Page 148 of 796
01-4
2. MAJOR COMPONENTS
Front view ▶
Vacuum pump
Camshaft position sensor
Oil filter assembly
Power steering pump pulley
Oil pressure switch
Water pump pulley
Idler pulley No. 22
Alternator pulley
Auto tensioner
Idler pulley No. 1
A/C compressor pulley
Rear view ▶
E-EGR valve
Fuel temperature sensor
Fuel HP pump assembly
Coolant temperature sensor
Crankshaft position sensorIMV valve
Isolation damper
Page 151 of 796
01-70000-00
1) Service Interval
DescriptionDaily
inspectionWeekly
inspectionService interval
Engine oil & oil
filterInspection - EU Change every 20,000 km or 12 months
(The service interval should be
shortened under severe conditions)
General Change every 15,000 km or 12 months
(The service interval should be
shortened under severe conditions)
Coolant Inspection - Change every 200,000 km or 5 years
Air cleaner
element- Inspection Diesel EU Change every 20,000 km
(The service interval should
be shortened under severe
conditions)
General Change every 15,000 km
(The service interval should
be shortened under severe
conditions)
Fuel filter - - EU Change every 40,000 km (Draining
water from fuel filter: whenever
replacing the engine oil)
General Change every 45,000 km (Draining
water from fuel filter: whenever
replacing the engine oil)
Page 158 of 796
01-14
Name SizeNumbers of
fastenerTightening
torque (Nm)Note (total
tightening
torque)
Idler pulley/tensioner pulley 1 45±4.5Nm -
Glow plug M5 4 20±2Nm -
Vacuum pumpM8×25 3 10±1Nm -
Timing gear case coverM6×40 7 10±1Nm -
M6×45 1 10±1Nm -
M6×50 3 10±1Nm -
Cylinder head coverM6×35 21 10±1Nm -
Oil dipstick gauge coverM6×16 1 10±1Nm -
Oil filter cap 1 25±2.5Nm -
Fuel railM8×25 2 25±2.5Nm -
Injector clamp boltM6×44 2 9±1.0Nm
130˚±10˚ -
High pressure pipe
(between high pressure
pump and fuel rail
assembly)M17 1 30±3Nm -
High pressure pipe
(between fuel rail assembly
and injector)M17 4 30±3Nm -
Crankshaft position sensorM5×14 1 8±0.4Nm -
Main wiringM6×16 5 10±1Nm -
Intake ductM8×25 3 25±2.5Nm -
Power steering pumpM8×100 3 25±2.5Nm -
Cylinder head front coverM6×10 5 10±1Nm -
Ladder frameM8×16 5 30±3Nm -
Page 166 of 796
02-70000-00
Cylinder head coverM6×352110±1Nm-
Oil gauge tubeM6×16110±1Nm-
Oil filter cap 125±2.5Nm-
Fuel railM8×25225±2.5Nm-
Injector clamp boltM6×4429±1.0Nm
130˚±10˚-
High pressure pipe
(between HP pump and
fuel rail)M17 130±3Nm-
High pressure pipe
(between fuel rail and
injector)M17 430±3Nm-
Crank position sensorM5×1418±0.4Nm-
Main wiringM6×16510±1Nm-
Intake ductM8×25325±2.5Nm-
Power steering pumpM8×100325±2.5Nm-
Cylinder head front coverM6×10510±1Nm-
Ladder frame M8x16 530±3Nm-
Component SizeBolt
QuantitySpecified torque
(Nm)Remark
(Total torque)
Glow plug M5 420±2Nm-
Vacuum pumpM8×25310±1Nm-
Timing gear case coverM6×40710±1Nm-
M6×45110±1Nm-
M6×50310±1Nm-
Page 210 of 796
03-32210-01
