Page 50 of 364
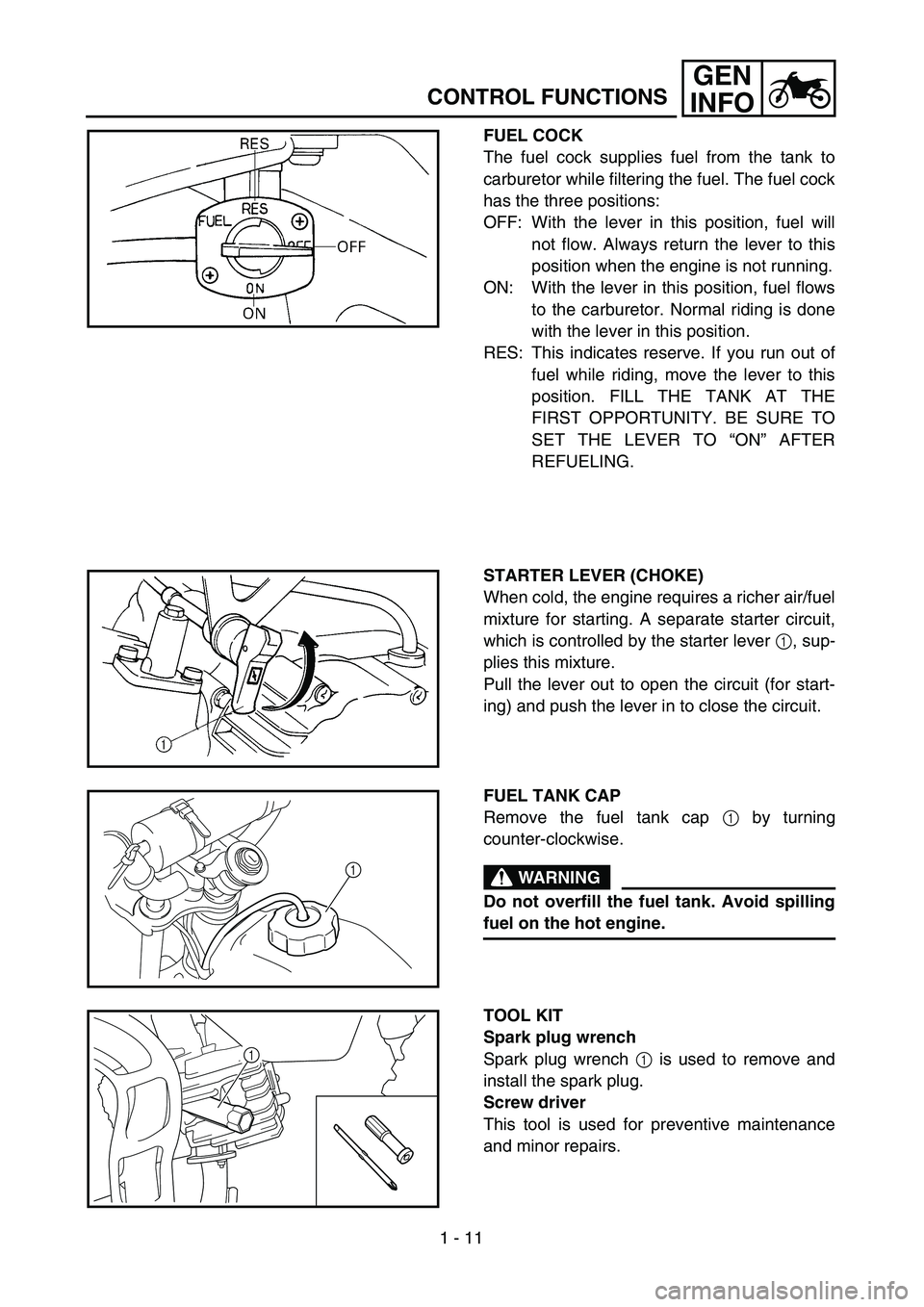
1 - 11
GEN
INFO
CONTROL FUNCTIONS
FUEL COCK
The fuel cock supplies fuel from the tank to
carburetor while filtering the fuel. The fuel cock
has the three positions:
OFF: With the lever in this position, fuel will
not flow. Always return the lever to this
position when the engine is not running.
