Page 2454 of 3419
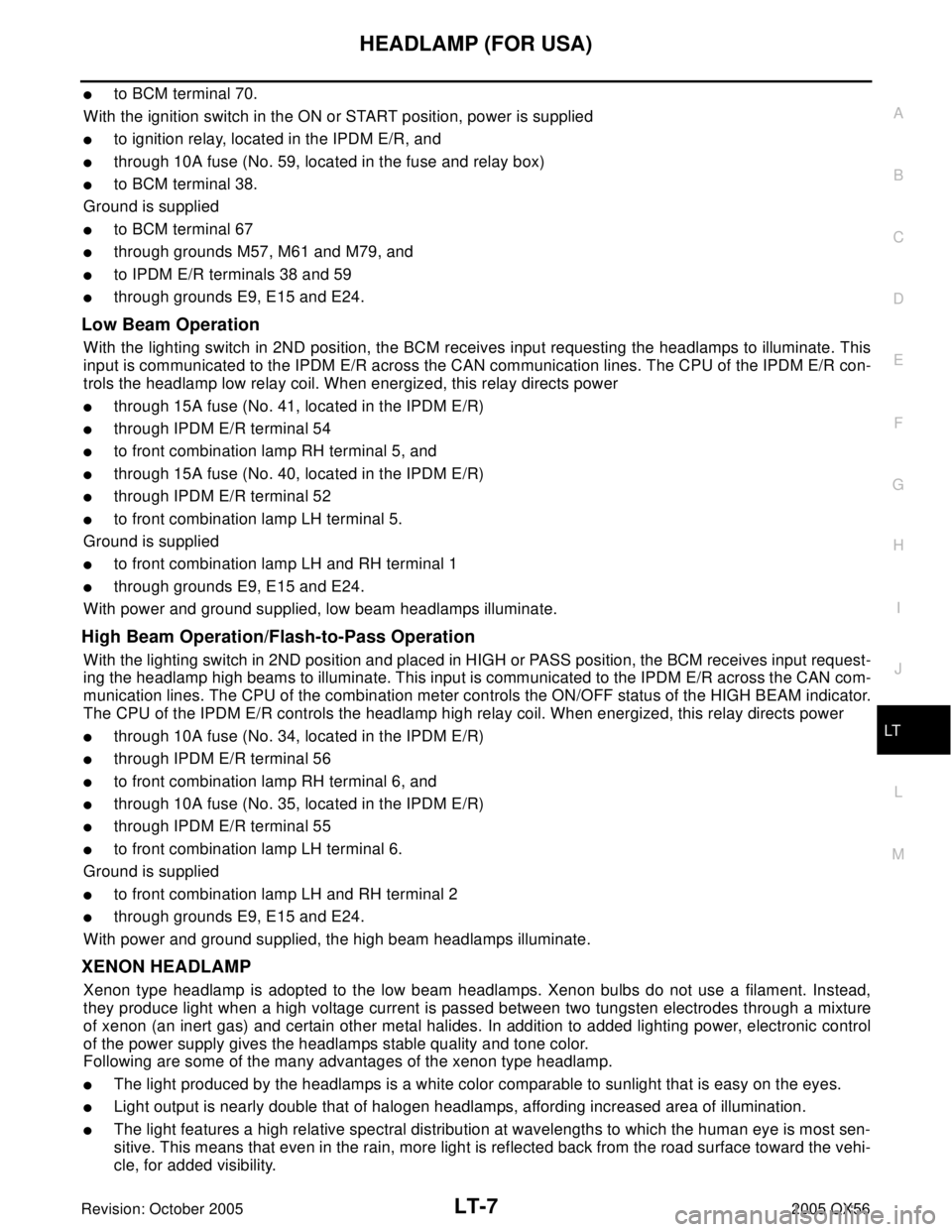
HEADLAMP (FOR USA)
LT-7
C
D
E
F
G
H
I
J
L
MA
B
LT
Revision: October 20052005 QX56
to BCM terminal 70.
With the ignition switch in the ON or START position, power is supplied
to ignition relay, located in the IPDM E/R, and
through 10A fuse (No. 59, located in the fuse and relay box)
to BCM terminal 38.
Ground is supplied
to BCM terminal 67
through grounds M57, M61 and M79, and
to IPDM E/R terminals 38 and 59
through grounds E9, E15 and E24.
