Page 326 of 444
0-8
RODIUS 2007.07
4892-01
ABS SYSTEM
Brake force
When depressing the brake pedal the
brake force increases to the maximum,
then the brake force decreases until the
wheel locks.
Cornering force
The cornering force is a maximum when
the wheel is turning freely with zero slip.
When braking the cornering force falls to
zero if the wheel locks (slip 100 %).
ABS operating range
The operating range starts just before the
maximum brake force and ends in
maximum, for the unstable range then
begins, in which no further modulation is
possible. The ABS controls the regulation
of the brake pressure so that the brake
force only becomes great enough for a
sufficient proportion of cornering force to
remain. With ABS we remain in the
Kamm circle as long as the car is driving
sensibly. We will leave driving physics
with these statements and turn to the
braking systems with and without ABS. -
-
- Brake and cornering force ▶
Page 327 of 444
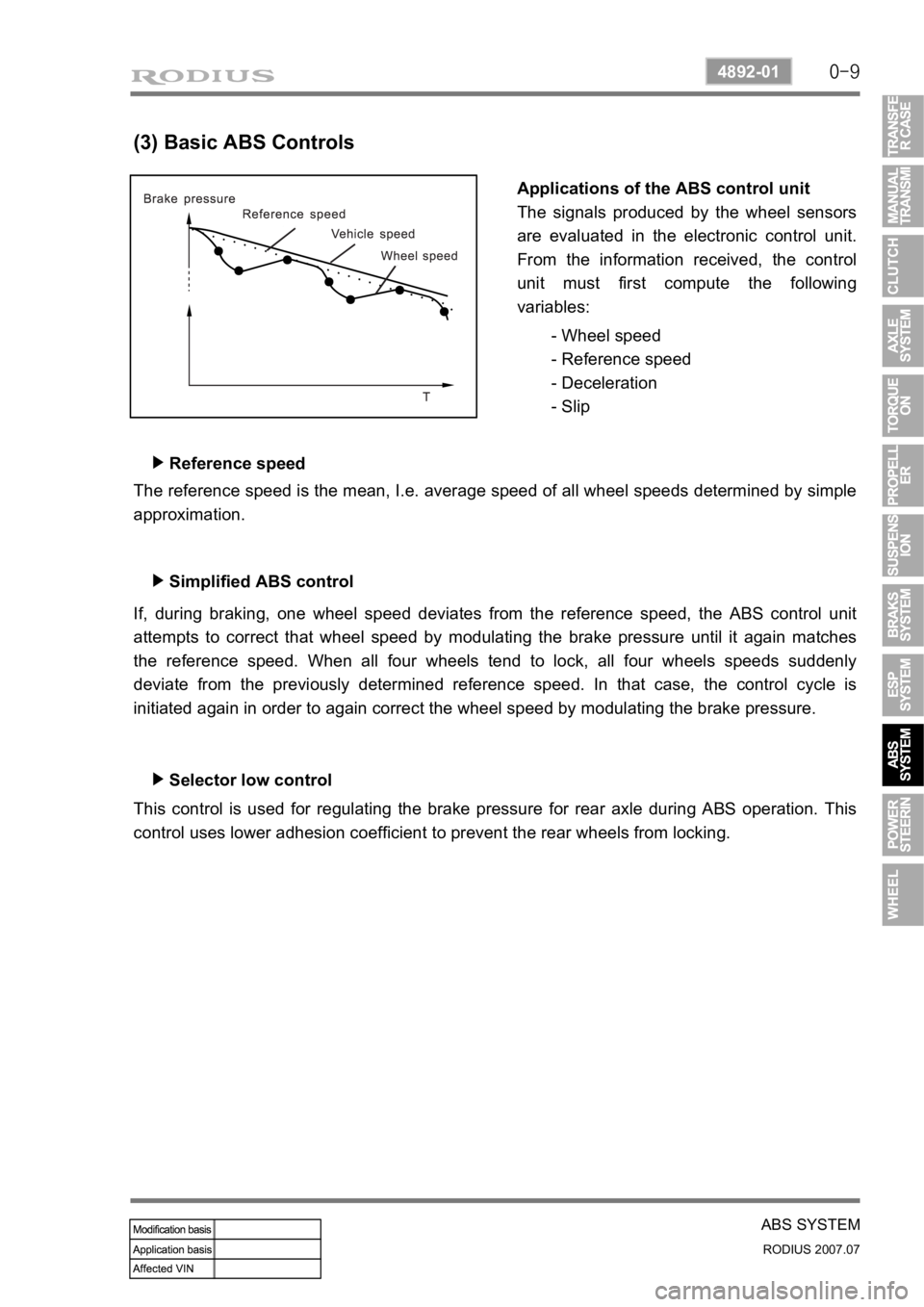
0-9
ABS SYSTEM
RODIUS 2007.07
4892-01
(3) Basic ABS Controls
Applications of the ABS control unit
The signals produced by the wheel sensors
are evaluated in the electronic control unit.