ON: With the lever in this position, fuel flows
to the carburetor. Normal riding is done
with the lever in this position.
RES: This indicates reserve. If you run out of
fuel while riding, move the lever to this
position. FILL THE TANK AT THE
FIRST OPPORTUNITY. BE SURE TO
SET THE LEVER TO “ON” AFTER
REFUELING.
STARTER LEVER (CHOKE)
When cold, the engine requires a richer air/fuel
mixture for starting. A separate starter circuit,
which is controlled by the starter lever 1, sup-
plies this mixture.
Pull the lever out to open the circuit (for start-
ing) and push the lever in to close the circuit.
FUEL TANK CAP
Remove the fuel tank cap 1 by turning
counter-clockwise.
WARNING
Do not overfill the fuel tank. Avoid spilling
fuel on the hot engine.
1
TOOL KIT
Spark plug wrench
Spark plug wrench 1 is used to remove and
install the spark plug.
Screw driver
This tool is used for preventive maintenance
and minor repairs.
1
Page 63 of 364
SPEC
2 - 6 Stem runout limit ---- 0.02 mm
(0.0008 in)
Valve seat width IN 0.9 ~ 1.1 mm
(0.0354 ~ 0.0433 in)1.6 mm
(0.0630 in)
EX 0.9 ~ 1.1 mm
(0.0354 ~ 0.0433 in)1.6 mm
(0.0630 in)
Valve spring:
Free length IN 32.45 mm (1.28 in) 26.9 mm
(1.06 in)
EX 32.45 mm (1.28 in) 26.9 mm
(1.06 in)
Set length (valve closed) IN 24.2 mm (0.95 in) ----
EX 24.2 mm (0.95 in) ----
Compressed pressure
(installed) IN 138 ~ 158 N
