Page 65 of 80
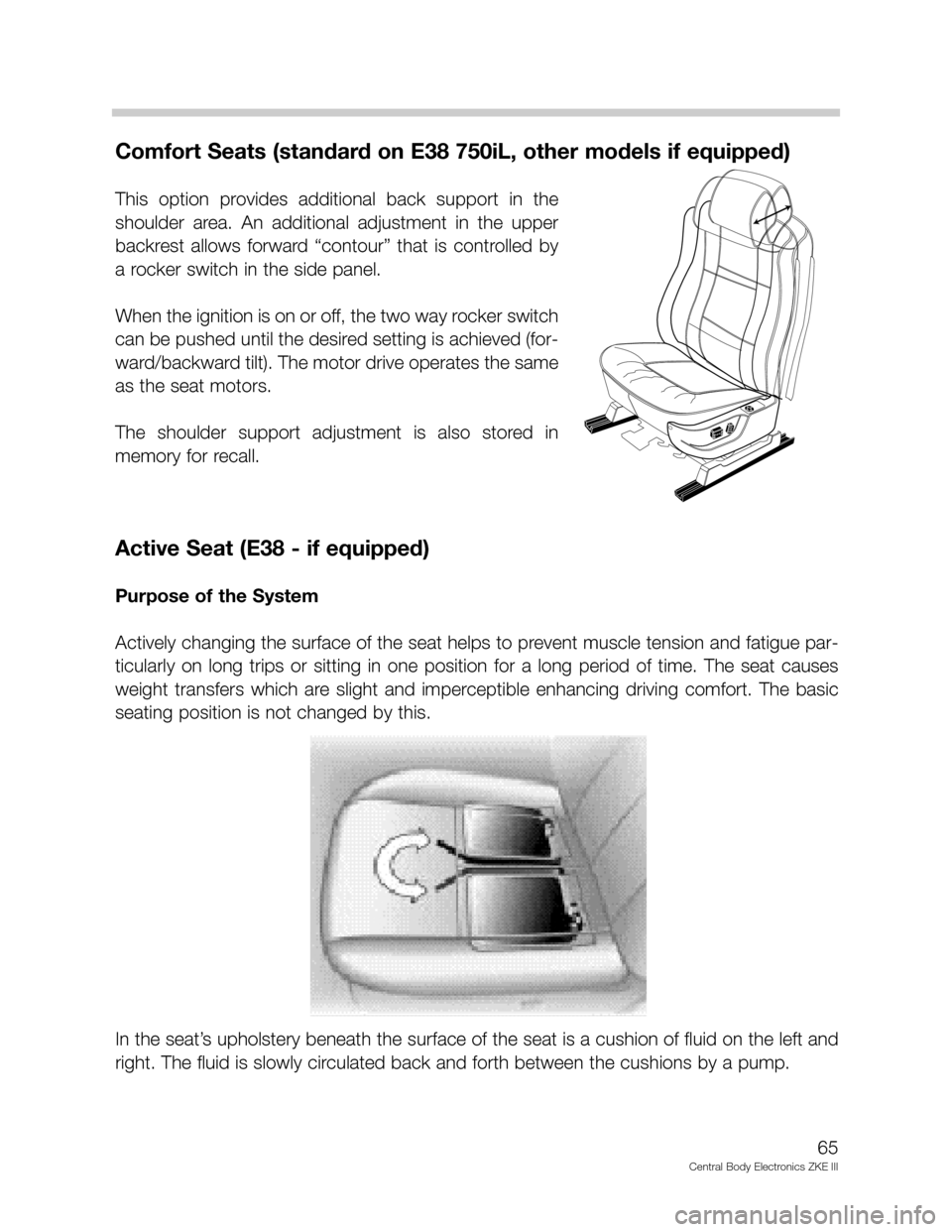
Comfort Seats (standard on E38 750iL, other models if equipped)
This option provides additional back support in the
shoulder area. An additional adjustment in the upper
backrest allows forward “contour” that is controlled by
a rocker switch in the side panel.
When the ignition is on or off, the two way rocker switch
can be pushed until the desired setting is achieved (for-
ward/backward tilt). The motor drive operates the same
as the seat motors.
The shoulder support adjustment is also stored in
memory for recall.
Active Seat (E38 - if equipped)
Purpose of the System
Actively changing the surface of the seat helps to prevent muscle tension and fatigue par-
ticularly on long trips or sitting in one position for a long period of time. The seat causes
weight transfers which are slight and imperceptible enhancing driving comfort. The basic
seating position is not changed by this.
