Page 299 of 557
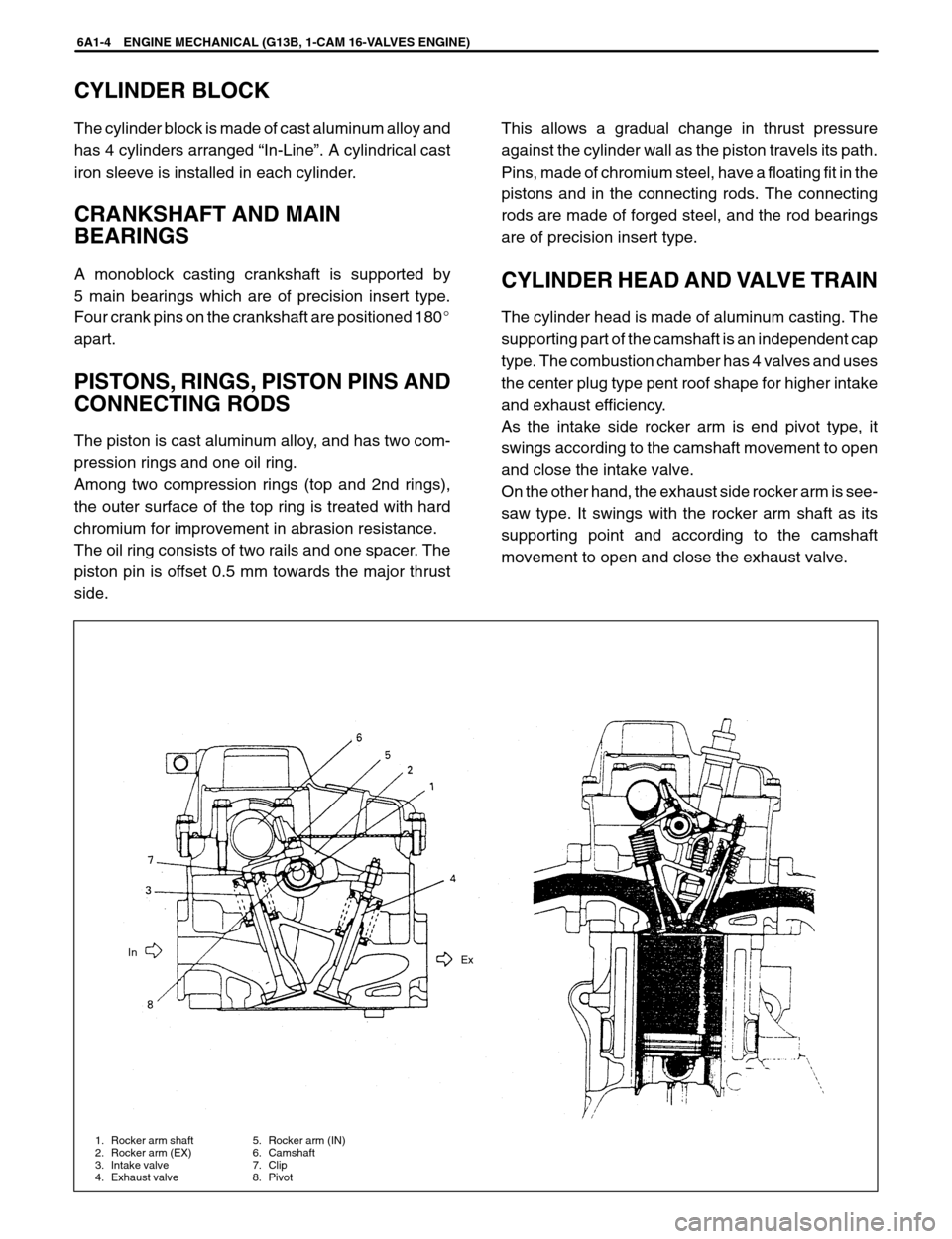
1. Rocker arm shaft
2. Rocker arm (EX)
3. Intake valve
4. Exhaust valve5. Rocker arm (IN)
6. Camshaft
7. Clip
8. PivotEx In
CYLINDER BLOCK
The cylinder block is made of cast aluminum alloy and
has 4 cylinders arranged “In-Line”. A cylindrical cast
iron sleeve is installed in each cylinder.
CRANKSHAFT AND MAIN
BEARINGS
A monoblock casting crankshaft is supported by
5 main bearings which are of precision insert type.
Four crank pins on the crankshaft are positioned 180
apart.
