Page 1068 of 1336
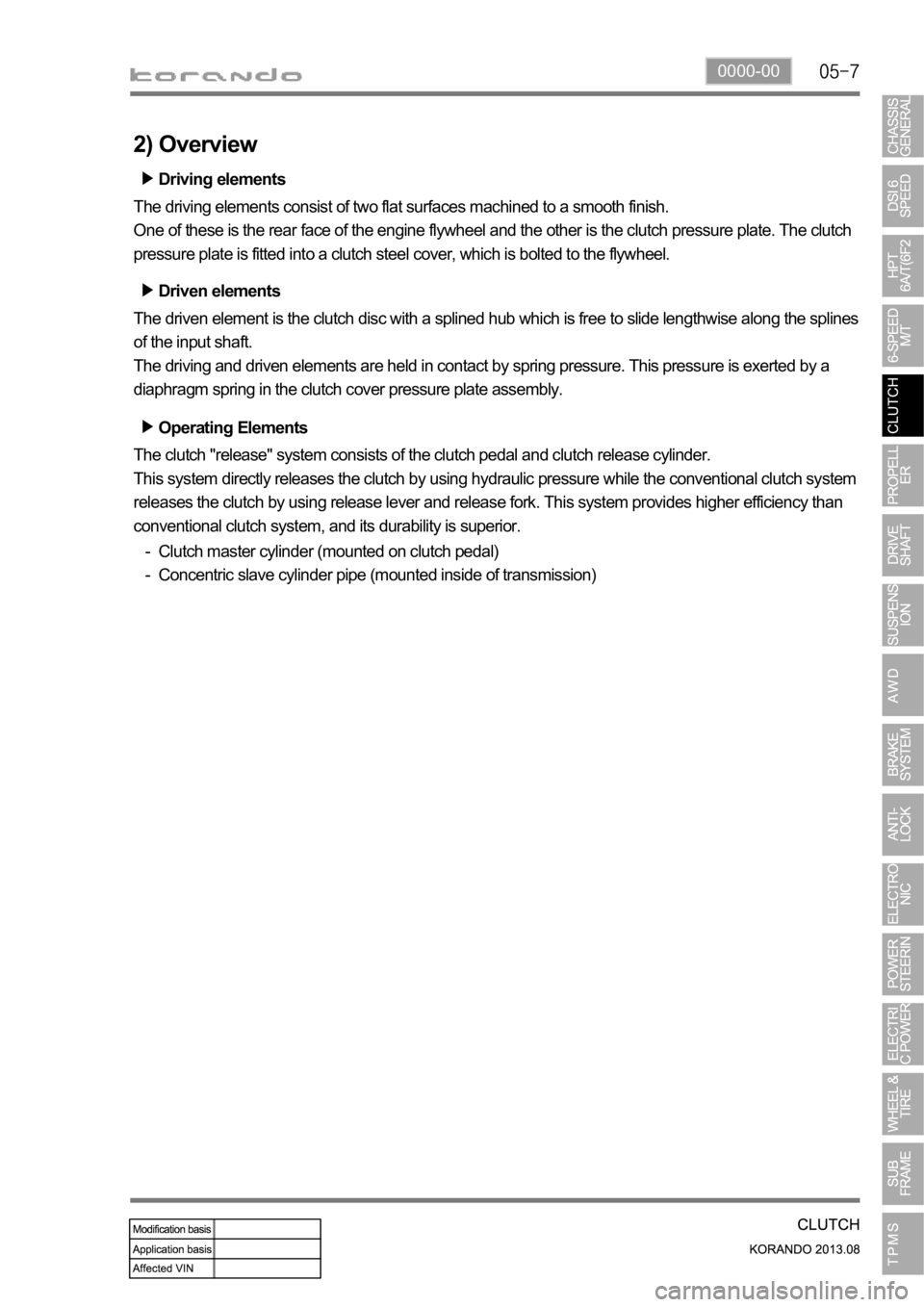
0000-00
Operating Elements
The clutch "release" system consists of the clutch pedal and clutch release cylinder.
This system directly releases the clutch by using hydraulic pressure while the conventional clutch system
releases the clutch by using release lever and release fork. This system provides higher efficiency than
conventional clutch system, and its durability is superior.
Clutch master cylinder (mounted on clutch pedal)
Concentric slave cylinder pipe (mounted inside of transmission) -
-Driving elements
The driving elements consist of two flat surfaces machined to a smooth finish.
One of these is the rear face of the engine flywheel and the other is the clutch pressure plate. The clutch
pressure plate is fitted into a clutch steel cover, which is bolted to the flywheel.
Driven elements
The driven element is the clutch disc with a splined hub which is free to slide lengthwise along the splines
of the input shaft.
The driving and driven elements are held in contact by spring pressure. This pressure is exerted by a
diaphragm spring in the clutch cover pressure plate assembly.
