Page 38 of 2896
A/T CONTROL SYSTEM
AT-25
D
E
F
G
H
I
J
K
L
MA
B
AT
Revision: June 20062007 Versa
“D1 ” and “21 ” Positions
*: Overrun clutch remains in engaged condition when throttle opening is less than 1/16.
Forward one-way clutch
Forward clutch
Low one-way clutchRear internal gear is locked to rotate counterclockwise because of the functioning of these three
clutches.
Overrun clutch
engagement conditions
(Engine brake)D
1 : OD OFF (OD OFF indicator lamp is on) and throttle opening is less than specification*
2
1 : Always engaged
At D
1 and 21 positions, engine brake is not activated due to free turning of low one- way clutch.
SAT3 7 7J
Page 267 of 2896

AT-254
TRANSAXLE ASSEMBLY
Revision: June 20062007 Versa
2. Disconnect the following connectors and remove the wire har-
ness.
Turbine revolution sensor (power train revolution sensor) har-
ness connector (1)
Terminal cord assembly harness connector (2)
PNP switch connector (3)
Revolution sensor harness connector (4)
3. Remove the four drive plate to torque converter bolts.
NOTE:
Rotate the crankshaft clockwise as viewed from front of engine
for access to drive plate to torque converter bolts.
4. Put matching marks on the drive plate and torque converter.
CAUTION:
For matching marks, use paint. Never damage the drive plate or torque converter.
5. Remove the transaxle to engine and engine to transaxle bolts.
6. Separate the transaxle from the engine.
CAUTION:
Secure torque converter to prevent it from dropping.
7. If necessary, remove the following from the transaxle:
Fluid cooler tubes (1) and copper washers
A/T fluid level gauge (2) and charging pipe (3)
PNP switch
Air breather hose
Engine mounting bracket (LH)
Any necessary brackets
INSTALLATION
Installation is in the reverse order of removal.
WCIA0647E
WCIA0616E
WCIA0648E
Page 268 of 2896
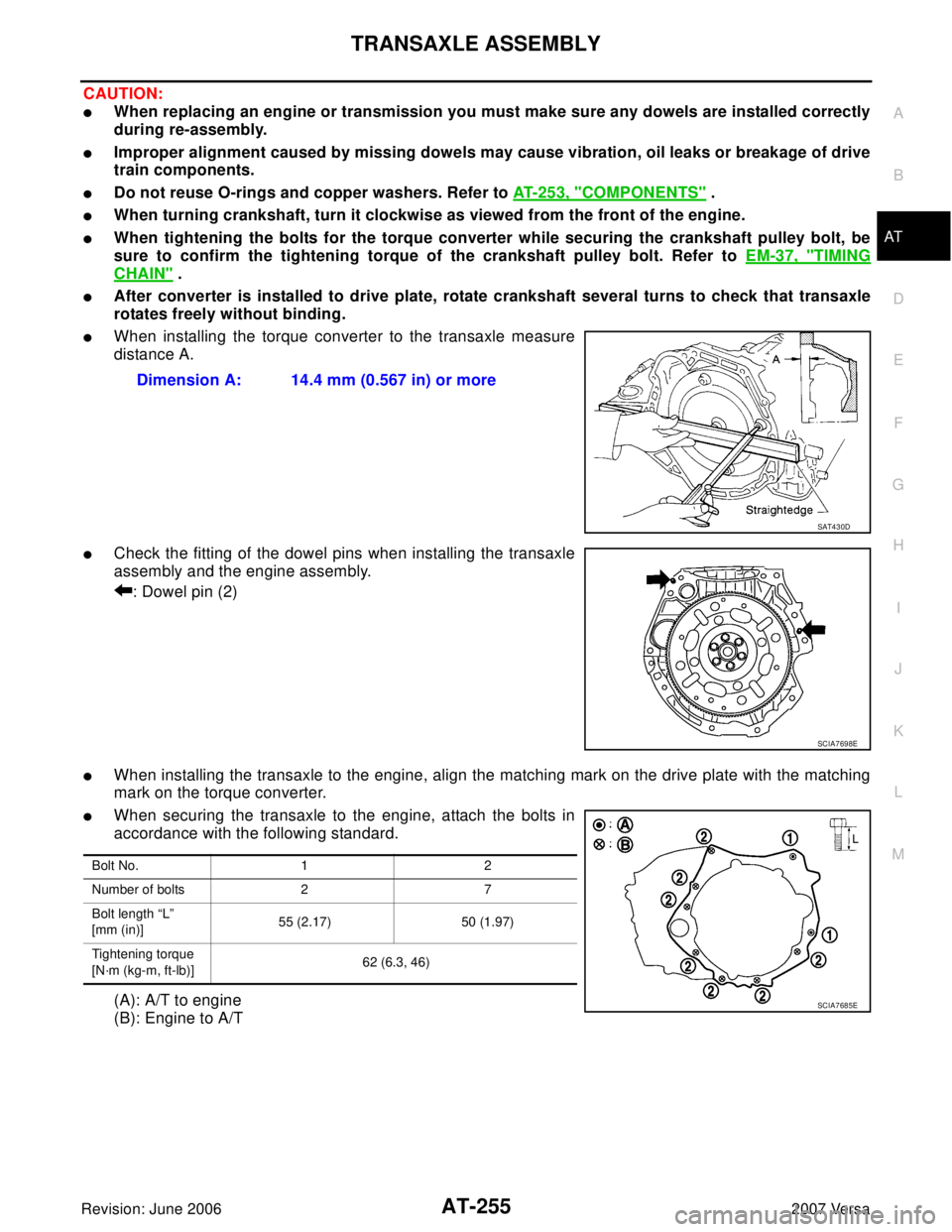
TRANSAXLE ASSEMBLY
AT-255
D
E
F
G
H
I
J
K
L
MA
B
AT
Revision: June 20062007 Versa
CAUTION:
When replacing an engine or transmission you must make sure any dowels are installed correctly
during re-assembly.
Improper alignment caused by missing dowels may cause vibration, oil leaks or breakage of drive
train components.