PISTONS, RINGS, PISTON PINS AND
CONNECTING RODS
The piston is cast aluminum alloy, and has two com-
pression rings and one oil ring.
Among two compression rings (top and 2nd rings),
the outer surface of the top ring is treated with hard
chromium for improvement in abrasion resistance.
The oil ring consists of two rails and one spacer. The
piston pin is offset 0.5 mm towards the major thrust
side.This allows a gradual change in thrust pressure
against the cylinder wall as the piston travels its path.
Pins, made of chromium steel, have a floating fit in the
pistons and in the connecting rods. The connecting
rods are made of forged steel, and the rod bearings
are of precision insert type.
CYLINDER HEAD AND VALVE TRAIN
The cylinder head is made of aluminum casting. The
supporting part of the camshaft is an independent cap
type. The combustion chamber has 4 valves and uses
the center plug type pent roof shape for higher intake
and exhaust efficiency.
As the intake side rocker arm is end pivot type, it
swings according to the camshaft movement to open
and close the intake valve.
On the other hand, the exhaust side rocker arm is see-
saw type. It swings with the rocker arm shaft as its
supporting point and according to the camshaft
movement to open and close the exhaust valve.
6A1-4 ENGINE MECHANICAL (G13B, 1-CAM 16-VALVES ENGINE)
Page 300 of 557
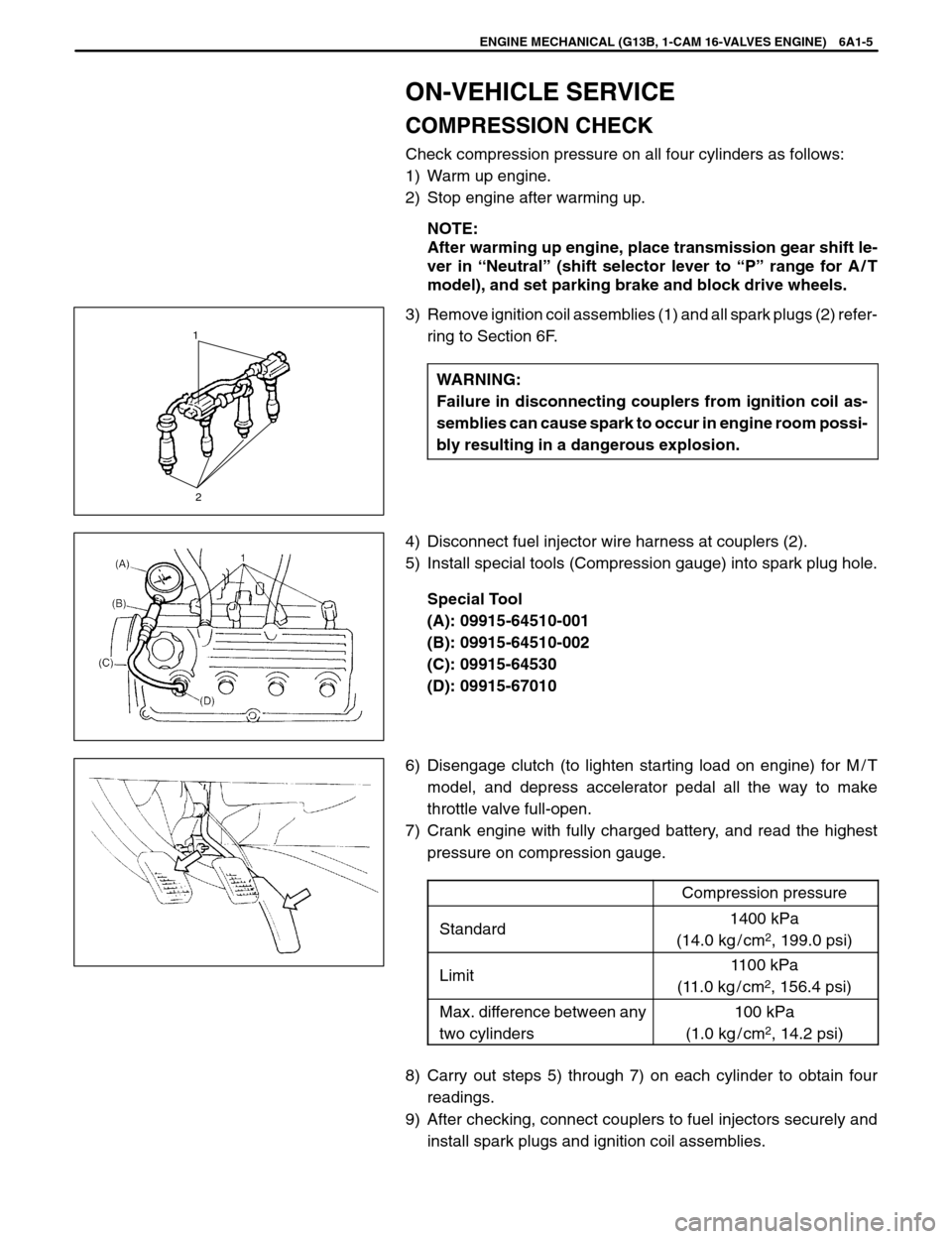
1
2
ENGINE MECHANICAL (G13B, 1-CAM 16-VALVES ENGINE) 6A1-5
ON-VEHICLE SERVICE
COMPRESSION CHECK
Check compression pressure on all four cylinders as follows:
1) Warm up engine.
