Page 176 of 694
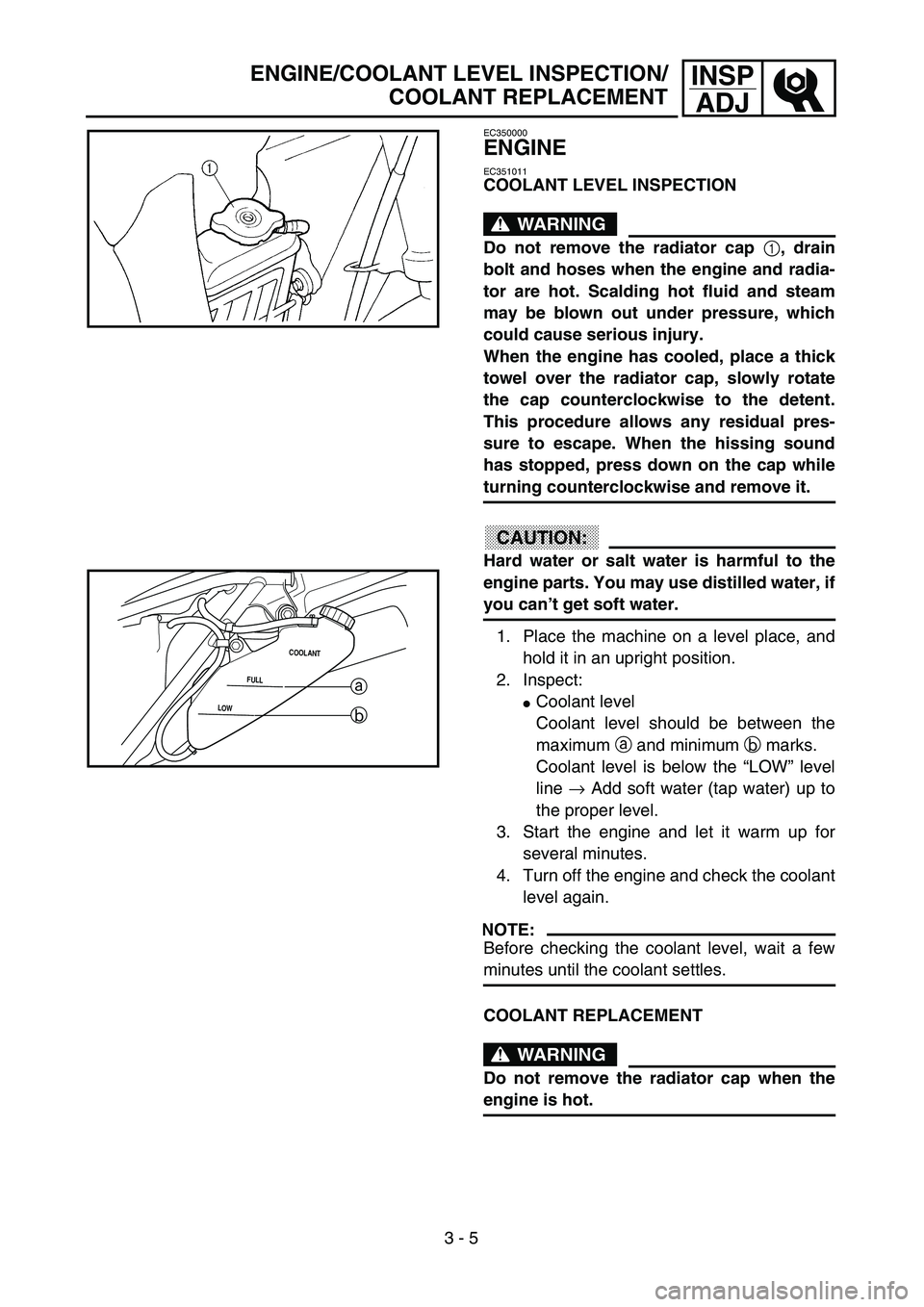
3 - 5
INSP
ADJ
EC350000
ENGINE
EC351011
COOLANT LEVEL INSPECTION
WARNING
Do not remove the radiator cap 1, drain
bolt and hoses when the engine and radia-
tor are hot. Scalding hot fluid and steam
may be blown out under pressure, which
could cause serious injury.
When the engine has cooled, place a thick
towel over the radiator cap, slowly rotate
the cap counterclockwise to the detent.
This procedure allows any residual pres-
sure to escape. When the hissing sound
has stopped, press down on the cap while
turning counterclockwise and remove it.
CAUTION:
Hard water or salt water is harmful to the
engine parts. You may use distilled water, if
you can’t get soft water.
1. Place the machine on a level place, and
hold it in an upright position.
2. Inspect:
Coolant level
Coolant level should be between the
maximum a and minimum b marks.
