Page 1954 of 3371
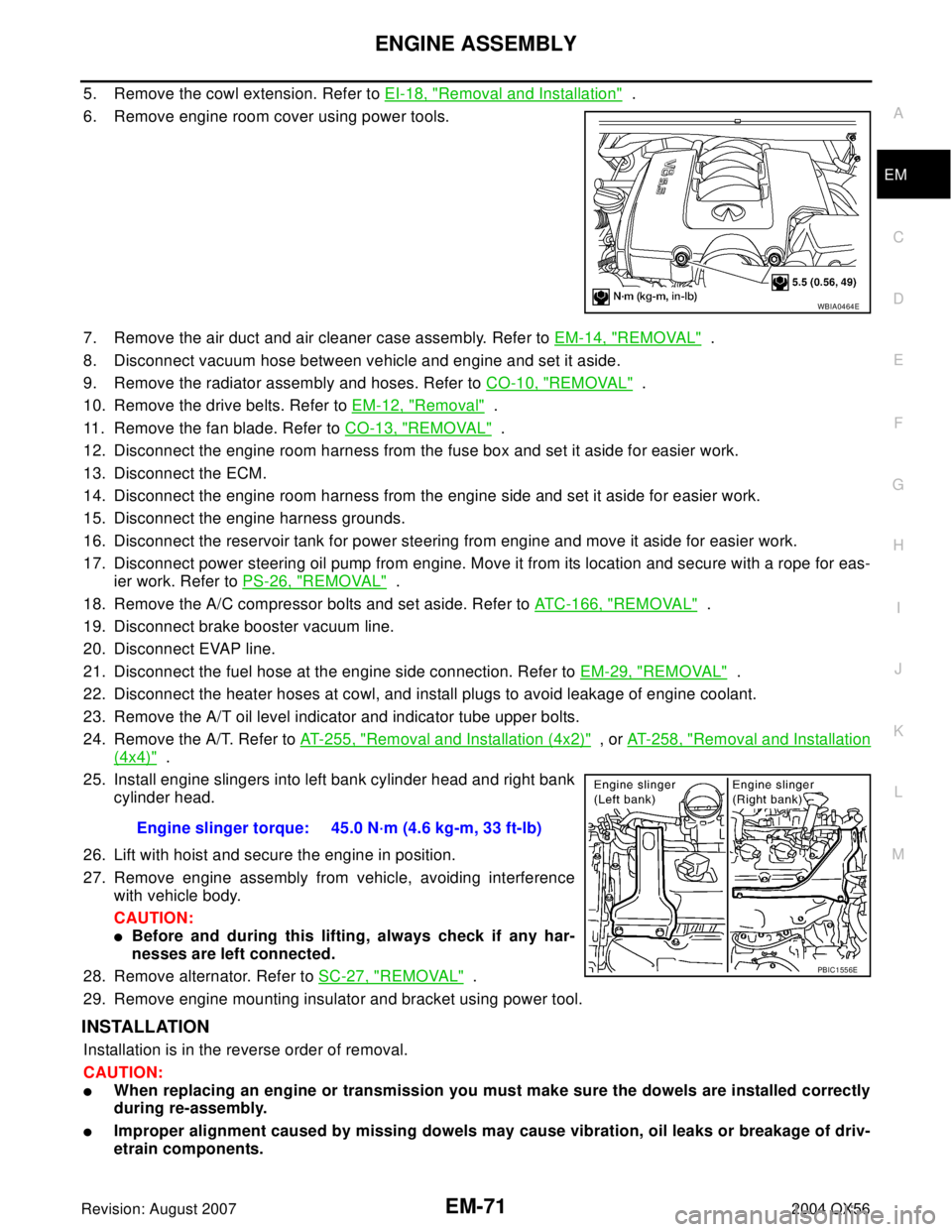
ENGINE ASSEMBLY
EM-71
C
D
E
F
G
H
I
J
K
L
MA
EM
Revision: August 20072004 QX56
5. Remove the cowl extension. Refer to EI-18, "Removal and Installation" .
6. Remove engine room cover using power tools.
7. Remove the air duct and air cleaner case assembly. Refer to EM-14, "
REMOVAL" .
