Page 362 of 558
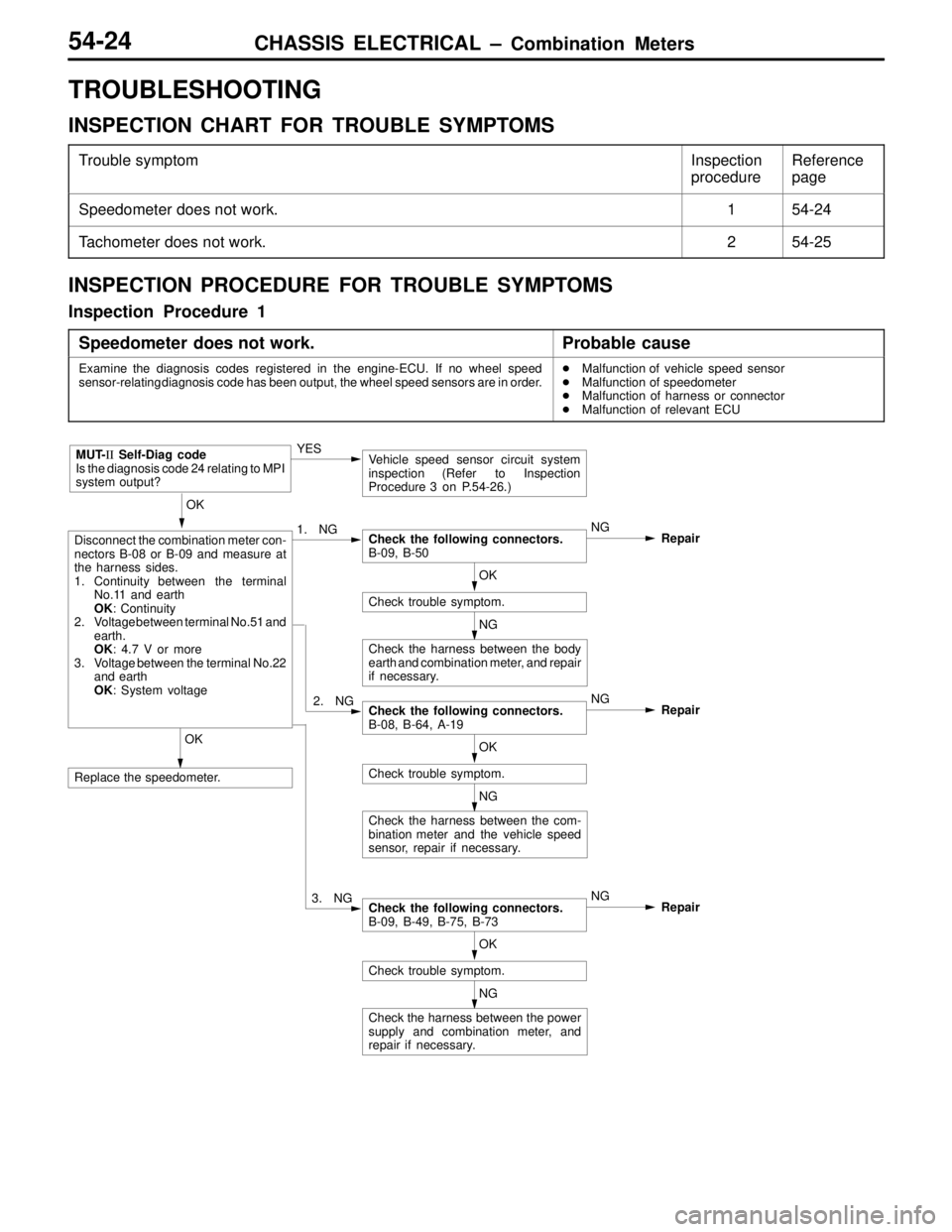
CHASSIS ELECTRICAL – Combination Meters54-24
TROUBLESHOOTING
INSPECTION CHART FOR TROUBLE SYMPTOMS
Trouble symptomInspection
procedureReference
page
Speedometer does not work.154-24
Tachometer does not work.254-25
INSPECTION PROCEDURE FOR TROUBLE SYMPTOMS
Inspection Procedure 1
Speedometer does not work.
Probable cause
Examine the diagnosis codes registered in the engine-ECU. If no wheel speed
sensor-relating diagnosis code has been output, the wheel speed sensors are in order.Malfunction of vehicle speed sensor
Malfunction of speedometer
Malfunction of harness or connector
Malfunction of relevant ECU
Disconnect the combination meter con-
nectors B-08 or B-09 and measure at
the harness sides.
1. Continuity between the terminal
No.11 and earth
OK: Continuity
2. Voltage between terminal No.51 and
earth.
OK: 4.7 V or more
3. Voltage between the terminal No.22
and earth
OK: System voltage1. NG
OK
Replace the speedometer.YES
Vehicle speed sensor circuit system
inspection (Refer to Inspection
Procedure 3 on P.54-26.)