Coolant level is below the “LOW” level
line → Add soft water (tap water) up to
the proper level.
3. Start the engine and let it warm up for
several minutes.
4. Turn off the engine and check the coolant
level again.
NOTE:
Before checking the coolant level, wait a few
minutes until the coolant settles.
LOWFULLCOOLANT
a
b
COOLANT REPLACEMENT
WARNING
Do not remove the radiator cap when the
engine is hot.
ENGINE/COOLANT LEVEL INSPECTION/
COOLANT REPLACEMENT
Page 180 of 694
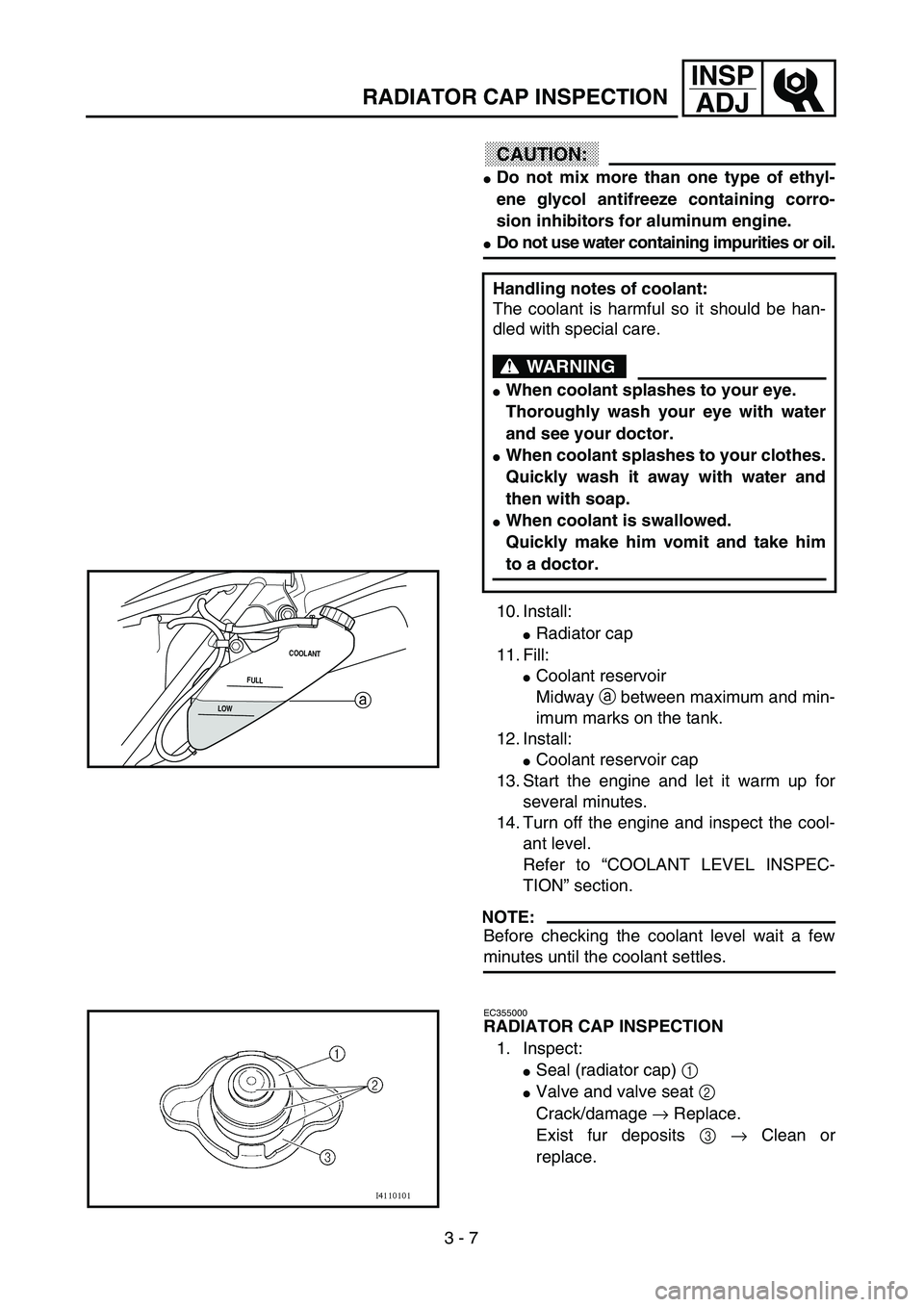
3 - 7
INSP
ADJ
RADIATOR CAP INSPECTION
CAUTION:
Do not mix more than one type of ethyl-
ene glycol antifreeze containing corro-
sion inhibitors for aluminum engine.
Do not use water containing impurities or oil.