8. Disconnect vacuum hose between vehicle and engine and set it aside.
9. Remove the radiator assembly and hoses. Refer to CO-10, "
REMOVAL" .
10. Remove the drive belts. Refer to EM-12, "
Removal" .
11. Remove the fan blade. Refer to CO-13, "
REMOVAL" .
12. Disconnect the engine room harness from the fuse box and set it aside for easier work.
13. Disconnect the ECM.
14. Disconnect the engine room harness from the engine side and set it aside for easier work.
15. Disconnect the engine harness grounds.
16. Disconnect the reservoir tank for power steering from engine and move it aside for easier work.
17. Disconnect power steering oil pump from engine. Move it from its location and secure with a rope for eas-
ier work. Refer to PS-26, "
REMOVAL" .
18. Remove the A/C compressor bolts and set aside. Refer to ATC-166, "
REMOVAL" .
19. Disconnect brake booster vacuum line.
20. Disconnect EVAP line.
21. Disconnect the fuel hose at the engine side connection. Refer to EM-29, "
REMOVAL" .
22. Disconnect the heater hoses at cowl, and install plugs to avoid leakage of engine coolant.
23. Remove the A/T oil level indicator and indicator tube upper bolts.
24. Remove the A/T. Refer to AT-255, "
Removal and Installation (4x2)" , or AT-258, "Removal and Installation
(4x4)" .
25. Install engine slingers into left bank cylinder head and right bank
cylinder head.
26. Lift with hoist and secure the engine in position.
27. Remove engine assembly from vehicle, avoiding interference
with vehicle body.
CAUTION:
