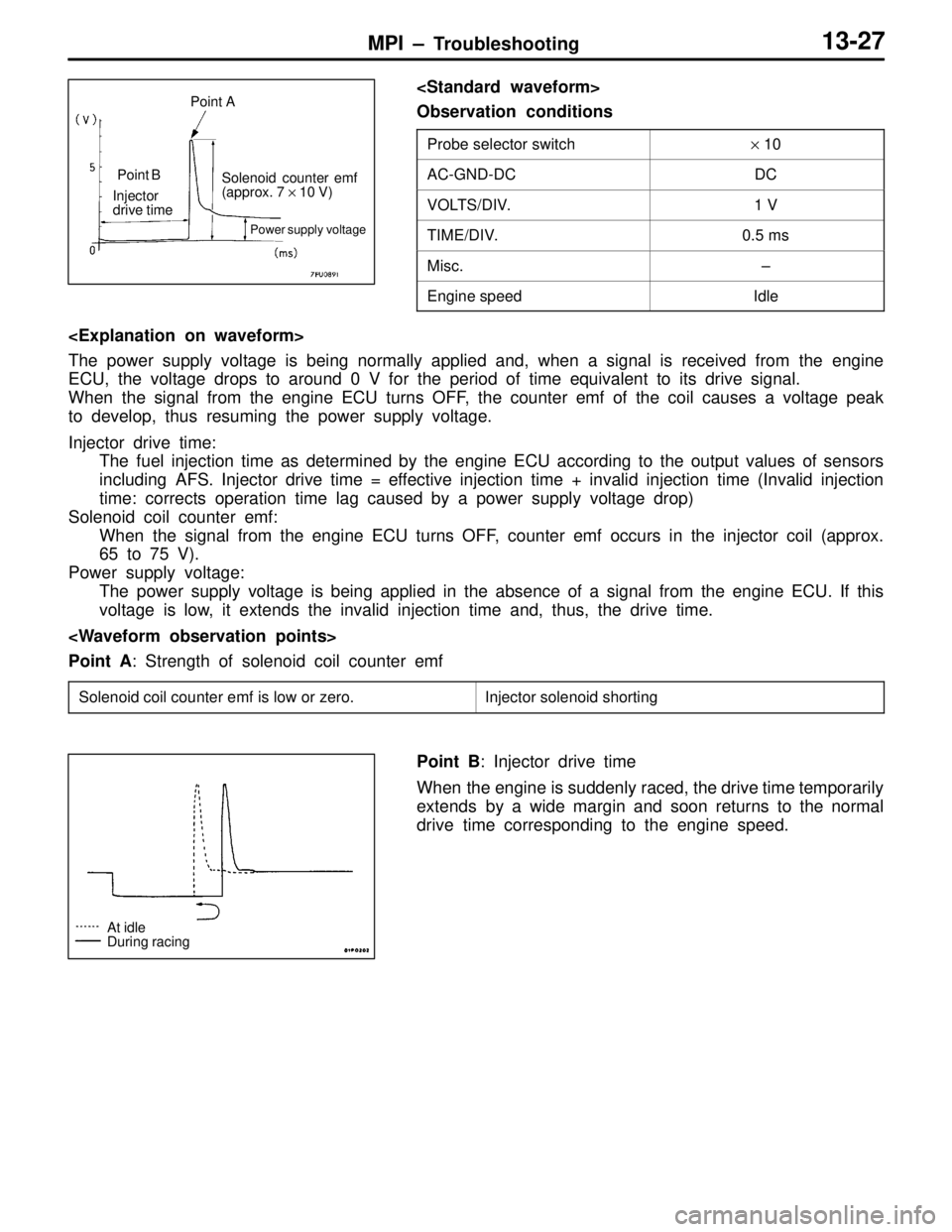
MPI – Troubleshooting13-27
Observation conditions
Probe selector switch× 10
AC-GND-DCDC
VOLTS/DIV.1 V
TIME/DIV.0.5 ms
Misc.–
Engine speedIdle
The power supply voltage is being normally applied and, when a signal is received from the engine
ECU, the voltage drops to around 0 V for the period of time equivalent to its drive signal.
