Page 72 of 128
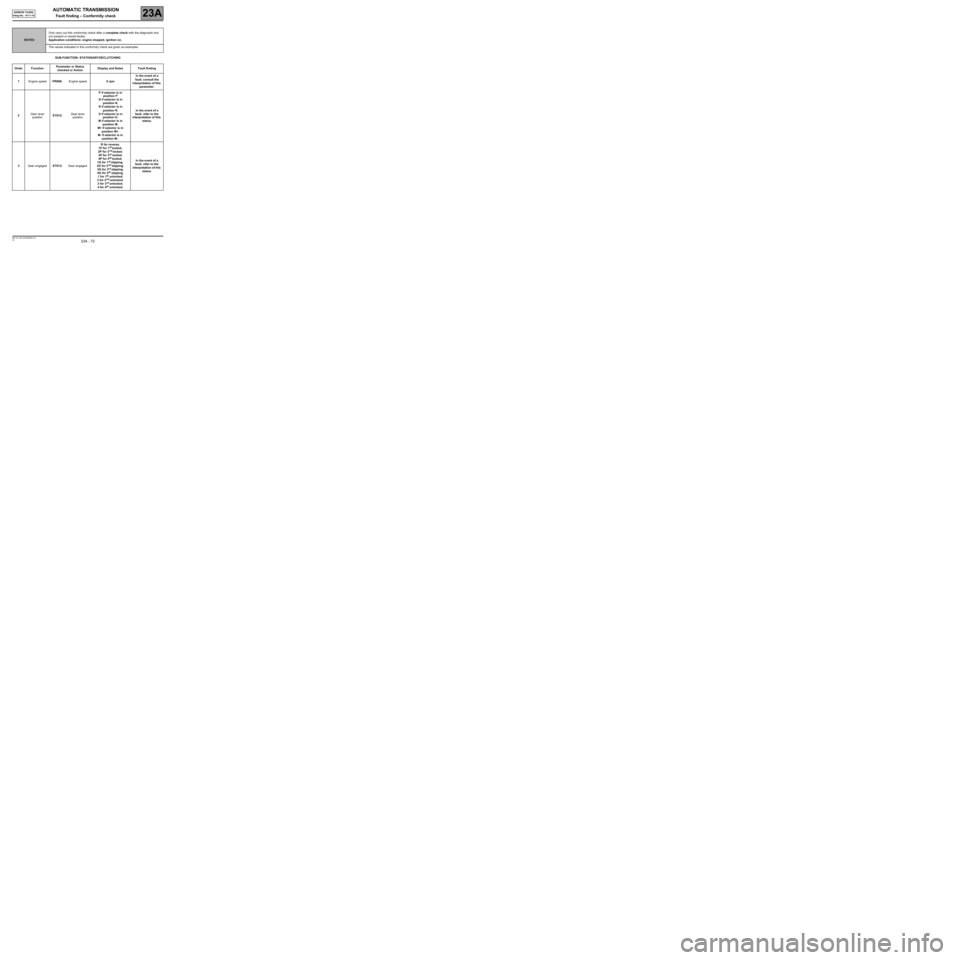
AUTOMATIC TRANSMISSION
Fault finding – Conformity check23A
23A - 72V4 MR-372-J84-23A050$462.mif
SIEMENS TA2000
Vdiag No.: 10-11-15
SUB-FUNCTION: STATIONARY DECLUTCHING
NOTESOnly carry out this conformity check after a complete check with the diagnostic tool
(no present or stored faults).
Application conditions: engine stopped, ignition on.
The values indicated in this conformity check are given as examples.
Order FunctionParameter or Status
checked or ActionDisplay and Notes Fault finding
1Engine speedPR006:Engine speed0 rpmIn the event of a
fault, consult the
interpretation of this
parameter.
2Gear lever
positionET012:Gear lever
positionP if selector is in
position P
N if selector is in
position N.
R if selector is in
position R.
D if selector is in
position D.
M if selector is in
position M.
M+ if selector is in
position M+.
M- if selector is in
position M-.In the event of a
fault, refer to the
interpretation of this
status.
3Gear engagedET013:Gear engagedR for reverse.
1P for 1
st locked.
2P for 2nd locked.
3P for 3rd locked.
4P for 4th locked.
1G for 1st slipping.
2G for 2nd slipping.
3G for 3rd slipping.
4G for 4th slipping.
1 for 1st unlocked.
2 for 2nd unlocked.
3 for 3rd unlocked.
4 for 4th unlocked.In the event of a
fault, refer to the
interpretation of this
status.
