Page 374 of 794
4 - 27
ENGCAMSHAFTS
6. Remove:
Clips
Exhaust camshaft 1
Intake camshaft 2
NOTE:
Attach a wire 3 to the timing chain to prevent
it from falling into the crankcase.
1
2
3
INSPECTION
Camshaft
1. Inspect:
Cam lobes
Pitting/scratches/blue discoloration →
Replace.
2. Measure:
Cam lobes length a and b
Out of specification → Replace.
Cam lobes length:
Intake:
a30.100 ~ 30.200 mm
(1.1850 ~ 1.1890 in)
: 30.000 mm
(1.1811 in)
b22.450 ~ 22.550 mm
(0.8839 ~ 0.8878 in)
: 22.350 mm
(0.8799 in)
Exhaust:
a30.200 ~ 30.300 mm
(1.1890 ~ 1.1929 in)
: 30.100 mm
(1.1850 in)
b22.450 ~ 22.550 mm
(0.8839 ~ 0.8878 in)
: 22.350 mm
(0.8799 in)
3. Measure:
Runout (camshaft)
Out of specification → Replace.
Runout (camshaft):
Less than 0.03 mm (0.0012 in)
Page 402 of 794
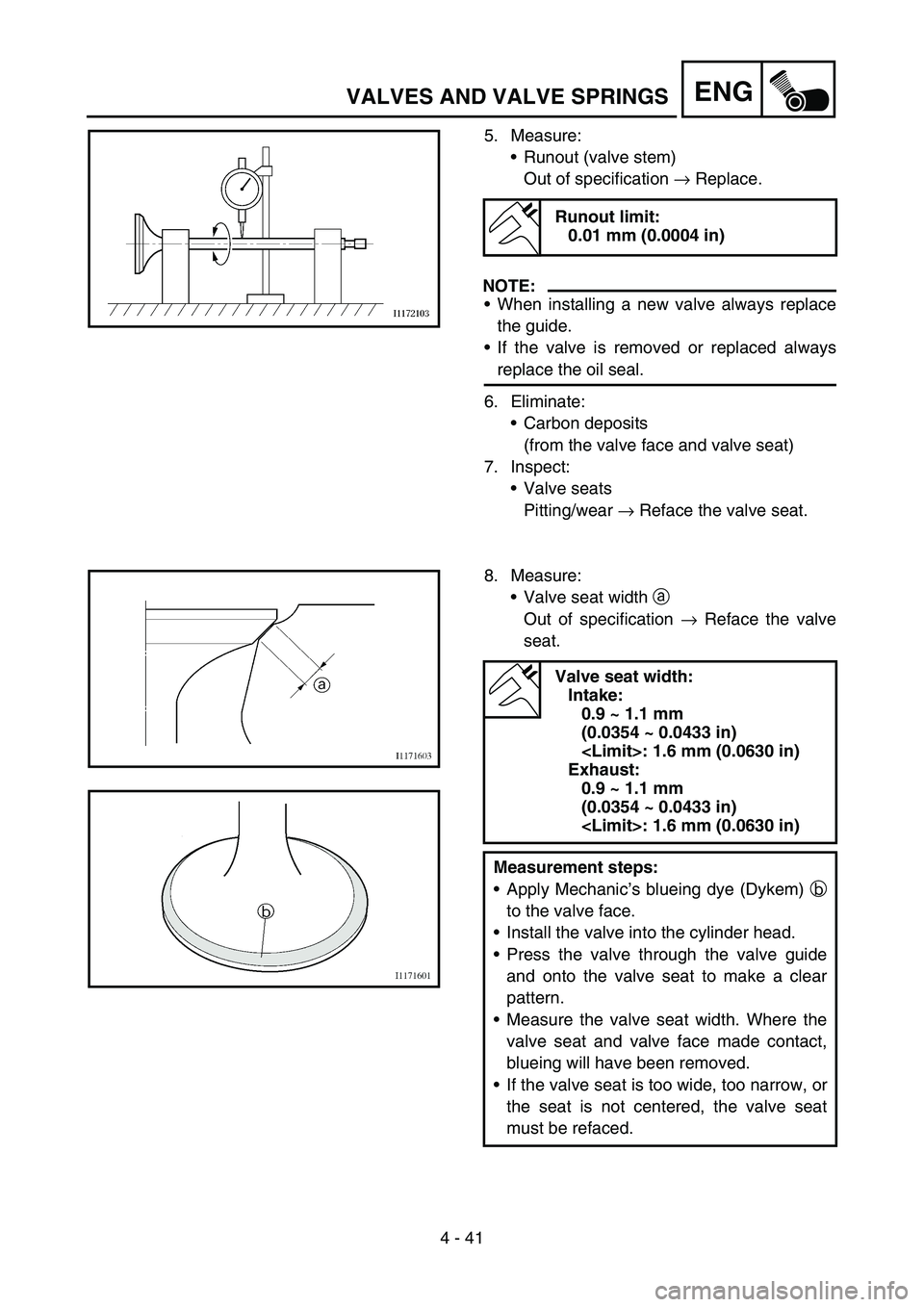
4 - 41
ENGVALVES AND VALVE SPRINGS
5. Measure:
Runout (valve stem)
Out of specification → Replace.
