Page 2 of 118
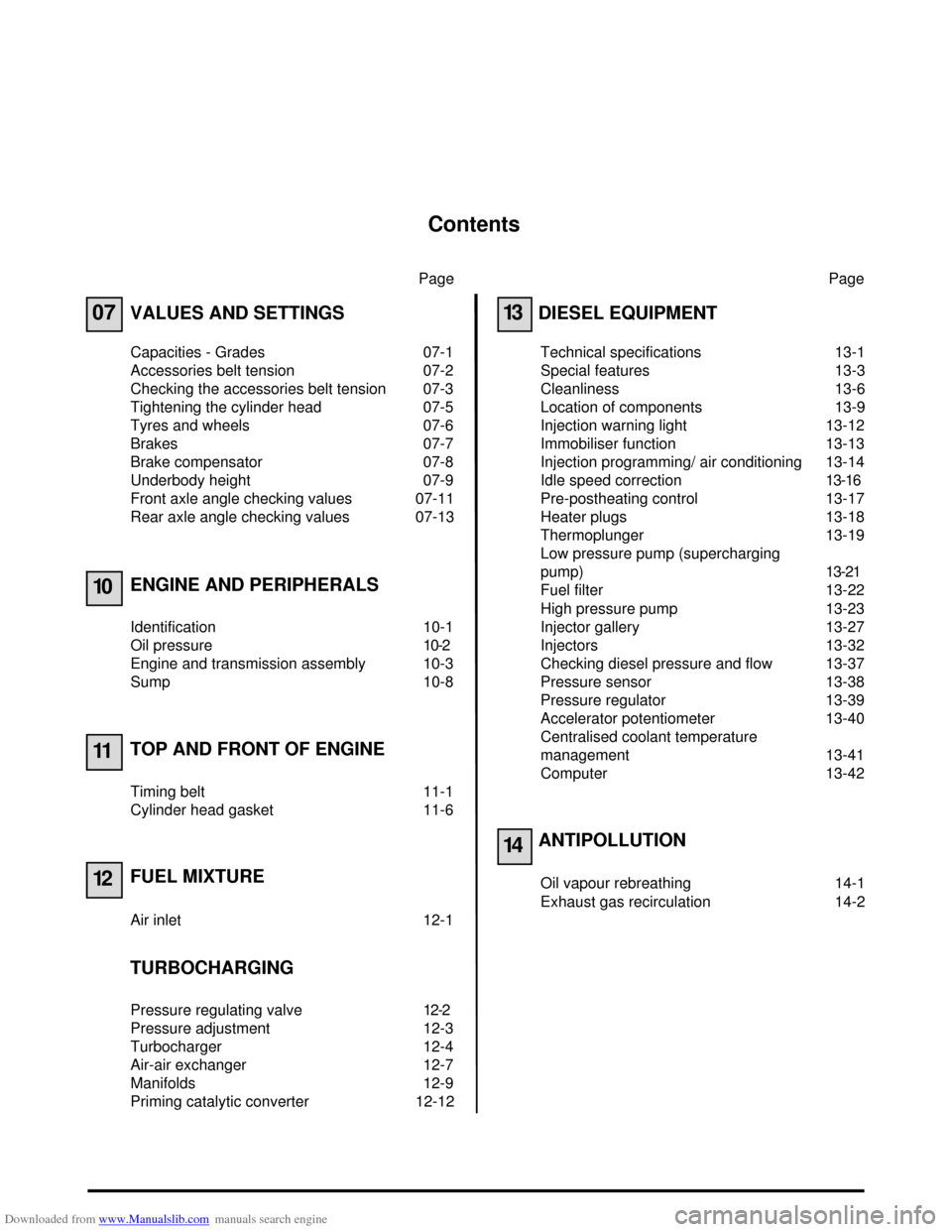
Downloaded from www.Manualslib.com manuals search engine Contents
Page
07
10
11
12
VALUES AND SETTINGS
Capacities - Grades 07-1
Accessories belt tension 07-2
Checking the accessories belt tension 07-3
Tightening the cylinder head 07-5
Tyres and wheels 07-6
Brakes 07-7
Brake compensator 07-8
Underbody height 07-9
Front axle angle checking values 07-11
Rear axle angle checking values 07-13
ENGINE AND PERIPHERALS
Identification 10-1
Oil pressure 10-2
Engine and transmission assembly 10-3
Sump 10-8
TOP AND FRONT OF ENGINE
Timing belt 11-1
Cylinder head gasket 11-6
FUEL MIXTURE
Air inlet 12-1
TURBOCHARGING
Pressure regulating valve 12-2
Pressure adjustment 12-3
Turbocharger 12-4
Air-air exchanger 12-7
Manifolds 12-9
Priming catalytic converter 12-12Page
13
14
DIESEL EQUIPMENT
Technical specifications 13-1
Special features 13-3
Cleanliness 13-6
Location of components 13-9
Injection warning light 13-12
Immobiliser function 13-13
Injection programming/ air conditioning 13-14
Idle speed correction13-16
Pre-postheating control 13-17
Heater plugs 13-18
Thermoplunger 13-19
Low pressure pump (supercharging
pump)13-21
Fuel filter 13-22
High pressure pump 13-23
Injector gallery 13-27
Injectors 13-32
Checking diesel pressure and flow 13-37
Pressure sensor 13-38
Pressure regulator 13-39
Accelerator potentiometer 13-40
Centralised coolant temperature
management 13-41
Computer 13-42