(14.07 ~ 16.11 kg,
31.02 ~ 35.52 lb)----
EX 138 ~ 158 N
(14.07 ~ 16.11 kg,
31.02 ~ 35.52 lb)----
Tilt limit IN ---- 2.5˚/1.4 mm
(2.5˚/0.06 in)
EX ---- 2.5˚/1.4 mm
(2.5˚/0.06 in)
Direction of winding
(top view) IN Clockwise ----
EX Clockwise ---- Item Standard Limit
*
MAINTENANCE SPECIFICATIONS
Page 144 of 364
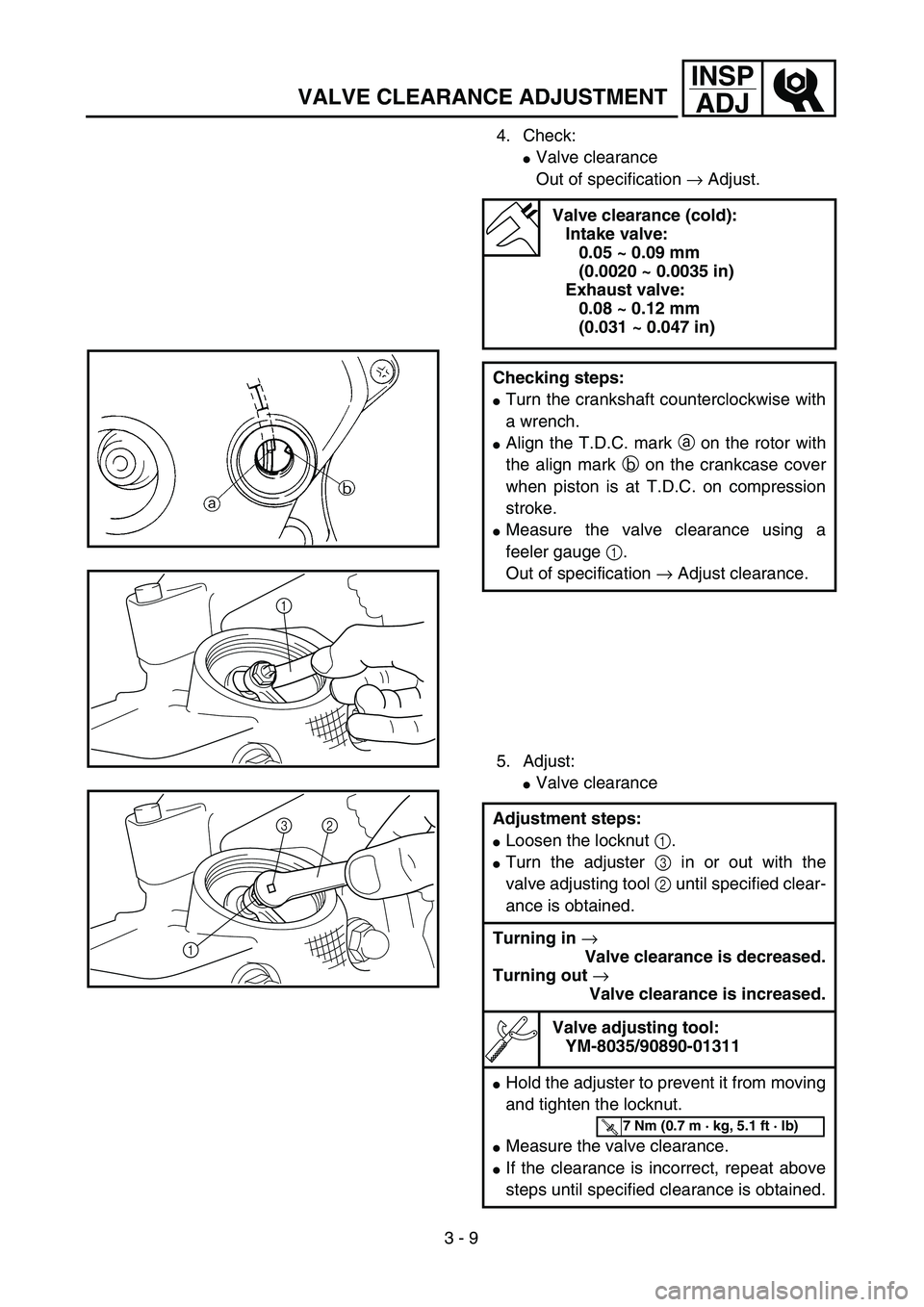
3 - 9
INSP
ADJ
VALVE CLEARANCE ADJUSTMENT
4. Check:
Valve clearance
Out of specification → Adjust.
5. Adjust:
Valve clearance
Valve clearance (cold):
Intake valve:
0.05 ~ 0.09 mm
(0.0020 ~ 0.0035 in)
Exhaust valve:
0.08 ~ 0.12 mm
(0.031 ~ 0.047 in)
Checking steps:
Turn the crankshaft counterclockwise with
a wrench.
Align the T.D.C. mark a on the rotor with
the align mark b on the crankcase cover
when piston is at T.D.C. on compression
stroke.
Measure the valve clearance using a
feeler gauge 1.
Out of specification → Adjust clearance.
Adjustment steps:
Loosen the locknut 1.
Turn the adjuster 3 in or out with the
valve adjusting tool 2 until specified clear-
ance is obtained.
Turning in →
Valve clearance is decreased.
Turning out →
Valve clearance is increased.
Valve adjusting tool:
YM-8035/90890-01311
Hold the adjuster to prevent it from moving
and tighten the locknut.
Measure the valve clearance.
If the clearance is incorrect, repeat above
steps until specified clearance is obtained.