OK
Check the following connectors.
B-09, B-50NG
Repair
OK
Check trouble symptom.
Check the harness between the body
earth and combination meter, and repair
if necessary.NG
2. NGCheck the following connectors.
B-08, B-64, A-19NG
Repair
OK
Check trouble symptom.
Check the harness between the com-
bination meter and the vehicle speed
sensor, repair if necessary.NG
3. NGCheck the following connectors.
B-09, B-49, B-75, B-73NG
Repair
OK
Check trouble symptom.
Check the harness between the power
supply and combination meter, and
repair if necessary.NG
MUT-II Self-Diag code
Is the diagnosis code 24 relating to MPI
system output?
Page 364 of 558
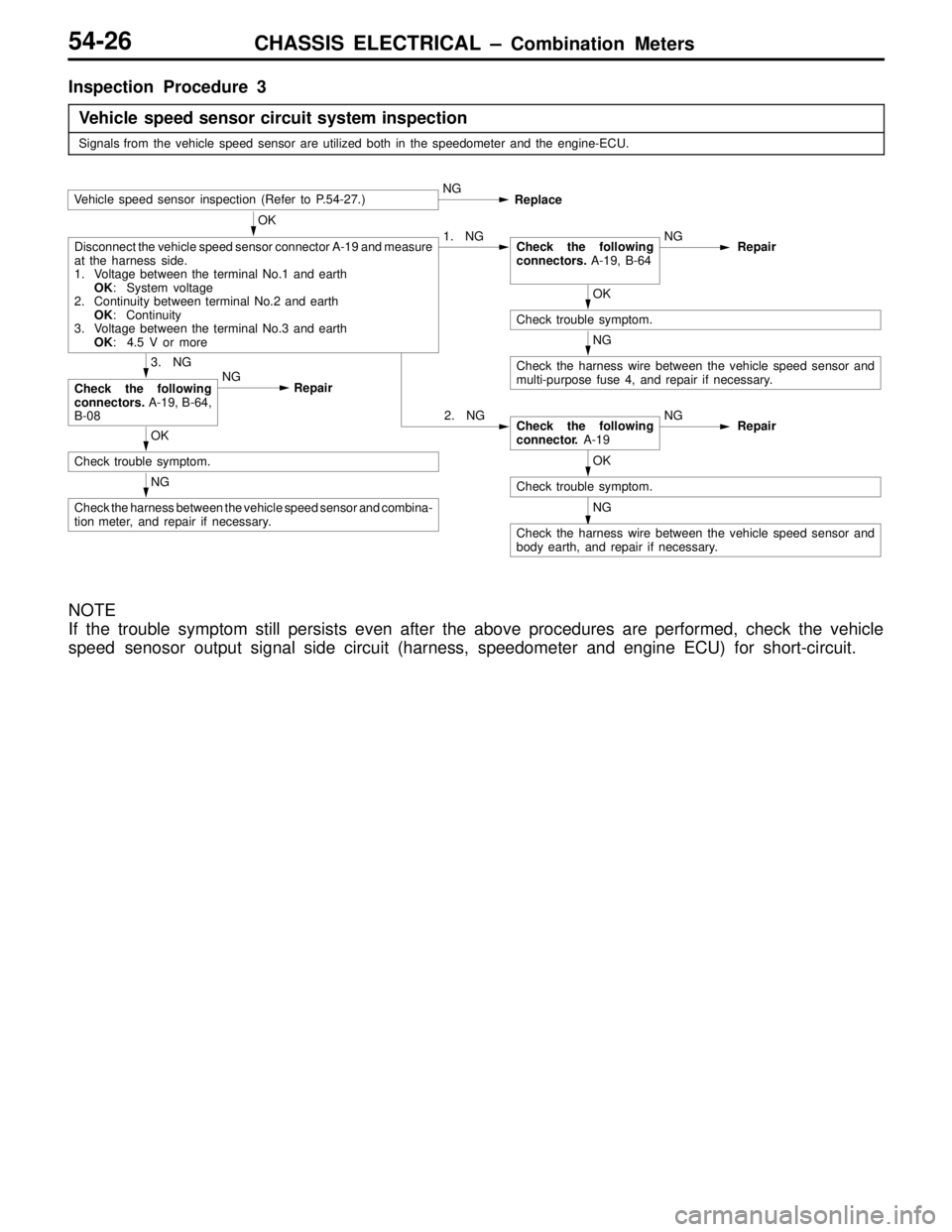
CHASSIS ELECTRICAL – Combination Meters54-26
Inspection Procedure 3
Vehicle speed sensor circuit system inspection
Signals from the vehicle speed sensor are utilized both in the speedometer and the engine-ECU.
Vehicle speed sensor inspection (Refer to P.54-27.)NG
Replace
OK
Disconnect the vehicle speed sensor connector A-19 and measure
at the harness side.
