Page 162 of 1529
ENGINE - V8
DESCRIPTION AND OPERATION 12-2-7
Oil sump
The oil sump is bolted to the bottom of the cylinder block and the timing cover and is sealed to both components with
a one piece gasket. A removable baffle to prevent oil surge is fitted in the sump. The oil pick-up pipe and strainer
assembly is positioned within the sump and is attached at the pick-up end to a stud screwed into number four main
bearing cap and at the delivery end to the oil pump. The oil drain plug is located in the bottom of the sump and is
sealed with a washer.
Pistons and connecting rods
Each of the aluminium alloy pistons has two compression rings and an oil control ring. The pistons are secured to the
connecting rods by semi-floating gudgeon pins. Each gudgeon pin is offset by 0.5 mm (0.02 in). The top of each piston
is recessed, the depth of recess determining the compression ratio of the engine. Plain, big-end bearing shells are
fitted to each connecting rod and cap.
Page 163 of 1529
ENGINE - V8
12-2-8 DESCRIPTION AND OPERATION
Lubrication
A - To oil cooler, B - From oil cooler
NOTE: The oil cooler is only fitted to vehicles up to VIN 756821.
1Rocker shaft assembly
2Hydraulic tappet
3Oil pump4Oil filter element
5Oil pick-up pipe and strainer
6Oil pressure switch
Page 164 of 1529
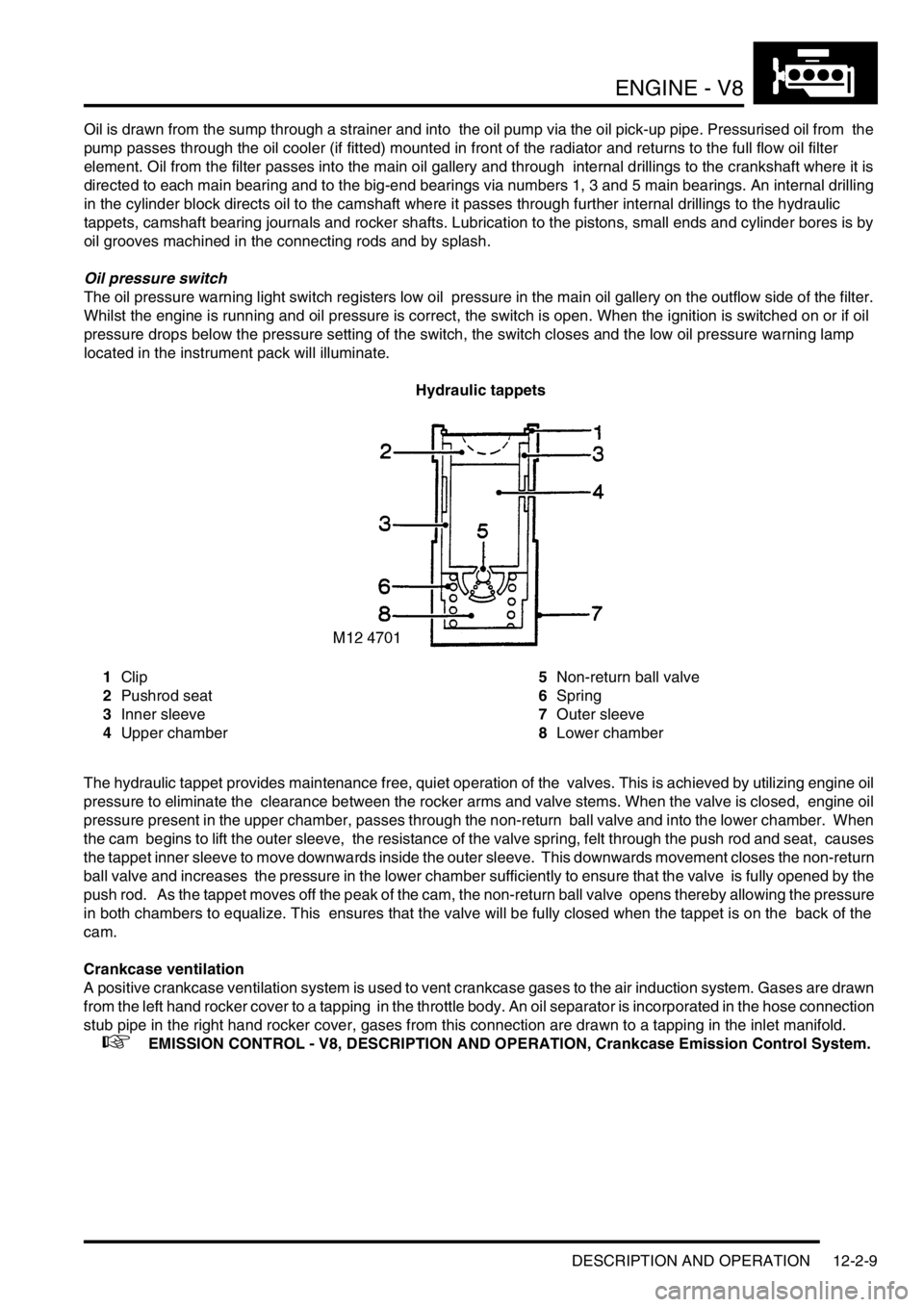
ENGINE - V8
DESCRIPTION AND OPERATION 12-2-9
Oil is drawn from the sump through a strainer and into the oil pump via the oil pick-up pipe. Pressurised oil from the
pump passes through the oil cooler (if fitted) mounted in front of the radiator and returns to the full flow oil filter
element. Oil from the filter passes into the main oil gallery and through internal drillings to the crankshaft where it is
directed to each main bearing and to the big-end bearings via numbers 1, 3 and 5 main bearings. An internal drilling
in the cylinder block directs oil to the camshaft where it passes through further internal drillings to the hydraulic
tappets, camshaft bearing journals and rocker shafts. Lubrication to the pistons, small ends and cylinder bores is by
oil grooves machined in the connecting rods and by splash.
Oil pressure switch
The oil pressure warning light switch registers low oil pressure in the main oil gallery on the outflow side of the filter.
Whilst the engine is running and oil pressure is correct, the switch is open. When the ignition is switched on or if oil
pressure drops below the pressure setting of the switch, the switch closes and the low oil pressure warning lamp
