Page 48 of 1600
4B-52 REAR AXLE
TROUBLESHOOTING
Refer to this Section to quickly diagnose and repair rear axle problems.
Each troubleshooting chart has three headings arranged from left to right.
(1) Checkpoint (2) Trouble Cause (3) Countermeasure
This Section is divided into five sub-sections:
1. Abnormal Rear Axle Noise
1) Noise when the engine is driving the vehicle
2) Noise when the vehicle is coasting
3) Intermittent noise
4) Noise when the vehicle is turning
5) Constant noise
2. Vibration
3. Oil Leakage
1) Differential carrier leakage
2) Axle case leakage
3) Axle case to inside hub leakage
4) Axle case to inside brake drum leakage
4. Power Not Being Transmitted to the Wheels (Propeller Shaft Operation is Normal)
Page 49 of 1600
REAR AXLE 4B-53
1. ABNORMAL REAR AXLE NOISE
1) Noise when the Engine is Driving the Vehicle
Checkpoint Trouble Cause Countermeasure
Replenish the gear oilInsufficient gear oil NG
Differential side bearingAdjust the differential side
bearing preload
Replace the drive pinion
bearings
Adjust the drive pinion bearing
preload
Replace the gear oil
Loose differential side
bearings
W orn drive pinion bearings
Loose drive pinion bearings
W rong or poor grade gear oil
Drive pinion to ring gear
backlash
Drive pinion end play
Adjust the backlashToo much or too little backlash
Continued on the next pageOK OK
NG NG NG NG NG
OK
OK
Rear axle gear oil
Replace the differential side
bearingsW orn differential side bearings NG
Page 383 of 1600
BRAKES 5-55
2. Vacuum Hose
1) W hen removing or replacing the vacuum hose make sure
that the arrow on the label of the hose is facing the engine.
2) Also confirm that the check valve is facing the engine.
Page 456 of 1600
10-2 CAB
SERVICING
Engine Hood Lock
Align the engine hood lock with the installation holes.
Engine Hood Striker
Apply a light coat of grease to the striker.
Door Checker Arm and Pin
Apply a light coat of grease to the checker arm and pin.
Page 499 of 1600
10-2 CAB
SERVICING
Engine Hood Lock
Align the engine hood lock with the installation holes.
Engine Hood Striker
Apply a light coat of grease to the striker.
Door Checker Arm and Pin
Apply a light coat of grease to the checker arm and pin.
Page 565 of 1600
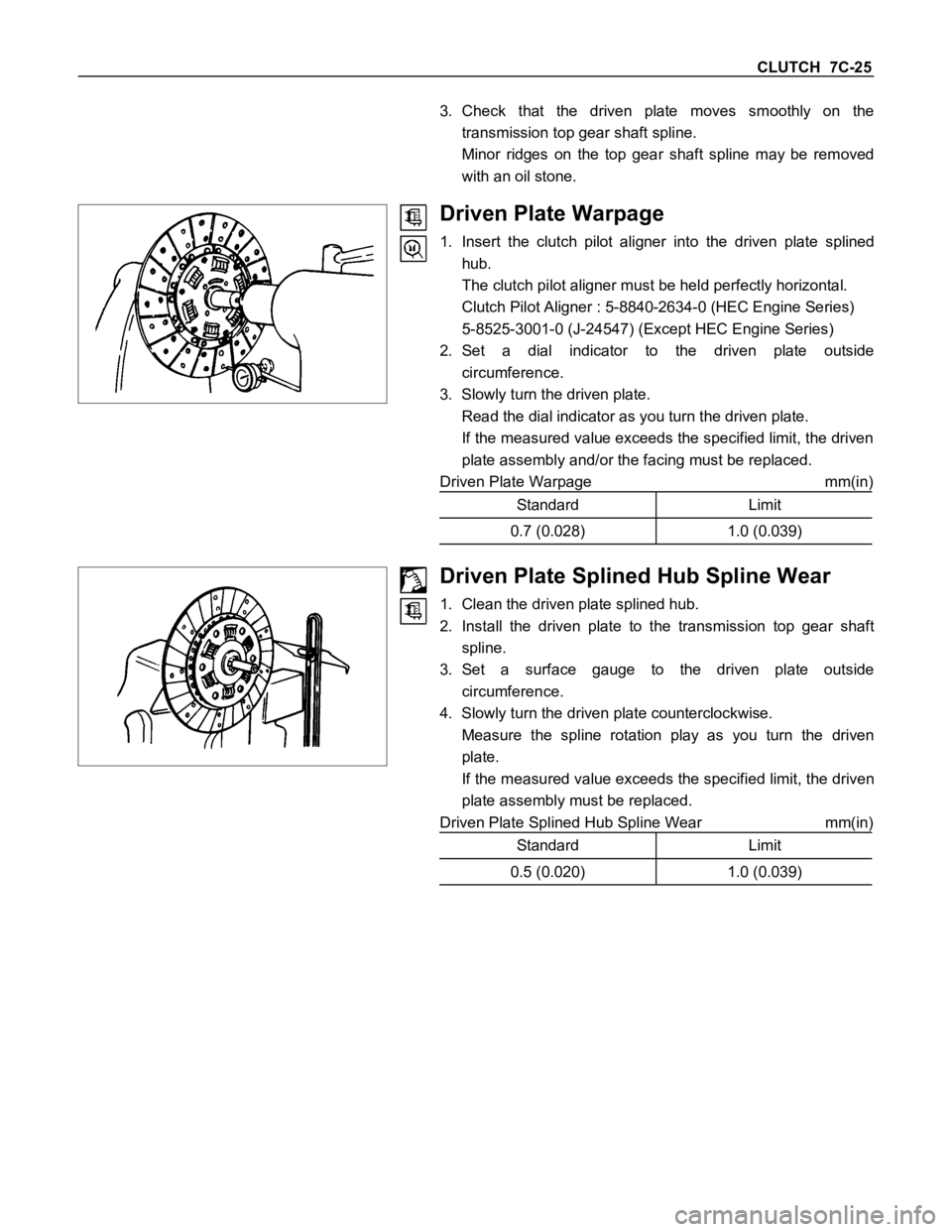
