Page 11 of 128
9
Basic operations
1 Reverse selector switch
Pull the switch to select Reverse (R).
2 Paddle shift switches ("P. 40)
Pull the right paddle shift switch to upshift and the left paddle shift switch to
downshift. Pull both paddle shift switches at once to select Neutral (N).
3 Control pad ("P. 66)
4 “ENGINE START” switch
5 Driving mode selector switch ("P. 26)
6 AUTO driving mode button ("P. 27)
7 Shift speed selector ("P. 41)
Allows the driver to choose their desired shift speeds for the manually shifted
SPORT, NORMAL, and WET driving modes.
8 Parking brake switch
9 Ignition switch
10 Accelerator pedal ("P. 32)
11 Tilt and telescopic steering lock release lever
12 Brake pedal ("P. 50)
13 Hood release lever ("P. 12)
14 Rear hatch opener switch ("P. 12)
15 Fuel filler door opener switch ("P. 12)
16 Outside rear view mirror switches
17 VSC off switch
Turns VSC and TRAC off. Press the switch again to turn VSC and TRAC back on.
Page 13 of 128
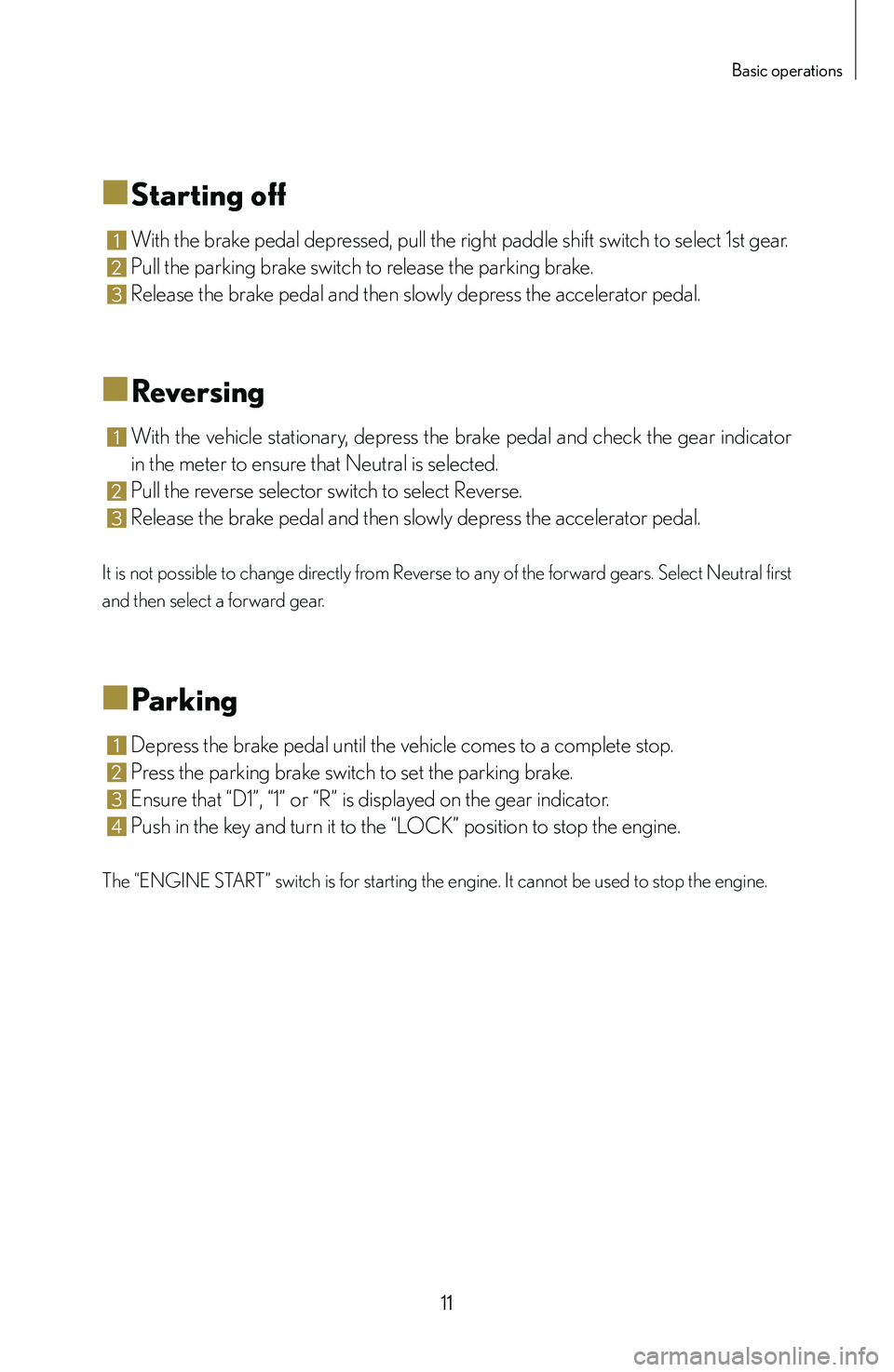
11
Basic operations
■
■Starting off
1 With the brake pedal depressed, pull the right paddle shift switch to select 1st gear.
2 Pull the parking brake switch to release the parking brake.
3 Release the brake pedal and then slowly depress the accelerator pedal.
■
■Reversing
1 With the vehicle stationary, depress the brake pedal and check the gear indicator
in the meter to ensure that Neutral is selected.
2 Pull the reverse selector switch to select Reverse.
3 Release the brake pedal and then slowly depress the accelerator pedal.
It is not possible to change directly from Reverse to any of the forward gears. Select Neutral first