located in the instrument pack will illuminate.
Hydraulic tappets
1Clip
2Pushrod seat
3Inner sleeve
4Upper chamber5Non-return ball valve
6Spring
7Outer sleeve
8Lower chamber
The hydraulic tappet provides maintenance free, quiet operation of the valves. This is achieved by utilizing engine oil
pressure to eliminate the clearance between the rocker arms and valve stems. When the valve is closed, engine oil
pressure present in the upper chamber, passes through the non-return ball valve and into the lower chamber. When
the cam begins to lift the outer sleeve, the resistance of the valve spring, felt through the push rod and seat, causes
the tappet inner sleeve to move downwards inside the outer sleeve. This downwards movement closes the non-return
ball valve and increases the pressure in the lower chamber sufficiently to ensure that the valve is fully opened by the
push rod. As the tappet moves off the peak of the cam, the non-return ball valve opens thereby allowing the pressure
in both chambers to equalize. This ensures that the valve will be fully closed when the tappet is on the back of the
cam.
Crankcase ventilation
A positive crankcase ventilation system is used to vent crankcase gases to the air induction system. Gases are drawn
from the left hand rocker cover to a tapping in the throttle body. An oil separator is incorporated in the hose connection
stub pipe in the right hand rocker cover, gases from this connection are drawn to a tapping in the inlet manifold.
+ EMISSION CONTROL - V8, DESCRIPTION AND OPERATION, Crankcase Emission Control System.
Page 166 of 1529
ENGINE - V8
ADJUSTMENTS 12-2-11
ADJUST ME NTS
Engine oil pressure check
$% 12.90.09.01
Check
1.Remove oil pressure switch.
+ ENGINE - V8, REPAIRS, Switch - oil
pressure.
2.Connect pressure check kit LRT-12-052C
adaptor and gauge to oil pressure switch
position on timing gear cover.
3.Check and if necessary top up engine oil.
4.Run engine at idle speed and check that oil
pressure is within limits given.
+ GENERAL DATA, Engine - V8.
5.Switch off ignition.
6.Remove pressure check kit LRT-12-052C.
7.Clean oil spillage.
8.Fit oil pressure switch.
+ ENGINE - V8, REPAIRS, Switch - oil
pressure.
Adjust
1.If engine oil pressure is below figures given,
check condition of oil pump and/or main and
big end bearings.
Page 168 of 1529
ENGINE - V8
REPAIRS 12-2-13
REPAIRS
Seal - crankshaft - rear
$% 12.21.20
Remove
1. Automatic gearbox models:Remove
converter drive plate.
