Page 23 of 392
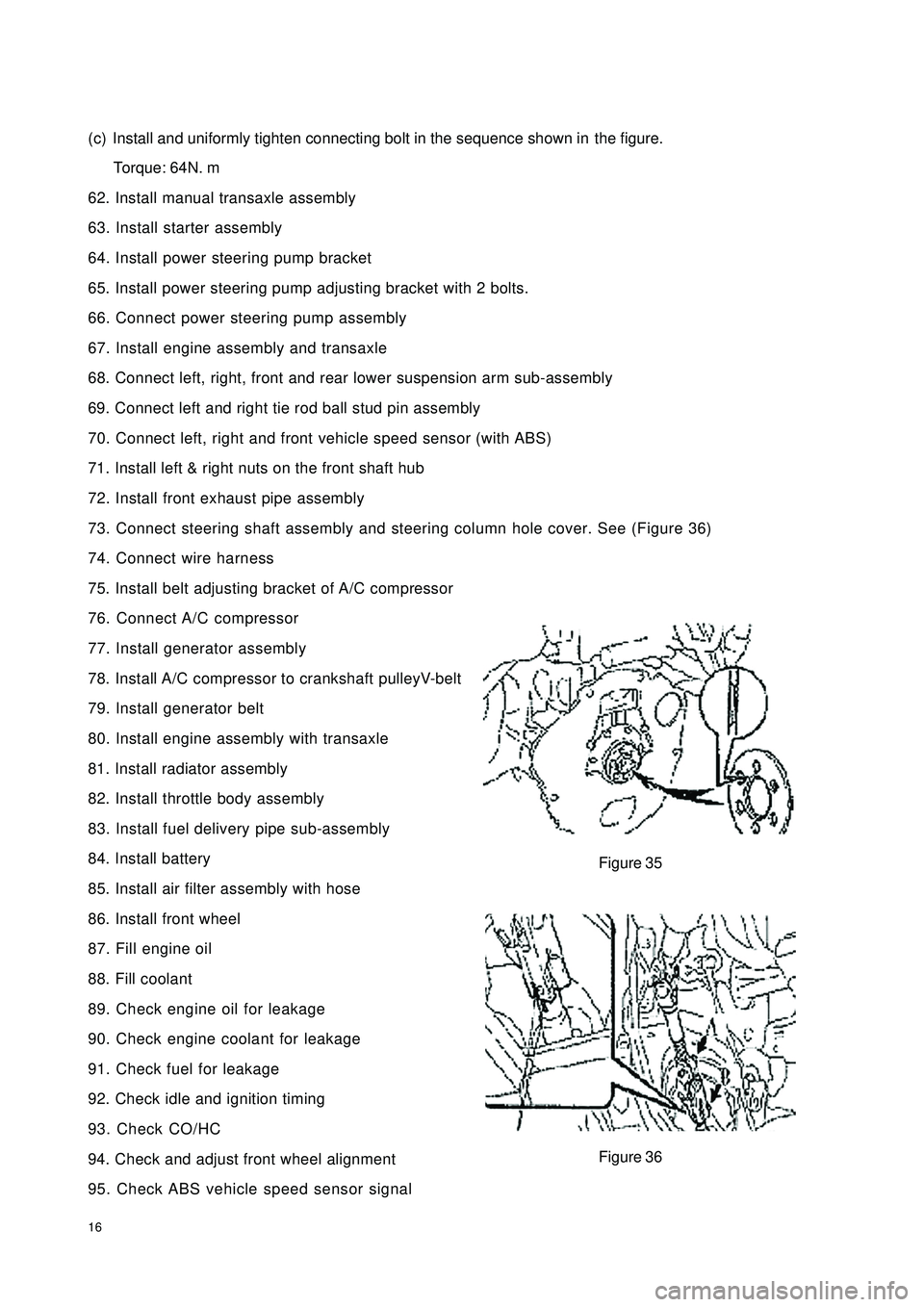
16(c) Install and uniformly tighten connecting bolt in the sequence shown inthe figure.
