Page 110 of 273

DIESEL INJECTION
Fault finding – Interpretation of faults13B
13B-110V3 MR-372-J84-13B250$405.mif
EDC16
PROGRAM No.: C1
Vdiag No.: 51
DF209
PRESENT
OR
STOREDEGR POSITION SENSOR CIRCUIT
CO.0 : Open circuit or short circuit to earth
CC.1 : Short circuit to + 12 V
1.DEF : Micro-breaks
NOTESConditions for applying the fault finding procedure to stored faults:
The fault is declared present after the engine is started or following a road test.
Special notes:
If the fault is present:
–there is smoke coming from the exhaust,
–the EGR offset fault finding function is disabled,
–the OBD warning light will come on after three consecutive driving cycles (starting
+ 5 seconds + switching off the ignition and waiting 1 minute).
Use bornier Ele. 1681 or Ele. 1590 for any operation on the injection computer
connectors.
Priorities when dealing with a number of faults:
–DF012 Sensor supply voltage no. 2 if it is present or stored.
IMPORTANT
If the EGR valve needs to be replaced to resolve the fault, use command SC036
Reinitialise programming and select EGR valve to reinitialise the EGR valve offsets
(see Replacement of components).
WARNING
This fault may appear if the wiring harness has been damaged.
Follow the procedure described in the Wiring Check in the Introduction.
This check enables the condition and the conformity of the engine wiring harness to be checked.
CO.0
NOTESNone.
Check the EGR valve connections.
Check the injection computer connections.
Repair if necessary.
AFTER REPAIRDeal with any faults.
Carry out a road test followed by another check with the diagnostic tool.
EDC16_V51_DF209
Page 246 of 273

DIESEL INJECTION
Fault finding – Test13B
13B -246V3 MR-372-J84-13B250$900.mif
EDC16
PROGRAM No.: C1
Vdiag No.: 51
* OCR = Opening Cycle Ratio.
TEST4 Air flowmeter
POLLUTION OF THE GRILLES:
Visual inspection: remove the flowmeter. There should be no foreign bodies in the grilles (see illustration on the
next page).
Do not clean the grilles using compressed air or any other procedure: this damages the sensors and
creates variations from the values displayed on the CLIP tool.
Check the sealing of the air circuit upstream of the air flowmeter:
disconnected or pierced pipes and air filter unit, seals present.
Replace the air flowmeter if necessary and clean upstream of this, if necessary.
ELECTRICAL COMPONENT BREAKAGE:
Visual inspection:
remove the flow sensor: the components must not be broken (see picture on following page).
Replace the air flowmeter if necessary.
OXIDATION OF THE ELECTRICAL COMPONENTS:
Visual inspection:
dismantle the air flowmeter, there should not be any green deposits on the electrical components.
Replace the air flowmeter if necessary.
CLOGGING OF THE AIR FLOWMETER:
Test:
–Check the values for conformity:
* During the first 5 seconds after starting:
–Coolant temperature: 80˚C,
–Engine speed: idle speed (800 ± 50 rpm);
–Measure the air flow: 47 kg/h ± 10.
–OCR* EGR valve: between - 10% and 0%.
* After the starting phase:
–Coolant temperature: 80˚C,
–Engine speed: idle speed (800 ± 50 rpm);
–Air flow measurement: 30 kg/h ± 5%;
–EGR valve OCR*: between 10% and 40%.
–Refer to DF056 Air flow sensor circuit 2.def, for the air flow sensor checks.
Replace the air flowmeter if necessary.
