Page 278 of 873
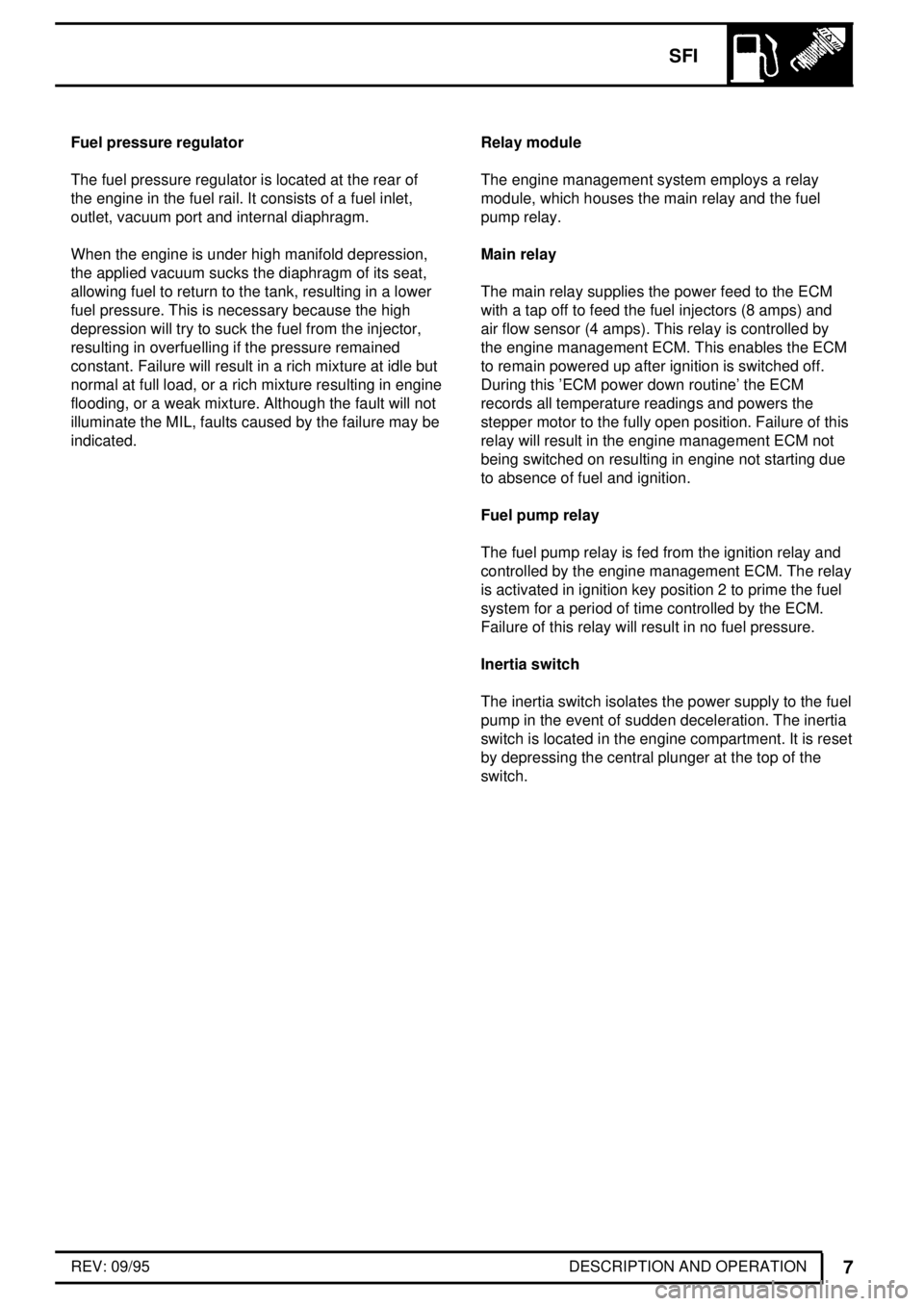
SFI
7
DESCRIPTION AND OPERATION REV: 09/95 Fuel pressure regulator
The fuel pressure regulator is located at the rear of
the engine in the fuel rail. It consists of a fuel inlet,
outlet, vacuum port and internal diaphragm.
