Page 968 of 1082
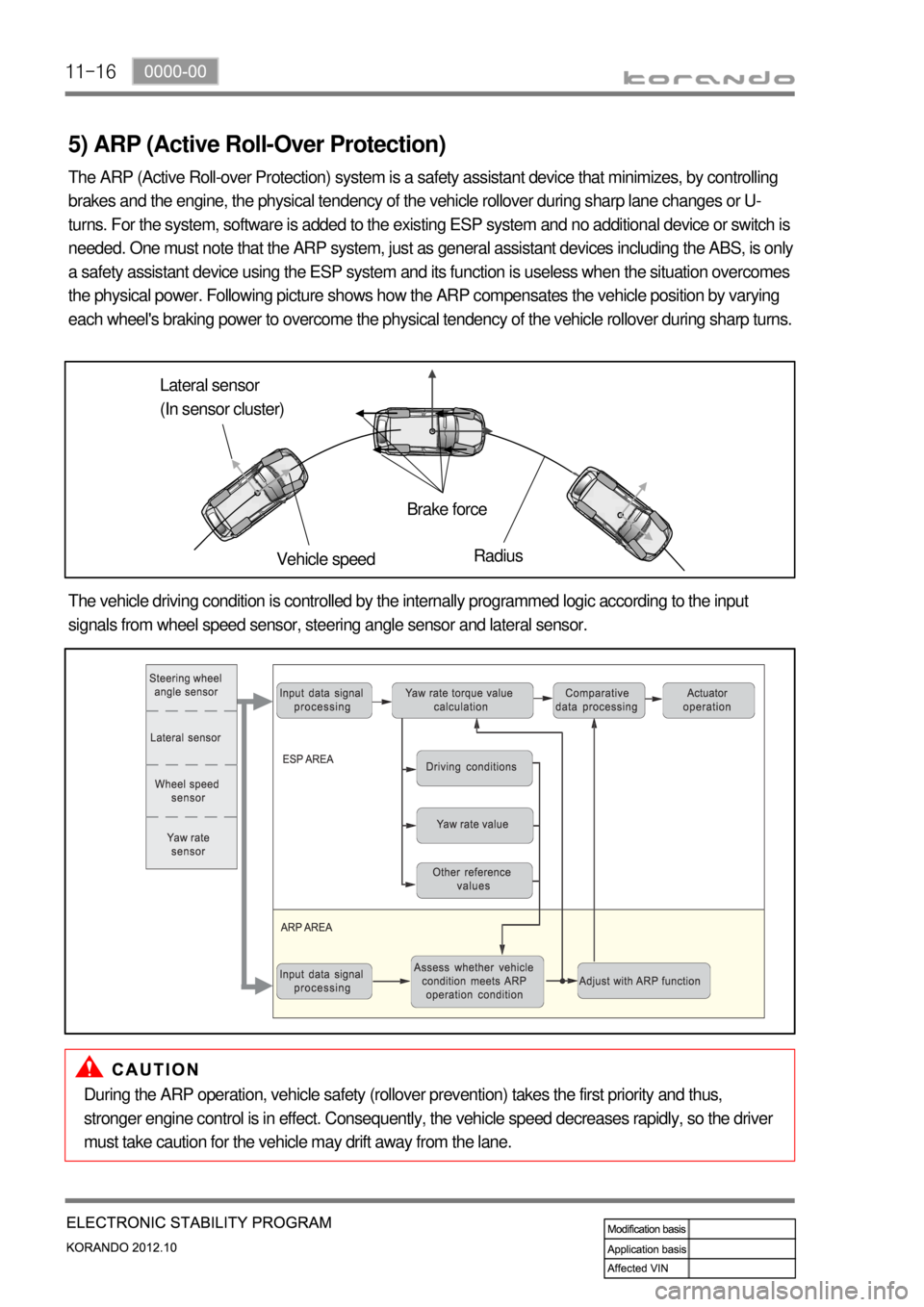
11-16
5) ARP (Active Roll-Over Protection)
The ARP (Active Roll-over Protection) system is a safety assistant device that minimizes, by controlling
brakes and the engine, the physical tendency of the vehicle rollover during sharp lane changes or U-
turns. For the system, software is added to the existing ESP system and no additional device or switch is
needed. One must note that the ARP system, just as general assistant devices including the ABS, is only
a safety assistant device using the ESP system and its function is useless when the situation overcomes
the physical power. Following picture shows how the ARP compensates the vehicle position by varying
each wheel's braking power to overcome the physical tendency of the vehicle rollover during sharp turns.
