Page 67 of 105
STEERING ASSEMBLY
Steering column
36
Under the vehicle, cut the retaining clip for the
rubber gaiter and push it back towards the
bulkhead.
Remove the eccentric bolt from the universal
joint.
Remove the two bolts and the two nuts mounting
the steering column.
12964R2
12965-1R2
Release:
- the steering column after disconnecting the
ignition switch,
- the gaiter from the bulkhead ( 1 ) and remove
it with the steering column.
REFITTING
Refit the steering column.
Fit the gaiter on the bulkhead, having tied the
flaps and the universal joint together with string.
Refitting is then the reverse of removal.
Check the instrument panel connectors are
correctly reconnected.
13116S
Remove the mounting bolts for the dashboard on
the steering column.
36-15
Page 68 of 105
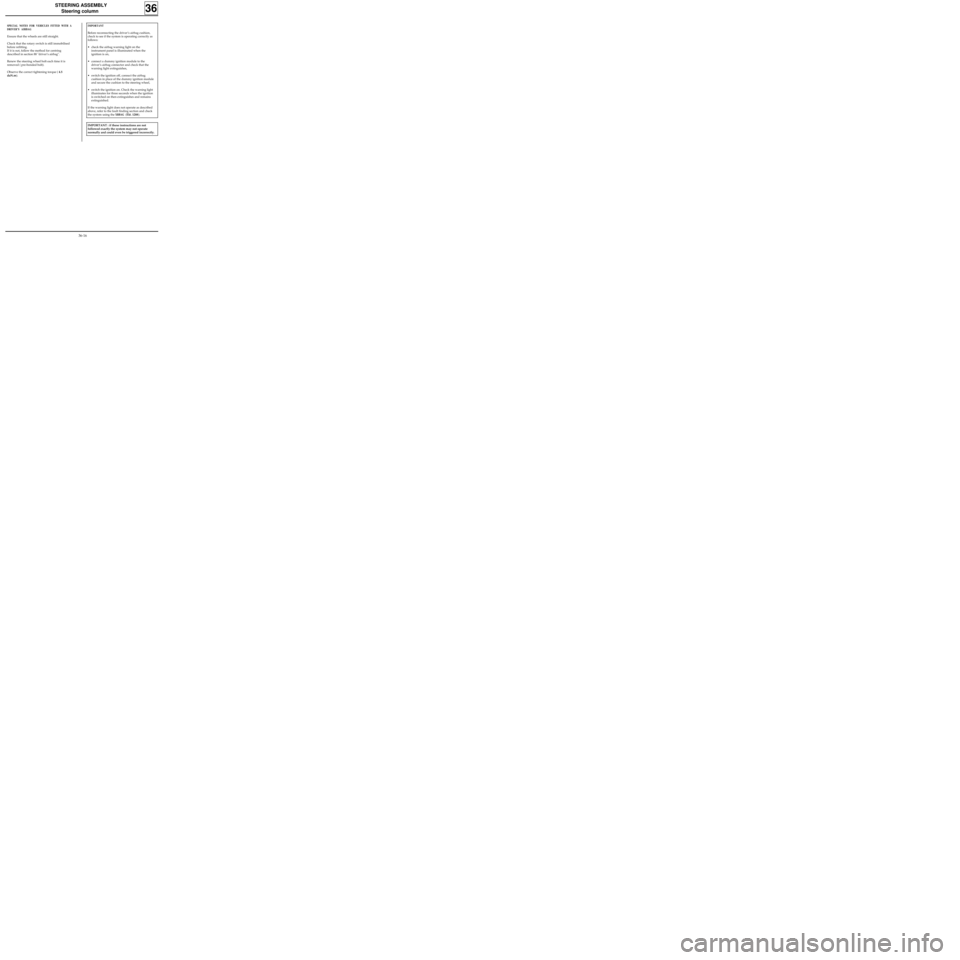
STEERING ASSEMBLY
Steering column
36
IMPORTANT : if these instructions are not
followed exactly the system may not operate
normally and could even be triggered incorrectly.