and then select a forward gear.
■
■Parking
1 Depress the brake pedal until the vehicle comes to a complete stop.
2 Press the parking brake switch to set the parking brake.
3 Ensure that “D1”, “1” or “R” is displayed on the gear indicator.
4 Push in the key and turn it to the “LOCK” position to stop the engine.
The “ENGINE START” switch is for starting the engine. It cannot be used to stop the engine.
Page 25 of 128

23
Ideal driving position
■
■Steering wheel adjustment range
The LFA has a tilt and telescopic steering column that allows you to manually adjust
the longitudinal and vertical position of the steering wheel.
The tilt fulcrum has been placed a significant distance away from the steering wheel
itself in order to minimize the change in steering wheel angle when adjusting its
vertical position. Minimizing the change in steering wheel angle prevents the top of
the steering wheel from moving too far away from the driver.
Meanwhile, the telescopic adjustment allows the steering wheel and column to be
moved as a whole so that the distance between the steering wheel and the paddle
shift switches remains the same.
Highest
position
Lowest position
Telescopic adjustment range:
1.57 in. (40 mm) Tilt range:
2.6°
Tilt fulcrum
Adjusting the steering wheel position
Pull the tilt and telescopic steering lock
r e l e a s e l e v e r d o w n w h i l e m o v i n g t h e
steering wheel longitudinally and vertically
into the desired position. After adjustment,
p u s h t h e l eve r u p a n d c h e c k t h a t t h e
steering wheel is securely fixed in place.
