Page 81 of 788
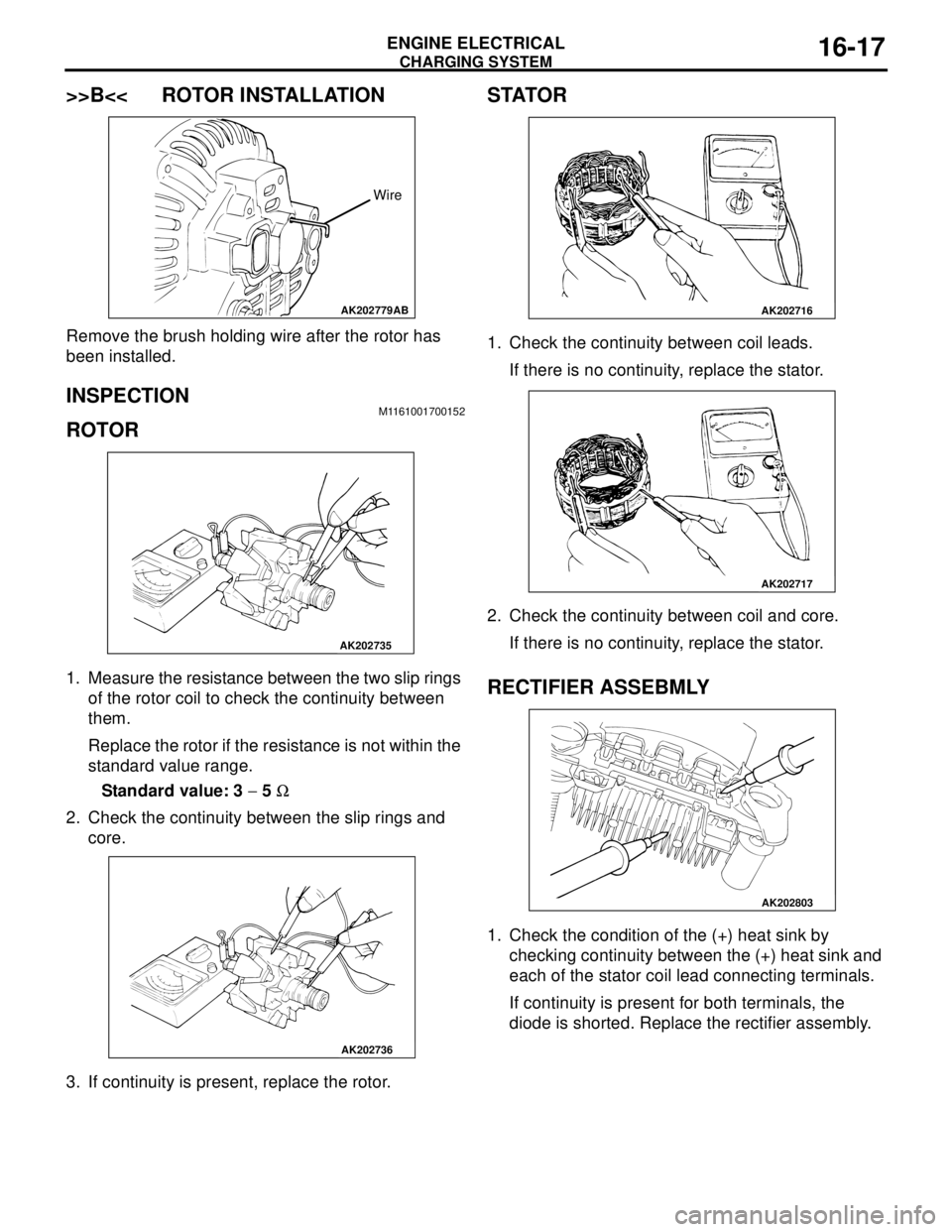
CHARGING SYSTEM
ENGINE ELECTRICAL16-17
>>B<< ROTOR INSTALLATION
Remove the brush holding wire after the rotor has
been installed.
INSPECTION M1161001700152
ROTOR
1. Measure the resistance between the two slip rings
of the rotor coil to check the continuity between
them.
Replace the rotor if the resistance is not within the
standard value range.
Standard value: 3 − 5 Ω
2. Check the continuity between the slip rings and
core.
3. If continuity is present, replace the rotor.
STATOR
1. Check the continuity between coil leads.
If there is no continuity, replace the stator.
2. Check the continuity between coil and core.
If there is no continuity, replace the stator.
RECTIFIER ASSEBMLY
1. Check the condition of the (+) heat sink by
checking continuity between the (+) heat sink and
each of the stator coil lead connecting terminals.
If continuity is present for both terminals, the
diode is shorted. Replace the rectifier assembly.
