Page 79 of 656
SPEC
2 - 6
MAINTENANCE SPECIFICATIONS
Stem runout limit ---- 0.01 mm
(0.0004 in)
Valve seat width IN 0.9 ~ 1.1 mm
(0.0354 ~ 0.0433 in)1.6 mm
(0.0630 in)
EX 0.9 ~ 1.1 mm
(0.0354 ~ 0.0433 in)1.6 mm
(0.0630 in)
Valve spring:
Free length IN 37.81 mm (1.49 in) 35.9 mm
(1.41 in)
EX 37.54 mm (1.48 in) 35.7 mm
(1.41 in)
Set length (valve closed) IN 29.13 mm (1.15 in) ----
EX 29.30 mm (1.15 in) ----
Compressed pressure
(installed) IN 99 ~ 114 N
(10.1 ~ 11.6 kg, 22.27 ~ 25.57 lb)----
EX 126 ~ 144 N
(12.9 ~ 14.7 kg, 28.44 ~ 32.41 lb)----
Tilt limit IN ----2.5˚/ 1.7 mm
(2.5˚/0.067 in)
EX ----2.5˚/1.6 mm
(2.5˚/0.063 in)
Direction of winding
(top view) IN Clockwise ----
EX Clockwise ----
Piston:
Piston to cylinder clearance 0.040 ~ 0.065 mm
(0.0016 ~ 0.0026 in)0.1 mm
(0.004 in)
Piston size “D” 76.955 ~ 76.970 mm
(3.0297 ~ 3.0303 in)----
Measuring point “H” 8 mm (0.31 in) ----
Piston off-set 0.5 mm (0.020 in)/IN-side ----Item Standard Limit
*
H
D
Page 168 of 656
3 - 5
INSP
ADJ
EC350000
ENGINE
COOLANT LEVEL INSPECTION
WARNING
Do not remove the radiator cap 1, drain
bolt and hoses when the engine and radia-
tor are hot. Scalding hot fluid and steam
may be blown out under pressure, which
could cause serious injury.
When the engine has cooled, place a thick
towel over the radiator cap, slowly rotate
the cap counterclockwise to the detent.
This procedure allows any residual pres-
sure to escape. When the hissing sound
has stopped, press down on the cap while
turning counterclockwise and remove it.
CAUTION:
Hard water or salt water is harmful to the
engine parts. You may use distilled water, if
you can’t get soft water.
1. Place the machine on a level place, and
hold it in an upright position.
2. Remove:
lRadiator cap
3. Check:
lCoolant level a
Coolant level low ® Add coolant.
1Radiator
1a
ENGINE/COOLANT LEVEL INSPECTION
Page 180 of 656
3 - 11
INSP
ADJTHROTTLE LUBRICATION/
DECOMPRESSION ADJUSTMENT
THROTTLE LUBRICATION
1. Remove:
lRubber cover 1
lThrottle grip cap 2
2. Apply:
lLithium soap base grease
On the throttle cable end a.
3. Install:
lThrottle grip cap
lScrew (throttle grip cap)
lRubber cover
T R..4 Nm (0.4 m · kg, 2.9 ft · lb)
DECOMPRESSION ADJUSTMENT
1. Check:
lDecompression lever free play a
Out of specification ® Adjust.
Checking steps:
lRemove the timing mark accessing screw
1 and crankshaft end accessing screw
2.
lTurn the crankshaft counterclockwise with
a wrench.
NOTE:
Squeezing the decompression lever allows
the crankshaft to be turned easily.
lAlign the T.D.C. mark b on the rotor with
the align mark c on the crankcase cover
when piston is at T.D.C. on compression
stroke.
lCheck the free play.
Free play a:
5 ~ 9 mm (0.20 ~ 0.35 in)
Page 200 of 656
3 - 21
INSP
ADJ
VALVE CLEARANCE INSPECTION AND ADJUSTMENT
Checking steps:
lTurn the crankshaft counterclockwise with
a wrench.
NOTE:
Squeezing the decompression lever allows
the crankshaft to be turned easily.
lAlign the T.D.C. mark a on the rotor with
the align mark b on the crankcase cover
when piston is at T.D.C. on compression
stroke.