When the signal from the engine ECU turns OFF, the counter emf of the coil causes a voltage peak
to develop, thus resuming the power supply voltage.
Injector drive time:
The fuel injection time as determined by the engine ECU according to the output values of sensors
including AFS. Injector drive time = effective injection time + invalid injection time (Invalid injection
time: corrects operation time lag caused by a power supply voltage drop)
Solenoid coil counter emf:
When the signal from the engine ECU turns OFF, counter emf occurs in the injector coil (approx.
65 to 75 V).
Power supply voltage:
The power supply voltage is being applied in the absence of a signal from the engine ECU. If this
voltage is low, it extends the invalid injection time and, thus, the drive time.
Point A: Strength of solenoid coil counter emf
Solenoid coil counter emf is low or zero.Injector solenoid shorting
Point B: Injector drive time
When the engine is suddenly raced, the drive time temporarily
extends by a wide margin and soon returns to the normal
drive time corresponding to the engine speed.
Point A
Point B
Injector
drive timeSolenoid counter emf
(approx. 7 × 10 V)
Power supply voltage
At idle
During racing
Page 74 of 396
MPI – On-vehicle Service13-31
5. MPI SYSTEM COMPONENTS LAYOUT
NameSymbolNameSymbol
A/C switchQExhaust temperature warning lampS
A/C relayHFuel pressure control valveA
