Page 263 of 667
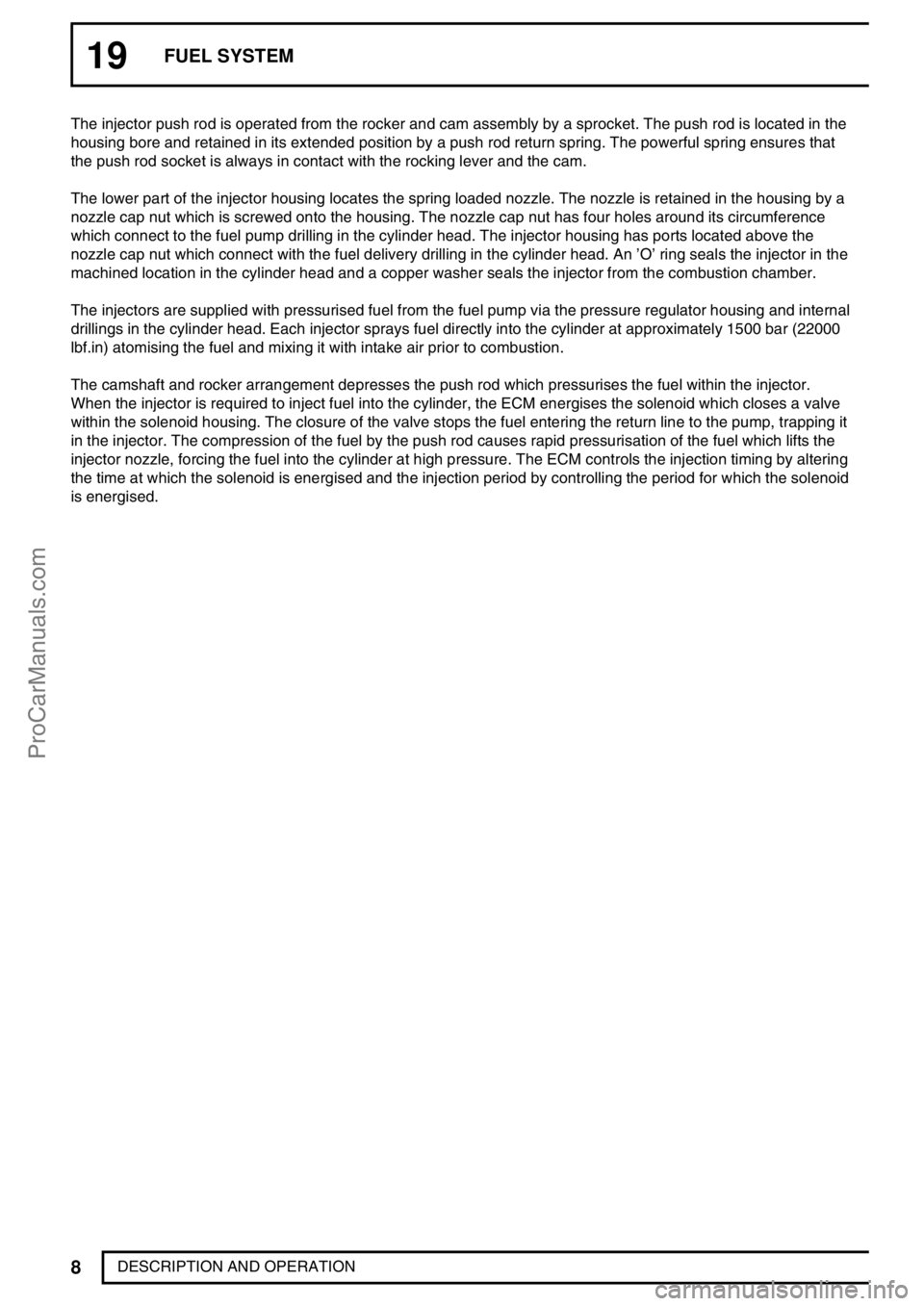
19FUEL SYSTEM
8
DESCRIPTION AND OPERATION The injector push rod is operated from the rocker and cam assembly by a sprocket. The push rod is located in the
housing bore and retained in its extended position by a push rod return spring. The powerful spring ensures that
the push rod socket is always in contact with the rocking lever and the cam.
