Page 33 of 96
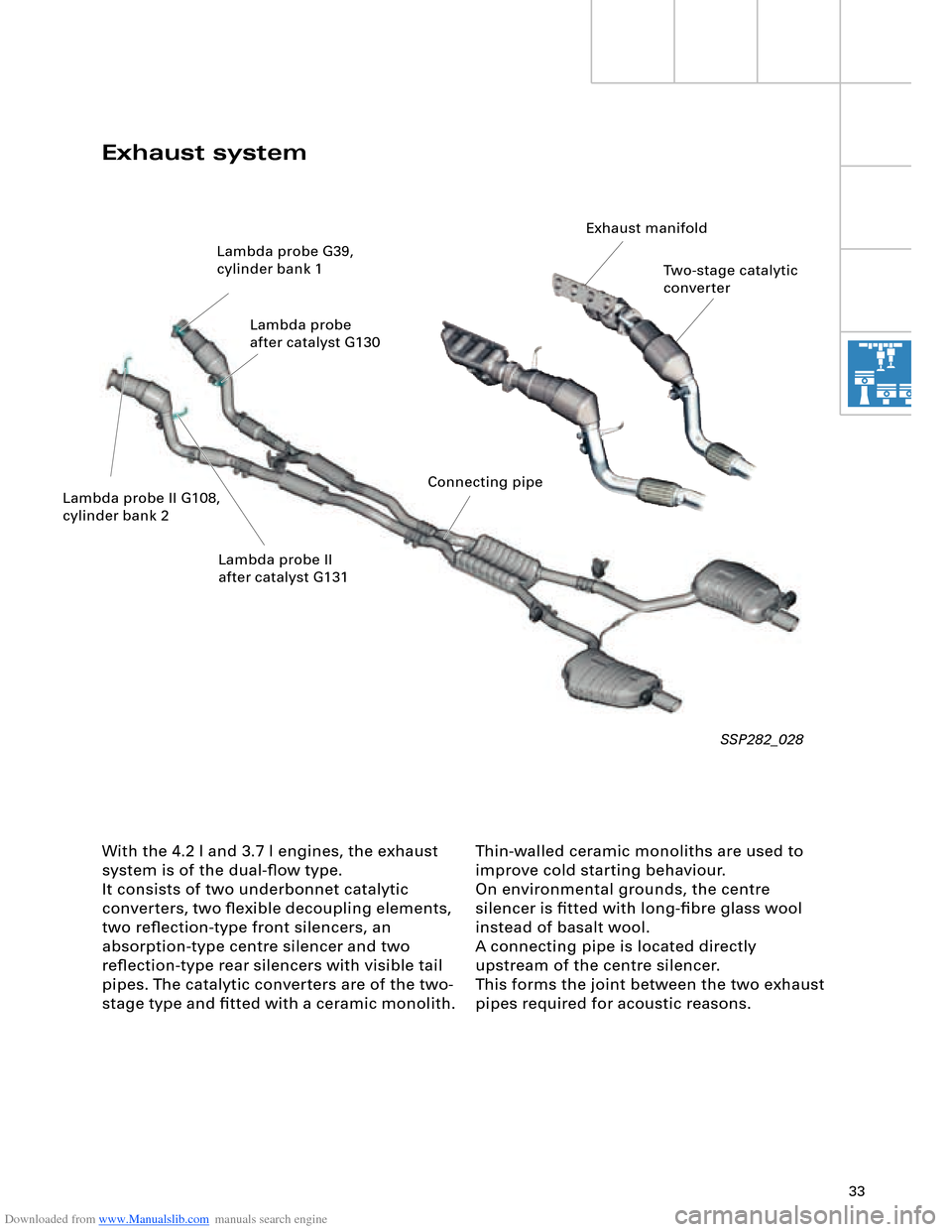
Downloaded from www.Manualslib.com manuals search engine 33
Thin-walled ceramic monoliths are used to
improve cold starting behaviour.
