Page 125 of 801
YH4
GRAND
VITARA
1B-54 AIR CONDITIONING (OPTIONAL)
2
4) Remove shims from shaft.
5) Using special tool (C), remove circlip.
Special Tool
(C): 09900-06107
6) Remove clutch coil lead wire clamp screw, and remove clutch
coil read wire ground terminal.
7) Remove clutch pulley with puller (1) from compressor (2).
NOTE:
Be careful not to damage pulley when tapping magnet
clutch assembly.
8) Remove clutch coil.
Special tool
(C): 09900-06107
INSTALLATION
1) Install clutch coil (2).
Protrusion on under side of coil ring must match hole in com-
pressor (3) to prevent movement ant correctly locate lead wire.
2) Using special tool (C), install snap ring (1) as shown.
Special Tool
(C): 09990-06107
3) Install clamp portion and ground terminal of lead wire.
Page 127 of 801
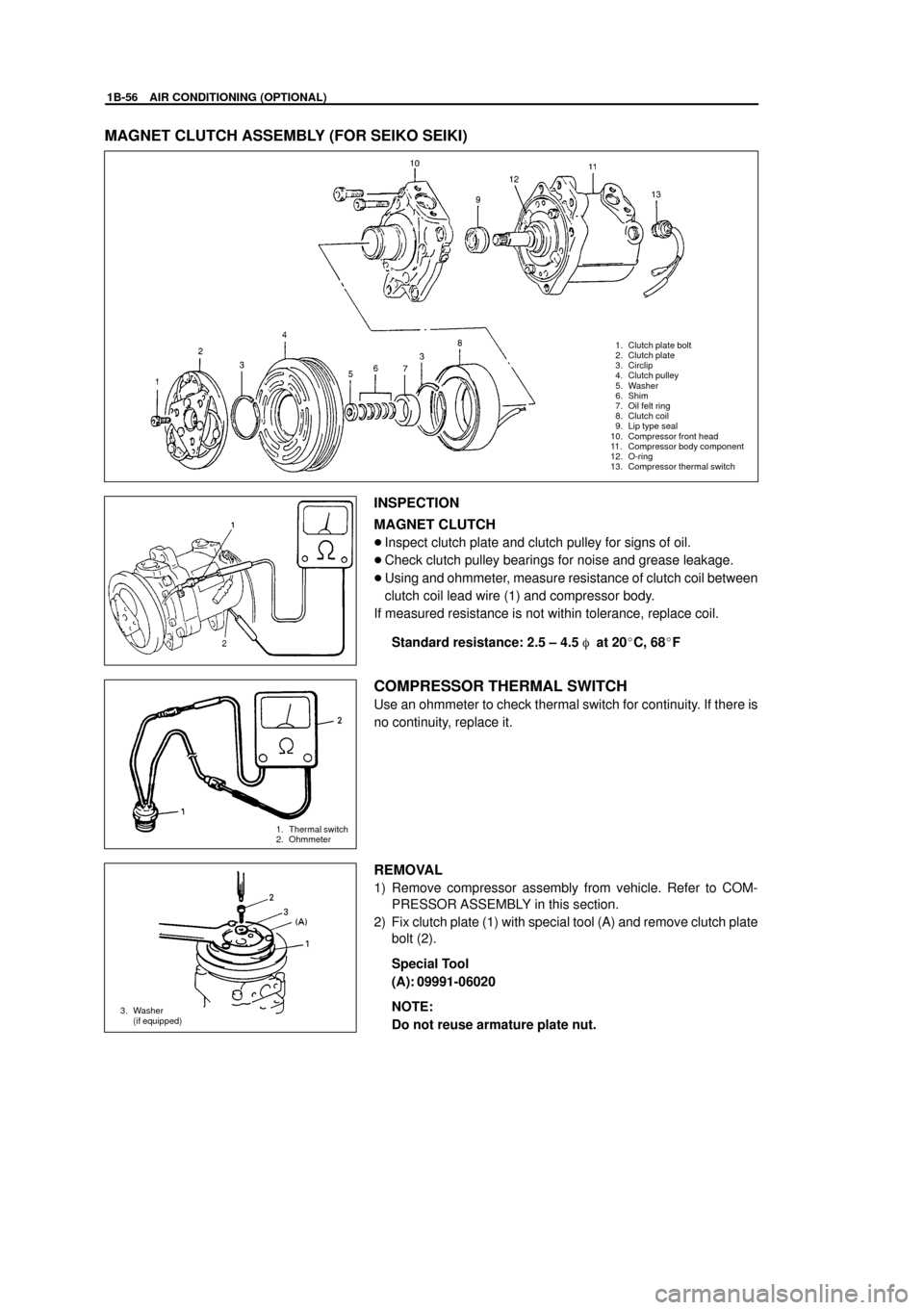
YH4
GRAND
VITARA
1B-56 AIR CONDITIONING (OPTIONAL)
1. Clutch plate bolt
2. Clutch plate
3. Circlip
4. Clutch pulley
5. Washer
6. Shim
7. Oil felt ring
8. Clutch coil
9. Lip type seal
10. Compressor front head
11. Compressor body component
12. O-ring
13. Compressor thermal switch
3. Washer
(if equipped)1. Thermal switch
2. Ohmmeter
MAGNET CLUTCH ASSEMBLY (FOR SEIKO SEIKI)
INSPECTION
MAGNET CLUTCH
Inspect clutch plate and clutch pulley for signs of oil.