AK202779
Wire
AB
AK202735
AK202736
AK202716
AK202717
AK202803
Page 82 of 788
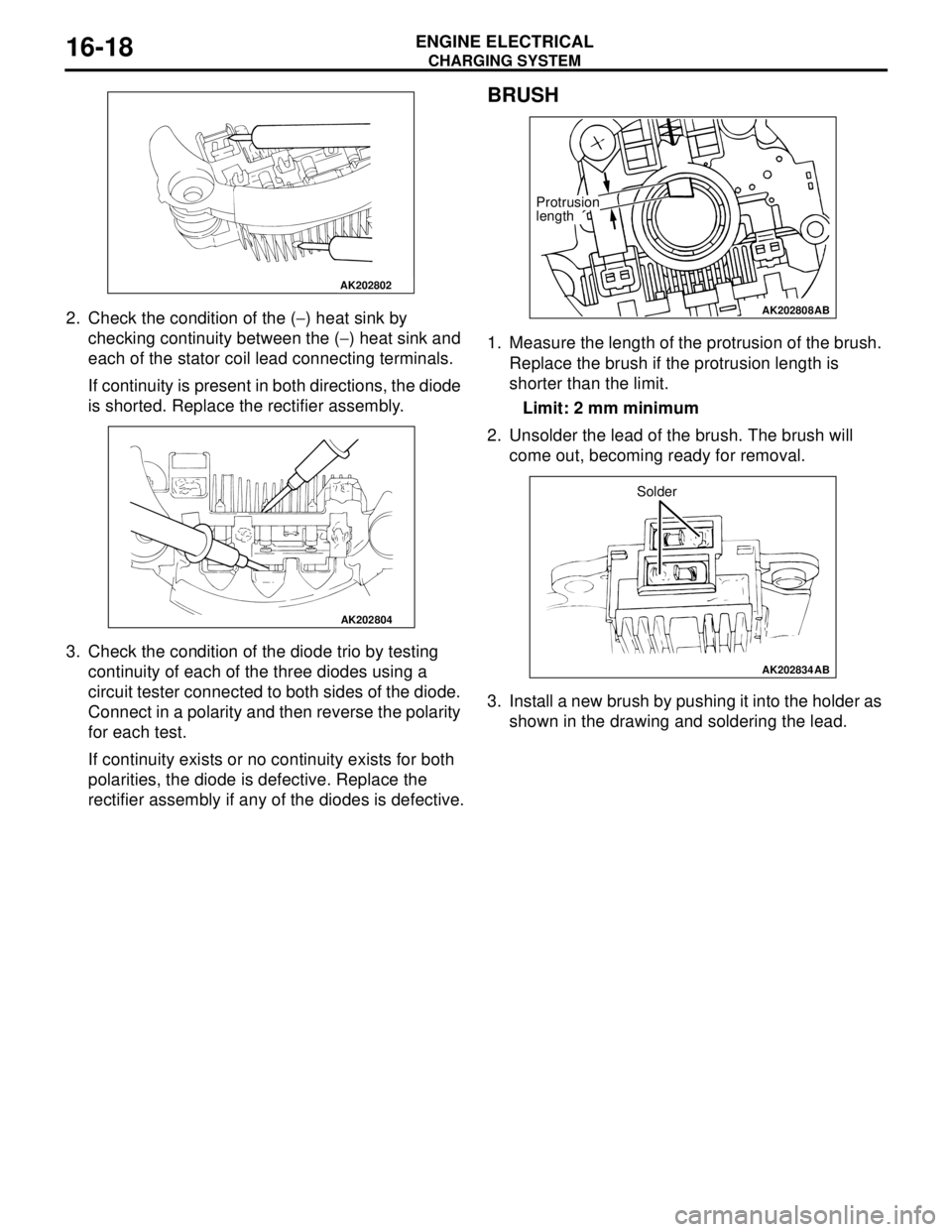
CHARGING SYSTEM
ENGINE ELECTRICAL16-18
2. Check the condition of the (−) heat sink by
checking continuity between the (−) heat sink and
each of the stator coil lead connecting terminals.
If continuity is present in both directions, the diode
is shorted. Replace the rectifier assembly.
3. Check the condition of the diode trio by testing
continuity of each of the three diodes using a
circuit tester connected to both sides of the diode.
Connect in a polarity and then reverse the polarity
for each test.
If continuity exists or no continuity exists for both
polarities, the diode is defective. Replace the
rectifier assembly if any of the diodes is defective.
BRUSH
1. Measure the length of the protrusion of the brush.
Replace the brush if the protrusion length is
shorter than the limit.
Limit: 2 mm minimum
2. Unsolder the lead of the brush. The brush will
come out, becoming ready for removal.
3. Install a new brush by pushing it into the holder as
shown in the drawing and soldering the lead.