On environmental grounds, the centre
silencer is fitted with long-fibre glass wool
instead of basalt wool.
A connecting pipe is located directly
upstream of the centre silencer.
This forms the joint between the two exhaust
pipes required for acoustic reasons.
With the 4.2 l and 3.7 l engines, the exhaust
system is of the dual-flow type.
It consists of two underbonnet catalytic
converters, two flexible decoupling elements,
two reflection-type front silencers, an
absorption-type centre silencer and two
reflection-type rear silencers with visible tail
pipes. The catalytic converters are of the two-
stage type and fitted with a ceramic monolith.
SSP282_028
Exhaust system
Two-stage catalytic
converter
Lambda probe G39,
cylinder bank 1
Lambda probe
after catalyst G130
Lambda probe II G108,
cylinder bank 2 Lambda probe II
after catalyst G131 Exhaust manifold
Connecting pipe
Page 34 of 96
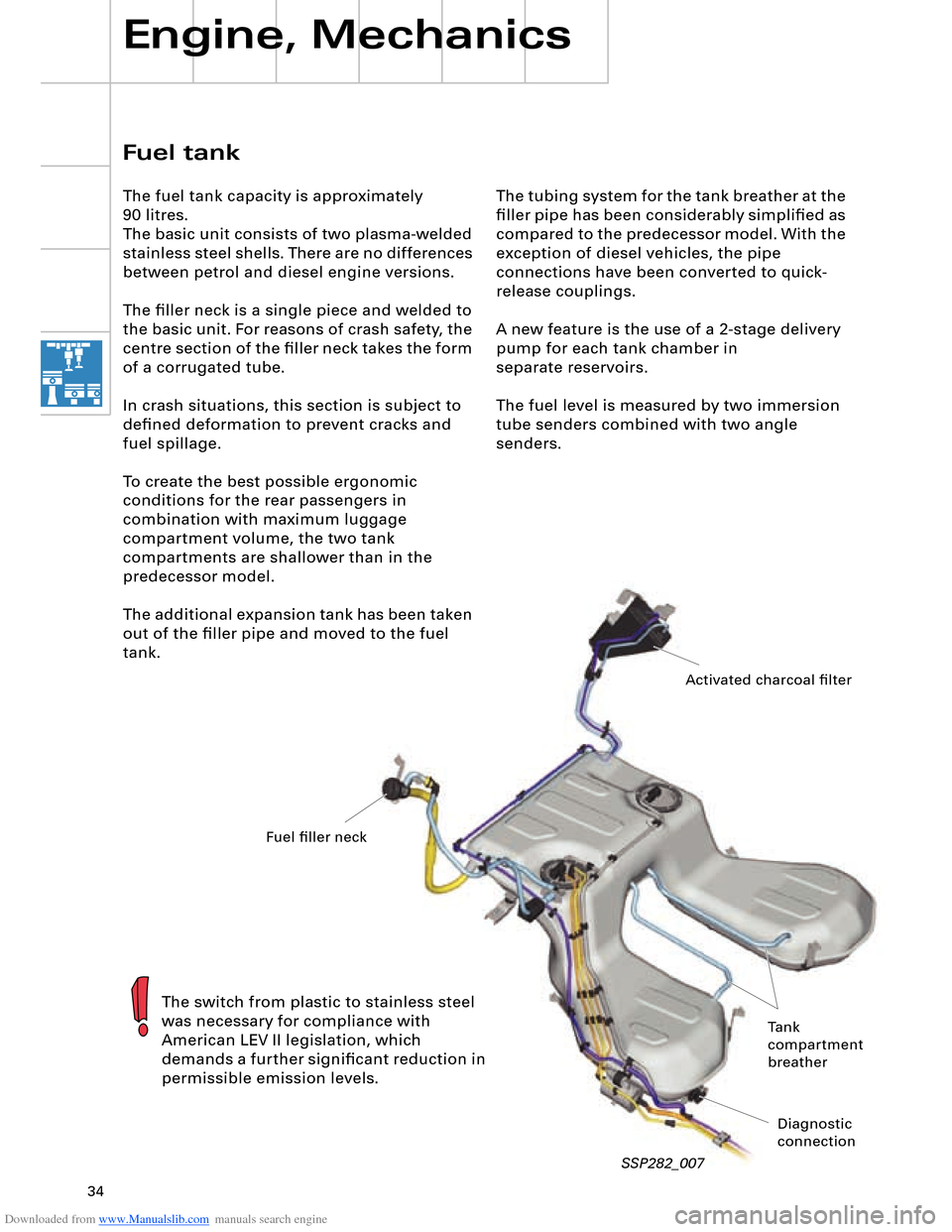
Downloaded from www.Manualslib.com manuals search engine 34
The tubing system for the tank breather at the
filler pipe has been considerably simplified as
compared to the predecessor model. With the
exception of diesel vehicles, the pipe
connections have been converted to quick-
release couplings.