+ ENGINE - V8, REPAIRS, Plate - drive
- automatic.
2. Manual gearbox models:Remove flywheel.
+ ENGINE - V8, REPAIRS, Flywheel.
3.Carefully remove oil seal from cylinder block to
avoid damage to seal location or running
surface on crankshaft. Discard seal.Refit
1.Ensure both seal location and running surface
on crankshaft are clean.
2.Lubricate replacement oil seal with engine oil.
3.Lubricate seal guide LRT-12-095 with engine
oil, fit seal guide to crankshaft.
4.Fit oil seal squarely onto crankshaft and
remove seal guide LRT-12-095.
5.Fit seal into location using tools LRT-12-091
and LRT-99-003.
6. Automatic gearbox models:Fit converter
drive plate.
+ ENGINE - V8, REPAIRS, Plate - drive
- automatic.
7. Manual gearbox models:Fit flywheel.
+ ENGINE - V8, REPAIRS, Flywheel.
Page 169 of 1529
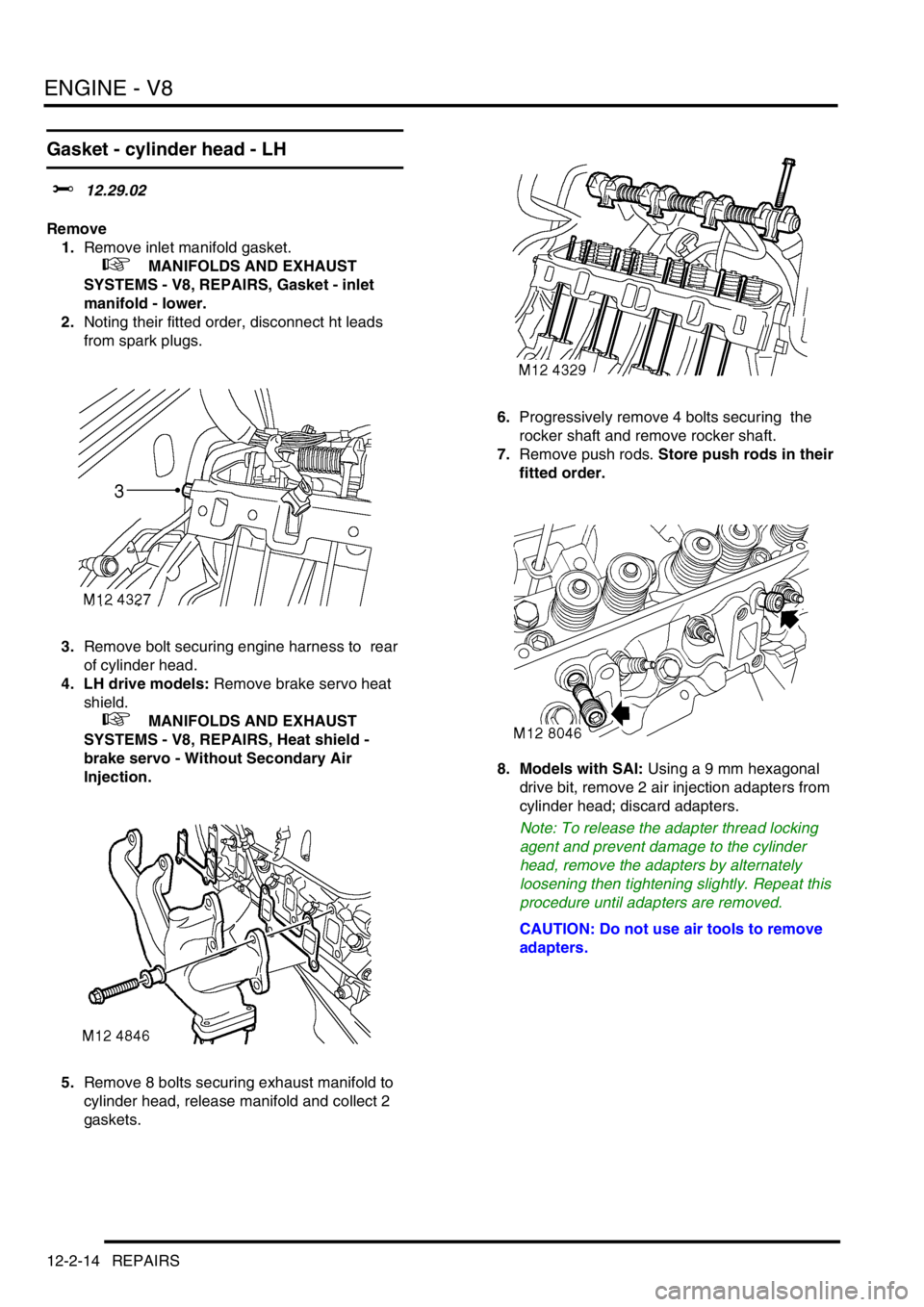
ENGINE - V8
12-2-14 REPAIRS
Gasket - cylinder head - LH
$% 12.29.02
Remove
1.Remove inlet manifold gasket.