10. Install:
Radiator cap
11. Fill:
Coolant reservoir
Midway a between maximum and min-
imum marks on the tank.
12. Install:
Coolant reservoir cap
13. Start the engine and let it warm up for
several minutes.
14. Turn off the engine and inspect the cool-
ant level.
Refer to “COOLANT LEVEL INSPEC-
TION” section.
NOTE:
Before checking the coolant level wait a few
minutes until the coolant settles.Handling notes of coolant:
The coolant is harmful so it should be han-
dled with special care.
WARNING
When coolant splashes to your eye.
Thoroughly wash your eye with water
and see your doctor.
When coolant splashes to your clothes.
Quickly wash it away with water and
then with soap.
When coolant is swallowed.
Quickly make him vomit and take him
to a doctor.
LOWFULLCOOLANTa
EC355000
RADIATOR CAP INSPECTION
1. Inspect:
Seal (radiator cap) 1
Valve and valve seat 2
Crack/damage → Replace.
Exist fur deposits 3 → Clean or
replace.
Page 186 of 694
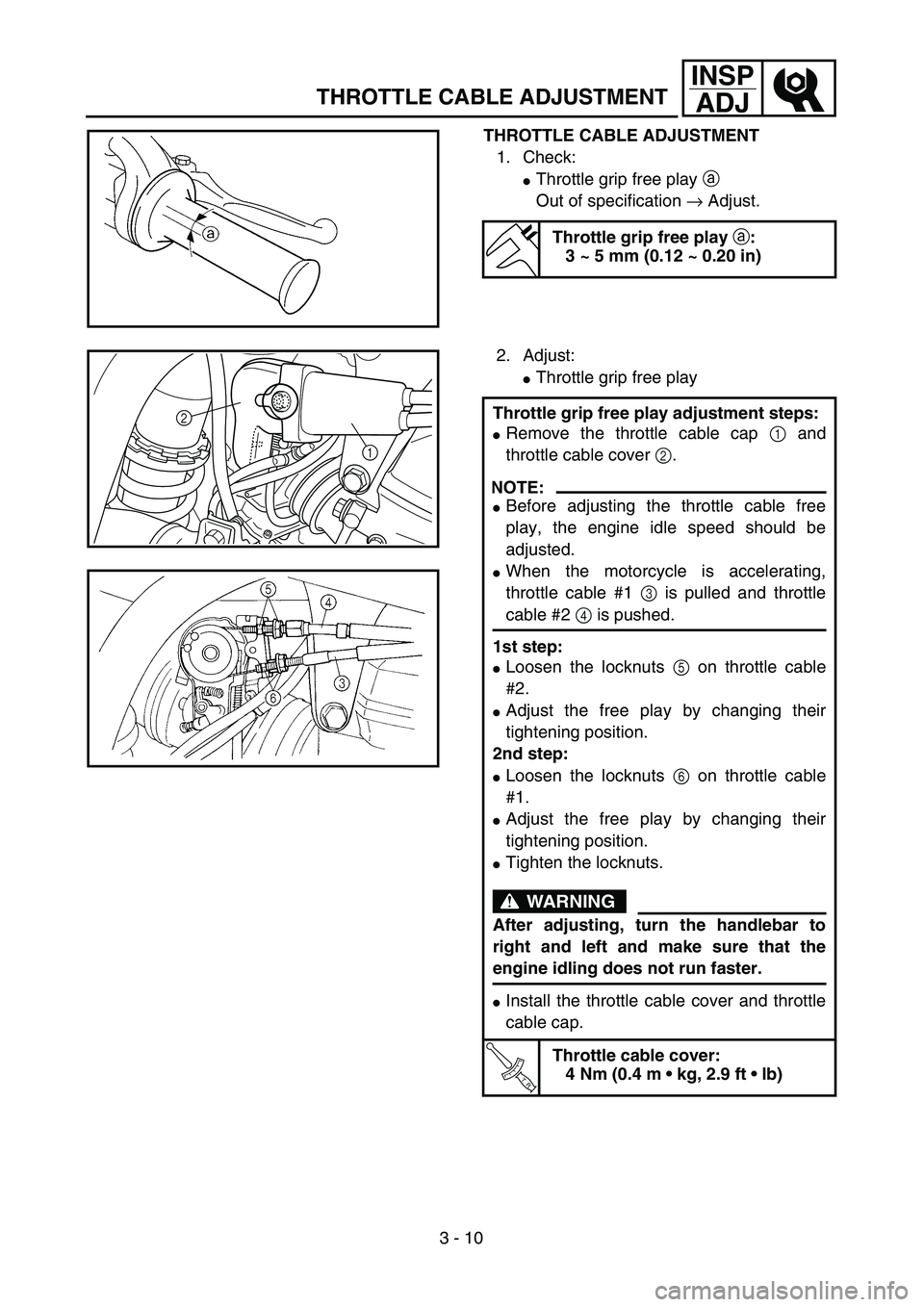
3 - 10
INSP
ADJ
THROTTLE CABLE ADJUSTMENT
THROTTLE CABLE ADJUSTMENT
1. Check:
Throttle grip free play a
Out of specification → Adjust.