AK202802
AK202804
AK202808
Protrusion
length
AB
AK202834
Solder
AB
Page 87 of 788
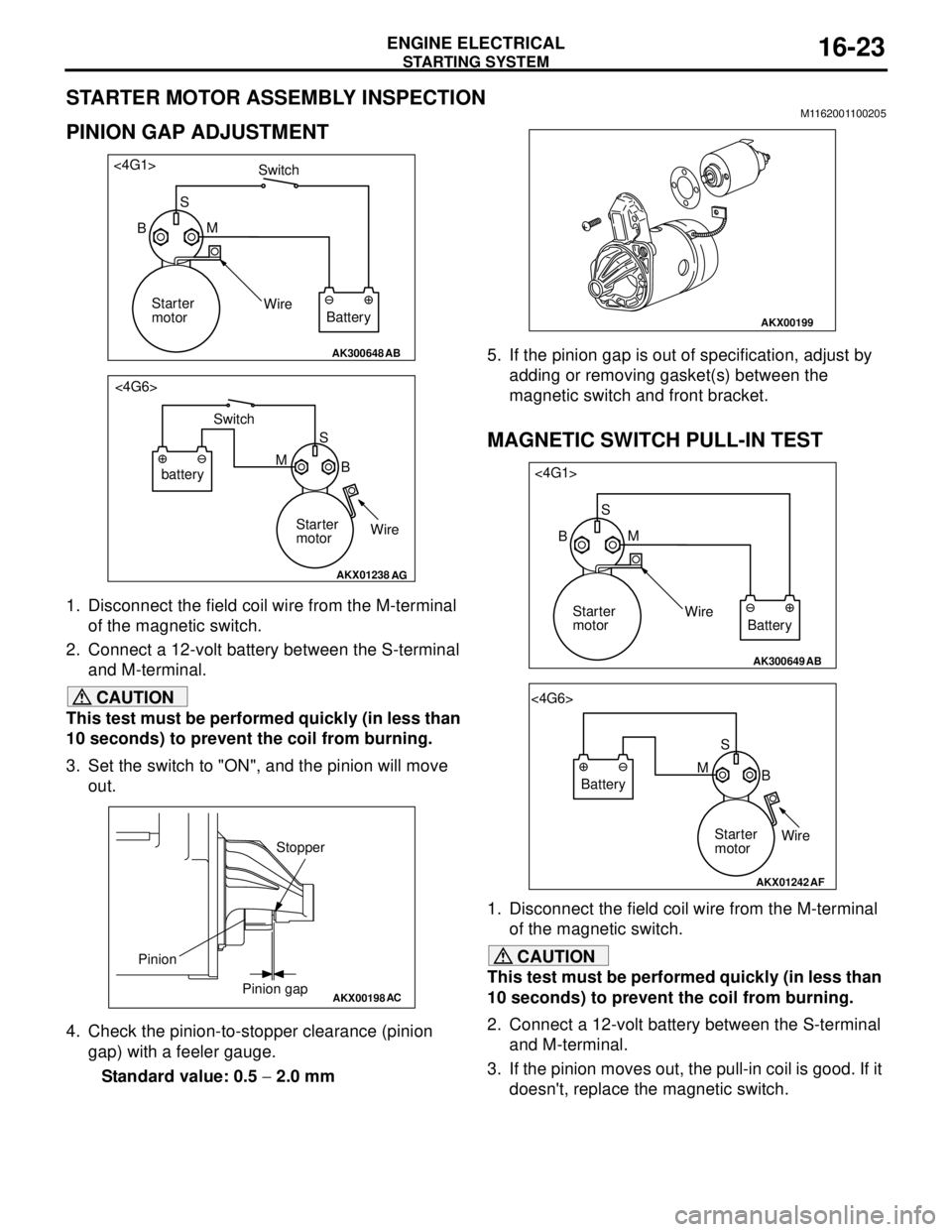
STARTING SYSTEM
ENGINE ELECTRICAL16-23
STARTER MOTOR ASSEMBLY INSPECTIONM1162001100205
PINION GAP ADJUSTMENT
1. Disconnect the field coil wire from the M-terminal
of the magnetic switch.
2. Connect a 12-volt battery between the S-terminal
and M-terminal.
CAUTION
This test must be performed quickly (in less than
10 seconds) to prevent the coil from burning.
3. Set the switch to "ON", and the pinion will move
out.
4. Check the pinion-to-stopper clearance (pinion
gap) with a feeler gauge.
Standard value: 0.5 − 2.0 mm5. If the pinion gap is out of specification, adjust by
adding or removing gasket(s) between the
magnetic switch and front bracket.
MAGNETIC SWITCH PULL-IN TEST
1. Disconnect the field coil wire from the M-terminal
of the magnetic switch.