A new feature is the use of a 2-stage delivery
pump for each tank chamber in
separate reservoirs.
The fuel level is measured by two immersion
tube senders combined with two angle
senders.
Engine, Mechanics
SSP282_007
Fuel tank
The fuel tank capacity is approximately
90 litres.
The basic unit consists of two plasma-welded
stainless steel shells. There are no differences
between petrol and diesel engine versions.
The filler neck is a single piece and welded to
the basic unit. For reasons of crash safety, the
centre section of the filler neck takes the form
of a corrugated tube.
In crash situations, this section is subject to
defined deformation to prevent cracks and
fuel spillage.
To create the best possible ergonomic
conditions for the rear passengers in
combination with maximum luggage
compartment volume, the two tank
compartments are shallower than in the
predecessor model.
The additional expansion tank has been taken
out of the filler pipe and moved to the fuel
tank.
The switch from plastic to stainless steel
was necessary for compliance with
American LEV II legislation, which
demands a further significant reduction in
permissible emission levels.
Activated charcoal filter
Fuel filler neck
Tank
compartment
breather
Diagnostic
connection
Page 35 of 96
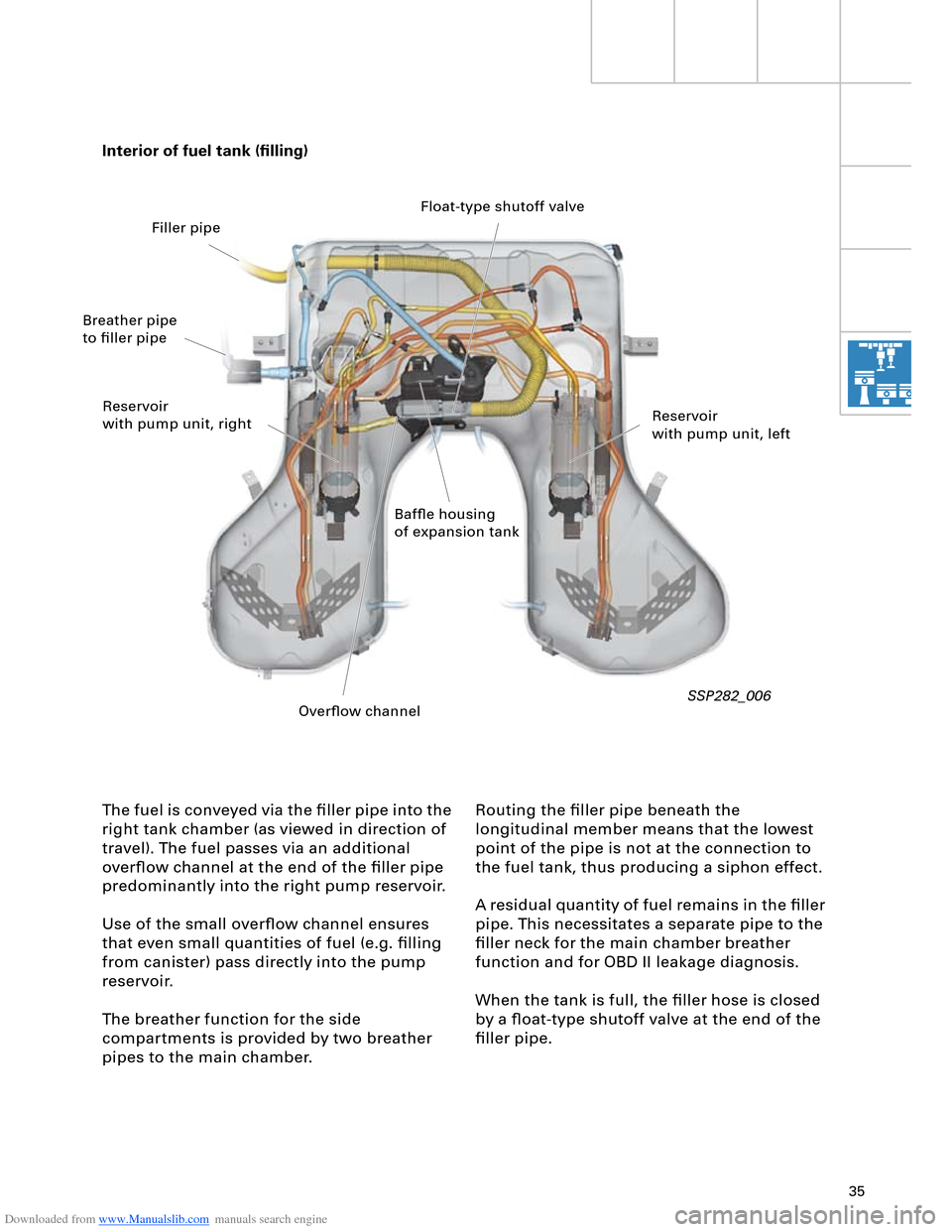
Downloaded from www.Manualslib.com manuals search engine 35
The fuel is conveyed via the filler pipe into the
right tank chamber (as viewed in direction of
travel). The fuel passes via an additional
overflow channel at the end of the filler pipe
predominantly into the right pump reservoir.
Use of the small overflow channel ensures