Low Beam Operation
With the lighting switch in 2ND position, the BCM receives input requesting the headlamps to illuminate. This
input is communicated to the IPDM E/R across the CAN communication lines. The CPU of the IPDM E/R con-
trols the headlamp low relay coil. When energized, this relay directs power
through 15A fuse (No. 41, located in the IPDM E/R)
through IPDM E/R terminal 54
to front combination lamp RH terminal 5, and
through 15A fuse (No. 40, located in the IPDM E/R)
through IPDM E/R terminal 52
to front combination lamp LH terminal 5.
Ground is supplied
to front combination lamp LH and RH terminal 1
through grounds E9, E15 and E24.
With power and ground supplied, low beam headlamps illuminate.
High Beam Operation/Flash-to-Pass Operation
With the lighting switch in 2ND position and placed in HIGH or PASS position, the BCM receives input request-
ing the headlamp high beams to illuminate. This input is communicated to the IPDM E/R across the CAN com-
munication lines. The CPU of the combination meter controls the ON/OFF status of the HIGH BEAM indicator.
The CPU of the IPDM E/R controls the headlamp high relay coil. When energized, this relay directs power
through 10A fuse (No. 34, located in the IPDM E/R)
through IPDM E/R terminal 56
to front combination lamp RH terminal 6, and
through 10A fuse (No. 35, located in the IPDM E/R)
through IPDM E/R terminal 55
to front combination lamp LH terminal 6.
Ground is supplied
to front combination lamp LH and RH terminal 2
through grounds E9, E15 and E24.