+ MANIFOLDS AND EXHAUST
SYSTEMS - V8, REPAIRS, Gasket - inlet
manifold - lower.
2.Noting their fitted order, disconnect ht leads
from spark plugs.
3.Remove bolt securing engine harness to rear
of cylinder head.
4. LH drive models: Remove brake servo heat
shield.
+ MANIFOLDS AND EXHAUST
SYSTEMS - V8, REPAIRS, Heat shield -
brake servo - Without Secondary Air
Injection.
5.Remove 8 bolts securing exhaust manifold to
cylinder head, release manifold and collect 2
gaskets.6.Progressively remove 4 bolts securing the
rocker shaft and remove rocker shaft.
7.Remove push rods. Store push rods in their
fitted order.
8. Models with SAI: Using a 9 mm hexagonal
drive bit, remove 2 air injection adapters from
cylinder head; discard adapters.
Note: To release the adapter thread locking
agent and prevent damage to the cylinder
head, remove the adapters by alternately
loosening then tightening slightly. Repeat this
procedure until adapters are removed.
CAUTION: Do not use air tools to remove
adapters.
Page 170 of 1529
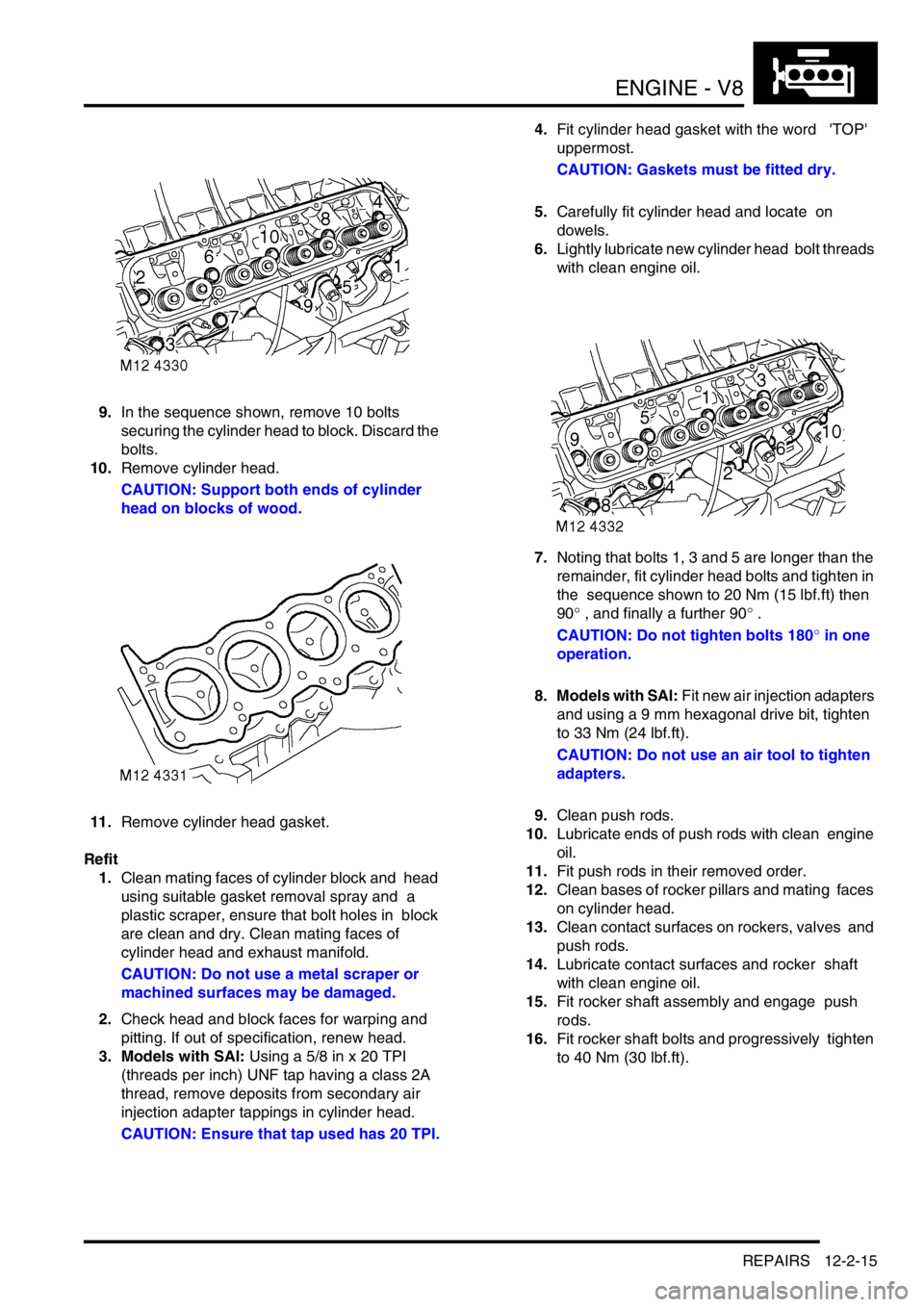
ENGINE - V8
REPAIRS 12-2-15
9.In the sequence shown, remove 10 bolts
securing the cylinder head to block. Discard the
bolts.
10.Remove cylinder head.
CAUTION: Support both ends of cylinder
head on blocks of wood.
11.Remove cylinder head gasket.
Refit
1.Clean mating faces of cylinder block and head
using suitable gasket removal spray and a
plastic scraper, ensure that bolt holes in block
are clean and dry. Clean mating faces of