Do not reuse O-rings and copper washers. Refer to AT- 2 5 3 , "COMPONENTS" .
When turning crankshaft, turn it clockwise as viewed from the front of the engine.
When tightening the bolts for the torque converter while securing the crankshaft pulley bolt, be
sure to confirm the tightening torque of the crankshaft pulley bolt. Refer to EM-37, "
TIMING
CHAIN" .
After converter is installed to drive plate, rotate crankshaft several turns to check that transaxle
rotates freely without binding.
When installing the torque converter to the transaxle measure
distance A.
Check the fitting of the dowel pins when installing the transaxle
assembly and the engine assembly.
: Dowel pin (2)
When installing the transaxle to the engine, align the matching mark on the drive plate with the matching
mark on the torque converter.
When securing the transaxle to the engine, attach the bolts in
accordance with the following standard.
(A): A/T to engine
(B): Engine to A/TDimension A: 14.4 mm (0.567 in) or more
SAT4 3 0D
SCIA7698E
Bolt No. 1 2
Number of bolts 2 7
Bolt length “L”
[mm (in)]55 (2.17) 50 (1.97)
Tightening torque
[N·m (kg-m, ft-lb)]62 (6.3, 46)
SCIA7685E
Page 281 of 2896
AT-268
DISASSEMBLY
Revision: June 20062007 Versa
DISASSEMBLYPFP:31020
DisassemblyUCS005W2
1. Drain ATF through drain hole.
2. Remove drain plug gasket from drain plug.
3. Remove torque converter.
4. Check torque converter one-way clutch using check tool as
shown in the figure.
a. Insert check tool into groove of bearing support built into one-
way clutch outer race.
b. When fixing bearing support with check tool, rotate one-way
clutch spline using screwdriver.
c. Check that inner race rotates clockwise only. If not, replace
torque converter assembly.
SCIA0003E
SAT0 0 8D
SAT0 0 9D
Page 291 of 2896
AT-278
DISASSEMBLY
Revision: June 20062007 Versa
37. Remove front planetary carrier and low one-way clutch according to the following procedures.
a. Remove snap ring using a flat-bladed screwdriver.
b. Remove low one-way clutch (1) and front planetary carrier (2) as
a set from transaxle case.
c. Check that low one-way clutch rotates counter-clockwise around
front planetary carrier. Then try to turn it clockwise and check
that it is locked.