Air flow sensor (with a built-in intake air temperaturesensor and barometric pressure sensor)FIgnition coil and power transistor unitLsensor and barometric pressure sensor)InjectorB
Camshaft position sensorMISC servoD
Control relay and fuel pump relayPOxygen sensorK
Coolant temperature sensorEPower steering fluid pressure switchI
Crank angle sensorJSecondary air control solenoid valveN
Detonation sensorCThrottle position sensor (with a built-in idle switch)D
Diagnosis connectorR
Engine ECUOVehicle speed sensorT
Engine warning lampSWastegate solenoid valveG
Page 94 of 396
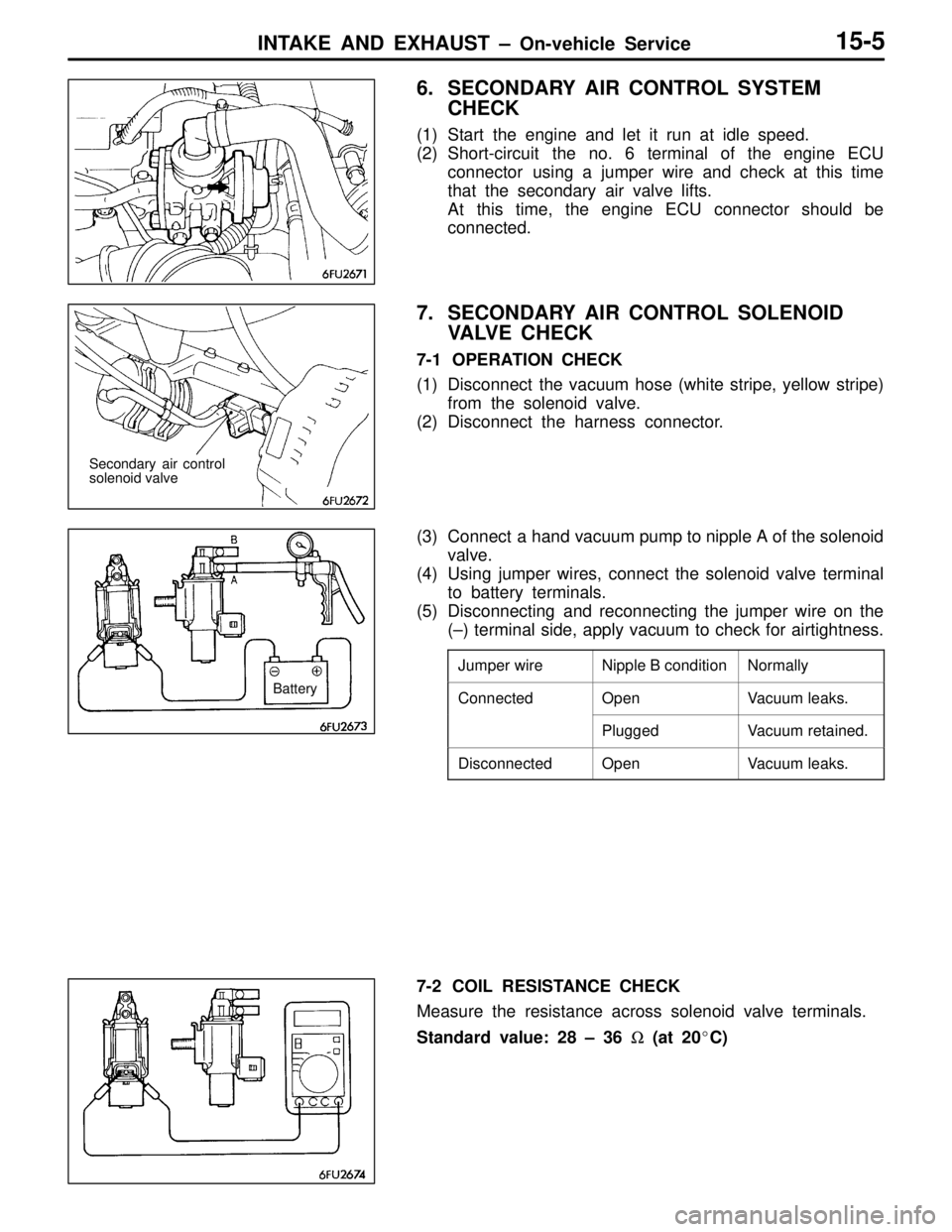
INTAKE AND EXHAUST – On-vehicle Service15-5
6. SECONDARY AIR CONTROL SYSTEM
CHECK
(1) Start the engine and let it run at idle speed.
(2) Short-circuit the no. 6 terminal of the engine ECU
connector using a jumper wire and check at this time
that the secondary air valve lifts.
At this time, the engine ECU connector should be
connected.
7. SECONDARY AIR CONTROL SOLENOID
VALVE CHECK
7-1 OPERATION CHECK
(1) Disconnect the vacuum hose (white stripe, yellow stripe)
from the solenoid valve.
(2) Disconnect the harness connector.
(3) Connect a hand vacuum pump to nipple A of the solenoid
valve.
(4) Using jumper wires, connect the solenoid valve terminal
to battery terminals.
(5) Disconnecting and reconnecting the jumper wire on the
(–) terminal side, apply vacuum to check for airtightness.
Jumper wireNipple B conditionNormally
ConnectedOpenVacuum leaks.
PluggedVacuum retained.
DisconnectedOpenVacuum leaks.
7-2 COIL RESISTANCE CHECK
