Page 1537 of 2643
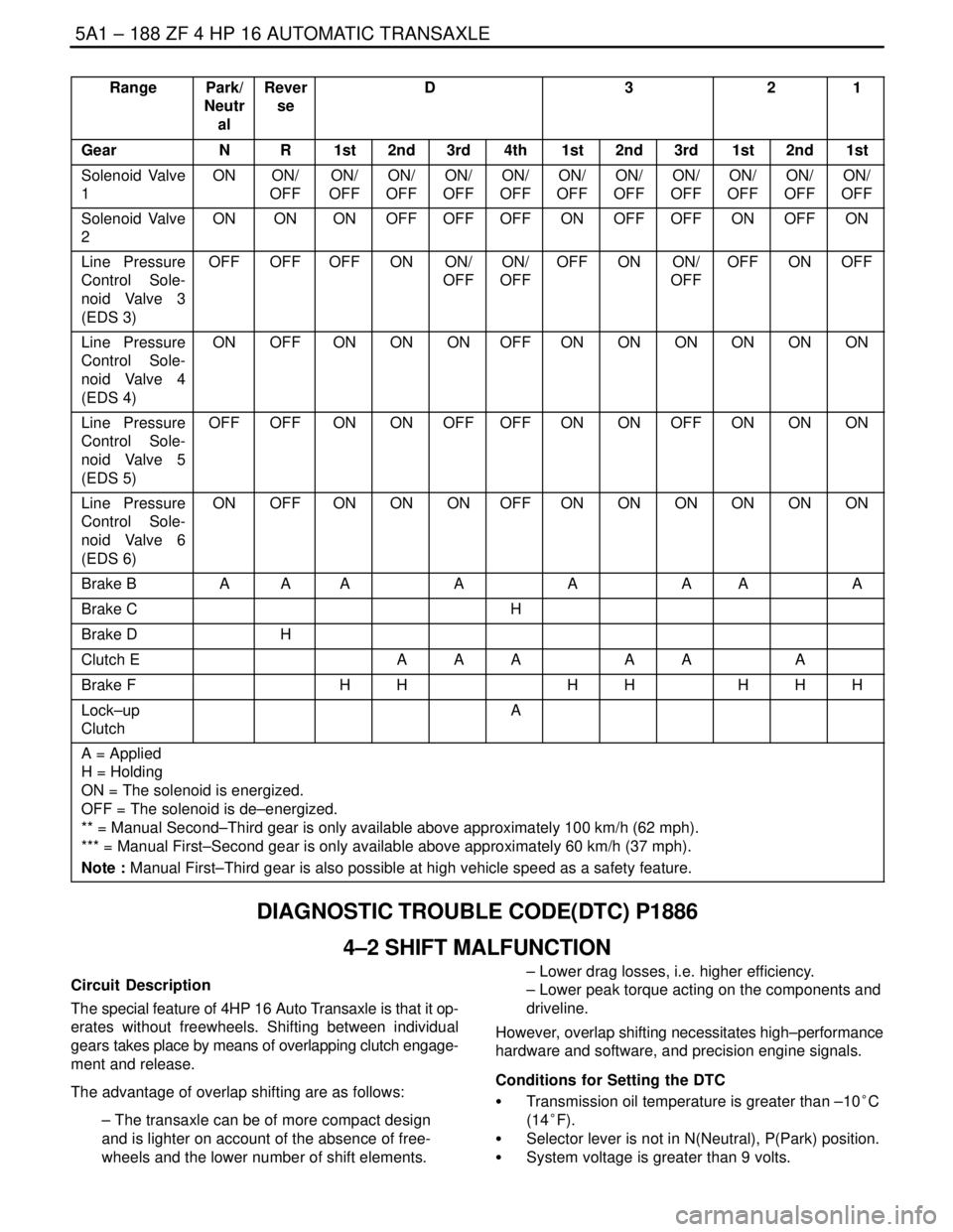
5A1 – 188IZF 4 HP 16 AUTOMATIC TRANSAXLE
DAEWOO V–121 BL4
RangePark/
Neutr
alRever
seD321
GearNR1st2nd3rd4th1st2nd3rd1st2nd1st
Solenoid Valve
1ONON/
OFFON/
OFFON/
OFFON/
OFFON/
OFFON/
OFFON/
OFFON/
OFFON/
OFFON/
OFFON/
OFF
Solenoid Valve
2ONONONOFFOFFOFFONOFFOFFONOFFON
Line Pressure
Control Sole-
noid Valve 3
(EDS 3)OFFOFFOFFONON/
OFFON/
OFFOFFONON/
OFFOFFONOFF
Line Pressure
Control Sole-
noid Valve 4
(EDS 4)ONOFFONONONOFFONONONONONON
Line Pressure
Control Sole-
noid Valve 5
(EDS 5)OFFOFFONONOFFOFFONONOFFONONON
Line Pressure
Control Sole-
noid Valve 6
(EDS 6)ONOFFONONONOFFONONONONONON
Brake BAAAAAAAA
Brake CH
Brake DH
Clutch EAAAAAA
Brake FHHHHHHH
Lock–up
ClutchA
A = Applied
H = Holding
ON = The solenoid is energized.