Before and during this lifting, always check if any har-
nesses are left connected.
28. Remove alternator. Refer to SC-27, "
REMOVAL" .
29. Remove engine mounting insulator and bracket using power tool.
INSTALLATION
Installation is in the reverse order of removal.
CAUTION:
When replacing an engine or transmission you must make sure the dowels are installed correctly
during re-assembly.
Improper alignment caused by missing dowels may cause vibration, oil leaks or breakage of driv-
etrain components.
WBIA0464E
Engine slinger torque: 45.0 N·m (4.6 kg-m, 33 ft-lb)
PBIC1556E
Page 1955 of 3371
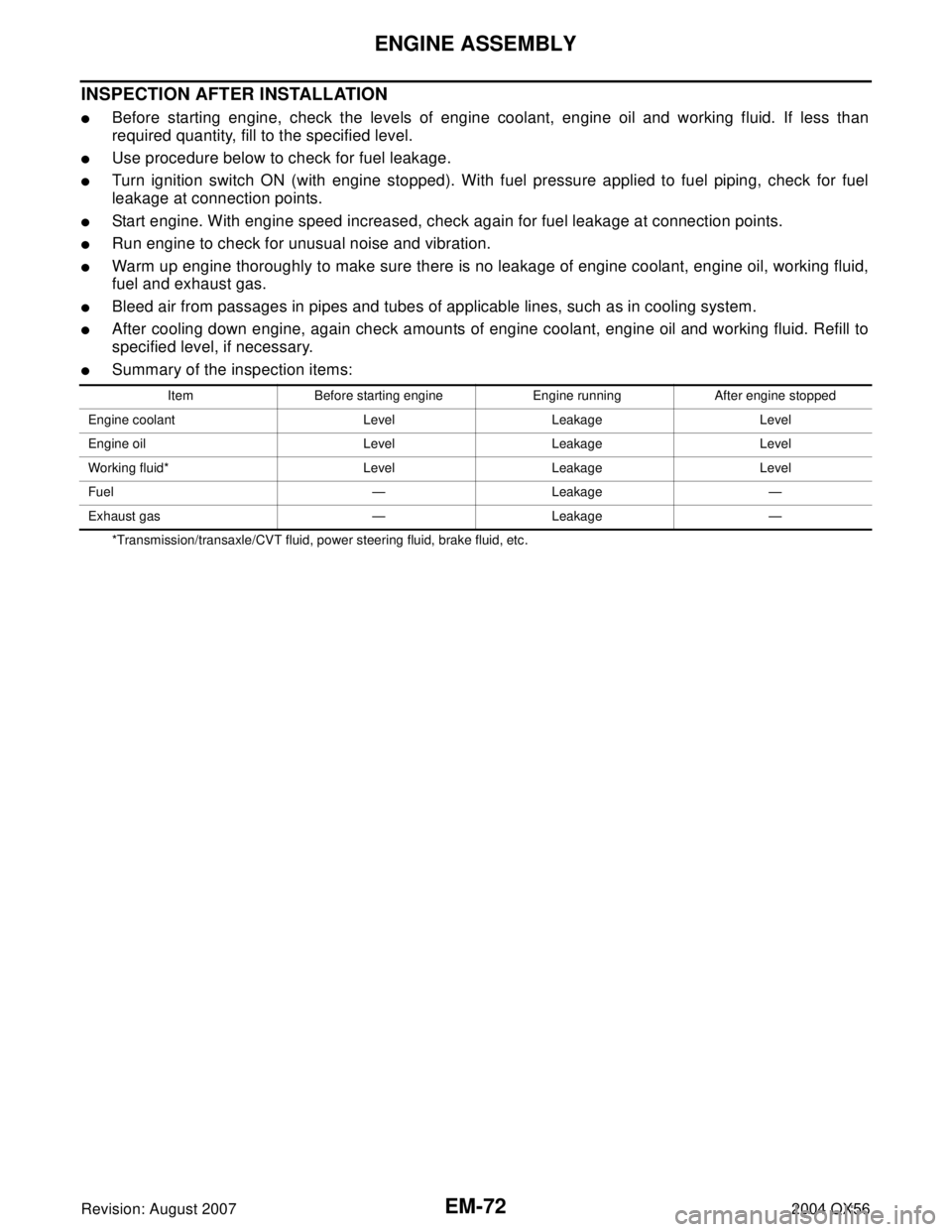
EM-72Revision: August 2007
ENGINE ASSEMBLY
2004 QX56
INSPECTION AFTER INSTALLATION
Before starting engine, check the levels of engine coolant, engine oil and working fluid. If less than
required quantity, fill to the specified level.
Use procedure below to check for fuel leakage.
Turn ignition switch ON (with engine stopped). With fuel pressure applied to fuel piping, check for fuel
leakage at connection points.
Start engine. With engine speed increased, check again for fuel leakage at connection points.
Run engine to check for unusual noise and vibration.
Warm up engine thoroughly to make sure there is no leakage of engine coolant, engine oil, working fluid,
fuel and exhaust gas.
Bleed air from passages in pipes and tubes of applicable lines, such as in cooling system.
After cooling down engine, again check amounts of engine coolant, engine oil and working fluid. Refill to
specified level, if necessary.