With power and ground supplied, the high beam headlamps illuminate.
XENON HEADLAMP
Xenon type headlamp is adopted to the low beam headlamps. Xenon bulbs do not use a filament. Instead,
they produce light when a high voltage current is passed between two tungsten electrodes through a mixture
of xenon (an inert gas) and certain other metal halides. In addition to added lighting power, electronic control
of the power supply gives the headlamps stable quality and tone color.
Following are some of the many advantages of the xenon type headlamp.
The light produced by the headlamps is a white color comparable to sunlight that is easy on the eyes.
Light output is nearly double that of halogen headlamps, affording increased area of illumination.
The light features a high relative spectral distribution at wavelengths to which the human eye is most sen-
sitive. This means that even in the rain, more light is reflected back from the road surface toward the vehi-
cle, for added visibility.
Page 2765 of 3419
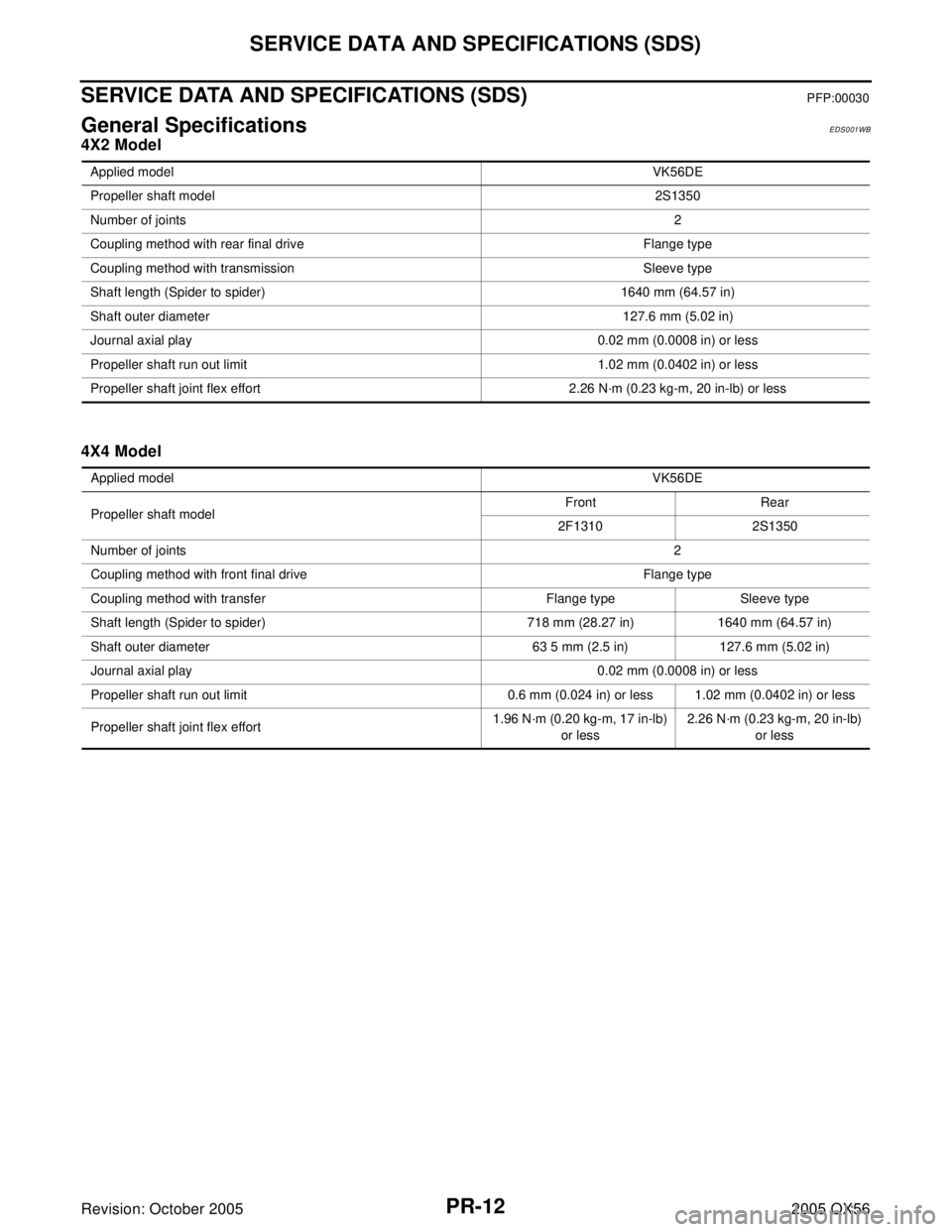
PR-12
SERVICE DATA AND SPECIFICATIONS (SDS)
Revision: October 20052005 QX56
SERVICE DATA AND SPECIFICATIONS (SDS)PFP:00030
General SpecificationsEDS001WB
4X2 Model
4X4 Model
Applied modelVK56DE
Propeller shaft model2S1350
Number of joints2
Coupling method with rear final drive Flange type
Coupling method with transmission Sleeve type
Shaft length (Spider to spider) 1640 mm (64.57 in)
Shaft outer diameter 127.6 mm (5.02 in)
Journal axial play 0.02 mm (0.0008 in) or less
Propeller shaft run out limit 1.02 mm (0.0402 in) or less