The lower part of the injector housing locates the spring loaded nozzle. The nozzle is retained in the housing by a
nozzle cap nut which is screwed onto the housing. The nozzle cap nut has four holes around its circumference
which connect to the fuel pump drilling in the cylinder head. The injector housing has ports located above the
nozzle cap nut which connect with the fuel delivery drilling in the cylinder head. An’O’ring seals the injector in the
machined location in the cylinder head and a copper washer seals the injector from the combustion chamber.
The injectors are supplied with pressurised fuel from the fuel pump via the pressure regulator housing and internal
drillings in the cylinder head. Each injector sprays fuel directly into the cylinder at approximately 1500 bar (22000
lbf.in) atomising the fuel and mixing it with intake air prior to combustion.
The camshaft and rocker arrangement depresses the push rod which pressurises the fuel within the injector.
When the injector is required to inject fuel into the cylinder, the ECM energises the solenoid which closes a valve
within the solenoid housing. The closure of the valve stops the fuel entering the return line to the pump, trapping it
in the injector. The compression of the fuel by the push rod causes rapid pressurisation of the fuel which lifts the
injector nozzle, forcing the fuel into the cylinder at high pressure. The ECM controls the injection timing by altering
the time at which the solenoid is energised and the injection period by controlling the period for which the solenoid
is energised.
ProCarManuals.com
Page 264 of 667
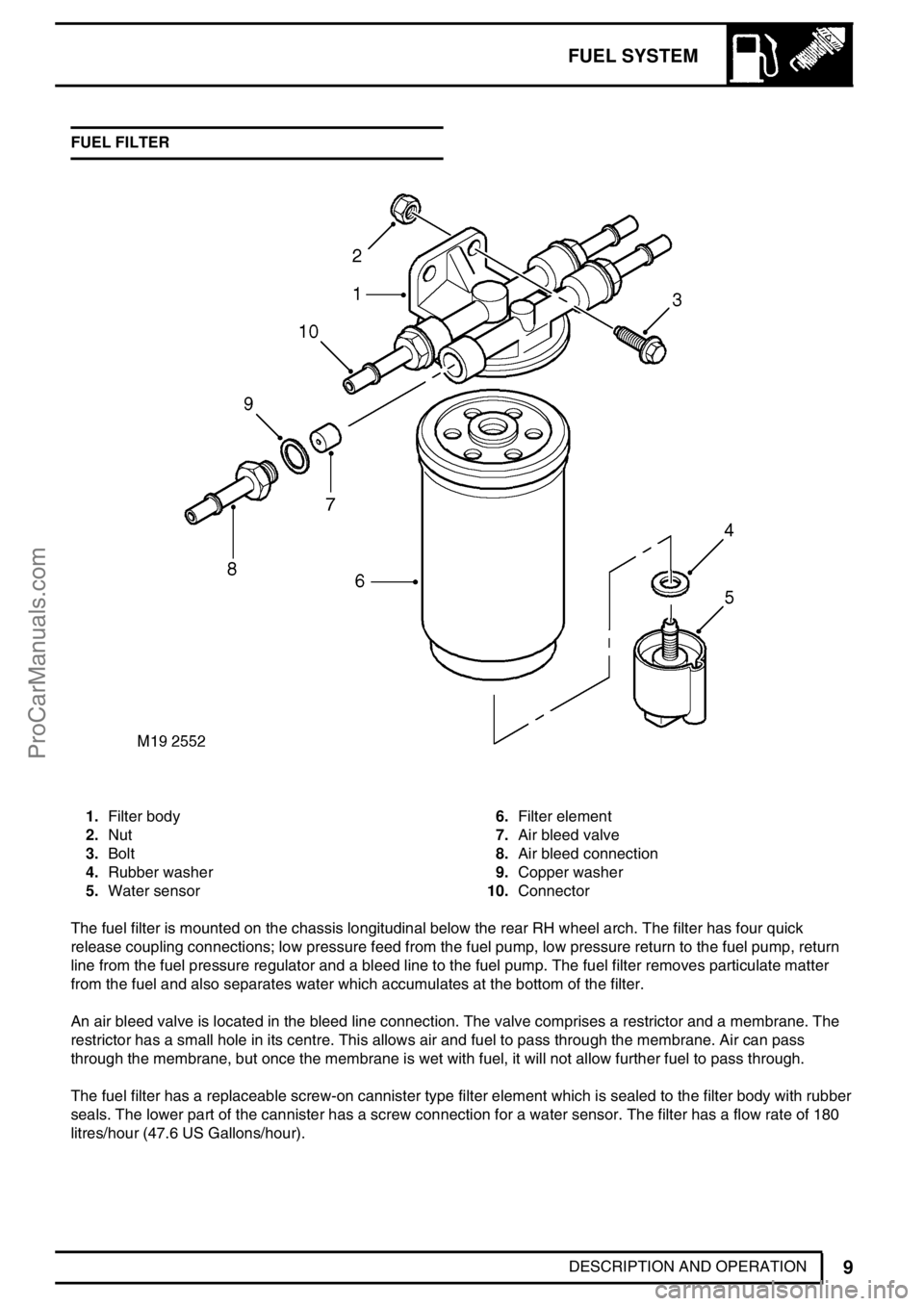
FUEL SYSTEM
9
DESCRIPTION AND OPERATION FUEL FILTER
1.Filter body
2.Nut
3.Bolt
4.Rubber washer
5.Water sensor6.Filter element
7.Air bleed valve
8.Air bleed connection
9.Copper washer
10.Connector
The fuel filter is mounted on the chassis longitudinal below the rear RH wheel arch. The filter has four quick
release coupling connections; low pressure feed from the fuel pump, low pressure return to the fuel pump, return
line from the fuel pressure regulator and a bleed line to the fuel pump. The fuel filter removes particulate matter
from the fuel and also separates water which accumulates at the bottom of the filter.
An air bleed valve is located in the bleed line connection. The valve comprises a restrictor and a membrane. The
restrictor has a small hole in its centre. This allows air and fuel to pass through the membrane. Air can pass
through the membrane, but once the membrane is wet with fuel, it will not allow further fuel to pass through.
The fuel filter has a replaceable screw-on cannister type filter element which is sealed to the filter body with rubber
