Page 223 of 432
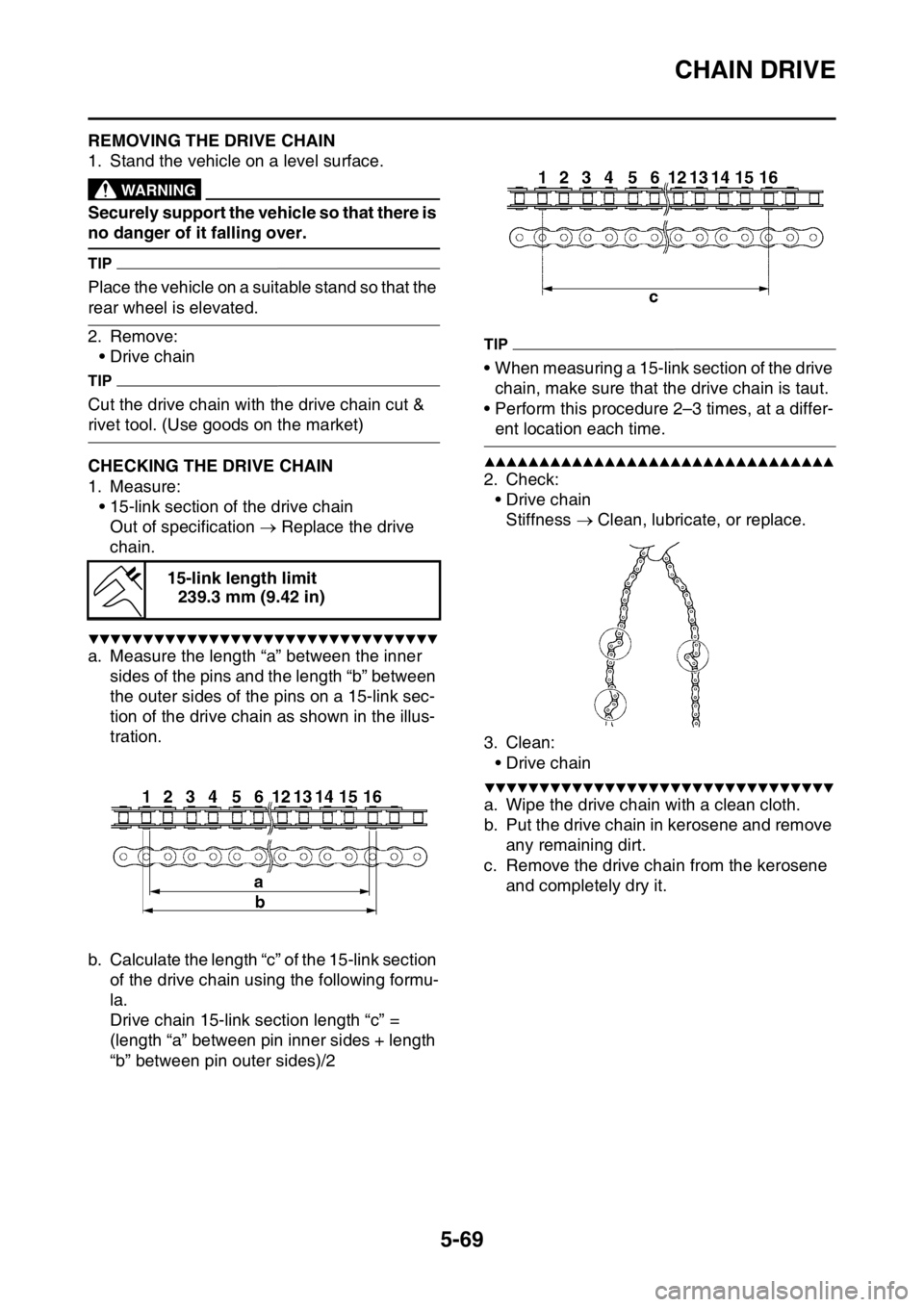
CHAIN DRIVE
5-69
EAS23420REMOVING THE DRIVE CHAIN
1. Stand the vehicle on a level surface.
EWA
WARNING
Securely support the vehicle so that there is
no danger of it falling over.
TIP
Place the vehicle on a suitable stand so that the
rear wheel is elevated.
2. Remove:
•Drive chain
TIP
Cut the drive chain with the drive chain cut &
rivet tool. (Use goods on the market)
EAS23441CHECKING THE DRIVE CHAIN
1. Measure:
• 15-link section of the drive chain
Out of specification Replace the drive
chain.
▼▼▼▼▼▼▼▼▼▼▼▼▼▼▼▼▼▼▼▼▼▼▼▼▼▼▼▼▼▼▼▼
a. Measure the length “a” between the inner
sides of the pins and the length “b” between
the outer sides of the pins on a 15-link sec-
tion of the drive chain as shown in the illus-
tration.
b. Calculate the length “c” of the 15-link section
of the drive chain using the following formu-
la.
Drive chain 15-link section length “c” =
(length “a” between pin inner sides + length
“b” between pin outer sides)/2
TIP
• When measuring a 15-link section of the drive
chain, make sure that the drive chain is taut.