Replace low one-way clutch if necessary.
d. Remove low one-way clutch from front planetary carrier by turn-
ing it in the direction of unlock.
Inspect low one-way clutch, and replace if damaged or
worn.
e. Remove needle bearing (1) from front planetary carrier (2).
Inspect needle bearing (1) and front planetary carrier (2),
and replace if damaged or worn.
SCIA3633E
SCIA5896J
SAT0 4 8D
SCIA6047J
Page 375 of 2896
AT-362
ASSEMBLY
Revision: June 20062007 Versa
4. Install needle bearing (1) on bearing retainer.
CAUTION:
Be careful with the direction of needle bearing.
5. Install thrust washer (1) on overrun clutch hub (2).
CAUTION:
Align pawls of thrust washer (1) with holes of overrun
clutch hub (2).
6. Install overrun clutch hub (1) into forward clutch drum.
CAUTION:
Align teeth of overrun clutch drive plates before installing.
7. Hold forward clutch hub, and check that rear internal gear locks
when tried to rotate counterclockwise.
CAUTION:
If rear internal gear rotates counterclockwise, check instal-
lation direction of forward one-way clutch.
8. Install needle bearing (1) on rear internal gear (2).
CAUTION:
Be careful with the direction of needle bearing (1).
SCIA8014E
SCIA5899J
SCIA5898J
SCIA7078E
SCIA6041J
Page 377 of 2896
AT-364
ASSEMBLY
Revision: June 20062007 Versa
14. Install low one-way clutch to front planetary carrier by turning it
in the direction of unlock.
15. Check that low one-way clutch rotates counterclockwise around
front planetary carrier. Then try to turn it clockwise and check
that it is locked.
16. Install front planetary carrier (2) and low one-way clutch (1) as a
set into transaxle case.
17. Install snap ring into transaxle case using a flat-bladed screw-
driver.
18. Install needle bearing (1) on front sun gear (2).
CAUTION:
Be careful with the direction of needle bearing (1).
19. Install front sun gear on front planetary carrier.
SAT0 4 8D
SCIA5896J
SCIA3633E
SCIA6960E
SAT3 6 8D
Page 497 of 2896
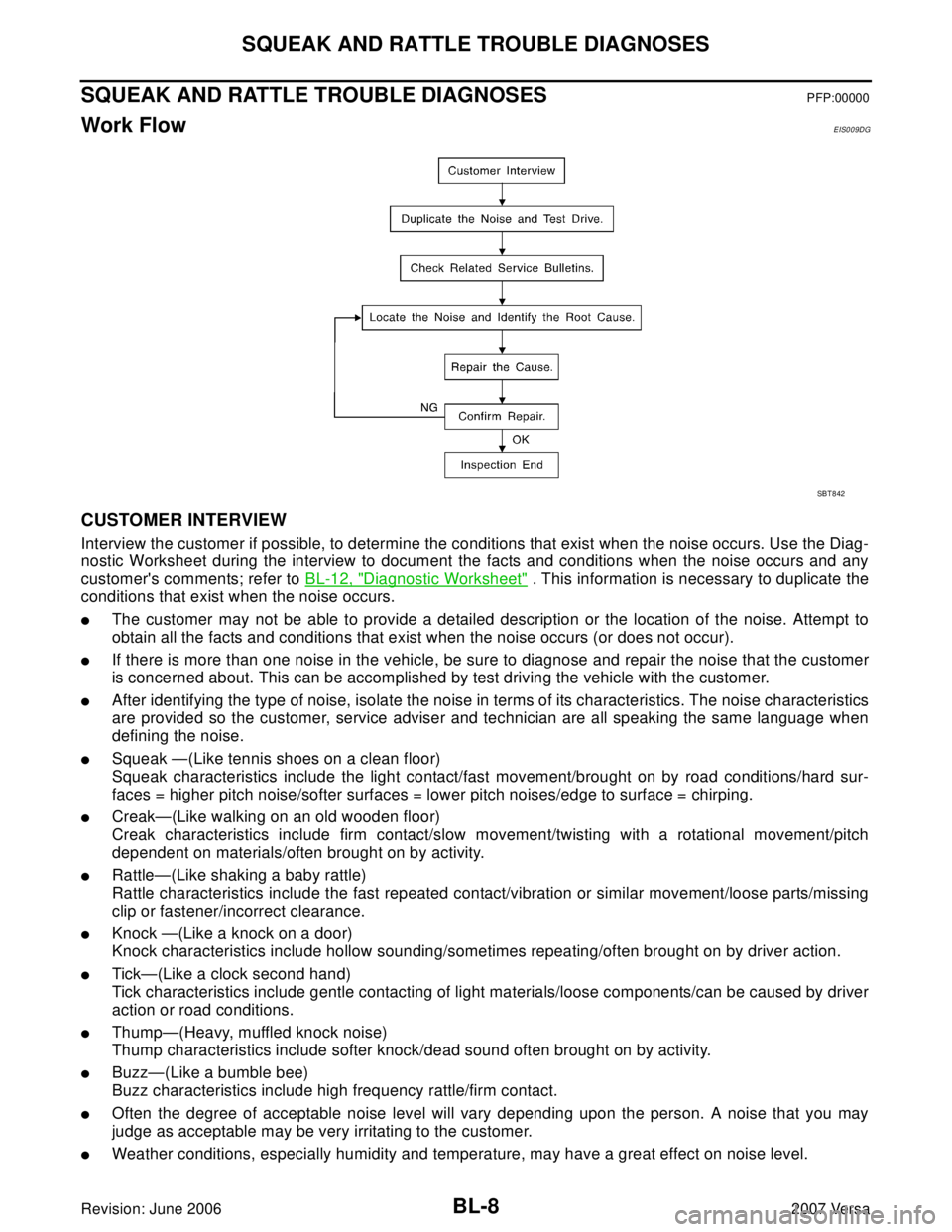
BL-8
SQUEAK AND RATTLE TROUBLE DIAGNOSES
Revision: June 20062007 Versa
SQUEAK AND RATTLE TROUBLE DIAGNOSESPFP:00000
Work FlowEIS009DG
CUSTOMER INTERVIEW
Interview the customer if possible, to determine the conditions that exist when the noise occurs. Use the Diag-