NOTE:
When installing a new valve always replace
the guide.
If the valve is removed or replaced always
replace the oil seal.
6. Eliminate:
Carbon deposits
(from the valve face and valve seat)
7. Inspect:
Valve seats
Pitting/wear → Reface the valve seat.
Runout limit:
0.01 mm (0.0004 in)
8. Measure:
Valve seat width a
Out of specification → Reface the valve
seat.
Valve seat width:
Intake:
0.9 ~ 1.1 mm
(0.0354 ~ 0.0433 in)
: 1.6 mm (0.0630 in)
Exhaust:
0.9 ~ 1.1 mm
(0.0354 ~ 0.0433 in)
: 1.6 mm (0.0630 in)
Measurement steps:
Apply Mechanic’s blueing dye (Dykem) b
to the valve face.
Install the valve into the cylinder head.
Press the valve through the valve guide
and onto the valve seat to make a clear
pattern.
Measure the valve seat width. Where the
valve seat and valve face made contact,
blueing will have been removed.
If the valve seat is too wide, too narrow, or
the seat is not centered, the valve seat
must be refaced.
Page 404 of 794
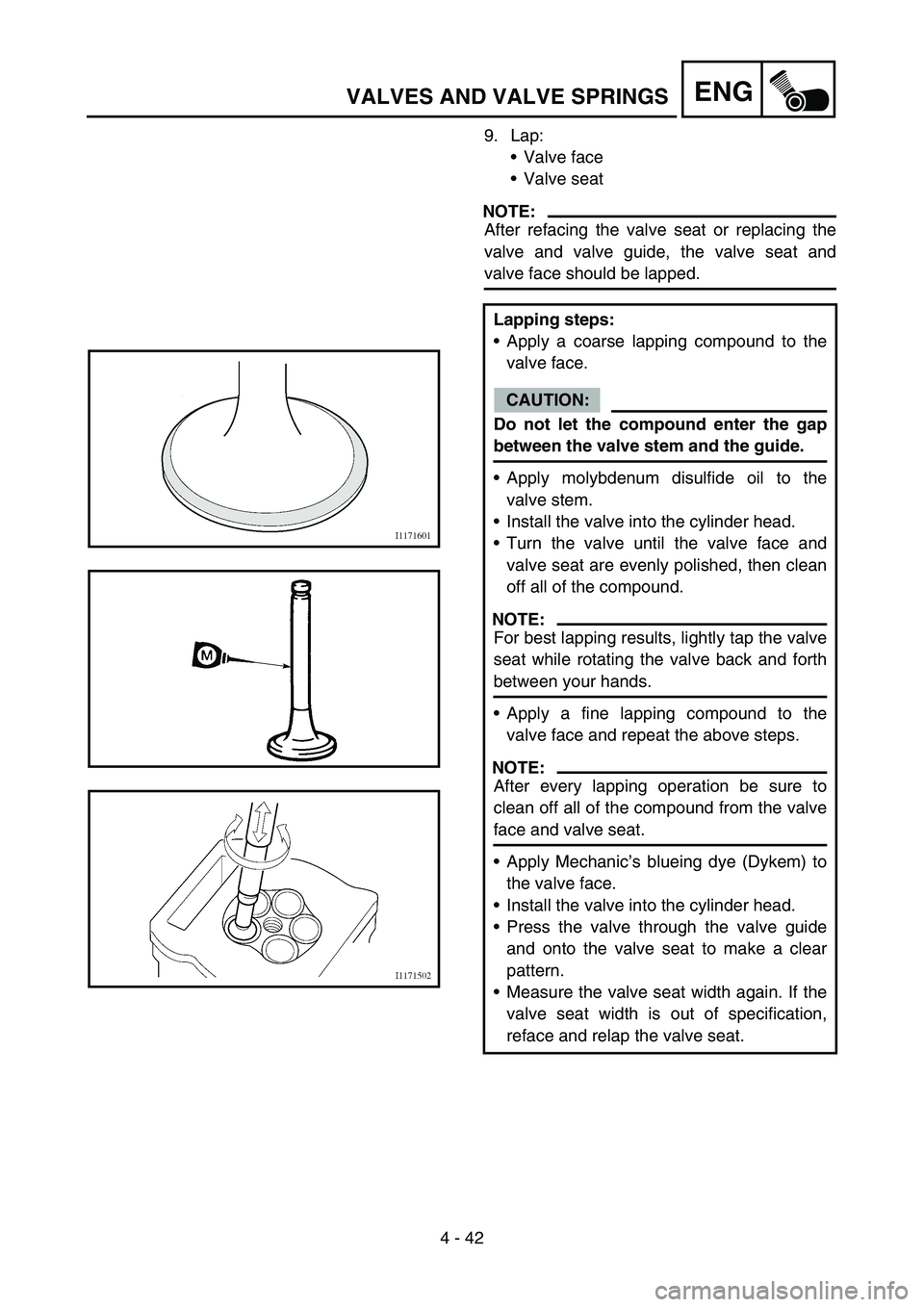
4 - 42
ENGVALVES AND VALVE SPRINGS
9. Lap:
Valve face
Valve seat
NOTE:
After refacing the valve seat or replacing the
valve and valve guide, the valve seat and
valve face should be lapped.
Lapping steps:
Apply a coarse lapping compound to the
valve face.
CAUTION:
Do not let the compound enter the gap
between the valve stem and the guide.
Apply molybdenum disulfide oil to the
valve stem.
Install the valve into the cylinder head.
Turn the valve until the valve face and
valve seat are evenly polished, then clean