EDC16_V51_TEST4
Page 259 of 273
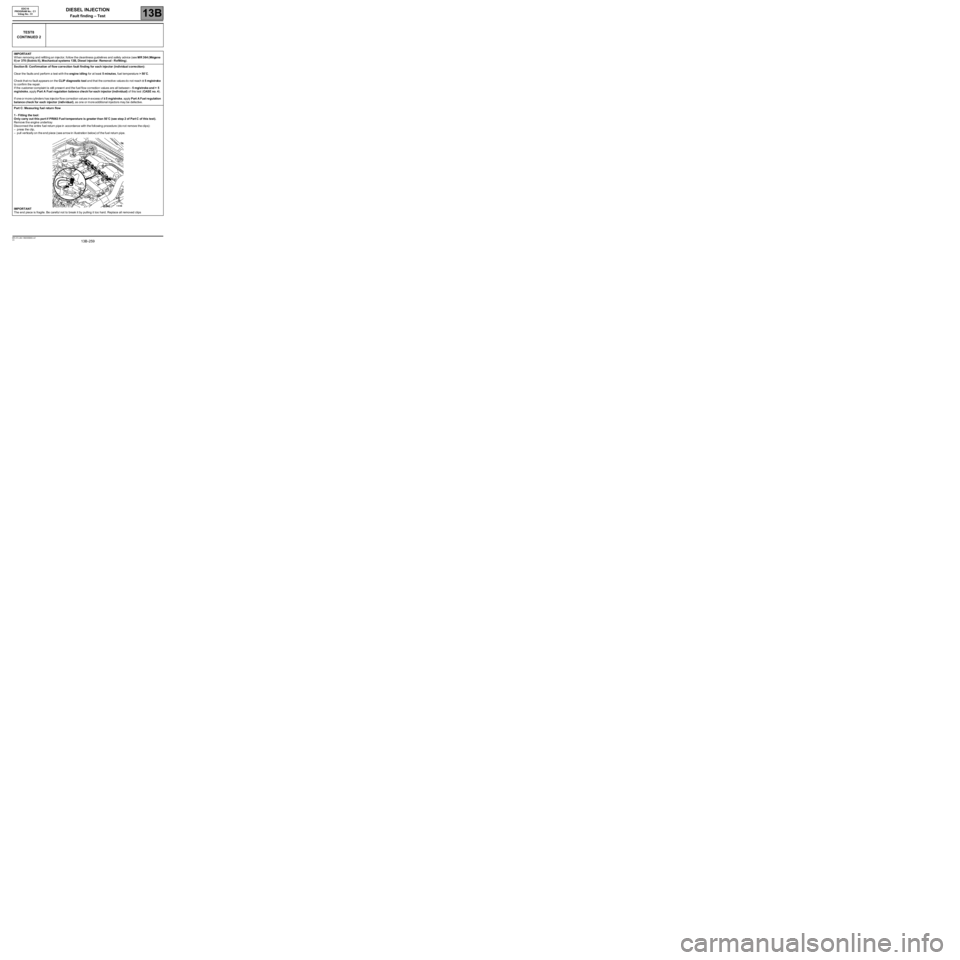
DIESEL INJECTION
Fault finding – Test13B
13B -259V3 MR-372-J84-13B250$900.mif
TEST8
CONTINUED 2
IMPORTA NT
When removing and refitting an injector, follow the cleanliness guidelines and safety advice (seeMR 364 (Mégane
II) or 370 (Scénic II), Mechanical systems 13B, Diesel injector: Removal - R efitting).
Section B: Conf irmation of flow corre ction fault finding for each inje ctor (individua l c orre ction):
Cle ar the faultsandperform a test wi th theengine idlingfor at l east5minutes,fueltemperature>50˚C.
Ch eck th at n o fault a p p e a r s o n t heCLIPdiagnostic tooland that the corrective values do not reach±5mg/stroke
to confirm therepair.
Ifthecustomer complaint is still present and the fuel flow correction values are all between-5mg/stroke a nd + 5
mg/strok e,applyPartAFuel regulation balanc e che ck f or each injector (individual)of this test (CAS Eno. 4).
If one or more cylinders has injector flow correction values in excess of±5 mg/stroke,applyPart AFuel re gulation
ba lance c heck for each inj e c t or(individu a l ),asoneormoreadditional injectors may be defective.
Part C: Measuring fuelreturnflow
1-Fitting the tool:
Only carryout this pa rt if PR063 Fuel t empera ture is greater t han 50˚C (see step 2 of Part C of this test).
Remove the engine undertray
Disco nnect the entire fuel return pipe in accordance with the foll owing procedure (do not remove the clips):
–pressthe clip ,
–pullvertically on the end piece ( see arrow in i llustration below) of the fuel return pipe.
IMPORTANT
The end piece is fragile. Be careful not to break it by pulling it too hard. Replace all removed clips
EDC16
PROGRAM No.: C1
Vdiag No.: 51
Page 270 of 273
DIESEL INJECTION
Fault finding – Test13B
13B -270V3 MR-372-J84-13B250$900.mif
EDC16
PROGRAM No.: C1
Vdiag No.: 51
Part 2: Fitting the tool:
Remove the engine undertray.
Disconnect the overpressure valve fuel return pipe according to the following procedure (do not remove the clips):
–press the clip,
–pull vertically on the end piece (1) of the fuel return pipe.
TEST11
CONTINUED 1
IMPORTANT
The end piece is fragile. Be careful not to break it by pulling it too hard. Replace