1
12 3
T R..7 Nm (0.7 m · kg, 5.1 ft · lb)
Page 150 of 364
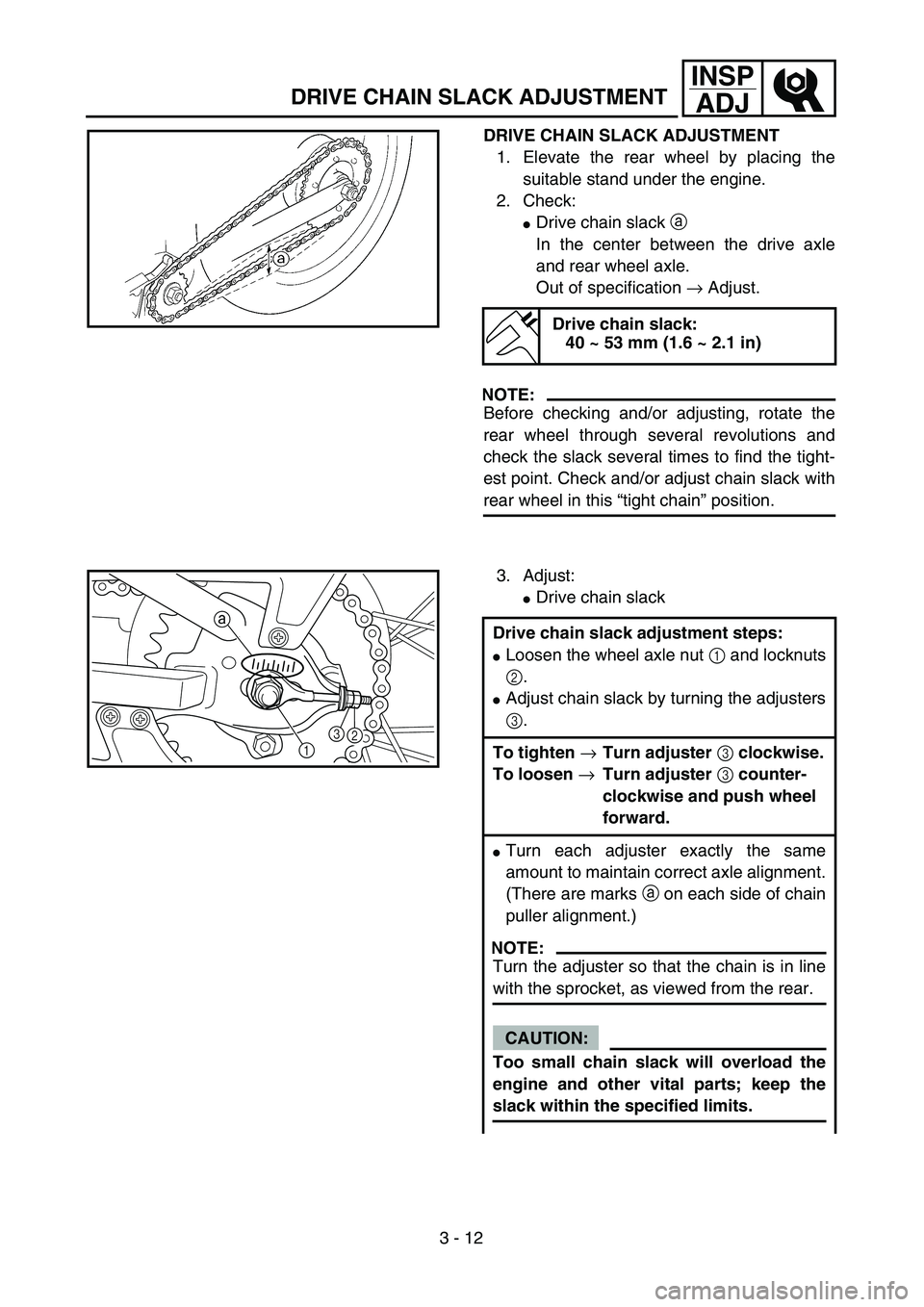
3 - 12
INSP
ADJ
DRIVE CHAIN SLACK ADJUSTMENT
DRIVE CHAIN SLACK ADJUSTMENT
1. Elevate the rear wheel by placing the
suitable stand under the engine.
2. Check:
Drive chain slack a
In the center between the drive axle
and rear wheel axle.
Out of specification → Adjust.