When the engine is under high manifold depression,
the applied vacuum sucks the diaphragm of its seat,
allowing fuel to return to the tank, resulting in a lower
fuel pressure. This is necessary because the high
depression will try to suck the fuel from the injector,
resulting in overfuelling if the pressure remained
constant. Failure will result in a rich mixture at idle but
normal at full load, or a rich mixture resulting in engine
flooding, or a weak mixture. Although the fault will not
illuminate the MIL, faults caused by the failure may be
indicated.Relay module
The engine management system employs a relay
module, which houses the main relay and the fuel
pump relay.
Main relay
The main relay supplies the power feed to the ECM
with a tap off to feed the fuel injectors (8 amps) and
air flow sensor (4 amps). This relay is controlled by
the engine management ECM. This enables the ECM
to remain powered up after ignition is switched off.
During this 'ECM power down routine' the ECM
records all temperature readings and powers the
stepper motor to the fully open position. Failure of this
relay will result in the engine management ECM not
being switched on resulting in engine not starting due
to absence of fuel and ignition.
Fuel pump relay
The fuel pump relay is fed from the ignition relay and
controlled by the engine management ECM. The relay
is activated in ignition key position 2 to prime the fuel
system for a period of time controlled by the ECM.
Failure of this relay will result in no fuel pressure.
Inertia switch
The inertia switch isolates the power supply to the fuel
pump in the event of sudden deceleration. The inertia
switch is located in the engine compartment. It is reset
by depressing the central plunger at the top of the
switch.
Page 310 of 873
SFI
27
REPAIR ADD: 09/95
11.Disconnect vent line quickfit connector from
liquid/vapour separator.
12.Remove torque screw cap from hose to tank
filler neck clip.
13.Loosen clip screw securing hose to tank filler
neck.
14.Release hose from filler neck and internal filler
neck breather hose from fuel tank.
15.Remove and discard fuel filler neck clip.
16.Disconnect the pressure sensor breather pipe
connection.
17.Disconnect the vent line hose connection.
18.Fit ignition key to fuel filler flap lock and open
flap.
19.Release fuel filler cap from filler neck.
20.Remove filler neck assembly from vehicle.
Do not carry out further dismantling if
component is removed for access only.
21.Remove torque screw cap from hose to filler
neck clip.
22.Loosen clip screw securing hose to filler neck.
23.Remove hose from filler neck.
24.Remove and discard fuel filler hose clip.
25.Remove vent line from filler neck.