Check clutch pulley bearings for noise and grease leakage.
Using and ohmmeter, measure resistance of clutch coil between
clutch coil lead wire (1) and compressor body.
If measured resistance is not within tolerance, replace coil.
Standard resistance: 2.5 ± 4.5 at 20C, 68F
COMPRESSOR THERMAL SWITCH
Use an ohmmeter to check thermal switch for continuity. If there is
no continuity, replace it.
REMOVAL
1) Remove compressor assembly from vehicle. Refer to COM-
PRESSOR ASSEMBLY in this section.
2) Fix clutch plate (1) with special tool (A) and remove clutch plate
bolt (2).
Special Tool
(A): 09991-06020
NOTE:
Do not reuse armature plate nut.
Page 128 of 801
YH4
GRAND
VITARA
AIR CONDITIONING (OPTIONAL) 1B-57
3) Using special tool (B), remove clutch plate (1).
Special Tool
(B): 09991-06030
4) Disconnect clutch coil lead wire from compressor thermal switch
led wire.
5) Remove felt ring (if equipped) and shims from shaft.
6) Using special tool (C), remove circlip.
Special Tool
(C): 09900-06107
7) Remove clutch coil lead wire clamp screw.
8) Remove clutch pulley with puller (1) from compressor (2).
NOTE:
Be careful not to damage pulley when tapping magnet
clutch.
9) Remove clutch coil.
INSTALLATION
1) Install clutch coil (2).
Protrusion on under side of clutch coil must match hole in com-
pressor (3) to prevent movement ant correctly locate lead wire.
2) Using special tool (C), install snap ring (1) as shown.
Special Tool
(C): 09990-06107
3) Clamp covering portion of lead wire.
Page 131 of 801
YH4
GRAND
VITARA
1B-60 AIR CONDITIONING (OPTIONAL)
1. Front head
2) Coat special tool (F) surface with oil and place it on the shaft.
Special Tool
(F): 09991-06040
3) Install O-ring (2) to case.
4) Apply compressor (refringent) oil to lip seal and O-ring.
5) Install compressor front head (1).
6) Tighten compressor front head bolt.
Tightening Torque
(a): 14 N
.m (1.4 kg-m, 10.5 lb-ft)
(b): 23 N
.m (2.3 kg-m, 17.0 lb-ft)
NOTE:
Be sure to use new front head bolt washer.
Tighten bolt (a) first, and next (b).