2) Overview
Page 1071 of 1336
3310-02
1. SPECIFICATION
Description Specification
Structure 2-piece type with CV joint, spider, and rubber
coupling
Weight below 12.0 kg
Joint type CV joint, spider, rubber coupling
Spider Numbers one (installed on center bearing side)
External diameter
Overall size
Dimension
(Length x Dia.)No.1 shaft (TM to spider)
No. 2 shaft (spider to axle)
Runout of tube (after installation) 0.3 mm
Unbalance 80g.mm @ 3,000rpm
(second measurement: 120 g.mm)
U-joint Starting torque 0.3 to 0.7 Nm
Minimum starting angle
Amount of grease in CV joint 210+-10g
2. TIGHTENING TORQUE
Fastener Tightening torque
Bolt/nut for rubber coupling (rear axle side) 39.2 to 49.0 Nm
Bolt/nut for CV joint (transaxle side) 29.4 to 39.2 Nm
Mounting bolt for center bearing 58.8 to 68.6 Nm
Page 1072 of 1336
1. OVERVIEW
The propeller shaft is a thin steel pipe which transfers the power from the transmission to the E-coupling,
and has high resistance to torsion and bending.
The propeller shaft has the universal joint (cross axle) mounted on the center of the shaft and splines for
the slip joint on the E-coupling side to accommodate the height and length changes which occur as the
shaft rotates at high speed.
And the rubber bushing for center bearing in the center of the propeller shaft keeps the balance of the
shaft and absorbs its vibration.
Function of propeller shaft
Transmits driving torque.
Accommodates the angle change (universal joint / CV joint).
Accommodates the axial length change (splines for the slip joint). -
-
-
CV joint
Universal yoke and
center bearingUniversal yoke and
rubber coupling
Page 1074 of 1336
4110-01
1. SPECIFICATION
Component Item Specifications
2WD,
4WDFront drive
shaftJoint type Inside: Tripod joint
Outside: Ball joint
Max. allowed angle
To compensate the bending
angleInstallation of equivalent
length shaft
Rear drive
shaftJoint type Inside: Cross groove joint
Outside: Ball joint
Max. allowed angle
Rear differential
carrierType Independent Rear Drive Axle
(IRDA)
Reduction gear type Hypoid gear
Gear reduction ratio 2.93
Diameter of gear
Oil type Hypoid gear oil
(SAE 75W/90)
Final drive gear backlash 0.10 to 0.15 mm