cylinder head and exhaust manifold.
CAUTION: Do not use a metal scraper or
machined surfaces may be damaged.
2.Check head and block faces for warping and
pitting. If out of specification, renew head.
3. Models with SAI: Using a 5/8 in x 20 TPI
(threads per inch) UNF tap having a class 2A
thread, remove deposits from secondary air
injection adapter tappings in cylinder head.
CAUTION: Ensure that tap used has 20 TPI.4.Fit cylinder head gasket with the word 'TOP'
uppermost.
CAUTION: Gaskets must be fitted dry.
5.Carefully fit cylinder head and locate on
dowels.
6.Lightly lubricate new cylinder head bolt threads
with clean engine oil.
7.Noting that bolts 1, 3 and 5 are longer than the
remainder, fit cylinder head bolts and tighten in
the sequence shown to 20 Nm (15 lbf.ft) then
90° , and finally a further 90° .
CAUTION: Do not tighten bolts 180° in one
operation.
8. Models with SAI: Fit new air injection adapters
and using a 9 mm hexagonal drive bit, tighten
to 33 Nm (24 lbf.ft).
CAUTION: Do not use an air tool to tighten
adapters.
9.Clean push rods.
10.Lubricate ends of push rods with clean engine
oil.
11.Fit push rods in their removed order.
12.Clean bases of rocker pillars and mating faces
on cylinder head.
13.Clean contact surfaces on rockers, valves and
push rods.
14.Lubricate contact surfaces and rocker shaft
with clean engine oil.
15.Fit rocker shaft assembly and engage push
rods.
16.Fit rocker shaft bolts and progressively tighten
to 40 Nm (30 lbf.ft).
