Page 180 of 558
3-26
FRONT FORK INSPECTION
INSP
ADJ
3. Adjust:
9Drive chain slack
EC36C000
FRONT FORK INSPECTION
1. Inspect:
9Front fork smooth action
Operate the front brake and stroke the
front fork.
Unsmooth action/oil leakage ÕRepair or
replace.
Drive chain slack adjustment steps:
9Loosen the axle nut 1and locknuts 2.
9Adjust chain slack by turning the
adjusters 3.
To tighten ÕTurn adjuster 3 3
counter-
clockwise.
To loosen ÕTurn adjuster 3 3
clockwise
and push wheel forward.
9Turn each adjuster exactly the same amount
to maintain correct axle alignment. (There are
marks aon each side of chain puller align-
ment.)
NOTE:
Turn the adjuster so that the chain is in line
with the sprocket, as viewed from the rear.
cC
Too small chain slack will overload the
engine and other vital parts; keep the
slack within the specified limits.
9Tighten the axle nut while pushing down the
drive chain.
9Tighten the locknuts.
Axle nut:
125 Nm (12.5 m•kg, 90 ft•lb)
5MV-9-30-3B 6/19/00 1:49 PM Page 16
Page 188 of 558
3-30
REAR SHOCK ABSORBER SPRING PRELOAD
ADJUSTMENTINSP
ADJ
EC36M013
REAR SHOCK ABSORBER SPRING
PRELOAD ADJUSTMENT
1. Elevate the rear wheel by placing the suit-
able stand under the engine.
2. Remove:
9Rear frame
3. Loosen:
9Locknut 1
4. Adjust:
9Spring preload
By turning the adjuster 2.
NOTE:
9Be sure to remove all dirt and mud from around
the locknut and adjuster before
adjustment.
9The length of the spring (installed) changes 1.5
mm (0.06 in) per turn of the adjuster.
cC
Never attempt to turn the adjuster beyond
the maximum or minimum setting.
5. Tighten:
9Locknut
6. Install:
9Rear frame
Stiffer ÕIncrease the spring preload.
(Turn the adjuster 2 2
in.)
Softer ÕDecrease the spring pre-
load. (Turn the adjuster 2 2
out.)
Extent of adjustment
242~260 mm
(9.53~10.24 in)
*257~275 mm
(10.12~10.83 in)
Spring length (installed) a a
:
Standard length
248 mm (9.76 in)
*262 mm (10.31 in)
*For EUROPE
29 Nm (2.9 m•kg, 21 ft•lb)
5MV-9-30-3B 6/19/00 1:49 PM Page 24
Page 196 of 558
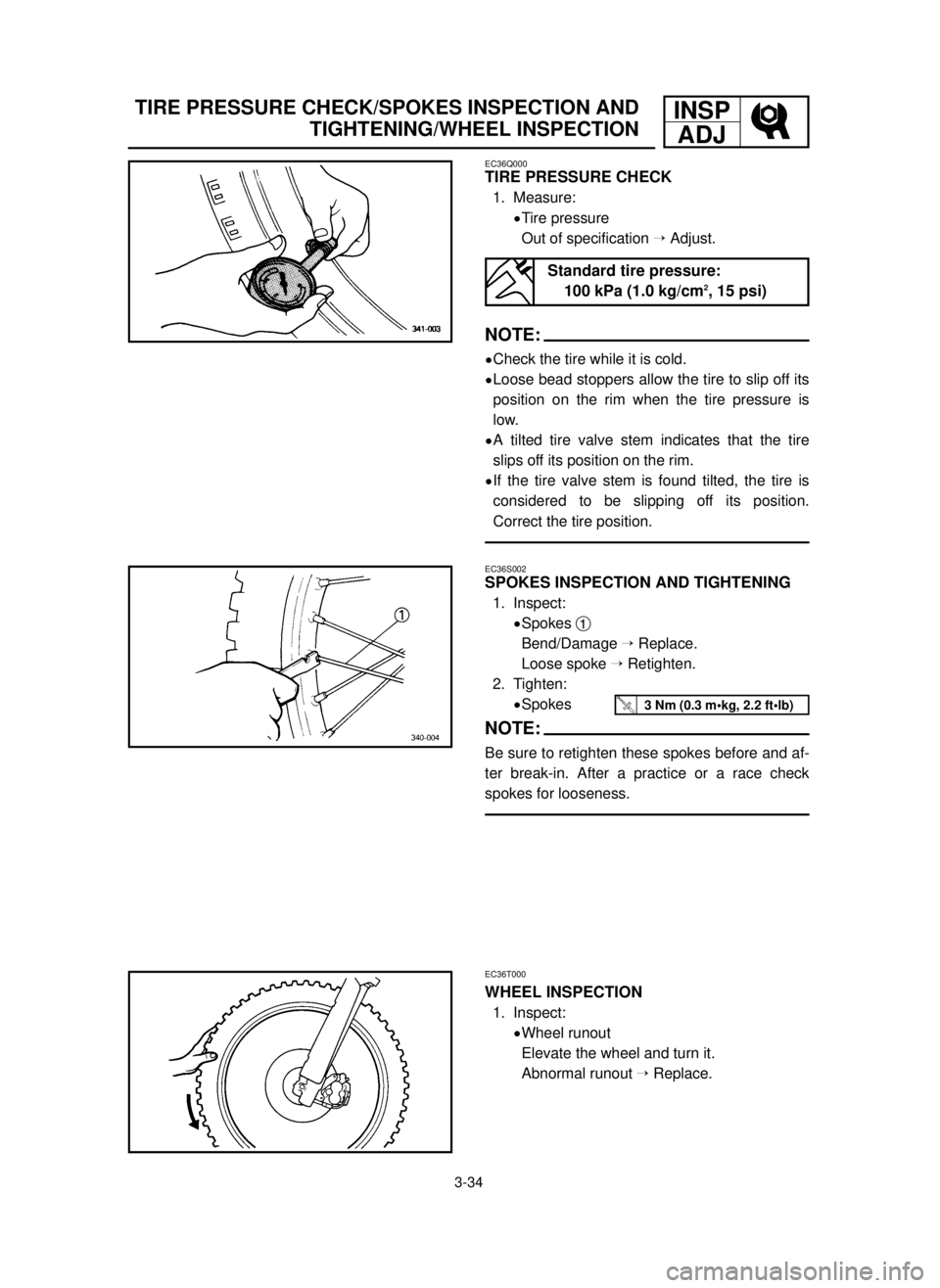