From the information received, the control
unit must first compute the following
variables:
- Wheel speed
- Reference speed
- Deceleration
- Slip
Reference speed ▶
The reference speed is the mean, I.e. average speed of all wheel speeds determined by simple
approximation.
Simplified ABS control ▶
If, during braking, one wheel speed deviates from the reference speed, the ABS control unit
attempts to correct that wheel speed by modulating the brake pressure until it again matches
the reference speed. When all four wheels tend to lock, all four wheels speeds suddenly
deviate from the previously determined reference speed. In that case, the control cycle is
initiated again in order to again correct the wheel speed by modulating the brake pressure.
Selector low control ▶
This control is used for regulating the brake pressure for rear axle during ABS operation. This
control uses lower adhesion coefficient to prevent the rear wheels from locking.
Page 328 of 444
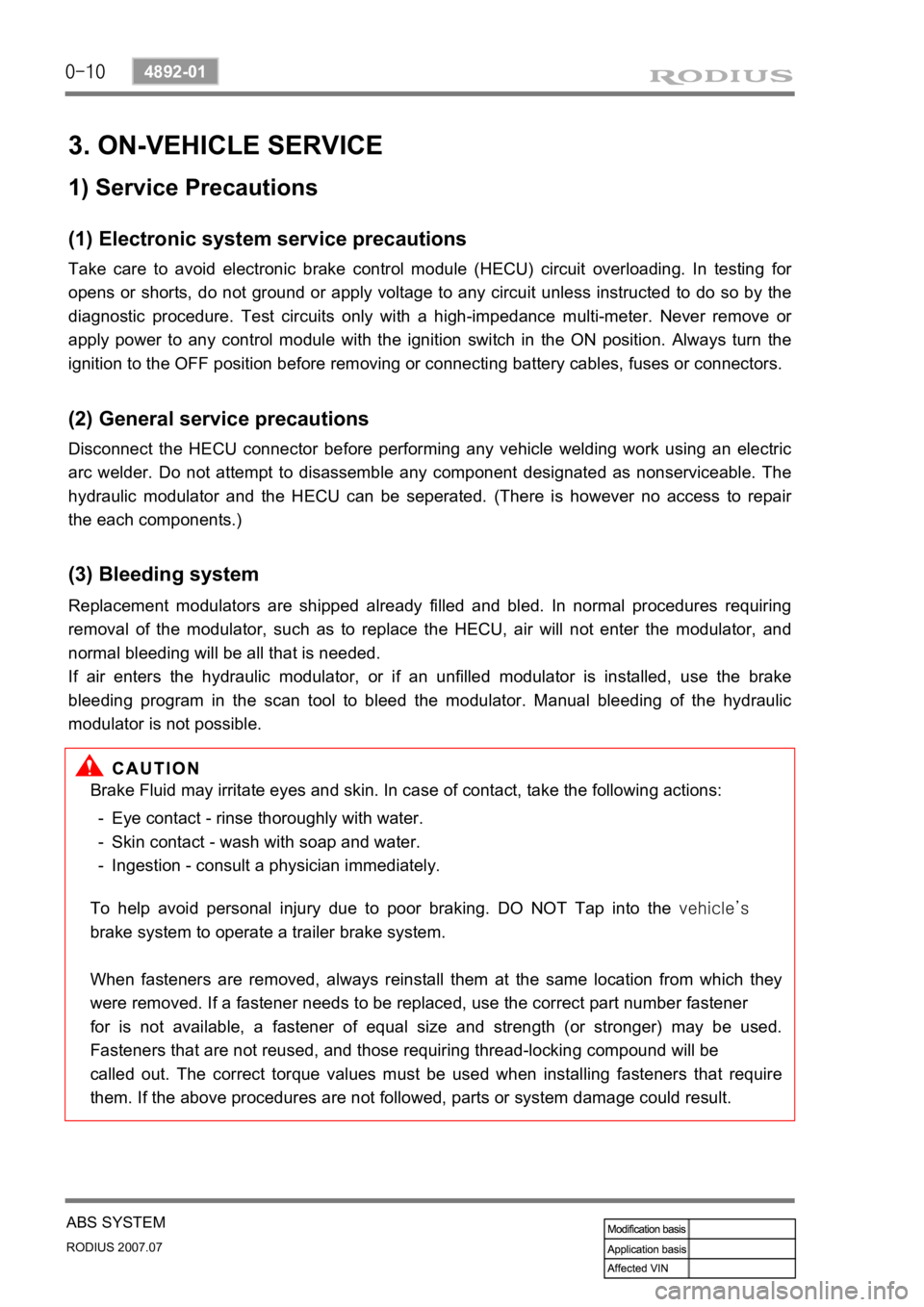
0-10
RODIUS 2007.07
4892-01
ABS SYSTEM
3. ON-VEHICLE SERVICE
(1) Electronic system service precautions
Take care to avoid electronic brake control module (HECU) circuit overloading. In testing for
opens or shorts, do not ground or apply voltage to any circuit unless instructed to do so by the
diagnostic procedure. Test circuits only with a high-impedance multi-meter. Never remove o
r
apply power to any control module with the ignition switch in the ON position. Always turn the
ignition to the OFF position before removing or connecting battery cables, fuses or connectors.
(2) General service precautions
