Page 878 of 2490
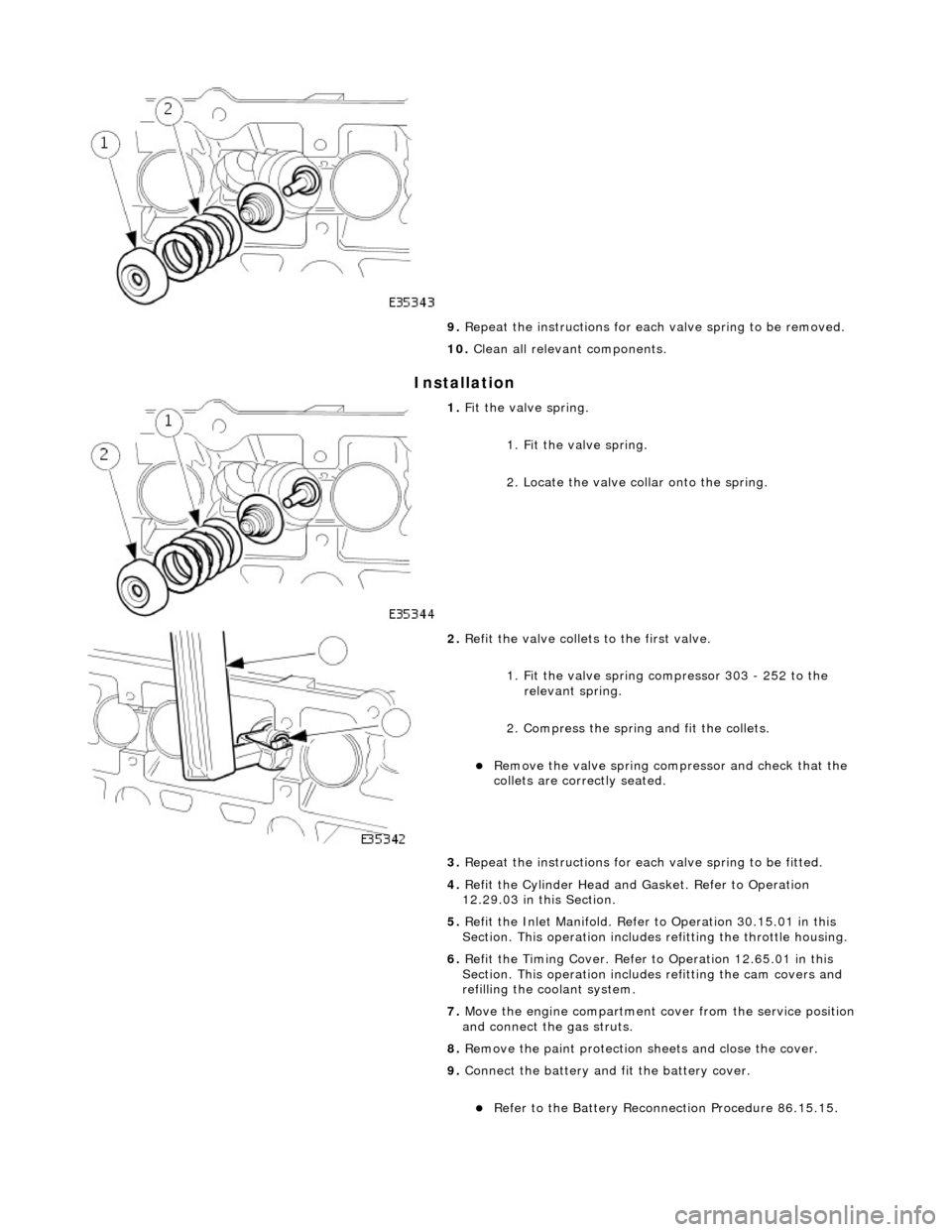
Installation
9. Repeat the instructions for each valve spring to be removed.
10. Clean all relevant components.
1. Fit the valve spring.
1. Fit the valve spring.
2. Locate the valve collar onto the spring.
2. Refit the valve collets to the first valve.
1. Fit the valve spring compressor 303 - 252 to the relevant spring.
2. Compress the spring and fit the collets.
Remove the valve spring compressor and check that the
collets are correctly seated.
