Page 2770 of 3383
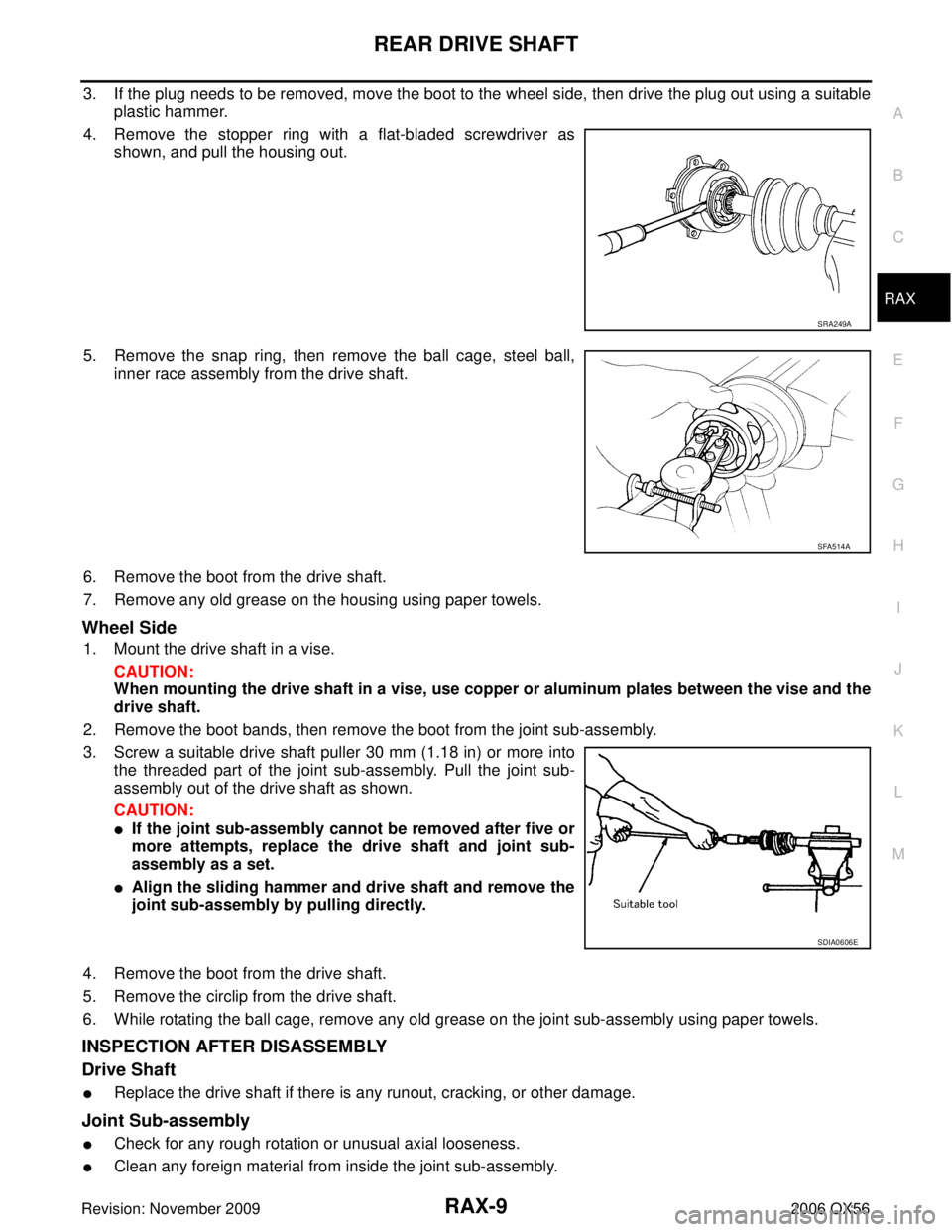
REAR DRIVE SHAFTRAX-9
CE F
G H
I
J
K L
M A
B
RAX
Revision: November 2009 2006 QX56
3. If the plug needs to be removed, move the boot to the wheel side, then drive the plug out using a suitable
plastic hammer.