Disconnect the HECU connector before performing any vehicle welding work using an electric
arc welder. Do not attempt to disassemble any component designated as nonserviceable. The
hydraulic modulator and the HECU can be seperated. (There is however no access to repai
r
the each components.)
(3) Bleeding system
Replacement modulators are shipped already filled and bled. In normal procedures requiring
removal of the modulator, such as to replace the HECU, air will not enter the modulator, and
normal bleeding will be all that is needed.
If air enters the hydraulic modulator, or if an unfilled modulator is installed, use the brake
bleeding program in the scan tool to bleed the modulator. Manual bleeding of the hydraulic
modulator is not possible.
1) Service Precautions
Brake Fluid may irritate eyes and skin. In case of contact, take the following actions:
Eye contact - rinse thoroughly with water.
Skin contact - wash with soap and water.
Ingestion - consult a physician immediately. -
-
-
To help avoid personal injury due to poor braking. DO NOT Tap into the vehicle’s
brake system to operate a trailer brake system.
When fasteners are removed, always reinstall them at the same location from which they
were removed. If a fastener needs to be replaced, use the correct part number fastener
for is not available, a fastener of equal size and strength (or stronger) may be used.
Fasteners that are not reused, and those requiring thread-locking compound will be
called out. The correct torque values must be used when installing fasteners that require
them. If the above procedures are not followed, parts or system damage could result.