seals. The lower part of the cannister has a screw connection for a water sensor. The filter has a flow rate of 180
litres/hour (47.6 US Gallons/hour).
ProCarManuals.com
Page 270 of 667
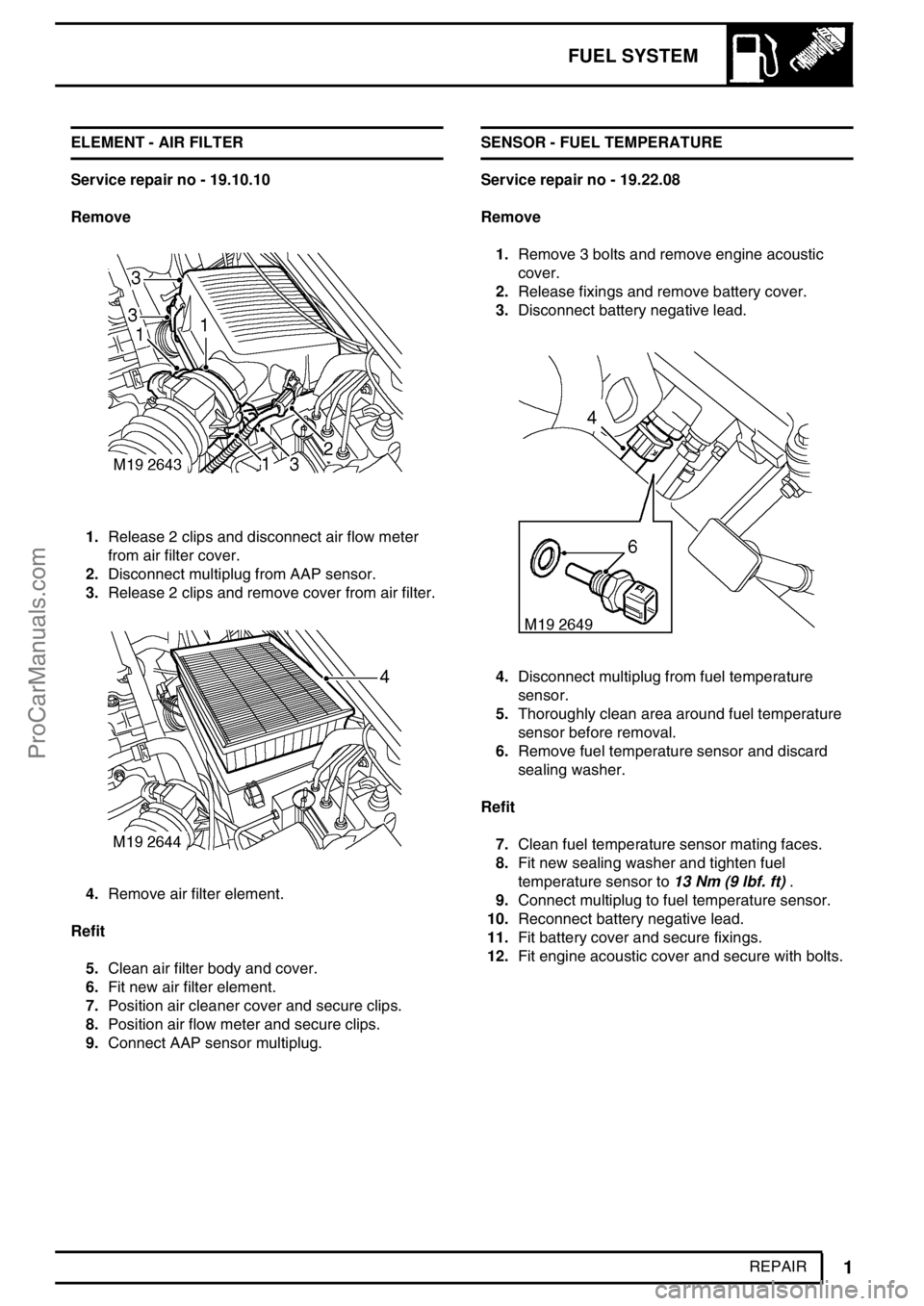
FUEL SYSTEM
1
REPAIR ELEMENT - AIR FILTER
Service repair no - 19.10.10
Remove
1.Release 2 clips and disconnect air flow meter
from air filter cover.
2.Disconnect multiplug from AAP sensor.
3.Release 2 clips and remove cover from air filter.
4.Remove air filter element.
Refit
5.Clean air filter body and cover.
6.Fit new air filter element.
7.Position air cleaner cover and secure clips.
8.Position air flow meter and secure clips.
9.Connect AAP sensor multiplug.SENSOR - FUEL TEMPERATURE
Service repair no - 19.22.08
Remove
1.Remove 3 bolts and remove engine acoustic
cover.
2.Release fixings and remove battery cover.
3.Disconnect battery negative lead.
4.Disconnect multiplug from fuel temperature
sensor.
5.Thoroughly clean area around fuel temperature
sensor before removal.
6.Remove fuel temperature sensor and discard
sealing washer.
Refit
7.Clean fuel temperature sensor mating faces.
8.Fit new sealing washer and tighten fuel
temperature sensor to13 Nm (9 lbf. ft).
9.Connect multiplug to fuel temperature sensor.
10.Reconnect battery negative lead.
11.Fit battery cover and secure fixings.
12.Fit engine acoustic cover and secure with bolts.