Page 46 of 128
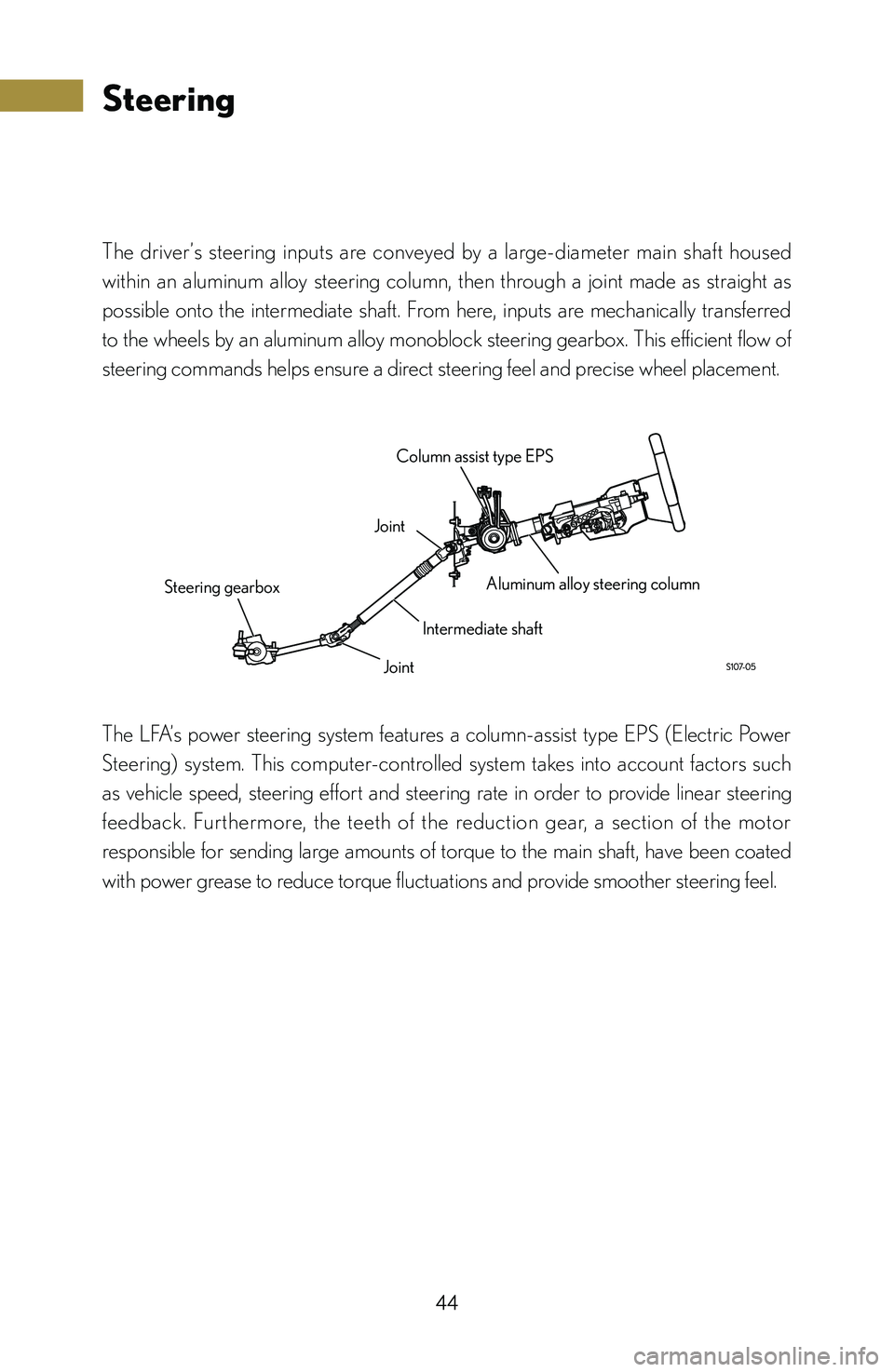
44
Steering
The driver’s steering inputs are conveyed by a large-diameter main shaft housed
within an aluminum alloy steering column, then through a joint made as straight as
possible onto the intermediate shaft. From here, inputs are mechanically transferred
to the wheels by an aluminum alloy monoblock steering gearbox. This efficient flow of
steering commands helps ensure a direct steering feel and precise wheel placement.
Joint Column assist type EPS
Aluminum alloy steering column
Intermediate shaft
Joint
Steering gearbox
The LFA’s power steering system features a column-assist type EPS (Electric Power
Steering) system. This computer-controlled system takes into account factors such
as vehicle speed, steering effort and steering rate in order to provide linear steering
feedback. Furthermore, the teeth of the reduction gear, a section of the motor
responsible for sending large amounts of torque to the main shaft, have been coated
with power grease to reduce torque fluctuations and provide smoother steering feel.