OFF = The solenoid is de–energized.
** = Manual Second–Third gear is only available above approximately 100 km/h (62 mph).
*** = Manual First–Second gear is only available above approximately 60 km/h (37 mph).
Note : Manual First–Third gear is also possible at high vehicle speed as a safety feature.
DIAGNOSTIC TROUBLE CODE(DTC) P1886
4–2 SHIFT MALFUNCTION
Circuit Description
The special feature of 4HP 16 Auto Transaxle is that it op-
erates without freewheels. Shifting between individual
gears takes place by means of overlapping clutch engage-
ment and release.
The advantage of overlap shifting are as follows:
– The transaxle can be of more compact design
and is lighter on account of the absence of free-
wheels and the lower number of shift elements.– Lower drag losses, i.e. higher efficiency.
– Lower peak torque acting on the components and
driveline.
However, overlap shifting necessitates high–performance
hardware and software, and precision engine signals.
Conditions for Setting the DTC
S Transmission oil temperature is greater than –10°C
(14°F).
S Selector lever is not in N(Neutral), P(Park) position.
S System voltage is greater than 9 volts.
Page 1542 of 2643
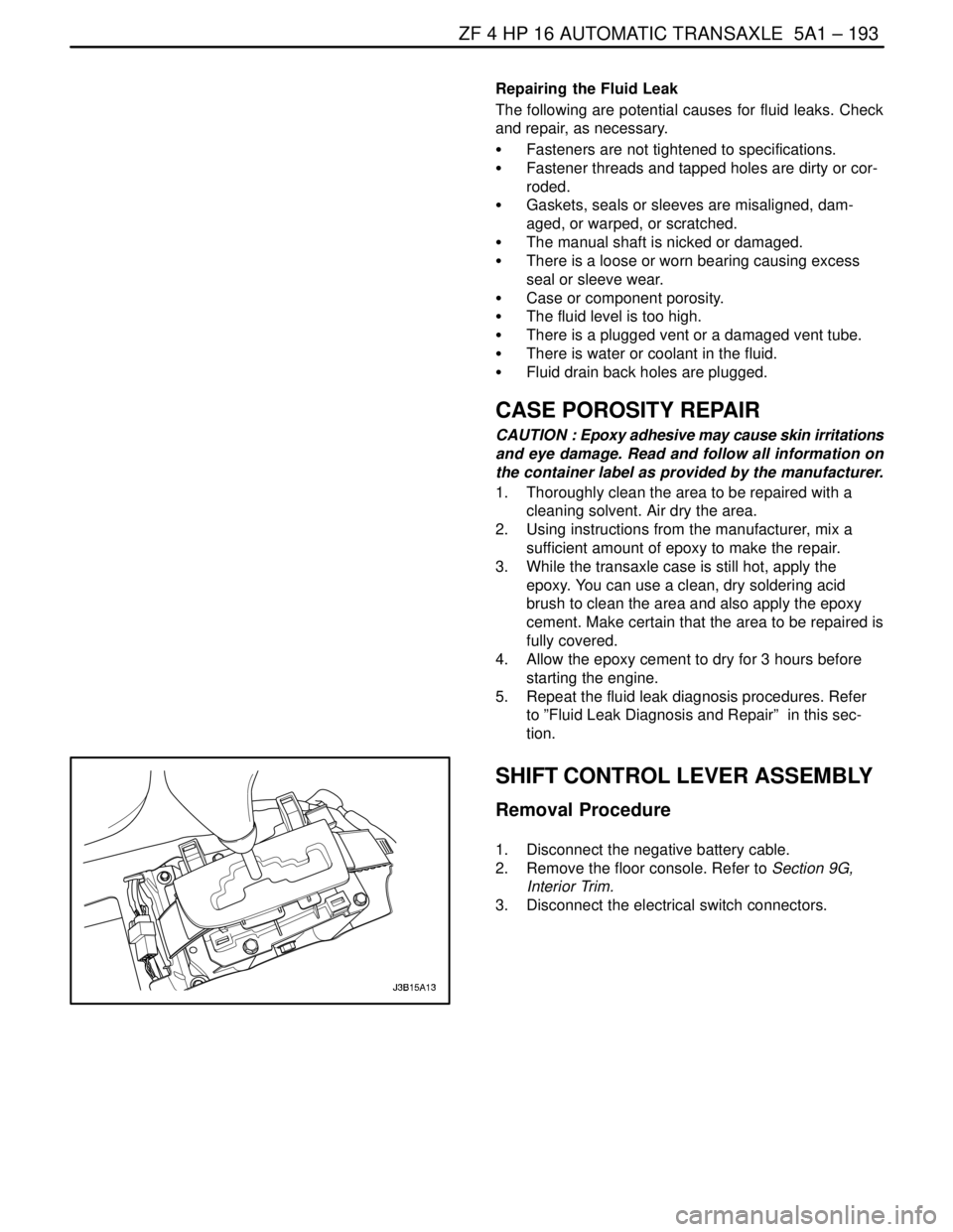
ZF 4 HP 16 AUTOMATIC TRANSAXLE 5A1 – 193
DAEWOO V–121 BL4
Repairing the Fluid Leak
The following are potential causes for fluid leaks. Check
and repair, as necessary.