2) Stop engine after warming up.
NOTE:
After warming up engine, place transmission gear shift le-
ver in “Neutral” (shift selector lever to “P” range for A / T
model), and set parking brake and block drive wheels.
3) Remove ignition coil assemblies (1) and all spark plugs (2) refer-
ring to Section 6F.
WARNING:
Failure in disconnecting couplers from ignition coil as-
semblies can cause spark to occur in engine room possi-
bly resulting in a dangerous explosion.
4) Disconnect fuel injector wire harness at couplers (2).
5) Install special tools (Compression gauge) into spark plug hole.
Special Tool
(A): 09915-64510-001
(B): 09915-64510-002
(C): 09915-64530
(D): 09915-67010
6) Disengage clutch (to lighten starting load on engine) for M / T
model, and depress accelerator pedal all the way to make
throttle valve full-open.
7) Crank engine with fully charged battery, and read the highest
pressure on compression gauge.
Compression pressure
Standard1400 kPa
(14.0 kg / cm
2, 199.0 psi)
Limit1100 kPa
(11.0 kg / cm
2, 156.4 psi)
Max. difference between any
two cylinders100 kPa
(1.0 kg / cm
2, 14.2 psi)
8) Carry out steps 5) through 7) on each cylinder to obtain four
readings.
9) After checking, connect couplers to fuel injectors securely and
install spark plugs and ignition coil assemblies.
Page 302 of 557
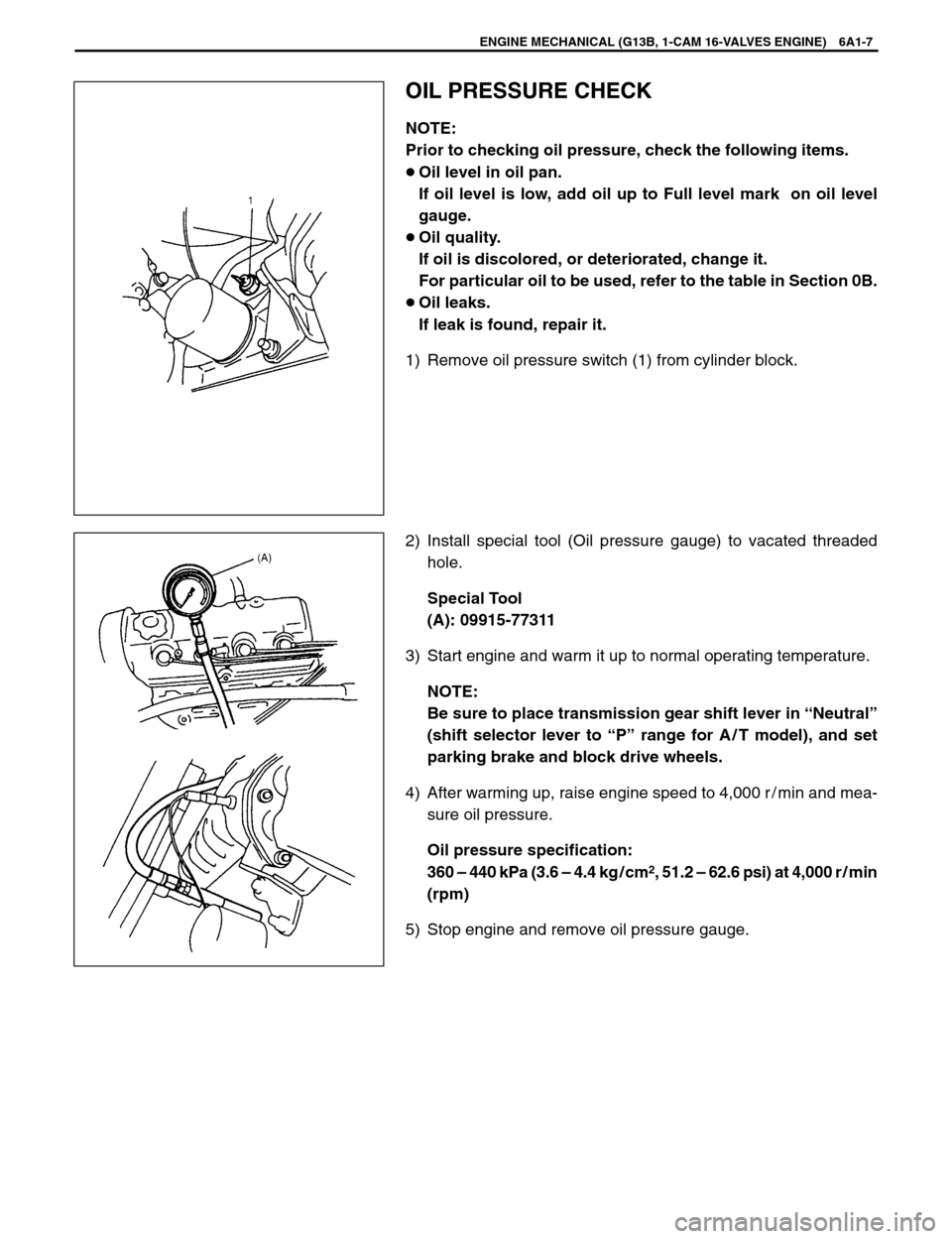
ENGINE MECHANICAL (G13B, 1-CAM 16-VALVES ENGINE) 6A1-7
OIL PRESSURE CHECK
NOTE:
Prior to checking oil pressure, check the following items.
Oil level in oil pan.
If oil level is low, add oil up to Full level mark on oil level
gauge.
Oil quality.
If oil is discolored, or deteriorated, change it.
