Page 257 of 391
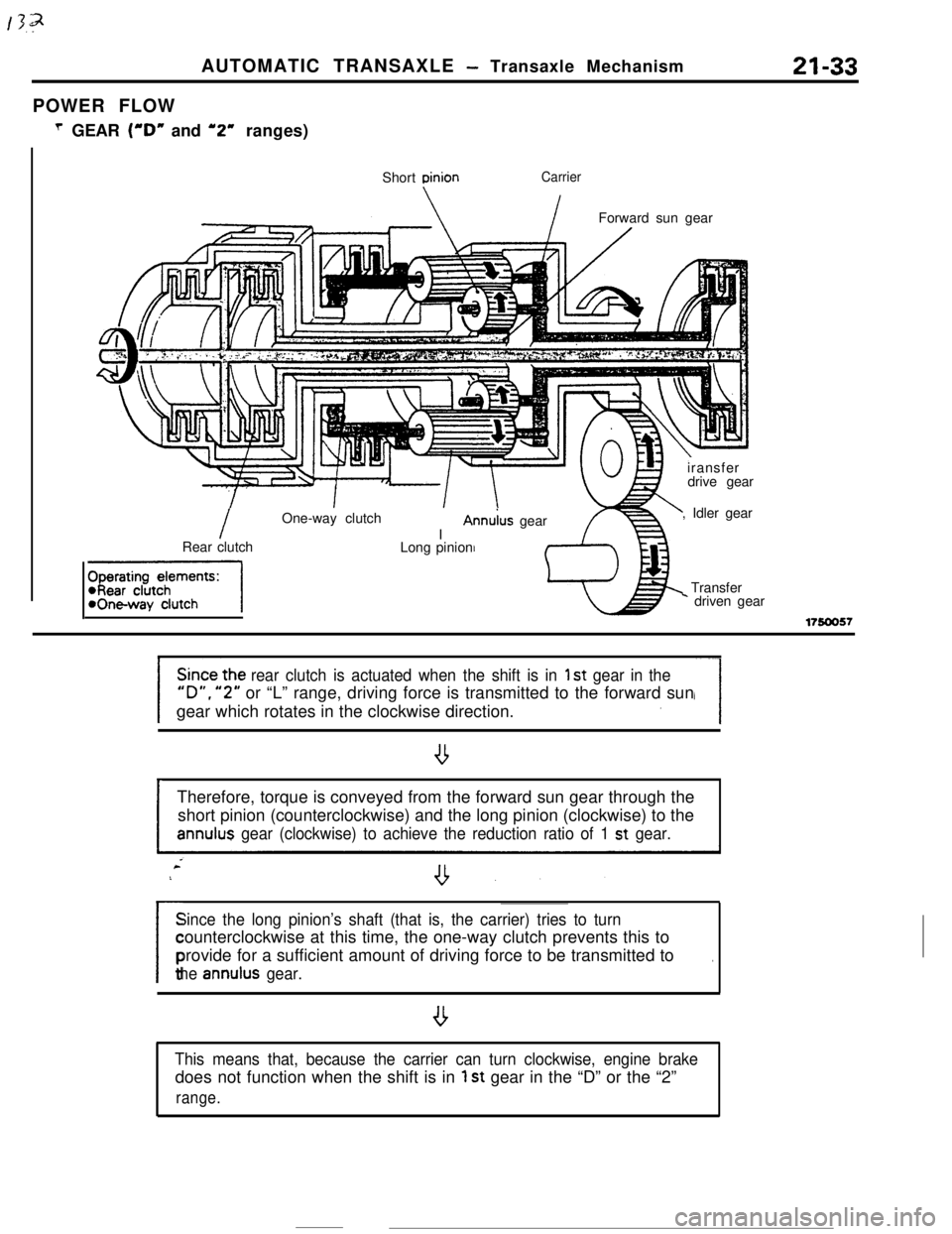
AUTOMATIC TRANSAXLE - Transaxle Mechanism21-33
POWER FLOW
T GEAR (“D” and ‘2” ranges)
Short
DinionCarrier
IForward sun gear
IOne-way clutch
IAnn&s gear
Rear clutch
-1Long pinioniransfer
drive gear
, Idler gear
Transfer* driven gear
17!50057
rear clutch is actuated when the shift is in 1 st gear in the
“D”. “2” or “L” range, driving force is transmitted to the forward sun
gear which rotates in the clockwise direction.