Propeller shaft joint flex effort 2.26 N·m (0.23 kg-m, 20 in-lb) or less
Applied modelVK56DE
Propeller shaft modelFront Rear
2F1310 2S1350
Number of joints2
Coupling method with front final drive Flange type
Coupling method with transfer Flange type Sleeve type
Shaft length (Spider to spider) 718 mm (28.27 in) 1640 mm (64.57 in)
Shaft outer diameter 63 5 mm (2.5 in) 127.6 mm (5.02 in)
Journal axial play 0.02 mm (0.0008 in) or less
Propeller shaft run out limit 0.6 mm (0.024 in) or less 1.02 mm (0.0402 in) or less
Propeller shaft joint flex effort1.96 N·m (0.20 kg-m, 17 in-lb)
or less2.26 N·m (0.23 kg-m, 20 in-lb)
or less
Page 2778 of 3419
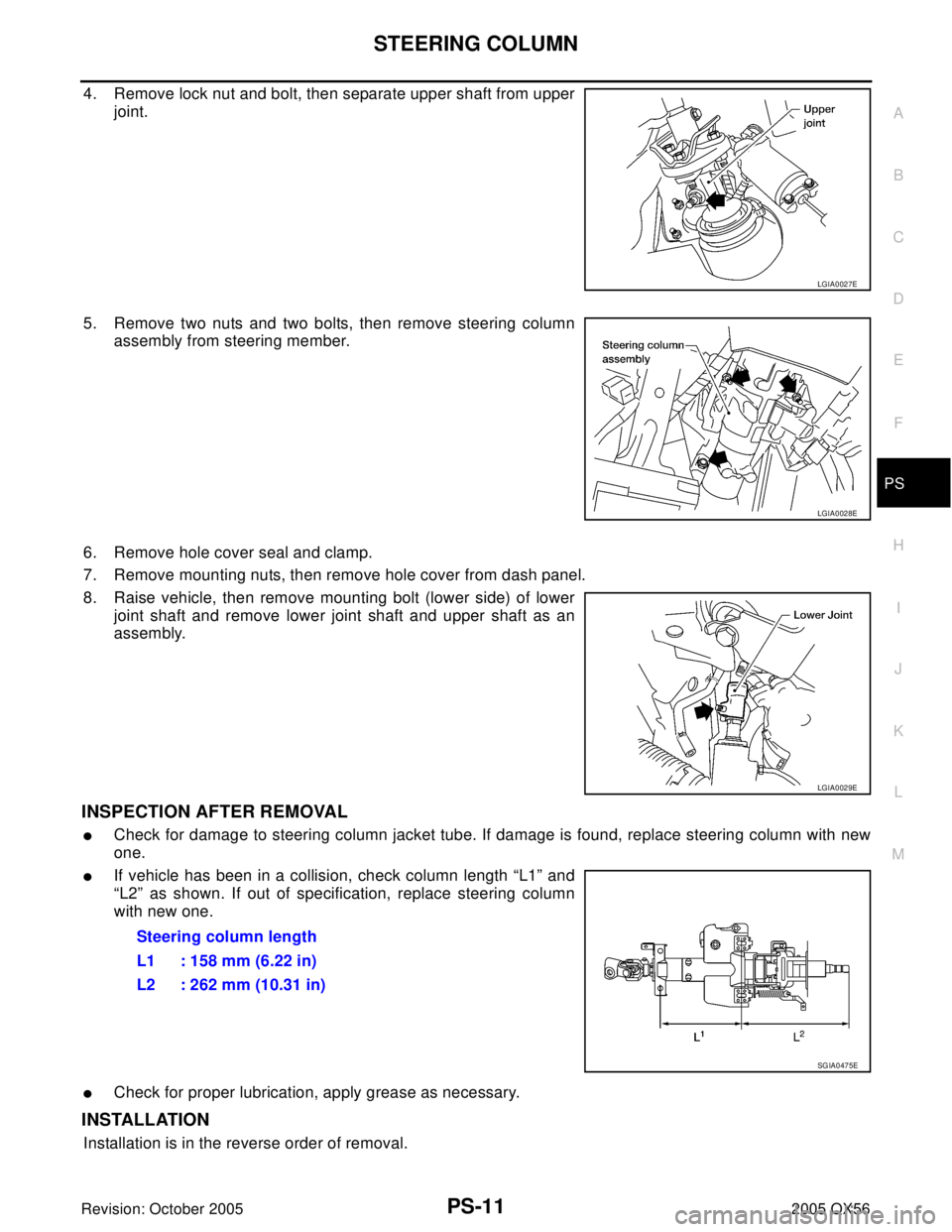
STEERING COLUMN
PS-11
C
D
E
F
H
I
J
K
L
MA
B
PS
Revision: October 20052005 QX56
4. Remove lock nut and bolt, then separate upper shaft from upper
joint.
5. Remove two nuts and two bolts, then remove steering column
assembly from steering member.
6. Remove hole cover seal and clamp.
7. Remove mounting nuts, then remove hole cover from dash panel.
8. Raise vehicle, then remove mounting bolt (lower side) of lower
joint shaft and remove lower joint shaft and upper shaft as an
assembly.
INSPECTION AFTER REMOVAL
Check for damage to steering column jacket tube. If damage is found, replace steering column with new
one.
If vehicle has been in a collision, check column length “L1” and
“L2” as shown. If out of specification, replace steering column
with new one.
Check for proper lubrication, apply grease as necessary.
INSTALLATION
Installation is in the reverse order of removal.