that even small quantities of fuel (e.g. filling
from canister) pass directly into the pump
reservoir.
The breather function for the side
compartments is provided by two breather
pipes to the main chamber.Routing the filler pipe beneath the
longitudinal member means that the lowest
point of the pipe is not at the connection to
the fuel tank, thus producing a siphon effect.
A residual quantity of fuel remains in the filler
pipe. This necessitates a separate pipe to the
filler neck for the main chamber breather
function and for OBD II leakage diagnosis.
When the tank is full, the filler hose is closed
by a float-type shutoff valve at the end of the
filler pipe. Interior of fuel tank (filling)
SSP282_006
Baffle housing
of expansion tankReservoir
with pump unit, left Reservoir
with pump unit, rightFloat-type shutoff valve
Breather pipe
to filler pipe
Overflow channel Filler pipe
Page 36 of 96
Downloaded from www.Manualslib.com manuals search engine 36
Engine, Mechanics
Function
The main functions of the float-type rollover
valve are as follows:
– Closing-off of pipe to filler neck in the
event of rollover
– Closing in dynamic driving mode
– Closing by rising of float in valve in the
event of a brief excess of fuel in the tank
due to sloshing
Closing-off of the pipe to the activated
charcoal filter stops fuel overflowing into it. Expansion tank
The expansion tank (capacity approx. 2 litres)
consists of a plastic housing clipped to the
upper shell of the tank.
The internal expansion tank houses a float-
type rollover valve and a small suction jet
pump which constantly pumps the tank empty
whilst driving.