Throttle grip free play a:
3 ~ 5 mm (0.12 ~ 0.20 in)
2. Adjust:
Throttle grip free play
Throttle grip free play adjustment steps:
Remove the throttle cable cap 1 and
throttle cable cover 2.
NOTE:
Before adjusting the throttle cable free
play, the engine idle speed should be
adjusted.
When the motorcycle is accelerating,
throttle cable #1 3 is pulled and throttle
cable #2 4 is pushed.
1st step:
Loosen the locknuts 5 on throttle cable
#2.
Adjust the free play by changing their
tightening position.
2nd step:
Loosen the locknuts 6 on throttle cable
#1.
Adjust the free play by changing their
tightening position.
Tighten the locknuts.
WARNING
After adjusting, turn the handlebar to
right and left and make sure that the
engine idling does not run faster.
Install the throttle cable cover and throttle
cable cap.
T R..
Throttle cable cover:
4 Nm (0.4 m • kg, 2.9 ft • lb)
2
1
Page 200 of 694
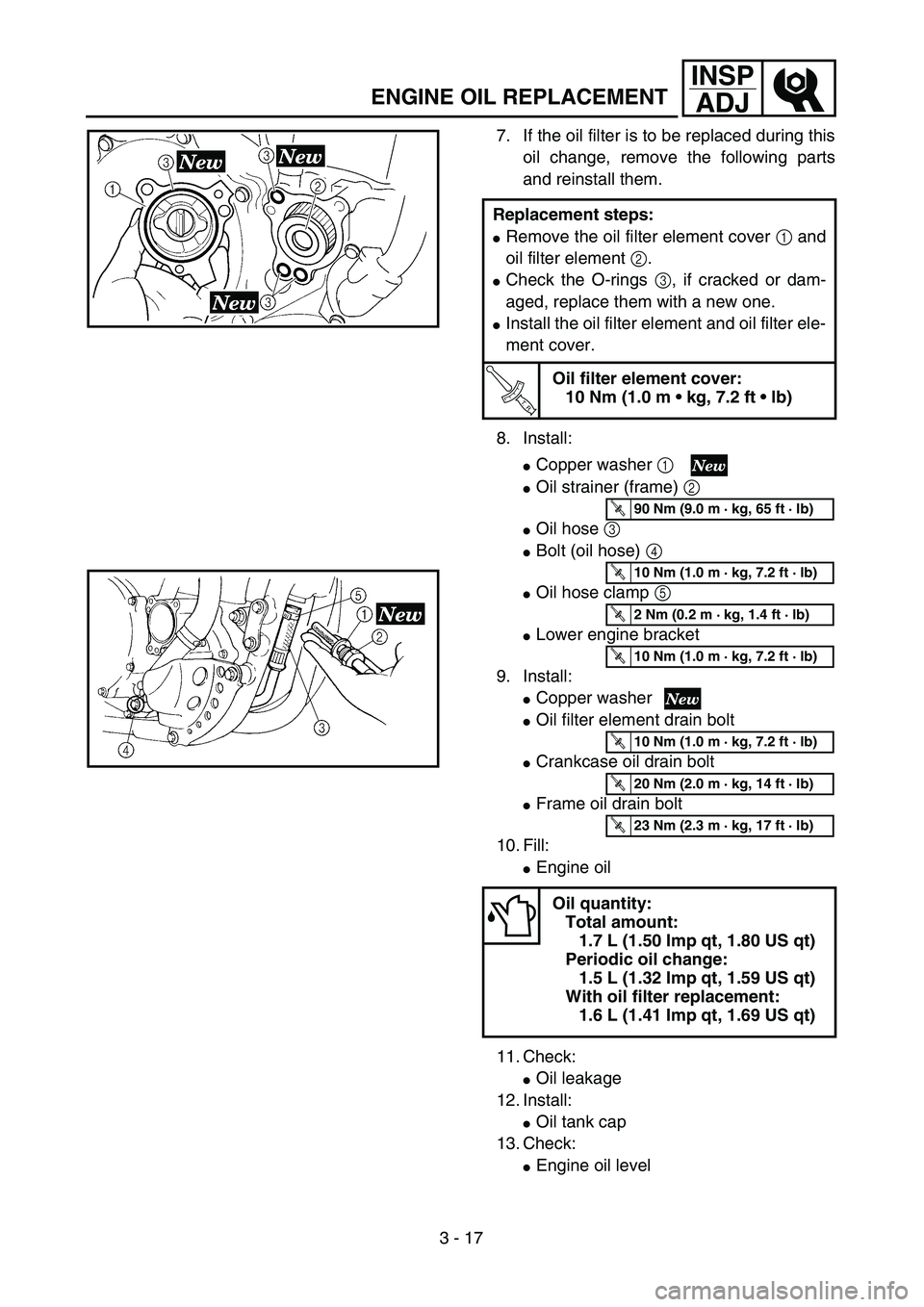
3 - 17
INSP
ADJ
ENGINE OIL REPLACEMENT
7. If the oil filter is to be replaced during this
oil change, remove the following parts
and reinstall them.