off all of the compound.
NOTE:
For best lapping results, lightly tap the valve
seat while rotating the valve back and forth
between your hands.
Apply a fine lapping compound to the
valve face and repeat the above steps.
NOTE:
After every lapping operation be sure to
clean off all of the compound from the valve
face and valve seat.
Apply Mechanic’s blueing dye (Dykem) to
the valve face.
Install the valve into the cylinder head.
Press the valve through the valve guide
and onto the valve seat to make a clear
pattern.
Measure the valve seat width again. If the
valve seat width is out of specification,
reface and relap the valve seat.
Page 408 of 794
4 - 44
ENGVALVES AND VALVE SPRINGS
ASSEMBLY AND INSTALLATION
1. Apply:
Molybdenum disulfide oil
Onto the valve stem and valve stem seal.
2. Install:
Valves 1
Valve spring seats 2
Valve stem seals 3
Valve springs 4
Valve spring retainers 5
NOTE:
Make sure that each valve is installed in its
original place, also referring to the painted
color as follows.
Intake (middle) a: blue
Intake (right/left) b: gray
Exhaust: not paint
Install the valve springs with the larger pitch
c facing upward.
dSmaller pitch
New
3. Install:
Valve cotters
NOTE:
While compressing the valve spring with a
valve spring compressor 1 install the valve
cotters.
4. To secure the valve cotters onto the valve
stem, lightly tap the valve tip with a piece of
wood.
CAUTION:
Hitting the valve tip with excessive force
could damage the valve.