• Perform this procedure 2–3 times, at a differ-
ent location each time.
▲▲▲▲▲▲▲▲▲▲▲▲▲▲▲▲▲▲▲▲▲▲▲▲▲▲▲▲▲▲▲▲
2. Check:
•Drive chain
Stiffness Clean, lubricate, or replace.
3. Clean:
•Drive chain
▼▼▼▼▼▼▼▼▼▼▼▼▼▼▼▼▼▼▼▼▼▼▼▼▼▼▼▼▼▼▼▼
a. Wipe the drive chain with a clean cloth.
b. Put the drive chain in kerosene and remove
any remaining dirt.
c. Remove the drive chain from the kerosene
and completely dry it. 15-link length limit
239.3 mm (9.42 in)
Page 236 of 432
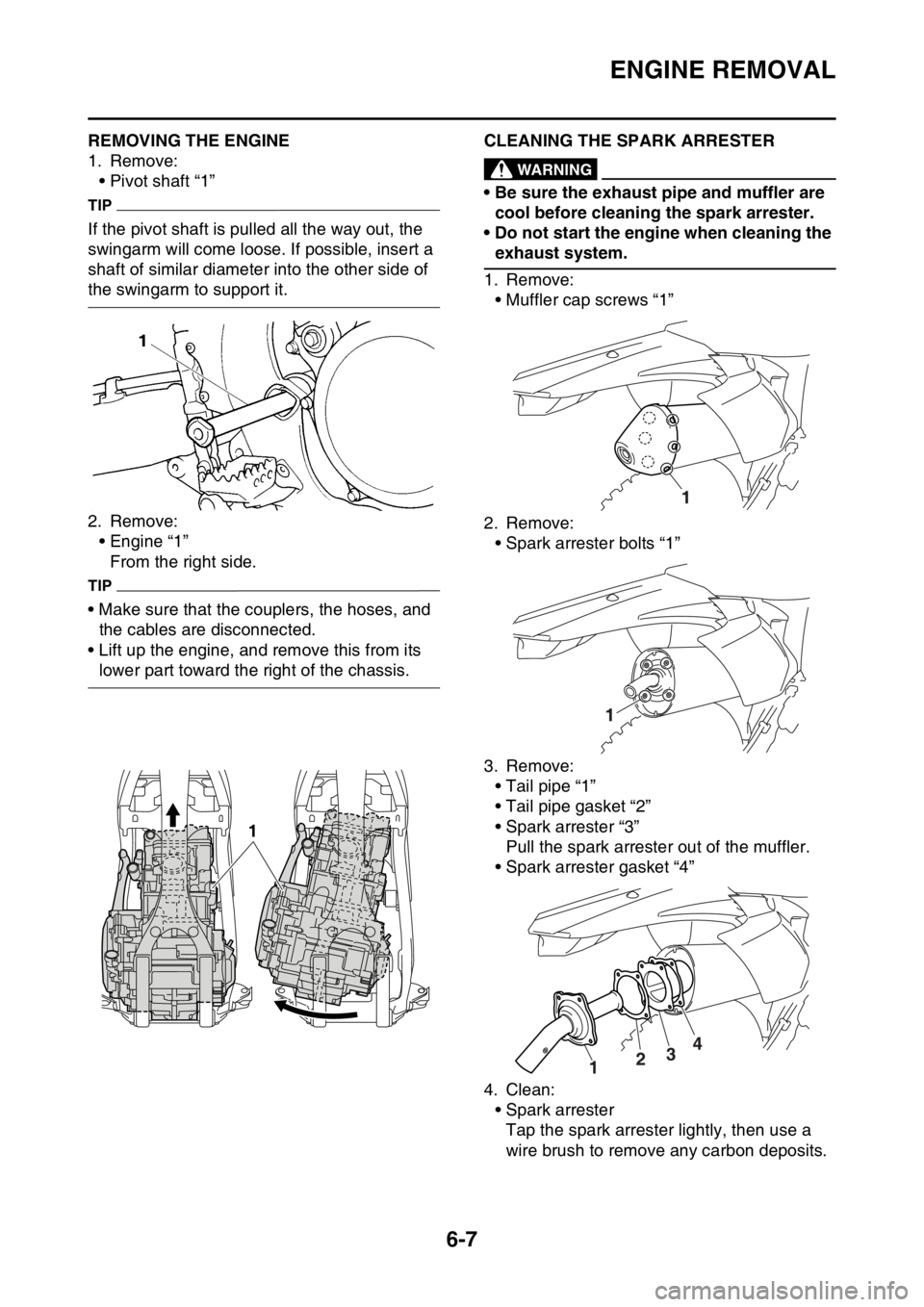
ENGINE REMOVAL
6-7
EAS2GBB230REMOVING THE ENGINE
1. Remove:
• Pivot shaft “1”
TIP
If the pivot shaft is pulled all the way out, the
swingarm will come loose. If possible, insert a
shaft of similar diameter into the other side of
the swingarm to support it.
2. Remove:
• Engine “1”
From the right side.