Measure the resistance across solenoid valve terminals.
Standard value: 28 – 36 Ω (at 20C)
Secondary air control
solenoid valve
Battery
Page 124 of 396
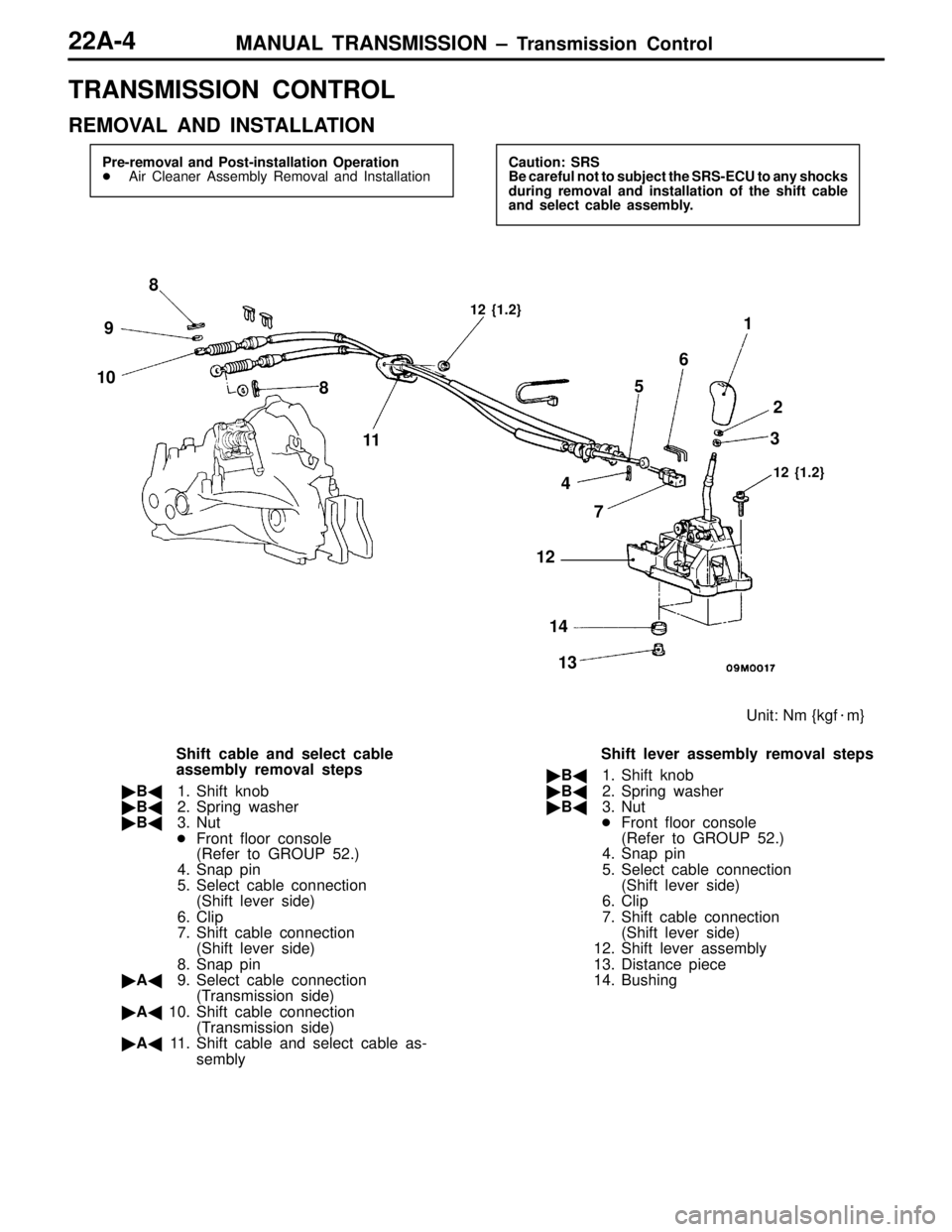
MANUAL TRANSMISSION – Transmission Control22A-4
TRANSMISSION CONTROL
REMOVAL AND INSTALLATION
Pre-removal and Post-installation Operation
Air Cleaner Assembly Removal and InstallationCaution: SRS
Be careful not to subject the SRS-ECU to any shocks
during removal and installation of the shift cable
and select cable assembly.
456
7 8
9
10
11
12
13 141
2
3 8
Unit: Nm {kgfm}
12 {1.2}
12 {1.2}
Shift cable and select cable
assembly removal steps
B1. Shift knob
B2. Spring washer
B3. Nut
Front floor console
(Refer to GROUP 52.)
4. Snap pin
5. Select cable connection
(Shift lever side)
6. Clip
7. Shift cable connection
(Shift lever side)
8. Snap pin
A9. Select cable connection
(Transmission side)
A10. Shift cable connection
(Transmission side)
A11. Shift cable and select cable as-
semblyShift lever assembly removal steps
B1. Shift knob
B2. Spring washer
B3. Nut
Front floor console
(Refer to GROUP 52.)
4. Snap pin
5. Select cable connection
(Shift lever side)
6. Clip
7. Shift cable connection
(Shift lever side)
12. Shift lever assembly
13. Distance piece
14. Bushing
Page 152 of 396
MANUAL TRANSMISSION OVERHAUL – Input Shaft22B-22
REASSEMBLY SERVICE POINTS
AOIL SEAL INSTALLATION
Make sure that the oil seal is pressed into the position shown
in the illustration.