SSP282_009
Inlet pipe
from tank filler neck
Float-type
rollover valve
Float-type shutoff valve Breather pipe
Suction jet pump
intake connection
Page 37 of 96
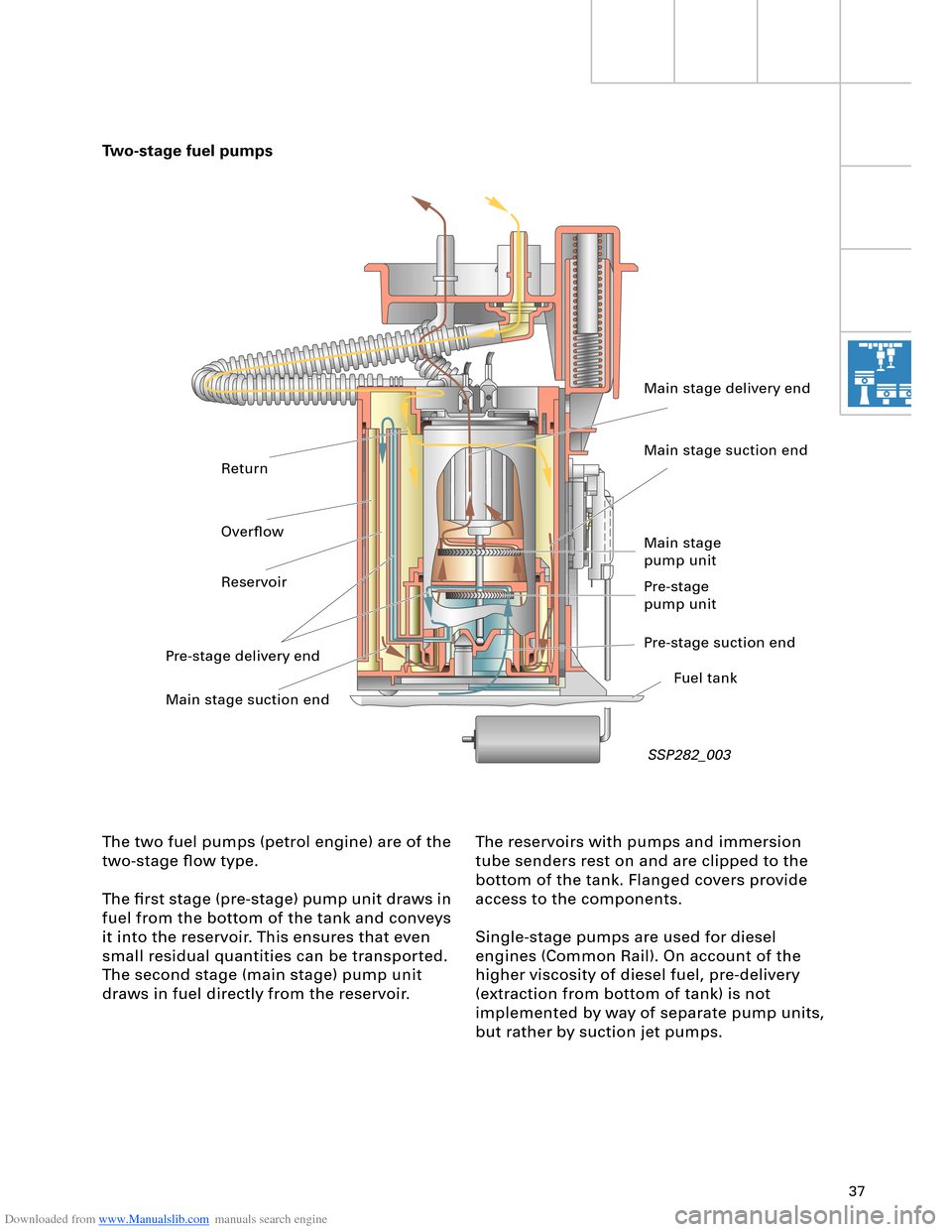
Downloaded from www.Manualslib.com manuals search engine 37
The reservoirs with pumps and immersion
tube senders rest on and are clipped to the
bottom of the tank. Flanged covers provide
access to the components.