NOTE:
In order to be sure that the piston is at Top
Dead Center, the punch mark c on the
exhaust camshaft and the punch mark d on
the intake camshaft must align with the cyl-
inder head surface, as shown in the illustra-
tion.
lMeasure the valve clearance e using a
feeler gauge 1.
NOTE:
Record the measured reading if the clear-
ance is incorrect.
6. Adjust:
lValve clearance
Adjustment steps:
lRemove the camshaft (intake and exhaust).
Refer to “CAMSHAFTS” section in the
CHAPTER 4.
Page 228 of 656
3 - 34
INSP
ADJ
FRONT FORK INSPECTION
3. Adjust:
lDrive chain slack
Drive chain slack adjustment steps:
lLoosen the axle nut 1 and locknuts 2.
lAdjust chain slack by turning the adjusters
3.
To tighten ® Turn adjuster 3 counter-
clockwise.
To loosen ® Turn adjuster 3 clockwise
and push wheel forward.
lTurn each adjuster exactly the same
amount to maintain correct axle alignment.
(There are marks a on each side of chain
puller alignment.)
NOTE:
Turn the adjuster so that the chain is in line
with the sprocket, as viewed from the rear.
CAUTION:
Too small chain slack will overload the
engine and other vital parts; keep the
slack within the specified limits.
lTighten the axle nut while pushing down
the drive chain.