Valve spring compressor:
YM-4019/90890-04019
Page 420 of 794
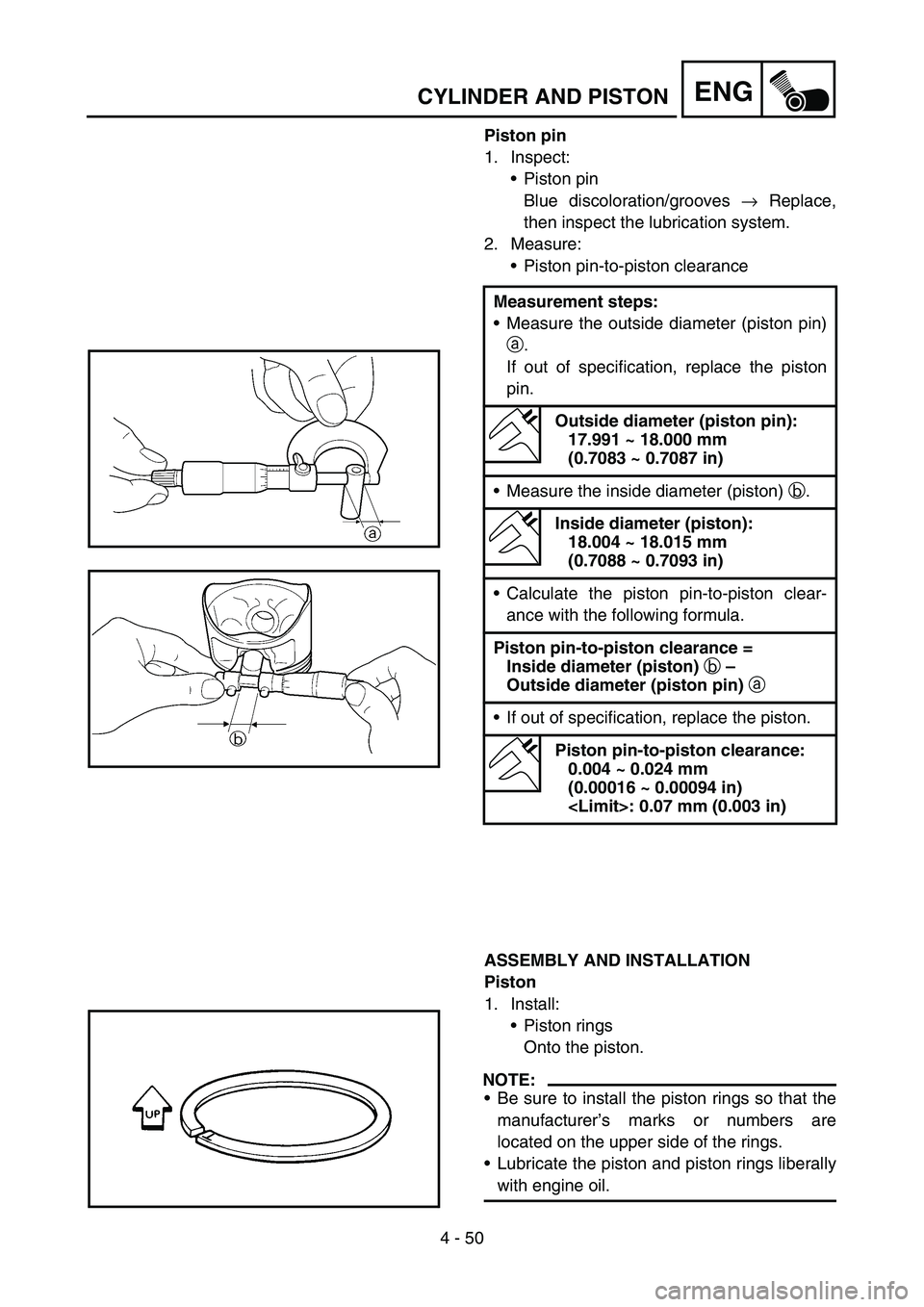
4 - 50
ENGCYLINDER AND PISTON
Piston pin
1. Inspect:
Piston pin
Blue discoloration/grooves → Replace,
then inspect the lubrication system.
2. Measure:
Piston pin-to-piston clearance
ASSEMBLY AND INSTALLATION
Piston
1. Install:
Piston rings
Onto the piston.