Torque: 64N. m
62. Install manual transaxle assembly
63. Install starter assembly
64. Install power steering pump bracket
65. Install power steering pump adjusting bracket with 2 bolts.
66. Connect power steering pump assembly
67. Install engine assembly and transaxle
68. Connect left, right, front and rear lower suspension arm sub-assembly
69. Connect left and right tie rod ball stud pin assembly
70. Connect left, right and front vehicle speed sensor (with ABS)
71. Install left & right nuts on the front shaft hub
72. Install front exhaust pipe assembly
73. Connect steering shaft assembly and steering column hole cover. See (Figure 36)
74. Connect wire harness
75. Install belt adjusting bracket of A/C compressor
76. Connect A/C compressor
77. Install generator assembly
78. Install A/C compressor to crankshaft pulleyV-belt
79. Install generator belt
80. Install engine assembly with transaxle
81. Install radiator assembly
82. Install throttle body assembly
83. Install fuel delivery pipe sub-assembly
84. Install battery
85. Install air filter assembly with hose
86. Install front wheel
87. Fill engine oil
88. Fill coolant
89. Check engine oil for leakage
90. Check engine coolant for leakage
91. Check fuel for leakage
92. Check idle and ignition timing
93. Check CO/HC
94. Check and adjust front wheel alignment
95. Check ABS vehicle speed sensor signalFigure 35
Figure 36
Page 42 of 392
35Chapter 3 Lubrication System