1. Voltage between the terminal No.1 and earth
OK: System voltage
2. Continuity between terminal No.2 and earth
OK: Continuity
3. Voltage between the terminal No.3 and earth
OK: 4.5 V or more1. NGCheck the following
connectors. A-19, B-64NG
Repair
OK
Check trouble symptom.
NG
Check the harness wire between the vehicle speed sensor and
multi-purpose fuse 4, and repair if necessary.3. NG
Check the following
connectors. A-19, B-64,
B-08NG
Repair
2. NGCheck the following
connector. A-19NG
RepairOK
Check trouble symptom.
NG
Check the harness between the vehicle speed sensor and combina-
tion meter, and repair if necessary.OK
Check trouble symptom.
NG
Check the harness wire between the vehicle speed sensor and
body earth, and repair if necessary.
NOTE
If the trouble symptom still persists even after the above procedures are performed, check the vehicle
speed senosor output signal side circuit (harness, speedometer and engine ECU) for short-circuit.
Page 367 of 558
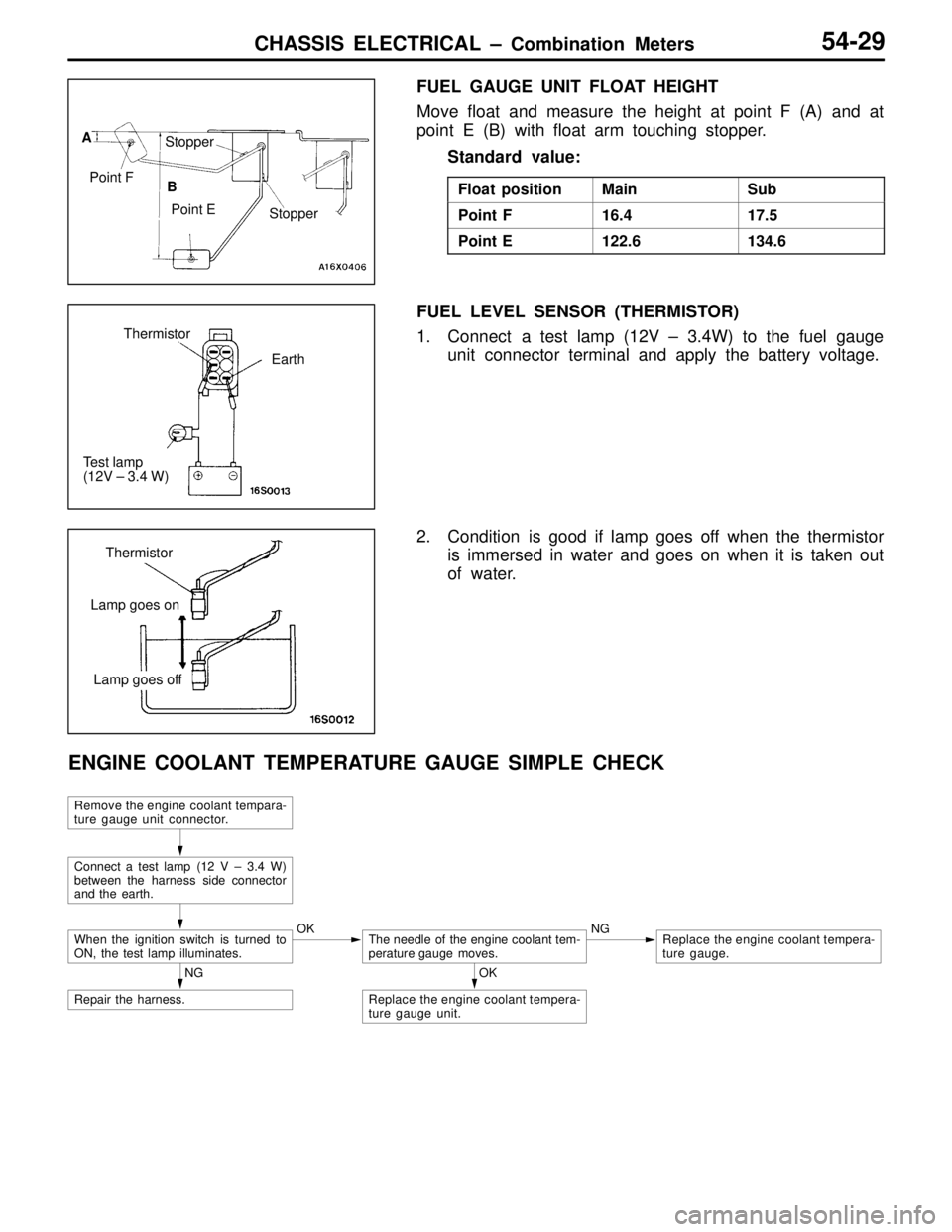
CHASSIS ELECTRICAL – Combination Meters54-29
FUEL GAUGE UNIT FLOAT HEIGHT
Move float and measure the height at point F (A) and at
point E (B) with float arm touching stopper.