Page 311 of 873
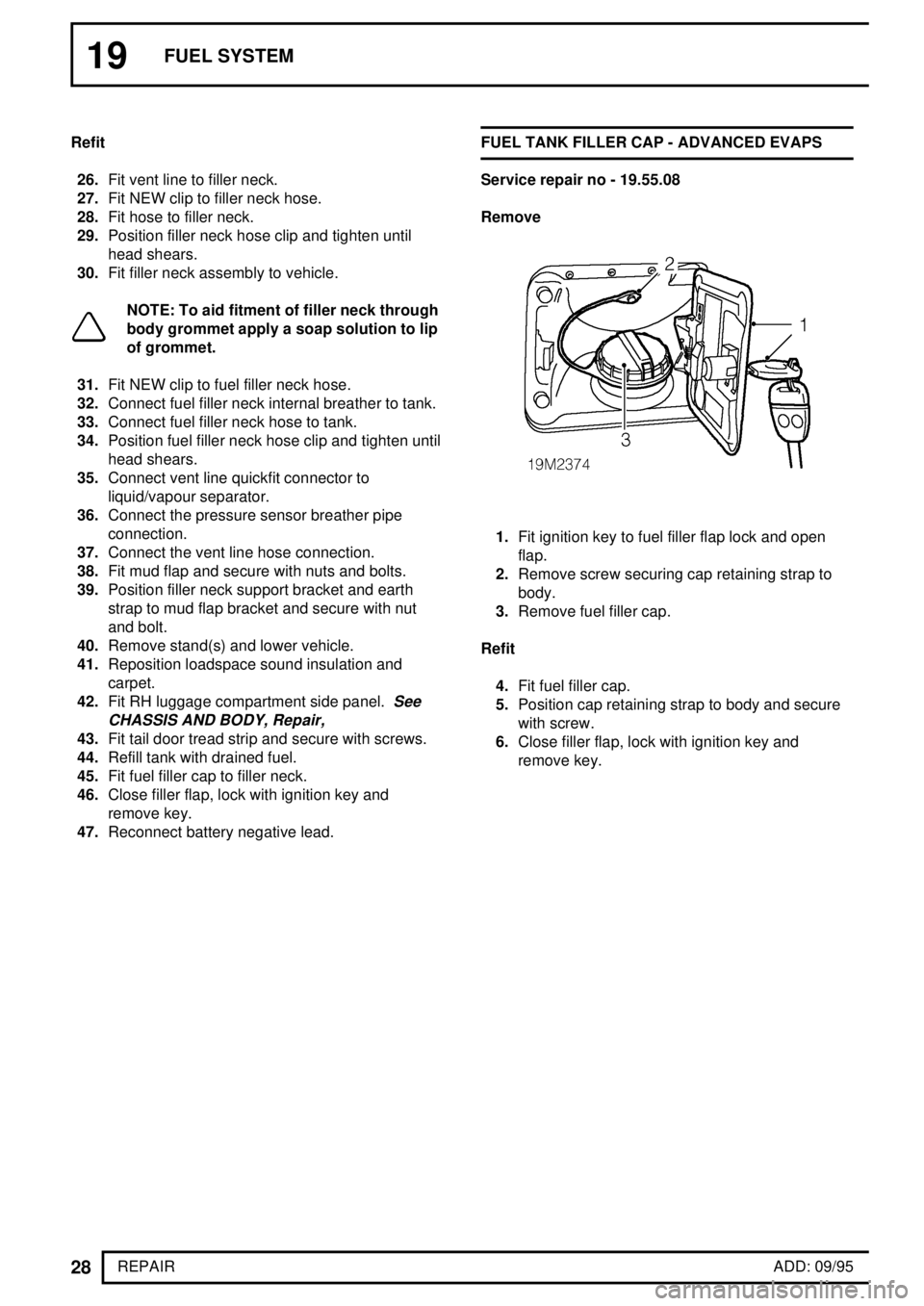
19FUEL SYSTEM
28
REPAIRADD: 09/95 Refit
26.Fit vent line to filler neck.
27.Fit NEW clip to filler neck hose.
28.Fit hose to filler neck.
29.Position filler neck hose clip and tighten until
head shears.
30.Fit filler neck assembly to vehicle.
NOTE: To aid fitment of filler neck through
body grommet apply a soap solution to lip
of grommet.
31.Fit NEW clip to fuel filler neck hose.
32.Connect fuel filler neck internal breather to tank.
33.Connect fuel filler neck hose to tank.
34.Position fuel filler neck hose clip and tighten until
head shears.
35.Connect vent line quickfit connector to
liquid/vapour separator.
36.Connect the pressure sensor breather pipe
connection.
37.Connect the vent line hose connection.
38.Fit mud flap and secure with nuts and bolts.
39.Position filler neck support bracket and earth
strap to mud flap bracket and secure with nut
and bolt.
40.Remove stand(s) and lower vehicle.
41.Reposition loadspace sound insulation and
carpet.
42.Fit RH luggage compartment side panel.