NOTE:
Before checking and/or adjusting, rotate the
rear wheel through several revolutions and
check the slack several times to find the tight-
est point. Check and/or adjust chain slack with
rear wheel in this “tight chain” position.
Drive chain slack:
40 ~ 53 mm (1.6 ~ 2.1 in)
3. Adjust:
Drive chain slack
Drive chain slack adjustment steps:
Loosen the wheel axle nut 1 and locknuts
2.
Adjust chain slack by turning the adjusters
3.
To tighten →Turn adjuster 3 clockwise.
To loosen →Turn adjuster 3 counter-
clockwise and push wheel
forward.
Turn each adjuster exactly the same
amount to maintain correct axle alignment.
(There are marks a on each side of chain
puller alignment.)
NOTE:
Turn the adjuster so that the chain is in line
with the sprocket, as viewed from the rear.
CAUTION:
Too small chain slack will overload the
engine and other vital parts; keep the
slack within the specified limits.
13 a2
Page 204 of 364
4 - 10
ENGCYLINDER HEAD
REMOVAL POINTS
Cylinder head
1. Align:
“I” mark
(with stationary pointer)
Checking steps:
Turn the crankshaft counterclockwise with
a wrench.
Align the “I” mark a on the rotor with the
stationary pointer b on the crankcase
cover. When the “I” mark is aligned with
the stationary pointer, the piston is at the
Top Dead Center (T.D.C.).
NOTE:
In order to be sure that the piston is at Top
Dead Center, the match mark c on the
camshaft sprocket must align with the sta-
tionary pointer d on the cylinder head as
shown in the illustration.
If there is no valve clearance, rotate the
crankshaft counterclockwise one turn.
2. Loosen:
Camshaft sprocket bolt 1
3. Remove:
Timing chain tensioner
Camshaft sprocket 2
NOTE:
Fasten a safety wire to the timing chain 3 to
prevent it from falling into the crankcase.
Remove the bolt 1 while holding the rotor
nut with a wrench.
Page 206 of 364
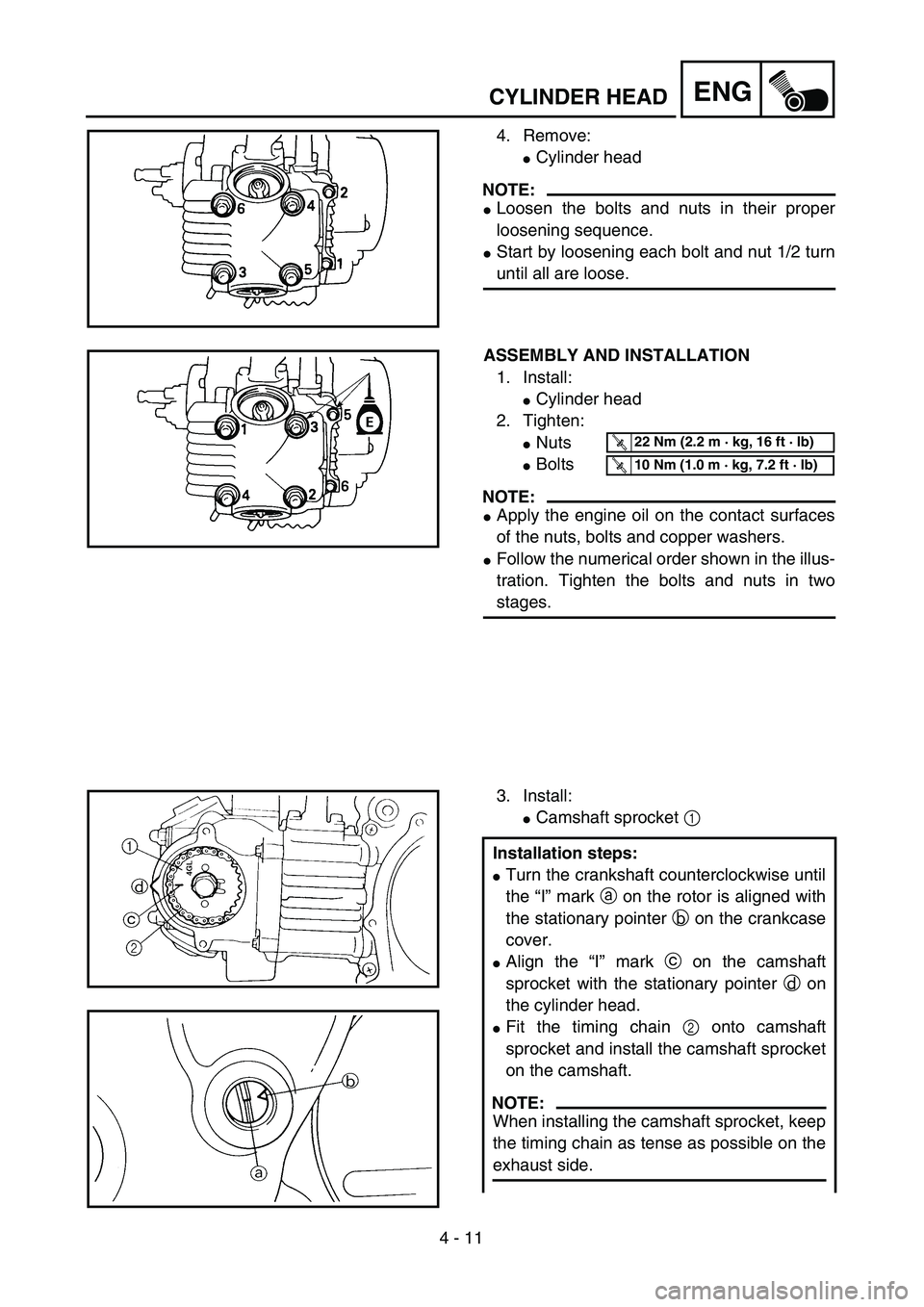