BBALL BEARING INSTALLATION
CSNAP RING INSTALLATION
Select and install a snap ring so that the input shaft front
bearing end play will have the standard value.
Standard value: 0 – 0.12 mm
DSYNCHRONIZER SPRING INSTALLATION
Install the synchronizer spring securely to the illustrated
position of the outer synchronizer ring.
E3RD-4TH SPEED SYNCHRONIZER HUB
INSTALLATION
Install the synchronizer hub in such a way that it will be oriented
in the direction shown.Oil seal
3.5 mm
MD998801MD998812
MD998813
MD998818
Snap ring
Synchronizer spring
Installation
direction
Identification mark
Page 178 of 396
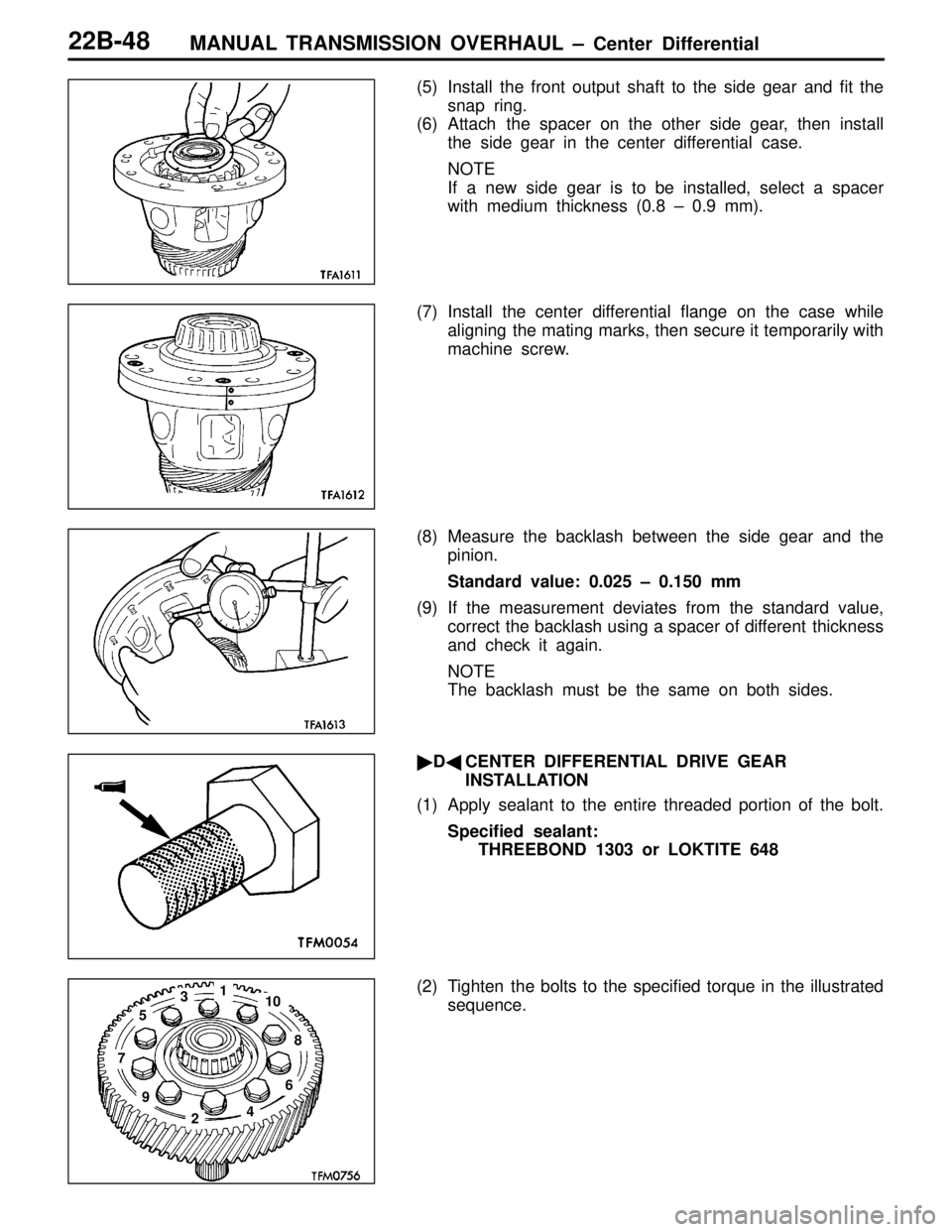
MANUAL TRANSMISSION OVERHAUL – Center Differential22B-48
(5) Install the front output shaft to the side gear and fit the
snap ring.