TIP
• Make sure that the couplers, the hoses, and
the cables are disconnected.
• Lift up the engine, and remove this from its
lower part toward the right of the chassis.
EAS2GBB231CLEANING THE SPARK ARRESTEREWA
WARNING
• Be sure the exhaust pipe and muffler are
cool before cleaning the spark arrester.
• Do not start the engine when cleaning the
exhaust system.
1. Remove:
• Muffler cap screws “1”
2. Remove:
• Spark arrester bolts “1”
3. Remove:
• Tail pipe “1”
• Tail pipe gasket “2”
• Spark arrester “3”
Pull the spark arrester out of the muffler.
• Spark arrester gasket “4”
4. Clean:
• Spark arrester
Tap the spark arrester lightly, then use a
wire brush to remove any carbon deposits.
1
Page 311 of 432
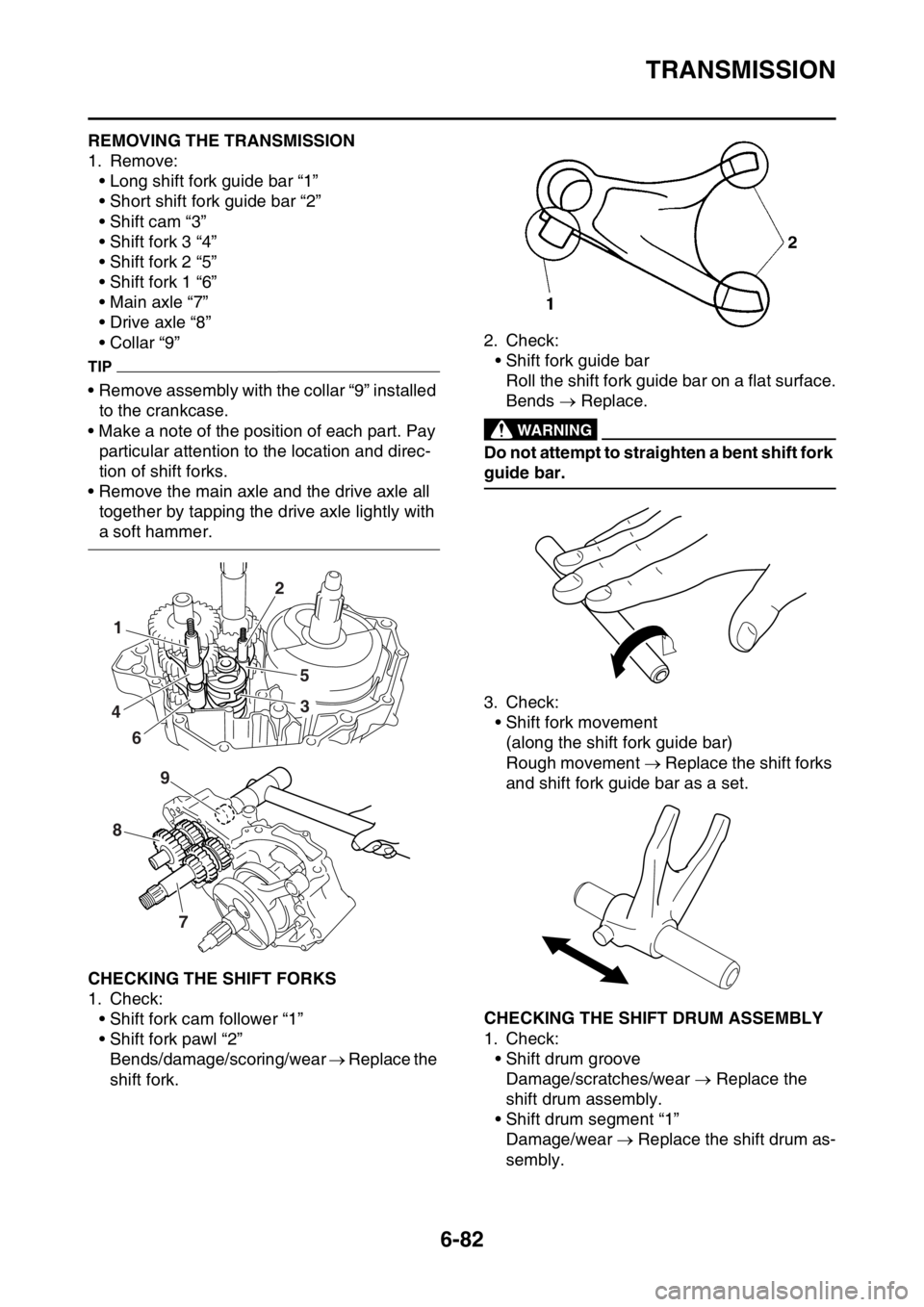
TRANSMISSION
6-82
EAS2GBB323REMOVING THE TRANSMISSION
1. Remove:
• Long shift fork guide bar “1”
• Short shift fork guide bar “2”
• Shift cam “3”
• Shift fork 3 “4”
• Shift fork 2 “5”
• Shift fork 1 “6”
• Main axle “7”
• Drive axle “8”
• Collar “9”
TIP
• Remove assembly with the collar “9” installed
to the crankcase.