ANTIPOLLUTION
Oil vapour rebreathing 14-1
Exhaust gas recirculation 14-2
Page 21 of 118
Downloaded from www.Manualslib.com manuals search engine ENGINE AND PERIPHERALS
Engine and transmission assembly
10
10-5
– the closure panel for the plenum chamber.
Remove (all types):
– the shock absorber cap protectors,
– the clutch cable,
– the brake servo vacuum pipe,
– the air intake pipe,
– the turbocharging air ducts between the exchanger
and the engine,
– the hoses on the heater radiator,
– the pipes (6) and the connectors (7),– the battery mounting,
– the expansion bottle mountings and the expansion
bottle,
– the precatalytic converter mountings and the
precatalytic converter,
– the relay plate at (1) and the fuse holder (2) as well
as the connectors (3) and (4),
– the injection computer connectors (8),
– the earth strap (9),
– the fuel pipes (10) and fit cleanliness plugs.
11036R2
16869R
16872R
16870R
Page 34 of 118
Downloaded from www.Manualslib.com manuals search engine TOP AND FRONT OF ENGINE
Cylinder head gasket
11
11 - 8
Remove:
– the air filter assembly and the air inlet pipe,
– the air ducts (A) and (B),
– the injector connectors and the heater plugs,
– the connectors (1) and (2),
– the oil rebreather pipe (3),
16871R
Page 52 of 118
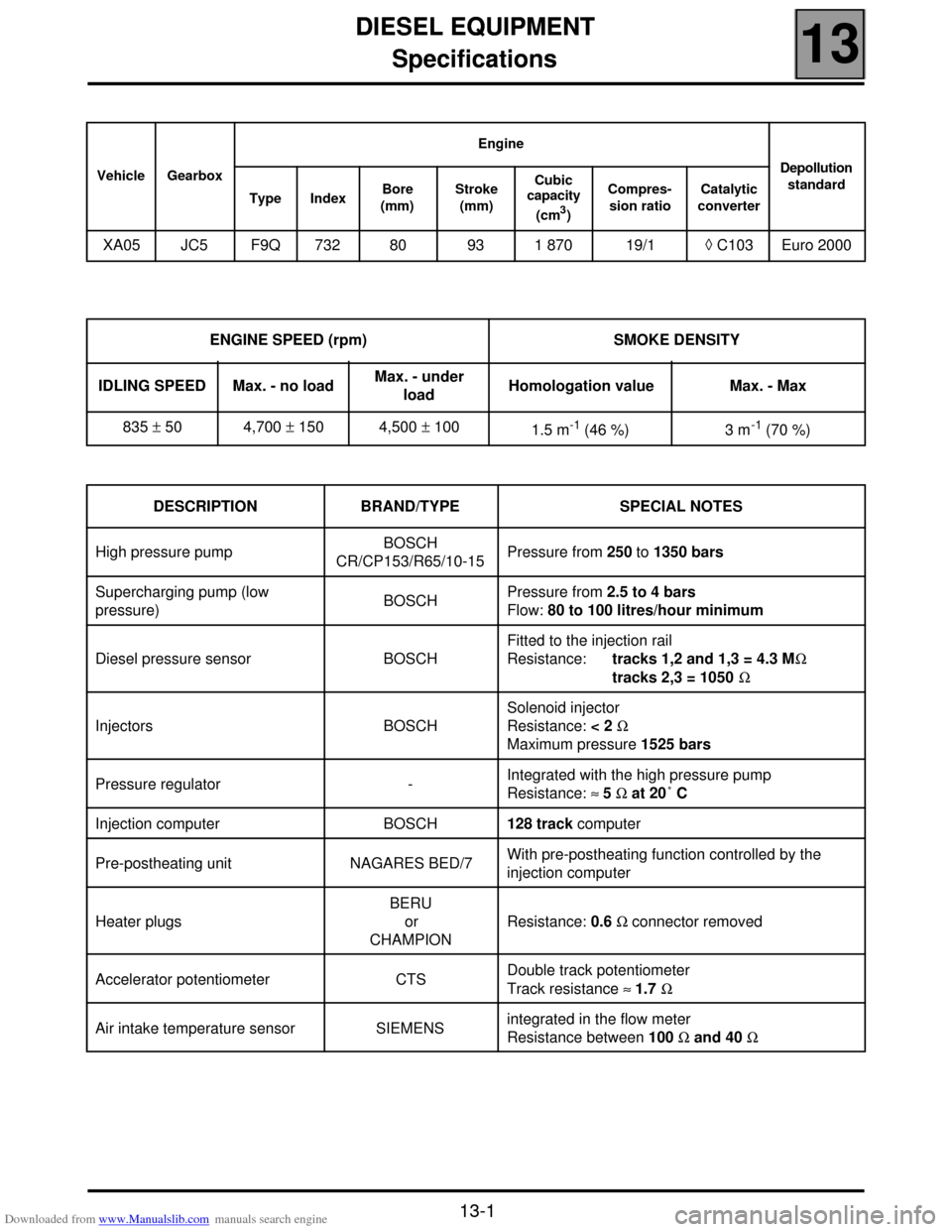
Downloaded from www.Manualslib.com manuals search engine DIESEL EQUIPMENT
Specifications
13
113
DIESEL EQUIPMENT
Specifications
Vehicle GearboxEngine