(MR479Q, MR479QA, MR481QA)Section 1 Oil Pressure Gage Sensor Replacement1. Check oil level
Warm up the engine. Check the dipstick to ensure oil level between "L" and "F" after engine stopped
5 minutes. Check for leakage if it is too low. Fill oil to "F.
2. Check oil for deterioration. Water entry, discolor and dilution. Replace oil if it is obviously
deteriorated.
3. Detach oil pressure sensor assembly. See (Figure 80)
4. Install oil pressure gage sensor. See (Figure 81) Start engine to
normal operation temperature.
5. Check for oil pressure
6. Smear adhesive on 2 or 3 threads of the oil pressure sensor.
Install oil pressure sensor. See (Figure 82)
Figure 81
Figure 82Figure 80
Page 53 of 392
461. Avoid fuel ejection
2. Disconnect fuel tank hose
3. Disconnect fuel tank return hose
4. Disconnect fuel tank gas exhaust hose
5. Detach fuel pump assembly with filter screen. See (Figure 103)
Using special tool, loose fuel tank cap. Be careful not to bend the fuel
level sensor arm when pulling out fuel pump.
6. Install fuel pump assembly. See (Figure 104). Replace ring seal .
Align the tab on the fuel pump to the notch on the fuel tank port. Tighten
the fuel tank cap with special tool.
Torque: 40N. m
7. Install fuel gas exhaust hose
(a) Install return hose;
(b) Install fuel hose;
(c) Check fuel for leakage.Figure 103
Figure 104New Washer
Page 60 of 392
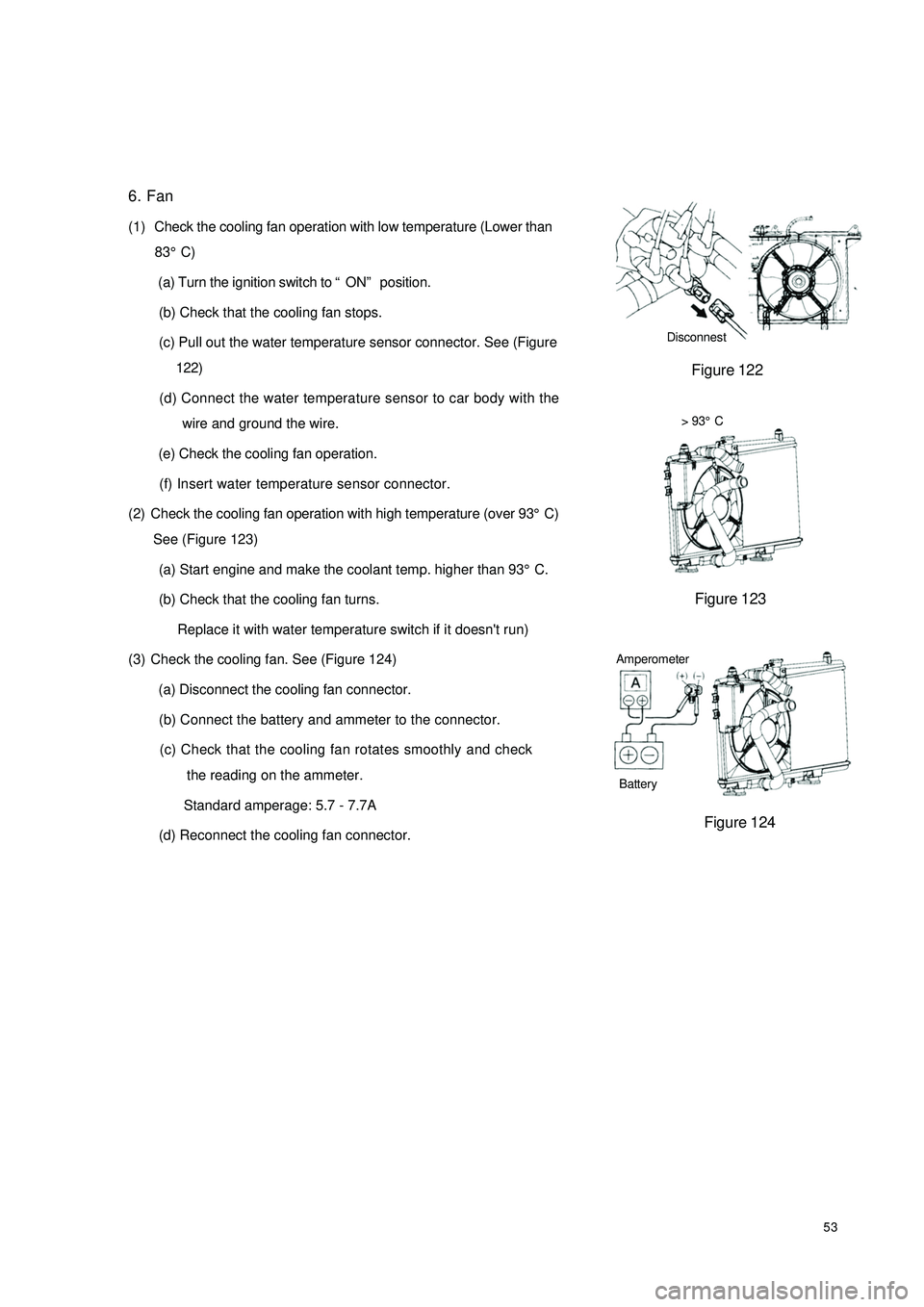
536. Fan