In the seat’s upholstery beneath the surface of the seat is a cushion of fluid on the left and
right. The fluid is slowly circulated back and forth between the cushions by a pump.
65
Central Body Electronics ZKE III
Page 66 of 80
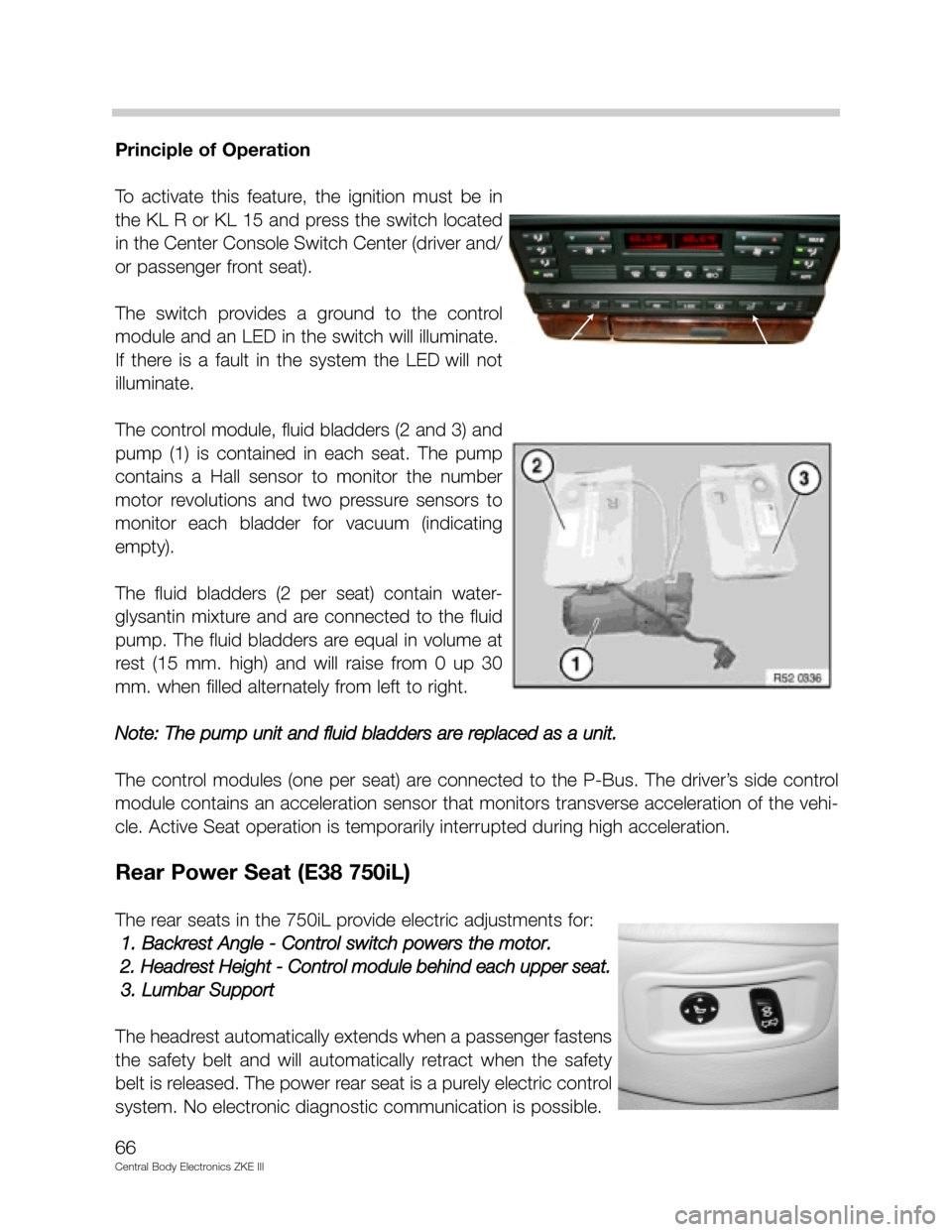
Principle of Operation
To activate this feature, the ignition must be in
the KL R or KL 15 and press the switch located
in the Center Console Switch Center (driver and/
or passenger front seat).
The switch provides a ground to the control
module and an LED in the switch will illuminate.
If there is a fault in the system the LED will not
illuminate.
The control module, fluid bladders (2 and 3) and
pump (1) is contained in each seat. The pump
contains a Hall sensor to monitor the number
motor revolutions and two pressure sensors to
monitor each bladder for vacuum (indicating
empty).
The fluid bladders (2 per seat) contain water-
glysantin mixture and are connected to the fluid
pump. The fluid bladders are equal in volume at
rest (15 mm. high) and will raise from 0 up 30
mm. when filled alternately from left to right.