Summary of the inspection items:
*Transmission/transaxle/CVT fluid, power steering fluid, brake fluid, etc.Item Before starting engine Engine running After engine stopped
Engine coolant Level Leakage Level
Engine oil Level Leakage Level
Working fluid* Level Leakage Level
Fuel — Leakage —
Exhaust gas — Leakage —
Page 1958 of 3371
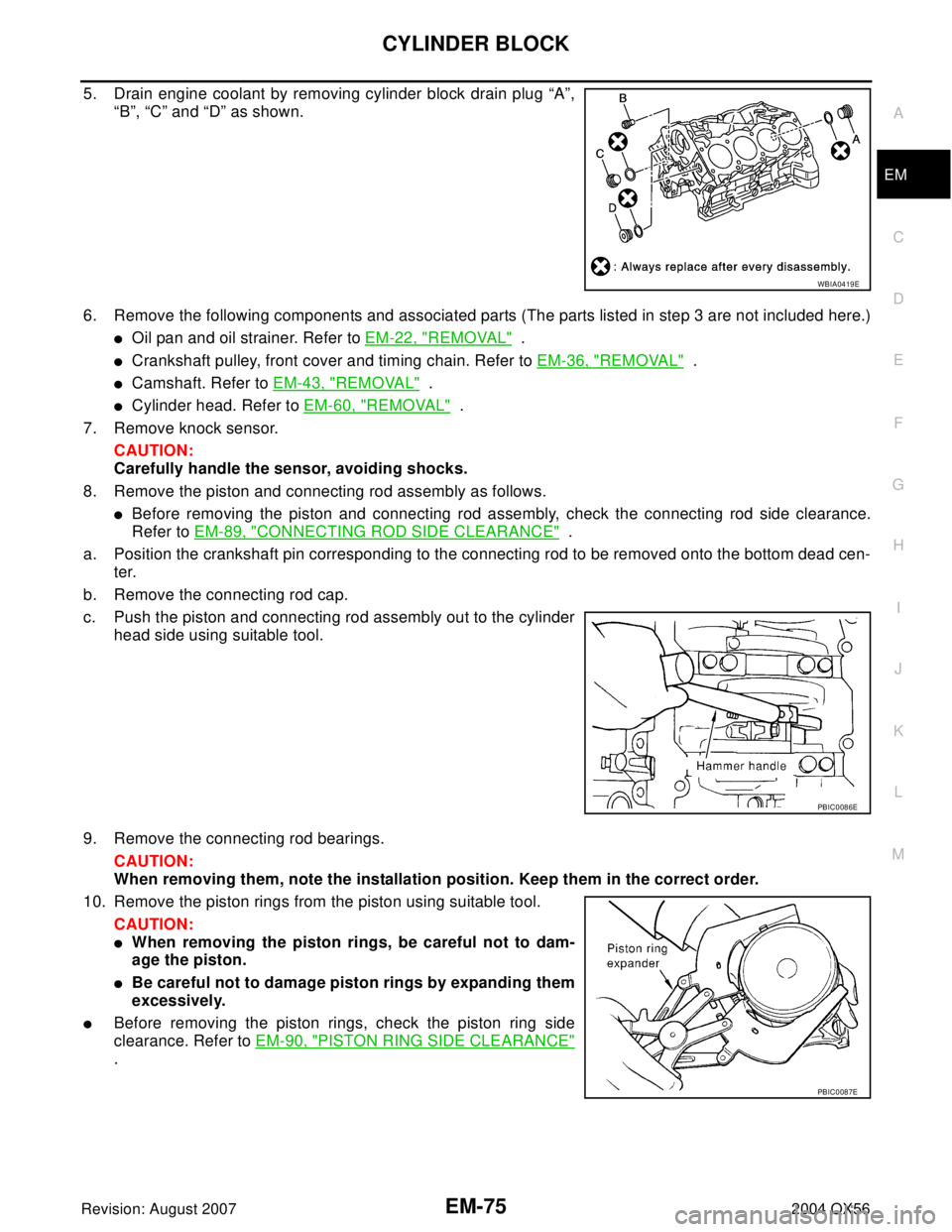
CYLINDER BLOCK
EM-75
C
D
E
F
G
H
I
J
K
L
MA
EM
Revision: August 20072004 QX56
5. Drain engine coolant by removing cylinder block drain plug “A”,
“B”, “C” and “D” as shown.
6. Remove the following components and associated parts (The parts listed in step 3 are not included here.)
Oil pan and oil strainer. Refer to EM-22, "REMOVAL" .
Crankshaft pulley, front cover and timing chain. Refer to EM-36, "REMOVAL" .
Camshaft. Refer to EM-43, "REMOVAL" .
Cylinder head. Refer to EM-60, "REMOVAL" .
7. Remove knock sensor.
CAUTION:
Carefully handle the sensor, avoiding shocks.
8. Remove the piston and connecting rod assembly as follows.
Before removing the piston and connecting rod assembly, check the connecting rod side clearance.
