Page 44 of 105
REAR AXLE
Four bar rear axle
- the first anti-roll bar, ensuring the angle of
the block is observed, and the bar is inserted
freely.
33
13134S
- the second anti-roll bar, ensuring it engages
freely.
In order to position the suspension arm so that the
bar may be correctly positioned, a tool must be lo-
cally made.
ANut, diameter 14 mm
BNut, diameter 12 mm
CThreaded rod, diameter 12 mm - length 660
mm
DBracket from flat sheet 30 x 5 mm
E 12 x 60 mm bolt, cut to a length of 20 mm
FWeld
75505-1R1
88637R2
Preset the tool to obtain dimension "X".
X = 430 mm
Fit the tool in place of the shock absorber.
Refit:
- the bar plugs,
- the shock absorbers,
- the wheels.
Put the vehicle on its wheels and measure the un-
derbody heights ( see section "values and set-
tings" ).
33-18
Page 45 of 105
REAR AXLE
Four bar rear axle
33
Check and if necessary adjust:
- the braking compensator,
- the headlights.
REMINDER
When adjusting for a wheel height difference
between the right and left hand sides, always
make the adjustment on the anti-roll bars.
The adjustment for a difference in dimension " X"
between the right and left hand sides should
always be made on the suspension bars.
33-19
Page 49 of 105
Offset
(in mm)
DI3501
WHEELS AND TYRES
Specifications
WHEEL RIMS
There are two forms of wheel identification marking:
- engraved markings for steel rims,
- cast marking for alloy rims.
The marking gives the main dimensional specifications of the wheel.
The marking may be complete:
Example : 5 1/2 J 14 4 CH 36
or simplified
Example : 5 1/2 J 14
35
The four wheel bolts are over a diameter of 100
mm (4 mounting bolts).
Maximum run-out: 1.2 mm measured on the rim
edge (at G).
Maximum eccentricity: 0.8 mm measured on the
pressure face of the tyre beads.
FE
Number
of holes
DCB
WIDTH
(in inches)
5 1/2
A
TYPE
OF WHEEL
5 1/2 J 14
4 CH 36J144CH36
RIM
PROFILE
NOMINAL DIAMETER
(in inches). under tyre
beadTyre bead
profile
35-1
Page 50 of 105
85920R2
WHEELS AND TYRES
Specifications
Examples of identification marking
165/70SR1383
125463
165/70 R 13 83 S
TYRES
35
1165
702
3S
R
513
4
Tyre width in mm ( l ) section
Ratio h/lheight
width
Speed index 180 km/h maximum
Radial structure
Inner diameter expressed in inches. Corresponds to the diameter of the rim.
836Load index
Some speed symbols :Maximum speed km/h
R 170
S 180
T 190
U 200
H 210
V 240
ZR over 240
Types of structure :
Diagonal No marking
Radial R
Bias belted B
35-2
Page 51 of 105
WHEELS AND TYRES
Specifications
The tyre inflation pressures are values for a fully laden vehicle or motorway use.
The tyre inflation pressure must be checked when cold. The increase in temperature during driving increases
the pressure by 0.2 to 0.3 bar.
If the inflation pressures are checked when the tyres are warm, take this pressure increase into consideration.
Never deflate a warm tyre.
(1) Reinforced tyre.
Chains
For safety reasons, chains may NEVER be fitted to the rear axle.
"Snow" or "thermorubber" tyres: all four wheels must be fitted with these tyres to retain vehicle adhesion as
far as possible.
35
TypeRim
Wheel bolt
torque
(daN.m)
Tyres
Inflation pressure
(bar) cold
FrontRear
FC0X
KC0X
5 B 13
5 B 13
5,5 J 14
9
2.8
2.6
2.4
3.6
2.9
3.0
165/70 R 13 C 88/86
165/70 R 13 83 (1)
165/70 R 14
35-3
Page 52 of 105
88659R
WHEELS AND TYRES
Wheel balancing
35
BALANCE WEIGHTS
Only use weights provided by the Parts
Department:
- fitted using hooks to steel wheels (hook is part
of the weight),
- fitted using hooks (flat hooks) or self adhesive
for alloy wheels.
A Steel wheel rim
B Alloy wheel rim
35-4
Page 53 of 105
STEERING ASSEMBLY
Axial ball joint
36
Put the vehicle on a two post lift.
REMOVAL
Disconnect the track rod end using tool T.Av. 476.
Slacken the bolt on the parallelism adjustment
sleeve and slacken the track rod end while
holding the axial ball joint using an open wrench.
Make a mark or count the number of turns of
thread taken up so the parallelism can be pre-
adjusted on refitting.
Remove the plastic retaining clip for the gaiter
and remove the gaiter.