8. Install:
Copper washer 1
Oil strainer (frame) 2
Oil hose 3
Bolt (oil hose) 4
Oil hose clamp 5
Lower engine bracket
9. Install:
Copper washer
Oil filter element drain bolt
Crankcase oil drain bolt
Frame oil drain bolt
10. Fill:
Engine oil
11. Check:
Oil leakage
12. Install:
Oil tank cap
13. Check:
Engine oil level Replacement steps:
Remove the oil filter element cover 1 and
oil filter element 2.
Check the O-rings 3, if cracked or dam-
aged, replace them with a new one.
Install the oil filter element and oil filter ele-
ment cover.
T R..
Oil filter element cover:
10 Nm (1.0 m • kg, 7.2 ft • lb)
Oil quantity:
Total amount:
1.7 L (1.50 Imp qt, 1.80 US qt)
Periodic oil change:
1.5 L (1.32 Imp qt, 1.59 US qt)
With oil filter replacement:
1.6 L (1.41 Imp qt, 1.69 US qt)
T R..90 Nm (9.0 m · kg, 65 ft · lb)
T R..10 Nm (1.0 m · kg, 7.2 ft · lb)
T R..2 Nm (0.2 m · kg, 1.4 ft · lb)
T R..10 Nm (1.0 m · kg, 7.2 ft · lb)
T R..10 Nm (1.0 m · kg, 7.2 ft · lb)
T R..20 Nm (2.0 m · kg, 14 ft · lb)
T R..23 Nm (2.3 m · kg, 17 ft · lb)
Page 202 of 694
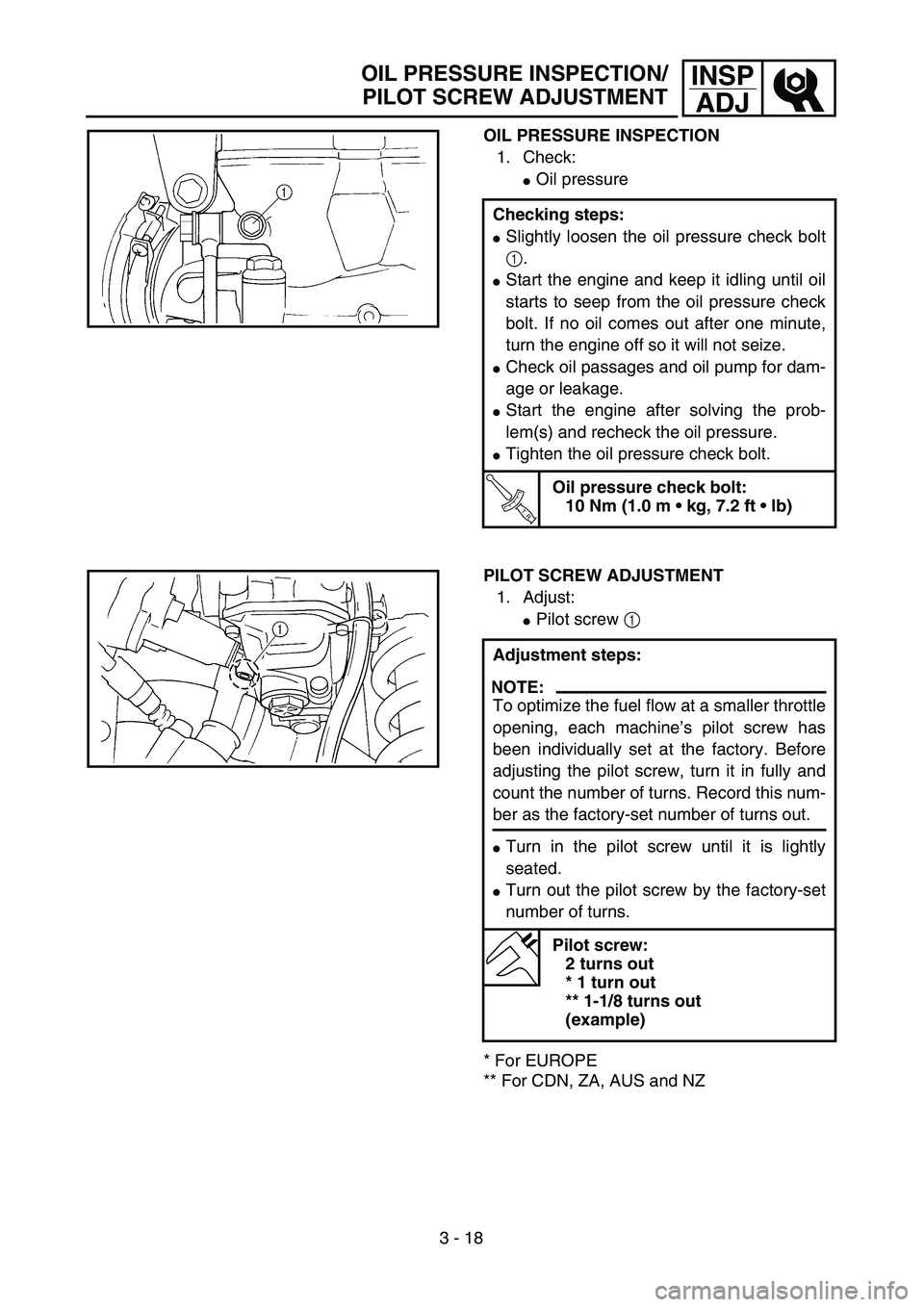
3 - 18
INSP
ADJ
OIL PRESSURE INSPECTION
1. Check:
Oil pressure
Checking steps:
Slightly loosen the oil pressure check bolt
1.
Start the engine and keep it idling until oil