For particular oil to be used, refer to the table in Section 0B.
Oil leaks.
If leak is found, repair it.
1) Remove oil pressure switch (1) from cylinder block.
2) Install special tool (Oil pressure gauge) to vacated threaded
hole.
Special Tool
(A): 09915-77311
3) Start engine and warm it up to normal operating temperature.
NOTE:
Be sure to place transmission gear shift lever in “Neutral”
(shift selector lever to “P” range for A / T model), and set
parking brake and block drive wheels.
4) After warming up, raise engine speed to 4,000 r / min and mea-
sure oil pressure.
Oil pressure specification:
360 – 440 kPa (3.6 – 4.4 kg / cm
2, 51.2 – 62.6 psi) at 4,000 r / min
(rpm)
5) Stop engine and remove oil pressure gauge.
Page 360 of 557
ENGINE MECHANICAL (G13B, 1-CAM 16-VALVES ENGINE) 6A1-65
12) Disconnect the following electric wires:
Ignition coil assembly
Ground wires from intake manifold
Engine oil pressure switch
EVAP canister purge valve (if equipped)
Engine coolant temp. sensor
Fuel injectors
Power steering pressure switch (if equipped)
Oxygen sensor-1
Back-up light switch (M / T)
Transmission range switch (A / T)
A/T vehicle speed sensor (A / T)
Solenoid coupler (A / T)
Generator
Starter
Battery negative cable from transmission
TP sensor
IAC valve
CMP sensor
MAP sensor
and then release wire harnesses from clamps.
13) Disconnect the following hoses:
Canister purge hose (2) from EVAP canister purge valve
Brake booster hose (1) from intake manifold
Radiator outlet hose from inlet pipe
Heater inlet and outlet hose from heater unit
14) Disconnect fuel feed (2) and return hoses (3) from fuel delivery
pipe (1).