Depollution
standard
Type IndexBore
(mm) Stroke
(mm) Cubic
capacity
(cm
3)Compres-
sion ratioCatalytic
converter
XA05 JC5 F9Q 732 80 93 1 870 19/1◊ C103 Euro 2000
ENGINE SPEED (rpm) SMOKE DENSITY
IDLING SPEED Max. - no loadMax. - under
loadHomologation value Max. - Max
835 ± 50 4,700 ± 150 4,500 ± 100
1.5 m
-1 (46 %) 3 m-1 (70 %)
DESCRIPTION BRAND/TYPE SPECIAL NOTES
High pressure pumpBOSCH
CR/CP153/R65/10-15Pressure from 250 to 1350 bars
Supercharging pump (low
pressure)BOSCHPressure from 2.5 to 4 bars
Flow: 80 to 100 litres/hour minimum
Diesel pressure sensor BOSCHFitted to the injection rail
Resistance: tracks 1,2 and 1,3 = 4.3 MΩ
tracks 2,3 = 1050 Ω
Injectors BOSCHSolenoid injector
Resistance: < 2 Ω
Maximum pressure 1525 bars
Pressure regulator - Integrated with the high pressure pump
Resistance: ≈ 5 Ω at 20˚ C
Injection computer BOSCH128 track computer
Pre-postheating unit NAGARES BED/7With pre-postheating function controlled by the
injection computer
Heater plugsBERU
or
CHAMPIONResistance: 0.6 Ω connector removed
Accelerator potentiometer CTSDouble track potentiometer
Track resistance ≈ 1.7 Ω
Air intake temperature sensor SIEMENSintegrated in the flow meter
Resistance between 100 Ω and 40 Ω
13-1
Page 68 of 118
Downloaded from www.Manualslib.com manuals search engine DIESEL EQUIPMENT
Pre-postheating control
13
13-17
Pre-postheating control
The pre-postheating function is controlled by the preheating unit.