Single-stage pumps are used for diesel
engines (Common Rail). On account of the
higher viscosity of diesel fuel, pre-delivery
(extraction from bottom of tank) is not
implemented by way of separate pump units,
but rather by suction jet pumps. Two-stage fuel pumps
The two fuel pumps (petrol engine) are of the
two-stage flow type.
The first stage (pre-stage) pump unit draws in
fuel from the bottom of the tank and conveys
it into the reservoir. This ensures that even
small residual quantities can be transported.
The second stage (main stage) pump unit
draws in fuel directly from the reservoir.
SSP282_003
Main stage delivery end
Main stage suction end
Main stage
pump unit
Pre-stage
pump unit
Pre-stage suction end
Fuel tank
Main stage suction end Pre-stage delivery endReservoirOverflow Return
Page 38 of 96
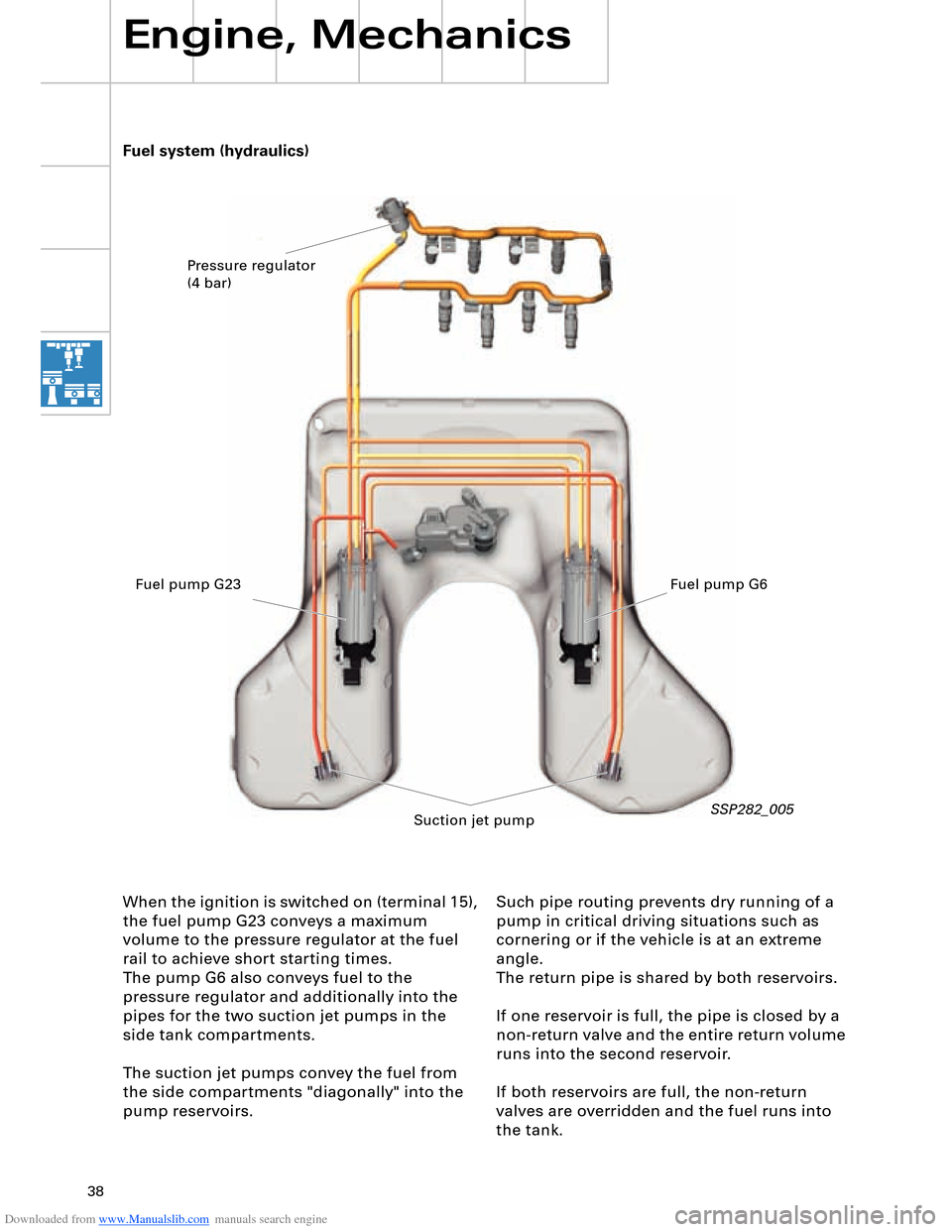
Downloaded from www.Manualslib.com manuals search engine 38
Engine, Mechanics
Such pipe routing prevents dry running of a
pump in critical driving situations such as
cornering or if the vehicle is at an extreme
angle.
The return pipe is shared by both reservoirs.
If one reservoir is full, the pipe is closed by a
non-return valve and the entire return volume
runs into the second reservoir.
If both reservoirs are full, the non-return
valves are overridden and the fuel runs into