NOTE:
Be sure to install the piston rings so that the
manufacturer’s marks or numbers are
located on the upper side of the rings.
Lubricate the piston and piston rings liberally
with engine oil. Measurement steps:
Measure the outside diameter (piston pin)
a.
If out of specification, replace the piston
pin.
Outside diameter (piston pin):
17.991 ~ 18.000 mm
(0.7083 ~ 0.7087 in)
Measure the inside diameter (piston) b.
Inside diameter (piston):
18.004 ~ 18.015 mm
(0.7088 ~ 0.7093 in)
Calculate the piston pin-to-piston clear-
ance with the following formula.
Piston pin-to-piston clearance =
Inside diameter (piston)
b –
Outside diameter (piston pin)
a
If out of specification, replace the piston.
Piston pin-to-piston clearance:
0.004 ~ 0.024 mm
(0.00016 ~ 0.00094 in)
: 0.07 mm (0.003 in)
Page 676 of 794
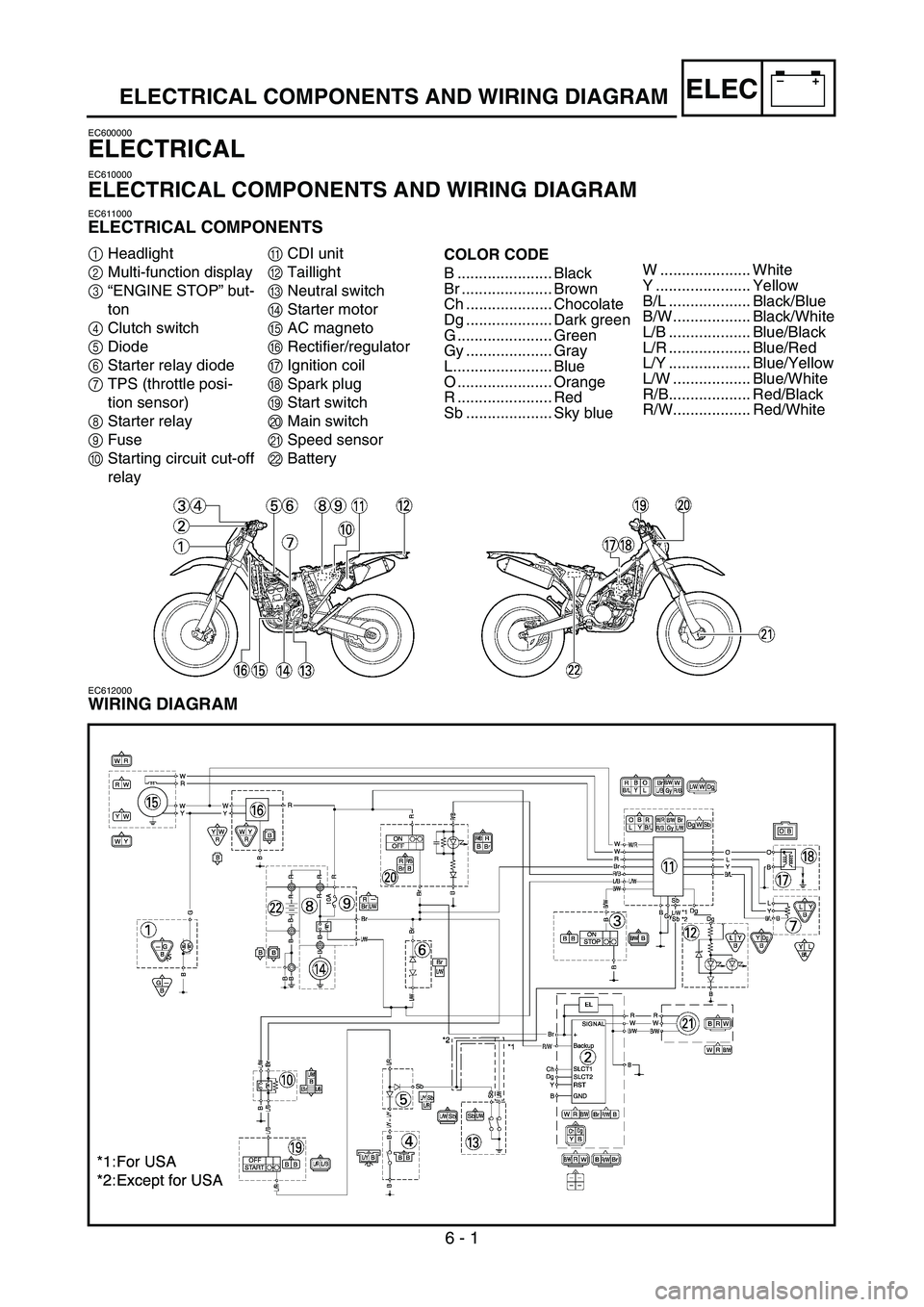
6 - 1
–+ELECELECTRICAL COMPONENTS AND WIRING DIAGRAM
EC600000
ELECTRICAL
EC610000
ELECTRICAL COMPONENTS AND WIRING DIAGRAM
EC611000
ELECTRICAL COMPONENTS
1Headlight
2Multi-function display