4. Remove the stopper ring with a flat-bladed screwdriver as shown, and pull the housing out.
5. Remove the snap ring, then remove the ball cage, steel ball, inner race assembly from the drive shaft.
6. Remove the boot from the drive shaft.
7. Remove any old grease on the housing using paper towels.
Wheel Side
1. Mount the drive shaft in a vise. CAUTION:
When mounting the drive shaft in a vise, use copper or aluminum plates between the vise and the
drive shaft.
2. Remove the boot bands, then remove the boot from the joint sub-assembly.
3. Screw a suitable drive shaft puller 30 mm (1.18 in) or more into the threaded part of the joint sub-assembly. Pull the joint sub-
assembly out of the drive shaft as shown.
CAUTION:
If the joint sub-assembly cannot be removed after five or
more attempts, replace the drive shaft and joint sub-
assembly as a set.
Align the sliding hammer and drive shaft and remove the
joint sub-assembly by pulling directly.
4. Remove the boot from the drive shaft.
5. Remove the circlip from the drive shaft.
6. While rotating the ball cage, remove any old grease on the joint sub-assembly using paper towels.
INSPECTION AFTER DISASSEMBLY
Drive Shaft
Replace the drive shaft if there is any runout, cracking, or other damage.
Joint Sub-assembly
Check for any rough rotation or unusual axial looseness.
Clean any foreign material from inside the joint sub-assembly.
SRA249A
SFA514A
SDIA0606E
Page 2824 of 3383
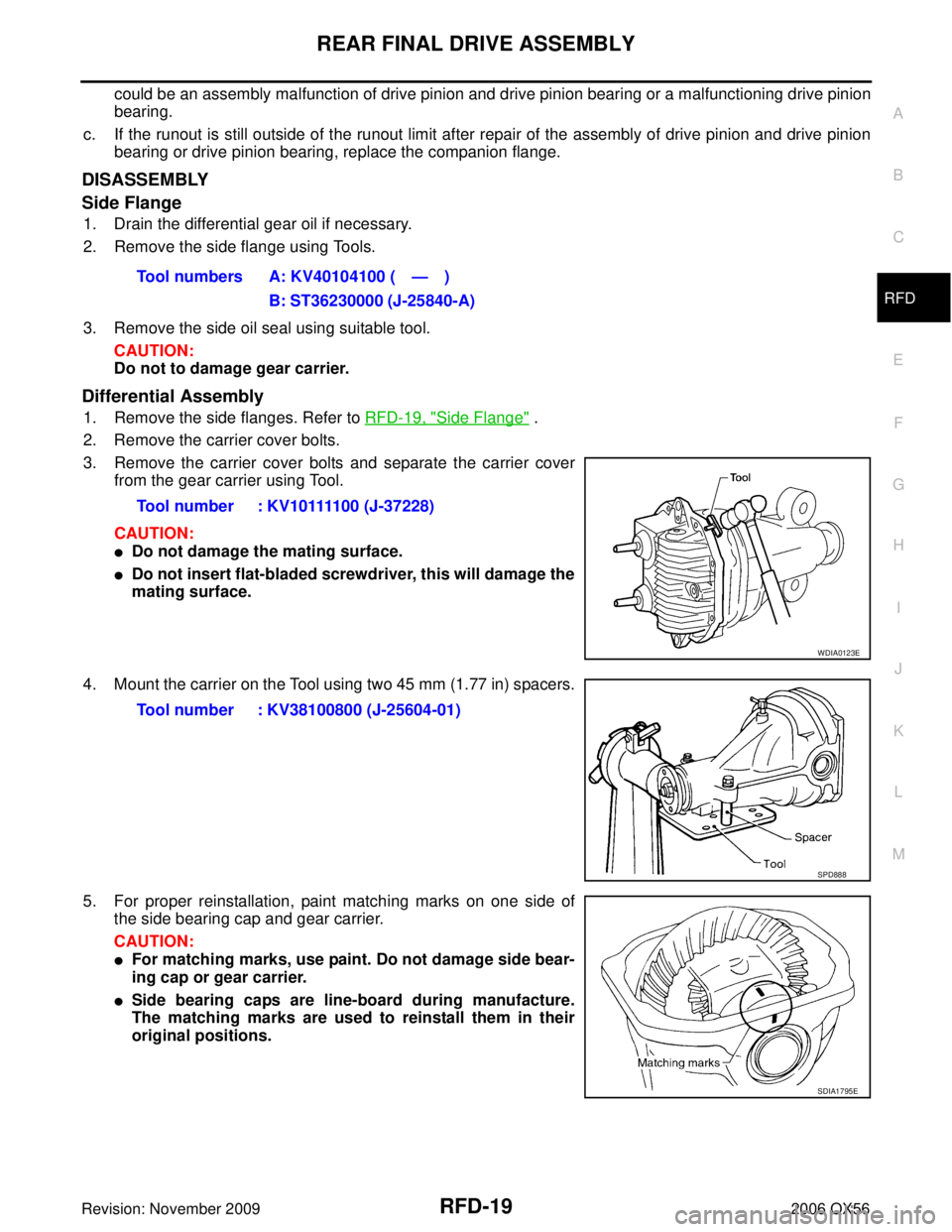
REAR FINAL DRIVE ASSEMBLYRFD-19
CE F
G H
I
J
K L