ProCarManuals.com
Page 274 of 667
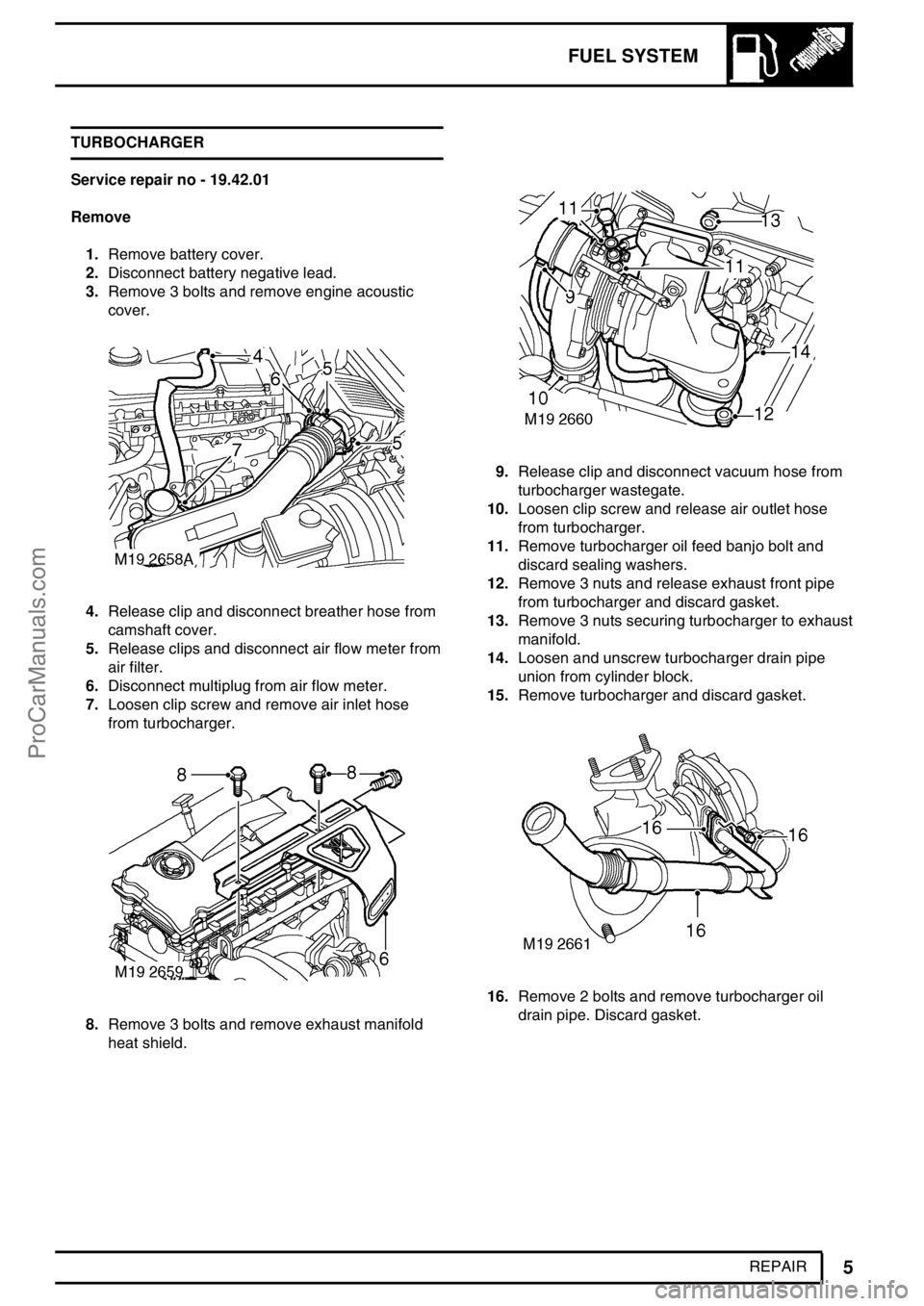
FUEL SYSTEM
5
REPAIR TURBOCHARGER
Service repair no - 19.42.01
Remove
1.Remove battery cover.