Page 398 of 557
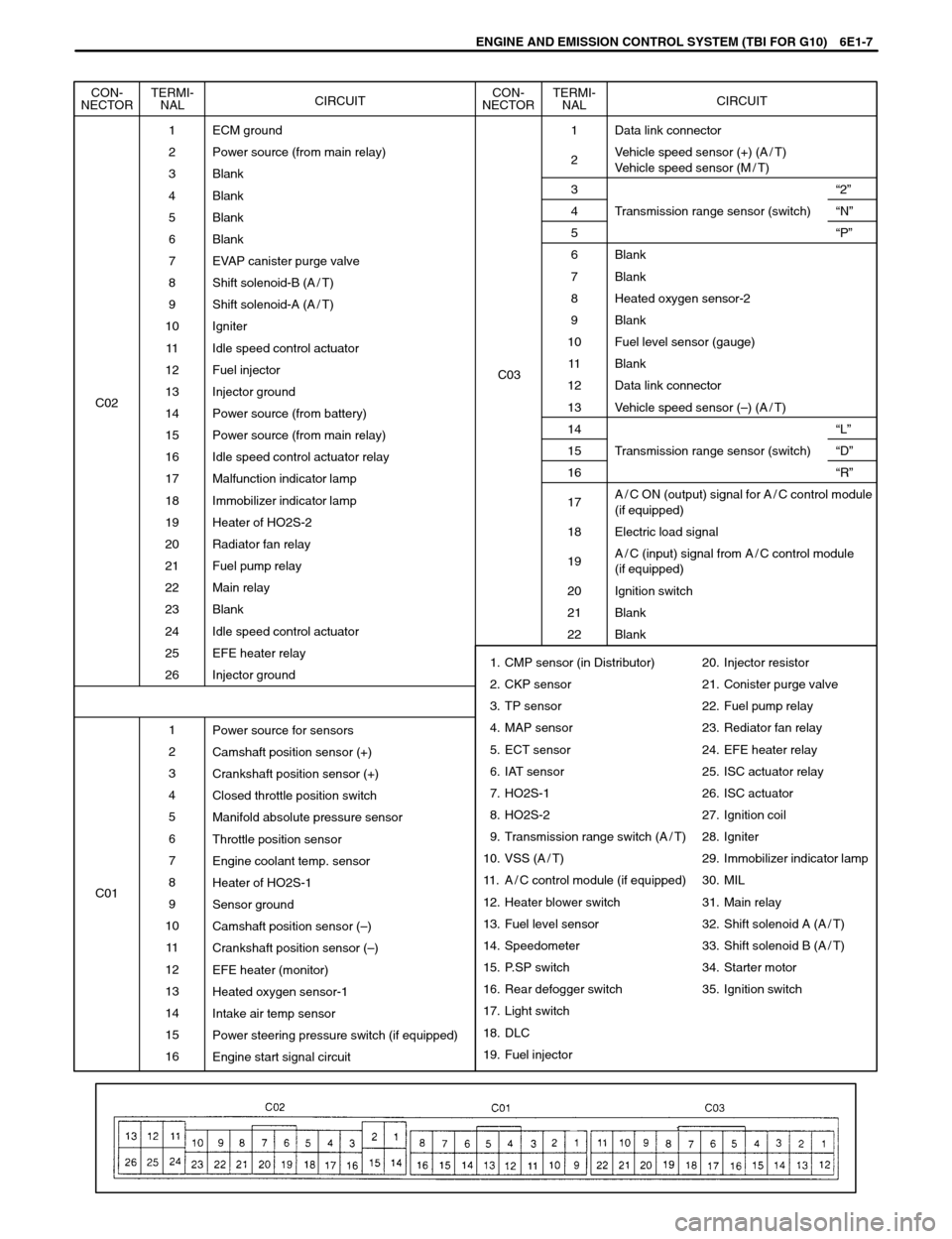
ENGINE AND EMISSION CONTROL SYSTEM (TBI FOR G10) 6E1-7
CON-
NECTOR
C02TERMI-
NAL
1
2
3
4
5
6
7
8
9
10
11
12
13
14
15
16
17
18
19
20
21
22
23
24
25
26ECM ground
Power source (from main relay)
Blank
Blank
Blank
Blank
EVAP canister purge valve
Shift solenoid-B (A / T)
Shift solenoid-A (A / T)
Igniter
Idle speed control actuator
Fuel injector
Injector ground
Power source (from battery)
Power source (from main relay)
Idle speed control actuator relay
Malfunction indicator lamp
Immobilizer indicator lamp
Heater of HO2S-2
Radiator fan relay
Fuel pump relay
Main relay
Blank
Idle speed control actuator
EFE heater relay
Injector groundC031
2
3
4
5
6
7
8
9
10
11
12
13
14
15
16
17
18
19
20
21
22Data link connector
Vehicle speed sensor (+) (A / T)
Vehicle speed sensor (M / T)
Transmission range sensor (switch)“2”
Transmission range sensor (switch)“N”
Transmission range sensor (switch)“P”
Blank
Blank
Heated oxygen sensor-2
Blank
Fuel level sensor (gauge)
Blank
Data link connector
Vehicle speed sensor (–) (A / T)
Transmission range sensor (switch)“L”
Transmission range sensor (switch)“D”
Transmission range sensor (switch)“R”
A / C ON (output) signal for A / C control module
(if equipped)
Electric load signal
A / C (input) signal from A / C control module
(if equipped)
Ignition switch
Blank
Blank CIRCUITCON-
NECTORTERMI-
NALCIRCUIT
1
2
3
4
5
6
7
8
9
10
11
12
13
14
15
16Power source for sensors
Camshaft position sensor (+)