S Fasteners are not tightened to specifications.
S Fastener threads and tapped holes are dirty or cor-
roded.
S Gaskets, seals or sleeves are misaligned, dam-
aged, or warped, or scratched.
S The manual shaft is nicked or damaged.
S There is a loose or worn bearing causing excess
seal or sleeve wear.
S Case or component porosity.
S The fluid level is too high.
S There is a plugged vent or a damaged vent tube.
S There is water or coolant in the fluid.
S Fluid drain back holes are plugged.
CASE POROSITY REPAIR
CAUTION : Epoxy adhesive may cause skin irritations
and eye damage. Read and follow all information on
the container label as provided by the manufacturer.
1. Thoroughly clean the area to be repaired with a
cleaning solvent. Air dry the area.
2. Using instructions from the manufacturer, mix a
sufficient amount of epoxy to make the repair.
3. While the transaxle case is still hot, apply the
epoxy. You can use a clean, dry soldering acid
brush to clean the area and also apply the epoxy
cement. Make certain that the area to be repaired is
fully covered.
4. Allow the epoxy cement to dry for 3 hours before
starting the engine.
5. Repeat the fluid leak diagnosis procedures. Refer
to ”Fluid Leak Diagnosis and Repair” in this sec-
tion.
SHIFT CONTROL LEVER ASSEMBLY
Removal Procedure
1. Disconnect the negative battery cable.
2. Remove the floor console. Refer to Section 9G,