(6) Attach the spacer on the other side gear, then install
the side gear in the center differential case.
NOTE
If a new side gear is to be installed, select a spacer
with medium thickness (0.8 – 0.9 mm).
(7) Install the center differential flange on the case while
aligning the mating marks, then secure it temporarily with
machine screw.
(8) Measure the backlash between the side gear and the
pinion.
Standard value: 0.025 – 0.150 mm
(9) If the measurement deviates from the standard value,
correct the backlash using a spacer of different thickness
and check it again.
NOTE
The backlash must be the same on both sides.
DCENTER DIFFERENTIAL DRIVE GEAR
INSTALLATION
(1) Apply sealant to the entire threaded portion of the bolt.
Specified sealant:
THREEBOND 1303 or LOKTITE 648
(2) Tighten the bolts to the specified torque in the illustrated
sequence.
1
8
7
6
5
4
3
2
10
9
Page 185 of 396
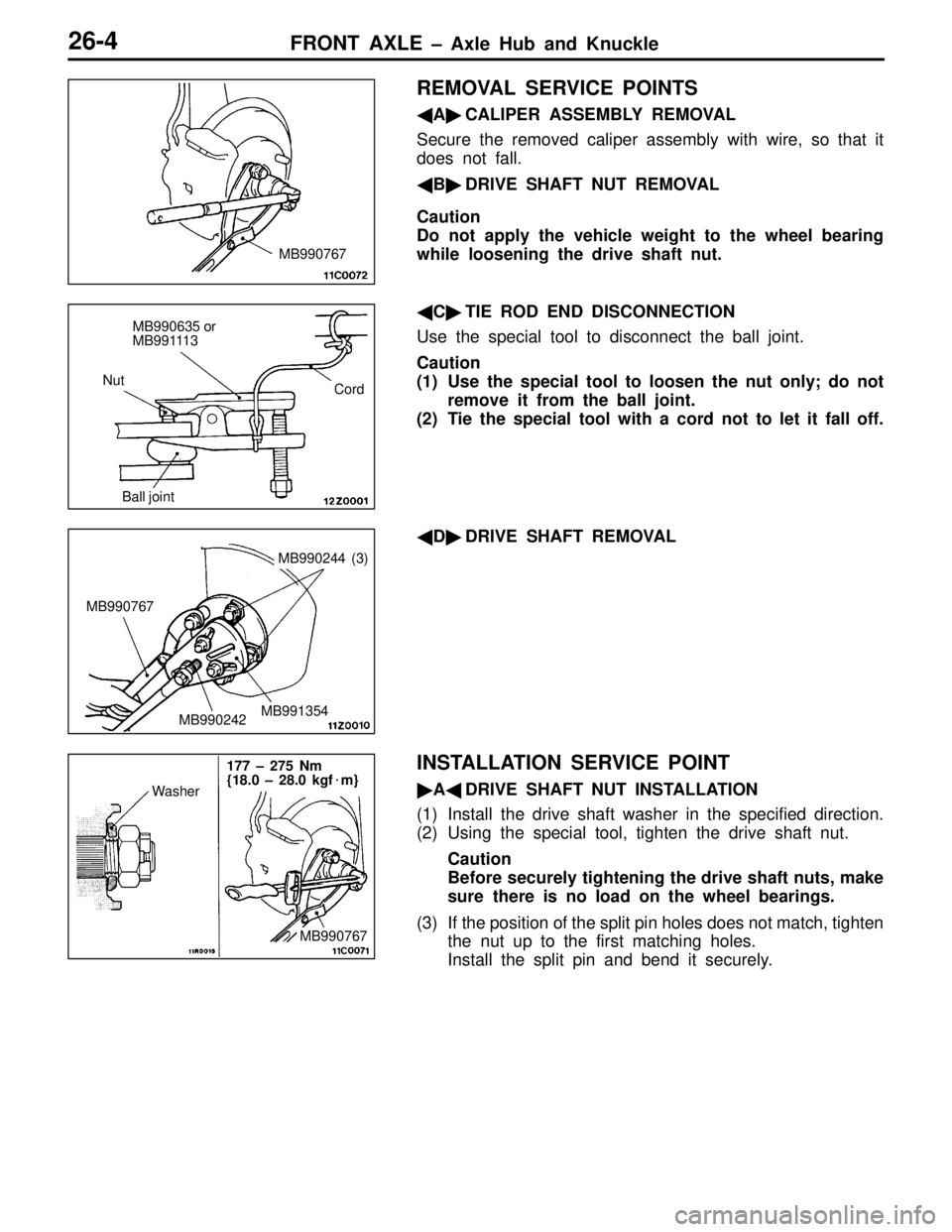
FRONT AXLE – Axle Hub and Knuckle26-4
REMOVAL SERVICE POINTS
ACALIPER ASSEMBLY REMOVAL
Secure the removed caliper assembly with wire, so that it
does not fall.
BDRIVE SHAFT NUT REMOVAL
Caution
Do not apply the vehicle weight to the wheel bearing