Note: The pump unit and fluid bladders are replaced as a unit.
The control modules (one per seat) are connected to the P-Bus. The driver’s side control
module contains an acceleration sensor that monitors transverse acceleration of the vehi-
cle. Active Seat operation is temporarily interrupted during high acceleration.
Rear Power Seat (E38 750iL)
The rear seats in the 750iL provide electric adjustments for:
1. Backrest Angle - Control switch powers the motor.
2. Headrest Height - Control module behind each upper seat.
3. Lumbar Support
The headrest automatically extends when a passenger fastens
the safety belt and will automatically retract when the safety
belt is released. The power rear seat is a purely electric control
system. No electronic diagnostic communication is possible.
66
Central Body Electronics ZKE III
Page 67 of 80
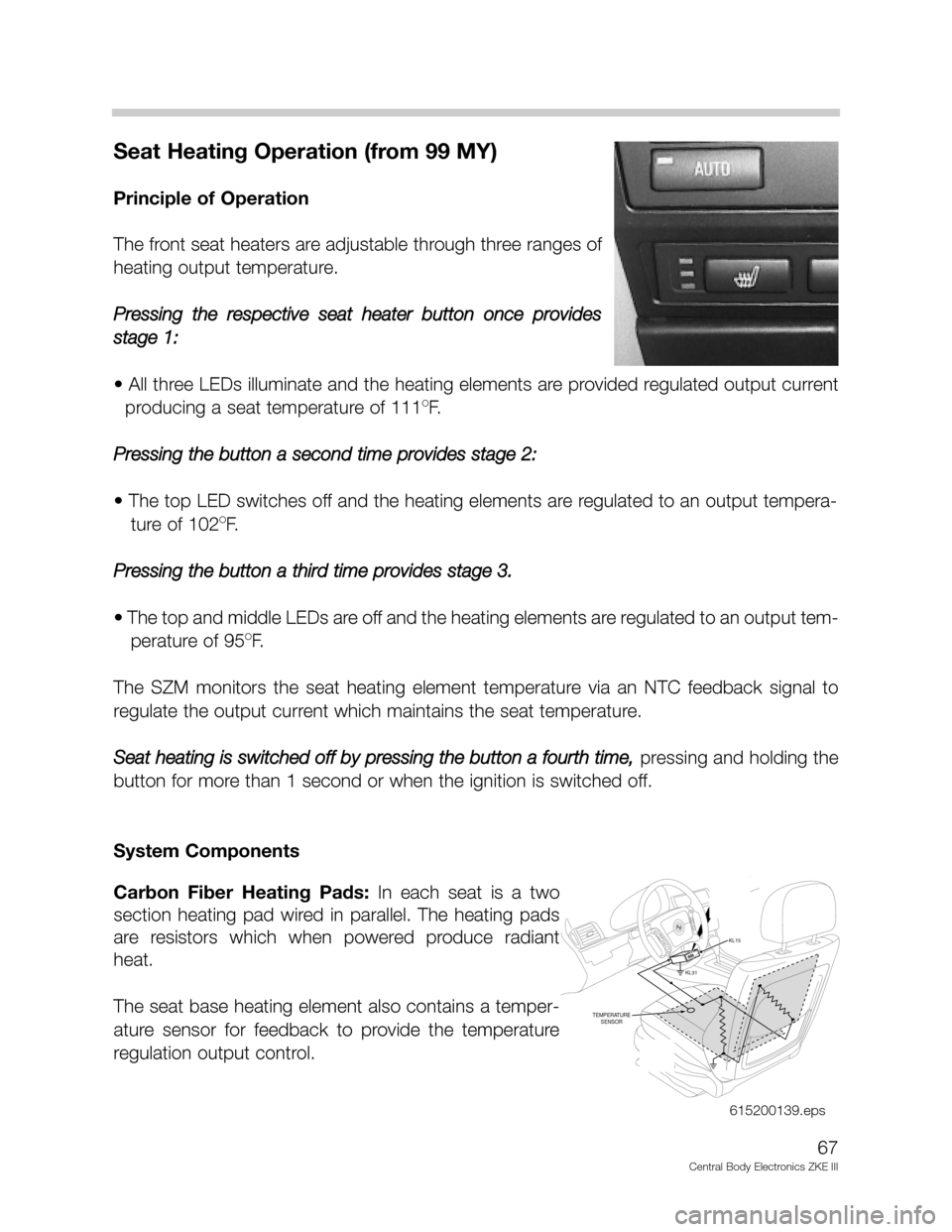
67
Central Body Electronics ZKE III
Seat Heating Operation (from 99 MY)
Principle of Operation
The front seat heaters are adjustable through three ranges of
heating output temperature.