ITherefore, torque is conveyed from the forward sun gear through the
short pinion (counterclockwise) and the long pinion (clockwise) to theannulus gear (clockwise) to achieve the reduction ratio of 1 st gear.
Since the long pinion’s shaft (that is, the carrier) tries to turn
/counterclockwise at this time, the one-way clutch prevents this to
provide for a sufficient amount of driving force to be transmitted to
.
the annulus gear.
,
This means that, because the carrier can turn clockwise, engine brakedoes not function when the shift is in
1 st gear in the “D” or the “2”
range.
Page 258 of 391
_____--._- .21-34AUTOMATIC TRANSAXLE
- Transaxde Mechanism
1ST GEAR (“L” range)
Low/Reverse brake
Carrier
IShort pinion
I
Forward sungearAnnulus gear
ODeratina elements:&ear clkch. .--. _.-__.I*Low-Reverse brake
1
I>\\PRear clutchLong pinion
1750058When the shift is in
1st gear in the “L” range, the low reverse brake is
actuated to fasten the planetan/ gear carrier, so that the gear does not
turn in either direction.
.
This means that engine brake works when the shift is in 1 st gear inthe “L” range.
cNOTEThe power flow in
1 st gear in the “L” range is the same as it is in 1 st gear
in the “D” and “2” ranges.
Page 260 of 391
21-36AUTOMATIC TRANSAXLE - Transaxle Mechanism3RD GEAR
Forward
,sun gear
I, CarrierEndclutch
Front clutch
Reverse
Angear
17soo60
,When the shift is in
3rd gear in the “D” range, the rear clutch and the
front clutch are actuated. and other elements are all released.Therefore, driving force is transmitted from the forward sun gear and
the reverse sun gear.
Since the short and long pinions rotate in the same direction, they are
placed under a locked condition, causing the planetary gear set to
rotate as one unit.