3“ENGINE STOP” but-
ton
4Clutch switch
5Diode
6Starter relay diode
7TPS (throttle posi-
tion sensor)
8Starter relay
9Fuse
0Starting circuit cut-off
relayACDI unit
BTaillight
CNeutral switch
DStarter motor
EAC magneto
FRectifier/regulator
GIgnition coil
HSpark plug
IStart switch
JMain switch
KSpeed sensor
LBatteryCOLOR CODE
B ...................... Black
Br ..................... Brown
Ch .................... Chocolate
Dg .................... Dark green
G ...................... Green
Gy .................... Gray
L....................... Blue
O ...................... Orange
R ...................... Red
Sb .................... Sky blue
EC612000
WIRING DIAGRAM
W ..................... White
Y ...................... Yellow
B/L ................... Black/Blue
B/W .................. Black/White
L/B ................... Blue/Black
L/R ................... Blue/Red
L/Y ................... Blue/Yellow
L/W .................. Blue/White
R/B................... Red/Black
R/W.................. Red/White
Page 686 of 794
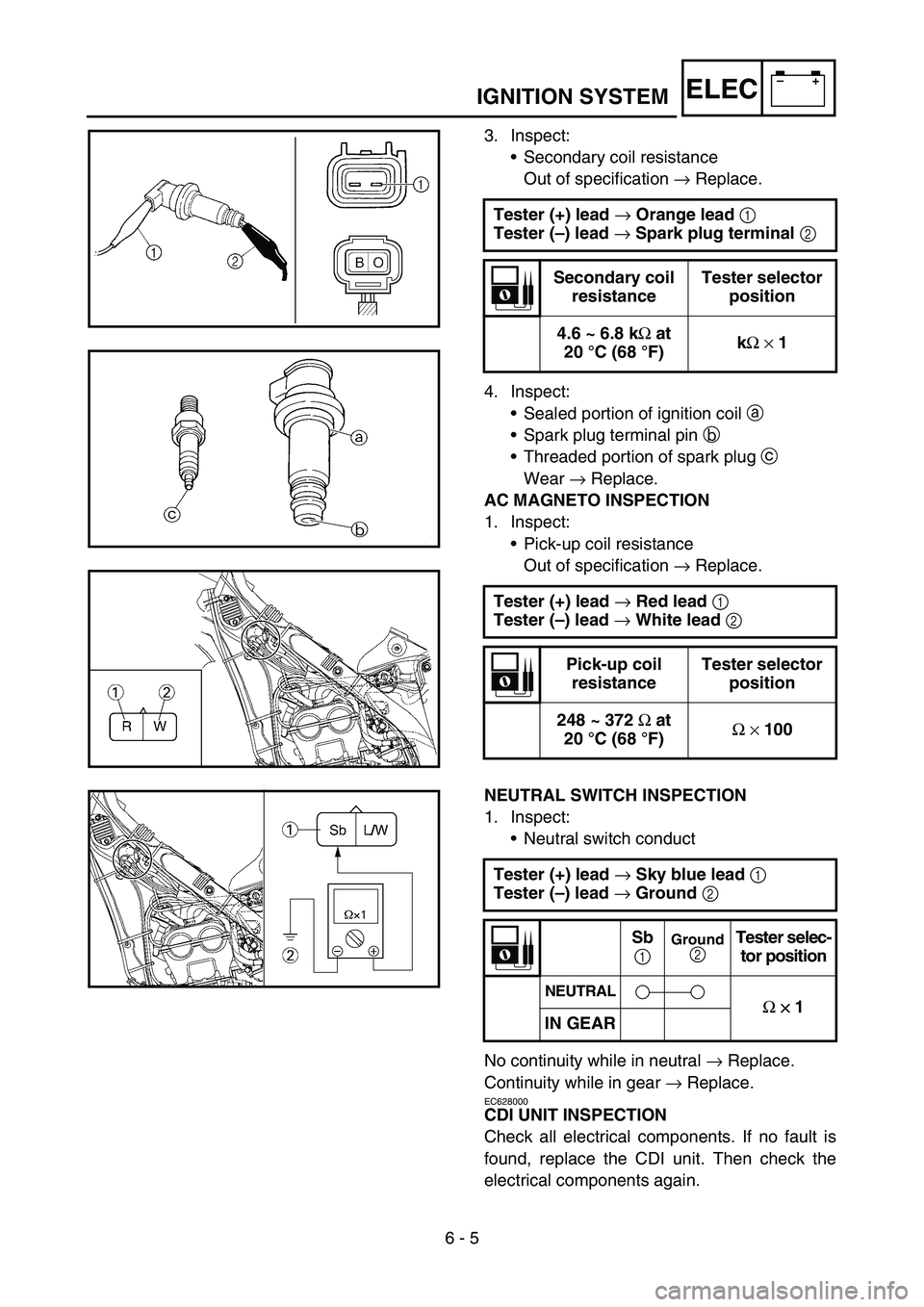