Pressing the respective seat heater button once provides
stage 1:
• All three LEDs illuminate and the heating elements are provided regulated output current
producing a seat temperature of 111
OF.
Pressing the button a second time provides stage 2:
• The top LED switches off and the heating elements are regulated to an output tempera-
ture of 102
OF.
Pressing the button a third time provides stage 3.
• The top and middle LEDs are off and the heating elements are regulated to an output tem-
perature of 95
OF.
The SZM monitors the seat heating element temperature via an NTC feedback signal to
regulate the output current which maintains the seat temperature.
Seat heating is switched off by pressing the button a fourth time,
pressing and holding the
button for more than 1 second or when the ignition is switched off.
System Components
Carbon Fiber Heating Pads:In each seat is a two
section heating pad wired in parallel. The heating pads
are resistors which when powered produce radiant
heat.
The seat base heating element also contains a temper-
ature sensor for feedback to provide the temperature
regulation output control.
KL31
KL15
TEMPERATURE
SENSOR
615200139.eps
Page 68 of 80
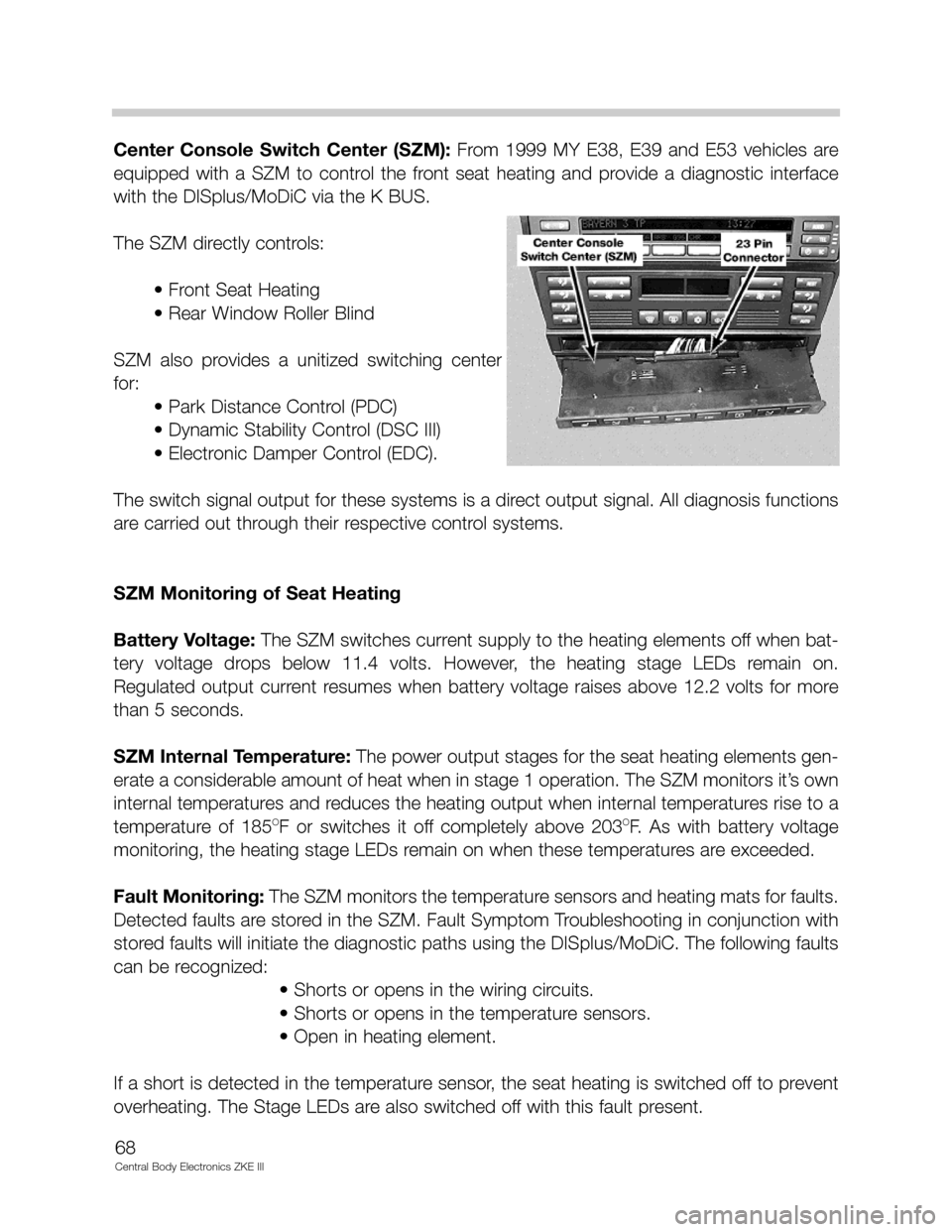
68
Central Body Electronics ZKE III
Center Console Switch Center (SZM): From 1999 MY E38, E39 and E53 vehicles are
equipped with a SZM to control the front seat heating and provide a diagnostic interface
with the DISplus/MoDiC via the K BUS.