CAUTION
This test must be performed quickly (in less than
10 seconds) to prevent the coil from burning.
2. Connect a 12-volt battery between the S-terminal
and M-terminal.
3. If the pinion moves out, the pull-in coil is good. If it
doesn't, replace the magnetic switch.
AK300648AB
<4G1>
Switch
S
M
Wire
Battery Starter
motor B
AKX01238
<4G6>
B MS
batterySwitch
Starter
motorWire
AG
AKX00198
Stopper
Pinion gap Pinion
AC
AKX00199
AK300649AB
<4G1>
S
M
Wire
Battery Starter
motor B
AKX01242
<4G6>
S
B M
Battery
Starter
motorWire
AF
Page 92 of 788
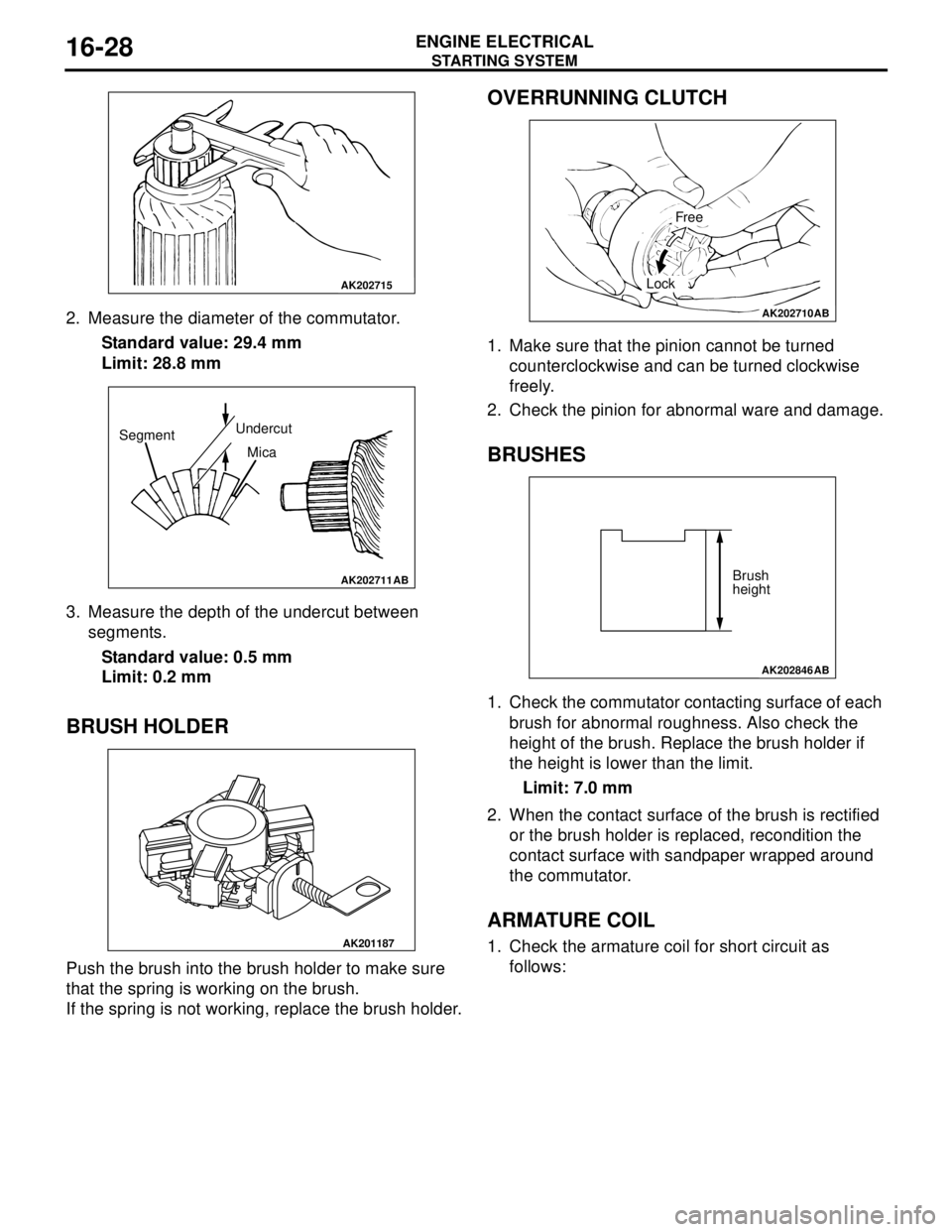
STARTING SYSTEM
ENGINE ELECTRICAL16-28
2. Measure the diameter of the commutator.
Standard value: 29.4 mm
Limit: 28.8 mm
3. Measure the depth of the undercut between
segments.
Standard value: 0.5 mm
Limit: 0.2 mm
BRUSH HOLDER
Push the brush into the brush holder to make sure
that the spring is working on the brush.