Page 73 of 128
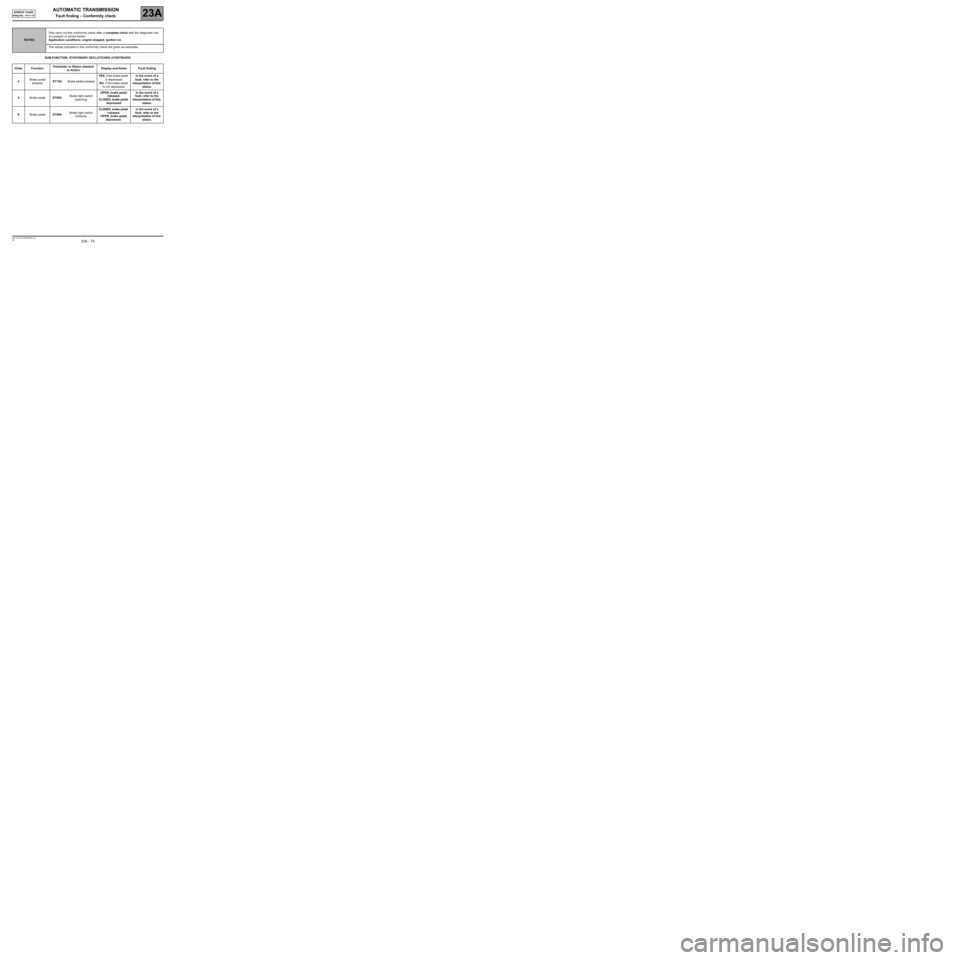
AUTOMATIC TRANSMISSION
Fault finding – Conformity check23A
23A - 73V4 MR-372-J84-23A050$462.mif
SIEMENS TA2000
Vdiag No.: 10-11-15
SUB-FUNCTION: STATIONARY DECLUTCHING (CONTINUED)
NOTESOnly carry out this conformity check after a complete check with the diagnostic tool
(no present or stored faults).
Application conditions: engine stopped, ignition on.
The values indicated in this conformity check are given as examples.
Order FunctionParameter or Status checked
or ActionDisplay and Notes Fault finding
4Brake pedal
pressedET142:Brake pedal pressedYES, if the brake pedal
is depressed
NO, if the brake pedal
is not depressedIn the event of a
fault, refer to the
interpretation of this
status.
5Brake pedalET003:Brake light switch
(opening)OPEN, brake pedal
released.
CLOSED, brake pedal
depressedIn the event of a
fault, refer to the
interpretation of this
status.
6Brake pedalET004:Brake light switch
(closure)CLOSED, brake pedal
released.
OPEN, brake pedal
depressed.In the event of a
fault, refer to the
interpretation of this
status.