the tank. Fuel system (hydraulics)
When the ignition is switched on (terminal 15),
the fuel pump G23 conveys a maximum
volume to the pressure regulator at the fuel
rail to achieve short starting times.
The pump G6 also conveys fuel to the
pressure regulator and additionally into the
pipes for the two suction jet pumps in the
side tank compartments.
The suction jet pumps convey the fuel from
the side compartments "diagonally" into the
pump reservoirs.
SSP282_005
Pressure regulator
(4 bar)
Fuel pump G23 Fuel pump G6
Suction jet pump
Page 39 of 96
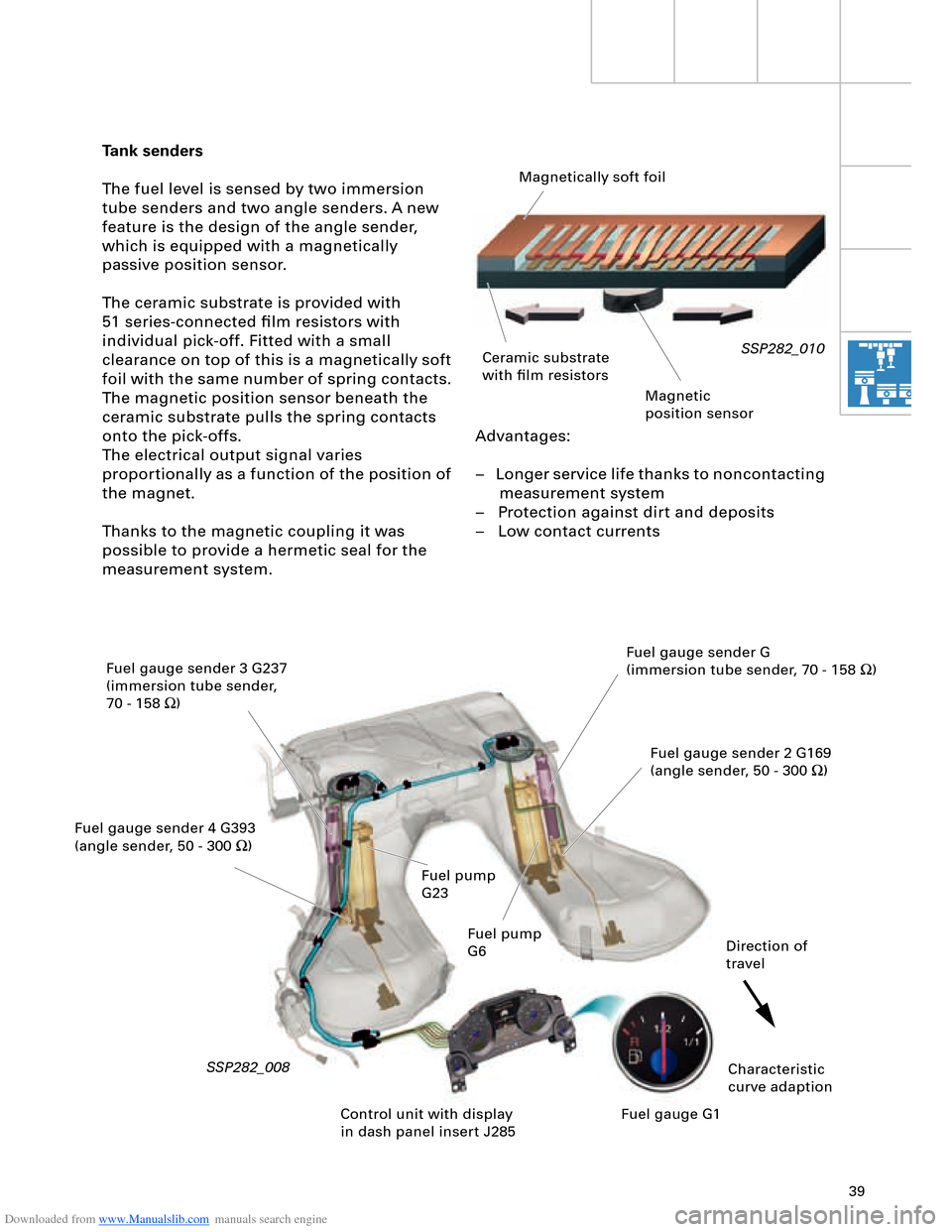
Downloaded from www.Manualslib.com manuals search engine 39
Advantages:
– Longer service life thanks to noncontacting
measurement system
– Protection against dirt and deposits
– Low contact currents
Tank senders
The fuel level is sensed by two immersion
tube senders and two angle senders. A new
feature is the design of the angle sender,
which is equipped with a magnetically
passive position sensor.
The ceramic substrate is provided with
51 series-connected film resistors with
individual pick-off. Fitted with a small
clearance on top of this is a magnetically soft
foil with the same number of spring contacts.
The magnetic position sensor beneath the
ceramic substrate pulls the spring contacts
onto the pick-offs.
The electrical output signal varies