M A
B
RFD
Revision: November 2009 2006 QX56
could be an assembly malfunction of drive pinion and drive pinion bearing or a malfunctioning drive pinion
bearing.
c. If the runout is still outside of the runout limit after repair of the assembly of drive pinion and drive pinion bearing or drive pinion bearing, replace the companion flange.
DISASSEMBLY
Side Flange
1. Drain the differential gear oil if necessary.
2. Remove the side flange using Tools.
3. Remove the side oil seal using suitable tool.
CAUTION:
Do not to damage gear carrier.
Differential Assembly
1. Remove the side flanges. Refer to RFD-19, "Side Flange" .
2. Remove the carrier cover bolts.
3. Remove the carrier cover bolts and separate the carrier cover from the gear carrier using Tool.
CAUTION:
Do not damage the mating surface.
Do not insert flat-bladed screwdriver, this will damage the
mating surface.
4. Mount the carrier on the Tool using two 45 mm (1.77 in) spacers.
5. For proper reinstallation, paint matching marks on one side of the side bearing cap and gear carrier.
CAUTION:
For matching marks, use paint. Do not damage side bear-
ing cap or gear carrier.
Side bearing caps are line-board during manufacture.
The matching marks are used to reinstall them in their
original positions.Tool numbers A: KV40104100 ( — )
B: ST36230000 (J-25840-A)
Tool number : KV10111100 (J-37228)
WDIA0123E
Tool number : KV38100800 (J-25604-01)
SPD888
SDIA1795E
Page 2867 of 3383
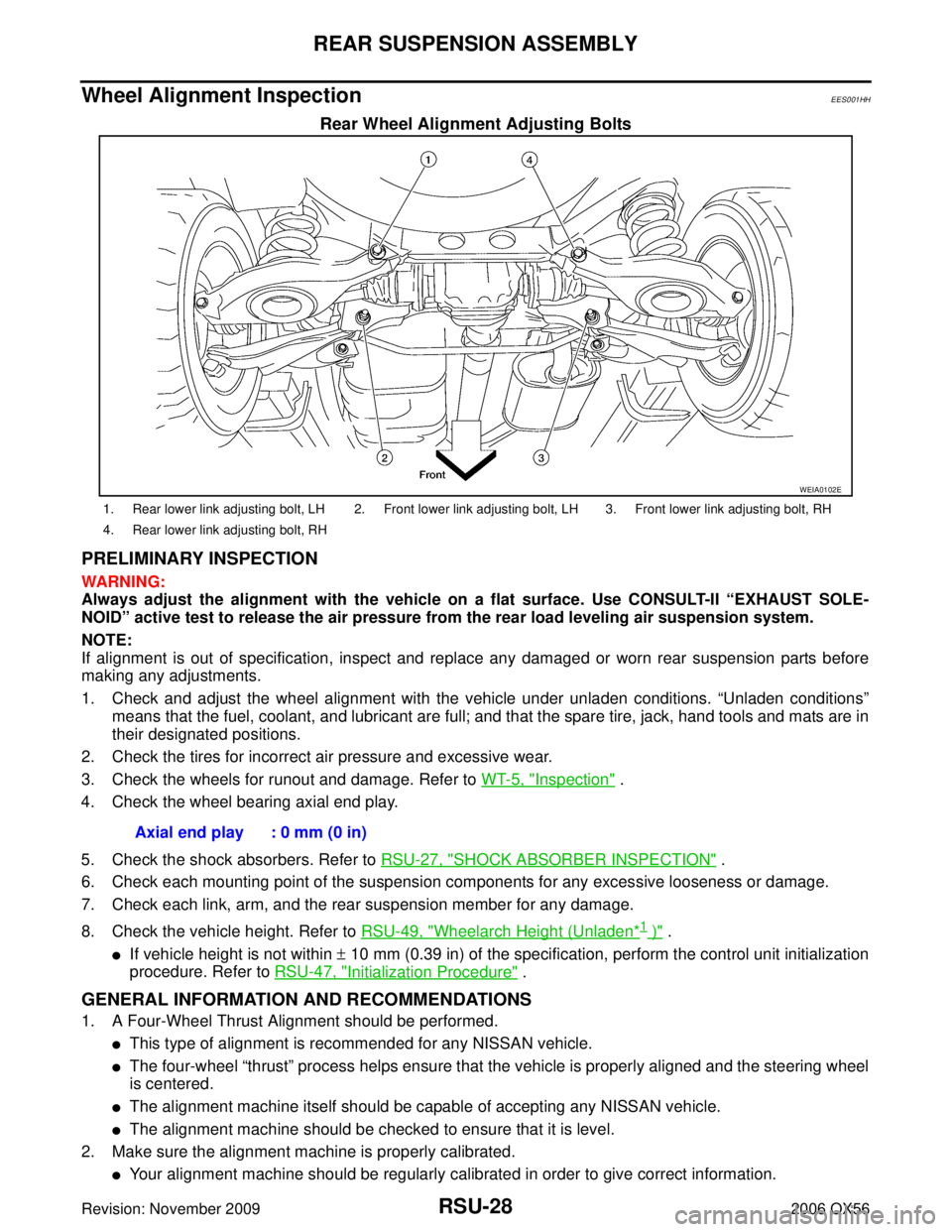
RSU-28
REAR SUSPENSION ASSEMBLY