LGIA0027E
LGIA0028E
LGIA0029E
Steering column length
L1 : 158 mm (6.22 in)
L2 : 262 mm (10.31 in)
SGIA0475E
Page 2781 of 3419
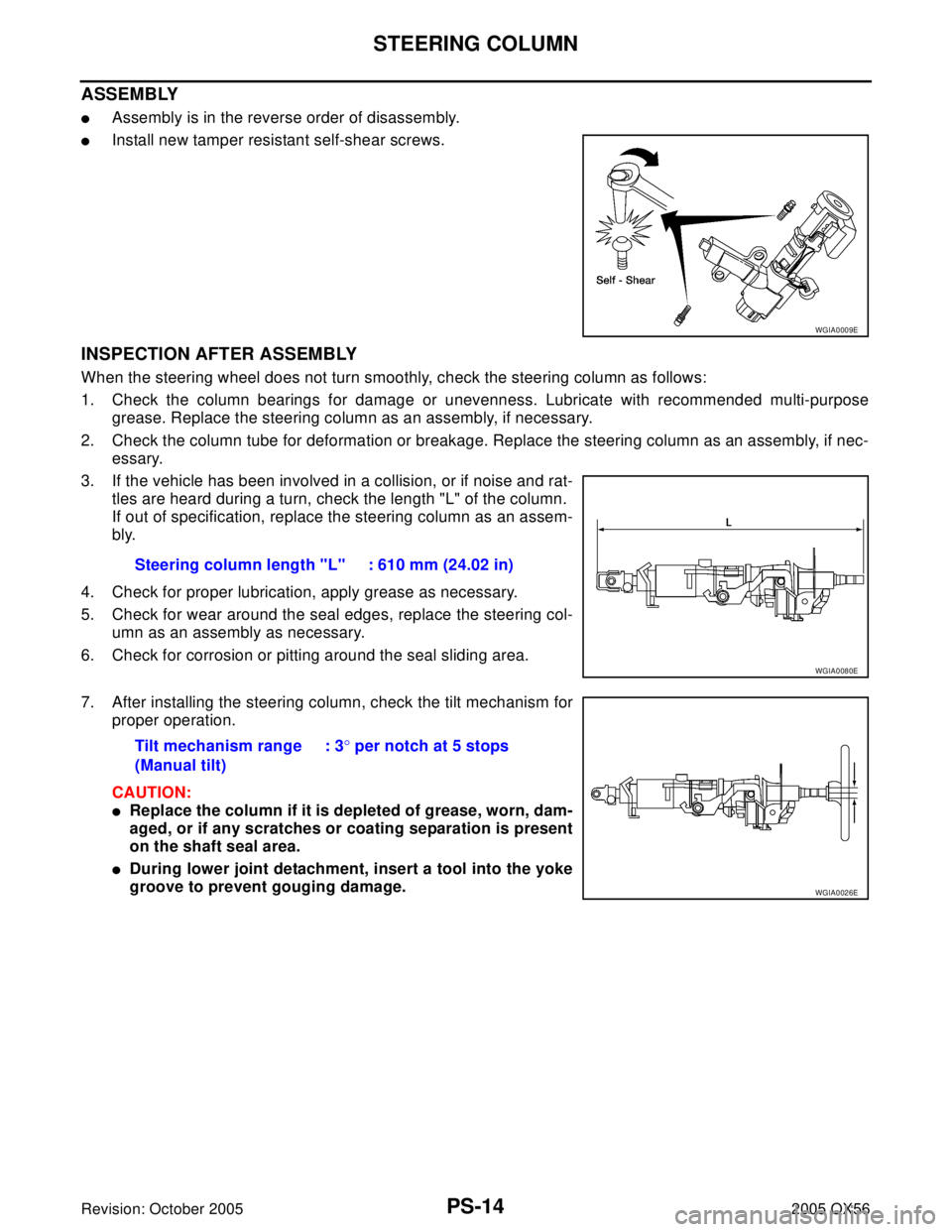
PS-14
STEERING COLUMN
Revision: October 20052005 QX56
ASSEMBLY
Assembly is in the reverse order of disassembly.
Install new tamper resistant self-shear screws.
INSPECTION AFTER ASSEMBLY
When the steering wheel does not turn smoothly, check the steering column as follows:
1. Check the column bearings for damage or unevenness. Lubricate with recommended multi-purpose
grease. Replace the steering column as an assembly, if necessary.
2. Check the column tube for deformation or breakage. Replace the steering column as an assembly, if nec-
essary.
3. If the vehicle has been involved in a collision, or if noise and rat-
tles are heard during a turn, check the length "L" of the column.
If out of specification, replace the steering column as an assem-
bly.
4. Check for proper lubrication, apply grease as necessary.
5. Check for wear around the seal edges, replace the steering col-
umn as an assembly as necessary.
6. Check for corrosion or pitting around the seal sliding area.
7. After installing the steering column, check the tilt mechanism for
proper operation.
CAUTION:
Replace the column if it is depleted of grease, worn, dam-
aged, or if any scratches or coating separation is present
on the shaft seal area.
During lower joint detachment, insert a tool into the yoke
groove to prevent gouging damage.