lThis means that the engine rotation is directly connected, setting the
ratio between the input to and output from the planetary gear set to
1:1. The reduction ratio of 3rd gear is achieved in this way.Note that the end clutch is aotuated to provide for smooth shift
change to 4th gear.&
Page 264 of 391
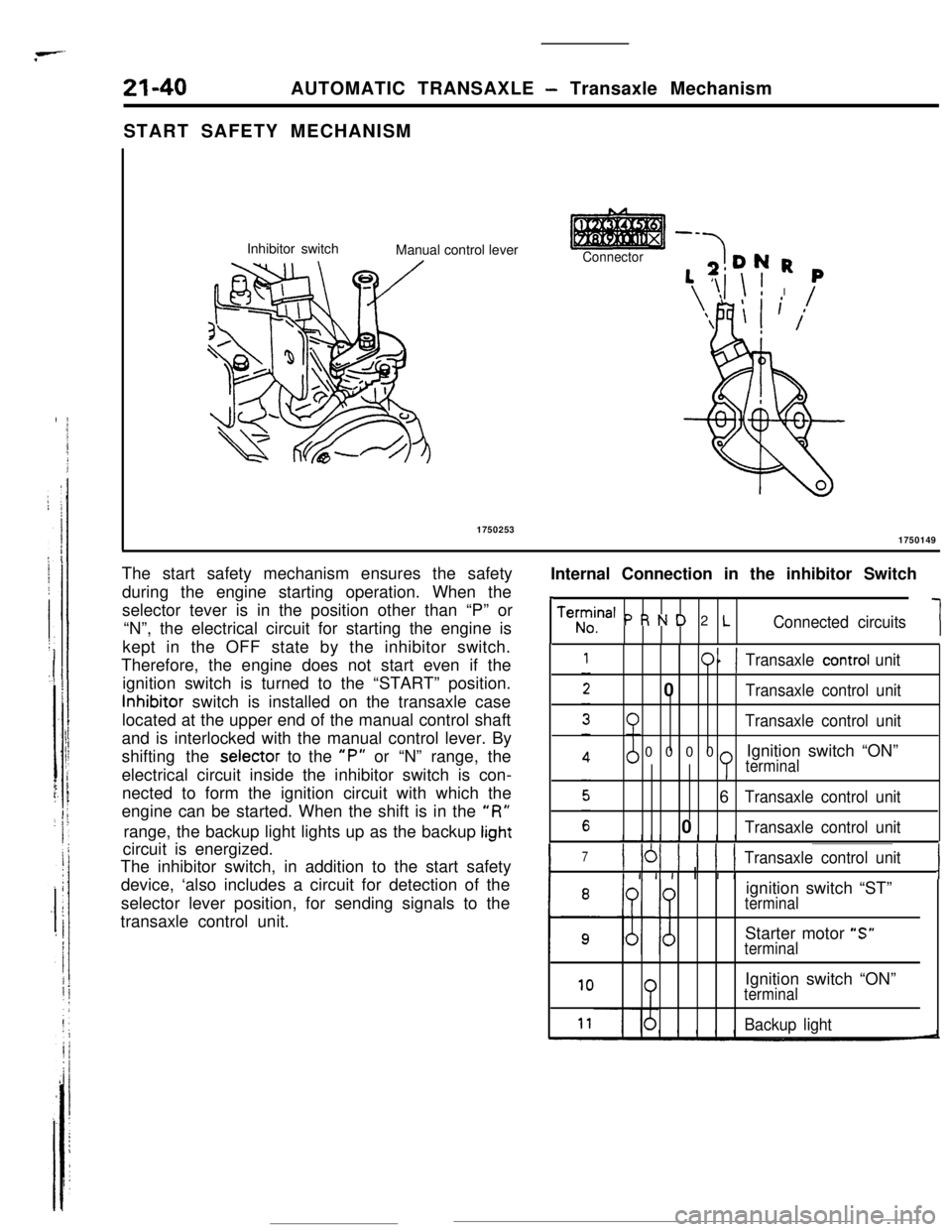
21-40AUTOMATIC TRANSAXLE - Transaxle Mechanism
START SAFETY MECHANISM
Inhibitor switch
Manual control lever
--
Connector-7DN R
‘,T,i \ ! I
‘\FlI
\ L
,p
( /1750253
1750149
Internal Connection in the inhibitor Switch
,
Teh;ina’ P R N D 2 LConnected circuits1 The start safety mechanism ensures the safety
during the engine starting operation. When the
selector tever is in the position other than “P” or
“N”, the electrical circuit for starting the engine is
kept in the OFF state by the inhibitor switch.
Therefore, the engine does not start even if the
ignition switch is turned to the “START” position.Inhibitor switch is installed on the transaxle case
located at the upper end of the manual control shaft
and is interlocked with the manual control lever. By
shifting the selector to the
“P” or “N” range, the
electrical circuit inside the inhibitor switch is con-
nected to form the ignition circuit with which the
engine can be started. When the shift is in the
“R”range, the backup light lights up as the backup
lightcircuit is energized.
The inhibitor switch, in addition to the start safety
device, ‘also includes a circuit for detection of the
selector lever position, for sending signals to the
transaxle control unit.
011Transaxle control unit0
Transaxle control unit
Transaxle control unit0000Ignition switch “ON”
terminal6
Transaxle control unit0
Transaxle control unit
I
7) 161 ) 1 ( 1Transaxle control unit
I I I I I I IIignition switch “ST”