SPECIAL TOOLING REQUIRED
Wheel bolts 9
Track rod end nut 3.7
Bolt on parallelism adjustment sleeve 1.7
Axial ball joint 5
Dir. 1305-01 Tool for removing - refitting
axial ball joint
Dir. 1306 Tool for retaining SMI unit rack
T.Av. 476 Ball joint extractor
TIGHTENING TORQUES (in daN.m)Turn the wheels so the rack teeth are freed on the
valve side.
Fit tool Dir. 1306.
In this position, release the axial ball joint using
tool Dir. 1305-01.
97469R1
36-1
Page 55 of 105
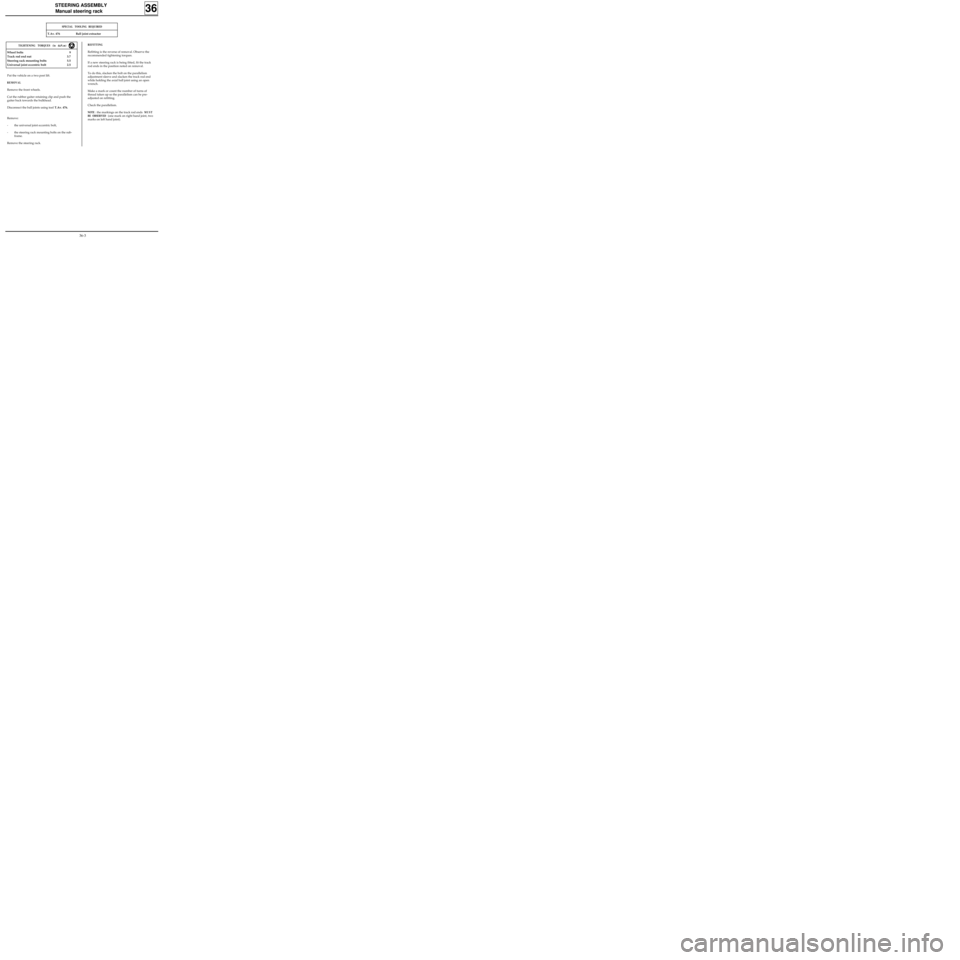
STEERING ASSEMBLY
Manual steering rack
36
Put the vehicle on a two post lift.
REMOVAL
Remove the front wheels.
Cut the rubber gaiter retaining clip and push the
gaiter back towards the bulkhead.
Disconnect the ball joints using tool T.Av. 476.
Remove:
- the universal joint eccentric bolt,
- the steering rack mounting bolts on the sub-
frame.
Remove the steering rack.
SPECIAL TOOLING REQUIRED
Wheel bolts 9
Track rod end nut 3.7
Steering rack mounting bolts 5.5
Universal joint eccentric bolt 2.5
T.Av. 476 Ball joint extractor
TIGHTENING TORQUES (in daN.m)REFITTING
Refitting is the reverse of removal. Observe the
recommended tightening torques.
If a new steering rack is being fitted, fit the track
rod ends in the position noted on removal.
To do this, slacken the bolt on the parallelism
adjustment sleeve and slacken the track rod end
while holding the axial ball joint using an open
wrench.
Make a mark or count the number of turns of
thread taken up so the parallelism can be pre-
adjusted on refitting.
Check the parallelism.
NOTE : the markings on the track rod ends MUST
BE OBSERVED
(one mark on right hand joint, two
marks on left hand joint).
36-3