Page 337 of 444
0-19
ABS SYSTEM
RODIUS 2007.07
4892-01
(2) ABS Circuit Per ABS Operation Range
Hydraulic Pressure Circuit when ABS is Not Operating ▶
No Hydraulic Pressure Circuit when ABS is Operating ▶
The hydraulic pressure in the master cylinder increases through the vacuum booster and it is
delivered to the wheel via the normal open inlet valve. At this moment, the normally-closed
outlet valve is closed. The speed of the wheel that hydraulic pressure is delivered reduces
gradually
As hydraulic pressure on each wheel increases, the wheel tends to lock. In order to prevent the
wheel from locking, the hydraulic valve modulator operates the inlet valve control solenoid to
close the inlet valve and stop the hydraulic pressure increases. At this moment, the outlet valve
is closed. This procedure helps the wheel to maintain a stable hydraulic pressure.
Page 338 of 444
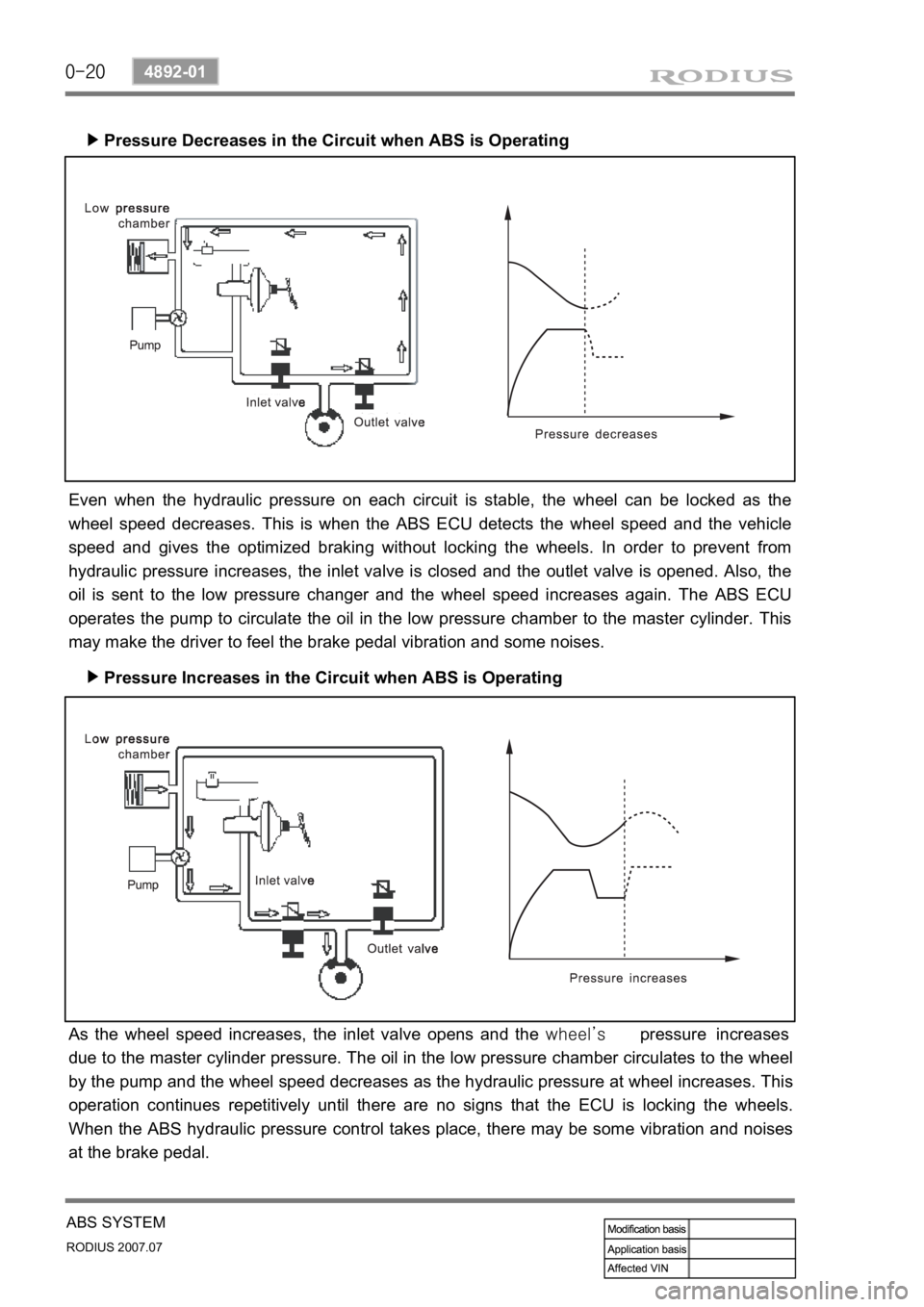
0-20
RODIUS 2007.07
4892-01
ABS SYSTEM
Pressure Decreases in the Circuit when ABS is Operating ▶
Pressure Increases in the Circuit when ABS is Operating ▶
Even when the hydraulic pressure on each circuit is stable, the wheel can be locked as the
wheel speed decreases. This is when the ABS ECU detects the wheel speed and the vehicle
speed and gives the optimized braking without locking the wheels. In order to prevent from
hydraulic pressure increases, the inlet valve is closed and the outlet valve is opened. Also, the
oil is sent to the low pressure changer and the wheel speed increases again. The ABS ECU