terminalStarter motor “S”
terminal
10Ignition switch “ON”terminal
Backup light
Page 269 of 391
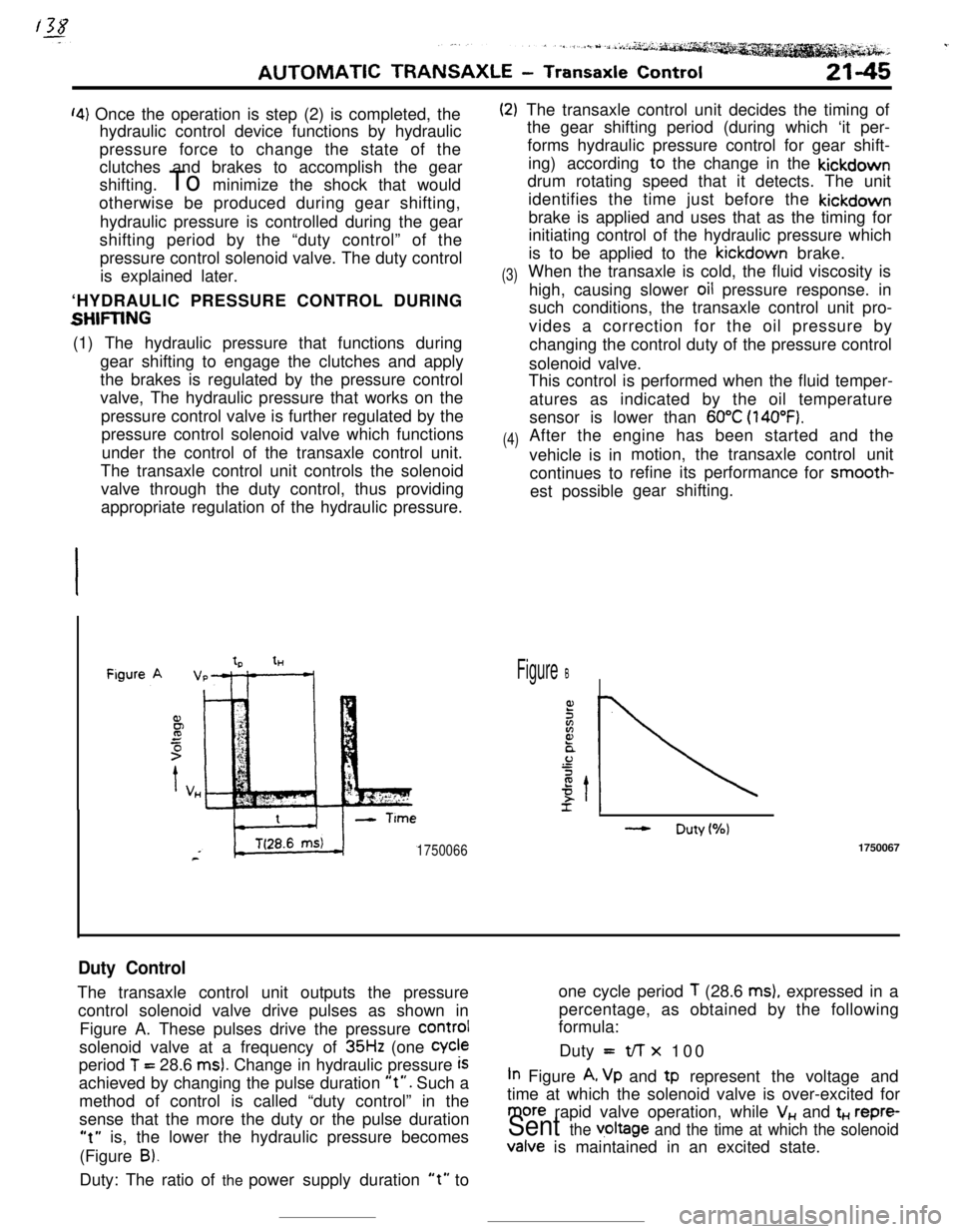
‘4) Once the operation is step (2) is completed, the
hydraulic control device functions by hydraulic
pressure force to change the state of the
clutches and brakes to accomplish the gear
shifting. To minimize the shock that would
otherwise be produced during gear shifting,
hydraulic pressure is controlled during the gear
shifting period by the “duty control” of the
pressure control solenoid valve. The duty control
is explained later.
‘HYDRAULIC PRESSURE CONTROL DURING
SHFIING(1) The hydraulic pressure that functions during
gear shifting to engage the clutches and apply
the brakes is regulated by the pressure control
valve, The hydraulic pressure that works on the
pressure control valve is further regulated by the
pressure control solenoid valve which functions
under the control of the transaxle control unit.
The transaxle control unit controls the solenoid
valve through the duty control, thus providing
appropriate regulation of the hydraulic pressure.
(2)
(3)
(4)The transaxle control unit decides the timing of
the gear shifting period (during which ‘it per-
forms hydraulic pressure control for gear shift-
ing) according to the change in the kickdown
drum rotating speed that it detects. The unit
identifies the time just before the kickdown
brake is applied and uses that as the timing for
initiating control of the hydraulic pressure which
is to be applied to the kickdown brake.
When the transaxle is cold, the fluid viscosity is
high, causing slower oil pressure response. in
such conditions, the transaxle control unit pro-
vides a correction for the oil pressure by
changing the control duty of the pressure control
solenoid valve.