The SZM directly controls:
• Front Seat Heating
• Rear Window Roller Blind
SZM also provides a unitized switching center
for:
• Park Distance Control (PDC)
• Dynamic Stability Control (DSC III)
• Electronic Damper Control (EDC).
The switch signal output for these systems is a direct output signal. All diagnosis functions
are carried out through their respective control systems.
SZM Monitoring of Seat Heating
Battery Voltage:The SZM switches current supply to the heating elements off when bat-
tery voltage drops below 11.4 volts. However, the heating stage LEDs remain on.
Regulated output current resumes when battery voltage raises above 12.2 volts for more
than 5 seconds.
SZM Internal Temperature: The power output stages for the seat heating elements gen-
erate a considerable amount of heat when in stage 1 operation. The SZM monitors it’s own
internal temperatures and reduces the heating output when internal temperatures rise to a
temperature of 185
OF or switches it off completely above 203OF. As with battery voltage
monitoring, the heating stage LEDs remain on when these temperatures are exceeded.
Fault Monitoring:The SZM monitors the temperature sensors and heating mats for faults.
Detected faults are stored in the SZM. Fault Symptom Troubleshooting in conjunction with
stored faults will initiate the diagnostic paths using the DISplus/MoDiC. The following faults
can be recognized:
• Shorts or opens in the wiring circuits.
• Shorts or opens in the temperature sensors.
• Open in heating element.
If a short is detected in the temperature sensor, the seat heating is switched off to prevent
overheating. The Stage LEDs are also switched off with this fault present.
Page 69 of 80
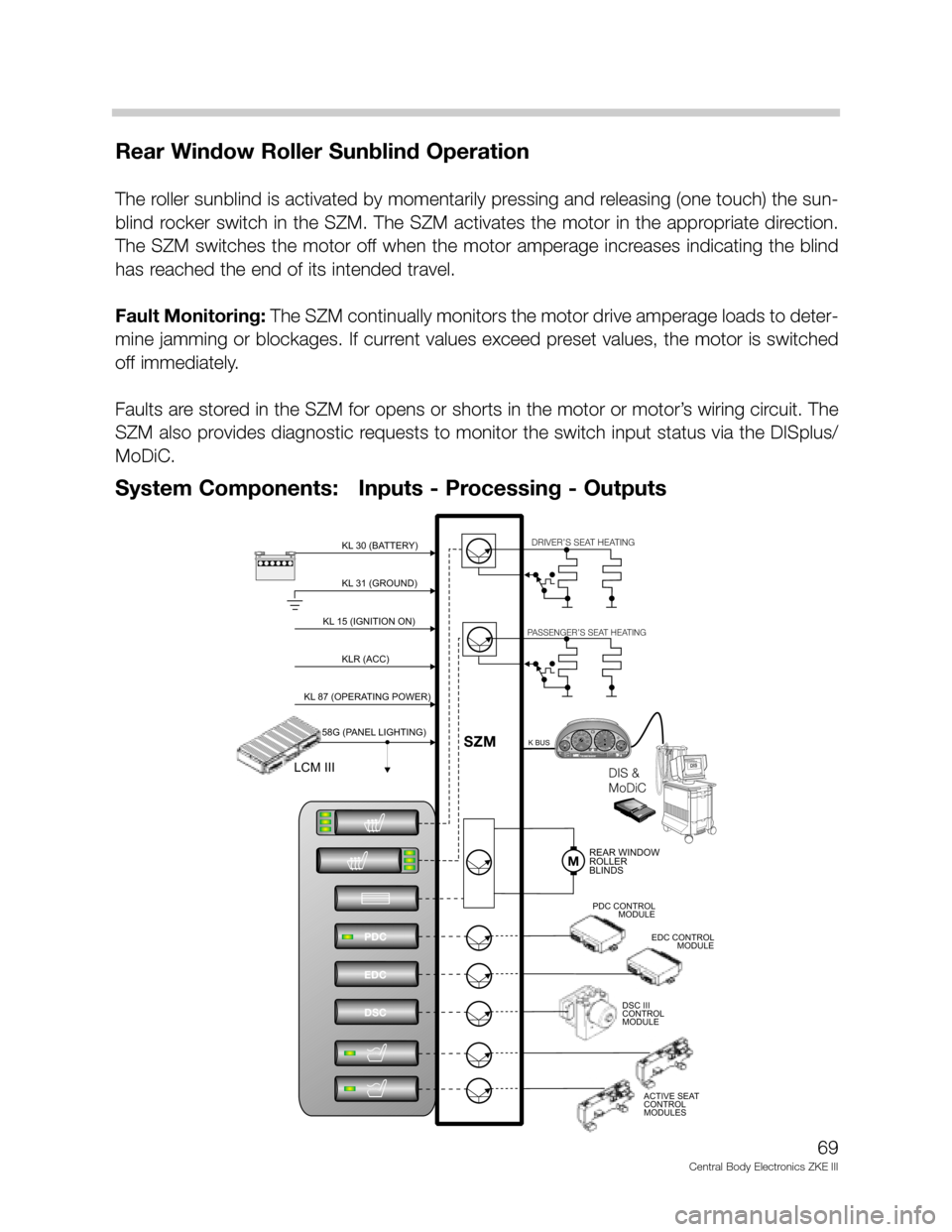
Rear Window Roller Sunblind Operation