starts to seep from the oil pressure check
bolt. If no oil comes out after one minute,
turn the engine off so it will not seize.
Check oil passages and oil pump for dam-
age or leakage.
Start the engine after solving the prob-
lem(s) and recheck the oil pressure.
Tighten the oil pressure check bolt.
T R..
Oil pressure check bolt:
10 Nm (1.0 m • kg, 7.2 ft • lb)
PILOT SCREW ADJUSTMENT
1. Adjust:
Pilot screw 1
* For EUROPE
** For CDN, ZA, AUS and NZAdjustment steps:
NOTE:
To optimize the fuel flow at a smaller throttle
opening, each machine’s pilot screw has
been individually set at the factory. Before
adjusting the pilot screw, turn it in fully and
count the number of turns. Record this num-
ber as the factory-set number of turns out.
Turn in the pilot screw until it is lightly
seated.
Turn out the pilot screw by the factory-set
number of turns.
Pilot screw:
2 turns out
* 1 turn out
** 1-1/8 turns out
(example)
OIL PRESSURE INSPECTION/
PILOT SCREW ADJUSTMENT
Page 204 of 694
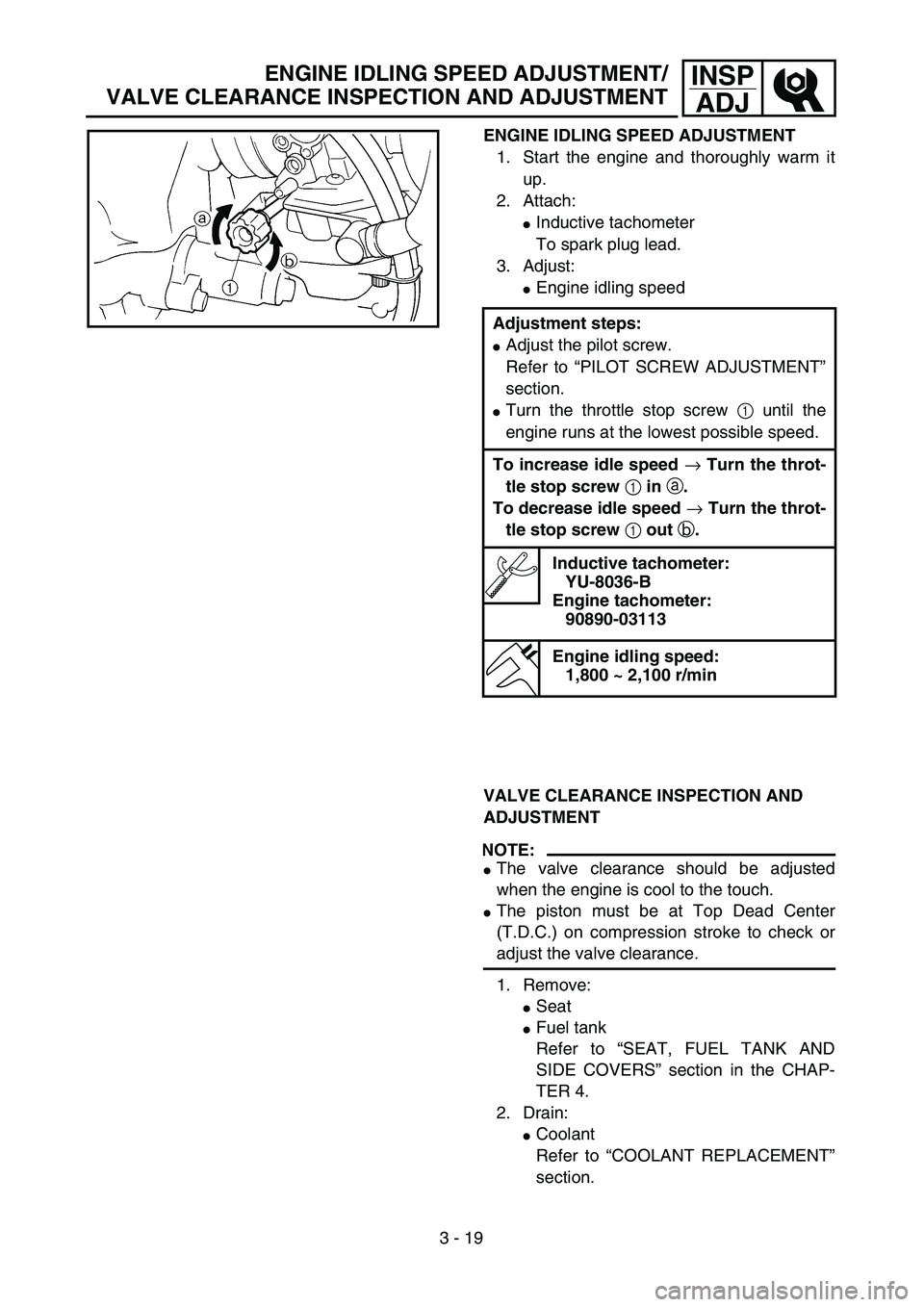
3 - 19
INSP
ADJ
ENGINE IDLING SPEED ADJUSTMENT
1. Start the engine and thoroughly warm it
up.
2. Attach:
Inductive tachometer
To spark plug lead.
3. Adjust:
Engine idling speed
Adjustment steps:
Adjust the pilot screw.