Page 74 of 128
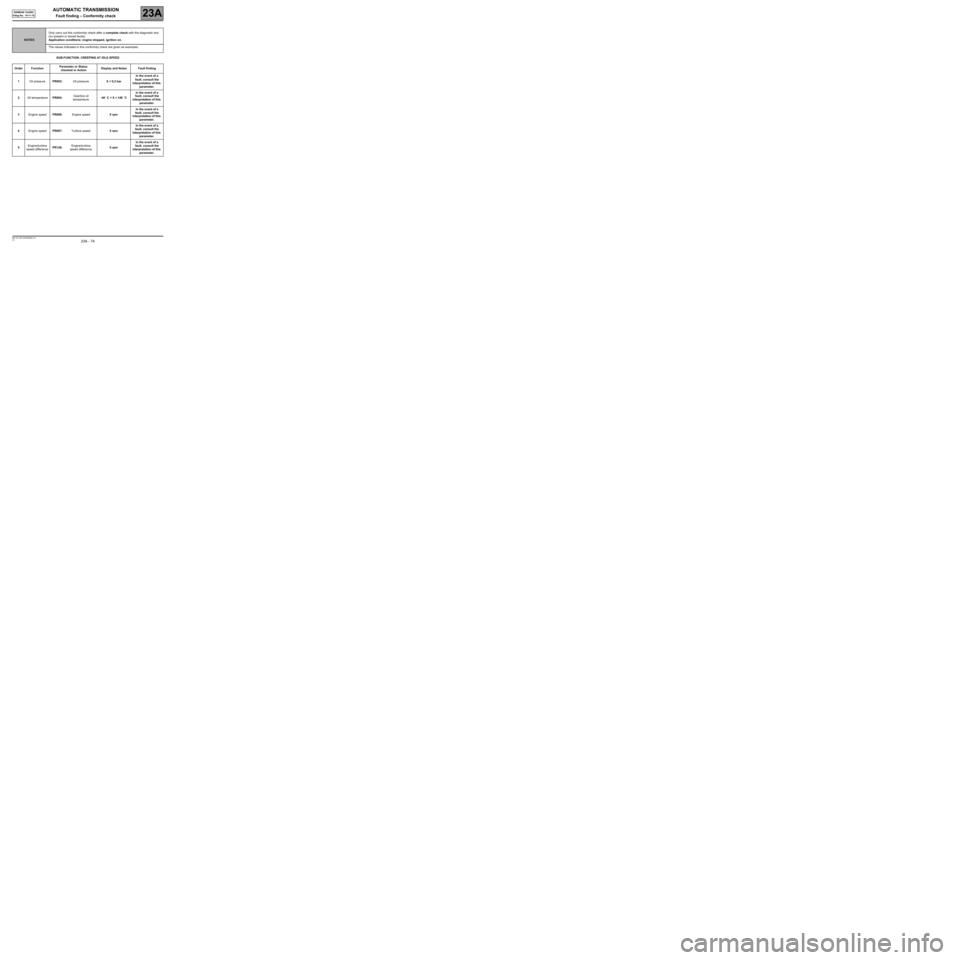
AUTOMATIC TRANSMISSION
Fault finding – Conformity check23A
23A - 74V4 MR-372-J84-23A050$462.mif
SIEMENS TA2000
Vdiag No.: 10-11-15
SUB-FUNCTION: CREEPING AT IDLE SPEED
NOTESOnly carry out this conformity check after a complete check with the diagnostic tool
(no present or stored faults).
Application conditions: engine stopped, ignition on.
The values indicated in this conformity check are given as examples.
Order FunctionParameter or Status
checked or ActionDisplay and Notes Fault finding
1Oil pressurePR003:Oil pressureX < 0.2 barIn the event of a
fault, consult the
interpretation of this
parameter.
2Oil temperaturePR004:Gearbox oil
temperature-40 ˚C < X < 140 ˚C In the event of a
fault, consult the
interpretation of this
parameter.
3Engine speedPR006:Engine speed0 rpmIn the event of a
fault, consult the
interpretation of this
parameter.
4Engine speedPR007:Turbine speed0 rpmIn the event of a
fault, consult the
interpretation of this
parameter.
5Engine/turbine
speed differencePR128:Engine/turbine
speed difference0 rpmIn the event of a
fault, consult the
interpretation of this
parameter.