Revision: November 20092006 QX56
Wheel Alignment InspectionEES001HH
Rear Wheel Alignment Adjusting Bolts
PRELIMINARY INSPECTION
WARNING:
Always adjust the alignment with the vehicle on a flat surface. Use CONSULT-II “EXHAUST SOLE-
NOID” active test to release the air pressure from the rear load leveling air suspension system.
NOTE:
If alignment is out of specification, inspect and replace any damaged or worn rear suspension parts before
making any adjustments.
1. Check and adjust the wheel alignment with the vehicle under unladen conditions. “Unladen conditions”
means that the fuel, coolant, and lubricant are full; and that the spare tire, jack, hand tools and mats are in
their designated positions.
2. Check the tires for incorrect air pressure and excessive wear.
3. Check the wheels for runout and damage. Refer to WT-5, "
Inspection" .
4. Check the wheel bearing axial end play.
5. Check the shock absorbers. Refer to RSU-27, "
SHOCK ABSORBER INSPECTION" .
6. Check each mounting point of the suspension components for any excessive looseness or damage.
7. Check each link, arm, and the rear suspension member for any damage.
8. Check the vehicle height. Refer to RSU-49, "
Wheelarch Height (Unladen*1 )" .
If vehicle height is not within ± 10 mm (0.39 in) of the specification, perform the control unit initialization
procedure. Refer to RSU-47, "
Initialization Procedure" .
GENERAL INFORMATION AND RECOMMENDATIONS
1. A Four-Wheel Thrust Alignment should be performed.
This type of alignment is recommended for any NISSAN vehicle.