Refer to “PILOT SCREW ADJUSTMENT”
section.
Turn the throttle stop screw 1 until the
engine runs at the lowest possible speed.
To increase idle speed → Turn the throt-
tle stop screw 1 in a.
To decrease idle speed → Turn the throt-
tle stop screw 1 out b.
Inductive tachometer:
YU-8036-B
Engine tachometer:
90890-03113
Engine idling speed:
1,800 ~ 2,100 r/min
VALVE CLEARANCE INSPECTION AND
ADJUSTMENT
NOTE:
The valve clearance should be adjusted
when the engine is cool to the touch.
The piston must be at Top Dead Center
(T.D.C.) on compression stroke to check or
adjust the valve clearance.
1. Remove:
Seat
Fuel tank
Refer to “SEAT, FUEL TANK AND
SIDE COVERS” section in the CHAP-
TER 4.
2. Drain:
Coolant
Refer to “COOLANT REPLACEMENT”
section.
ENGINE IDLING SPEED ADJUSTMENT/
VALVE CLEARANCE INSPECTION AND ADJUSTMENT
Page 206 of 694
3 - 20
INSP
ADJ
VALVE CLEARANCE INSPECTION AND ADJUSTMENT
3. Remove:
Right radiator
Refer to “RADIATOR” section in the
CHAPTER 4.
Carburetor
Refer to “CARBURETOR” section in
the CHAPTER 4.
Spark plug
Upper engine bracket
Cylinder head cover
Refer to “CAMSHAFTS” section in the
CHAPTER 4.
4. Remove:
Timing mark accessing screw 1
Crankshaft end accessing screw 2
O-ring
5. Check:
Valve clearance
Out of specification → Adjust.