4 - 11
ENGCYLINDER HEAD
4. Remove:
Cylinder head
NOTE:
Loosen the bolts and nuts in their proper
loosening sequence.
Start by loosening each bolt and nut 1/2 turn
until all are loose.
ASSEMBLY AND INSTALLATION
1. Install:
Cylinder head
2. Tighten:
Nuts
Bolts
NOTE:
Apply the engine oil on the contact surfaces
of the nuts, bolts and copper washers.
Follow the numerical order shown in the illus-
tration. Tighten the bolts and nuts in two
stages.
T R..22 Nm (2.2 m · kg, 16 ft · lb)
T R..10 Nm (1.0 m · kg, 7.2 ft · lb)
3. Install:
Camshaft sprocket 1
Installation steps:
Turn the crankshaft counterclockwise until
the “I” mark a on the rotor is aligned with
the stationary pointer b on the crankcase
cover.
Align the “I” mark c on the camshaft
sprocket with the stationary pointer d on
the cylinder head.
Fit the timing chain 2 onto camshaft
sprocket and install the camshaft sprocket
on the camshaft.
NOTE:
When installing the camshaft sprocket, keep
the timing chain as tense as possible on the
exhaust side.
Page 270 of 364
4 - 43
ENG
INSPECTION
Starter clutch
1. Inspect:
Starter idle gear teeth a
Starter drive gear teeth b
Starter wheel gear teeth c
Burrs/chips/roughness/wear →
Replace.
2. Check:
Starter clutch operation
Push the dowel pins to the arrow direc-
tion.
Unsmooth operation → Replace.
Checking steps:
Hold the starter clutch.
When turning the starter wheel gear clock-
wise Å, the starter clutch and the starter
wheel gear should be engaged.
If not, the starter clutch is faulty. Replace
it.
When turning the starter wheel gear coun-
terclockwise ı, it should turn freely.
If not, the starter clutch is faulty. Replace
it.
ı
Å
ASSEMBLY AND INSTALLATION
Starter clutch
1. Install:
Starter clutch 1
1T R..14 Nm (1.4 m · kg, 10 ft · lb)
2. Unloosen the starter clutch assembly by
using the center punch.
CDI MAGNETO AND STARTER CLUTCH (TT-R90E)