Refer to EM-89, "
CONNECTING ROD SIDE CLEARANCE" .
a. Position the crankshaft pin corresponding to the connecting rod to be removed onto the bottom dead cen-
ter.
b. Remove the connecting rod cap.
c. Push the piston and connecting rod assembly out to the cylinder
head side using suitable tool.
9. Remove the connecting rod bearings.
CAUTION:
When removing them, note the installation position. Keep them in the correct order.
10. Remove the piston rings from the piston using suitable tool.
CAUTION:
When removing the piston rings, be careful not to dam-
age the piston.
Be careful not to damage piston rings by expanding them
excessively.
Before removing the piston rings, check the piston ring side
clearance. Refer to EM-90, "
PISTON RING SIDE CLEARANCE"
.
WBIA0419E
PBIC0086E
PBIC0087E
Page 2014 of 3371
PRECAUTIONS
FFD-3
C
E
F
G
H
I
J
K
L
MA
B
FFD
Revision: August 20072004 QX56
3. Attach liquid gasket tube to Tool.
Use Genuine RTV Silicone Sealant or equivalent. Refer to
GI-45, "
Recommended Chemical Products and Sealants" .
4. Apply liquid gasket without breaks to the specified location with
the specified dimensions.
If there is a groove for liquid gasket application, apply liquid
gasket to the groove.
As for bolt holes, normally apply liquid gasket inside the
holes. Occasionally, it should be applied outside the holes.
Make sure to read the text of this manual.
Within five minutes of liquid gasket application, install the mat-
ing component.
If liquid gasket protrudes, wipe it off immediately.
Do not retighten nuts or bolts after the installation.
After 30 minutes or more have passed from the installation, fill
engine oil and engine coolant.
CAUTION:
If there are specific instructions in this manual, observe
them.Tool number : WS39930000 ( — )
WBIA0567E
SEM 15 9F
Page 2061 of 3371
FSU-2