Standard value:
Float positionMainSub
Point F16.417.5
Point E122.6134.6
FUEL LEVEL SENSOR (THERMISTOR)
1. Connect a test lamp (12V – 3.4W) to the fuel gauge
unit connector terminal and apply the battery voltage.
2. Condition is good if lamp goes off when the thermistor
is immersed in water and goes on when it is taken out
of water.
ENGINE COOLANT TEMPERATURE GAUGE SIMPLE CHECK
Remove the engine coolant tempara-
ture gauge unit connector.
Connect a test lamp (12 V – 3.4 W)
between the harness side connector
and the earth.
When the ignition switch is turned to
ON, the test lamp illuminates.OKThe needle of the engine coolant tem-
perature gauge moves.NGReplace the engine coolant tempera-
ture gauge.
OK
Replace the engine coolant tempera-
ture gauge unit.
NG
Repair the harness.
Point F
Point E
A
B Stopper
Stopper
Test lamp
(12V – 3.4 W)
Earth
Thermistor
Thermistor
Lamp goes on
Lamp goes off
Page 368 of 558
CHASSIS ELECTRICAL – Combination Meters54-30
ENGINE COOLANT TEMPERATURE GAUGE UNIT
CHECK
1. Bleed the engine coolant.
2. Remove the engine coolant temperature gauge unit.
3. Immerse the unit in 70C water to measure the resistance.
Standard value: 104 ±13.5 Ω
4. After checking, apply the specified adhesive around the
thread of engine coolant temperature gauge unit. Then,
tighten the unit to the specified torque.
Specified sealant:
3M Adhesive Nut Locking No. 4171 or equivalent
5. Add engine coolant.
COMBINATION METERS
REMOVAL AND INSTALLATION
2 1
3
Vehicle speed sensor removal
steps
Battery and battery tray
Air cleaner assembly
1. Vehicle speed sensorCombination meter removal steps
2. Meter bezel
3. Combination meter
ThermometerCircuit tester
10 – 12 Nm
Page 369 of 558
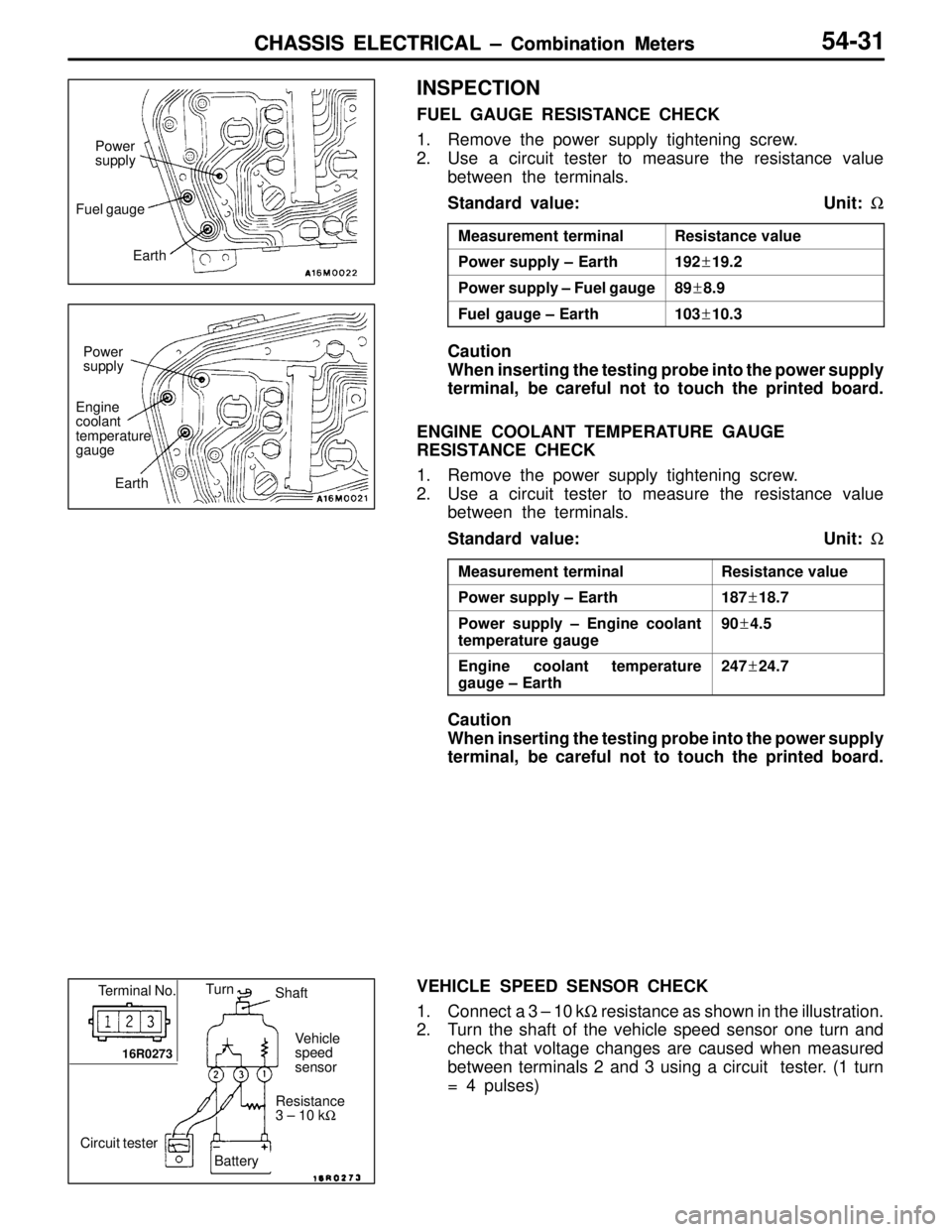
CHASSIS ELECTRICAL – Combination MetersCHASSIS ELECTRICAL – Combination MetersCHASSIS ELECTRICAL – Combination Meters54-31