Page 132 of 801
YH4
GRAND
VITARA
AIR CONDITIONING (OPTIONAL) 1B-61
09900-06107
Snap ring pliers
(Opening type)09991-06010
Magnet clutch pulley installer09991-06020
Armature plate spanner09991-06030
Armature plate remover
09991-06040
Lip type seal protector09991-06050
Lip type seal installer
REQUIRED SERVICE MATERIAL
MATERIALRECOMMENDED
SUZUKI PRODUCTUSE
Compressor oil for DENSO
compressor (Refrigerant oil)COMPRESSOR OIL (ND-OIL 8, 250 cc)
99000-27080O-ring
Each component
Compressor oil for
SEIKO SEIKI compressor
(Refrigerant oil)COMPRESSOR OIL RS20 (150 cc)
99000-99088-00DO-ring
Each component
RefrigerantREFRIGERANT DRUM (200 g)
95794-50G00Refrigerant charge
SPECIAL TOOLS
Page 148 of 801
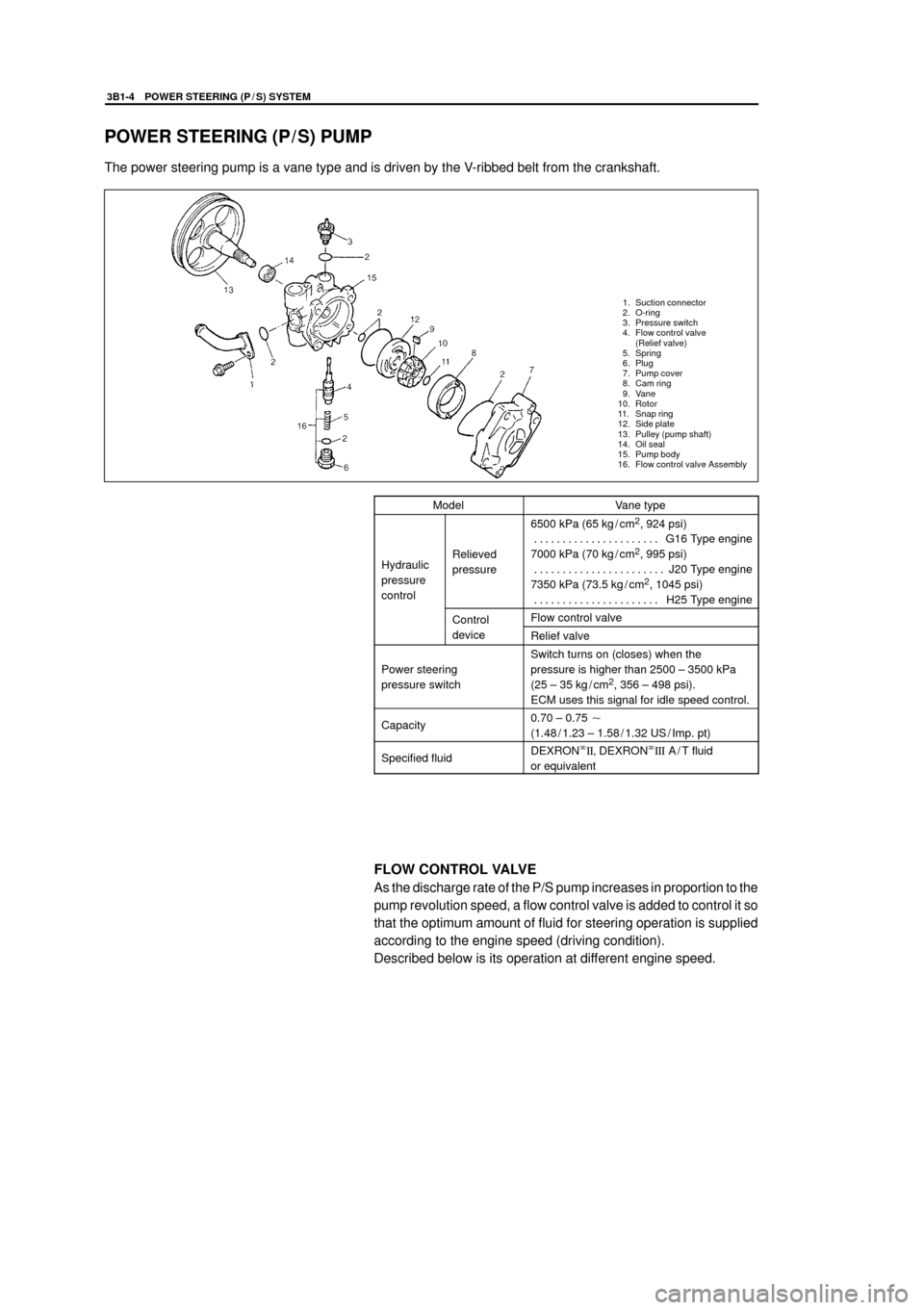
YH4
GRAND
VITARA
1. Suction connector
2. O-ring
3. Pressure switch
4. Flow control valve
(Relief valve)
5. Spring
6. Plug
7. Pump cover
8. Cam ring
9. Vane
10. Rotor
11. Snap ring
12. Side plate
13. Pulley (pump shaft)
14. Oil seal
15. Pump body
16. Flow control valve Assembly
3B1-4 POWER STEERING (P / S) SYSTEM
POWER STEERING (P / S) PUMP
The power steering pump is a vane type and is driven by the V-ribbed belt from the crankshaft.