3-34
TIRE PRESSURE CHECK/SPOKES INSPECTION AND
TIGHTENING/WHEEL INSPECTIONINSP
ADJ
EC36Q000
TIRE PRESSURE CHECK
1. Measure:
9Tire pressure
Out of specification ÕAdjust.
NOTE:
9Check the tire while it is cold.
9Loose bead stoppers allow the tire to slip off its
position on the rim when the tire pressure is
low.
9A tilted tire valve stem indicates that the tire
slips off its position on the rim.
9If the tire valve stem is found tilted, the tire is
considered to be slipping off its position.
Correct the tire position.
EC36S002
SPOKES INSPECTION AND TIGHTENING
1. Inspect:
9Spokes 1
Bend/Damage ÕReplace.
Loose spoke ÕRetighten.
2. Tighten:
9Spokes
NOTE:
Be sure to retighten these spokes before and af-
ter break-in. After a practice or a race check
spokes for looseness.
EC36T000
WHEEL INSPECTION
1. Inspect:
9Wheel runout
Elevate the wheel and turn it.
Abnormal runout ÕReplace.
Standard tire pressure:
100 kPa (1.0 kg/cm
2, 15 psi)
3 Nm (0.3 m•kg, 2.2 ft•lb)
5MV-9-30-3B 6/19/00 1:49 PM Page 32
Page 198 of 558
3-35
STEERING HEAD INSPECTION AND ADJUSTMENT
INSP
ADJ
2. Inspect:
9Bearing free play
Exist play ÕReplace.
EC36U013
STEERING HEAD INSPECTION AND
ADJUSTMENT
1. Elevate the front wheel by placing a suitable
stand under the engine.
2. Check:
9Steering shaft
Grasp the bottom of the forks and gently
rock the fork assembly back and forth.
Free play ÕAdjust steering head.
3. Check:
9Steering smooth action
Turn the handlebar lock to lock.
Unsmooth action ÕAdjust steering ring
nut.
4. Adjust:
9Steering ring nut
Steering ring nut adjustment steps:
9Remove the number plate.
9Remove the handlebar and handle crown.
9Loosen the ring nut 1using the ring nut
wrench 2.
9Tighten the ring nut 3using ring nut wrench
4.
NOTE:
Set the torque wrench to the ring nut wrench
so that they form a right angle.
Ring nut wrench:
YU-33975/90890-01403
5MV-9-30-3B 6/19/00 1:49 PM Page 34
Page 316 of 558
4-54
ENGCDI MAGNETO
EC4L3000
REMOVAL POINTS
EC4L3102
Rotor
1. Remove:
9Nut (rotor) 1
9Plain washer 2
Use the rotor holding tool 3.