2.Disconnect battery negative lead.
3.Remove 3 bolts and remove engine acoustic
cover.
4.Release clip and disconnect breather hose from
camshaft cover.
5.Release clips and disconnect air flow meter from
air filter.
6.Disconnect multiplug from air flow meter.
7.Loosen clip screw and remove air inlet hose
from turbocharger.
8.Remove 3 bolts and remove exhaust manifold
heat shield.
9.Release clip and disconnect vacuum hose from
turbocharger wastegate.
10.Loosen clip screw and release air outlet hose
from turbocharger.
11.Remove turbocharger oil feed banjo bolt and
discard sealing washers.
12.Remove 3 nuts and release exhaust front pipe
from turbocharger and discard gasket.
13.Remove 3 nuts securing turbocharger to exhaust
manifold.
14.Loosen and unscrew turbocharger drain pipe
union from cylinder block.
15.Remove turbocharger and discard gasket.
16.Remove 2 bolts and remove turbocharger oil
drain pipe. Discard gasket.
ProCarManuals.com
Page 275 of 667
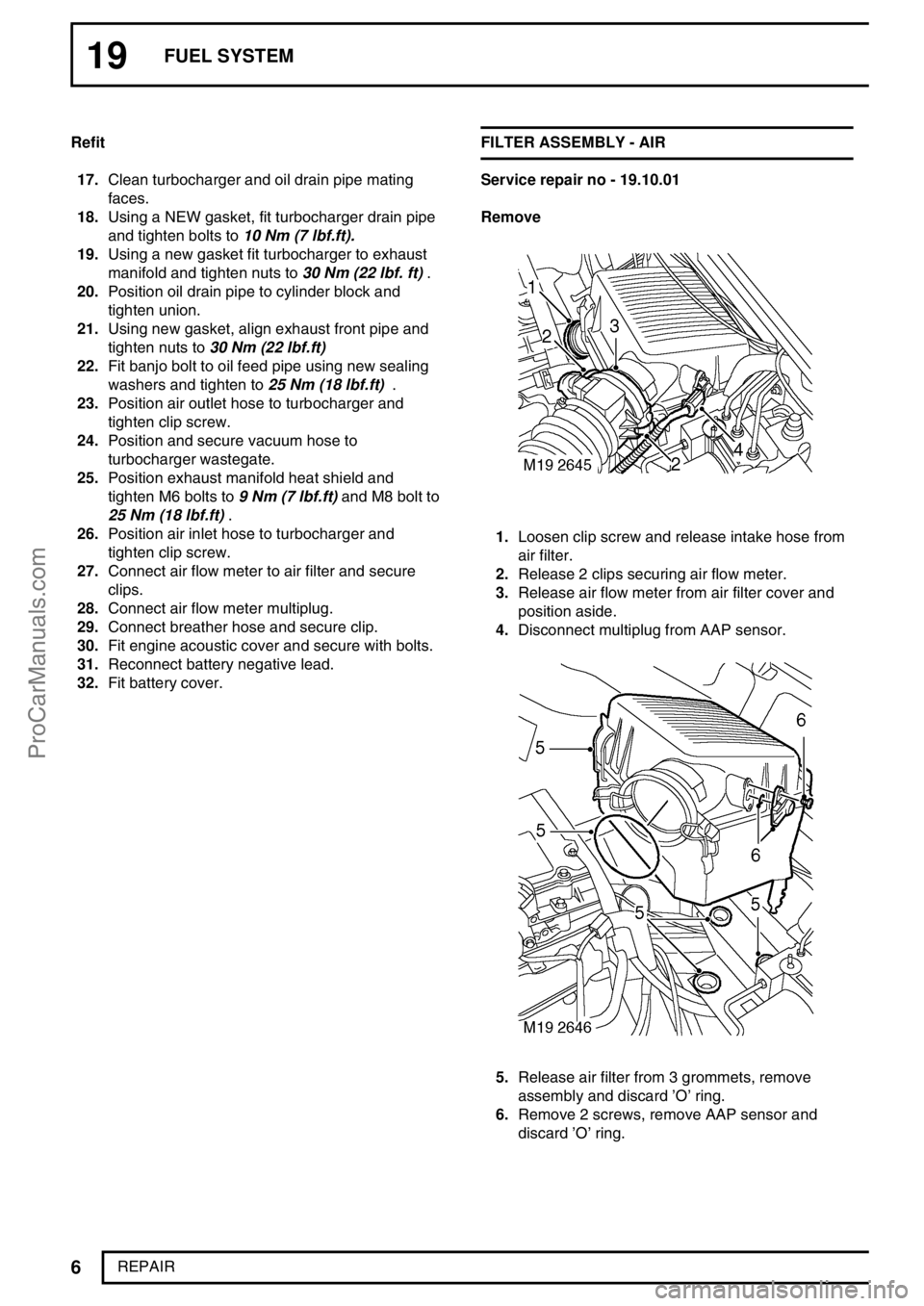
19FUEL SYSTEM
6
REPAIR Refit
17.Clean turbocharger and oil drain pipe mating
faces.