This control is performed when the fluid temper-
atures as indicated by the oil temperature
sensor is lower than
60°C (140°F).After the engine has been started and the
vehicle is inmotion, the transaxle
continues torefine its performance
est possiblegear shifting.control unit
for smooth-
tHFigure B
- Duty(%)
17500661750067
Duty ControlThe transaxle control unit outputs the pressureone cycle period
T (28.6 ms), expressed in a
control solenoid valve drive pulses as shown inpercentage, as obtained by the following
formula:
Figure A. These pulses drive the pressure
COrmIsolenoid valve at a frequency of
35Hz (one Cycleperiod
T = 28.6 ms). Change in hydraulic pressure iSDuty =t/-r x 100
achieved by changing the pulse duration
“t”. Such aIn Figure A, Vp and tp represent the voltage and
method of control is called “duty control” in thetime at which the solenoid valve is over-excited for
sense that the more the duty or the pulse duration
more rapid valve operation, while V,, and t+., repre-
“t” is, the lower the hydraulic pressure becomesSent the v,oltage and the time at which the solenoid(Figure
B).Valve is maintained in an excited state.
Duty: The ratio of the power supply duration
“t” to
Page 274 of 391
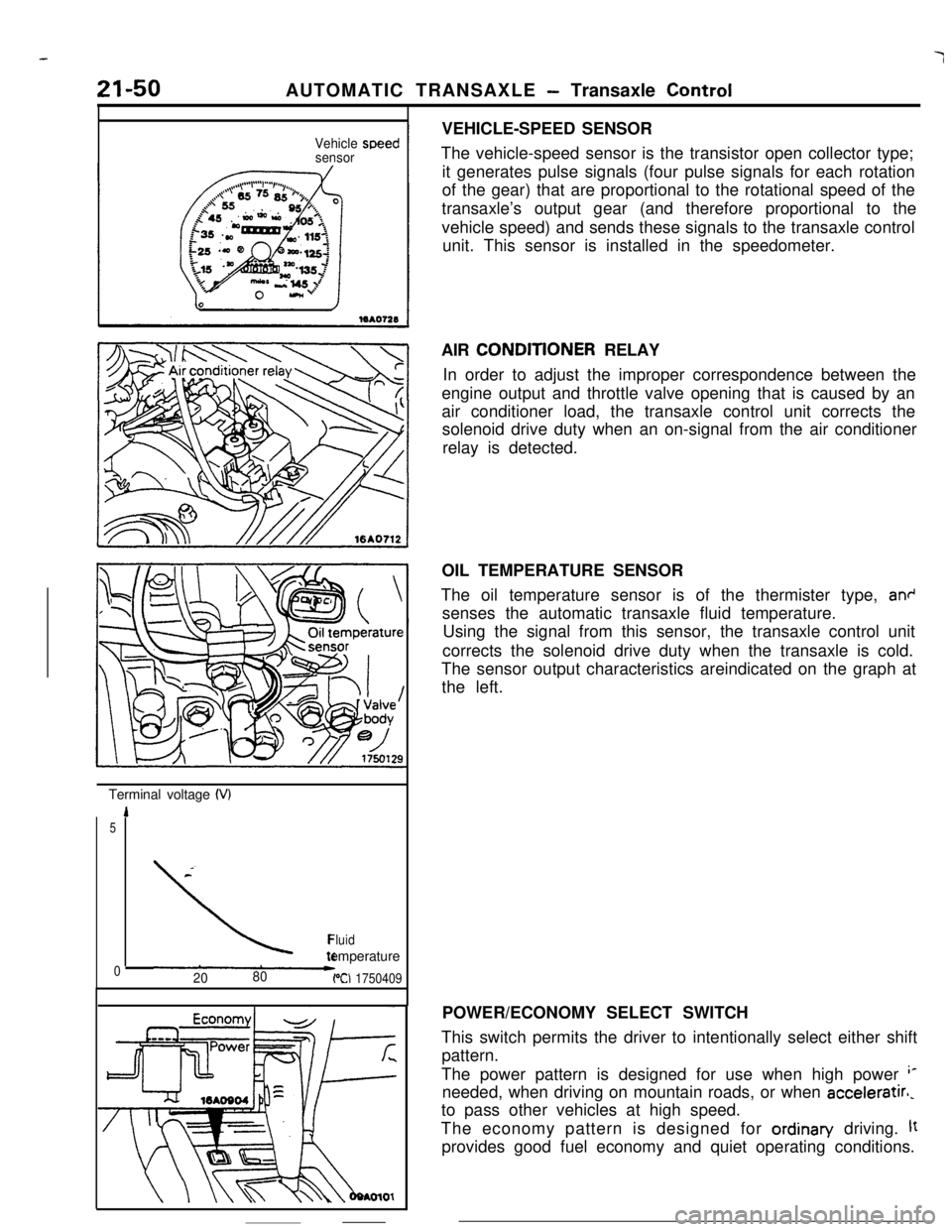
21-50AUTOMATIC TRANSAXLE - Transaxle Control
Vehicle
sensorspeedTerminal voltage
(VI
1
5
\*Fluidtemperature
02080PCI 1750409VEHICLE-SPEED SENSOR
The vehicle-speed sensor is the transistor open collector type;
it generates pulse signals (four pulse signals for each rotation
of the gear) that are proportional to the rotational speed of the
transaxle’s output gear (and therefore proportional to the
vehicle speed) and sends these signals to the transaxle control
unit. This sensor is installed in the speedometer.