operates the pump to circulate the oil in the low pressure chamber to the master cylinder. This
may make the driver to feel the brake pedal vibration and some noises.
As the wheel speed increases, the inlet valve opens and the wheel’s pressure increases
due to the master cylinder pressure. The oil in the low pressure chamber circulates to the wheel
by the pump and the wheel speed decreases as the hydraulic pressure at wheel increases. This
operation continues repetitively until there are no signs that the ECU is locking the wheels.
When the ABS hydraulic pressure control takes place, there may be some vibration and noises
at the brake pedal.
Page 346 of 444
0-8
RODIUS 2007.07
4610-00
POWER STEERING SYSTEM
3. POWER STEERING PUMP
The vane type pump that is connected to engine by belt is used for the power steering system.
This pump generates and controls a proper hydraulic pressure and flows by using the flow
control valve and pressure relief valve.
The flow control valve regulates the excessive amount of discharging oil. When the steering
wheel is stationary or the oil circuit is blocked, the pressure relief valve returns the ove
r
pressurized oil to the oil reservoir.
4. OIL RESERVOIR
The oil reservoir sends the oil to the power steering pump and receives the oil from the power
steering gear.
The oil level in the reservoir depends on the steering wheel positions. therefore, measure the oil
level when the steering wheel is positioned at straight ahead direction (neutral).
Steering pump Reservoir tank
Page 387 of 444
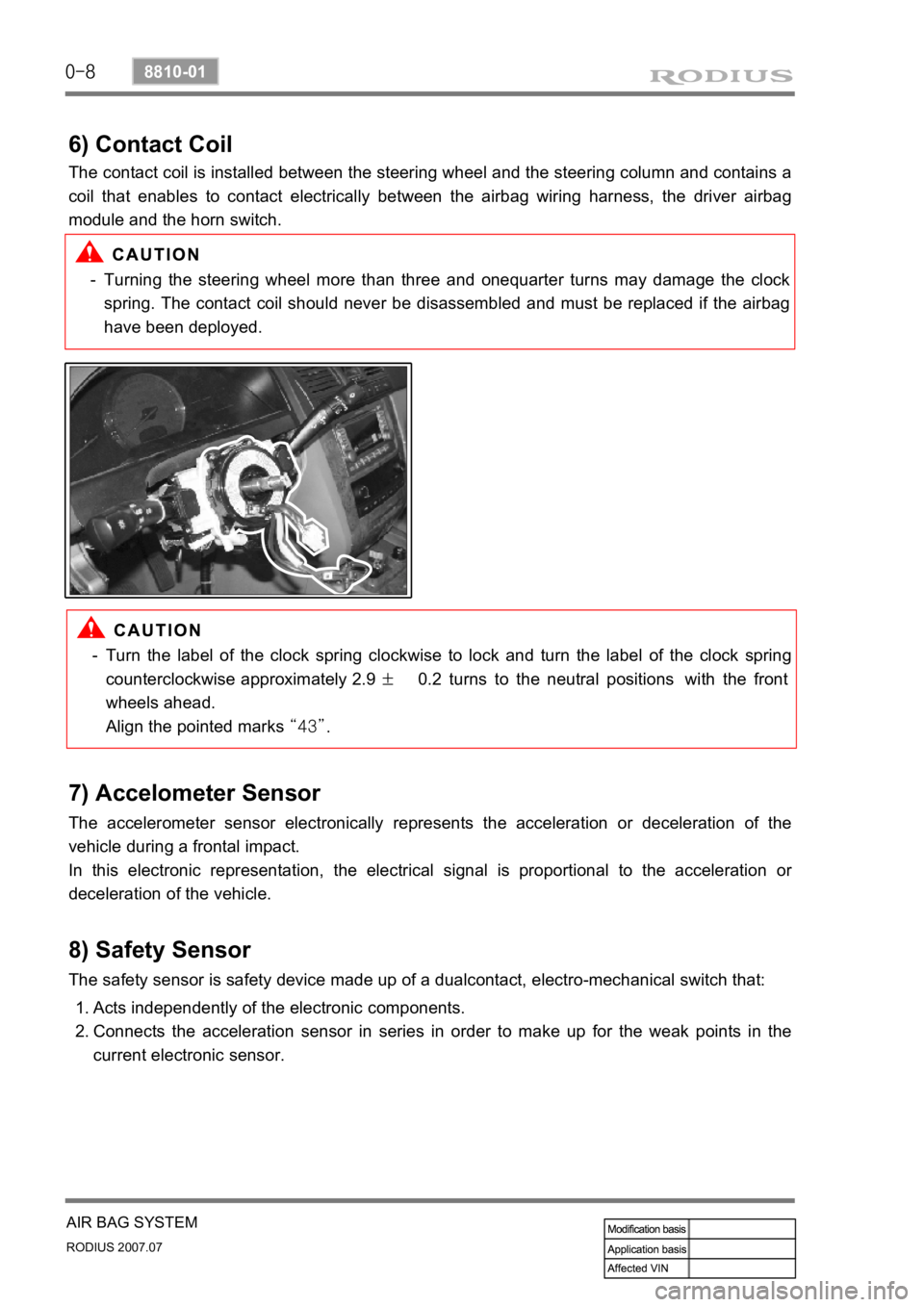