3. Repeat the instructions for each valve spring to be fitted.
4. Refit the Cylinder Head and Gasket. Refer to Operation
12.29.03 in this Section.
5. Refit the Inlet Manifold. Refer to Operation 30.15.01 in this
Section. This operation includes refitting the throttle housing.
6. Refit the Timing Cover. Refer to Operation 12.65.01 in this
Section. This operation includes refitting the cam covers and
refilling the coolant system.
7. Move the engine compartment co ver from the service position
and connect the gas struts.
8. Remove the paint protection sheets and close the cover.
9. Connect the battery and fit the battery cover.
Refer to the Battery Reconnection Procedure 86.15.15.
Page 892 of 2490
2. Fit the bush carrier to the cylinder block.
Lubricate the seal (scarf jointed) and the bush.
1. Fit the bush carrier assembly.
Check that the seals are in pl ace and that the ring dowels
are engaged squarely. Fully locate the assembly as much
as possible by hand pressure.
2. Fit the two securing bolts and one nut. Tighten to 19- 23 Nm.
3. Refit the Timing Cover. Refer to Operation 12.65.01 in this
Section.
4. Move the engine compartment co ver from the service position
and connect the gas struts.
5. Remove the paint protection sheets and close the cover.
6. Connect the battery and fit the battery cover.
Refer to the Battery Reconnection Procedure 86.15.15.
Page 895 of 2490
2
. Fit the bush carrier to the cylinder block.
Lubricate the seal (scarf jointed) and the bush.
1. Fit the bush carrier assembly.
Check that the seals are in place and that the ring dowels are engaged squarely. Fully locate the
assembly as much as possible by hand pressure. 2. Fit the three securing bolts. Tighten to 19-23 Nm.
3. Refit the Timing Cover. Refer to Operation <<12.65.01>> in this Section.
4. Move the engine compartment cover from the service position and connect the gas struts.
5. Remove the paint protection sheets and close the cover.
6. Connect the battery and fit the battery cover. Refer to the Battery Reconnection Procedure <<86.15.15>>.
Page 918 of 2490
1.
Remove the blanking plugs from the pipes and
unions. Fit a new sealing washer to the high pressure
hose joint.
2. Connect the high pressure hose union.
3. Connect the feed hose to the pump.
34 . Conne
ct the engine oil
pressure transmitter.
35 .
Fit the radiator and
condense
r assembly. Check that the
lower mounting rubbers are located correctly.
36 . Fit the radiator top
retaining panel.
1. Fit the panel.
2. Check that the radiator top mounting bushes are
located correctly.
37. Fit the radiator top retaining panel.
Fit
the ten bolts which secure the panel.