INSPECTION
FUEL GAUGE RESISTANCE CHECK
1. Remove the power supply tightening screw.
2. Use a circuit tester to measure the resistance value
between the terminals.
Standard value: Unit: Ω
Measurement terminalResistance value
Power supply – Earth192±19.2
Power supply – Fuel gauge89±8.9
Fuel gauge – Earth103±10.3
Caution
When inserting the testing probe into the power supply
terminal, be careful not to touch the printed board.
ENGINE COOLANT TEMPERATURE GAUGE
RESISTANCE CHECK
1. Remove the power supply tightening screw.
2. Use a circuit tester to measure the resistance value
between the terminals.
Standard value: Unit: Ω
Measurement terminalResistance value
Power supply – Earth187±18.7
Power supply – Engine coolant
temperature gauge90±4.5
Engine coolant temperature
gauge – Earth247±24.7
Caution
When inserting the testing probe into the power supply
terminal, be careful not to touch the printed board.
VEHICLE SPEED SENSOR CHECK
1. Connect a 3 – 10 kΩ resistance as shown in the illustration.
2. Turn the shaft of the vehicle speed sensor one turn and
check that voltage changes are caused when measured
between terminals 2 and 3 using a circuit tester. (1 turn
= 4 pulses)
Fuel gauge
Power
supply
Earth
Earth
Power
supply
Engine
coolant
temperature
gauge
TurnShaft
Circuit testerResistance
3 – 10 kΩ Vehicle
speed
sensor Terminal No.
16R0273
Battery
Page 373 of 558
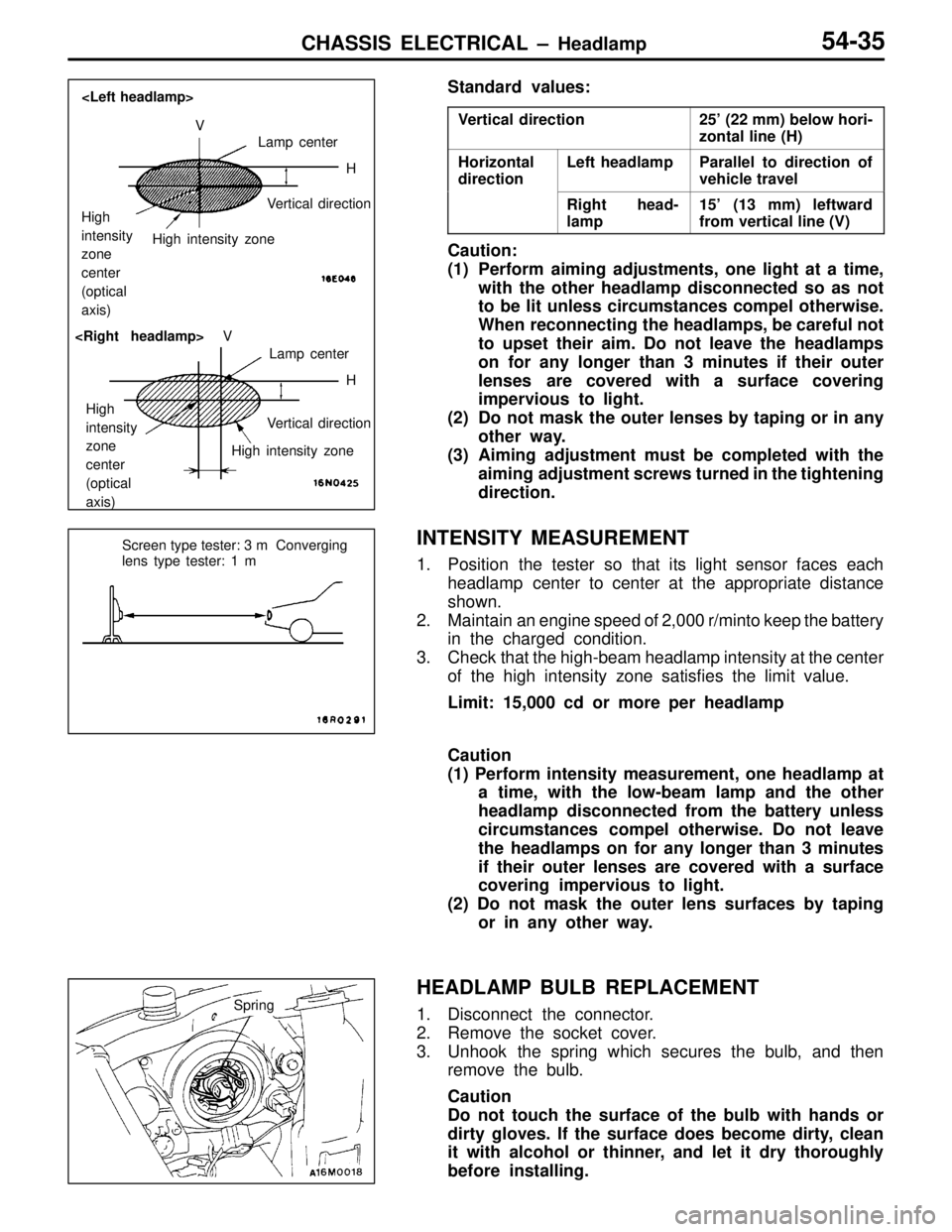
CHASSIS ELECTRICAL – Headlamp54-35
Standard values:
Vertical direction25’ (22 mm) below hori-
zontal line (H)
Horizontal
directionLeft headlampParallel to direction of
vehicle travel
Right head-
lamp15’ (13 mm) leftward
from vertical line (V)