(1) Check the cooling fan operation with low temperature (Lower than
83°C)
(a) Turn the ignition switch to “ON” position.
(b) Check that the cooling fan stops.
(c) Pull out the water temperature sensor connector. See (Figure
122)
(d) Connect the water temperature sensor to car body with the
wire and ground the wire.
(e) Check the cooling fan operation.
(f) Insert water temperature sensor connector.> 93°C
See (Figure 123)
(a) Start engine and make the coolant temp. higher than 93°C.
(b) Check that the cooling fan turns.
Replace it with water temperature switch if it doesn't run)
(3) Check the cooling fan. See (Figure 124)
(a) Disconnect the cooling fan connector.
(b) Connect the battery and ammeter to the connector.
(c) Check that the cooling fan rotates smoothly and check
the reading on the ammeter.
Standard amperage: 5.7 - 7.7A
(d) Reconnect the cooling fan connector.Disconnest
Figure 123
Figure 124 Figure 122
(2) Check the cooling fan operation with high temperature (over 93°C)Battery Amperometer
Page 67 of 392
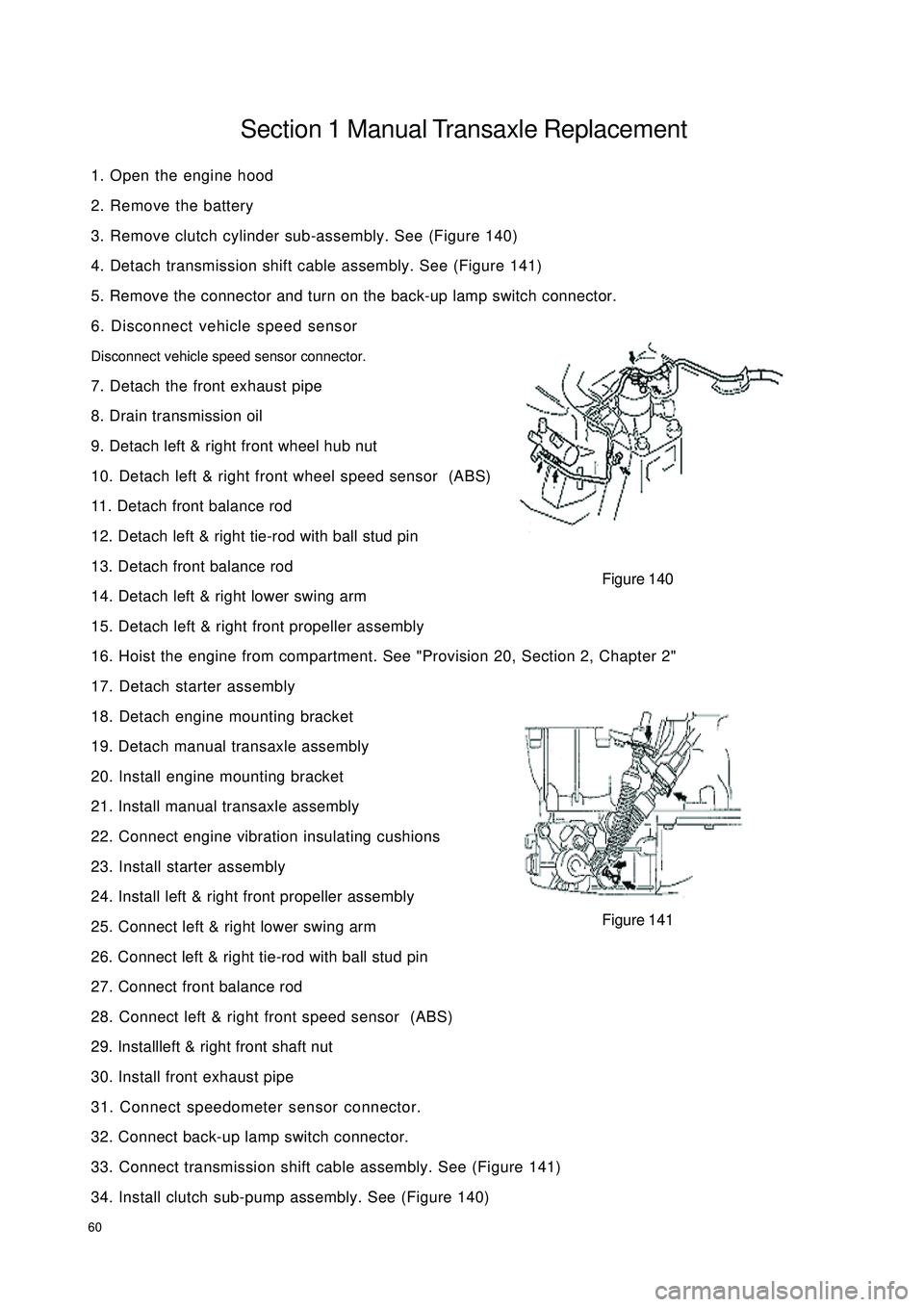
60Section 1 Manual Transaxle Replacement1. Open the engine hood
2. Remove the battery
3. Remove clutch cylinder sub-assembly. See (Figure 140)
4. Detach transmission shift cable assembly. See (Figure 141)
5. Remove the connector and turn on the back-up lamp switch connector.
6. Disconnect vehicle speed sensor
Disconnect vehicle speed sensor connector.