See
CHASSIS AND BODY, Repair,
43.Fit tail door tread strip and secure with screws.
44.Refill tank with drained fuel.
45.Fit fuel filler cap to filler neck.
46.Close filler flap, lock with ignition key and
remove key.
47.Reconnect battery negative lead.FUEL TANK FILLER CAP - ADVANCED EVAPS
Service repair no - 19.55.08
Remove
1.Fit ignition key to fuel filler flap lock and open
flap.
2.Remove screw securing cap retaining strap to
body.
3.Remove fuel filler cap.
Refit
4.Fit fuel filler cap.
5.Position cap retaining strap to body and secure
with screw.
6.Close filler flap, lock with ignition key and
remove key.
Page 418 of 873
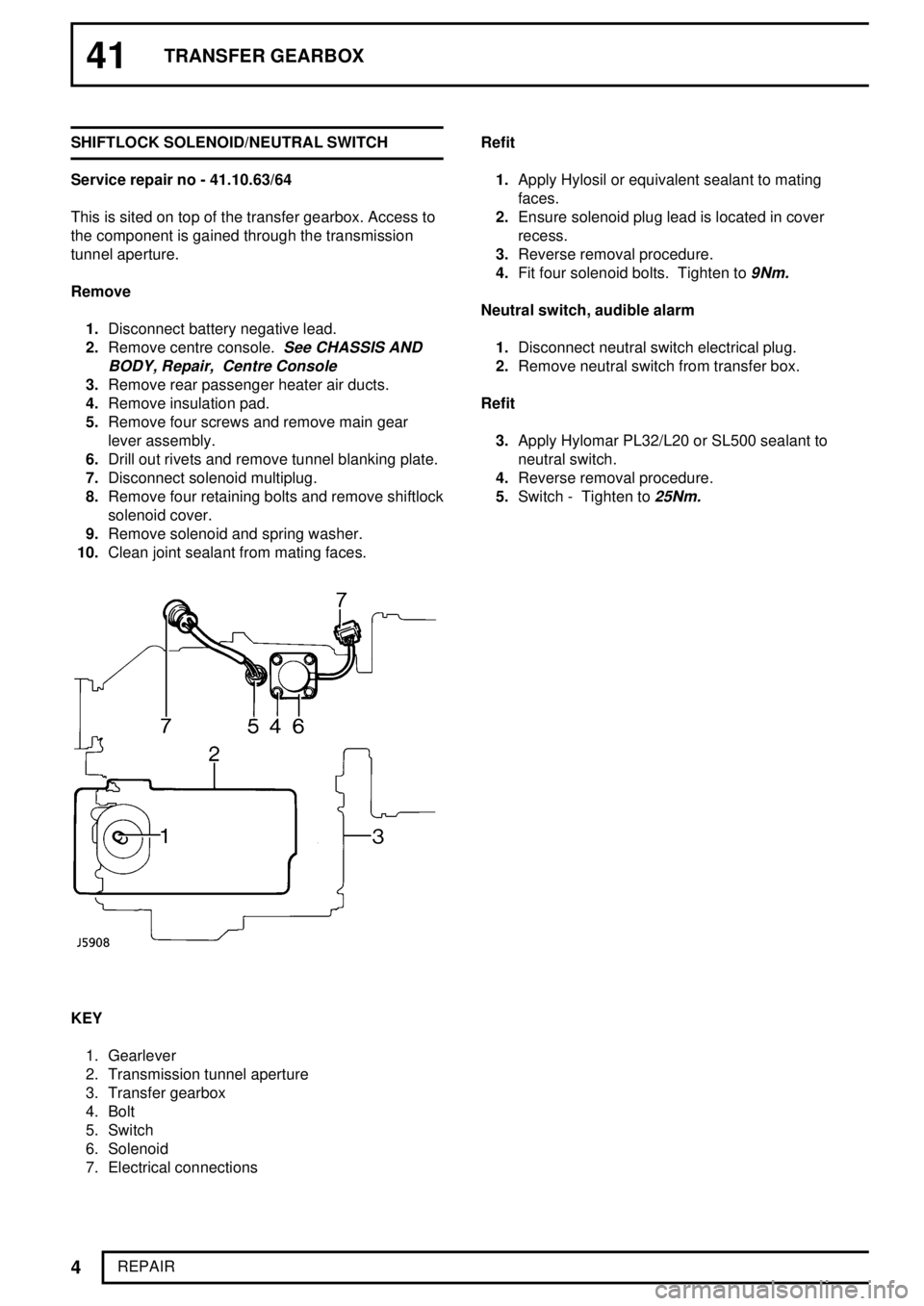
41TRANSFER GEARBOX
4
REPAIR SHIFTLOCK SOLENOID/NEUTRAL SWITCH
Service repair no - 41.10.63/64
This is sited on top of the transfer gearbox. Access to
the component is gained through the transmission
tunnel aperture.