ModelVane type
Hydraulic
pressure
controlRelieved
pressure
6500 kPa (65 kg / cm2, 924 psi)
G16 Type engine . . . . . . . . . . . . . . . . . . . . . .
7000 kPa (70 kg / cm
2, 995 psi)
J20 Type engine . . . . . . . . . . . . . . . . . . . . . . .
7350 kPa (73.5 kg / cm
2, 1045 psi)
H25 Type engine . . . . . . . . . . . . . . . . . . . . . .
ControlFlow control valve
deviceRelief valve
Power steering
pressure switch
Switch turns on (closes) when the
pressure is higher than 2500 ± 3500 kPa
(25 ± 35 kg / cm
2, 356 ± 498 psi).
ECM uses this signal for idle speed control.
Capacity0.70 ± 0.75
(1.48 / 1.23 ± 1.58 / 1.32 US / Imp. pt)
Specified fluidDEXRONII, DEXRONIII A / T fluid
or equivalent
FLOW CONTROL VALVE
As the discharge rate of the P/S pump increases in proportion to the
pump revolution speed, a flow control valve is added to control it so
that the optimum amount of fluid for steering operation is supplied
according to the engine speed (driving condition).
Described below is its operation at different engine speed.
Page 154 of 801
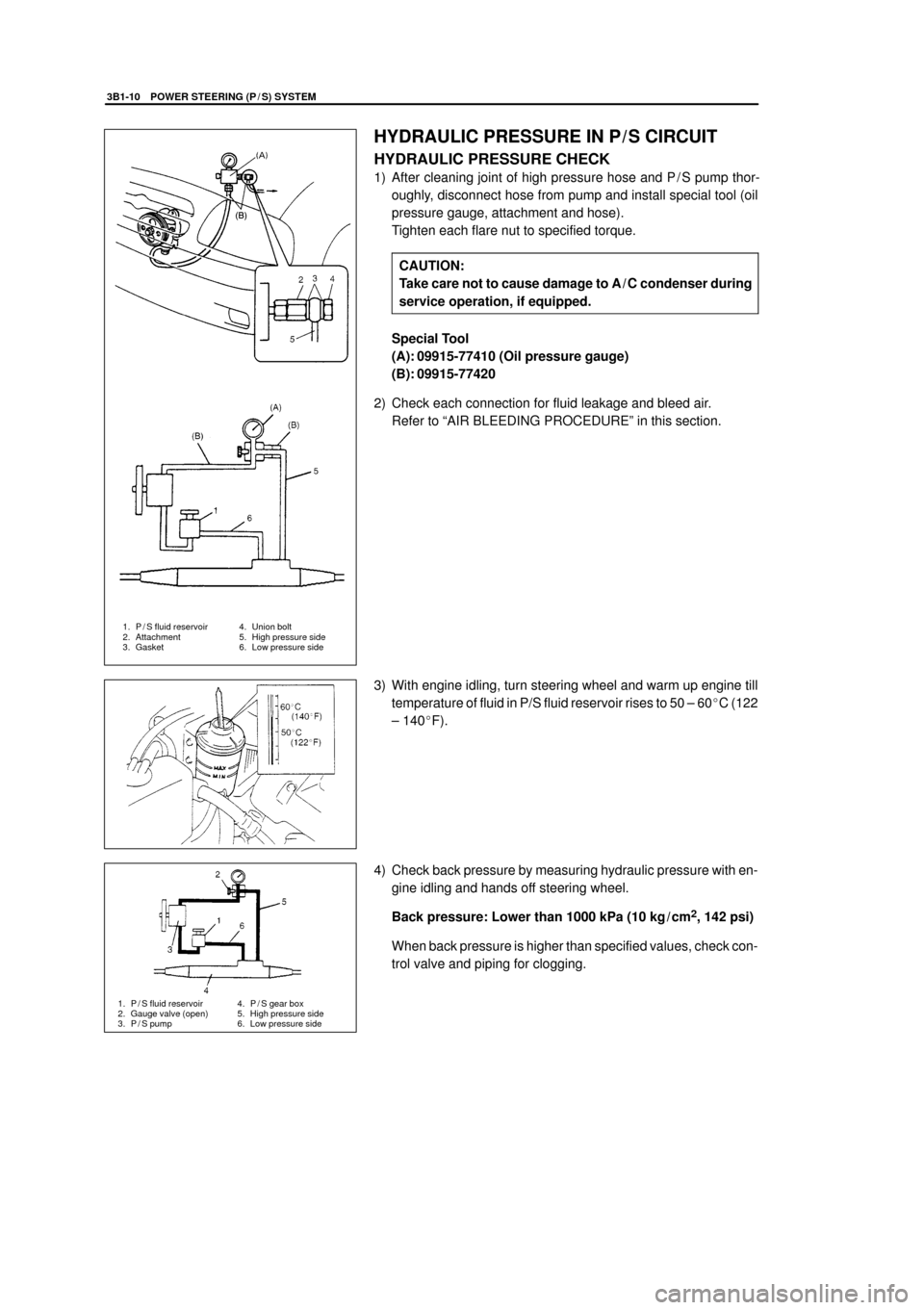
YH4
GRAND
VITARA
1. P / S fluid reservoir
2. Attachment
3. Gasket4. Union bolt
5. High pressure side
6. Low pressure side
1. P / S fluid reservoir
2. Gauge valve (open)
3. P / S pump4. P / S gear box
5. High pressure side
6. Low pressure side
3B1-10 POWER STEERING (P / S) SYSTEM
HYDRAULIC PRESSURE IN P / S CIRCUIT
HYDRAULIC PRESSURE CHECK
1) After cleaning joint of high pressure hose and P / S pump thor-