PRECAUTIONS
Revision: August 20072004 QX56
PRECAUTIONSPFP:00001
PrecautionsEES0010D
When installing the rubber bushings, the final tightening must be done under unladen condition and with
the tires on level ground. Oil will shorten the life of the rubber bushings, so wipe off any spilled oil immedi-
ately.
Unladen condition means the fuel tank, engine coolant and lubricants are at the full specification. The
spare tire, jack, hand tools, and mats are in their designated positions.
After installing suspension components, check the wheel alignment.
Lock nuts are not reusable. Always use new lock nuts for installation. New lock nuts are pre-oiled, do not
apply any additional lubrication.
Page 2079 of 3371
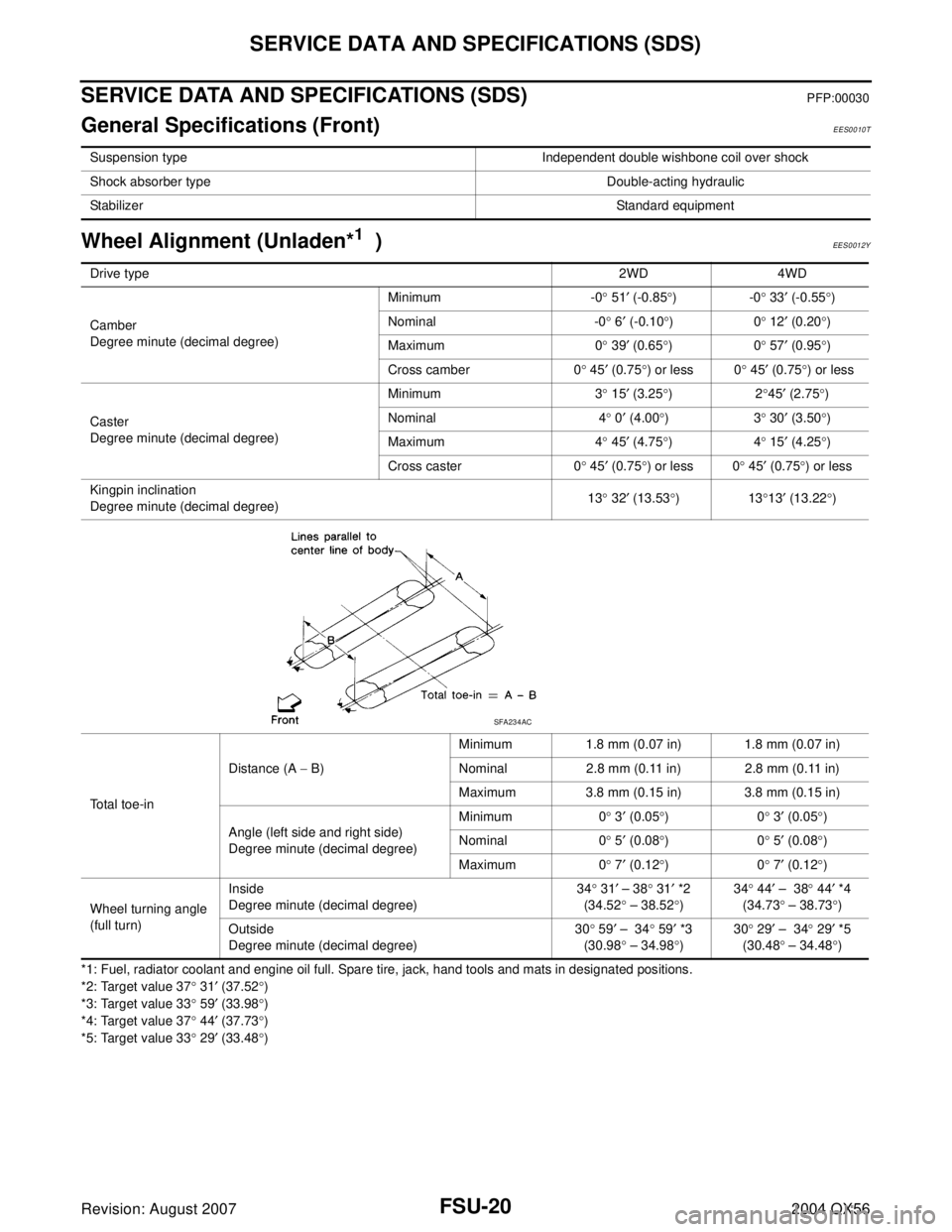
FSU-20
SERVICE DATA AND SPECIFICATIONS (SDS)
Revision: August 20072004 QX56
SERVICE DATA AND SPECIFICATIONS (SDS)PFP:00030
General Specifications (Front)EES0010T
Wheel Alignment (Unladen*1 )EES0012Y
*1: Fuel, radiator coolant and engine oil full. Spare tire, jack, hand tools and mats in designated positions.
*2: Target value 37° 31′ (37.52°)
*3: Target value 33° 59′ (33.98°)
*4: Target value 37° 44′ (37.73°)
*5: Target value 33° 29′ (33.48°) Suspension type Independent double wishbone coil over shock
Shock absorber type Double-acting hydraulic
StabilizerStandard equipment
Drive type2WD 4WD
Camber
Degree minute (decimal degree)Minimum -0° 51′ (-0.85°)-0° 33′ (-0.55°)
Nominal -0° 6′ (-0.10°)0° 12′ (0.20°)
Maximum 0° 39′ (0.65°)0° 57′ (0.95°)
Cross camber 0° 45′ (0.75°) or less 0° 45′ (0.75°) or less
Caster
Degree minute (decimal degree)Minimum 3° 15′ (3.25°)2°45′ (2.75°)
Nominal 4° 0′ (4.00°)3° 30′ (3.50°)
Maximum 4° 45′ (4.75°)4° 15′ (4.25°)
Cross caster 0° 45′ (0.75°) or less 0° 45′ (0.75°) or less
Kingpin inclination
Degree minute (decimal degree)13° 32′ (13.53°)13°13′ (13.22°)