Page 75 of 128
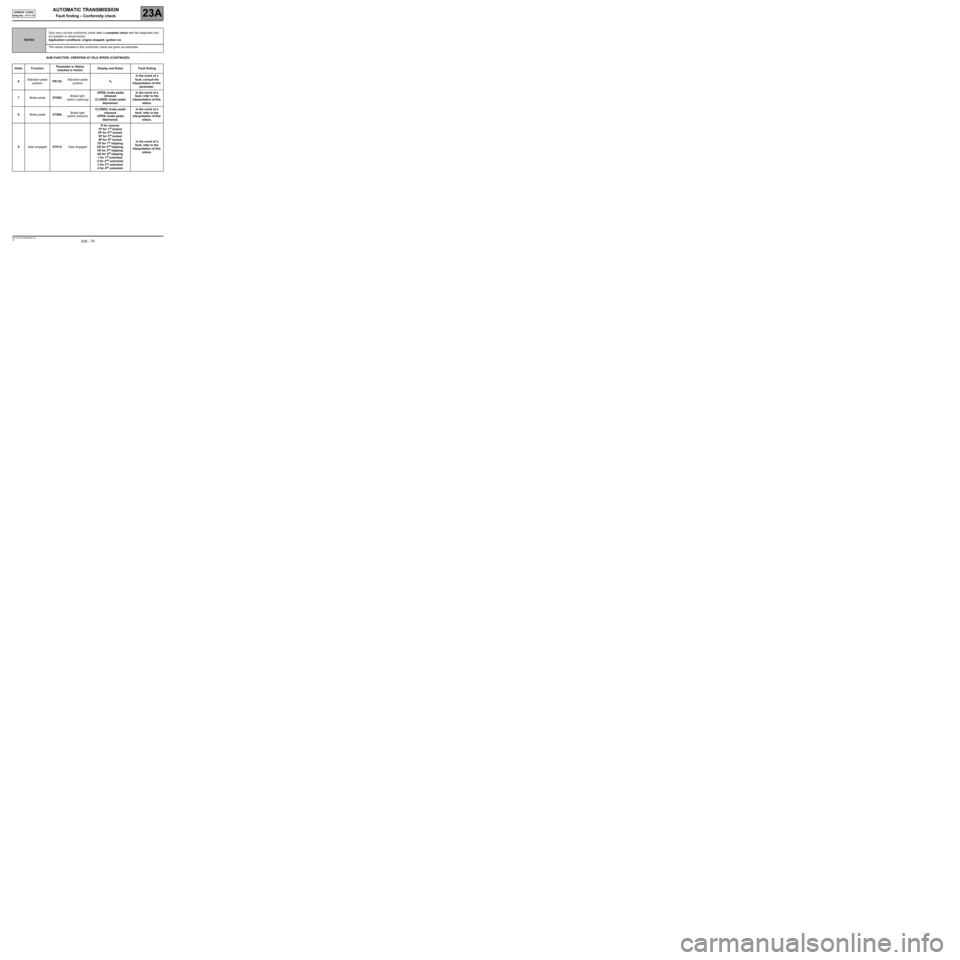
AUTOMATIC TRANSMISSION
Fault finding – Conformity check23A
23A - 75V4 MR-372-J84-23A050$462.mif
SIEMENS TA2000
Vdiag No.: 10-11-15
SUB-FUNCTION: CREEPING AT IDLE SPEED (CONTINUED)
NOTESOnly carry out this conformity check after a complete check with the diagnostic tool
(no present or stored faults).
Application conditions: engine stopped, ignition on.
The values indicated in this conformity check are given as examples.
Order FunctionParameter or Status
checked or ActionDisplay and Notes Fault finding
6Standard pedal
positionPR135:Standard pedal
position% In the event of a
fault, consult the
interpretation of this
parameter.
7Brake pedalET003:Brake light
switch (opening)OPEN, brake pedal
released.
CLOSED, brake pedal
depressed.In the event of a
fault, refer to the
interpretation of this
status.
8Brake pedalET004:Brake light
switch (closure)CLOSED, brake pedal
released.
OPEN, brake pedal
depressed.In the event of a
fault, refer to the
interpretation of this
status.
9Gear engagedET013:Gear engagedR for reverse.
1P for 1
st locked.
2P for 2nd locked.
3P for 3rd locked.
4P for 4th locked.
1G for 1st slipping.
2G for 2nd slipping.
3G for 3rd slipping.
4G for 4th slipping.
1 for 1st unlocked.
2 for 2nd unlocked.
3 for 3rd unlocked.
4 for 4th unlocked.In the event of a
fault, refer to the
interpretation of this
status.