The four-wheel “thrust” process helps ensure that the vehicle is properly aligned and the steering wheel
is centered.
The alignment machine itself should be capable of accepting any NISSAN vehicle.
The alignment machine should be checked to ensure that it is level.
2. Make sure the alignment machine is properly calibrated.
Your alignment machine should be regularly calibrated in order to give correct information.
WEIA0102E
1. Rear lower link adjusting bolt, LH 2. Front lower link adjusting bolt, LH 3. Front lower link adjusting bolt, RH
4. Rear lower link adjusting bolt, RH
Axial end play : 0 mm (0 in)
Page 3109 of 3383
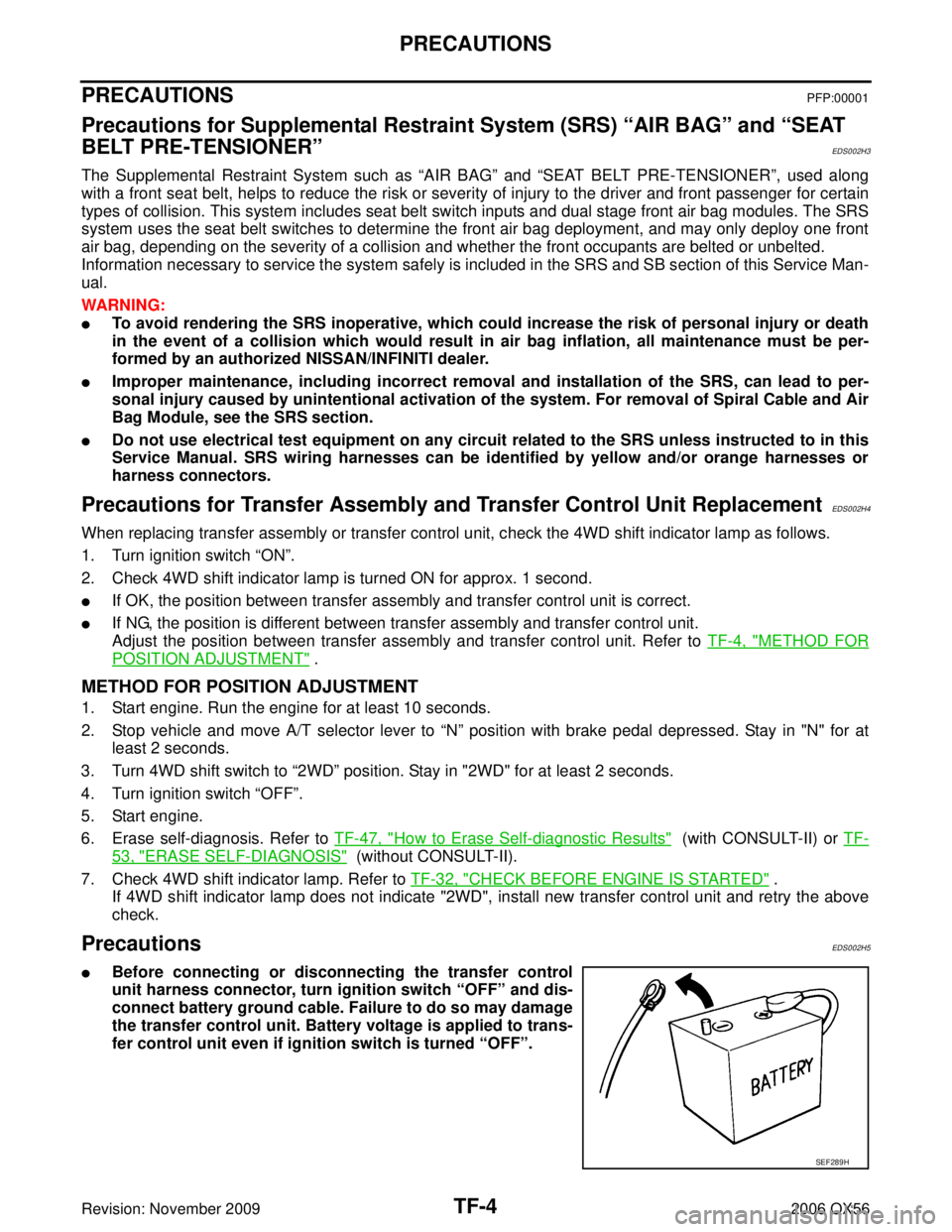
TF-4
PRECAUTIONS
Revision: November 20092006 QX56
PRECAUTIONSPFP:00001
Precautions for Supplemental Restraint System (SRS) “AIR BAG” and “SEAT
BELT PRE-TENSIONER”
EDS002H3
The Supplemental Restraint System such as “AIR BAG” and “SEAT BELT PRE-TENSIONER ”, used along
with a front seat belt, helps to reduce the risk or severity of injury to the driver and front passenger for certain
types of collision. This system includes seat belt switch inputs and dual stage front air bag modules. The SRS
system uses the seat belt switches to determine the front air bag deployment, and may only deploy one front
air bag, depending on the severity of a collision and whether the front occupants are belted or unbelted.