The roller sunblind is activated by momentarily pressing and releasing (one touch) the sun-
blind rocker switch in the SZM. The SZM activates the motor in the appropriate direction.
The SZM switches the motor off when the motor amperage increases indicating the blind
has reached the end of its intended travel.
Fault Monitoring: The SZM continually monitors the motor drive amperage loads to deter-
mine jamming or blockages. If current values exceed preset values, the motor is switched
off immediately.
Faults are stored in the SZM for opens or shorts in the motor or motor’s wiring circuit. The
SZM also provides diagnostic requests to monitor the switch input status via the DISplus/
MoDiC.
69
Central Body Electronics ZKE III
KL 31 (GROUND)KL 31 (GROUND)
DIS
DIS
BMWDIS
B
M
WD
I
S
BMWDIS
BMW
DIS
D
ia
g
n
o
s
e
-
a
n
d
In
fo
r
m
a
ti
o
n
S
y
s
t
e
mDIS &
MoDiCDIS &
MoDiC
M
o
Di
C
0½
CHECK
ENGINE
CHECK
ENGINEOIL SERVICEOIL SERVICEINSPECTIONINSPECTIONP
1/min
x1000km/hELECTRONICMPH1
2020404060608080100180160140 1201002001202201402400234
5
6
7!!ABS20 DIGIT READOUT20 DIGIT READOUT
123456
prnd432
m
prnd432
m
122.4 +72.0 fo
+72.0 fomiles0
10
15 20 40
KL 30 (BATTERY)KL 30 (BATTERY)-+
KL 15 (IGNITION ON)KL 15 (IGNITION ON)
KLR (ACC)KLR (ACC)
KL 87 (OPERATING POWER)KL 87 (OPERATING POWER)
58G (PANEL LIGHTING)58G (PANEL LIGHTING)
LCM IIILCM III
PDC
EDC
DSC
MREAR WINDOW
ROLLER
BLINDSREAR WINDOW
ROLLER
BLINDS
DRIVER’S SEAT HEATINGDRIVER’S SEAT HEATING
PASSENGER’S SEAT HEATINGPASSENGER’S SEAT HEATING
K BUSK BUS
PDC CONTROL
MODULEPDC CONTROL
MODULE
EDC CONTROL
MODULEEDC CONTROL
MODULE
SZMSZM
DSC III
CONTROL
MODULEDSC III
CONTROL
MODULE
ACTIVE SEAT
CONTROL
MODULESACTIVE SEAT
CONTROL
MODULES
System Components: Inputs - Processing - Outputs
Page 70 of 80