18.Using a NEW gasket, fit turbocharger drain pipe
and tighten bolts to10 Nm (7 lbf.ft).
19.Using a new gasket fit turbocharger to exhaust
manifold and tighten nuts to30 Nm (22 lbf. ft).
20.Position oil drain pipe to cylinder block and
tighten union.
21.Using new gasket, align exhaust front pipe and
tighten nuts to30 Nm (22 lbf.ft)
22.Fit banjo bolt to oil feed pipe using new sealing
washers and tighten to25 Nm (18 lbf.ft).
23.Position air outlet hose to turbocharger and
tighten clip screw.
24.Position and secure vacuum hose to
turbocharger wastegate.
25.Position exhaust manifold heat shield and
tighten M6 bolts to9 Nm (7 lbf.ft)and M8 bolt to
25 Nm (18 lbf.ft).
26.Position air inlet hose to turbocharger and
tighten clip screw.
27.Connect air flow meter to air filter and secure
clips.
28.Connect air flow meter multiplug.
29.Connect breather hose and secure clip.
30.Fit engine acoustic cover and secure with bolts.
31.Reconnect battery negative lead.
32.Fit battery cover.FILTER ASSEMBLY - AIR
Service repair no - 19.10.01
Remove
1.Loosen clip screw and release intake hose from
air filter.
2.Release 2 clips securing air flow meter.
3.Release air flow meter from air filter cover and
position aside.
4.Disconnect multiplug from AAP sensor.