7. Detach the front exhaust pipe
8. Drain transmission oil
9. Detach left & right front wheel hub nut
10. Detach left & right front wheel speed sensor (ABS)
11. Detach front balance rod
12. Detach left & right tie-rod with ball stud pin
13. Detach front balance rod
14. Detach left & right lower swing arm
15. Detach left & right front propeller assembly
16. Hoist the engine from compartment. See "Provision 20, Section 2, Chapter 2"
17. Detach starter assembly
18. Detach engine mounting bracket
19. Detach manual transaxle assembly
20. Install engine mounting bracket
21. Install manual transaxle assembly
22. Connect engine vibration insulating cushions
23. Install starter assembly
24. Install left & right front propeller assembly
25. Connect left & right lower swing arm
26. Connect left & right tie-rod with ball stud pin
27. Connect front balance rod
28. Connect left & right front speed sensor (ABS)
29. Installleft & right front shaft nut
30. Install front exhaust pipe
31. Connect speedometer sensor connector.
32. Connect back-up lamp switch connector.
33. Connect transmission shift cable assembly. See (Figure 141)
34. Install clutch sub-pump assembly. See (Figure 140)Figure 140
Figure 141
Page 68 of 392
61Section 2 Vehicle Speed Sensor Replacement1. Disconnect vehicle speed sensor. See (Figure 142)
2. Remove bolt and vehicle speed sensor.
3. Install vehicle speed sensor. See (Figure 142)
4. Connect vehicle speed sensor connector. See (Figure 143)
Figure 142 Figure 143
Page 71 of 392

64Chapter 9 General Engine Troubles and Their
TroubleshootingSection 1 Overview The wide application of the electronic technologies to the vehicles brings innovation on diagnosis of the
vehicle, many varieties of diagnosis instruments that are very effective and efficient for the vehicle diagnosis
are innovated. Once the fault occurs, the best choice is to go to service station for help. However, even the
most advanced instrument has its limit. For some faults, manual diagnosis is far more convenient and easier
than that of instrument. In case of the crack, distortion and leakage of the components, the manual diagnosis
is even superior to the instrument diagnosis. The faults occurred shall be carefully analyzed and troubleshot
in accordance with the repair manual for normal usage.Section 2 General Engine Fault and TroubleshootingI. Fuel pipeline and circuit fault causing the engine starting failureengine starting failure normally include: starter does not run or starter runs but fails to crank the engine, or
cranks the engine but cranks slowly; starter can crank but fail to start the engine. There are many causes that
result in starting failure, such as failures in starting system, ignition system, fuel injection system and engine
mechanical failure.
1. starter does not run or fails to crank the engine or cranks slowly
(1) Symptom: starter does not run or spongy rotation
(2) Causes:
b. Low battery voltage, excessive battery discharge, damaged generator or failure in charging circuit;
c. Battery terminal rust and backed out;
d. Failure in starting circuit, ECU can not receive STA signal;
e. Damaged starter.
2. engine can not start and crank
(1) Symptom
With the start switch on, starter can crank but fail to start the engine.
(2) Causes
a. Empty fuel tank;