Page 47 of 128
45
Steering
■
■Steering wheel
The steering wheel features a flat-bottomed design that has 1.10 in. (28 mm) of the
lower half cut away. This reduces the steering wheel’s inertial moment and locates
the wheel’s rotational center and its center of gravity in almost the same place, almost
completely eliminating any imbalance within the steering wheel itself, reducing the
amount of steering fluctuations imparted by lateral and vertical forces. Ultimately
this provides the driver with a more natural and accurate steering feel. Furthermore,
the use of an aluminum alloy frame and hollow CFRP rim reduces the inertial force
generated by steering inputs.
H o l l o w C F R P
steering wheel rim
Center of rotation
Center of gravity
Turns lock-to-lock: 2.35
Aluminum alloy frame
Steering wheel center
Page 48 of 128
46
■
■Steering rack and gearbox
The steering gearbox consists of a monoblock aluminum alloy rack and pinion unit
mounted to the front suspension member using four rigid mounts. This allows the
driver to feel as if they are solidly connected to the road. An overall steering ratio of
14.3:1 allows the driver to precisely follow their intended line through a corner.
S107-06The joint between the steering shaft and gearbox is set at a narrow angle (approx. 10˚)
for a highly efficient connection that allows even subtle steering inputs to be accurately
conveyed, keeping the LFA directly on the driver’s intended path no matter what the
situation, whether it be a winding road or an extremely fast straightaway. Joint angle: Approx. 10˚
Page 52 of 128
