Page 219 of 715
03-152210-01
Static test for backleak of injector ▶
Disconnect the injector return hose and
cover the openings with caps shaped
screw (included in the special tool). 1.
Connect the hose of the container for
measuring backleak to the return nipple of
the injector.
(prevent air entry to the low pressure line) 2.
Disconnect the IMV connector of the
high pressure pump and then fuel
pressure sensor connector. 3.
The connector of the injector can be easily
contaminated. Always keep it clean.
Crank the engine 2 times for 5 seconds.
Check the time for flow if injector backleak
and confirm that it is within the specified
range. 4.
5.
If the value is out of the specified range,
replace the injector.
SpecificationBelow 20 sec.
Page 221 of 715
03-172210-01
HP pump pressure test ▶
Prepare a special tool for high pressure
test and clean it thoroughly to prevent
foreign materials from entering. 1.
Disconnect the high pressure fuel supply
pipe on the HP pump and install the close
rail in the tool kit. 2.
Connect the other end of the close rail to
the fuel rail for test. 3.
Disconnect the return hose for HP pump
and connect the clear hose and connect its
the other end to the return port of the fuel
rail for test. 4.
Connect the digital tester connector to the
sensor connector of the fuel rail for test.
Crank the engine 2 times for 5 seconds after
removing the IMV connector and fuel rail
pressure sensor connector.
Read the pressure value displayed on the
tester display is within the specified. 5.
6.
7.
Specification1,050 bar or more
Page 225 of 715
03-212210-01
1. OVERVIEW
The components in fuel system supply the fuel and generate the high pressure to inject the fuel to
each injector. They are controlled by the engine ECU.
The common rail fuel injection system consists of fuel tank, fuel line, low pressure line which
supplies low pressure fuel to the low pressure pump (including high pressure pump), common rail
which distributes and accumulates the high pressurized fuel from the fuel pump, high pressure
line which connected to the injector, and the engine control unit (ECU) which calculates the
accelerator pedal position and controls the overall performance of vehicle based on the input