proportionally as a function of the position of
the magnet.
Thanks to the magnetic coupling it was
possible to provide a hermetic seal for the
measurement system.
SSP282_010
SSP282_008
Magnetically soft foil
Ceramic substrate
with film resistors
Magnetic
position sensor
Fuel gauge sender 3 G237
(immersion tube sender,
70 - 158 W)
Fuel gauge sender 4 G393
(angle sender, 50 - 300 W)Fuel gauge sender G
(immersion tube sender, 70 - 158 W)
Fuel gauge sender 2 G169
(angle sender, 50 - 300 W)
Characteristic
curve adaption Direction of
travel
Control unit with display
in dash panel insert J285Fuel gauge G1 Fuel pump
G23
Fuel pump
G6
Page 40 of 96
Downloaded from www.Manualslib.com manuals search engine 40
Engine, Mechanics
The fuel level is determined by way of a
logical system of immersion tube and angle
sender signals.
a - Low levels are determined exclusively by
way of the angle sender measured values
b - High levels are determined exclusively by
way of the immersion tube sender
measured values.
c - Medium levels are determined by a
combination of all sender signals
SSP282_004
The sender signals are evaluated by the dash
panel insert. All senders are connected in
parallel.
The wires are bunched beneath the fuel tank,
thus enabling resistance measurements to be
taken without the need for further
dismantling. Determining fuel level
a c b