WGIA0009E
Steering column length "L" : 610 mm (24.02 in)
WGIA0080E
Tilt mechanism range
(Manual tilt): 3° per notch at 5 stops
WGIA0026E
Page 2792 of 3419
POWER STEERING GEAR AND LINKAGE
PS-25
C
D
E
F
H
I
J
K
L
MA
B
PS
Revision: October 20052005 QX56
21. Install new boot clamps and crimp securely.
CAUTION:
Do not reuse boot clamps.
22. Install cylinder tubes to gear housing assembly.
23. Install lock nut and outer socket to inner socket.
24. Tighten lightly tie-rod in specified length “L”, then tighten lock nut
at specified torque. Refer to PS-17, "
Disassembly and Assem-
bly" . Reconfirm if tie-rod length is within limit of specified length
“L”.
CAUTION:
Perform toe-in adjustment after this procedure. Length
achieved after toe-in adjustment is not necessarily the
value given here.
AST 1 39
Inner socket length “L” : 115.2 mm (4.54 in)
SGIA0167E
Page 2800 of 3419
SERVICE DATA AND SPECIFICATIONS (SDS)
PS-33
C
D
E
F
H
I
J
K
L
MA
B
PS
Revision: October 20052005 QX56
SERVICE DATA AND SPECIFICATIONS (SDS)PFP:00030
Steering WheelEGS000UN
Steering ColumnEGS000UO
Inspection After Assembly
Unit: mm (in)
Inspection After Removal
Unit: mm (in) End play of the axial direction for steering wheel 0 mm (0 in)
Steering wheel play on the outer circumference 0 − 35 mm (0 − 1.38 in)
Steering wheel turning force 39 N (4 kg-f, 9 lb-f) or less
Steering column length “L”610 (24.02)
WGIA0080E
Steering column length “L2”262 (10.31)
Steering column length “L1” 158 (6.22)
SGIA0475E
Page 2801 of 3419
PS-34
SERVICE DATA AND SPECIFICATIONS (SDS)
Revision: October 20052005 QX56
Inspection After Installation
Steering Outer Socket and Inner SocketEGS000UP
Unit: mm (in) Range “A”61.3 mm (2.41 in)
Tilt mechanism range (Manual tilt) 3° per notch at 5 steps
WGIA0083E
Tie-rod ball joint outer socketSwinging torque 0.3 − 2.9 N·m (0.03 − 0.29 kg-m, 3 − 25 in-lb)
Measurement on spring balanceMeasuring point: cotter pin hole of stud4.84 − 46.7 N (0.50 − 4.7 kg, 4 − 34 lb)
Rotating torque 0.3 − 2.9 N·m (0.03 − 0.29 kg-m, 3 − 25 in-lb)
Axial end play 0.5 mm (0.020 in) or less