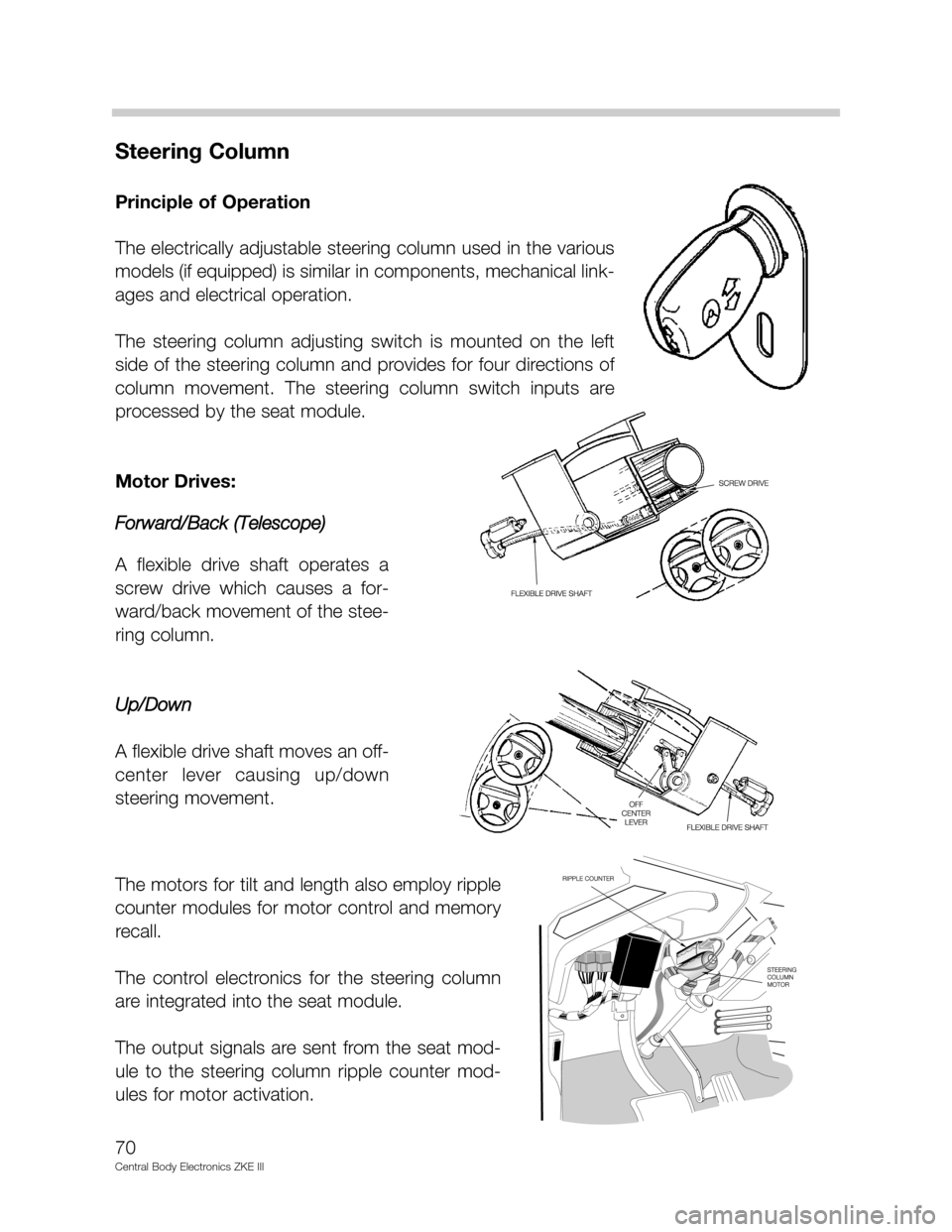
Steering Column
Principle of Operation
The electrically adjustable steering column used in the various
models (if equipped) is similar in components, mechanical link-
ages and electrical operation.
The steering column adjusting switch is mounted on the left
side of the steering column and provides for four directions of
column movement. The steering column switch inputs are
processed by the seat module.
Motor Drives:
Forward/Back (Telescope)
A flexible drive shaft operates a
screw drive which causes a for-
ward/back movement of the stee-
ring column.
Up/Down
A flexible drive shaft moves an off-
center lever causing up/down
steering movement.
The motors for tilt and length also employ ripple
counter modules for motor control and memory
recall.
The control electronics for the steering column
are integrated into the seat module.
The output signals are sent from the seat mod-
ule to the steering column ripple counter mod-
ules for motor activation.
70
Central Body Electronics ZKE III
Page 71 of 80
71
Central Body Electronics ZKE III
System Components: Inputs - Processing - Outputs
Entry/Exit Aid
The Steering Column Memory provides the feature of raising the steering column to ease
in exiting the vehicle and return it to the previous position after the vehicle is entered.
Raising the Steering Column:
Lowering the Steering Column:
• The ignition is switched “off”. • The ignition is switched to KL 15.
• The ignition is switched to KL R • The Handbrake is released or the door is closed.
and the driver’s door is opened.
• The ignition is switched to KL 15, The steering column recall movement can be inter-
driver’s door open with the hand- rupted at any time by tapping the adjusting lever.
brake applied.