Page 934 of 2490
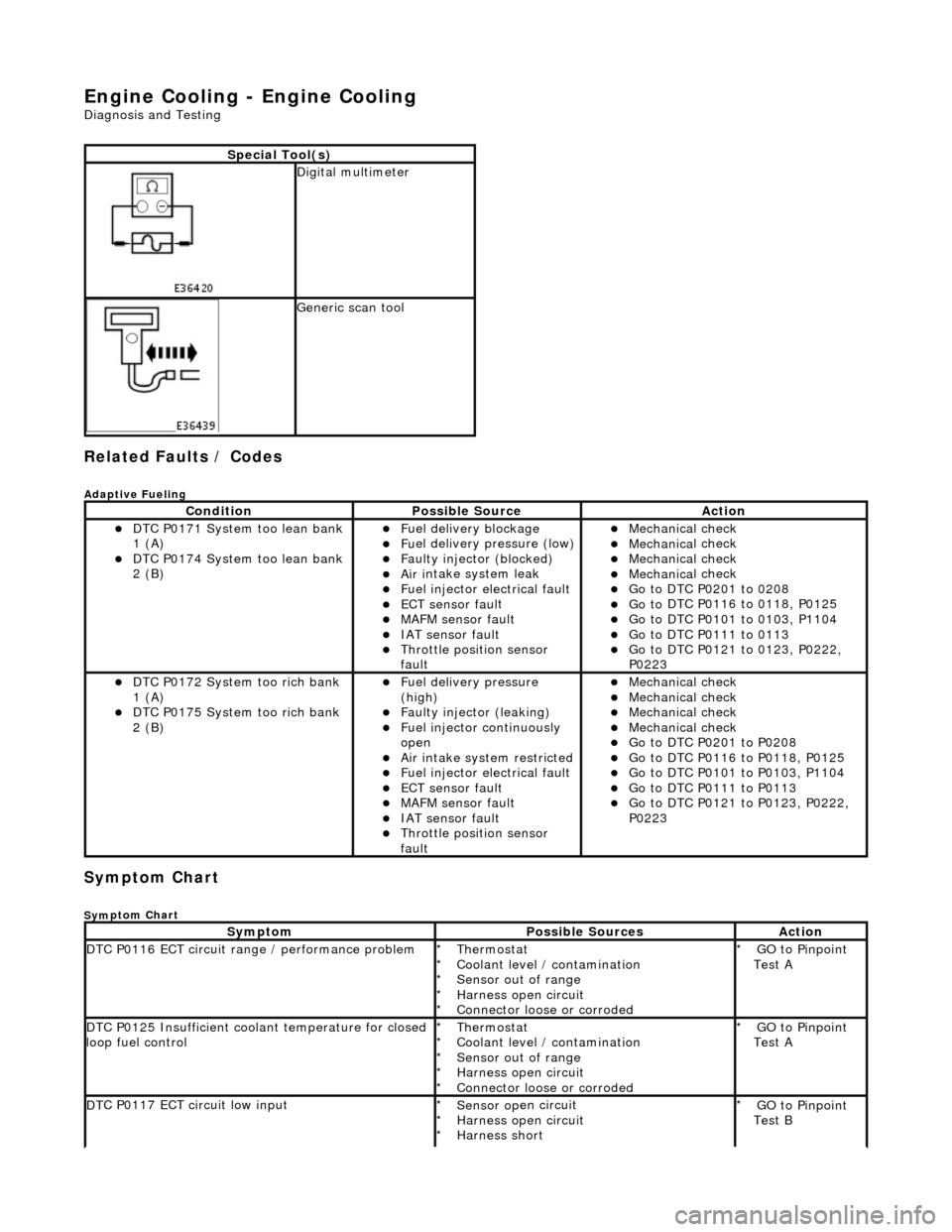
Engine Cooling - Engine Cooling
Diagn
osis and Testing
Related Faults / Codes
Adaptive
Fue
ling
Sym
p
tom Chart
Sy
m
ptom Chart
S
p
ecial Tool(s)
D
i
gital multimeter
Generi
c scan tool
Conditi
on
Possib
l
e Source
Acti
o
n
D
T
C P0171 System too lean bank
1 (A)
D T
C P0174 System too lean bank
2 (B)
Fuel delivery blockage Fu
el delivery pressure (low)
F
a
ulty injector (blocked)
Ai
r i
ntake system leak
F
u
el injector electrical fault
ECT sensor
faul
t
MAFM sensor fault IAT se
nsor fault
Thro
tt
le position sensor
fault
Mec hanica
l check
Mec
hanica
l check
Mec
hanica
l check
Mec
hanica
l check
Go t
o DTC P020
1 to 0208
Go t
o
DTC P0116 to 0118, P0125
Go t
o
DTC P0101 to 0103, P1104
Go t
o DTC P011
1 to 0113
Go t
o
DTC P0121 to 0123, P0222,
P0223
D T
C P0172 System too rich bank
1 (A)
D T
C P0175 System too rich bank
2 (B)
F u
el delivery pressure
(high)
F a
ulty injector (leaking)
F
u
el injector continuously
open
Ai r i
ntake system restricted
Fu
el injector electrical fault
ECT sensor
faul
t
MAFM sensor fault IAT sensor fault
Thrott
le position sensor
fault
Mec hanica
l check
Mec
hanica
l check
Mec
hanica
l check
Mec
hanica
l check
Go t
o DTC P020
1 to P0208
Go t
o
DTC P0116 to P0118, P0125
Go t
o
DTC P0101 to P0103, P1104
Go t
o DTC P011
1 to P0113
Go t
o
DTC P0121 to P0123, P0222,
P0223
Sy m
ptom