Differential gear backlash 0 to 0.076 mm
Propeller shaft Joint type PTU side: CV joint
Rear axle side: Rubber coupling
Sliding distance
Unbalance 80 g.mm or less at 3,000 rpm
Total runout 0.3 mm or less
4WD
only
Page 1076 of 1336
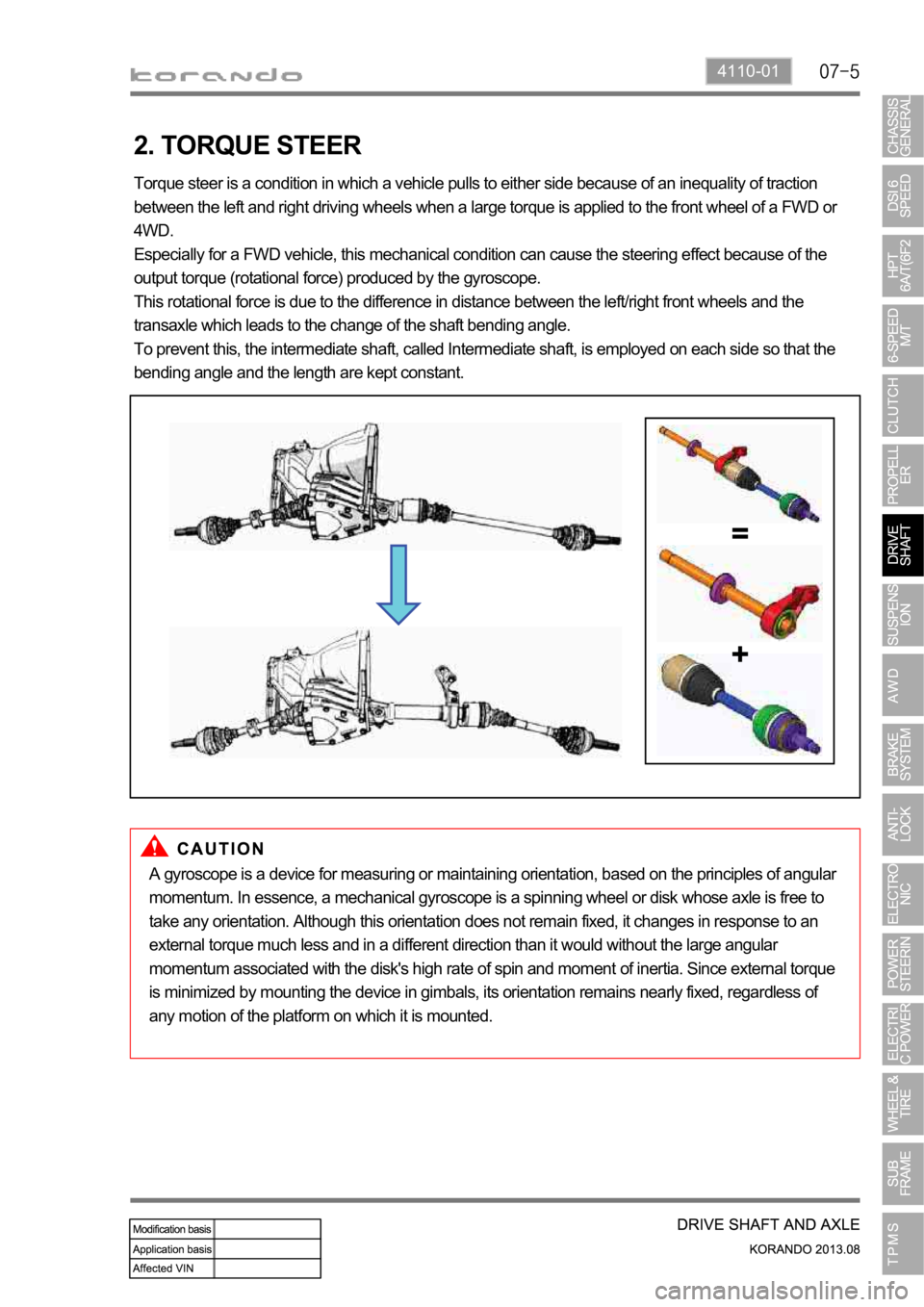
4110-01
2. TORQUE STEER
Torque steer is a condition in which a vehicle pulls to either side because of an inequality of traction
between the left and right driving wheels when a large torque is applied to the front wheel of a FWD or
4WD.
Especially for a FWD vehicle, this mechanical condition can cause the steering effect because of the
output torque (rotational force) produced by the gyroscope.
This rotational force is due to the difference in distance between the left/right front wheels and the
transaxle which leads to the change of the shaft bending angle.
To prevent this, the intermediate shaft, called Intermediate shaft, is employed on each side so that the
bending angle and the length are kept constant.
A gyroscope is a device for measuring or maintaining orientation, based on the principles of angular
momentum. In essence, a mechanical gyroscope is a spinning wheel or disk whose axle is free to
take any orientation. Although this orientation does not remain fixed, it changes in response to an
external torque much less and in a different direction than it would without the large angular
momentum associated with the disk's high rate of spin and moment of inertia. Since external torque
is minimized by mounting the device in gimbals, its orientation remains nearly fixed, regardless of
any motion of the platform on which it is mounted.
Page 1078 of 1336
0000-00
System Description Specification
Front
suspensionSuspension type Macperson strut type
Spring type Coil spring
Stabilizer type Torsion bar type
Shock absorber Type Cylindrical reciprocation type
Max. length (extended)
564 mm
Min. length
(compressed)372 mm
Min. length
(compressed)Inner diameter (A) Upper: 84.0 mm
Lower: 100.0 mm
Outer diameter (B) 163.1 mm
Free length (C) 356.1 mm
Installed length (D) 276.0 mm
Coil windings 5.32 turns
Winding direction Right direction
Rear