Crankshaft position sensor (+)
Closed throttle position switch
Manifold absolute pressure sensor
Throttle position sensor
Engine coolant temp. sensor
Heater of HO2S-1
Sensor ground
Camshaft position sensor (–)
Crankshaft position sensor (–)
EFE heater (monitor)
Heated oxygen sensor-1
Intake air temp sensor
Power steering pressure switch (if equipped)
Engine start signal circuit
C01
1. CMP sensor (in Distributor)
2. CKP sensor
3. TP sensor
4. MAP sensor
5. ECT sensor
6. IAT sensor
7. HO2S-1
8. HO2S-2
9. Transmission range switch (A / T)
10. VSS (A / T)
11. A / C control module (if equipped)
12. Heater blower switch
13. Fuel level sensor
14. Speedometer
15. P.SP switch
16. Rear defogger switch
17. Light switch
18. DLC
19. Fuel injector20. Injector resistor
21. Conister purge valve
22. Fuel pump relay
23. Rediator fan relay
24. EFE heater relay
25. ISC actuator relay
26. ISC actuator
27. Ignition coil
28. Igniter
29. Immobilizer indicator lamp
30. MIL
31. Main relay
32. Shift solenoid A (A / T)
33. Shift solenoid B (A / T)
34. Starter motor
35. Ignition switch
Page 407 of 557
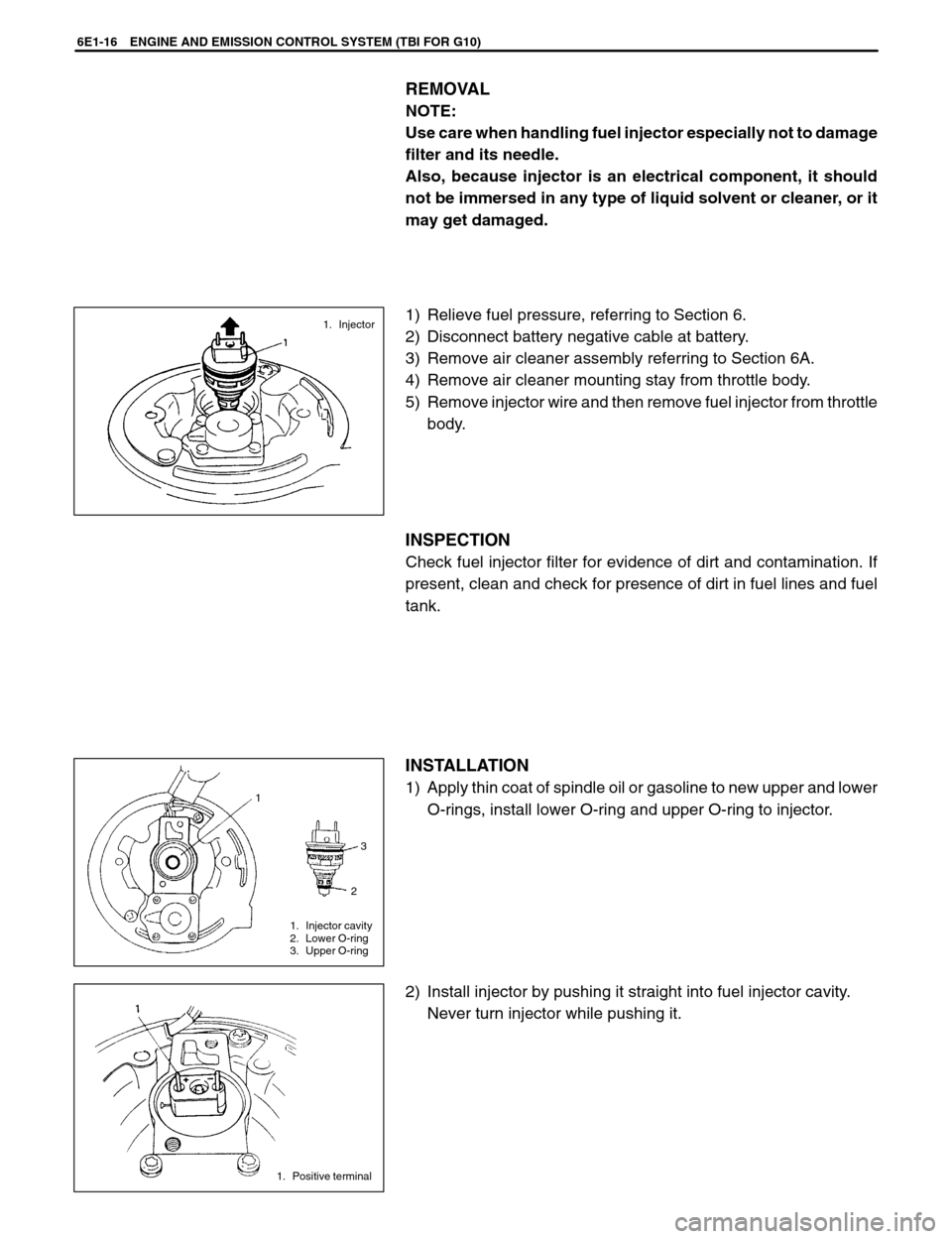
6E1-16 ENGINE AND EMISSION CONTROL SYSTEM (TBI FOR G10)
1. Injector
1
3
2
1. Injector cavity
2. Lower O-ring
3. Upper O-ring
1. Positive terminal
REMOVAL
NOTE:
Use care when handling fuel injector especially not to damage
filter and its needle.
Also, because injector is an electrical component, it should
not be immersed in any type of liquid solvent or cleaner, or it