Interior Trim.
3. Disconnect the electrical switch connectors.
Page 1594 of 2643
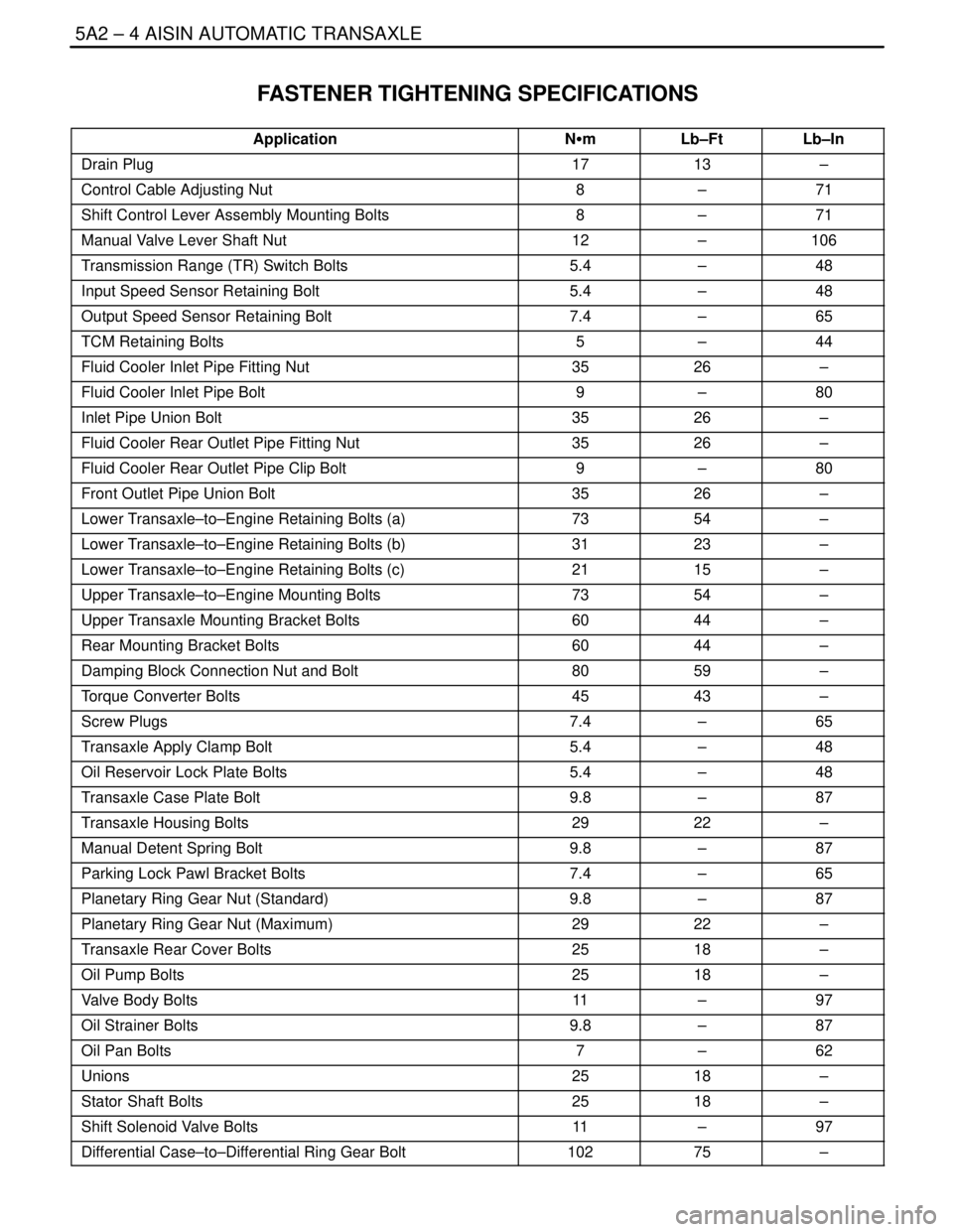
5A2 – 4IAISIN AUTOMATIC TRANSAXLE
DAEWOO V–121 BL4
FASTENER TIGHTENING SPECIFICATIONS
ApplicationNSmLb–FtLb–In
Drain Plug1713–
Control Cable Adjusting Nut8–71
Shift Control Lever Assembly Mounting Bolts8–71
Manual Valve Lever Shaft Nut12–106
Transmission Range (TR) Switch Bolts5.4–48
Input Speed Sensor Retaining Bolt5.4–48
Output Speed Sensor Retaining Bolt7.4–65
TCM Retaining Bolts5–44
Fluid Cooler Inlet Pipe Fitting Nut3526–
Fluid Cooler Inlet Pipe Bolt9–80
Inlet Pipe Union Bolt3526–
Fluid Cooler Rear Outlet Pipe Fitting Nut3526–
Fluid Cooler Rear Outlet Pipe Clip Bolt9–80
Front Outlet Pipe Union Bolt3526–
Lower Transaxle–to–Engine Retaining Bolts (a)7354–
Lower Transaxle–to–Engine Retaining Bolts (b)3123–
Lower Transaxle–to–Engine Retaining Bolts (c)2115–
Upper Transaxle–to–Engine Mounting Bolts7354–
Upper Transaxle Mounting Bracket Bolts6044–
Rear Mounting Bracket Bolts6044–
Damping Block Connection Nut and Bolt8059–
Torque Converter Bolts4543–
Screw Plugs7.4–65
Transaxle Apply Clamp Bolt5.4–48
Oil Reservoir Lock Plate Bolts5.4–48
Transaxle Case Plate Bolt9.8–87
Transaxle Housing Bolts2922–
Manual Detent Spring Bolt9.8–87
Parking Lock Pawl Bracket Bolts7.4–65
Planetary Ring Gear Nut (Standard)9.8–87
Planetary Ring Gear Nut (Maximum)2922–
Transaxle Rear Cover Bolts2518–