If the spring is not working, replace the brush holder.
OVERRUNNING CLUTCH
1. Make sure that the pinion cannot be turned
counterclockwise and can be turned clockwise
freely.
2. Check the pinion for abnormal ware and damage.
BRUSHES
1. Check the commutator contacting surface of each
brush for abnormal roughness. Also check the
height of the brush. Replace the brush holder if
the height is lower than the limit.
Limit: 7.0 mm
2. When the contact surface of the brush is rectified
or the brush holder is replaced, recondition the
contact surface with sandpaper wrapped around
the commutator.
ARMATURE COIL
1. Check the armature coil for short circuit as
follows:
AK202715
AK202711
SegmentUndercut
Mica
AB
AK201187
AK202710
Free
Lock
AB
AK202846
Brush
height
AB
Page 93 of 788
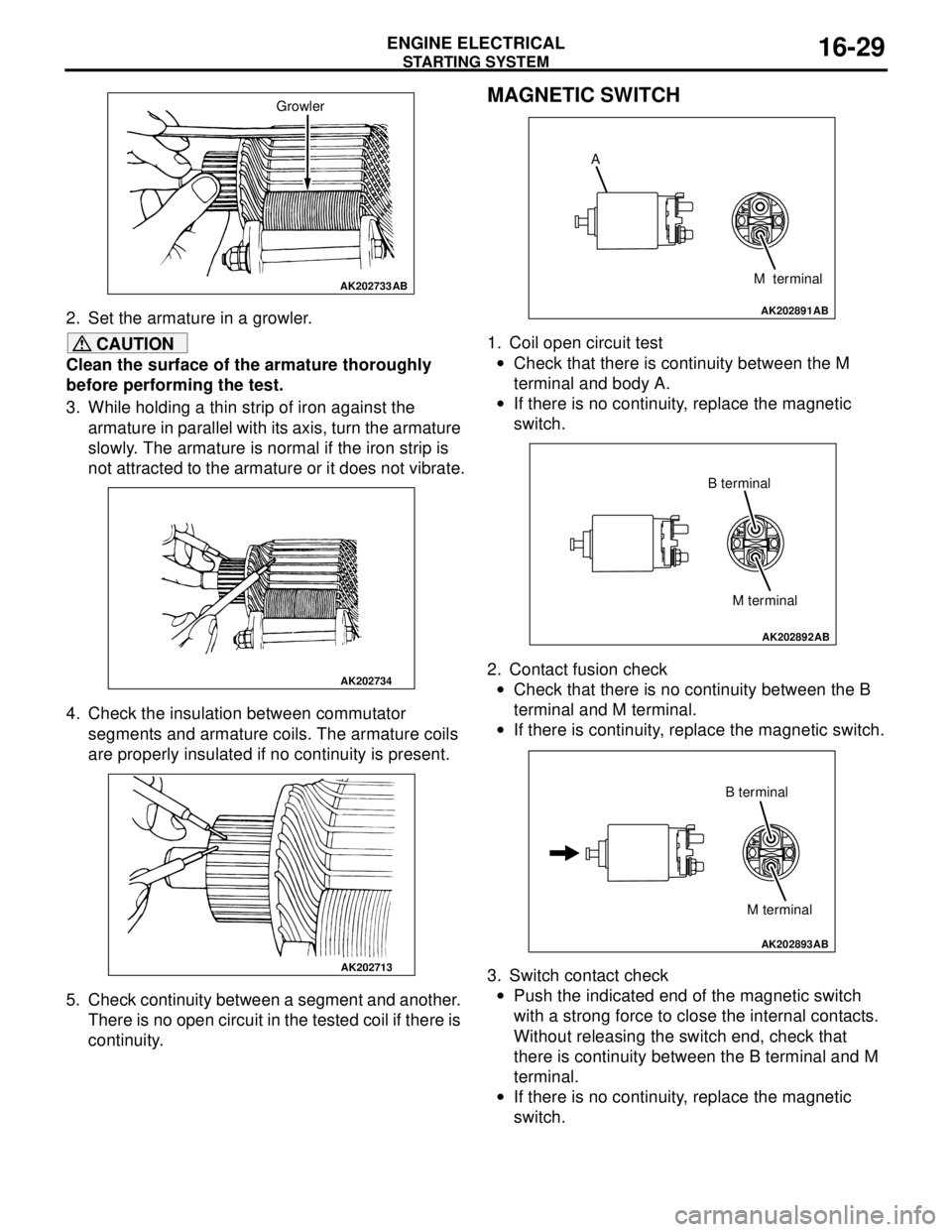
STARTING SYSTEM
ENGINE ELECTRICAL16-29
2. Set the armature in a growler.
CAUTION
Clean the surface of the armature thoroughly
before performing the test.