b. Electrical fuel pump inoperative;
c. Injector inoperative;
d. Low fuel pressure;
e. Unreasonable starting operation;
f. Damaged throttle position sensor or no signal is sent to ECU due to the open in throttle position
sensor circuit;
Page 72 of 392
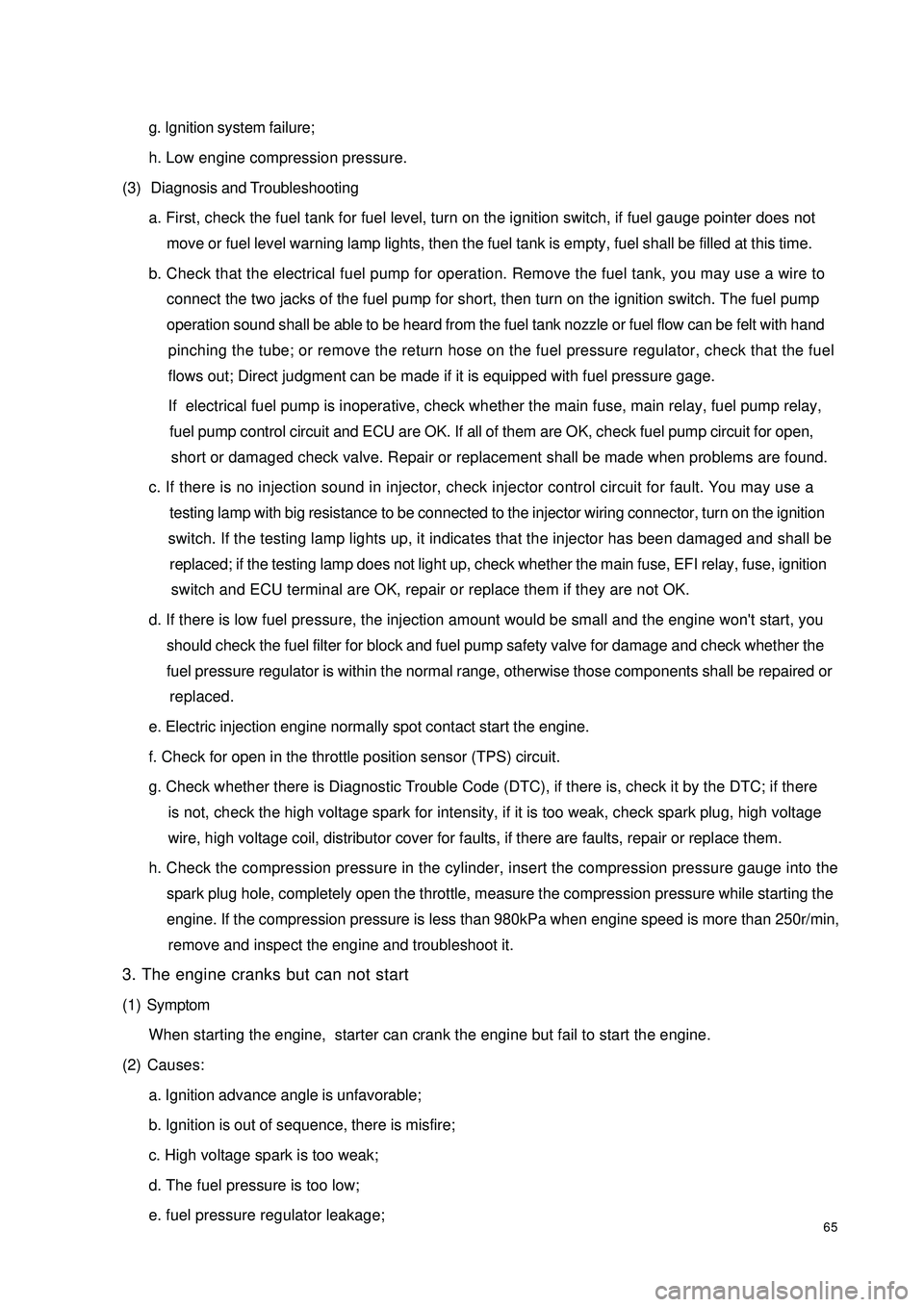
65g. Ignition system failure;
h. Low engine compression pressure.
(3) Diagnosis and Troubleshooting
a. First, check the fuel tank for fuel level, turn on the ignition switch, if fuel gauge pointer does not
move or fuel level warning lamp lights, then the fuel tank is empty, fuel shall be filled at this time.
b. Check that the electrical fuel pump for operation. Remove the fuel tank, you may use a wire to
connect the two jacks of the fuel pump for short, then turn on the ignition switch. The fuel pump
operation sound shall be able to be heard from the fuel tank nozzle or fuel flow can be felt with hand
pinching the tube; or remove the return hose on the fuel pressure regulator, check that the fuel
flows out; Direct judgment can be made if it is equipped with fuel pressure gage.
If electrical fuel pump is inoperative, check whether the main fuse, main relay, fuel pump relay,
fuel pump control circuit and ECU are OK. If all of them are OK, check fuel pump circuit for open,
short or damaged check valve. Repair or replacement shall be made when problems are found.
c. If there is no injection sound in injector, check injector control circuit for fault. You may use a
testing lamp with big resistance to be connected to the injector wiring connector, turn on the ignition
switch. If the testing lamp lights up, it indicates that the injector has been damaged and shall be
replaced; if the testing lamp does not light up, check whether the main fuse, EFI relay, fuse, ignition
switch and ECU terminal are OK, repair or replace them if they are not OK.
d. If there is low fuel pressure, the injection amount would be small and the engine won't start, you
should check the fuel filter for block and fuel pump safety valve for damage and check whether the
fuel pressure regulator is within the normal range, otherwise those components shall be repaired or
replaced.
e. Electric injection engine normally spot contact start the engine.
f. Check for open in the throttle position sensor (TPS) circuit.
g. Check whether there is Diagnostic Trouble Code (DTC), if there is, check it by the DTC; if there
is not, check the high voltage spark for intensity, if it is too weak, check spark plug, high voltage
wire, high voltage coil, distributor cover for faults, if there are faults, repair or replace them.
h. Check the compression pressure in the cylinder, insert the compression pressure gauge into the
spark plug hole, completely open the throttle, measure the compression pressure while starting the
engine. If the compression pressure is less than 980kPa when engine speed is more than 250r/min,
remove and inspect the engine and troubleshoot it.
3. The engine cranks but can not start
(1) Symptom
When starting the engine, starter can crank the engine but fail to start the engine.
(2) Causes:
a. Ignition advance angle is unfavorable;
b. Ignition is out of sequence, there is misfire;
c. High voltage spark is too weak;
d. The fuel pressure is too low;
e. fuel pressure regulator leakage;