6 - 5
–+ELECIGNITION SYSTEM
3. Inspect:
•Secondary coil resistance
Out of specification → Replace.
4. Inspect:
•Sealed portion of ignition coil a
•Spark plug terminal pin b
•Threaded portion of spark plug c
Wear → Replace.
AC MAGNETO INSPECTION
1. Inspect:
•Pick-up coil resistance
Out of specification → Replace.
NEUTRAL SWITCH INSPECTION
1. Inspect:
•Neutral switch conduct
No continuity while in neutral → Replace.
Continuity while in gear → Replace.
EC628000
CDI UNIT INSPECTION
Check all electrical components. If no fault is
found, replace the CDI unit. Then check the
electrical components again.Tester (+) lead
→ Orange lead
1
Tester (–) lead
→ Spark plug terminal
2
Secondary coil
resistanceTester selector
position
4.6 ~ 6.8 k
Ω at
20 °C (68 °F)k
Ω
× 1
Tester (+) lead
→ Red lead
1
Tester (–) lead
→ White lead
2
Pick-up coil
resistanceTester selector
position
248 ~ 372
Ω at
20 °C (68 °F)Ω
× 100
Tester (+) lead
→ Sky blue lead
1
Tester (–) lead
→ Ground
2
Sb
1 Ground 2
Tester selec-
tor position
NEUTRAL
Ω
×
×× × 1
IN GEAR