3. While holding a thin strip of iron against the
armature in parallel with its axis, turn the armature
slowly. The armature is normal if the iron strip is
not attracted to the armature or it does not vibrate.
4. Check the insulation between commutator
segments and armature coils. The armature coils
are properly insulated if no continuity is present.
5. Check continuity between a segment and another.
There is no open circuit in the tested coil if there is
continuity.
MAGNETIC SWITCH
1. Coil open circuit test
•Check that there is continuity between the M
terminal and body A.
•If there is no continuity, replace the magnetic
switch.
2. Contact fusion check
•Check that there is no continuity between the B
terminal and M terminal.
•If there is continuity, replace the magnetic switch.
3. Switch contact check
•Push the indicated end of the magnetic switch
with a strong force to close the internal contacts.
Without releasing the switch end, check that
there is continuity between the B terminal and M
terminal.
•If there is no continuity, replace the magnetic
switch.
AK202733
Growler
AB
AK202734
AK202713
AK202891
A
M terminal
AB
AK202892
M terminal B terminal
AB
AK202893
M terminal B terminal
AB
Page 96 of 788
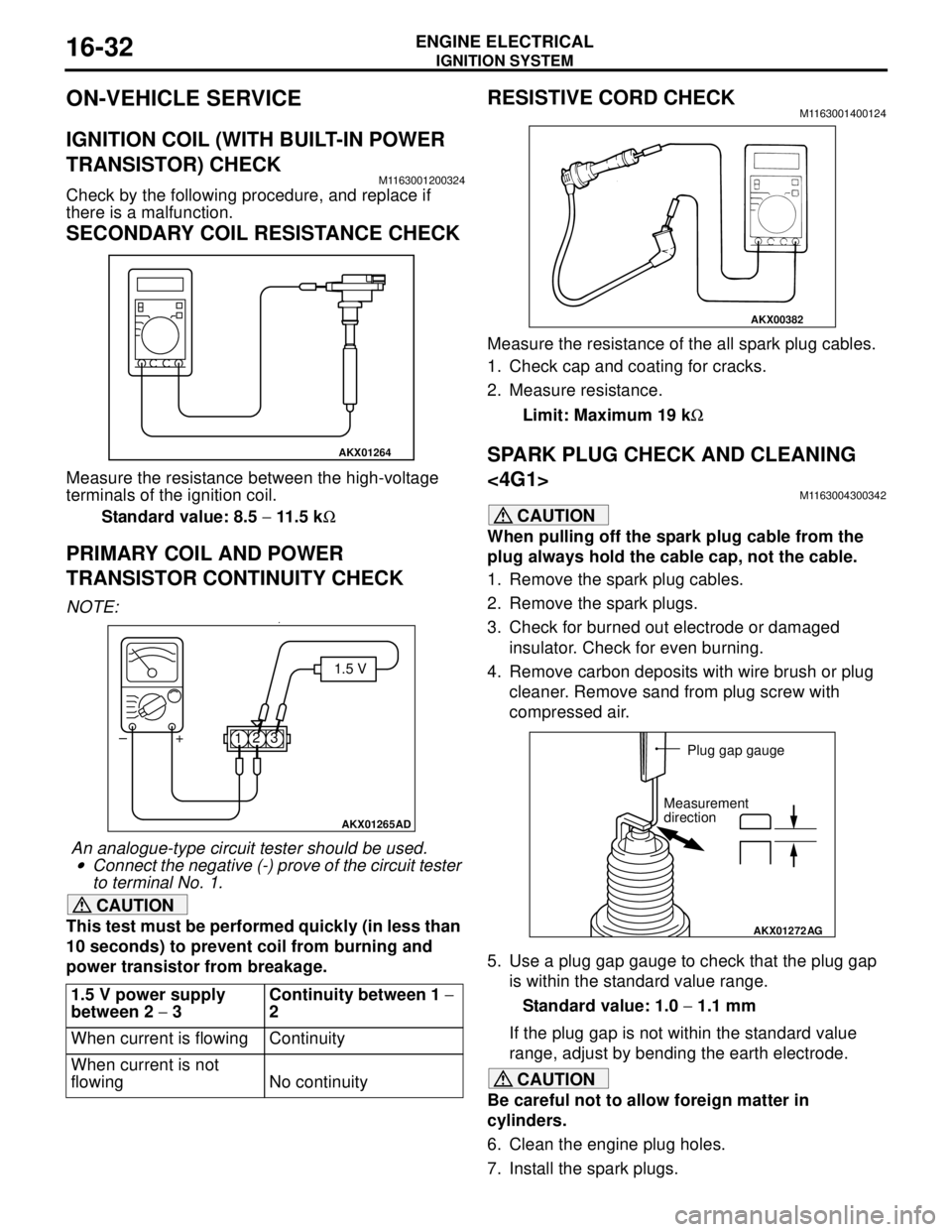
IGNITION SYSTEM
ENGINE ELECTRICAL16-32
ON-VEHICLE SERVICE
IGNITION COIL (WITH BUILT-IN POWER
TRANSISTOR) CHECK
M1163001200324
Check by the following procedure, and replace if
there is a malfunction.