oughly, disconnect hose from pump and install special tool (oil
pressure gauge, attachment and hose).
Tighten each flare nut to specified torque.
CAUTION:
Take care not to cause damage to A / C condenser during
service operation, if equipped.
Special Tool
(A): 09915-77410 (Oil pressure gauge)
(B): 09915-77420
2) Check each connection for fluid leakage and bleed air.
Refer to ªAIR BLEEDING PROCEDUREº in this section.
3) With engine idling, turn steering wheel and warm up engine till
temperature of fluid in P/S fluid reservoir rises to 50 ± 60C (122
± 140F).
4) Check back pressure by measuring hydraulic pressure with en-
gine idling and hands off steering wheel.
Back pressure: Lower than 1000 kPa (10 kg / cm
2, 142 psi)
When back pressure is higher than specified values, check con-
trol valve and piping for clogging.
Page 155 of 801
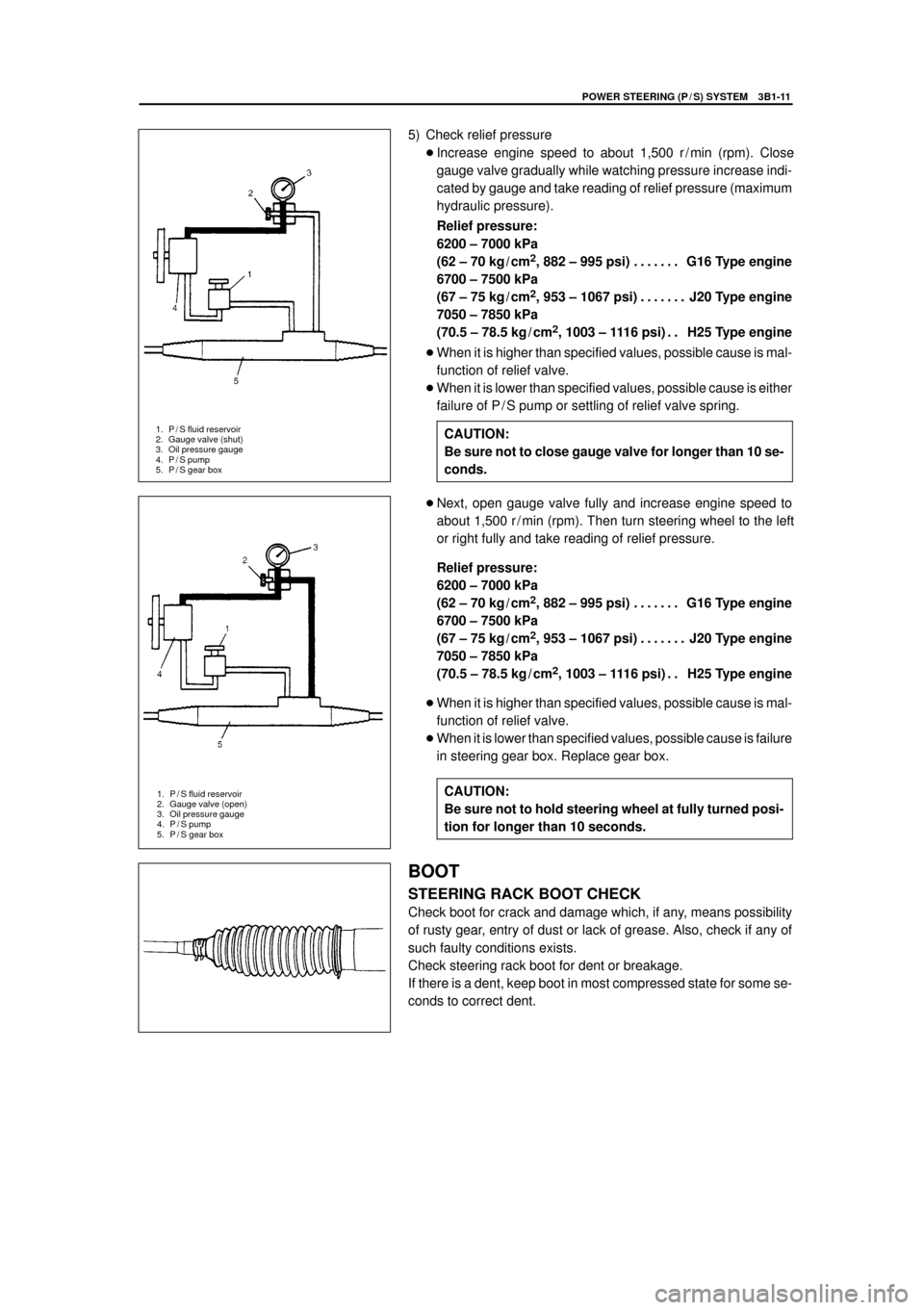
YH4
GRAND
VITARA
1. P / S fluid reservoir
2. Gauge valve (shut)
3. Oil pressure gauge
4. P / S pump
5. P / S gear box
1. P / S fluid reservoir
2. Gauge valve (open)
3. Oil pressure gauge
4. P / S pump
5. P / S gear box
POWER STEERING (P / S) SYSTEM 3B1-11
5) Check relief pressure
Increase engine speed to about 1,500 r / min (rpm). Close
gauge valve gradually while watching pressure increase indi-
cated by gauge and take reading of relief pressure (maximum
hydraulic pressure).
Relief pressure:
6200 ± 7000 kPa
(62 ± 70 kg / cm
2, 882 ± 995 psi) G16 Type engine. . . . . . .
6700 ± 7500 kPa