• Make a note of the position of each part. Pay
particular attention to the location and direc-
tion of shift forks.
• Remove the main axle and the drive axle all
together by tapping the drive axle lightly with
a soft hammer.
EAS2GBB324CHECKING THE SHIFT FORKS
1. Check:
• Shift fork cam follower “1”
• Shift fork pawl “2”
Bends/damage/scoring/wear Replace the
shift fork.2. Check:
• Shift fork guide bar
Roll the shift fork guide bar on a flat surface.
Bends Replace.
EWA
WARNING
Do not attempt to straighten a bent shift fork
guide bar.
3. Check:
• Shift fork movement
(along the shift fork guide bar)
Rough movement Replace the shift forks
and shift fork guide bar as a set.
EAS2GBB325CHECKING THE SHIFT DRUM ASSEMBLY
1. Check:
• Shift drum groove
Damage/scratches/wear Replace the
shift drum assembly.
• Shift drum segment “1”
Damage/wear Replace the shift drum as-
sembly.
1
4
62
5
3
8
7
9
Page 318 of 432
RADIATOR
7-3
EAS2GBB330HANDLING NOTEEWA
WARNING
If coolant seems hot, do not remove the ra-
diator cap.
EAS2GBB331CHECKING THE RADIATOR
1. Check:
• Radiator fins “1”
Obstructions Clean.
Apply compressed air to the rear of the radi-
ator.
Damage Repair or replace.
TIP
Correct any flattened fins with a thin, flat-head
screwdriver.
2. Check:
• Radiator hoses
• Radiator pipes
Crack/damage Replace.
Page 326 of 432
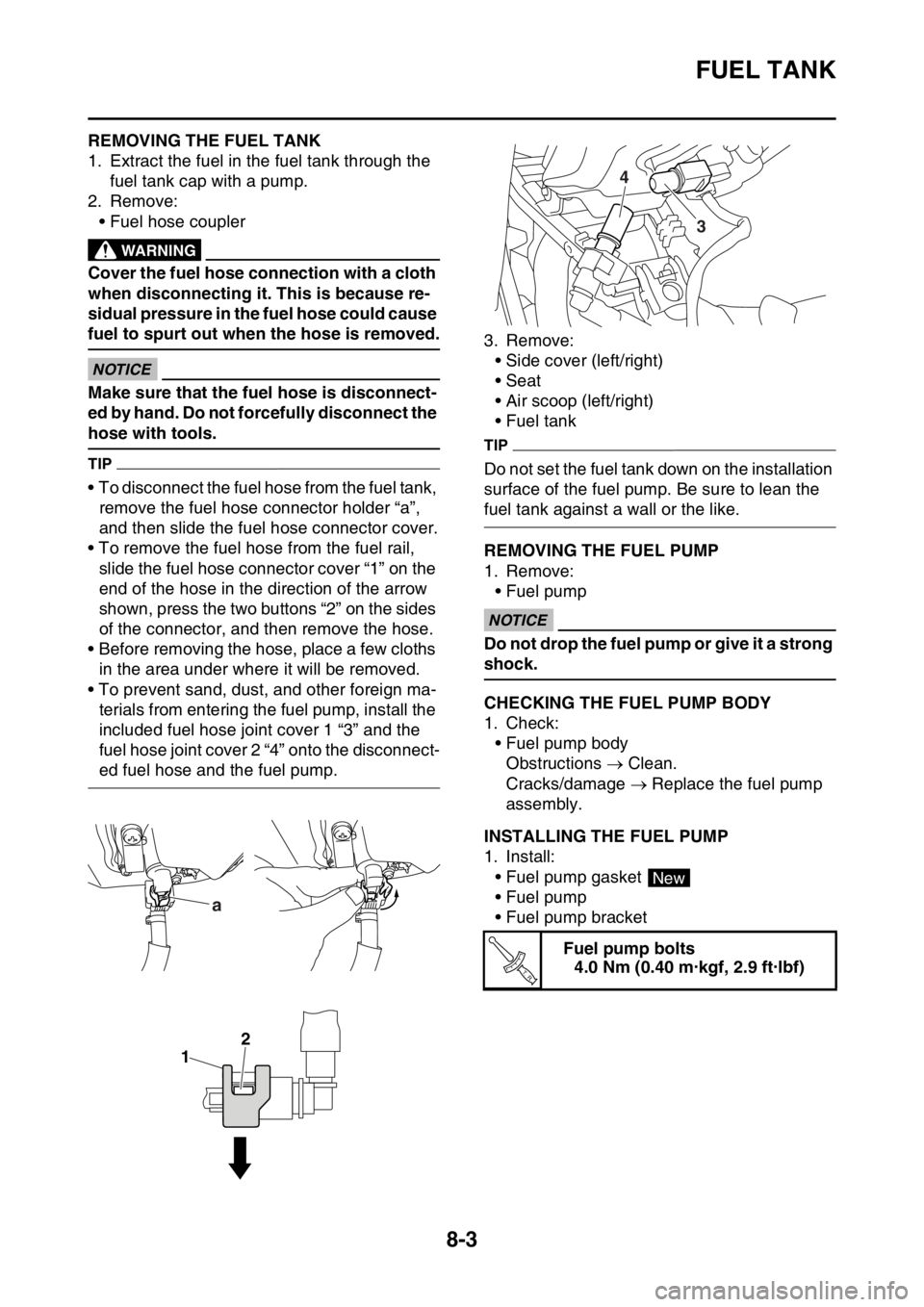
FUEL TANK
8-3
EAS2GBB340REMOVING THE FUEL TANK
1. Extract the fuel in the fuel tank through the
fuel tank cap with a pump.