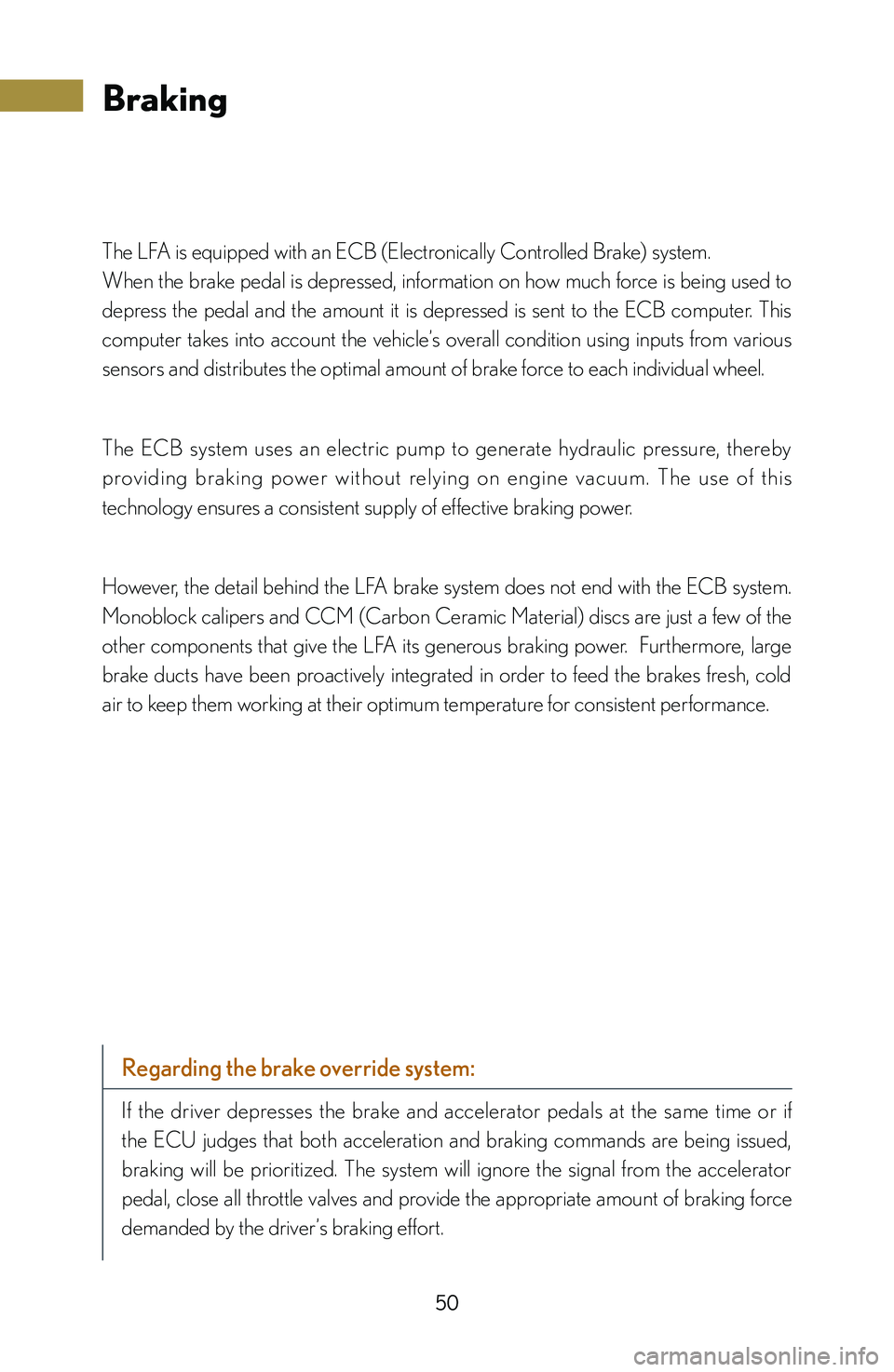
50
Braking
The LFA is equipped with an ECB (Electronically Controlled Brake) system.
When the brake pedal is depressed, information on how much force is being used to
depress the pedal and the amount it is depressed is sent to the ECB computer. This
computer takes into account the vehicle’s overall condition using inputs from various
sensors and distributes the optimal amount of brake force to each individual wheel.
The ECB system uses an electric pump to generate hydraulic pressure, thereby
providing braking power without relying on engine vacuum. The use of this
technology ensures a consistent supply of effective braking power.
However, the detail behind the LFA brake system does not end with the ECB system.
Monoblock calipers and CCM (Carbon Ceramic Material) discs are just a few of the
other components that give the LFA its generous braking power. Furthermore, large
brake ducts have been proactively integrated in order to feed the brakes fresh, cold
air to keep them working at their optimum temperature for consistent performance.
Regarding the brake override system:
If the driver depresses the brake and accelerator pedals at the same time or if
the ECU judges that both acceleration and braking commands are being issued,
braking will be prioritized. The system will ignore the signal from the accelerator
pedal, close all throttle valves and provide the appropriate amount of braking force
demanded by the driver’s braking effort.
Page 54 of 128
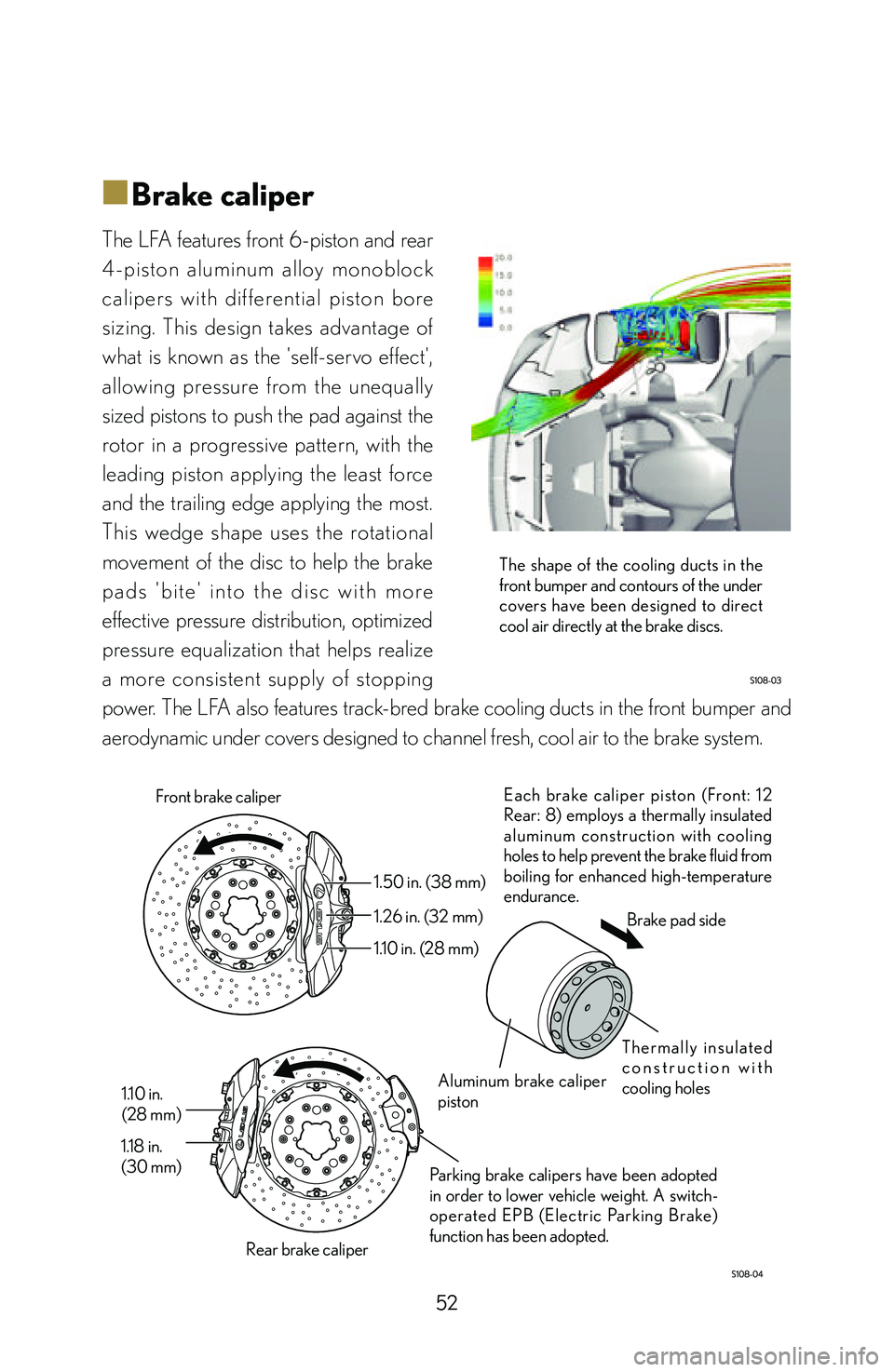
52
■
■Brake caliper