Lateral sensor
(In sensor cluster)
Vehicle speedBrake force
Radius
The vehicle driving condition is controlled by the internally programmed logic according to the input
signals from wheel speed sensor, steering angle sensor and lateral sensor.
During the ARP operation, vehicle safety (rollover prevention) takes the first priority and thus,
stronger engine control is in effect. Consequently, the vehicle speed decreases rapidly, so the driver
must take caution for the vehicle may drift away from the lane.
Page 973 of 1082
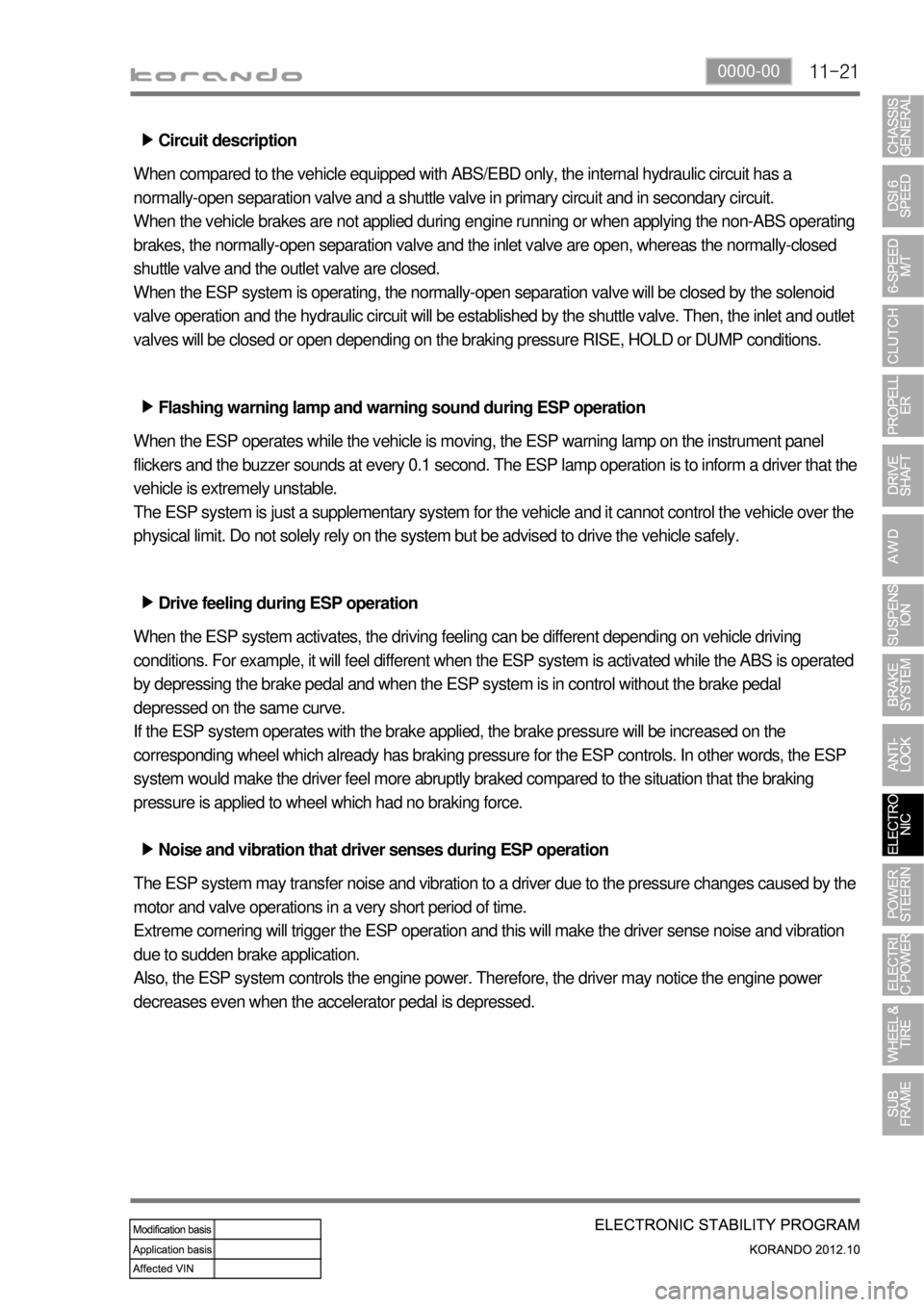
11-210000-00
Circuit description ▶
When compared to the vehicle equipped with ABS/EBD only, the internal hydraulic circuit has a
normally-open separation valve and a shuttle valve in primary circuit and in secondary circuit.