OPERATING PRINCIPLE FOR PRE-POST HEATING
1) "Preheating" on ignition
a) Variable preheating
The warning light lighting time and the
supply to heater plugs time depends on the
coolant temperature and the battery
voltage.
In all cases the injection warning light
lighting time cannot exceed 15 seconds.
b) Fixed preheating
After the warning light goes out the plugs
remain supplied for a fixed period of
10 seconds.2) Starting
The plugs remain supplied while the starter is
being activated.
3) "Postheating" while the engine is running
During this phase the plugs are supplied
continuously according to coolant temperature.
time (s)
Coolant
temperature °C For idling speed without
depression of the accelerator
pedal.
Page 69 of 118
Downloaded from www.Manualslib.com manuals search engine DIESEL EQUIPMENT
Heater plugs
13
13-18
Heater plugs
The resistance of a heater plug is 0.6 Ω.
Plugs may be removed without having to open the
high pressure circuit.
REMOVAL
Unclip the plug connector.
Clean the plug exterior to avoid any dirt entering the
cylinder.
Undo and then remove the plugs.
To undo the plug on cylinder 4 use a 10 mm long radio
socket attached to a universal joint. Once the plug is
loosened use a pipe socket to unscrew it completely.
REFITTING
Proceed in the reverse order to removal.TIGHTENING TORQUES (in daN.m)
Heater plug 1.5
15762S
Page 103 of 118
Downloaded from www.Manualslib.com manuals search engine COOLING SYSTEM
Filling and bleeding
19
119 COOLING SYSTEM
Filling and bleeding
There is no heater matrix water control valve.
Water flow is continuous in the heater matrix, which
contributes to the cooling of the engine.
FILLING
It is essential to open the bleed screw on the
cylinder head coolant pipe housing outlet.
Fill the circuit through the expansion bottle opening.
Close the bleed screw as soon as the fluid runs out in
a continuous jet.
Start the engine (2500 rpm).
Adjust the level by overflow for a period of about
4 minutes.
Tighten the expansion bottle cap.
BLEEDING
Let the engine run for 20 minutes at 2500 rpm, until
the engine cooling fan operates (time required for
automatic degassing).
Check the liquid level is at the "Maximum" marker.
DO NOT OPEN THE BLEED SCREW(S) WITH THE
ENGINE RUNNING.
REFIT THE EXPANSION BOTTLE CAP WHILE THE
ENGINE IS WARM.
19-1
Page 104 of 118
Downloaded from www.Manualslib.com manuals search engine COOLING SYSTEM
Diagram
19
19-2
Diagram
1 Engine
2 Radiator
3 "Hot" container with degassing after thermostat
4 Heater matrix
5 Thermostat mounting
6 Thermoplunger mounting (if fitted)7 3 mm ∅ restriction
8 6 mm ∅ restriction
9 Oil/water exchanger
10 Water pump
11 Thermostat
12 Bleed screw
The expansion bottle valve rating is 1.2 bar
(colour: brown).