0-8
RODIUS 2007.07
8810-01
AIR BAG SYSTEM
6) Contact Coil
The contact coil is installed between the steering wheel and the steering column and contains a
coil that enables to contact electrically between the airbag wiring harness, the driver airbag
module and the horn switch.
Turning the steering wheel more than three and onequarter turns may damage the clock
spring. The contact coil should never be disassembled and must be replaced if the airbag
have been deployed. -
Turn the label of the clock spring clockwise to lock and turn the label of the clock spring
counterclockwise approximately 2.9 ± 0.2 turns to the neutral positions with the front
wheels ahead.
Align the pointed marks “43”. -
7) Accelometer Sensor
The accelerometer sensor electronically represents the acceleration or deceleration of the
vehicle during a frontal impact.
In this electronic representation, the electrical signal is proportional to the acceleration o
r
deceleration of the vehicle.
8) Safety Sensor
The safety sensor is safety device made up of a dualcontact, electro-mechanical switch that:
Acts independently of the electronic components.
Connects the acceleration sensor in series in order to make up for the weak points in the
current electronic sensor. 1.
2.
Page 428 of 444
06-9
BODY EXTERIOR
RODIUS 2007.07
7115-01
4) OPERATION - DOOR LOCK / UNLOCK
(1) Front Door
Connecting rod - key cylinder Door key cylinder Outside door handle
Lock / Unlock cable
Connecting rod
- outside handle
Door latch Operating cable - Inside handle
Lock / Unlock Inside door handle