Page 84 of 128
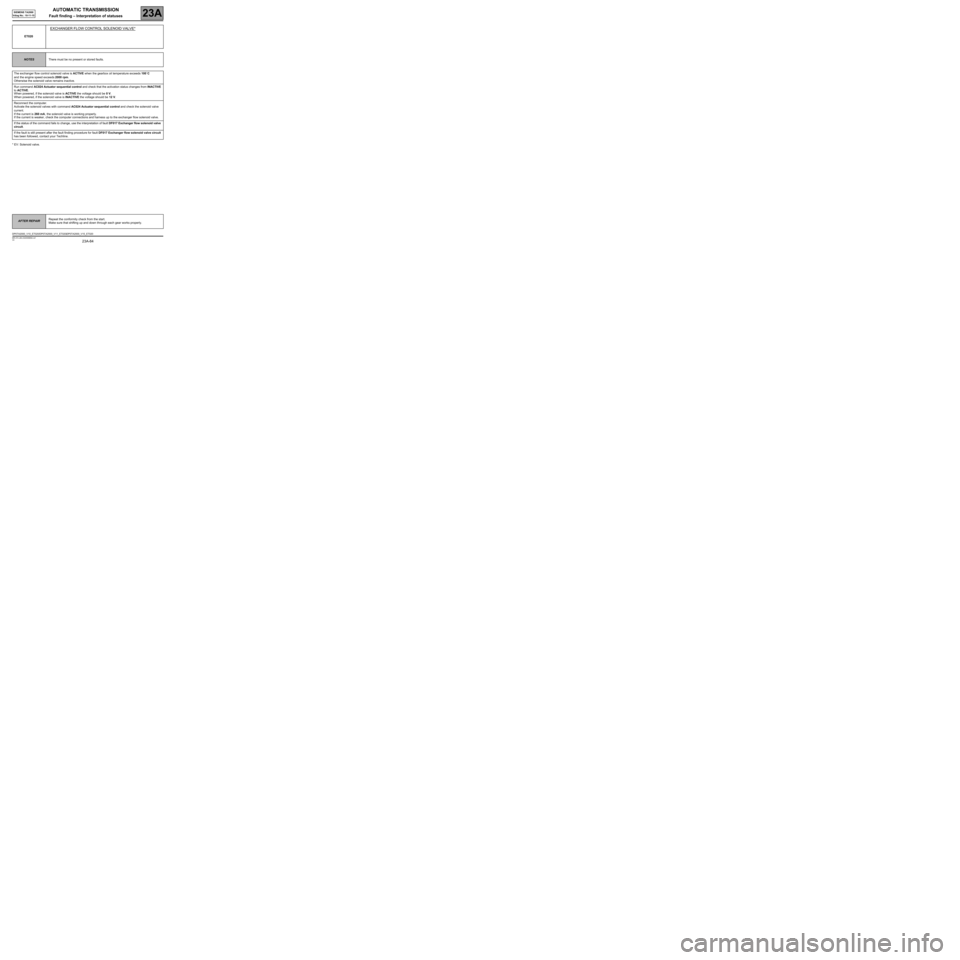
AUTOMATIC TRANSMISSION
Fault finding – Interpretation of statuses23A
23A-84V4 MR-372-J84-23A050$594.mif
SIEMENS TA2000
Vdiag No.: 10-11-15
* EV: Solenoid valve.ET020
EXCHANGER FLOW CONTROL SOLENOID VALVE*
NOTESThere must be no present or stored faults.
The exchanger flow control solenoid valve is ACTIVE when the gearbox oil temperature exceeds 100˚C
and the engine speed exceeds 2000 rpm.
Otherwise the solenoid valve remains inactive.
Run command AC024 Actuator sequential control and check that the activation status changes from INACTIVE
to ACTIVE.
When powered, if the solenoid valve is ACTIVE the voltage should be 0 V.
When powered, if the solenoid valve is INACTIVE the voltage should be 12 V.
Reconnect the computer.
Activate the solenoid valves with command AC024 Actuator sequential control and check the solenoid valve
current.
If the current is 260 mA, the solenoid valve is working properly.
If the current is weaker, check the computer connections and harness up to the exchanger flow solenoid valve.
If the status of the command fails to change, use the interpretation of fault DF017 Exchanger flow solenoid valve
circuit.
If the fault is still present after the fault finding procedure for fault DF017 Exchanger flow solenoid valve circuit
has been followed, contact your Techline.
AFTER REPAIRRepeat the conformity check from the start.
Make sure that shifting up and down through each gear works properly.