When the vehicle brakes are not applied during engine running or when applying the non-ABS operating
brakes, the normally-open separation valve and the inlet valve are open, whereas the normally-closed
shuttle valve and the outlet valve are closed.
When the ESP system is operating, the normally-open separation valve will be closed by the solenoid
valve operation and the hydraulic circuit will be established by the shuttle valve. Then, the inlet and outlet
valves will be closed or open depending on the braking pressure RISE, HOLD or DUMP conditions.
Flashing warning lamp and warning sound during ESP operation ▶
When the ESP operates while the vehicle is moving, the ESP warning lamp on the instrument panel
flickers and the buzzer sounds at every 0.1 second. The ESP lamp operation is to inform a driver that the
vehicle is extremely unstable.
The ESP system is just a supplementary system for the vehicle and it cannot control the vehicle over the
physical limit. Do not solely rely on the system but be advised to drive the vehicle safely.
Drive feeling during ESP operation ▶
When the ESP system activates, the driving feeling can be different depending on vehicle driving
conditions. For example, it will feel different when the ESP system is activated while the ABS is operated
by depressing the brake pedal and when the ESP system is in control without the brake pedal
depressed on the same curve.
If the ESP system operates with the brake applied, the brake pressure will be increased on the
corresponding wheel which already has braking pressure for the ESP controls. In other words, the ESP
system would make the driver feel more abruptly braked compared to the situation that the braking
pressure is applied to wheel which had no braking force.
Noise and vibration that driver senses during ESP operation ▶
The ESP system may transfer noise and vibration to a driver due to the pressure changes caused by the
motor and valve operations in a very short period of time.
Extreme cornering will trigger the ESP operation and this will make the driver sense noise and vibration
due to sudden brake application.
Also, the ESP system controls the engine power. Therefore, the driver may notice the engine power
decreases even when the accelerator pedal is depressed.
Page 978 of 1082
11-26
5) Hydraulic Circuit of HBA
The above figure shows one front and one rear wheel and the same hydraulic circuit forms as in the ESP
operation. When HECU recognizes that it is an emergency and it is required for hard braking, depending
on the pressure value of the brake pressure sensor and pressure changes caused by the pressure sensor
timing, it operates the pump immediately to apply the brake pressure at the wheels. Then, the pressure in
the pump increases until just before the corresponding wheel gets locked. The motor still keeps rotating
and the outlet valve and the separation valve will stay closed. When the wheel starts to lock, the HBA
function cancels and switches to ABS operation.
Page 980 of 1082
12-30000-00
1. SPECIFICATION (HPS)
Component Item Specification
Steering wheel Type 3-spoke
Outside diameterΦ 380 mm
Number of revolutions 3.11 rotations
Heated wire Simple ON/OFF
Gear box Type Rack and pinion
Gear ratio 46.94
Rack stroke± 73 mm
Steering angle Inner39°
Outer31.24°
Wheel alignment Toe-in2 ± 2 mm
Oil pump Type Vane (removable pump and reservoir)
Maximum pressure100 ± 3 bar
Displacement6.0 to 9.75 ℓ/min
Pulley diameterΦ 115 mm
Steering column Tilting angle Up + 2.0
Down - 30
Lower shaft Type Ball slip
Steering oil Oil typeATF Dexron Ⅱ or Ⅲ
Oil reservoir capacity1 ℓ
Change interval EU (Diesel): Check and add at every 20,000
km
GEN (Diesel, Gasoline): Check and add at
every 15,000 km
Turning capability Min. turning radius 5.4 m
Page 983 of 1082
12-6
4. MAJOR CHANGES
1) Steering Heating System
Steering wheel heating unit
Old New
The steering wheel heated wire and the heating unit are
installed in the steering wheel assembly.Lower switch cluster
Old
New
The steering wheel heating switch has
been added on the lower switch cluster.
Specifications ▶
Description Specification
Power consumption Below 95W
Rated voltage 12V
Operating voltage 9V~16V
Rated current6±2.0A
Steering wheel
heating unit
Steering wheel
heating switch