AIR CONDlTlONER RELAY
In order to adjust the improper correspondence between the
engine output and throttle valve opening that is caused by an
air conditioner load, the transaxle control unit corrects the
solenoid drive duty when an on-signal from the air conditioner
relay is detected.
OIL TEMPERATURE SENSOR
The oil temperature sensor is of the thermister type,
an+senses the automatic transaxle fluid temperature.
Using the signal from this sensor, the transaxle control unit
corrects the solenoid drive duty when the transaxle is cold.
The sensor output characteristics areindicated on the graph at
the left.
POWER/ECONOMY SELECT SWITCH
This switch permits the driver to intentionally select either shift
pattern.
The power pattern is designed for use when high power
‘*needed, when driving on mountain roads, or when acceleratirl,
to pass other vehicles at high speed.
The economy pattern is designed for ordinan/ driving.
ltprovides good fuel economy and quiet operating conditions.
Page 275 of 391
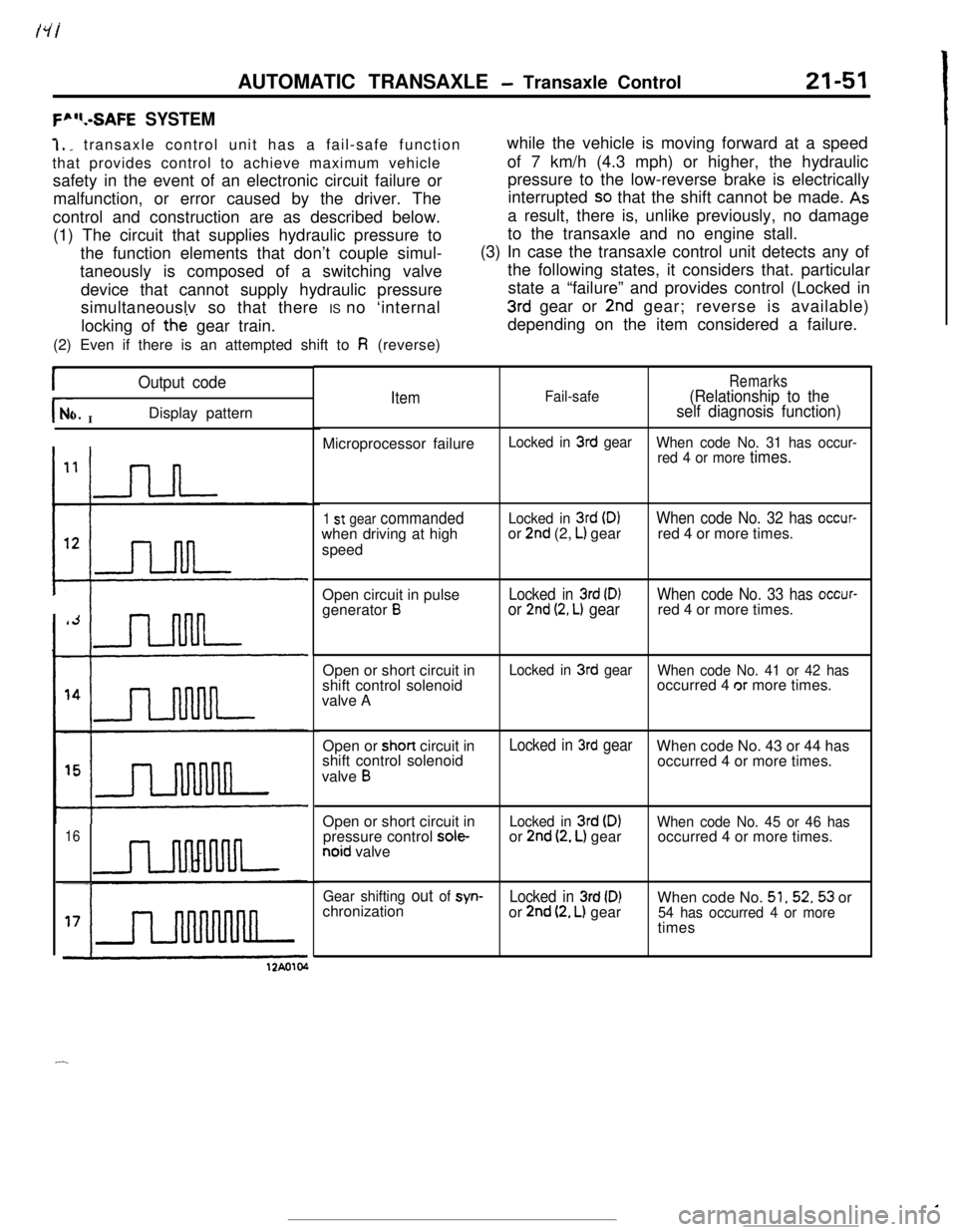
AUTOMATIC TRANSAXLE - Transaxle Control21-51
F”“.-SAFE SYSTEM7,
_ transaxle control unit has a fail-safe function
that provides control to achieve maximum vehicle
safety in the event of an electronic circuit failure or
malfunction, or error caused by the driver. The
control and construction are as described below.
(1) The circuit that supplies hydraulic pressure to
the function elements that don’t couple simul-
taneously is composed of a switching valve
device that cannot supply hydraulic pressure
simultaneouslv so that there IS no ‘internal
locking of the gear train.
(2) Even if there is an attempted shift to
Fi (reverse)while the vehicle is moving forward at a speed
of 7 km/h (4.3 mph) or higher, the hydraulic
pressure to the low-reverse brake is electrically
interrupted
SO that the shift cannot be made. Asa result, there is, unlike previously, no damage
to the transaxle and no engine stall.
(3) In case the transaxle control unit detects any of