2. Remove:
• Fuel hose coupler
EWA
WARNING
Cover the fuel hose connection with a cloth
when disconnecting it. This is because re-
sidual pressure in the fuel hose could cause
fuel to spurt out when the hose is removed.
ECA
NOTICE
Make sure that the fuel hose is disconnect-
ed by hand. Do not forcefully disconnect the
hose with tools.
TIP
• To disconnect the fuel hose from the fuel tank,
remove the fuel hose connector holder “a”,
and then slide the fuel hose connector cover.
• To remove the fuel hose from the fuel rail,
slide the fuel hose connector cover “1” on the
end of the hose in the direction of the arrow
shown, press the two buttons “2” on the sides
of the connector, and then remove the hose.
• Before removing the hose, place a few cloths
in the area under where it will be removed.
• To prevent sand, dust, and other foreign ma-
terials from entering the fuel pump, install the
included fuel hose joint cover 1 “3” and the
fuel hose joint cover 2 “4” onto the disconnect-
ed fuel hose and the fuel pump.3. Remove:
• Side cover (left/right)
• Seat
• Air scoop (left/right)
• Fuel tank
TIP
Do not set the fuel tank down on the installation
surface of the fuel pump. Be sure to lean the
fuel tank against a wall or the like.
EAS2GBB341REMOVING THE FUEL PUMP
1. Remove:
• Fuel pump
ECA
NOTICE
Do not drop the fuel pump or give it a strong
shock.
EAS2GBB342CHECKING THE FUEL PUMP BODY
1. Check:
• Fuel pump body
Obstructions Clean.
Cracks/damage Replace the fuel pump
assembly.
EAS2GBB343INSTALLING THE FUEL PUMP
1. Install:
• Fuel pump gasket
• Fuel pump
• Fuel pump bracket
a
1
2
Fuel pump bolts