Caution:
(1) Perform aiming adjustments, one light at a time,
with the other headlamp disconnected so as not
to be lit unless circumstances compel otherwise.
When reconnecting the headlamps, be careful not
to upset their aim. Do not leave the headlamps
on for any longer than 3 minutes if their outer
lenses are covered with a surface covering
impervious to light.
(2) Do not mask the outer lenses by taping or in any
other way.
(3) Aiming adjustment must be completed with the
aiming adjustment screws turned in the tightening
direction.
INTENSITY MEASUREMENT
1. Position the tester so that its light sensor faces each
headlamp center to center at the appropriate distance
shown.
2. Maintain an engine speed of 2,000 r/minto keep the battery
in the charged condition.
3. Check that the high-beam headlamp intensity at the center
of the high intensity zone satisfies the limit value.
Limit: 15,000 cd or more per headlamp
Caution
(1) Perform intensity measurement, one headlamp at
a time, with the low-beam lamp and the other
headlamp disconnected from the battery unless
circumstances compel otherwise. Do not leave
the headlamps on for any longer than 3 minutes
if their outer lenses are covered with a surface
covering impervious to light.
(2) Do not mask the outer lens surfaces by taping
or in any other way.
HEADLAMP BULB REPLACEMENT
1. Disconnect the connector.
2. Remove the socket cover.
3. Unhook the spring which secures the bulb, and then
remove the bulb.
Caution
Do not touch the surface of the bulb with hands or
dirty gloves. If the surface does become dirty, clean
it with alcohol or thinner, and let it dry thoroughly
before installing.