T R..
Axle nut:
125 Nm (12.5 m • kg, 90 ft • lb)
lTighten the locknuts.
EC36C000
FRONT FORK INSPECTION
1. Inspect:
lFront fork smooth action
Operate the front brake and stroke the
front fork.
Unsmooth action/oil leakage ® Repair
or replace.
Page 264 of 656
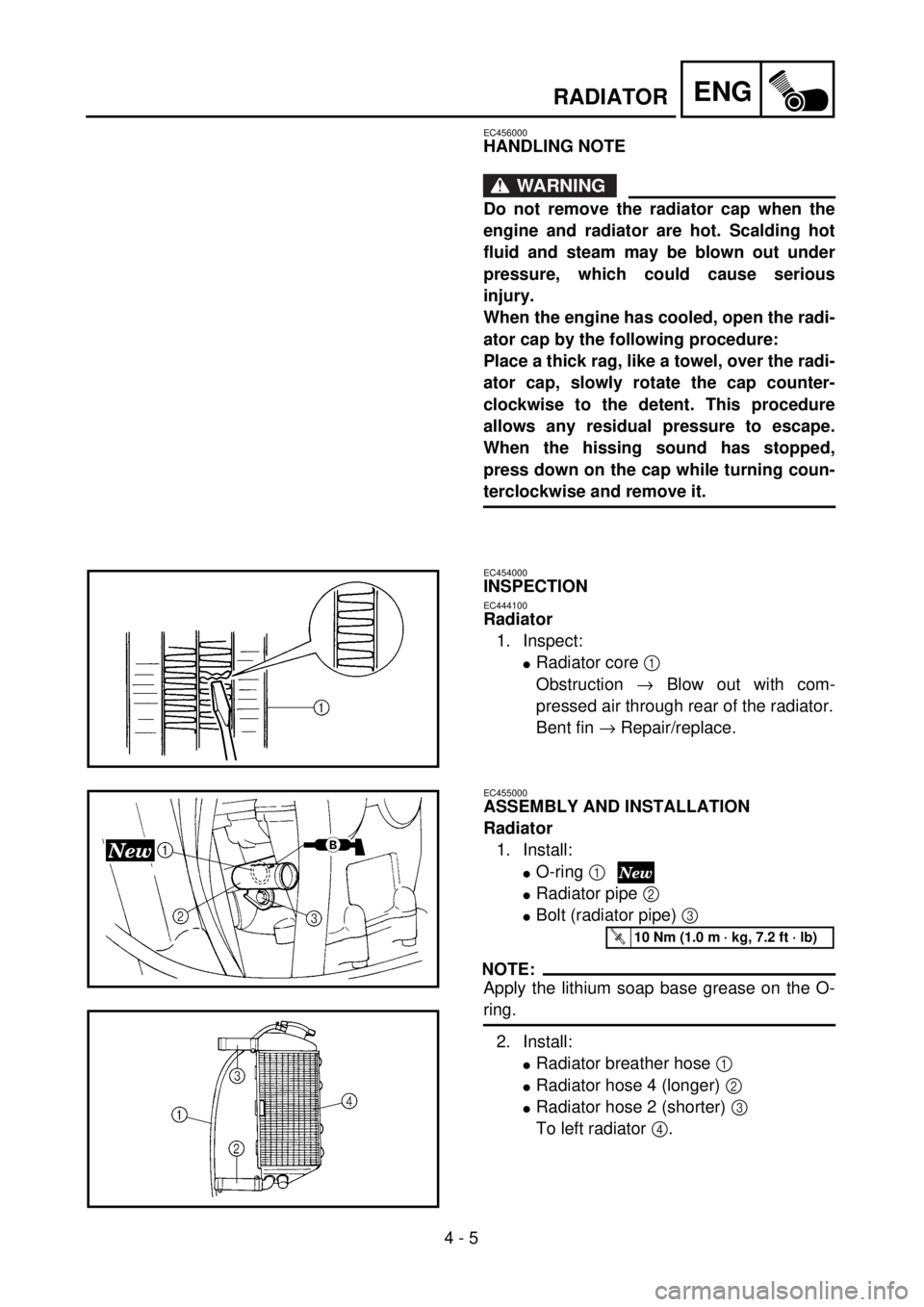
4 - 5
ENG
RADIATOR
EC456000
HANDLING NOTE
WARNING
Do not remove the radiator cap when the
engine and radiator are hot. Scalding hot
fluid and steam may be blown out under
pressure, which could cause serious
injury.
When the engine has cooled, open the radi-
ator cap by the following procedure:
Place a thick rag, like a towel, over the radi-
ator cap, slowly rotate the cap counter-
clockwise to the detent. This procedure
allows any residual pressure to escape.
When the hissing sound has stopped,
press down on the cap while turning coun-
terclockwise and remove it.
EC454000
INSPECTION
EC444100
Radiator
1. Inspect:
l
Radiator core
1
Obstruction
®
Blow out with com-
pressed air through rear of the radiator.
Bent fin
®
Repair/replace.
EC455000
ASSEMBLY AND INSTALLATION
Radiator
1. Install:
l
O-ring
1
l
Radiator pipe
2
l
Bolt (radiator pipe)
3
NOTE:
Apply the lithium soap base grease on the O-
ring.
2. Install:
l