Oil Pump Bolts2518–
Valve Body Bolts11–97
Oil Strainer Bolts9.8–87
Oil Pan Bolts7–62
Unions2518–
Stator Shaft Bolts2518–
Shift Solenoid Valve Bolts11–97
Differential Case–to–Differential Ring Gear Bolt10275–
Page 1610 of 2643
5A2 – 20IAISIN AUTOMATIC TRANSAXLE
DAEWOO V–121 BL4
1. Transaxle Housing
2. Oil Seal
3. Oil Reservoir Plate
4. Transaxle Oil Apply Pipe
5. Differential Gear Oil Apply Pipe
6. Transaxle Oil Apply Pipe Clamp
7. Spring
8. Check Valve Pipe Clamp
9. Apply Gasket
10. Brake Drun Gasket
11. Transaxle Wire
12. O–ring
13. Valve Body
14. Parking Lock Pawl
15. Parking Lock Pawl Shaft
16. Torsion Spring
17. Manual Valve lever Shaft
18. Manual Valve Lever
19. Parking Lock Rod
20. Parking Lock Pawl Bracket
21. Manual Detent Spring
22. Pin
23. Spacer24. Oil Seal
25. Transmission Range (TR) Switch
26. Lock Washer
27. Control Lever
28. Washer
29. Gasket
30. Oil Strainer
31. Oil Pan
32. Gasket
33. Magnet
34. Direct Clutch Accumulator Piston
35. O–ring
36. Spring
37. O–ring
38. Forward Clutch Accumulator Piston
39. O–ring
40. Spring
41. O–ring
42. Overdrive Brake Accumulator Piston
43. O–ring
44. O–ring
45. Spring
Page 1620 of 2643
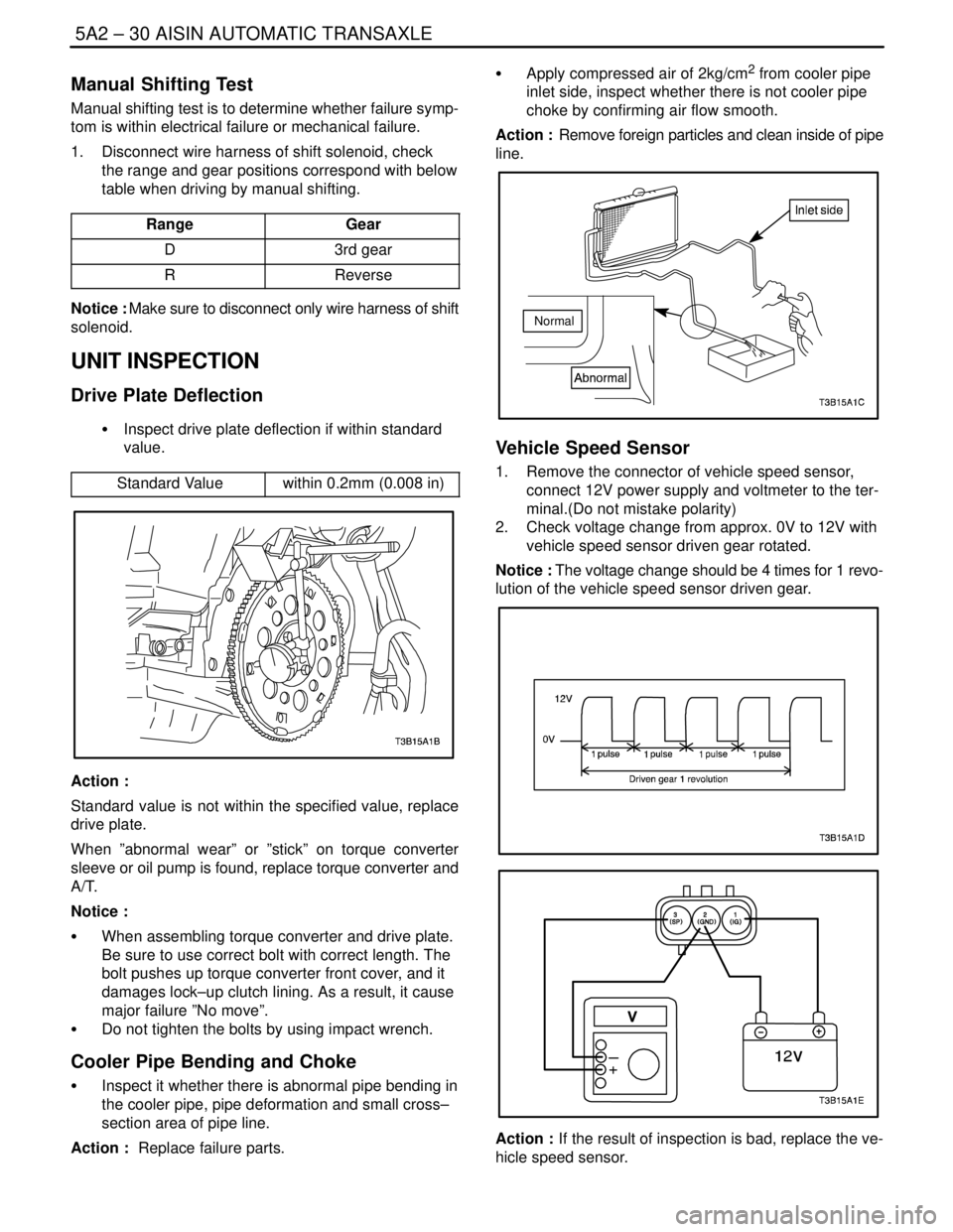
5A2 – 30IAISIN AUTOMATIC TRANSAXLE
DAEWOO V–121 BL4
Manual Shifting Test
Manual shifting test is to determine whether failure symp-
tom is within electrical failure or mechanical failure.