Remove
1.Disconnect battery negative lead.
2.Remove centre console.
See CHASSIS AND
BODY, Repair, Centre Console
3.Remove rear passenger heater air ducts.
4.Remove insulation pad.
5.Remove four screws and remove main gear
lever assembly.
6.Drill out rivets and remove tunnel blanking plate.
7.Disconnect solenoid multiplug.
8.Remove four retaining bolts and remove shiftlock
solenoid cover.
9.Remove solenoid and spring washer.
10.Clean joint sealant from mating faces.
KEY
1. Gearlever
2. Transmission tunnel aperture
3. Transfer gearbox
4. Bolt
5. Switch
6. Solenoid
7. Electrical connectionsRefit
1.Apply Hylosil or equivalent sealant to mating
faces.
2.Ensure solenoid plug lead is located in cover
recess.
3.Reverse removal procedure.
4.Fit four solenoid bolts. Tighten to
9Nm.
Neutral switch, audible alarm
1.Disconnect neutral switch electrical plug.
2.Remove neutral switch from transfer box.
Refit
3.Apply Hylomar PL32/L20 or SL500 sealant to
neutral switch.
4.Reverse removal procedure.
5.Switch - Tighten to
25Nm.
Page 548 of 873
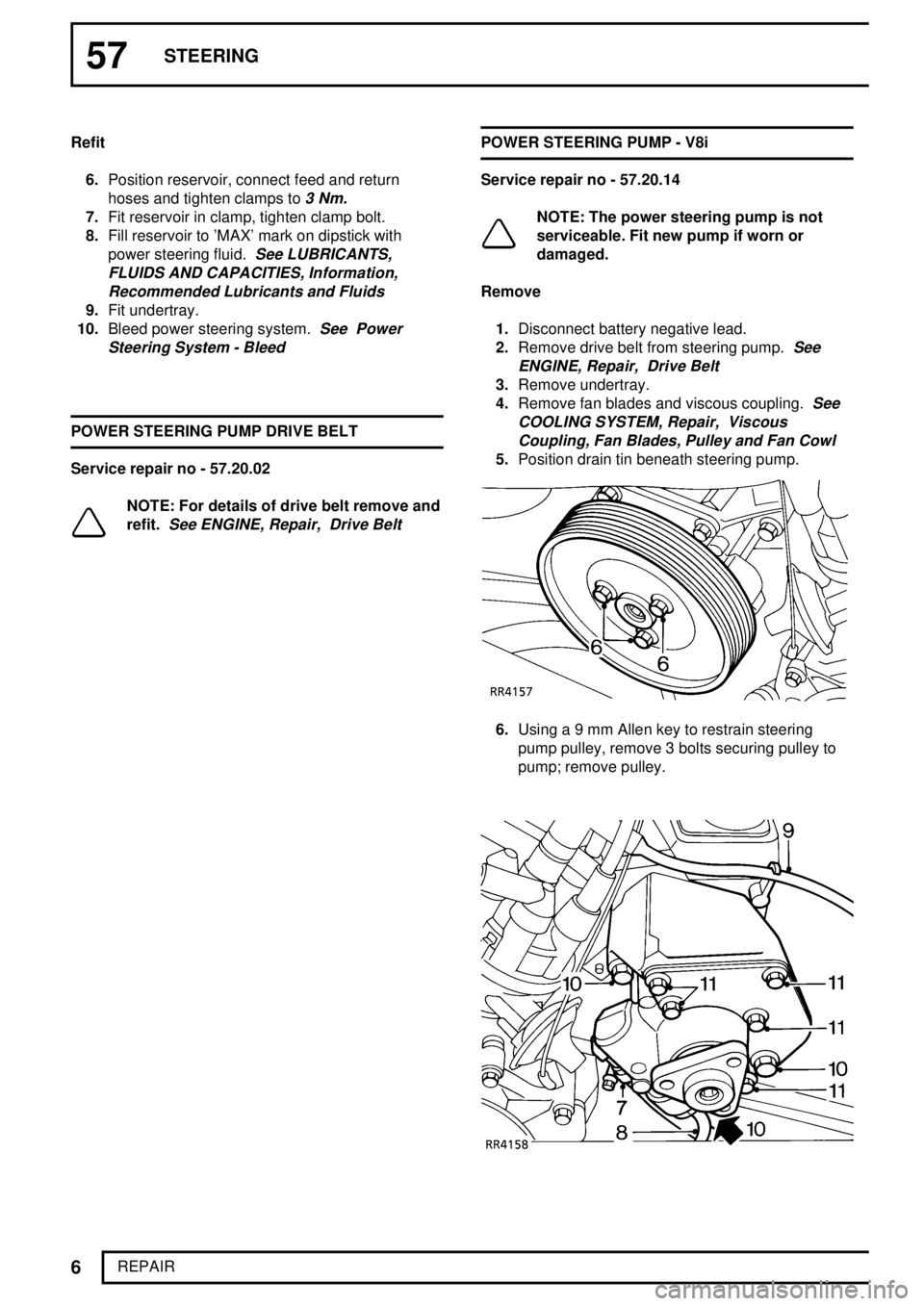