4.0 Nm (0.40 m·kgf, 2.9 ft·lbf)
3 4
New
T R..
Page 327 of 432
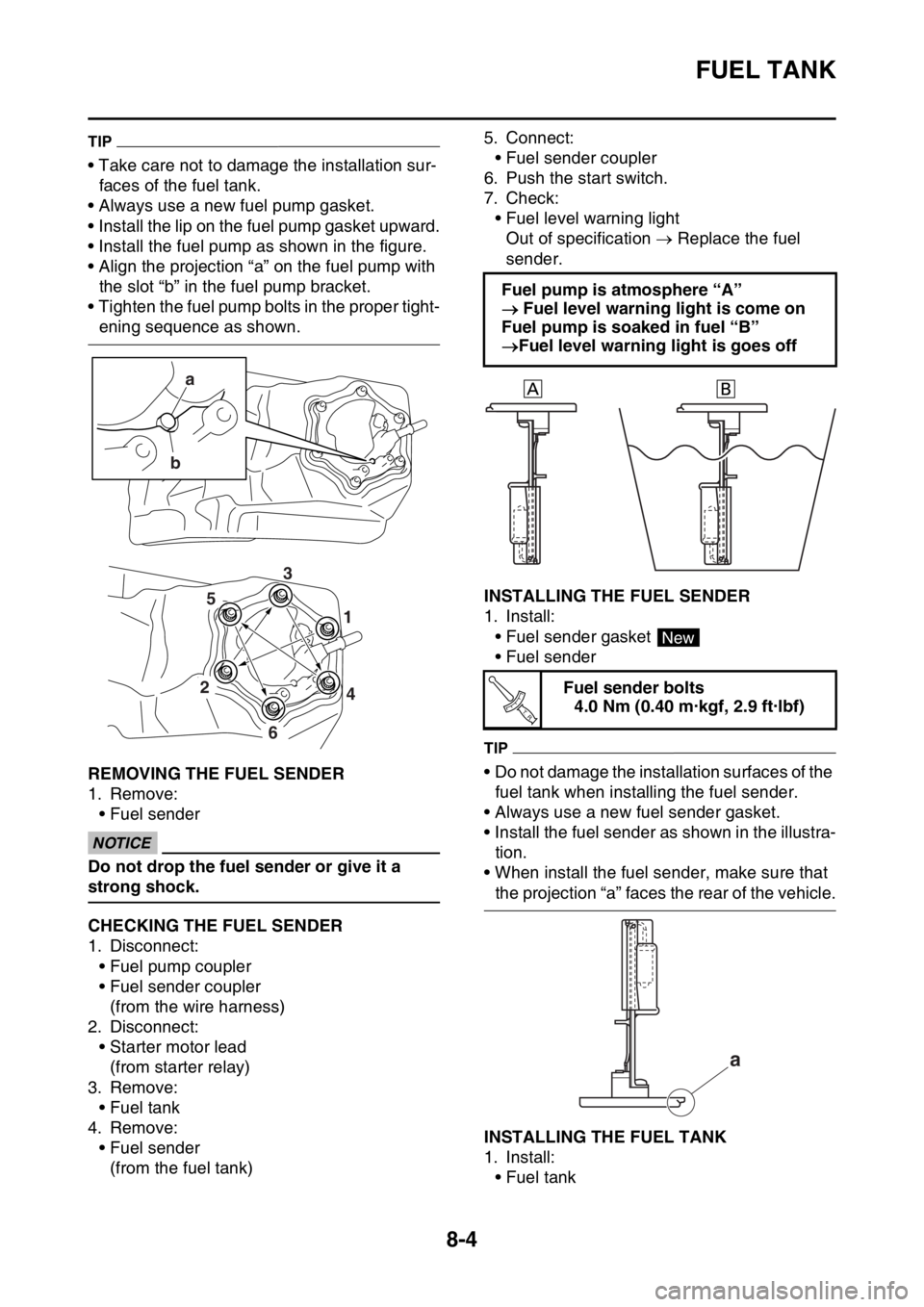
FUEL TANK
8-4
TIP
• Take care not to damage the installation sur-
faces of the fuel tank.
• Always use a new fuel pump gasket.
• Install the lip on the fuel pump gasket upward.
• Install the fuel pump as shown in the figure.
• Align the projection “a” on the fuel pump with
the slot “b” in the fuel pump bracket.
• Tighten the fuel pump bolts in the proper tight-
ening sequence as shown.
EAS2GBB344REMOVING THE FUEL SENDER
1. Remove:
• Fuel sender
ECA
NOTICE
Do not drop the fuel sender or give it a
strong shock.
EAS2GBB345CHECKING THE FUEL SENDER
1. Disconnect:
• Fuel pump coupler
• Fuel sender coupler
(from the wire harness)
2. Disconnect:
• Starter motor lead
(from starter relay)
3. Remove:
• Fuel tank
4. Remove:
• Fuel sender
(from the fuel tank)5. Connect:
• Fuel sender coupler
6. Push the start switch.
7. Check:
• Fuel level warning light
Out of specification Replace the fuel
sender.
EAS2GBB346INSTALLING THE FUEL SENDER
1. Install:
• Fuel sender gasket
• Fuel sender
TIP
• Do not damage the installation surfaces of the
fuel tank when installing the fuel sender.
• Always use a new fuel sender gasket.
• Install the fuel sender as shown in the illustra-
tion.
• When install the fuel sender, make sure that
the projection “a” faces the rear of the vehicle.
EAS2GBB347INSTALLING THE FUEL TANK
1. Install:
• Fuel tank
a
b
4 1
2
6
53
Fuel pump is atmosphere “A”
Fuel level warning light is come on
Fuel pump is soaked in fuel “B”
Fuel level warning light is goes off
Fuel sender bolts