Radiator breather hose
1
lRadiator hose 4 (longer) 2
lRadiator hose 2 (shorter) 3
To left radiator 4.
T R..10 Nm (1.0 m · kg, 7.2 ft · lb)
Page 296 of 656
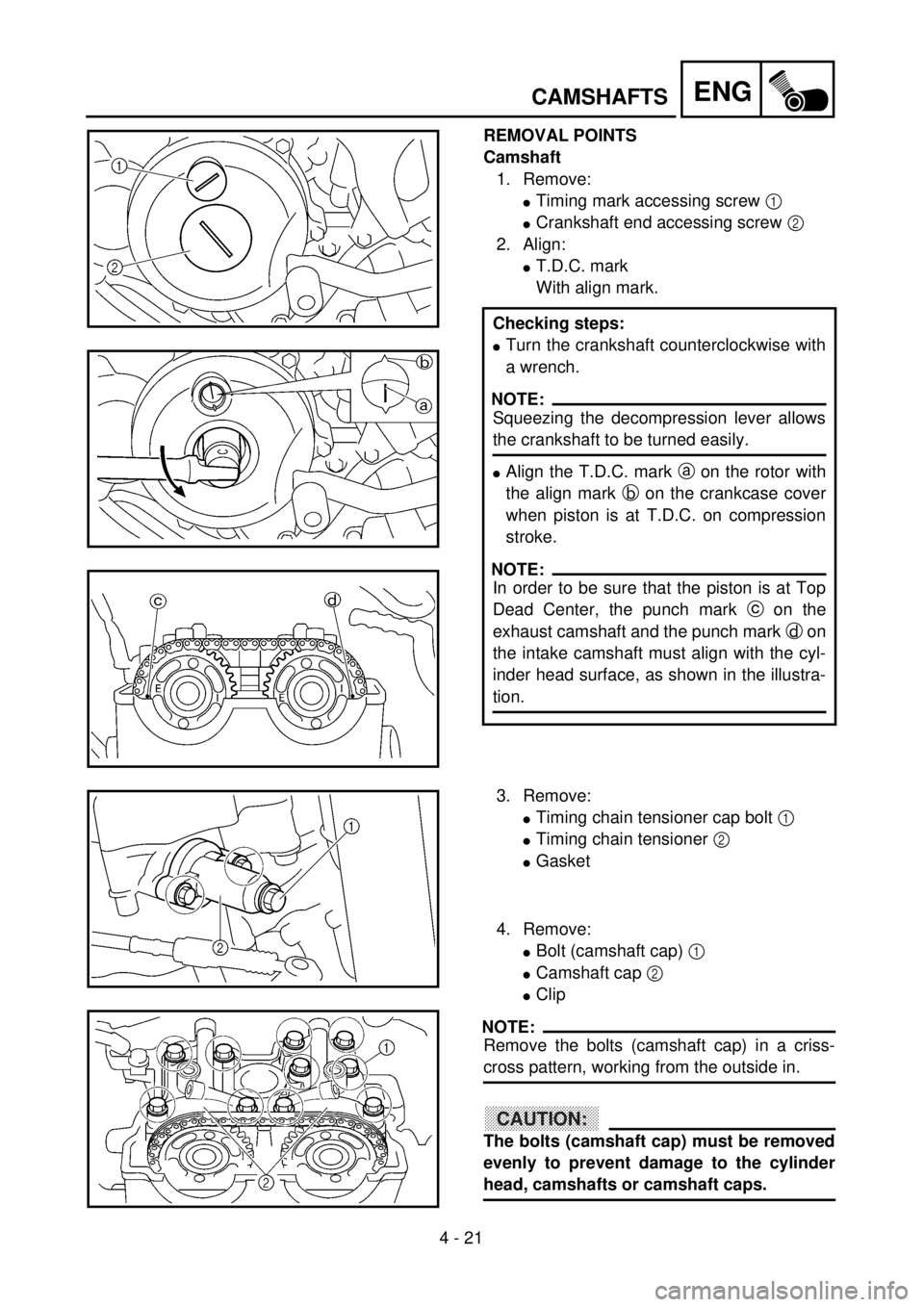
4 - 21
ENGCAMSHAFTS
REMOVAL POINTS
Camshaft
1. Remove:
lTiming mark accessing screw 1
lCrankshaft end accessing screw 2
2. Align:
lT.D.C. mark
With align mark.
Checking steps:
lTurn the crankshaft counterclockwise with
a wrench.
NOTE:
Squeezing the decompression lever allows
the crankshaft to be turned easily.
lAlign the T.D.C. mark a on the rotor with
the align mark b on the crankcase cover
when piston is at T.D.C. on compression
stroke.
NOTE:
In order to be sure that the piston is at Top
Dead Center, the punch mark c on the
exhaust camshaft and the punch mark d on
the intake camshaft must align with the cyl-
inder head surface, as shown in the illustra-
tion.
3. Remove:
lTiming chain tensioner cap bolt 1
lTiming chain tensioner 2
lGasket
4. Remove:
lBolt (camshaft cap) 1
lCamshaft cap 2
lClip
NOTE:
Remove the bolts (camshaft cap) in a criss-
cross pattern, working from the outside in.
CAUTION:
The bolts (camshaft cap) must be removed
evenly to prevent damage to the cylinder
head, camshafts or camshaft caps.