while loosening the drive shaft nut.
CTIE ROD END DISCONNECTION
Use the special tool to disconnect the ball joint.
Caution
(1) Use the special tool to loosen the nut only; do not
remove it from the ball joint.
(2) Tie the special tool with a cord not to let it fall off.
DDRIVE SHAFT REMOVAL
INSTALLATION SERVICE POINT
ADRIVE SHAFT NUT INSTALLATION
(1) Install the drive shaft washer in the specified direction.
(2) Using the special tool, tighten the drive shaft nut.
Caution
Before securely tightening the drive shaft nuts, make
sure there is no load on the wheel bearings.
(3) If the position of the split pin holes does not match, tighten
the nut up to the first matching holes.
Install the split pin and bend it securely.
MB990767
MB990635 or
MB991113
Ball joint
CordNut
MB990767
MB990242MB991354
MB990244 (3)
177 – 275 Nm
{18.0 – 28.0 kgfm}
Washer
MB990767
Page 187 of 396
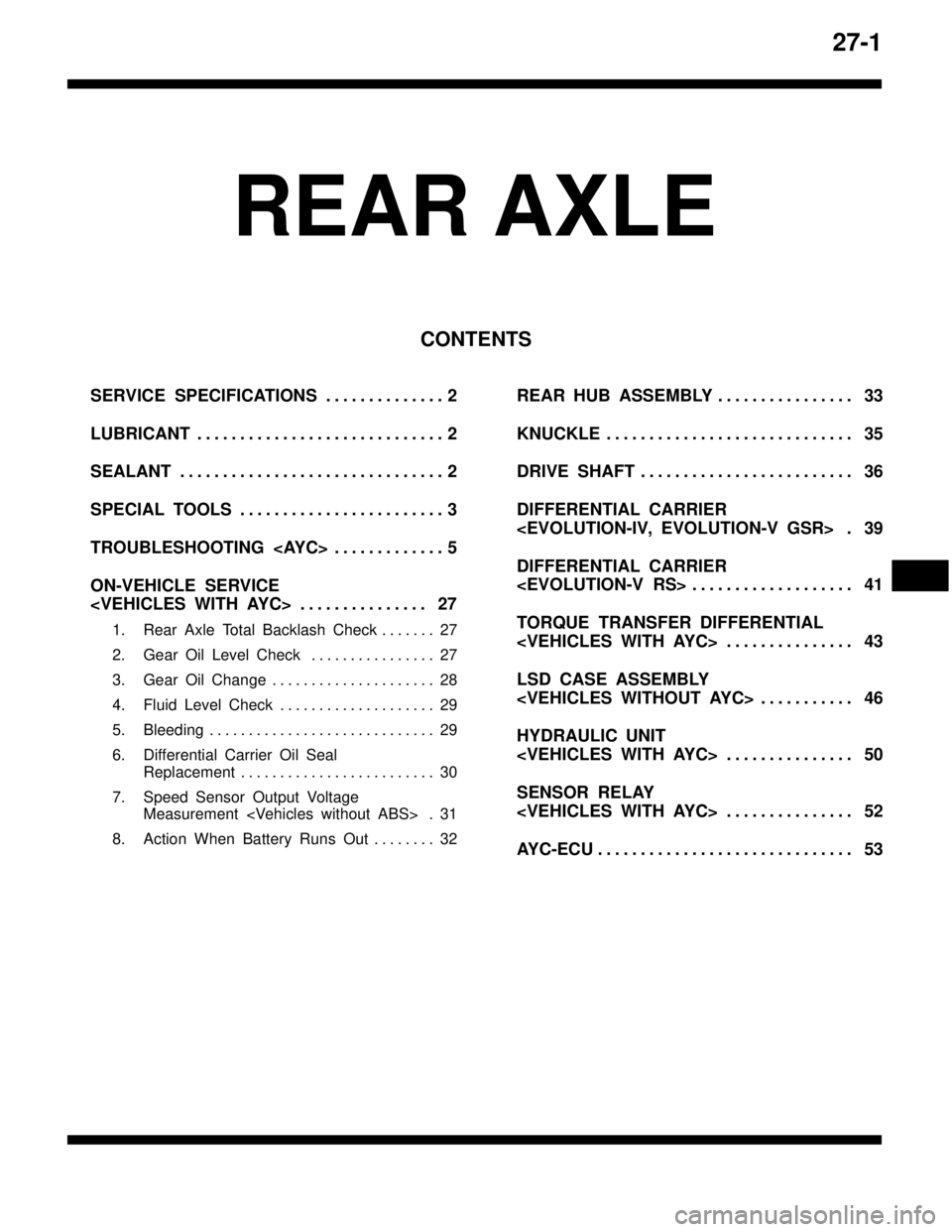
27-1
REAR AXLE
CONTENTS
SERVICE SPECIFICATIONS 2. . . . . . . . . . . . . .
LUBRICANT 2. . . . . . . . . . . . . . . . . . . . . . . . . . . . .
SEALANT 2. . . . . . . . . . . . . . . . . . . . . . . . . . . . . . .