CLUTCH 7C-25
3. Check that the driven plate moves smoothly on the
transmission top gear shaft spline.
Minor ridges on the top gear shaft spline may be removed
with an oil stone.
Driven Plate Warpage
1. Insert the clutch pilot aligner into the driven plate splined
hub.
The clutch pilot aligner must be held perfectly horizontal.
Clutch Pilot Aligner : 5-8840-2634-0 (HEC Engine Series)
5-8525-3001-0 (J-24547) (Except HEC Engine Series)
2. Set a dial indicator to the driven plate outside
circumference.
3. Slowly turn the driven plate.
Read the dial indicator as you turn the driven plate.
If the measured value exceeds the specified limit, the driven
plate assembly and/or the facing must be replaced.
Driven Plate Warpage mm(in)
Standard Limit
0.7 (0.028) 1.0 (0.039)
Driven Plate Splined Hub Spline Wear
1. Clean the driven plate splined hub.
2. Install the driven plate to the transmission top gear shaft
spline.
3. Set a surface gauge to the driven plate outside
circumference.
4. Slowly turn the driven plate counterclockwise.
Measure the spline rotation play as you turn the driven
plate.
If the measured value exceeds the specified limit, the driven
plate assembly must be replaced.
Driven Plate Splined Hub Spline Wear mm(in)
Standard Limit
0.5 (0.020) 1.0 (0.039)
Page 578 of 1600
7C-38 CLUTCH
SLAVE CYLINDER (6VD1 Engine)
6VD1
Disassembly Steps
1. Boot
2. Push rod
3. Piston and piston cup
4. Spring
5. Cylinder body
Reassembly Steps
To reassemble, follow disassembly steps in
the reverse order.
DISASSEMBLY
1. Boot
2. Push Rod
3. Piston and Piston Cup
4. Spring
5. Cylinder Body
INSPECTION AND REPAIR
Make the necessary adjustments, repairs, and part
replacements if excessive wear or damage is discovered
during inspection.
6VD1Cylinder body
1) Clean the cylinder body.
2) Check the fluid return port for restrictions and clean it if
necessary.
Page 580 of 1600
7C-40 CLUTCH
HYDRAULEC DAMPER CYLINDER (Except 6VD1 Engine)
INSPECTION AND REPAIR
Make the necessary adjustments, repairs, and part replacements if excessive wear or damage is discovered during
inspection.
Visually check for oil leakage and other damage.
If oil leakage or other damage is discovered during the
inspection; the damper cylinder assembly must be replaced as
a unit.