4.0 Nm (0.40 m·kgf, 2.9 ft·lbf)
New
T R..
a
Page 328 of 432
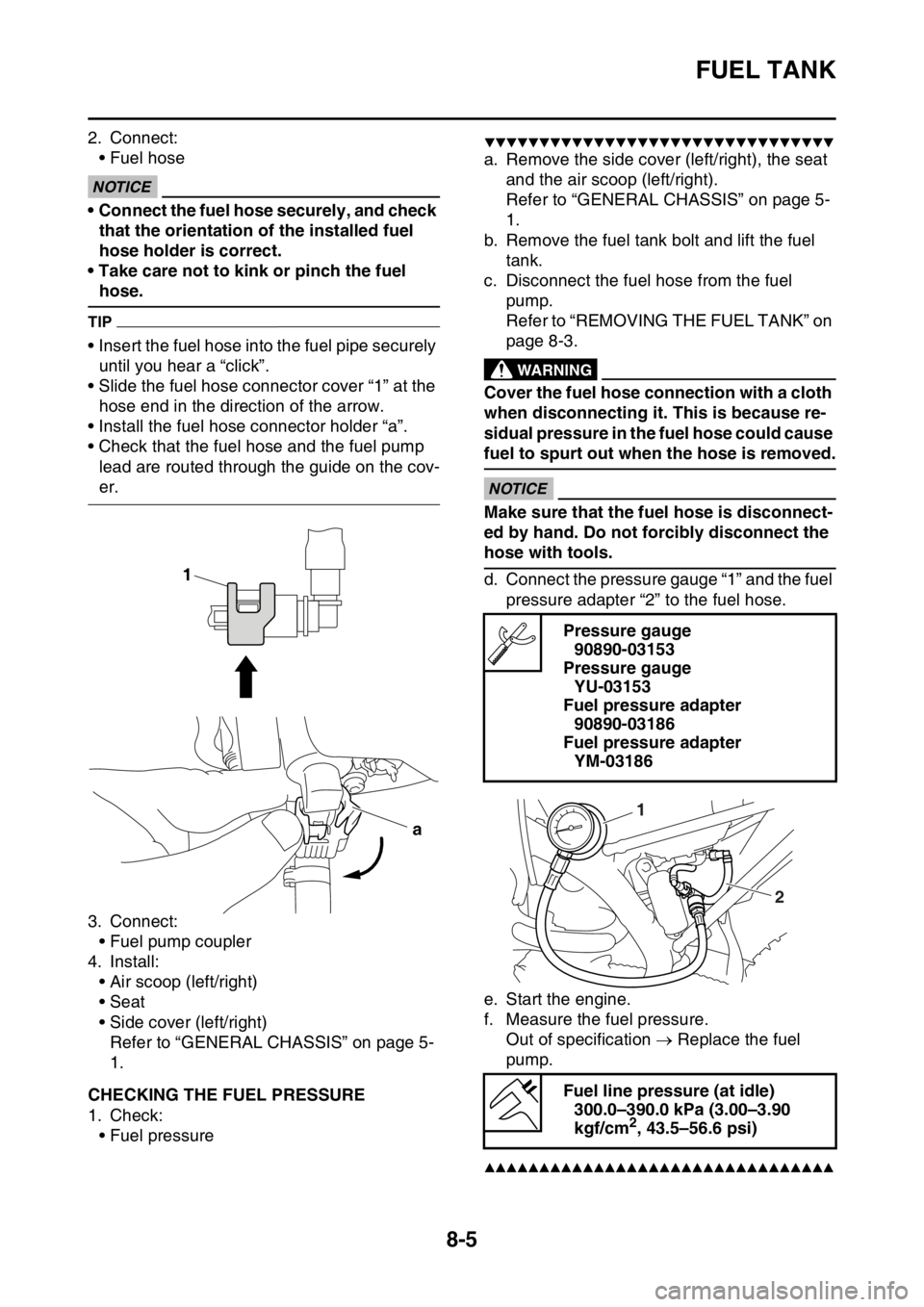
FUEL TANK
8-5
2. Connect:
• Fuel hose
ECA
NOTICE
• Connect the fuel hose securely, and check
that the orientation of the installed fuel
hose holder is correct.
• Take care not to kink or pinch the fuel
hose.
TIP
• Insert the fuel hose into the fuel pipe securely
until you hear a “click”.
• Slide the fuel hose connector cover “1” at the
hose end in the direction of the arrow.
• Install the fuel hose connector holder “a”.
• Check that the fuel hose and the fuel pump
lead are routed through the guide on the cov-
er.
3. Connect:
• Fuel pump coupler
4. Install:
• Air scoop (left/right)
• Seat
• Side cover (left/right)
Refer to “GENERAL CHASSIS” on page 5-
1.
EAS2GBB348CHECKING THE FUEL PRESSURE
1. Check:
• Fuel pressure
▼▼▼▼▼▼▼▼▼▼▼▼▼▼▼▼▼▼▼▼▼▼▼▼▼▼▼▼▼▼▼▼
a. Remove the side cover (left/right), the seat
and the air scoop (left/right).
Refer to “GENERAL CHASSIS” on page 5-
1.
b. Remove the fuel tank bolt and lift the fuel
tank.
c. Disconnect the fuel hose from the fuel
pump.
Refer to “REMOVING THE FUEL TANK” on
page 8-3.
EWA
WARNING
Cover the fuel hose connection with a cloth
when disconnecting it. This is because re-
sidual pressure in the fuel hose could cause
fuel to spurt out when the hose is removed.
ECA
NOTICE
Make sure that the fuel hose is disconnect-
ed by hand. Do not forcibly disconnect the
hose with tools.
d. Connect the pressure gauge “1” and the fuel
pressure adapter “2” to the fuel hose.
e. Start the engine.
f. Measure the fuel pressure.
Out of specification Replace the fuel
pump.