the following states, it considers that. particular
state a “failure” and provides control (Locked in
3rd gear or 2nd gear; reverse is available)
depending on the item considered a failure.
IOutput code
r- INo.Display pattern
16
ItemFail-safeRemarks(Relationship to the
self diagnosis function)Microprocessor failure
Locked in 3rd gear
When code No. 31 has occur-
red 4 or more
times.
1 st gear commandedwhen driving at high
speedLocked in 3rd (D)or 2nd (2, L) gearWhen code No. 32 has occur-red 4 or more times.
Open circuit in pulse
generator
BLocked in 3rd (D)or 2nd (2, L) gearWhen code No. 33 has occur-red 4 or more times.
Open or short circuit in
shift control solenoid
valve A
Locked in 3rd gear
When code No. 41 or 42 hasoccurred 4 or more times.
Open or short circuit in
shift control solenoid
valve
B
Locked in 3rd gearWhen code No. 43 or 44 has
occurred 4 or more times.
Open or short circuit in
pressure control
sole-noid valve
Locked in 3rd (DIor 2nd (2, L) gearWhen code No. 45 or 46 hasoccurred 4 or more times.
Gear shifting out of syn-Locked in 3rd (D)When code No. 51,52,53 or
chronization
or 2nd (2, L) gear54 has occurred 4 or moretimes
12Ao104
-
Page 279 of 391
AUTOMATIC TRANSAXLE - Transaxle Control21-55HYDRAULIC CONTROL SYSTEM
Reaction shaft
support
BushingThe hydraulic control system consists of an oil pump which
generates hydraulic pressure for the system, and valves and
solenoid valves to control the pressure or switch the oil
passages. The valves and solenoid valves are all built in the
valve body.
OIL PUMPOil pump generates the pressure for supplying oil to the torque
converter, for lubricating frictional parts of the planetary gear
set and the overrunning clutch, etc., and for activating the
hydraulic control system.
The pump is of the inner-teeth engaging involute gear type. It
always generates the oil pressure when the engine is running
since the drive gear
is driven by 2 pawls of the pump drive hub
welded at the center of the torque converter shell.