SECONDARY COIL RESISTANCE CHECK
Measure the resistance between the high-voltage
terminals of the ignition coil.
Standard value: 8.5 − 11.5 kΩ
PRIMARY COIL AND POWER
TRANSISTOR CONTINUITY CHECK
NOTE: .•
An analogue-type circuit tester should be used.
•Connect the negative (-) prove of the circuit tester
to terminal No. 1.
CAUTION
This test must be performed quickly (in less than
10 seconds) to prevent coil from burning and
power transistor from breakage.
RESISTIVE CORD CHECKM1163001400124
Measure the resistance of the all spark plug cables.
1. Check cap and coating for cracks.
2. Measure resistance.
Limit: Maximum 19 kΩ
SPARK PLUG CHECK AND CLEANING
<4G1>
M1163004300342
CAUTION
When pulling off the spark plug cable from the
plug always hold the cable cap, not the cable.
1. Remove the spark plug cables.
2. Remove the spark plugs.
3. Check for burned out electrode or damaged
insulator. Check for even burning.
4. Remove carbon deposits with wire brush or plug
cleaner. Remove sand from plug screw with
compressed air.
5. Use a plug gap gauge to check that the plug gap
is within the standard value range.
Standard value: 1.0 − 1.1 mm
If the plug gap is not within the standard value
range, adjust by bending the earth electrode.
CAUTION
Be careful not to allow foreign matter in
cylinders.
6. Clean the engine plug holes.
7. Install the spark plugs. 1.5 V power supply
between 2 − 3Continuity between 1 −
2
When current is flowing Continuity
When current is not
flowing No continuity
AKX01264
AKX01265AD
1.5 V
123 +
–
AKX00382
AKX01272
AG
Plug gap gauge
Measurement
direction
Page 97 of 788
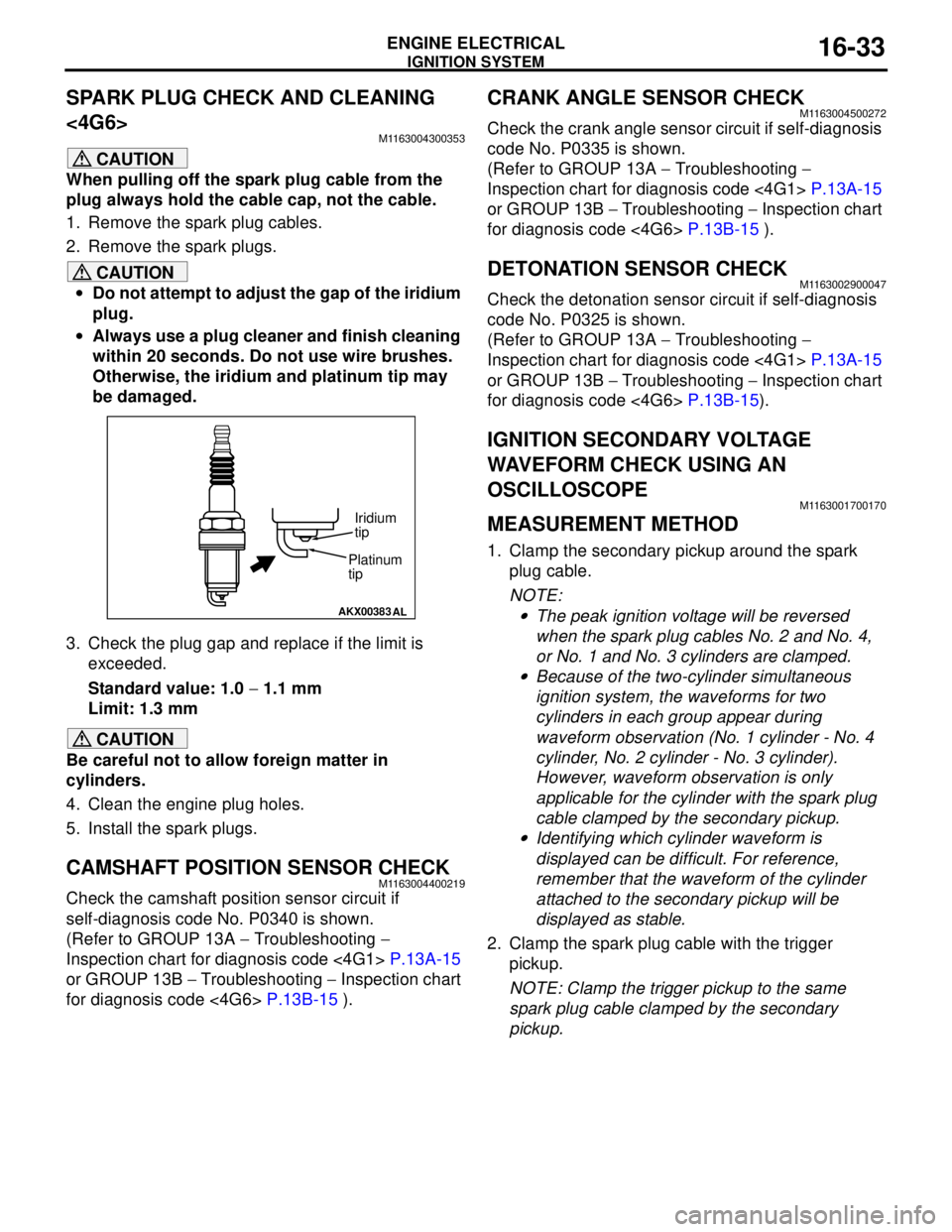
IGNITION SYSTEM
ENGINE ELECTRICAL16-33
SPARK PLUG CHECK AND CLEANING
<4G6>
M1163004300353
CAUTION
When pulling off the spark plug cable from the
plug always hold the cable cap, not the cable.
1. Remove the spark plug cables.
2. Remove the spark plugs.
CAUTION
•Do not attempt to adjust the gap of the iridium
plug.
•Always use a plug cleaner and finish cleaning
within 20 seconds. Do not use wire brushes.
Otherwise, the iridium and platinum tip may
be damaged.
3. Check the plug gap and replace if the limit is
exceeded.
Standard value: 1.0 − 1.1 mm
Limit: 1.3 mm
CAUTION
Be careful not to allow foreign matter in
cylinders.
4. Clean the engine plug holes.