57STEERING
6
REPAIR Refit
6.Position reservoir, connect feed and return
hoses and tighten clamps to
3 Nm.
7.Fit reservoir in clamp, tighten clamp bolt.
8.Fill reservoir to 'MAX' mark on dipstick with
power steering fluid.
See LUBRICANTS,
FLUIDS AND CAPACITIES, Information,
Recommended Lubricants and Fluids
9.Fit undertray.
10.Bleed power steering system.
See Power
Steering System - Bleed
POWER STEERING PUMP DRIVE BELT
Service repair no - 57.20.02
NOTE: For details of drive belt remove and
refit.
See ENGINE, Repair, Drive Belt
POWER STEERING PUMP - V8i
Service repair no - 57.20.14
NOTE: The power steering pump is not
serviceable. Fit new pump if worn or
damaged.
Remove
1.Disconnect battery negative lead.
2.Remove drive belt from steering pump.
See
ENGINE, Repair, Drive Belt
3.Remove undertray.
4.Remove fan blades and viscous coupling.
See
COOLING SYSTEM, Repair, Viscous
Coupling, Fan Blades, Pulley and Fan Cowl
5.Position drain tin beneath steering pump.
6.Using a 9 mm Allen key to restrain steering
pump pulley, remove 3 bolts securing pulley to
pump; remove pulley.