Page 72 of 80
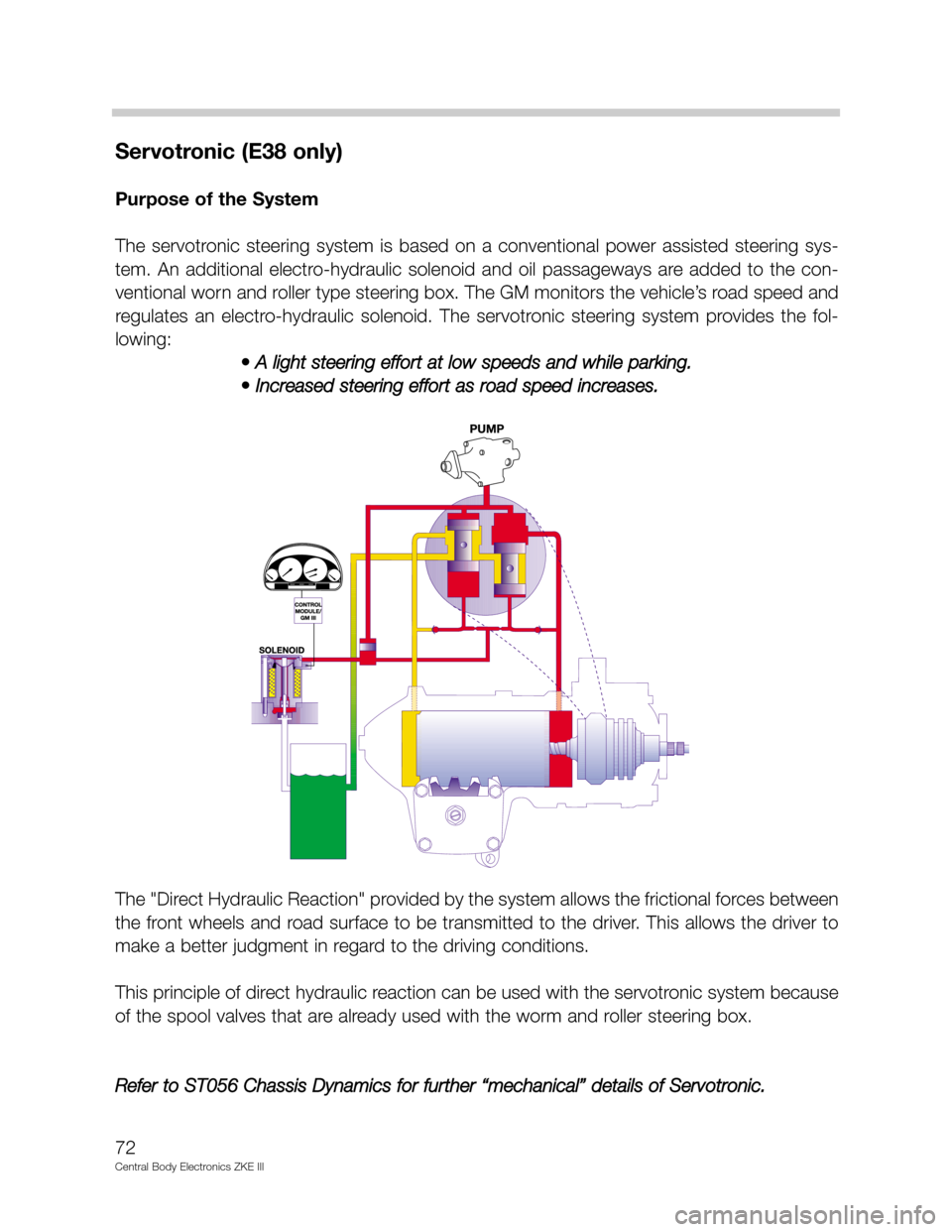
Servotronic (E38 only)
Purpose of the System
The servotronic steering system is based on a conventional power assisted steering sys-
tem. An additional electro-hydraulic solenoid and oil passageways are added to the con-
ventional worn and roller type steering box. The GM monitors the vehicle’s road speed and
regulates an electro-hydraulic solenoid. The servotronic steering system provides the fol-
lowing:
• A light steering effort at low speeds and while parking.
• Increased steering effort as road speed increases.
The "Direct Hydraulic Reaction" provided by the system allows the frictional forces between
the front wheels and road surface to be transmitted to the driver. This allows the driver to
make a better judgment in regard to the driving conditions.
This principle of direct hydraulic reaction can be used with the servotronic system because
of the spool valves that are already used with the worm and roller steering box.
Refer to ST056 Chassis Dynamics for further “mechanical” details of Servotronic.
72
Central Body Electronics ZKE III