signals from various sensors.
1) Fuel Flow Diagram
Page 226 of 715
03-22
Camshaft position sensor
Determining injection orderFuel tank
Fuel metering by sender
2. SYSTEM LAYOUT AND OPERATION
1) Layout
For sensor and actuator control logic, refer to Chapter "Engine Control".
Engine ECU (D20DTR)
Engine control by various
signalsInjector (C3I)
Pre-injection, main injection,
after-injection by signals from
ECU
HFM sensor
Measuring intake air mass
and temperature
Crankshaft position sensor
Measuring engine rpm
Page 227 of 715
03-232210-01
T-MAP sensor
Measuring booster pressure
and temperatureFuel rail assembly
Relieving the pulsation.
Measuring the fuel pressure.
Distributing the fuel to injectors.
High pressure pump
Generating high pressurized fuel
and supplying it according to
engine rpm, required volume,
required pressure
Plunger type HP pump (1,800 bar)
Vane type LP pump (6 bar)
Accelerator pedal position
sensor
Detecting driver's intention for
speed up/down
Fuel filter assembly
Supplying clean fuel/fuel
heating/water separation by
priming pump
Page 228 of 715
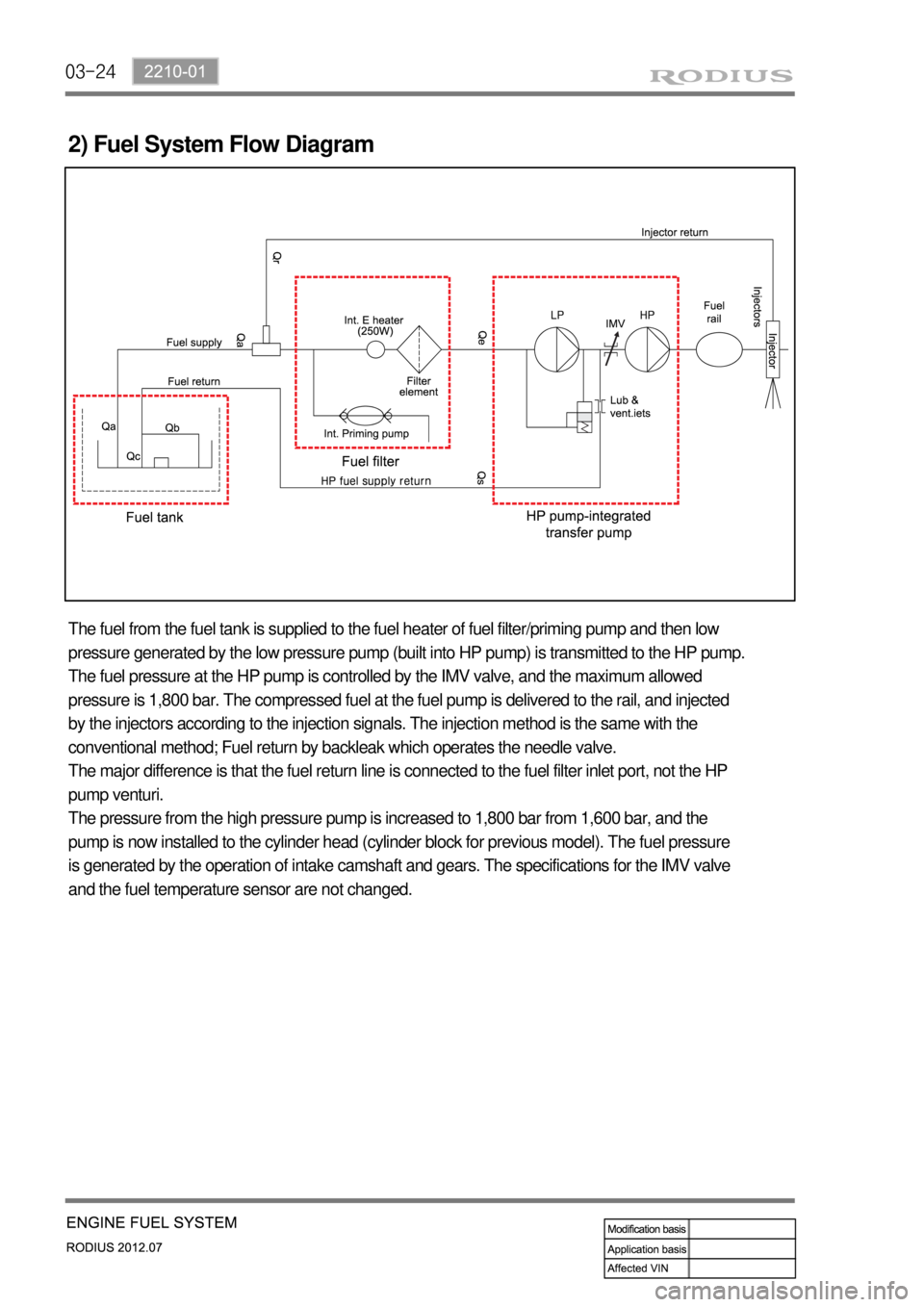
03-24
2) Fuel System Flow Diagram
The fuel from the fuel tank is supplied to the fuel heater of fuel filter/priming pump and then low
pressure generated by the low pressure pump (built into HP pump) is transmitted to the HP pump.
The fuel pressure at the HP pump is controlled by the IMV valve, and the maximum allowed
pressure is 1,800 bar. The compressed fuel at the fuel pump is delivered to the rail, and injected
by the injectors according to the injection signals. The injection method is the same with the
conventional method; Fuel return by backleak which operates the needle valve.
The major difference is that the fuel return line is connected to the fuel filter inlet port, not the HP
pump venturi.
The pressure from the high pressure pump is increased to 1,800 bar from 1,600 bar, and the
pump is now installed to the cylinder head (cylinder block for previous model). The fuel pressure
is generated by the operation of intake camshaft and gears. The specifications for the IMV valve
and the fuel temperature sensor are not changed.