Page 549 of 873
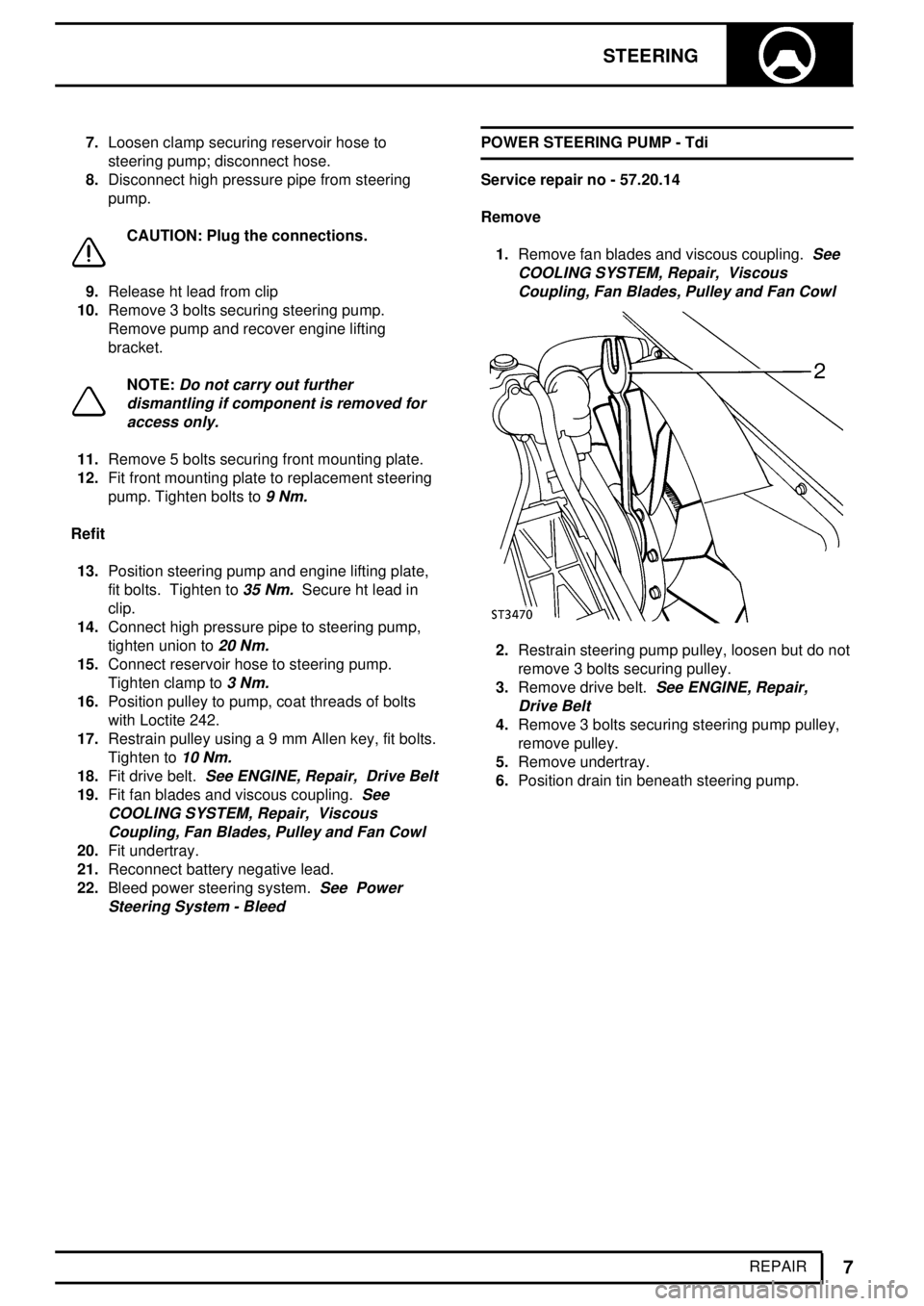
STEERING
7
REPAIR 7.Loosen clamp securing reservoir hose to
steering pump; disconnect hose.
8.Disconnect high pressure pipe from steering
pump.
CAUTION: Plug the connections.
9.Release ht lead from clip
10.Remove 3 bolts securing steering pump.