Lamp center
Vertical direction
Vertical direction High
intensity
zone
center
(optical
axis)
High
intensity
zone
center
(optical
axis)High intensity zone
High intensity zoneLamp center V
H
V
H
Screen type tester: 3 m Converging
lens type tester: 1 m
Spring
Page 392 of 558
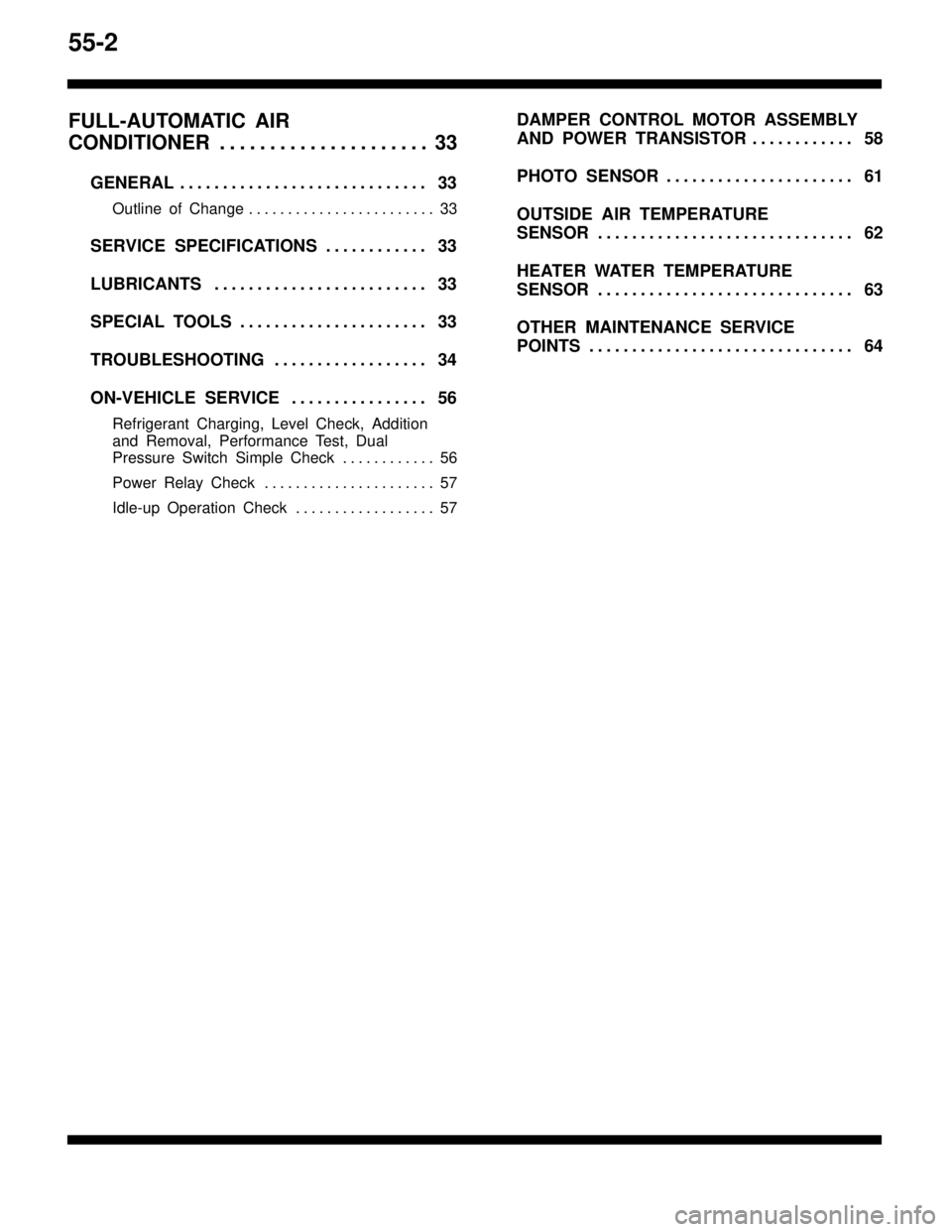
55-2
FULL-AUTOMATIC AIR
CONDITIONER 33. . . . . . . . . . . . . . . . . . . . .
GENERAL 33. . . . . . . . . . . . . . . . . . . . . . . . . . . . .
Outline of Change 33. . . . . . . . . . . . . . . . . . . . . . . .
SERVICE SPECIFICATIONS 33. . . . . . . . . . . .
LUBRICANTS 33. . . . . . . . . . . . . . . . . . . . . . . . .
SPECIAL TOOLS 33. . . . . . . . . . . . . . . . . . . . . .
TROUBLESHOOTING 34. . . . . . . . . . . . . . . . . .
ON-VEHICLE SERVICE 56. . . . . . . . . . . . . . . .
Refrigerant Charging, Level Check, Addition
and Removal, Performance Test, Dual
Pressure Switch Simple Check 56. . . . . . . . . . . .
Power Relay Check 57. . . . . . . . . . . . . . . . . . . . . .
Idle-up Operation Check 57. . . . . . . . . . . . . . . . . .
DAMPER CONTROL MOTOR ASSEMBLY
AND POWER TRANSISTOR 58. . . . . . . . . . . .
PHOTO SENSOR 61. . . . . . . . . . . . . . . . . . . . . .
OUTSIDE AIR TEMPERATURE
SENSOR 62. . . . . . . . . . . . . . . . . . . . . . . . . . . . . .
HEATER WATER TEMPERATURE
SENSOR 63. . . . . . . . . . . . . . . . . . . . . . . . . . . . . .
OTHER MAINTENANCE SERVICE
POINTS 64. . . . . . . . . . . . . . . . . . . . . . . . . . . . . . .