2. Remove:
9Rotor 1
Use the flywheel puller 2.
NOTE:
When installing the flywheel puller, turn it coun-
terclockwise.
EC4L4000
INSPECTION
EC4L4101
CDI magneto
1. Inspect:
9Rotor inner surface a
9Stator outer surface b
Damage ÕInspect the crankshaft runout
and crankshaft bearing.
If necessary, replace CDI magneto and/or
stator.
EC4L4200
Woodruff key
1. Inspect:
9Woodruff key 1
Damage ÕReplace.
EC4L5000
ASSEMBLY AND INSTALLATION
EC4L5172
CDI magneto
1. Install:
9Stator 1
9Screw (stator) 2
NOTE:
Temporarily tighten the screw (stator) at this
point.
Rotor holding tool:
YU-1235/90890-01235
Flywheel puller:
YM-1189/90890-01189
5MV-9-30-4C 6/19/00 1:42 PM Page 34
Page 352 of 558
4-72
ENGTRANSMISSION, SHIFT CAM AND SHIFT FORK
2. Install:
92nd wheel gear (28T) 1
96th wheel gear (24T) 2
94th wheel gear (27T) 3
93rd wheel gear (26T) 4
95th wheel gear (26T) 5
91st wheel gear (30T) 6
To drive axle 7.
NOTE:
9Apply the molybdenum disulfide oil on the 1st,
2nd, 3rd and 4th wheel gears inner circumfer-
ence.
9Apply the transmission oil on the 5th and 6th
wheel gears inner circumference.
3. Install:
9Plain washer 1
9Circlip 2
NOTE:
9Be sure the circlip sharp-edged corner ais po-
sitioned opposite side to the plain washer and
gear b.
9Be sure the circlip end cis positioned at axle
spline groove d.
4. Install:
9Main axle 1
9Drive axle 2
NOTE:
9Apply the lithium soap base grease on the
crankcase oil seal lip.
9When installing the drive axle into the
crankcase, pay careful attention to the
crankcase oil seal lip.
5MV-9-30-4D 6/19/00 1:39 PM Page 32
Page 354 of 558
4-73
ENGTRANSMISSION, SHIFT CAM AND SHIFT FORK
EC4H5331
Shift cam and shift fork
1. Install:
9Shift fork 1 (L) 1
9Shift fork 2 2
9Shift fork 3 (R) 3
NOTE:
9Mesh the shift fork #1 (L) with the 6th wheel
gear 4and #3 (R) with the 5th wheel gear 6
on the drive axle.
9Mesh the shift fork #2 with the 3rd/4th pinion
gear 5on the main axle.
2. Install:
9Shift cam 1
NOTE:
Apply the transmission oil on the shift cam.
3. Install:
9Guide bar (short) 1
9Guide bar (long) 2
NOTE:
9Apply the transmission oil on the guide bars.
9Be sure the long bar is inserted into the shift
forks #1 and #3 and the short one into #2.
4. Check:
9Shifter operation
9Transmission operation
Unsmooth operation ÕRepair.
5MV-9-30-4D 6/19/00 1:39 PM Page 34
Page 356 of 558
5-1
CHASFRONT WHEEL AND REAR WHEEL
Extent of removal Order Part name Q’ty Remarks
FRONT WHEEL REMOVAL
Preparation for
Hold the machine by placing the
removalsuitable stand under the engine.
1 Hose cover 1
2 Bolt (brake hose holder) 2 Only loosening.
3 Bolt (axle holder) 4 Only loosening.
4 Nut (front wheel axle) 1
5 Front wheel axle 1
6 Front wheel 1
7 Collar 2
8 Oil seal 2
9 Bearing 2 Refer to “REMOVAL POINTS”.
10 Brake disk 1
EC500000
CHASSISEC590000
FRONT WHEEL AND REAR WHEELEC598000
FRONT WHEEL
2
13
3
Extent of removal:1Front wheel removal2Wheel bearing removal3Break disc removal
w
Support the machine securely so there is no dan-
ger of it falling over.
5
23 Nm (2.3 m•kg, 17 ft•lb)
23 Nm (2.3 m•kg, 17 ft•lb)
10 Nm (1.0 m•kg, 7.2 ft•lb)
105 Nm (10.5 m•kg, 75 ft•lb)
16 Nm (1.6 m•kg, 11 ft•lb)
7 Nm (0.7 m•kg, 5.1 ft•lb)
12 Nm (1.2 m•kg, 8.7 ft•lb)
5MV-9-30-5A 6/19/00 1:35 PM Page 2