(67 ± 75 kg / cm
2, 953 ± 1067 psi) J20 Type engine. . . . . . .
7050 ± 7850 kPa
(70.5 ± 78.5 kg / cm
2, 1003 ± 1116 psi) H25 Type engine. .
When it is higher than specified values, possible cause is mal-
function of relief valve.
When it is lower than specified values, possible cause is either
failure of P / S pump or settling of relief valve spring.
CAUTION:
Be sure not to close gauge valve for longer than 10 se-
conds.
Next, open gauge valve fully and increase engine speed to
about 1,500 r / min (rpm). Then turn steering wheel to the left
or right fully and take reading of relief pressure.
Relief pressure:
6200 ± 7000 kPa
(62 ± 70 kg / cm
2, 882 ± 995 psi) G16 Type engine. . . . . . .
6700 ± 7500 kPa
(67 ± 75 kg / cm
2, 953 ± 1067 psi) J20 Type engine. . . . . . .
7050 ± 7850 kPa
(70.5 ± 78.5 kg / cm
2, 1003 ± 1116 psi) H25 Type engine. .
When it is higher than specified values, possible cause is mal-
function of relief valve.
When it is lower than specified values, possible cause is failure
in steering gear box. Replace gear box.
CAUTION:
Be sure not to hold steering wheel at fully turned posi-
tion for longer than 10 seconds.
BOOT
STEERING RACK BOOT CHECK
Check boot for crack and damage which, if any, means possibility
of rusty gear, entry of dust or lack of grease. Also, check if any of
such faulty conditions exists.
Check steering rack boot for dent or breakage.
If there is a dent, keep boot in most compressed state for some se-
conds to correct dent.