1. Disconnect wire harness of shift solenoid, check
the range and gear positions correspond with below
table when driving by manual shifting.
Range
Gear
D3rd gear
RReverse
Notice : Make sure to disconnect only wire harness of shift
solenoid.
UNIT INSPECTION
Drive Plate Deflection
S Inspect drive plate deflection if within standard
value.
Standard Value
within 0.2mm (0.008 in)
Action :
Standard value is not within the specified value, replace
drive plate.
When ”abnormal wear” or ”stick” on torque converter
sleeve or oil pump is found, replace torque converter and
A/T.
Notice :
S When assembling torque converter and drive plate.
Be sure to use correct bolt with correct length. The
bolt pushes up torque converter front cover, and it
damages lock–up clutch lining. As a result, it cause
major failure ”No move”.
S Do not tighten the bolts by using impact wrench.
Cooler Pipe Bending and Choke
S Inspect it whether there is abnormal pipe bending in
the cooler pipe, pipe deformation and small cross–
section area of pipe line.
Action : Replace failure parts.S Apply compressed air of 2kg/cm
2 from cooler pipe
inlet side, inspect whether there is not cooler pipe
choke by confirming air flow smooth.
Action : Remove foreign particles and clean inside of pipe
line.
Normal
Vehicle Speed Sensor
1. Remove the connector of vehicle speed sensor,
connect 12V power supply and voltmeter to the ter-
minal.(Do not mistake polarity)
2. Check voltage change from approx. 0V to 12V with
vehicle speed sensor driven gear rotated.
Notice : The voltage change should be 4 times for 1 revo-
lution of the vehicle speed sensor driven gear.
Action : If the result of inspection is bad, replace the ve-
hicle speed sensor.
Page 1692 of 2643
5A2 – 102IAISIN AUTOMATIC TRANSAXLE
DAEWOO V–121 BL4
3. Remove the E–ring.
4. Disconnect the shift control cable from the TR
switch lever.
5. Remove the retaining nut and then remove the
washer and the control lever.
6. Using a driver, unstake the lock washer and re-
move the nut.
Installation Procedure
1. Install the Transmission Range (TR) switch onto the
manual valve lever shaft and temporarily install the
2 adjusting bolts.
2. Install the new lock washer and nuts.
Tighten
Tighten the nuts to 12 NSm (106 Ib–in).
3. Temporarily install the control lever.
4. Turn the lever counterclockwise until it stops, then
turn it clockwise 2 notches.
5. Remove the control lever.
Page 1710 of 2643
5A2 – 120IAISIN AUTOMATIC TRANSAXLE
DAEWOO V–121 BL4
22. Disconnect the manual valve control rod from the
manual valve lever, then remove the valve body
assembly.
23. Remove the check valve and spring.
24. Remove the brake drum gasket.
25. Remove the apply gasket.
Page 1720 of 2643
5A2 – 130IAISIN AUTOMATIC TRANSAXLE
DAEWOO V–121 BL4
65. Remove the planetary ring gear nut using planetary
ring gear nut removal/installation socket DW
260–041.
Notice : Remove the nut without unstaking the planetary
ring gear. If chisel or other tool is used to unstake the plan-
etary ring gear, such impact may damage the bearing.
66. Remove the 2 bolts and parking lock pawl bracket.
67. Remove the parking lock pawl shaft, torsion spring
and parking lock pawl.
68. Remove the bolt and manual detent spring.