suspensionDriving type AWD 2WD
Suspension type (trailing, upper, lower & track
rod)Multi-link type
Spring type Coil spring
Stabilizer type Torsion bar type
Shock absorber Type Cylindrical
reciprocation type
Max. length (extended) 551 mm
Min. length
(compressed)361 mm
Coil spring Diameter (A) 12.8 mm 12.6 mm
Free length (B) 287.1 mm 291.7 mm
Coil windings 6.64 turns 6.32
Winding direction Right direction
1. SPECIFICATION
Page 1155 of 1336
4170-00
1. SPECIFICATION
Description Specification Remark
Tire16 inch 215 / 65R 16 Standard
17 inch 225 / 60R 17 Optional
18 inch 225 / 55R 18 Optional
Tire inflation pressure32psi -
Wheel16 inch 6.5 J X 16 Standard
17 inch 6.5 J X 17 Optional
18 inch 6.5 J X 18 Optional
Balance weightInner: Clip-on type
Outer: Adhesive type-
-
Tightening torquse of wheel bolt127.4 ~ 156.8 Nm 17mm X 5
(Length:56.5 mm)
Page 1178 of 1336
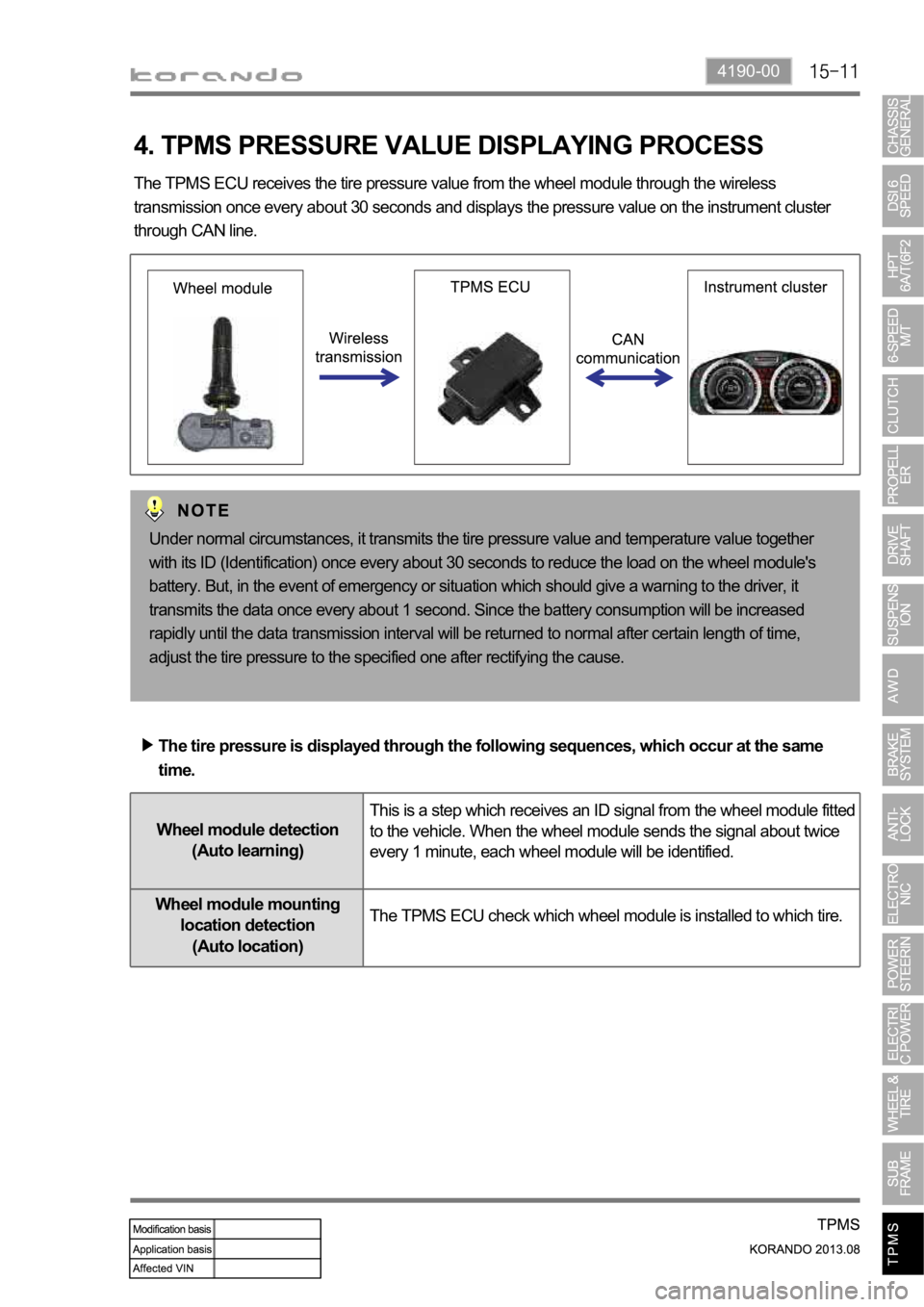
4190-00
4. TPMS PRESSURE VALUE DISPLAYING PROCESS
The TPMS ECU receives the tire pressure value from the wheel module through the wireless
transmission once every about 30 seconds and displays the pressure value on the instrument cluster
through CAN line.
Under normal circumstances, it transmits the tire pressure value and temperature value together
with its ID (Identification) once every about 30 seconds to reduce the load on the wheel module's
battery. But, in the event of emergency or situation which should give a warning to the driver, it
transmits the data once every about 1 second. Since the battery consumption will be increased
rapidly until the data transmission interval will be returned to normal after certain length of time,
adjust the tire pressure to the specified one after rectifying the cause.
The tire pressure is displayed through the following sequences, which occur at the same
time.
Wheel module detection
(Auto learning)This is a step which receives an ID signal from the wheel module fitted
to the vehicle. When the wheel module sends the signal about twice
every 1 minute, each wheel module will be identified.
Wheel module mounting
location detection
(Auto location)The TPMS ECU check which wheel module is installed to which tire.