1. SPECIFICATIONS
Description Specification
Fuel Diesel
Fuel filter Type Fuel heater + priming pump + water
separator integrated type
Filter type Changeable filter element type
Change interval EU every 40,000 km
GEN every 45,000 km
Water separation
intervalEU every 20,000 km
GEN every 15,000 km
Water accumulating capacity 200 cc
Heater capacity 250W 13.5V
Injector System pressure 1800 bar
High pressure fuel
pumpType Eccentric cam/Plunger type
Operating type Gear driven type
Normal operating temperature-40 ~ 125˚C
Operating pressure 1800 bar
Operating temperature-30 ~ 120˚C
Low pressure fuel
pumpType Vane type
Gear ratio (pump/engine) 0.5 : 1
Pressure 6 bar
Fuel tank Capacity 80 L
Material Plastic
Fuel sender Single sender type
Page 212 of 796
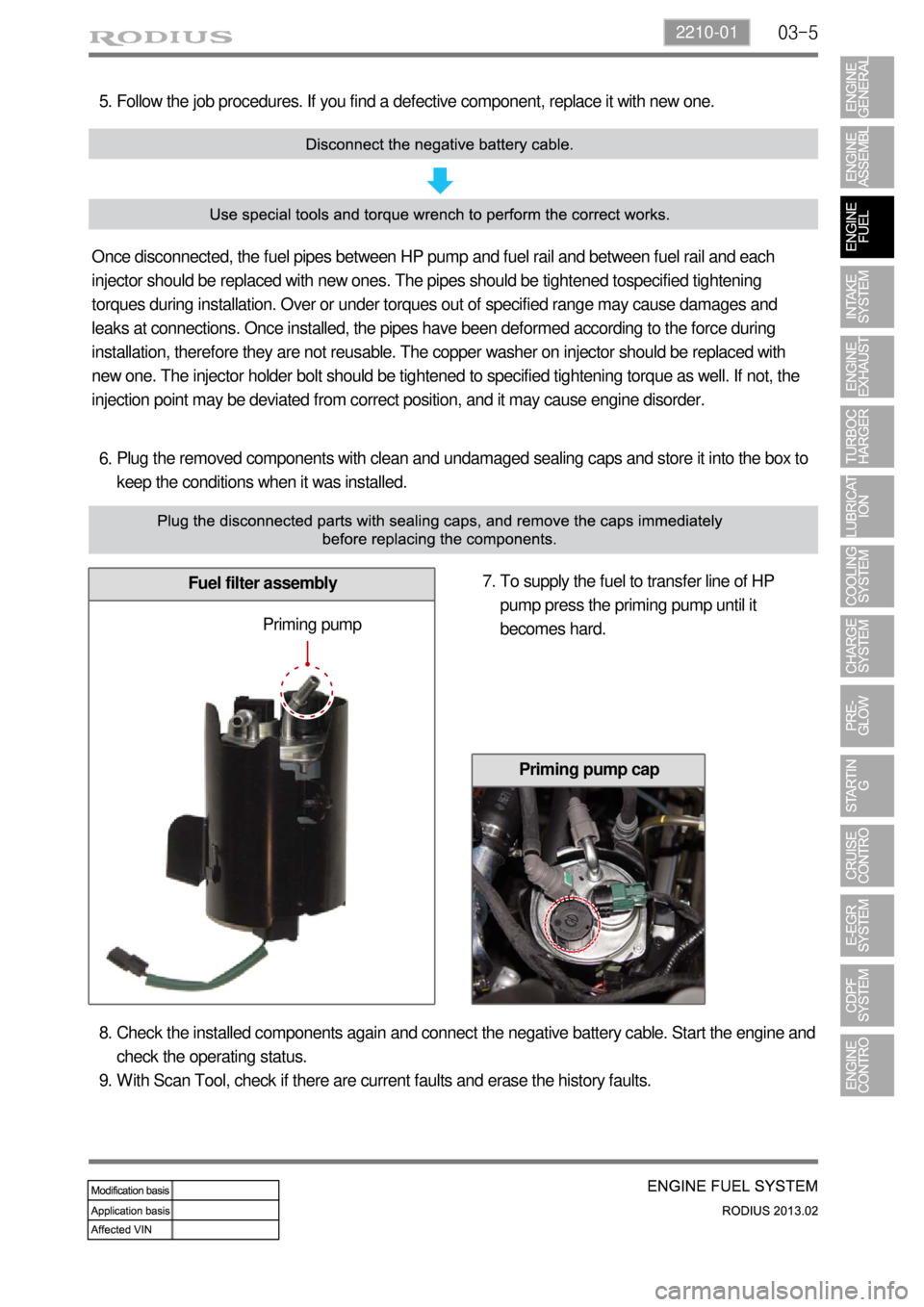
03-52210-01
Plug the removed components with clean and undamaged sealing caps and store it into the box to
keep the conditions when it was installed. 6.
Fuel filter assembly
Follow the job procedures. If you find a defective component, replace it with new one. 5.
Once disconnected, the fuel pipes between HP pump and fuel rail and between fuel rail and each
injector should be replaced with new ones. The pipes should be tightened tospecified tightening
torques during installation. Over or under torques out of specified range may cause damages and
leaks at connections. Once installed, the pipes have been deformed according to the force during
installation, therefore they are not reusable. The copper washer on injector should be replaced with
new one. The injector holder bolt should be tightened to specified tightening torque as well. If not, the
injection point may be deviated from correct position, and it may cause engine disorder.
To supply the fuel to transfer line of HP
pump press the priming pump until it
becomes hard. 7.
Priming pump
Check the installed components again and connect the negative battery cable. Start the engine and
check the operating status.
With Scan Tool, check if there are current faults and erase the history faults. 8.
9.
Priming pump cap
Page 216 of 796
03-92210-01
Device for high pressure
Device for low pressure
3) DI Engine Fuel System Pressure Test
(1) Test device (Tool kit)
(2) Pre-check
Check-tighten fuel supply line
Check fuel level in fuel tank
Check air in fuel supply line (bubble in fuel supply line or fuel)
Check fuel supply line for leaks (low pressure and high pressure)
Check that specified fuel is used
Check fuel filter for contamination -
-
-
-
-
-
Page 217 of 796
03-10
(3) DI Engine Fuel System Check Procedure
If several DTCs are output simultaneously, check the electric wiring for open or short circuit.
Check the low pressure fuel system and fuel filter and confirm that there are no abnormalities.
Carry out the high pressure fuel system check.