Remove pump and recover engine lifting
bracket.
NOTE:Do not carry out further
dismantling if component is removed for
access only.
11.Remove 5 bolts securing front mounting plate.
12.Fit front mounting plate to replacement steering
pump. Tighten bolts to
9 Nm.
Refit
13.Position steering pump and engine lifting plate,
fit bolts. Tighten to
35 Nm.Secure ht lead in
clip.
14.Connect high pressure pipe to steering pump,
tighten union to
20 Nm.
15.Connect reservoir hose to steering pump.
Tighten clamp to
3 Nm.
16.Position pulley to pump, coat threads of bolts
with Loctite 242.
17.Restrain pulley using a 9 mm Allen key, fit bolts.
Tighten to
10 Nm.
18.Fit drive belt.See ENGINE, Repair, Drive Belt
19.Fit fan blades and viscous coupling.See
COOLING SYSTEM, Repair, Viscous
Coupling, Fan Blades, Pulley and Fan Cowl
20.Fit undertray.
21.Reconnect battery negative lead.
22.Bleed power steering system.
See Power
Steering System - Bleed
POWER STEERING PUMP - Tdi
Service repair no - 57.20.14
Remove
1.Remove fan blades and viscous coupling.
See
COOLING SYSTEM, Repair, Viscous
Coupling, Fan Blades, Pulley and Fan Cowl
2.Restrain steering pump pulley, loosen but do not
remove 3 bolts securing pulley.
3.Remove drive belt.
See ENGINE, Repair,
Drive Belt
4.Remove 3 bolts securing steering pump pulley,
remove pulley.
5.Remove undertray.
6.Position drain tin beneath steering pump.
Page 582 of 873
FRONT SUSPENSION
5
REPAIR ANTI-ROLL[SWAY] BAR ASSEMBLY FRONT
Service repair no - 60.10.01
KEY
1. Anti-roll[sway] bar
2. Rubber bush
3. Strap
4. Nut, bolt, washer5. Nut and washer
6. Castellated nut and cotter pin
7. Ball joint link arm
Remove
1.Mark for reassembly position of rubber bushes
on anti- roll[sway] bar.
2.Remove four nuts, bolts and washers securing
two bush straps.
3.Remove nuts, bolts, washers and rubber bushes
from ball joint links and remove anti-roll[sway]
bar.Refit
4.Position bushes on anti-roll[sway] bar. Ensure
split points towards axle on RH bush and away
from axle on LH bush.
5.Fit anti-roll[sway] bar with two straps. To ensure
correct fit angled sides of bar should point down
as shown. Loosely fit the bolts, washers and
nyloc nuts.
6.Fit bolt, washers and rubber bushes. Using new
nuts fit anti-roll[sway] bar to ball joint links.
Tighten to
68Nm.
7.Tighten nuts securing straps to30Nm
Page 589 of 873
64REAR SUSPENSION
4
REPAIR ANTI-ROLL[SWAY] BAR ASSEMBLY REAR
Service repair no - 64.35.08.
KEY
1. Anti-roll[sway] bar
2. Rubber bush
3. Strap
4. Nut, bolt, washer5. Nut and washer
6. Ball joint link arm
7. Bolt and washer
8. Castellated nut and cotter pin
Remove
1.Note for reassembly, position of rubber bushes
on anti-roll bar.
2.Remove four nuts, bolts and washers securing
two bush straps.
3.Remove nuts, bolts, washers and rubber bushes
from the ball joint links and remove anti-roll bar.Refit
4.Position rubber bushes on anti-roll bar. Fit joint
towards axle.
5.Fit anti-roll bar with two straps. Ensure ball joint
link arms point down as shown. Loosely fit, bolts,
washers and new nyloc nuts.
6.Fit bolt, washers and rubber bushes. Fit anti-roll
bar to ball joint links. Tighten to
68Nm.
7.Tighten nuts securing straps to30Nm.