Valve clearance (cold):
Intake valve:
0.10 ~ 0.15 mm (0.0039 ~ 0.0059 in)
Exhaust valve:
0.17 ~ 0.22 mm (0.0067 ~ 0.0087 in)
Page 238 of 694
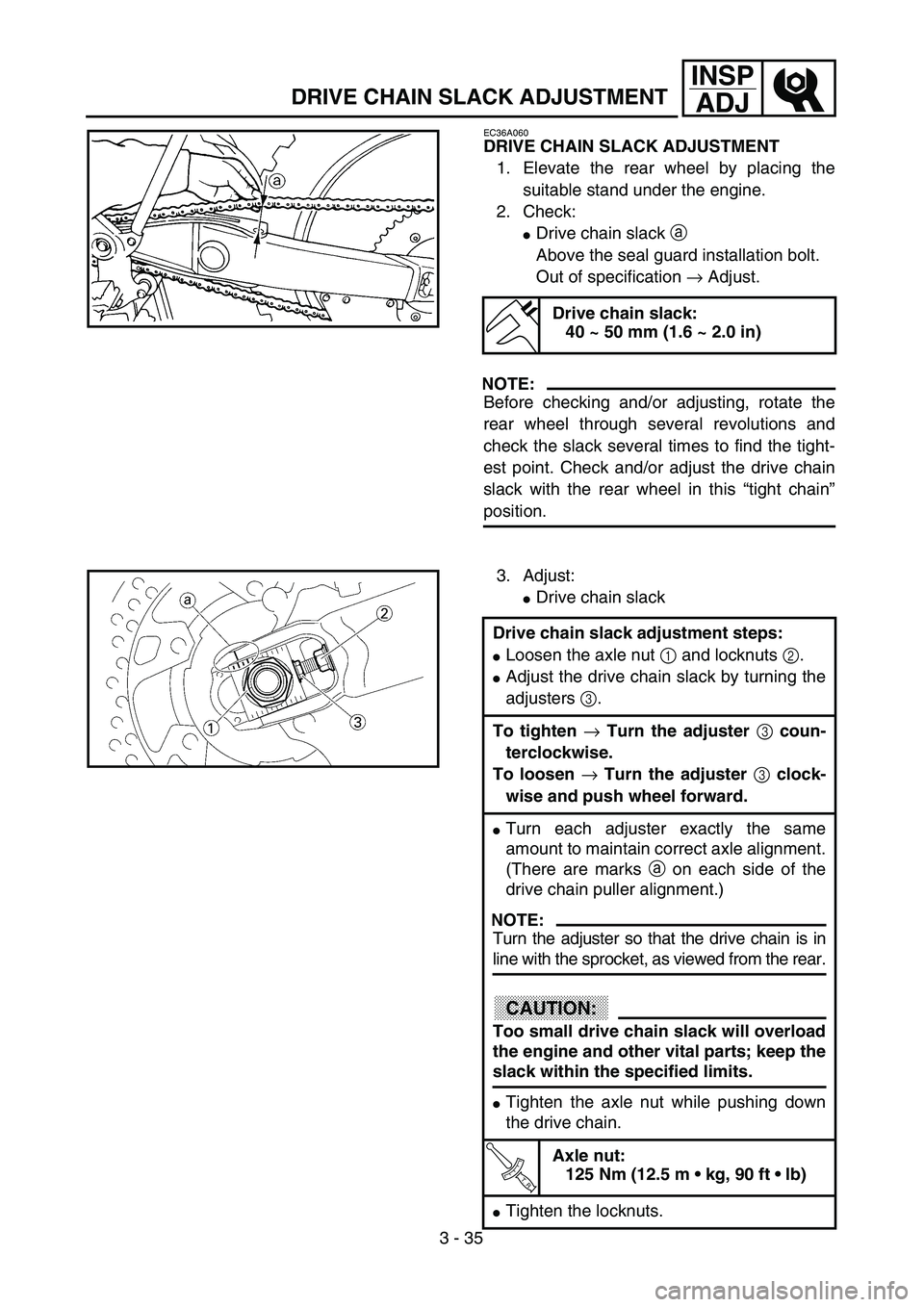
3 - 35
INSP
ADJ
DRIVE CHAIN SLACK ADJUSTMENT
EC36A060
DRIVE CHAIN SLACK ADJUSTMENT
1. Elevate the rear wheel by placing the
suitable stand under the engine.
2. Check:
Drive chain slack a
Above the seal guard installation bolt.
Out of specification → Adjust.
NOTE:
Before checking and/or adjusting, rotate the
rear wheel through several revolutions and
check the slack several times to find the tight-
est point. Check and/or adjust the drive chain
slack with the rear wheel in this “tight chain”
position.
Drive chain slack:
40 ~ 50 mm (1.6 ~ 2.0 in)
3. Adjust:
Drive chain slack
Drive chain slack adjustment steps:
Loosen the axle nut 1 and locknuts 2.
Adjust the drive chain slack by turning the
adjusters 3.
To tighten → Turn the adjuster 3 coun-
terclockwise.
To loosen → Turn the adjuster 3 clock-
wise and push wheel forward.
Turn each adjuster exactly the same
amount to maintain correct axle alignment.
(There are marks a on each side of the
drive chain puller alignment.)
NOTE:
Turn the adjuster so that the drive chain is in
line with the sprocket, as viewed from the rear.
CAUTION:
Too small drive chain slack will overload
the engine and other vital parts; keep the
slack within the specified limits.
Tighten the axle nut while pushing down
the drive chain.
T R..
Axle nut:
125 Nm (12.5 m • kg, 90 ft • lb)
Tighten the locknuts.