Tie-rod ball joint inner socketSwinging torque 1.0 − 7.8 N·m (0.11 − 0.79 kg-m, 9 − 69 in-lb)
Measurement on spring balance
Measuring point: "L" mark see above,
"L"=83.2 mm (3.276 in).12.1 − 93.7 N (1.3 − 9.5 kg, 9 − 69 lb)
Axial end play 0.2 mm (0.08 in) or less
SGIA0358E
Inner socket length “L” 115.2 (4.54)
SGIA0167E
Page 2814 of 3419
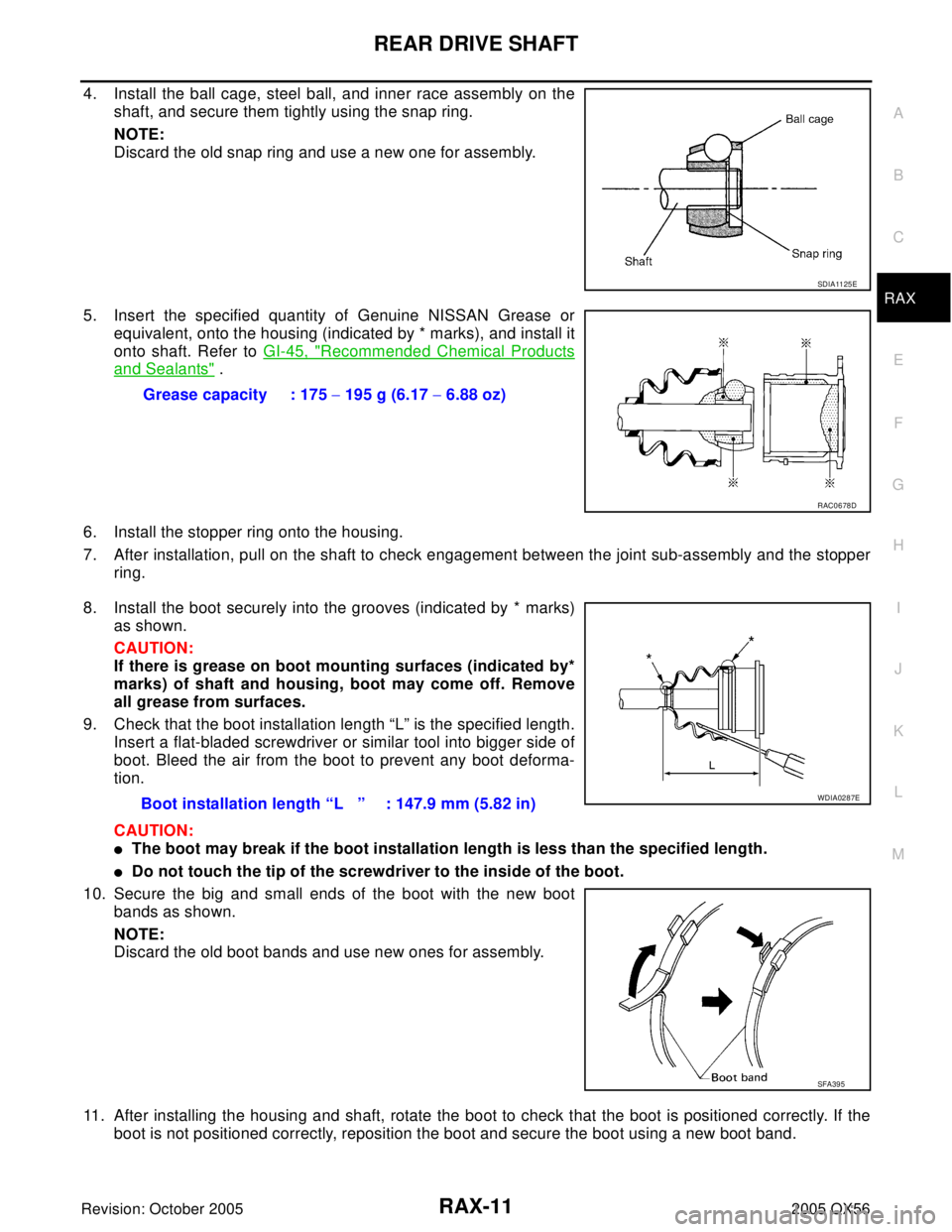
REAR DRIVE SHAFT
RAX-11
C
E
F
G
H
I
J
K
L
MA
B
RAX
Revision: October 20052005 QX56
4. Install the ball cage, steel ball, and inner race assembly on the
shaft, and secure them tightly using the snap ring.
NOTE:
Discard the old snap ring and use a new one for assembly.
5. Insert the specified quantity of Genuine NISSAN Grease or
equivalent, onto the housing (indicated by * marks), and install it
onto shaft. Refer to GI-45, "
Recommended Chemical Products
and Sealants" .
6. Install the stopper ring onto the housing.
7. After installation, pull on the shaft to check engagement between the joint sub-assembly and the stopper
ring.
8. Install the boot securely into the grooves (indicated by * marks)
as shown.
CAUTION:
If there is grease on boot mounting surfaces (indicated by*
marks) of shaft and housing, boot may come off. Remove
all grease from surfaces.
9. Check that the boot installation length “L” is the specified length.
Insert a flat-bladed screwdriver or similar tool into bigger side of
boot. Bleed the air from the boot to prevent any boot deforma-
tion.
CAUTION:
The boot may break if the boot installation length is less than the specified length.
Do not touch the tip of the screwdriver to the inside of the boot.
10. Secure the big and small ends of the boot with the new boot
bands as shown.
NOTE:
Discard the old boot bands and use new ones for assembly.
11. After installing the housing and shaft, rotate the boot to check that the boot is positioned correctly. If the
boot is not positioned correctly, reposition the boot and secure the boot using a new boot band.
SDIA11 25 E
Grease capacity : 175 − 195 g (6.17 − 6.88 oz)
RAC0678D
Boot installation length “L ” : 147.9 mm (5.82 in)WDIA0287E
SFA39 5