Total toe-inDistance (A − B)Minimum 1.8 mm (0.07 in) 1.8 mm (0.07 in)
Nominal 2.8 mm (0.11 in) 2.8 mm (0.11 in)
Maximum 3.8 mm (0.15 in) 3.8 mm (0.15 in)
Angle (left side and right side)
Degree minute (decimal degree)Minimum 0° 3′ (0.05°)0° 3′ (0.05°)
Nominal 0° 5′ (0.08°)0° 5′ (0.08°)
Maximum 0° 7′ (0.12°)0° 7′ (0.12°)
Wheel turning angle
(full turn)Inside
Degree minute (decimal degree)34° 31′ – 38° 31′ *2
(34.52° – 38.52°)34° 44′ – 38° 44′ *4
(34.73° – 38.73°)
Outside
Degree minute (decimal degree)30° 59′ – 34° 59′ *3
(30.98° – 34.98°)30° 29′ – 34° 29′ *5
(30.48° – 34.48°)
SFA234AC
Page 2080 of 3371
SERVICE DATA AND SPECIFICATIONS (SDS)
FSU-21
C
D
F
G
H
I
J
K
L
MA
B
FSU
Revision: August 20072004 QX56
Ball JointEES0013H
*1 Measure at cotter pin hole
*2 Measure at groove
Wheelarch Height (Unladen*1 )EES0010W
Unit: mm (in)
*1: Fuel, radiator coolant and engine oil full. Spare tire, jack, hand tools and mats in designated positions.
*2: Confirm level using Consult-II, register 1103. Set rear wheel arch height to “0” if necessary.Swinging force “A”Upper ball joint 8.1 – 103.2 N (0.8 – 10.5 kg-f, 1.8 – 23.2 lb-f) *1
Lower ball joint 11.4 – 145.5 N (1.1 – 14.8 kg-f, 2.5 – 32.7 lb-f) *2
Turning torque “B” 0.5 - 6.4 N·m (0.05 - 0.65 kg-m, 4 - 57 in-lb)
Vertical end play “C”0 mm (0 in)
SFA858AWEIA0076E
Suspension type
Air leveling*2
Applied model 2WD 4WD
Front wheelarch height (Hf)913
(35.94)931
(36.65)
Rear wheelarch height (Hr)912
(35.91)932
(36.69)
LEIA0085E
Page 2131 of 3371
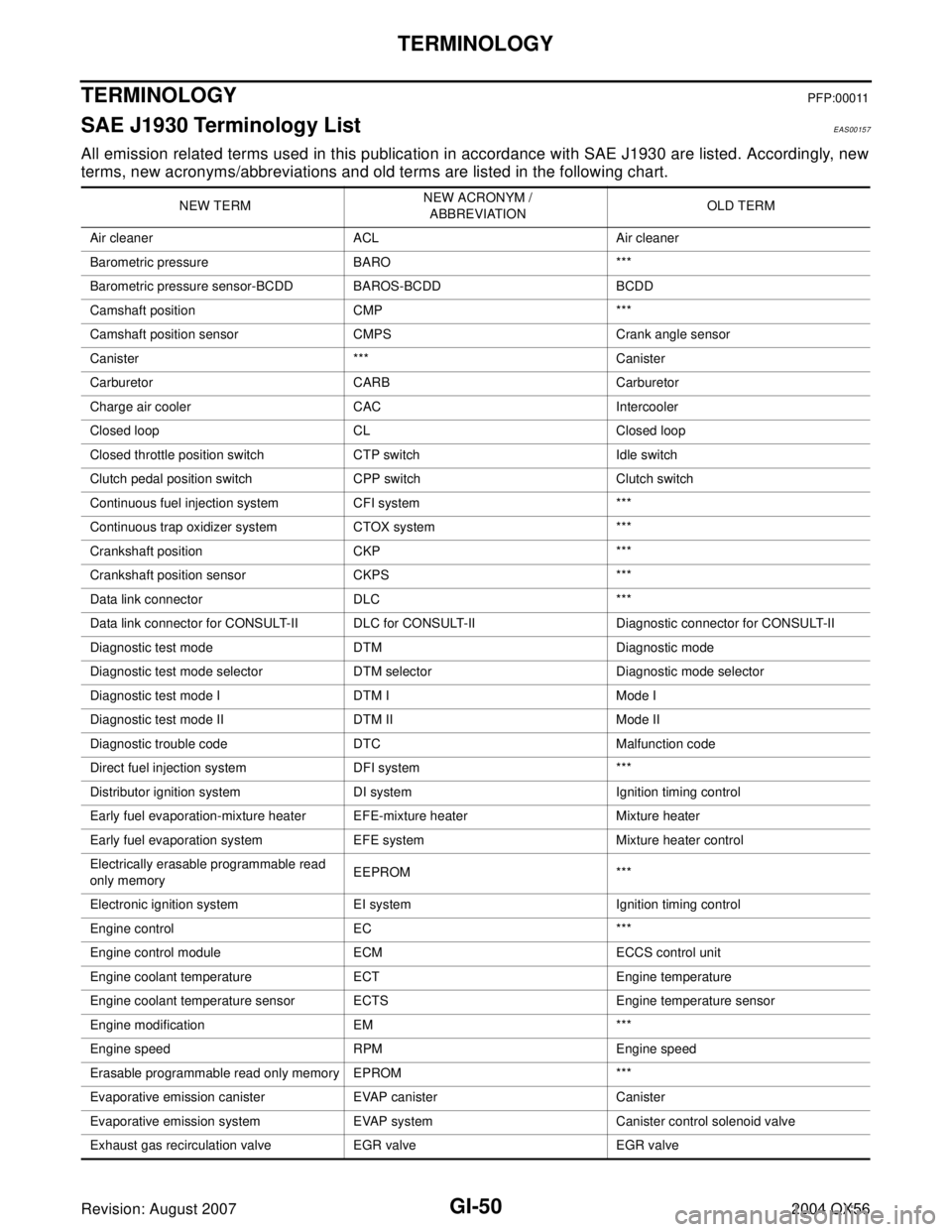
GI-50
TERMINOLOGY
Revision: August 20072004 QX56
TERMINOLOGYPFP:00011
SAE J1930 Terminology List EAS00157
All emission related terms used in this publication in accordance with SAE J1930 are listed. Accordingly, new