Page 394 of 558
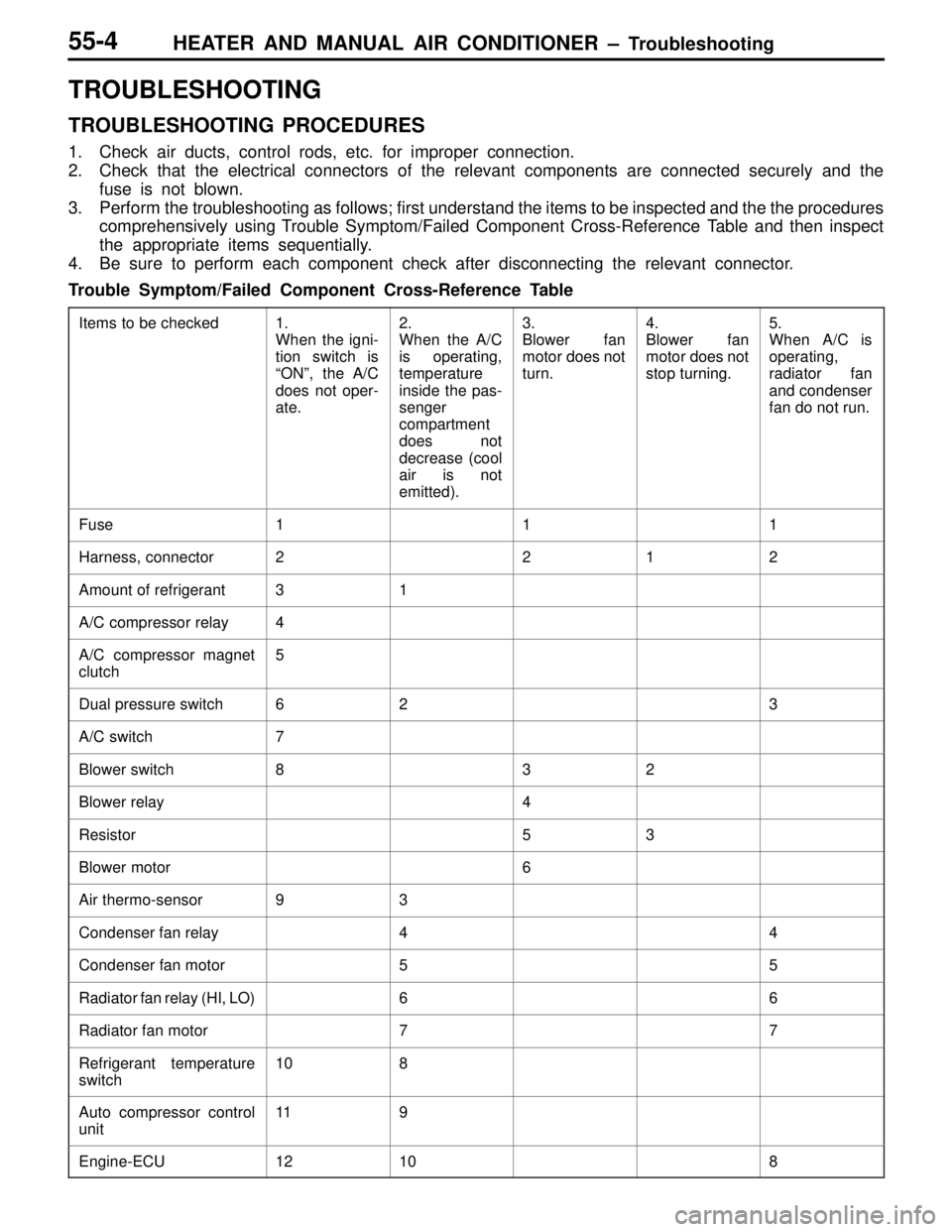
HEATER AND MANUAL AIR CONDITIONER – Troubleshooting55-4
TROUBLESHOOTING
TROUBLESHOOTING PROCEDURES
1. Check air ducts, control rods, etc. for improper connection.
2. Check that the electrical connectors of the relevant components are connected securely and the
fuse is not blown.
3. Perform the troubleshooting as follows; first understand the items to be inspected and the the procedures
comprehensively using Trouble Symptom/Failed Component Cross-Reference Table and then inspect
the appropriate items sequentially.
4. Be sure to perform each component check after disconnecting the relevant connector.
Trouble Symptom/Failed Component Cross-Reference Table
Items to be checked1.
When the igni-
tion switch is
“ON”, the A/C
does not oper-
ate.2.
When the A/C
is operating,
temperature
inside the pas-
senger
compartment
does not
decrease (cool
air is not
emitted).3.
Blower fan
motor does not
turn.4.
Blower fan
motor does not
stop turning.5.
When A/C is
operating,
radiator fan
and condenser
fan do not run.
Fuse111
Harness, connector2212
Amount of refrigerant31
A/C compressor relay4
A/C compressor magnet
clutch5
Dual pressure switch623
A/C switch7
Blower switch832
Blower relay4
Resistor53
Blower motor6
Air thermo-sensor93
Condenser fan relay44
Condenser fan motor55
Radiator fan relay (HI, LO)66
Radiator fan motor77
Refrigerant temperature
switch108
Auto compressor control
unit119
Engine-ECU12108