may get damaged.
1) Relieve fuel pressure, referring to Section 6.
2) Disconnect battery negative cable at battery.
3) Remove air cleaner assembly referring to Section 6A.
4) Remove air cleaner mounting stay from throttle body.
5) Remove injector wire and then remove fuel injector from throttle
body.
INSPECTION
Check fuel injector filter for evidence of dirt and contamination. If
present, clean and check for presence of dirt in fuel lines and fuel
tank.
INSTALLATION
1) Apply thin coat of spindle oil or gasoline to new upper and lower
O-rings, install lower O-ring and upper O-ring to injector.
2) Install injector by pushing it straight into fuel injector cavity.
Never turn injector while pushing it.
Page 418 of 557
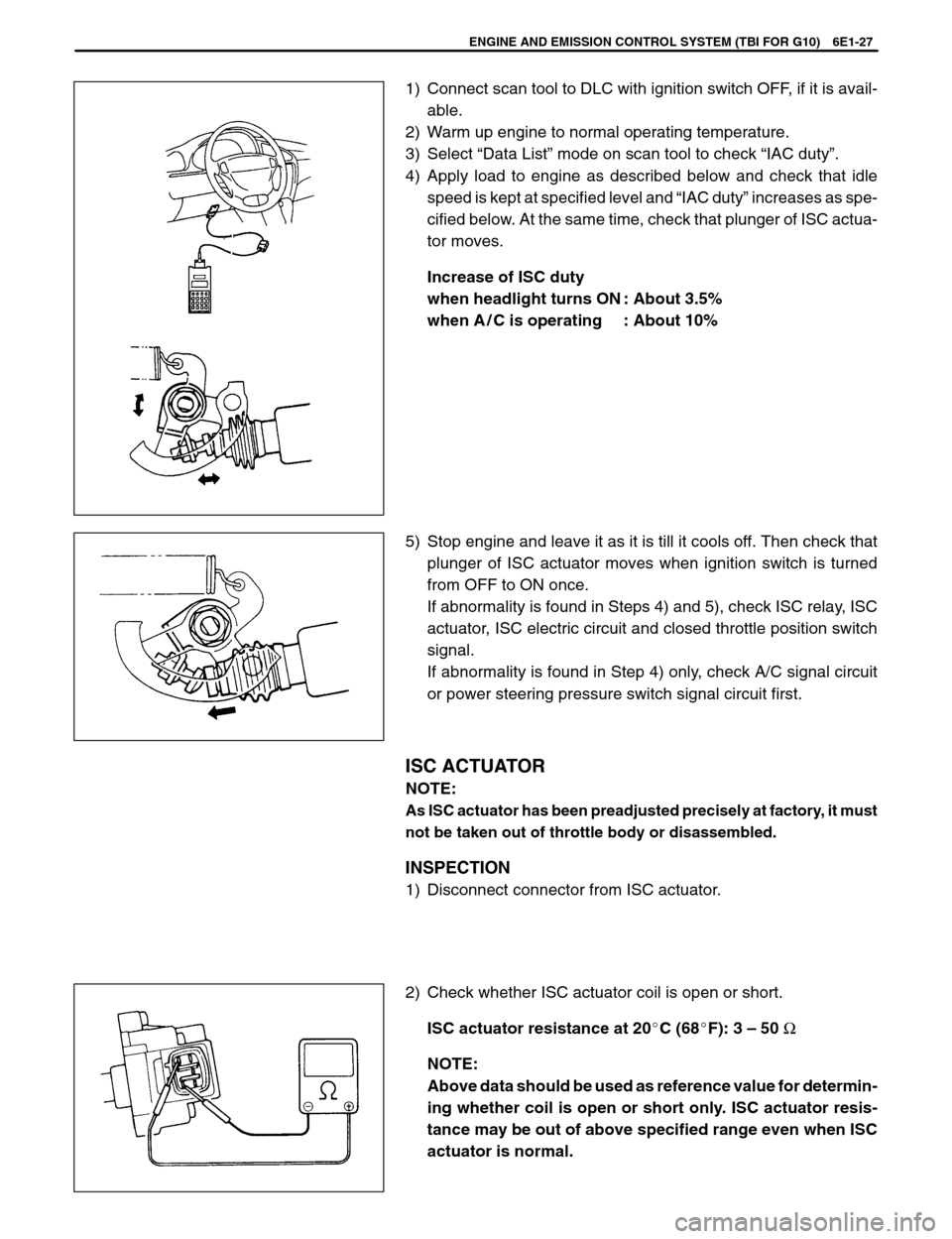
ENGINE AND EMISSION CONTROL SYSTEM (TBI FOR G10) 6E1-27
1) Connect scan tool to DLC with ignition switch OFF, if it is avail-
able.
2) Warm up engine to normal operating temperature.
3) Select “Data List” mode on scan tool to check “IAC duty”.
4) Apply load to engine as described below and check that idle
speed is kept at specified level and “IAC duty” increases as spe-
cified below. At the same time, check that plunger of ISC actua-
tor moves.
Increase of ISC duty
when headlight turns ON : About 3.5%
when A / C is operating : About 10%
5) Stop engine and leave it as it is till it cools off. Then check that
plunger of ISC actuator moves when ignition switch is turned
from OFF to ON once.