5. Install the spark plugs.
CAMSHAFT POSITION SENSOR CHECKM1163004400219
Check the camshaft position sensor circuit if
self-diagnosis code No. P0340 is shown.
(Refer to GROUP 13A − Troubleshooting −
Inspection chart for diagnosis code <4G1> P.13A-15
or GROUP 13B − Troubleshooting − Inspection chart
for diagnosis code <4G6> P.13B-15 ).
CRANK ANGLE SENSOR CHECKM1163004500272
Check the crank angle sensor circuit if self-diagnosis
code No. P0335 is shown.
(Refer to GROUP 13A − Troubleshooting −
Inspection chart for diagnosis code <4G1> P.13A-15
or GROUP 13B − Troubleshooting − Inspection chart
for diagnosis code <4G6> P.13B-15 ).
DETONATION SENSOR CHECKM1163002900047
Check the detonation sensor circuit if self-diagnosis
code No. P0325 is shown.
(Refer to GROUP 13A − Troubleshooting −
Inspection chart for diagnosis code <4G1> P.13A-15
or GROUP 13B − Troubleshooting − Inspection chart
for diagnosis code <4G6> P.13B-15).
IGNITION SECONDARY VOLTAGE
WAVEFORM CHECK USING AN
OSCILLOSCOPE
M1163001700170
MEASUREMENT METHOD
1. Clamp the secondary pickup around the spark
plug cable.
NOTE: .
•The peak ignition voltage will be reversed
when the spark plug cables No. 2 and No. 4,
or No. 1 and No. 3 cylinders are clamped.
•Because of the two-cylinder simultaneous
ignition system, the waveforms for two
cylinders in each group appear during
waveform observation (No. 1 cylinder - No. 4
cylinder, No. 2 cylinder - No. 3 cylinder).
However, waveform observation is only
applicable for the cylinder with the spark plug
cable clamped by the secondary pickup.
•Identifying which cylinder waveform is
displayed can be difficult. For reference,
remember that the waveform of the cylinder
attached to the secondary pickup will be
displayed as stable.
2. Clamp the spark plug cable with the trigger
pickup.
NOTE: Clamp the trigger pickup to the same
spark plug cable clamped by the secondary
pickup.
AKX00383
AL
Platinum
tipIridium
tip
Page 101 of 788
IGNITION SYSTEM
ENGINE ELECTRICAL16-37
IGNITION COIL RELAY CHECKM1163006500018
AC301727
2 1
3 4
AC304311AB
Battery
Ignition coil relay
Battery
voltageTerminal No.to
be connected to
testerContinuity test
results
Not applied 1 − 4 Open circuit
Connect
terminal
No.2 and
battery (+)
terminal.
Connect
terminal
No.3 and
battery (−)
terminal.1 − 4 Less than 2 ohms