nostic Worksheet during the interview to document the facts and conditions when the noise occurs and any
customer's comments; refer to BL-12, "
Diagnostic Worksheet" . This information is necessary to duplicate the
conditions that exist when the noise occurs.
The customer may not be able to provide a detailed description or the location of the noise. Attempt to
obtain all the facts and conditions that exist when the noise occurs (or does not occur).
If there is more than one noise in the vehicle, be sure to diagnose and repair the noise that the customer
is concerned about. This can be accomplished by test driving the vehicle with the customer.
After identifying the type of noise, isolate the noise in terms of its characteristics. The noise characteristics
are provided so the customer, service adviser and technician are all speaking the same language when
defining the noise.
Squeak —(Like tennis shoes on a clean floor)
Squeak characteristics include the light contact/fast movement/brought on by road conditions/hard sur-
faces = higher pitch noise/softer surfaces = lower pitch noises/edge to surface = chirping.
Creak—(Like walking on an old wooden floor)
Creak characteristics include firm contact/slow movement/twisting with a rotational movement/pitch
dependent on materials/often brought on by activity.
Rattle—(Like shaking a baby rattle)
Rattle characteristics include the fast repeated contact/vibration or similar movement/loose parts/missing
clip or fastener/incorrect clearance.
Knock —(Like a knock on a door)
Knock characteristics include hollow sounding/sometimes repeating/often brought on by driver action.
Tick—(Like a clock second hand)
Tick characteristics include gentle contacting of light materials/loose components/can be caused by driver
action or road conditions.
Thump—(Heavy, muffled knock noise)
Thump characteristics include softer knock/dead sound often brought on by activity.
Buzz—(Like a bumble bee)
Buzz characteristics include high frequency rattle/firm contact.
Often the degree of acceptable noise level will vary depending upon the person. A noise that you may
judge as acceptable may be very irritating to the customer.
Weather conditions, especially humidity and temperature, may have a great effect on noise level.
SBT 8 42