SPECIAL TOOLS 3. . . . . . . . . . . . . . . . . . . . . . . .
TROUBLESHOOTING 5. . . . . . . . . . . . .
ON-VEHICLE SERVICE
27. . . . . . . . . . . . . . .
1. Rear Axle Total Backlash Check 27. . . . . . .
2. Gear Oil Level Check 27. . . . . . . . . . . . . . . .
3. Gear Oil Change 28. . . . . . . . . . . . . . . . . . . . .
4. Fluid Level Check 29. . . . . . . . . . . . . . . . . . . .
5. Bleeding 29. . . . . . . . . . . . . . . . . . . . . . . . . . . . .
6. Differential Carrier Oil Seal
Replacement 30. . . . . . . . . . . . . . . . . . . . . . . . .
7. Speed Sensor Output Voltage
Measurement 31.
8. Action When Battery Runs Out 32. . . . . . . .
REAR HUB ASSEMBLY 33. . . . . . . . . . . . . . . .
KNUCKLE 35. . . . . . . . . . . . . . . . . . . . . . . . . . . . .
DRIVE SHAFT 36. . . . . . . . . . . . . . . . . . . . . . . . .
DIFFERENTIAL CARRIER
39.
DIFFERENTIAL CARRIER
41. . . . . . . . . . . . . . . . . . .
TORQUE TRANSFER DIFFERENTIAL
43. . . . . . . . . . . . . . .
LSD CASE ASSEMBLY
46. . . . . . . . . . .
HYDRAULIC UNIT
50. . . . . . . . . . . . . . .
SENSOR RELAY
52. . . . . . . . . . . . . . .
AYC-ECU 53. . . . . . . . . . . . . . . . . . . . . . . . . . . . . .