▲▲▲▲▲▲▲▲▲▲▲▲▲▲▲▲▲▲▲▲▲▲▲▲▲▲▲▲▲▲▲▲
1
a
Pressure gauge
90890-03153
Pressure gauge
YU-03153
Fuel pressure adapter
90890-03186
Fuel pressure adapter
YM-03186
Fuel line pressure (at idle)
300.0–390.0 kPa (3.00–3.90
kgf/cm
2, 43.5–56.6 psi)
1
2
Page 334 of 432
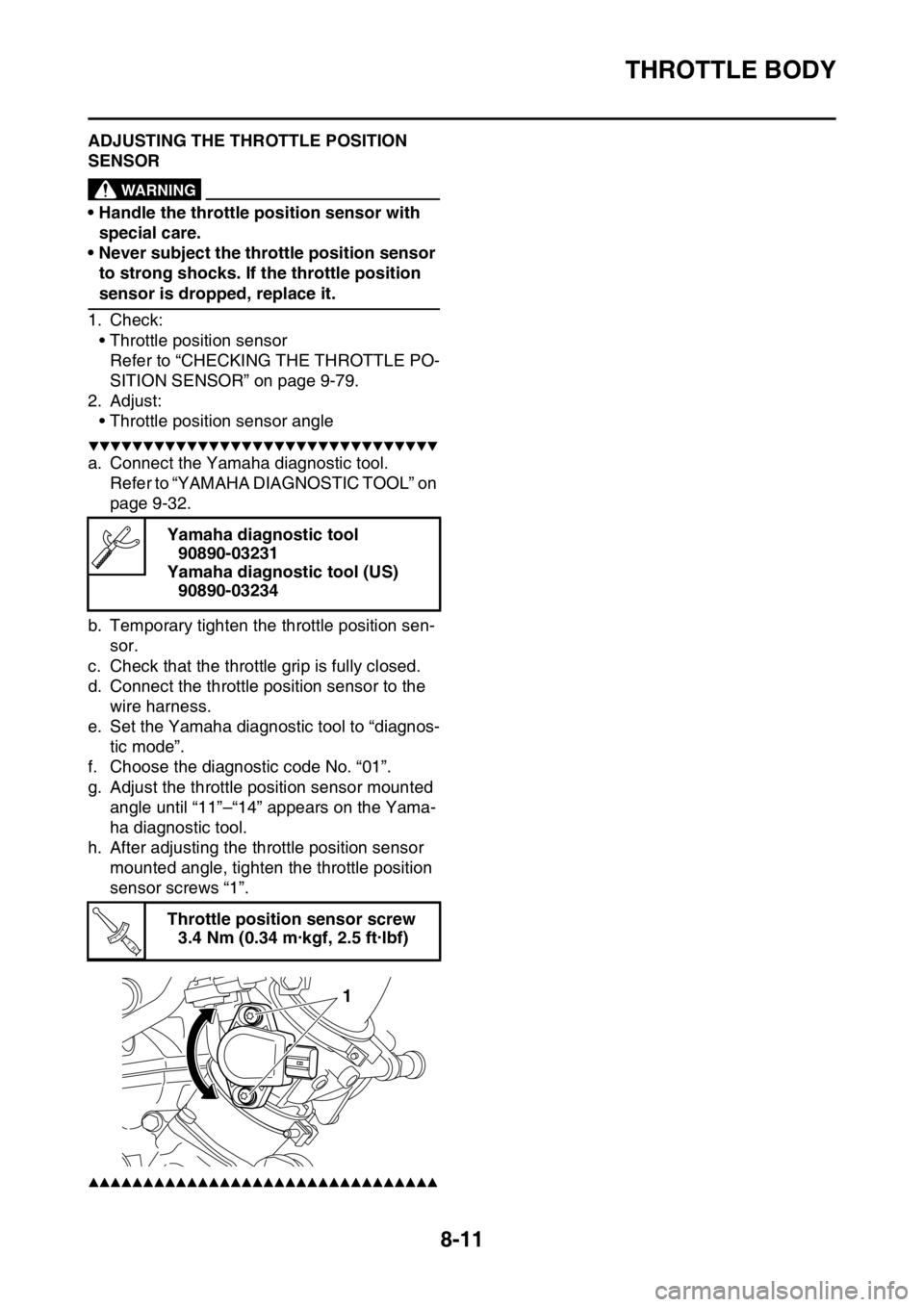
THROTTLE BODY
8-11
EAS2GBB355ADJUSTING THE THROTTLE POSITION
SENSOR
EWA
WARNING
• Handle the throttle position sensor with
special care.
• Never subject the throttle position sensor
to strong shocks. If the throttle position
sensor is dropped, replace it.
1. Check:
• Throttle position sensor
Refer to “CHECKING THE THROTTLE PO-
SITION SENSOR” on page 9-79.
2. Adjust:
• Throttle position sensor angle
▼▼▼▼▼▼▼▼▼▼▼▼▼▼▼▼▼▼▼▼▼▼▼▼▼▼▼▼▼▼▼▼
a. Connect the Yamaha diagnostic tool.
Refer to “YAMAHA DIAGNOSTIC TOOL” on
page 9-32.
b. Temporary tighten the throttle position sen-
sor.
c. Check that the throttle grip is fully closed.
d. Connect the throttle position sensor to the
wire harness.
e. Set the Yamaha diagnostic tool to “diagnos-
tic mode”.
f. Choose the diagnostic code No. “01”.
g. Adjust the throttle position sensor mounted
angle until “11”–“14” appears on the Yama-
ha diagnostic tool.
h. After adjusting the throttle position sensor
mounted angle, tighten the throttle position
sensor screws “1”.
▲▲▲▲▲▲▲▲▲▲▲▲▲▲▲▲▲▲▲▲▲▲▲▲▲▲▲▲▲▲▲▲
Yamaha diagnostic tool
90890-03231
Yamaha diagnostic tool (US)
90890-03234
Throttle position sensor screw
3.4 Nm (0.34 m·kgf, 2.5 ft·lbf)
T R..
1