If abnormality is found in Steps 4) and 5), check ISC relay, ISC
actuator, ISC electric circuit and closed throttle position switch
signal.
If abnormality is found in Step 4) only, check A/C signal circuit
or power steering pressure switch signal circuit first.
ISC ACTUATOR
NOTE:
As ISC actuator has been preadjusted precisely at factory, it must
not be taken out of throttle body or disassembled.
INSPECTION
1) Disconnect connector from ISC actuator.
2) Check whether ISC actuator coil is open or short.
ISC actuator resistance at 20C (68F): 3 – 50 Ω
NOTE:
Above data should be used as reference value for determin-
ing whether coil is open or short only. ISC actuator resis-
tance may be out of above specified range even when ISC
actuator is normal.
Page 437 of 557
ENGINE AND EMISSION CONTROL SYSTEM (SFI FOR G13) 6E2-9
FUEL PUMP RELAY
FUEL INJECTOR
HO2S HEATER
IAC VALVE
IGNITION COIL WITH IGNITER
EGR VALVE
EVAP CANISTER PURGE VALVE
A/C CONTROL MODULE
RADIATOR FAN RELAY
MIL
MAIN RELAY
SIGNAL FROM SENSOR, SWITCH AND CONTROL MODULE
OUTPUT
INPUT
ENGINE & EMISSION CONTROL INPUT / OUTPUT TABLE
ELECTRIC CONTROL DEVICE
FUEL LEVEL SENSORFor detecting fuel level
BAROMETRIC PRESSURE SENSOR
START SWITCH
IGNITION SWITCH
LIGHTING SWITCH
REAR DEFOGGER SWITCH (IF EQUIPPED)
BLOWER SWITCH
A / C SWITCH
VSS
HEATED OXYGEN SENSOR-1
HEATED OXYGEN SENSOR-2For detecting deterioration of
three way catalytic convertor
IAT SENSOR
ECT SENSOR
TP SENSOR
MAP SENSOR
CMP SENSOR
CKP SENSOR