Page 171 of 1529
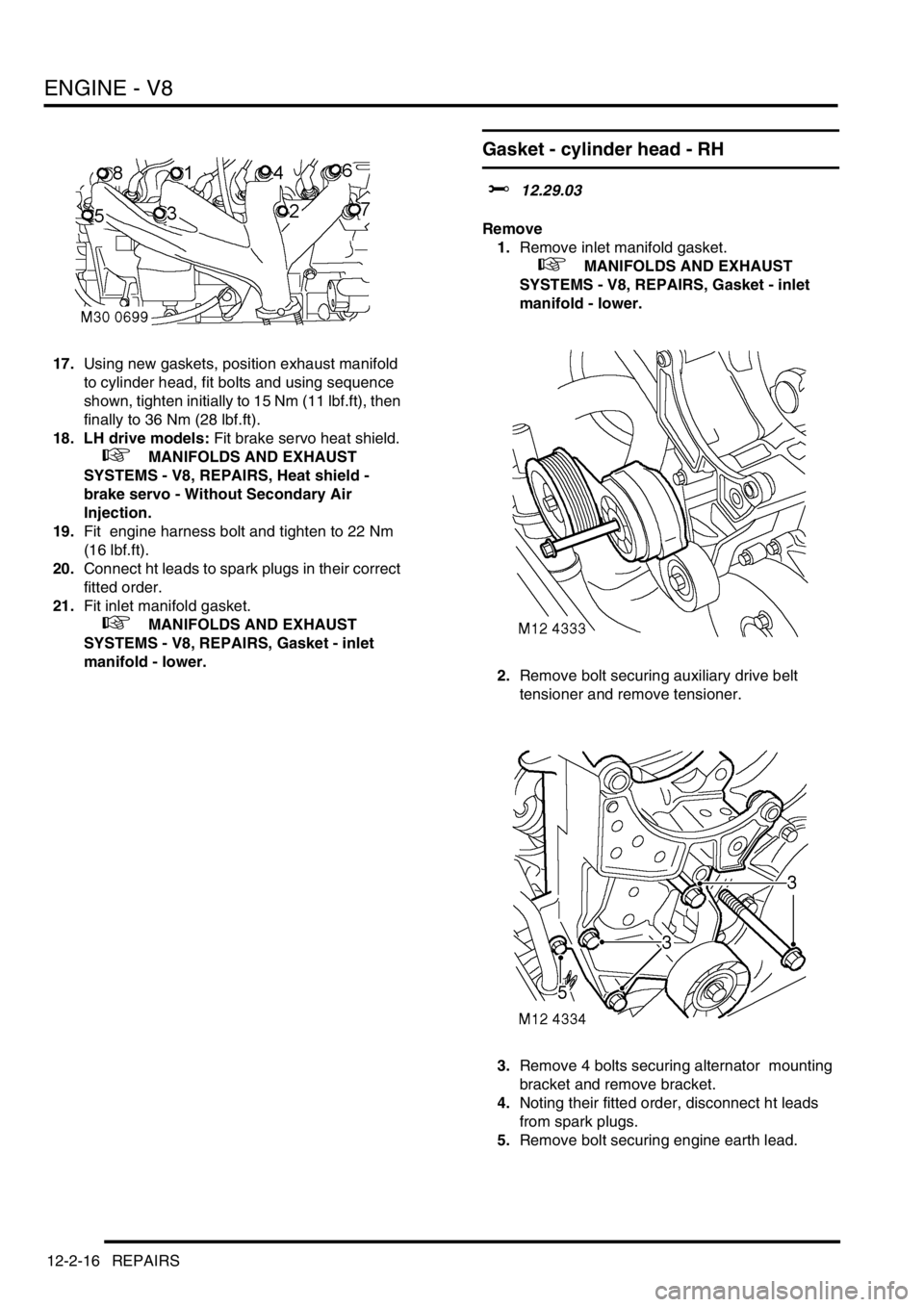
ENGINE - V8
12-2-16 REPAIRS
17.Using new gaskets, position exhaust manifold
to cylinder head, fit bolts and using sequence
shown, tighten initially to 15 Nm (11 lbf.ft), then
finally to 36 Nm (28 lbf.ft).
18. LH drive models: Fit brake servo heat shield.
+ MANIFOLDS AND EXHAUST
SYSTEMS - V8, REPAIRS, Heat shield -
brake servo - Without Secondary Air
Injection.
19.Fit engine harness bolt and tighten to 22 Nm
(16 lbf.ft).
20.Connect ht leads to spark plugs in their correct
fitted order.
21.Fit inlet manifold gasket.
+ MANIFOLDS AND EXHAUST
SYSTEMS - V8, REPAIRS, Gasket - inlet
manifold - lower.
Gasket - cylinder head - RH
$% 12.29.03
Remove
1.Remove inlet manifold gasket.
+ MANIFOLDS AND EXHAUST
SYSTEMS - V8, REPAIRS, Gasket - inlet
manifold - lower.
2.Remove bolt securing auxiliary drive belt
tensioner and remove tensioner.
3.Remove 4 bolts securing alternator mounting
bracket and remove bracket.
4.Noting their fitted order, disconnect ht leads
from spark plugs.
5.Remove bolt securing engine earth lead.