IMPORTANT
Before reconnecting the driver’s airbag cushion,
check to see if the system is operating correctly as
follows:
•check the airbag warning light on the
instrument panel is illuminated when the
ignition is on,
•connect a dummy ignition module to the
driver’s airbag connector and check that the
warning light extinguishes,
•switch the ignition off, connect the airbag
cushion in place of the dummy ignition module
and secure the cushion to the steering wheel,
•switch the ignition on. Check the warning light
illuminates for three seconds when the ignition
is switched on then extinguishes and remains
extinguished.
If the warning light does not operate as described
above, refer to the fault finding section and check
the system using the
XRBAG (Elé. 1288).
SPECIAL NOTES FOR VEHICLES FITTED WITH A
DRIVER’S AIRBAG
Ensure that the wheels are still straight.
Check that the rotary switch is still immobilised
before refitting.
If it is not, follow the method for centring
described in section 88 "driver’s airbag".
Renew the steering wheel bolt each time it is
removed ( pre-bonded bolt).
Observe the correct tightening torque ( 4.5
daN.m).
36-16
Page 100 of 105
WIRING DIAGRAM KEY
104Ignition switch
118 ABS computer
150Rear right wheel sensor
151Rear left wheel sensor
152Front right wheel sensor
153Front left wheel sensor
160Stop switch
225Diagnostic socket
247Instrument panel
260Fuse box
777Power feed fuse board
R2Dashboard / rear left
R36ABS / Dashboard
R101Right hand side member / Right hand
headlight
ELECTRONICALLY CONTROLLED HYDRAULIC SYSTEMS
BOSCH ABS
38
38-5
Page 101 of 105
ELECTRONICALLY CONTROLLED HYDRAULIC SYSTEMS
BOSCH ABS
38
PRN3813
31 TRACK CONNECTOR
Track Description
1
2
3
4
5
6
7
8
9
10
11
12
13
14Sensor earth - RRH
Sensor information -
RRH
Sensor earth - FRH
Not connected
Sensor information -
FRH
Sensor earth - FLH
Sensor information - FLH
Sensor earth - RLH
Sensor information - RLH
Not connected
Diagnostic line K
Diagnostic line L
Not connected
Stop lights switch information
AMicro-spring connecting earth (terminal 19) to pins 20 and 21 (ABS and NIVOCODE warning lights) if the
connector is disconnected.
Allocation of connector tracks
Track Description
15
16
17
18
19
20
21
22
25
26
27
31+ after ignition computer feed
Pump motor earth
+ BAT (solenoid valves and pump
motor)