DP0TA2000_V10_ET020/DP0TA2000_V11_ET020/DP0TA2000_V15_ET020
Page 103 of 128
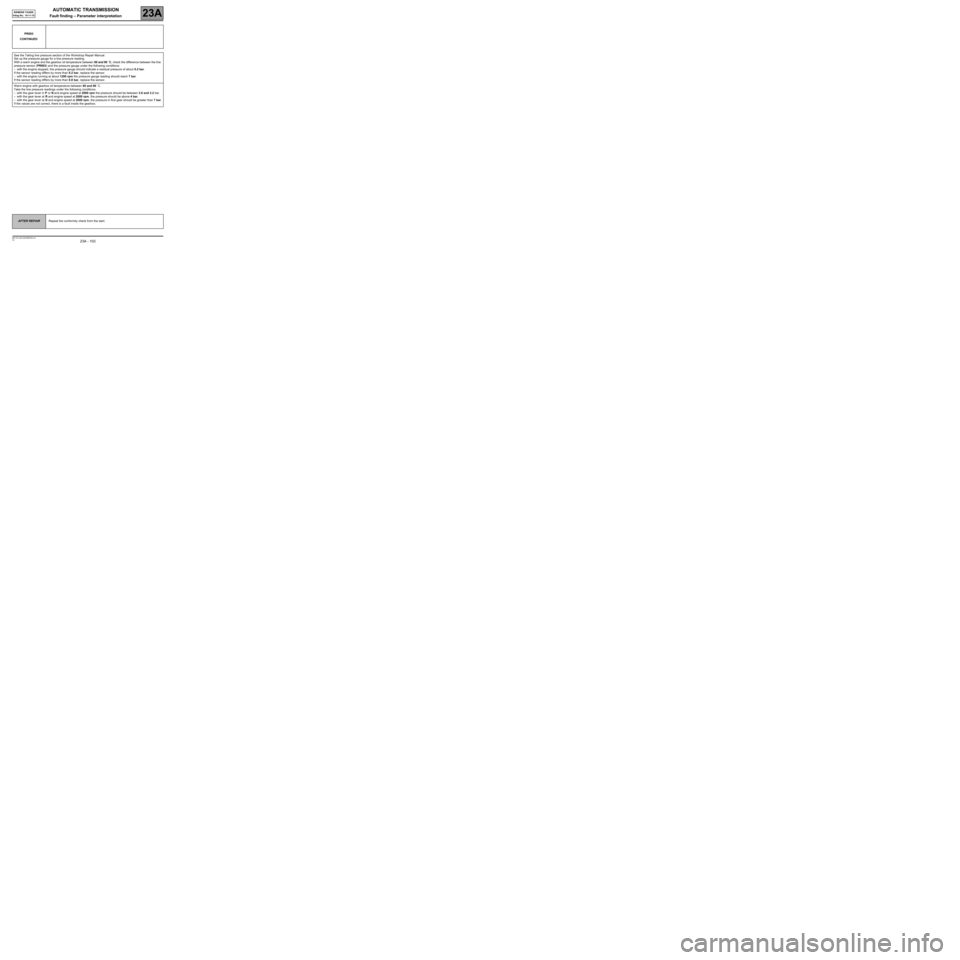
AUTOMATIC TRANSMISSION
Fault finding – Parameter interpretation23A
23A - 103V4 MR-372-J84-23A050$726.mif
SIEMENS TA2000
Vdiag No.: 10-11-15
PR003
CONTINUED
See the Taking line pressure section of the Workshop Repair Manual.
Set up the pressure gauge for a line pressure reading.
With a warm engine and the gearbox oil temperature between 60 and 80 ˚C, check the difference between the line
pressure sensor (PR003) and the pressure gauge under the following conditions:
–with the engine stopped, the pressure gauge should indicate a residual pressure of about 0.2 bar.
If the sensor reading differs by more than 0.2 bar, replace the sensor.
–with the engine running at about 1200 rpm the pressure gauge reading should reach 7 bar.
If the sensor reading differs by more than 0.8 bar, replace the sensor.
Warm engine with gearbox oil temperature between 60 and 80 ˚C.
Take the line pressure readings under the following conditions:
–with the gear lever in P or N and engine speed at 2000 rpm the pressure should be between 2.6 and 3.2 bar.
–with the gear lever at R and engine speed at 2000 rpm, the pressure should be above 4 bar.
–with the gear lever at D and engine speed at 2000 rpm, the pressure in first gear should be greater than 7 bar.
If the values are not correct, there is a fault inside the gearbox.
AFTER REPAIRRepeat the conformity check from the start.