terms, new acronyms/abbreviations and old terms are listed in the following chart.
NEW TERMNEW ACRONYM /
ABBREVIATIONOLD TERM
Air cleaner ACL Air cleaner
Barometric pressure BARO ***
Barometric pressure sensor-BCDD BAROS-BCDD BCDD
Camshaft position CMP ***
Camshaft position sensor CMPS Crank angle sensor
Canister *** Canister
Carburetor CARB Carburetor
Charge air cooler CAC Intercooler
Closed loop CL Closed loop
Closed throttle position switch CTP switch Idle switch
Clutch pedal position switch CPP switch Clutch switch
Continuous fuel injection system CFI system ***
Continuous trap oxidizer system CTOX system ***
Crankshaft position CKP ***
Crankshaft position sensor CKPS ***
Data link connector DLC ***
Data link connector for CONSULT-II DLC for CONSULT-II Diagnostic connector for CONSULT-II
Diagnostic test mode DTM Diagnostic mode
Diagnostic test mode selector DTM selector Diagnostic mode selector
Diagnostic test mode I DTM I Mode I
Diagnostic test mode II DTM II Mode II
Diagnostic trouble code DTC Malfunction code
Direct fuel injection system DFI system ***
Distributor ignition system DI system Ignition timing control
Early fuel evaporation-mixture heater EFE-mixture heater Mixture heater
Early fuel evaporation system EFE system Mixture heater control
Electrically erasable programmable read
only memoryEEPROM ***
Electronic ignition system EI system Ignition timing control
Engine control EC ***
Engine control module ECM ECCS control unit
Engine coolant temperature ECT Engine temperature
Engine coolant temperature sensor ECTS Engine temperature sensor
Engine modification EM ***
Engine speed RPM Engine speed
Erasable programmable read only memory EPROM ***
Evaporative emission canister EVAP canister Canister
Evaporative emission system EVAP system Canister control solenoid valve
Exhaust gas recirculation valve EGR valve EGR valve