Page 302 of 656
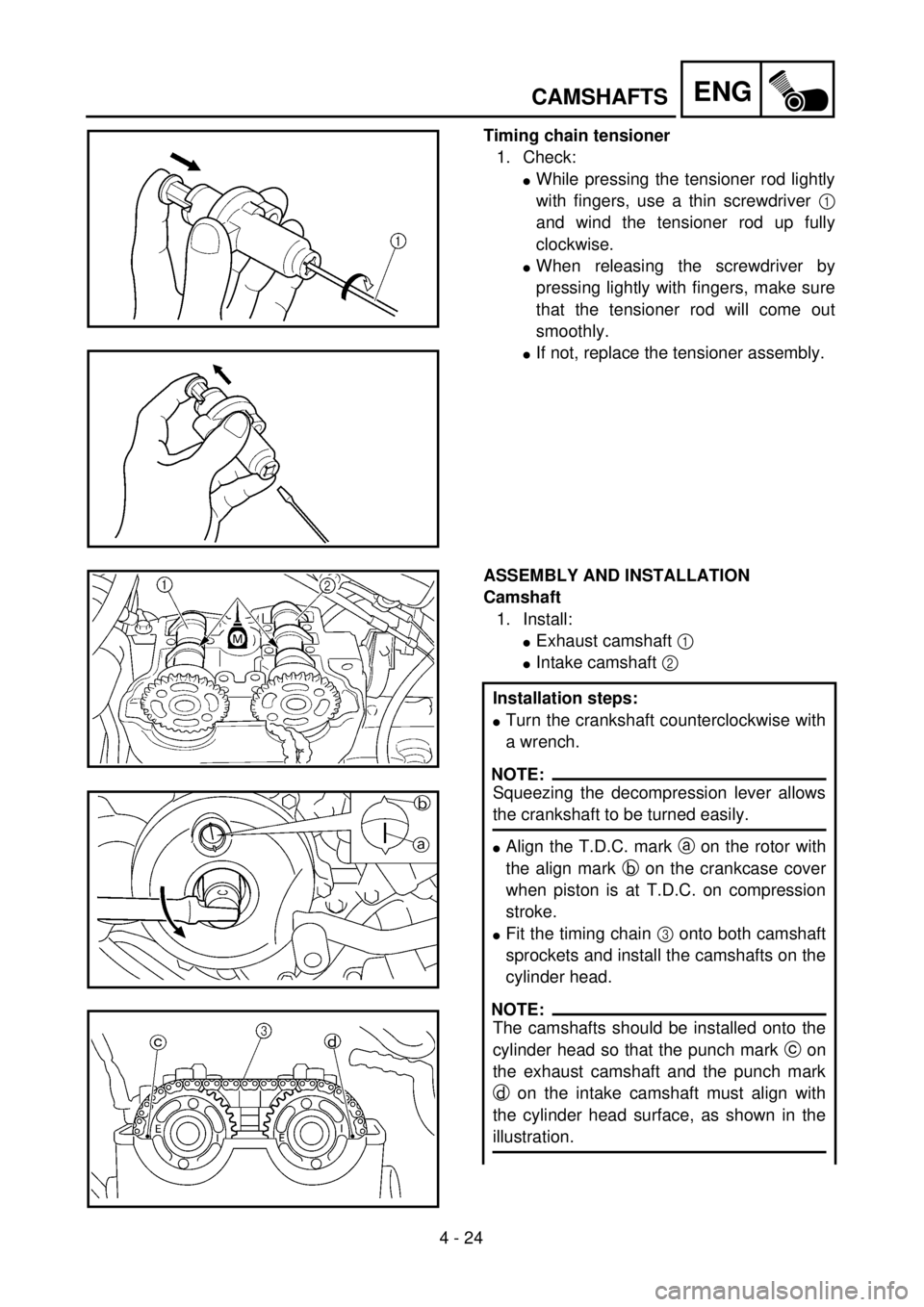
4 - 24
ENGCAMSHAFTS
Timing chain tensioner
1. Check:
lWhile pressing the tensioner rod lightly
with fingers, use a thin screwdriver 1
and wind the tensioner rod up fully
clockwise.
lWhen releasing the screwdriver by
pressing lightly with fingers, make sure
that the tensioner rod will come out
smoothly.
lIf not, replace the tensioner assembly.
ASSEMBLY AND INSTALLATION
Camshaft
1. Install:
lExhaust camshaft 1
lIntake camshaft 2
Installation steps:
lTurn the crankshaft counterclockwise with
a wrench.
NOTE:
Squeezing the decompression lever allows
the crankshaft to be turned easily.
lAlign the T.D.C. mark a on the rotor with
the align mark b on the crankcase cover
when piston is at T.D.C. on compression
stroke.
lFit the timing chain 3 onto both camshaft
sprockets and install the camshafts on the
cylinder head.
NOTE:
The camshafts should be installed onto the
cylinder head so that the punch mark c on
the exhaust camshaft and the punch mark
d on the intake camshaft must align with
the cylinder head surface, as shown in the
illustration.