Page 107 of 128
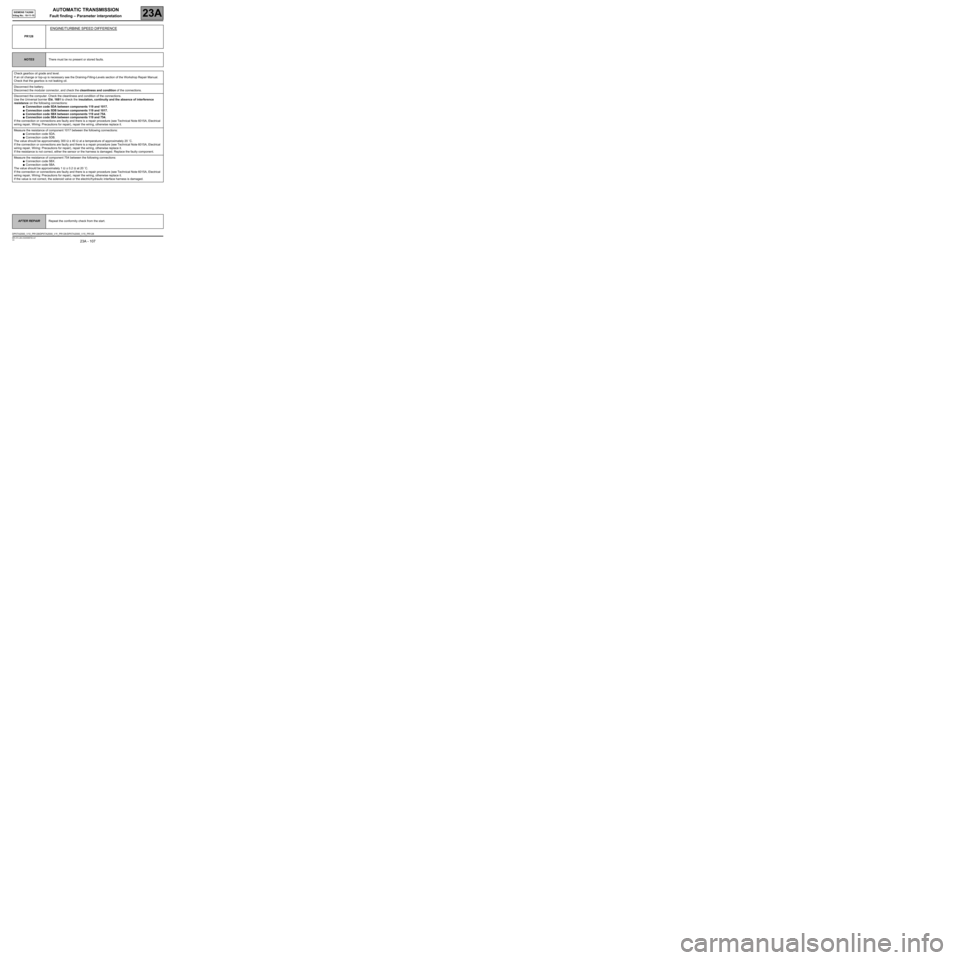
AUTOMATIC TRANSMISSION
Fault finding – Parameter interpretation23A
23A - 107V4 MR-372-J84-23A050$726.mif
SIEMENS TA2000
Vdiag No.: 10-11-15
PR128
ENGINE/TURBINE SPEED DIFFERENCE
NOTESThere must be no present or stored faults.
Check gearbox oil grade and level.
If an oil change or top-up is necessary see the Draining-Filling-Levels section of the Workshop Repair Manual.
Check that the gearbox is not leaking oil.
Disconnect the battery.
Disconnect the modular connector, and check the cleanliness and condition of the connections.
Disconnect the computer. Check the cleanliness and condition of the connections.
Use the Universal bornier Elé. 1681 to check the insulation, continuity and the absence of interference
resistance on the following connections:
●Connection code 5DA between components 119 and 1017.
●Connection code 5DB between components 119 and 1017.
●Connection code 5BX between components 119 and 754.
●Connection code 5BA between components 119 and 754.
If the connection or connections are faulty and there is a repair procedure (see Technical Note 6015A, Electrical
wiring repair, Wiring: Precautions for repair), repair the wiring, otherwise replace it.
Measure the resistance of component 1017 between the following connections:
●Connection code 5DA.
●Connection code 5DB.
The value should be approximately 300 Ω ± 40 Ω at a temperature of approximately 20 ˚C.
If the connection or connections are faulty and there is a repair procedure (see Technical Note 6015A, Electrical
wiring repair, Wiring: Precautions for repair), repair the wiring, otherwise replace it.
If the resistance is not correct, either the sensor or the harness is damaged. Replace the faulty component.
Measure the resistance of component 754 between the following connections:
●Connection code 5BX.
●Connection code 5BA.
The value should be approximately 1 Ω ± 0.2 Ω at 20 ˚C.