Information necessary to service the system safely is included in the SRS and SB section of this Service Man-
ual.
WARNING:
To avoid rendering the SRS inoperative, which could increase the risk of personal injury or death
in the event of a collision which would result in air bag inflation, all maintenance must be per-
formed by an authorized NISSAN/INFINITI dealer.
Improper maintenance, including incorrect removal and installation of the SRS, can lead to per-
sonal injury caused by unintentional activation of the system. For removal of Spiral Cable and Air
Bag Module, see the SRS section.
Do not use electrical test equipment on any circuit related to the SRS unless instructed to in this
Service Manual. SRS wiring harnesses can be identified by yellow and/or orange harnesses or
harness connectors.
Precautions for Transfer Assembly and Transfer Control Unit ReplacementEDS002H4
When replacing transfer assembly or transfer control unit, check the 4WD shift indicator lamp as follows.
1. Turn ignition switch “ON ”.
2. Check 4WD shift indicator lamp is turned ON for approx. 1 second.
If OK, the position between transfer assembly and transfer control unit is correct.
If NG, the position is different between transfer assembly and transfer control unit.
Adjust the position between transfer assembly and transfer control unit. Refer to TF-4, "
METHOD FOR
POSITION ADJUSTMENT" .
METHOD FOR POSITION ADJUSTMENT
1. Start engine. Run the engine for at least 10 seconds.
2. Stop vehicle and move A/T selector lever to “N” position with brake pedal depressed. Stay in "N" for at
least 2 seconds.
3. Turn 4WD shift switch to “2WD ” position. Stay in "2WD" for at least 2 seconds.
4. Turn ignition switch “ OFF”.
5. Start engine.
6. Erase self-diagnosis. Refer to TF-47, "
How to Erase Self-diagnostic Results" (with CONSULT-II) or TF-
53, "ERASE SELF-DIAGNOSIS" (without CONSULT-II).
7. Check 4WD shift indicator lamp. Refer to TF-32, "
CHECK BEFORE ENGINE IS STARTED" .
If 4WD shift indicator lamp does not indicate "2WD", install new transfer control unit and retry the above
check.
PrecautionsEDS002H5
Before connecting or disconnecting the transfer control
unit harness connector, turn ignition switch “OFF” and dis-
connect battery ground cable. Failure to do so may damage
the transfer control unit. Battery voltage is applied to trans-
fer control unit even if ignition switch is turned “OFF”.
SEF289H
Page 3294 of 3383
WHEELWT-5
C
DF
G H
I
J
K L
M A
B
WT
Revision: November 2009 2006 QX56
WHEELPFP:40300
InspectionEES001HZ
1. Check tires for wear and improper inflation.
2. Check wheels for deformation, cracks and other damage. If
deformed, remove wheel and check wheel runout.
a. Remove tire from wheel and mount wheel on a tire balance machine.
b. Set dial indicator as shown. Refer to WT-38, "
Road Wheel" .
3. Check front wheel bearings for looseness.
4. Check front suspension for looseness.
SFA975B