Page 230 of 715
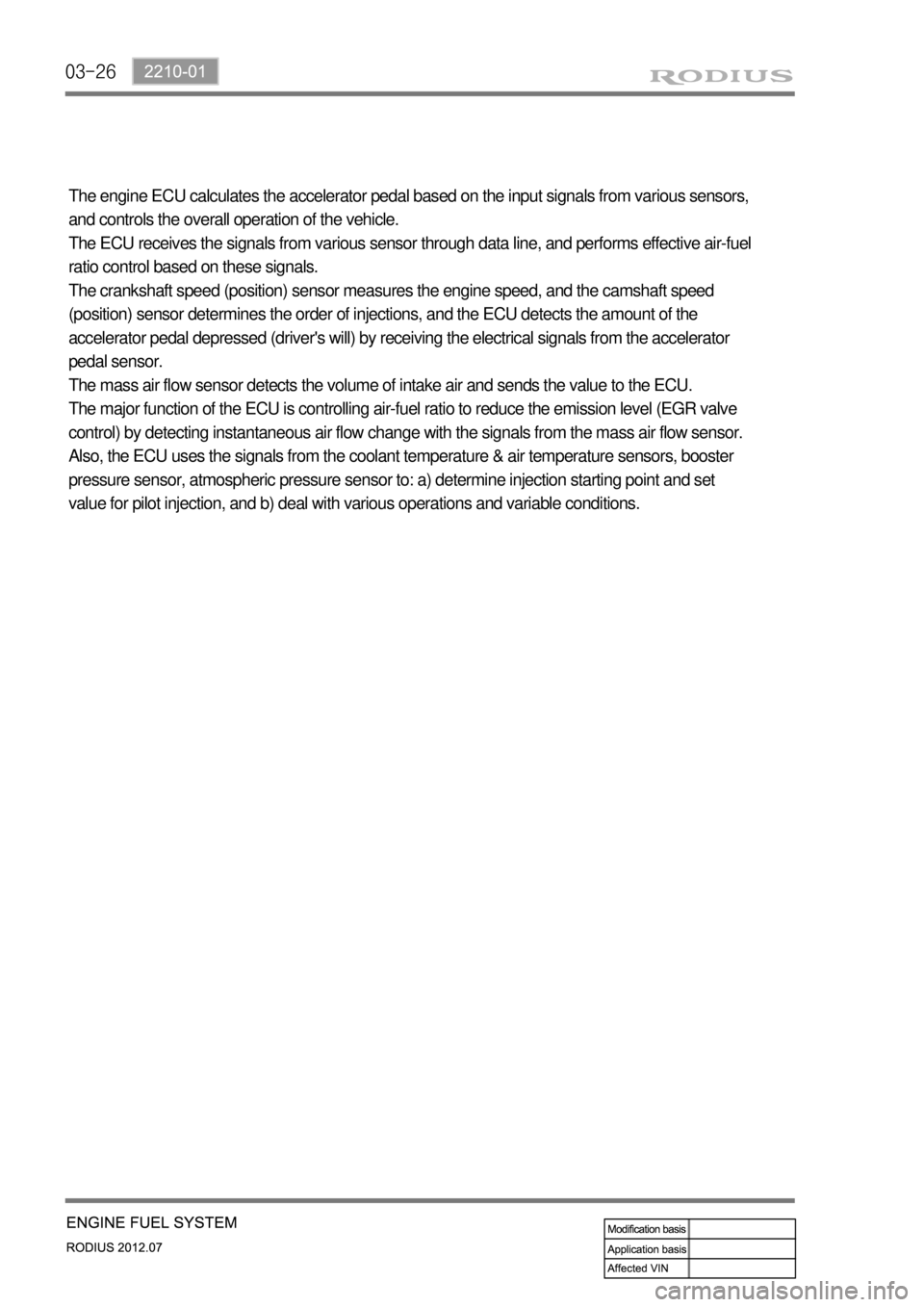
03-26
The engine ECU calculates the accelerator pedal based on the input signals from various sensors,
and controls the overall operation of the vehicle.
The ECU receives the signals from various sensor through data line, and performs effective air-fuel
ratio control based on these signals.
The crankshaft speed (position) sensor measures the engine speed, and the camshaft speed
(position) sensor determines the order of injections, and the ECU detects the amount of the
accelerator pedal depressed (driver's will) by receiving the electrical signals from the accelerator
pedal sensor.
The mass air flow sensor detects the volume of intake air and sends the value to the ECU.
The major function of the ECU is controlling air-fuel ratio to reduce the emission level (EGR valve
control) by detecting instantaneous air flow change with the signals from the mass air flow sensor.
Also, the ECU uses the signals from the coolant temperature & air temperature sensors, booster
pressure sensor, atmospheric pressure sensor to: a) determine injection starting point and set
value for pilot injection, and b) deal with various operations and variable conditions.
Page 234 of 715
04-6
1. OVERVIEW
The intake system for D20DTR engine is equipped with a throttle body which includes a flap. This
flap is controlled by an electrical signal to cut off the intake air entering to the engine when the
ignition switch is turned off. Because of this, the shape of the intake manifold has been changed
and improved HFM sensor is newly adopted to control the intake air volume more precisely.
2. COMPONENT
2330-01 Intercooler assembly
2313-15 HFM sensor
HFM sensor, version 7
*For more information, refer to Chapter "Engine
Control".
2313-01 Air cleaner assembly