The LFA features front 6-piston and rear
4-piston aluminum alloy monoblock
calipers with dif ferential piston bore
sizing. This design takes advantage of
what is known as the 'self-servo effect',
allowing pressure from the unequally
sized pistons to push the pad against the
rotor in a progressive pattern, with the
leading piston applying the least force
and the trailing edge applying the most.
This wedge shape uses the rotational
movement of the disc to help the brake
p a d s ' b i t e ' i n t o t h e d i s c w i t h m o r e
effective pressure distribution, optimized
pressure equalization that helps realize
a more consistent supply of stopping
power. The LFA also features track-bred brake cooling ducts in the front bumper and
aerodynamic under covers designed to channel fresh, cool air to the brake system.
Each brake caliper piston (Front: 12
Rear: 8) employs a thermally insulated
aluminum construction with cooling
holes to help prevent the brake fluid from
boiling for enhanced high-temperature
endurance.
Parking brake calipers have been adopted
in order to lower vehicle weight. A switch-
operated EPB (Electric Parking Brake)
function has been adopted.
1.50 in. (38 mm)
1.26 in. (32 mm)
1.10 in. (28 mm)
1.10 in.
(28 mm)
1.18 in.
(30 mm) Front brake caliper
Rear brake caliper Aluminum brake caliper
piston
T h e r m a l l y i n s u l a t e d
c o n s t r u c t i o n w i t h
cooling holesBrake pad side
The shape of the cooling ducts in the
front bumper and contours of the under
covers have been designed to direct
cool air directly at the brake discs.