+ BAT (solenoid valves and pump
motor)
Electronic earth
Not connected
ABS warning light
Not connected
Not connected
Not connected
Not connected
Not connected
38-6
Page 104 of 105
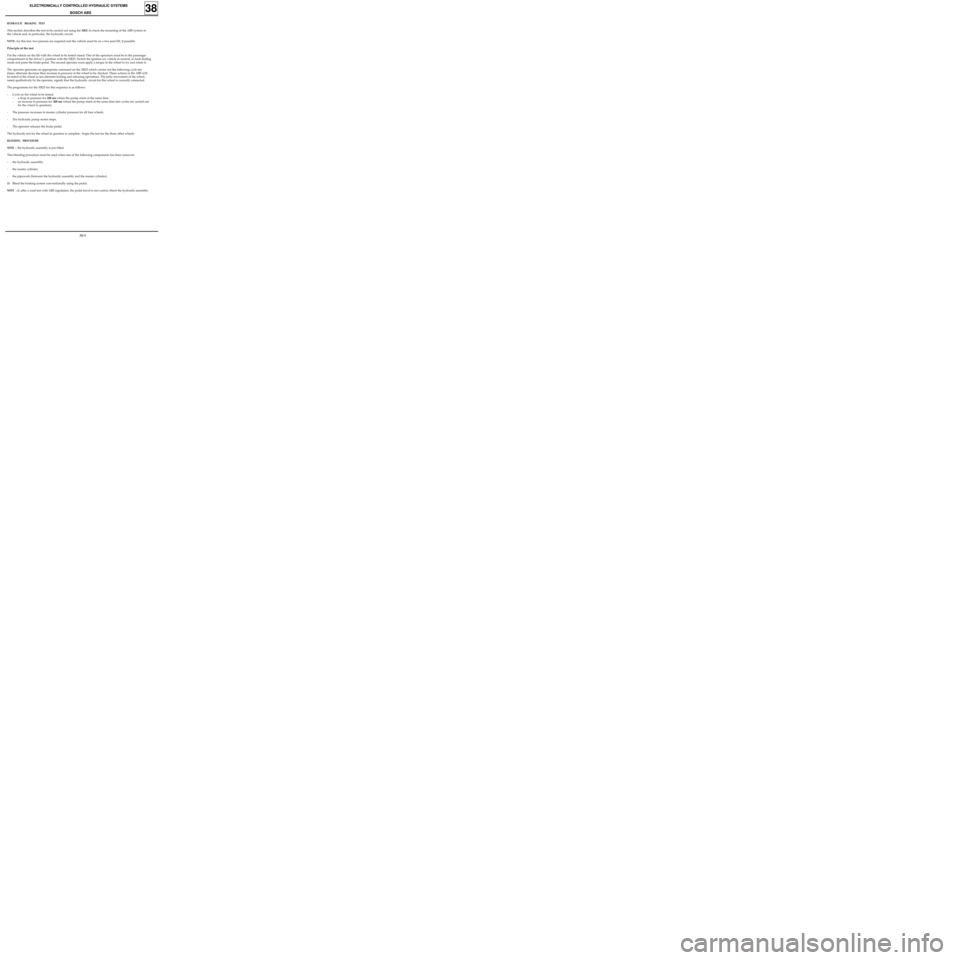
ELECTRONICALLY CONTROLLED HYDRAULIC SYSTEMS
BOSCH ABS
38
HYDRAULIC BRAKING TEST
This section describes the test to be carried out using the XR25, to check the mounting of the ABS system in
the vehicle and, in particular, the hydraulic circuit.
NOTE: for this test, two persons are required and the vehicle must be on a two post lift, if possible.
Principle of the test
Put the vehicle on the lift with the wheel to be tested raised. One of the operators must be in the passenger
compartment in the driver’s position with the XR25. Switch the ignition on, vehicle in neutral, in fault finding
mode and press the brake pedal. The second operator must apply a torque to the wheel to try and rotate it.
The operator generates an appropriate command on the XR25 which carries out the following cycle ten
times: alternate decrease then increase in pressure at the wheel to be checked. These actions in the ABS will
be noted at the wheel as ten alternate locking and releasing operations. The jerky movement of the wheel,
noted qualitatively by the operator, signify that the hydraulic circuit for this wheel is correctly connected.
The programme for the XR25 for this sequence is as follows:
- Cycle on the wheel to be tested:
- a drop in pressure for 200 ms where the pump starts at the same time,
- an increase in pressure for 300 ms where the pump starts at the same time (ten cycles are carried out
for the wheel in question).
- The pressure increases to master cylinder pressure for all four wheels.
- The hydraulic pump motor stops.
- The operator releases the brake pedal.
The hydraulic test for the wheel in question is complete - begin the test for the three other wheels.
BLEEDING PROCEDURE
NOTE :
the hydraulic assembly is pre-filled.
This bleeding procedure must be used when one of the following components has been removed:
- the hydraulic assembly,
- the master cylinder,
- the pipework (between the hydraulic assembly and the master cylinder).
1)Bleed the braking system conventionally using the pedal.
NOTE : if, after a road test with ABS regulation, the pedal travel is not correct, bleed the hydraulic assembly.
38-9