Page 694 of 794
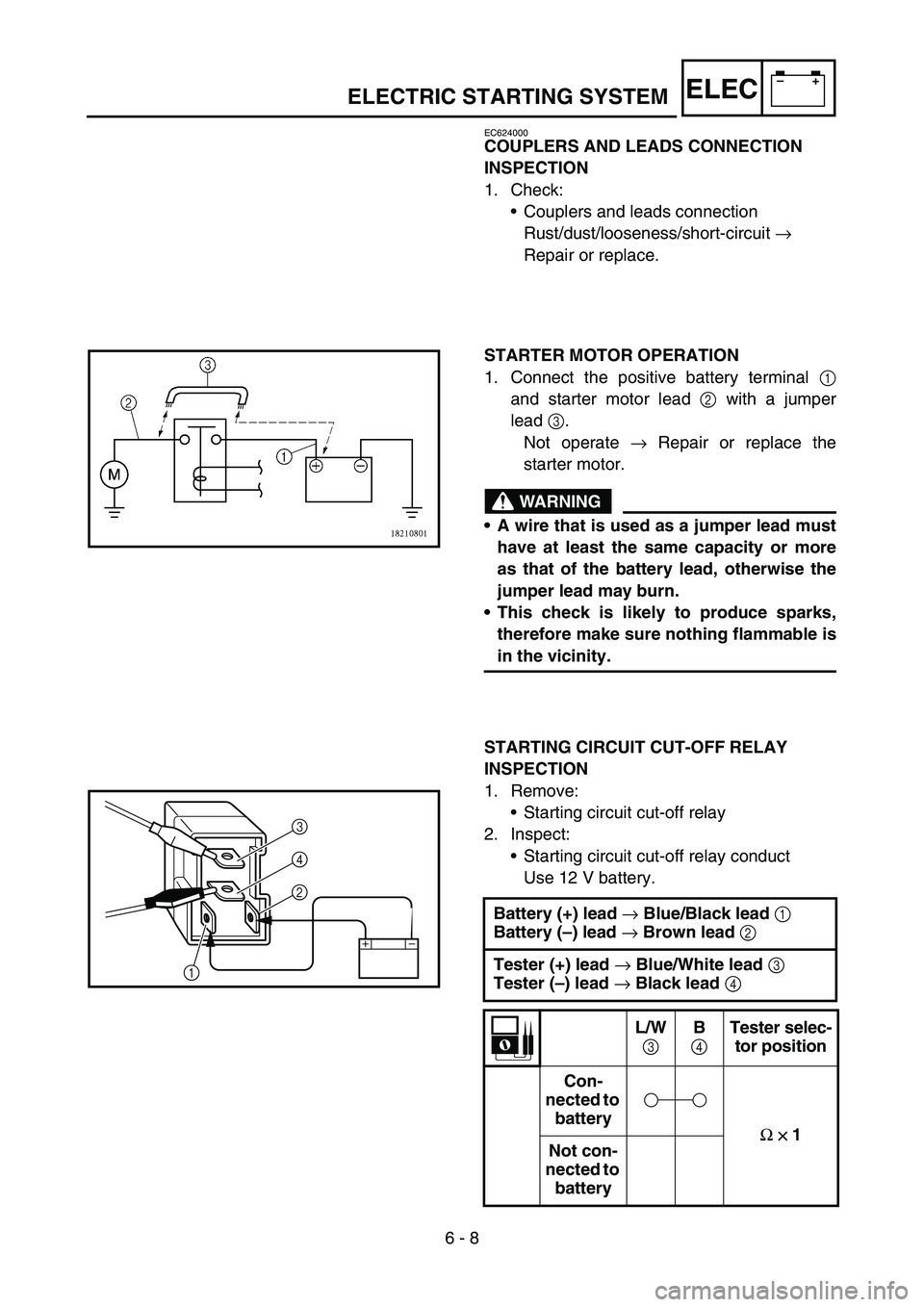
6 - 8
–+ELECELECTRIC STARTING SYSTEM
EC624000
COUPLERS AND LEADS CONNECTION
INSPECTION
1. Check:
•Couplers and leads connection
Rust/dust/looseness/short-circuit →
Repair or replace.
STARTER MOTOR OPERATION
1. Connect the positive battery terminal 1
and starter motor lead 2 with a jumper
lead 3.
Not operate → Repair or replace the
starter motor.
WARNING
A wire that is used as a jumper lead must
have at least the same capacity or more
as that of the battery lead, otherwise the
jumper lead may burn.
This check is likely to produce sparks,
therefore make sure nothing flammable is
in the vicinity.
STARTING CIRCUIT CUT-OFF RELAY
INSPECTION
1. Remove:
•Starting circuit cut-off relay
2. Inspect:
•Starting circuit cut-off relay conduct
Use 12 V battery.
Battery (+) lead
→ Blue/Black lead
1
Battery (–) lead
→ Brown lead
2
Tester (+) lead
→ Blue/White lead
3
Tester (–) lead
→ Black lead
4
L/W
3 B
4 Tester selec-
tor position
Con-
nected to
battery
Ω
×
×× × 1
Not con-
nected to
battery
2 4
3
1