If the connection or connections are faulty and there is a repair procedure (see Technical Note 6015A, Electrical
wiring repair, Wiring: Precautions for repair), repair the wiring, otherwise replace it.
If the value is not correct, the solenoid valve or the electric/hydraulic interface harness is damaged.
AFTER REPAIRRepeat the conformity check from the start.
DP0TA2000_V10_PR128/DP0TA2000_V11_PR128 /DP0TA2000_V15_PR128
Page 108 of 128
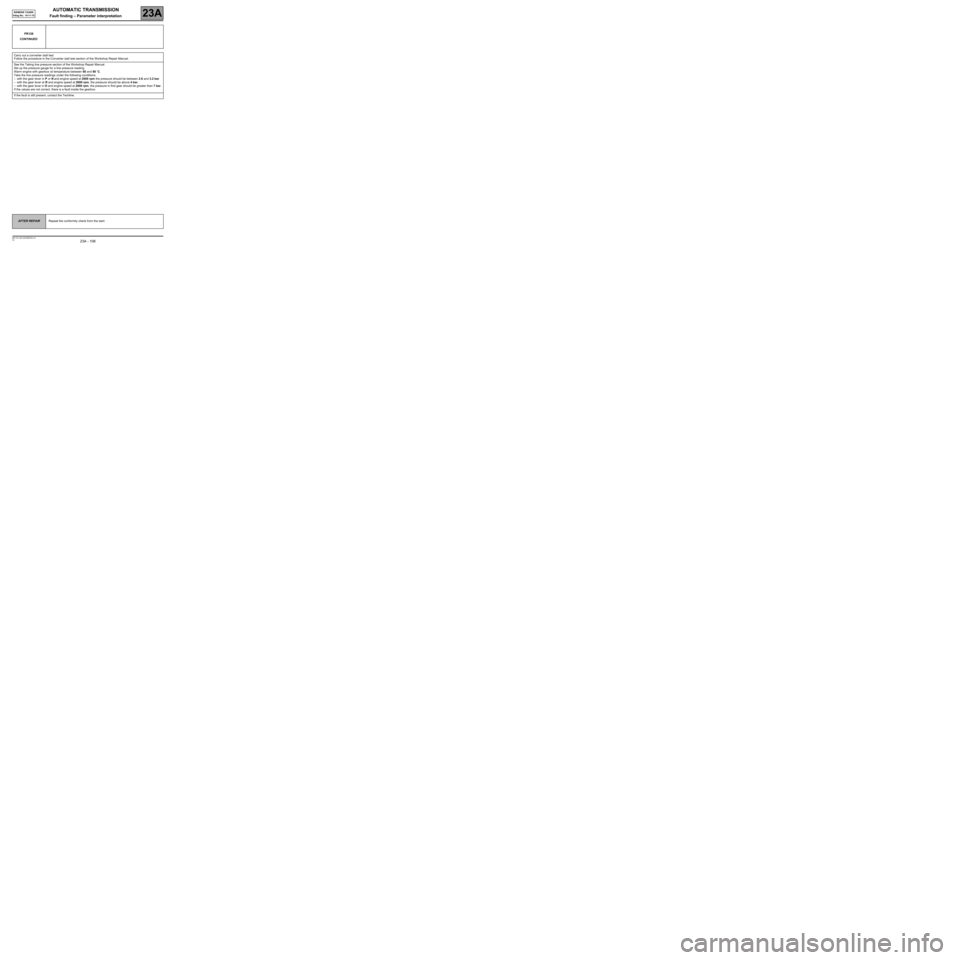
AUTOMATIC TRANSMISSION
Fault finding – Parameter interpretation23A
23A - 108V4 MR-372-J84-23A050$726.mif
SIEMENS TA2000
Vdiag No.: 10-11-15
PR128
CONTINUED
Carry out a converter stall test.
Follow the procedure in the Converter stall test section of the Workshop Repair Manual.
See the Taking line pressure section of the Workshop Repair Manual.
Set up the pressure gauge for a line pressure reading.
Warm engine with gearbox oil temperature between 60 and 80 ˚C.
Take the line pressure readings under the following conditions:
–with the gear lever in P or N and engine speed at 2000 rpm the pressure should be between 2.6 and 3.2 bar.
–with the gear lever at R and engine speed at 2000 rpm, the pressure should be above 4 bar.
–with the gear lever in D and engine speed at 2000 rpm, the pressure in first gear should be greater than 7 bar.
If the values are not correct, there is a fault inside the gearbox.
If the fault is still present, contact the Techline.
AFTER REPAIRRepeat the conformity check from the start.