Possib
l
e Sources
Acti
o
n
D
T
C P0116 ECT circuit range / performance problem
Thermostat
Coo
l
ant level / contamination
Sensor out of range
Harness open circuit
Connector loose or corroded
*
*
*
*
*
GO to Pinpoint
Test A
*
D
T
C P0125 Insufficient coolant temperature for closed
loop fuel control
Thermostat
Coo l
ant level / contamination
Sensor out of range
Harness open circuit
Connector loose or corroded
*
*
*
*
*
GO to Pinpoint
Test A
*
D
T
C P0117 ECT circuit low input
Sensor o
p
en circuit
Harness open circuit
Harness short
*
*
*
GO to Pinpoint
Test B
*
Page 935 of 2490
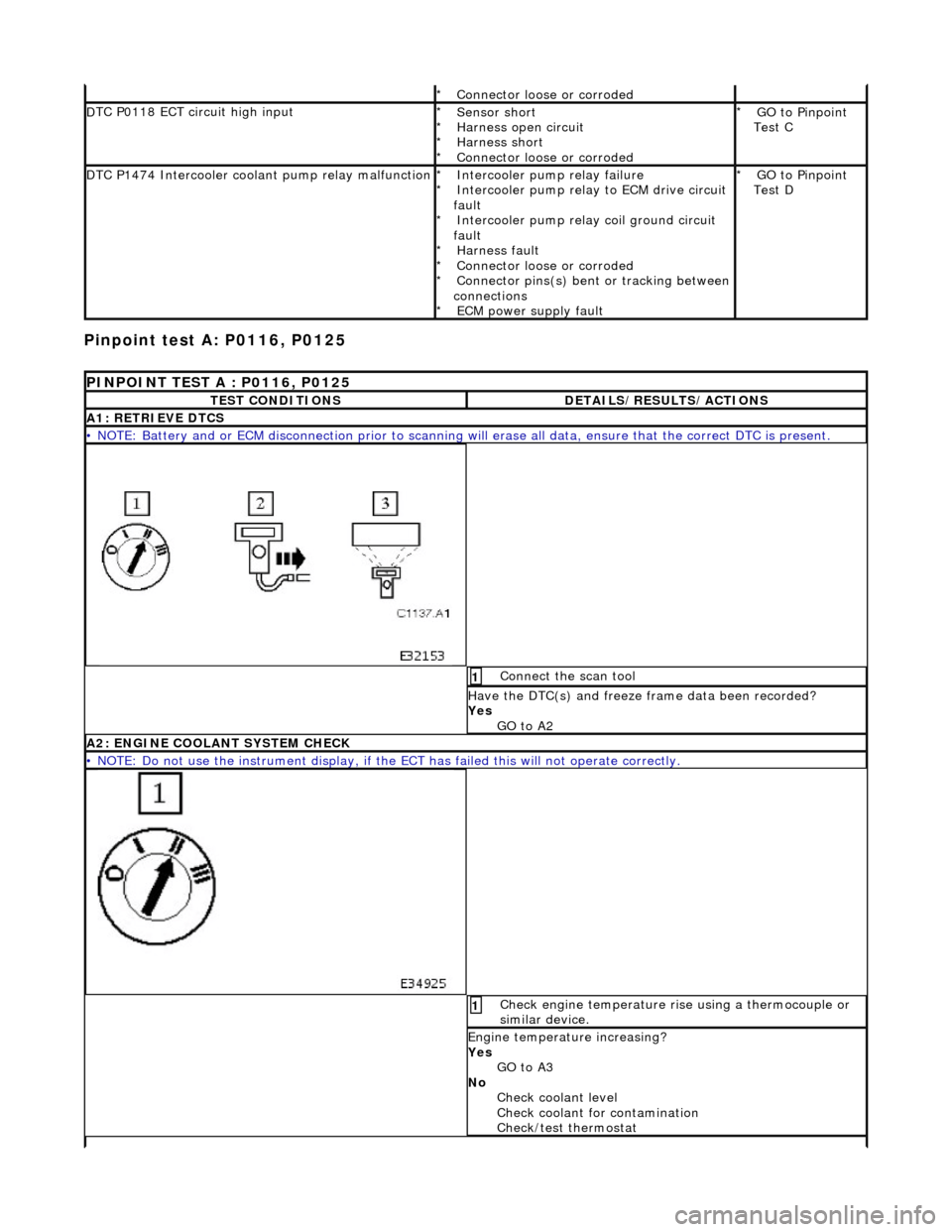
Pinpoint test
A: P0116, P0125
Connector
loose or corroded
*
D
TC P0118 ECT circuit high input
Sensor short
Harness open circui
t
Harness short
Connector loose or corroded
*
*
*
*
GO to Pinpoint
Test C
*
D
TC P1474 Intercooler coolant pump relay malfunction
Intercooler pump relay
failure
Intercooler pump relay to ECM drive circuit
fault Intercooler pump relay coil ground circuit
fault Harness fault
Connector loose or corroded
Connector pins(s) bent or tracking between
connections ECM power supply fault
*
*
*
*
*
*
*
GO to Pinpoint
Test D
*
P
INPOINT TEST A : P0116, P0125
T
EST CONDITIONS
D
ETAILS/RESULTS/ACTIONS
A1
: RETRIEVE DTCS
•
NOTE: Battery and or ECM disconnection prior to scanning wi
ll erase all data, ensure that the correct DTC is present.
Conne
ct the scan tool
1
Have the DTC(s) and fr
eeze
frame data been recorded?
Yes GO to A2
A2: ENGINE
COOLANT SYSTEM CHECK
•
NOTE: Do not use the instrument display, if th
e ECT has failed this will not operate correctly.
Chec
k engine temperature rise using a thermocouple or
similar device.
1
Engine
temperature increasing?
Yes GO to A3
No Check coolant level
Check coolant for contamination
Check/test thermostat
Page 936 of 2490
A3: CHECK ECT SE
NSOR RANGE
All
o
w the engine to achieve any noted temperature within
the specified range, refer to temperature / resistance
relationship table or graph
1
I g
nition switch to position 0
2
D
i
sconnect PI004
Re
ar
of top hose
3
Meas
ure t
he resistance between sensor pins 1 and 2.
4
Tem
p
erature / resistance relationship OK?
Yes GO to A4
No Remove sensor and check temperature / resistance
relationship for 3 different temperatures. Renew as
required and test the syst em for normal operation.
A4: CHECK
HARNESS
CONTINUITY
Page 947 of 2490
Conne
ct the scan tool
1
Have the DTC(s) and fr
eeze
frame data been recorded?
Yes GO to D2
D
2: CHECK FUSE
•
NOTE: See further steps for poss
ible cause of fuse failure.
Chec
k fuse F2 integrity (located in the engine
management fuse box).
1
OK
?
Yes GO to D3
No Renew fuse and test the syst em for normal operation.
D3: C
HECK RELAY SOCKET SUPPLY VOLTAGE
•
NOTE: Do not replace relay.