5.Release air filter from 3 grommets, remove
assembly and discard’O’ring.
6.Remove 2 screws, remove AAP sensor and
discard’O’ring.
ProCarManuals.com
Page 277 of 667
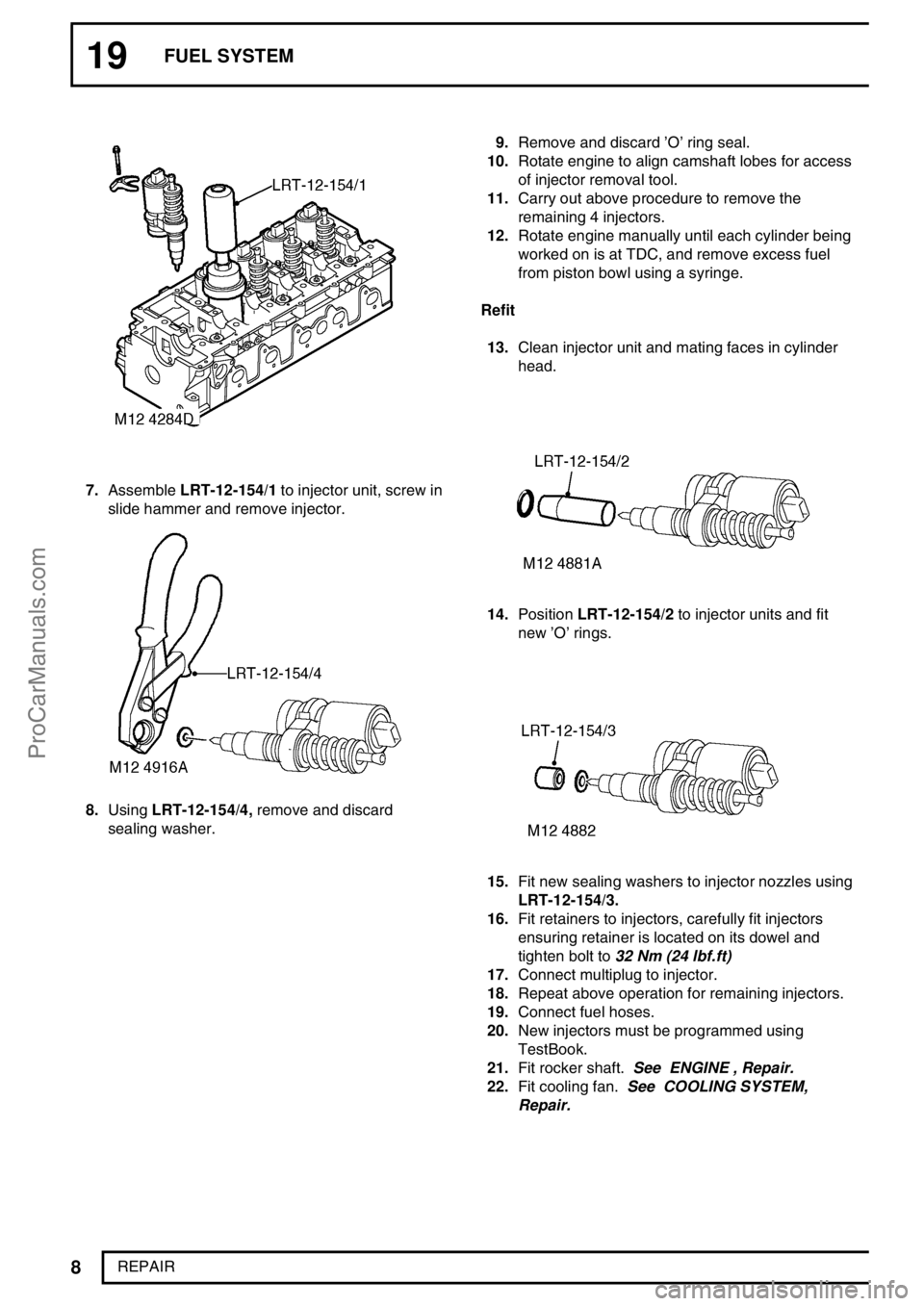
19FUEL SYSTEM
8
REPAIR
7.AssembleLRT-12-154/1to injector unit, screw in
slide hammer and remove injector.
8.UsingLRT-12-154/4,remove and discard
sealing washer.9.Remove and discard’O’ring seal.
10.Rotate engine to align camshaft lobes for access
of injector removal tool.
11.Carry out above procedure to remove the
remaining 4 injectors.
12.Rotate engine manually until each cylinder being
worked on is at TDC, and remove excess fuel
from piston bowl using a syringe.
Refit
13.Clean injector unit and mating faces in cylinder
head.
14.PositionLRT-12-154/2to injector units and fit
new’O’rings.
15.Fit new sealing washers to injector nozzles using
LRT-12-154/3.
16.Fit retainers to injectors, carefully fit injectors
ensuring retainer is located on its dowel and
tighten bolt to32 Nm (24 lbf.ft)
17.Connect multiplug to injector.
18.Repeat above operation for remaining injectors.
19.Connect fuel hoses.
20.New injectors must be programmed using
TestBook.
21.Fit rocker shaft.See ENGINE , Repair.
22.Fit cooling fan.See COOLING SYSTEM,
Repair.
ProCarManuals.com
Page 280 of 667
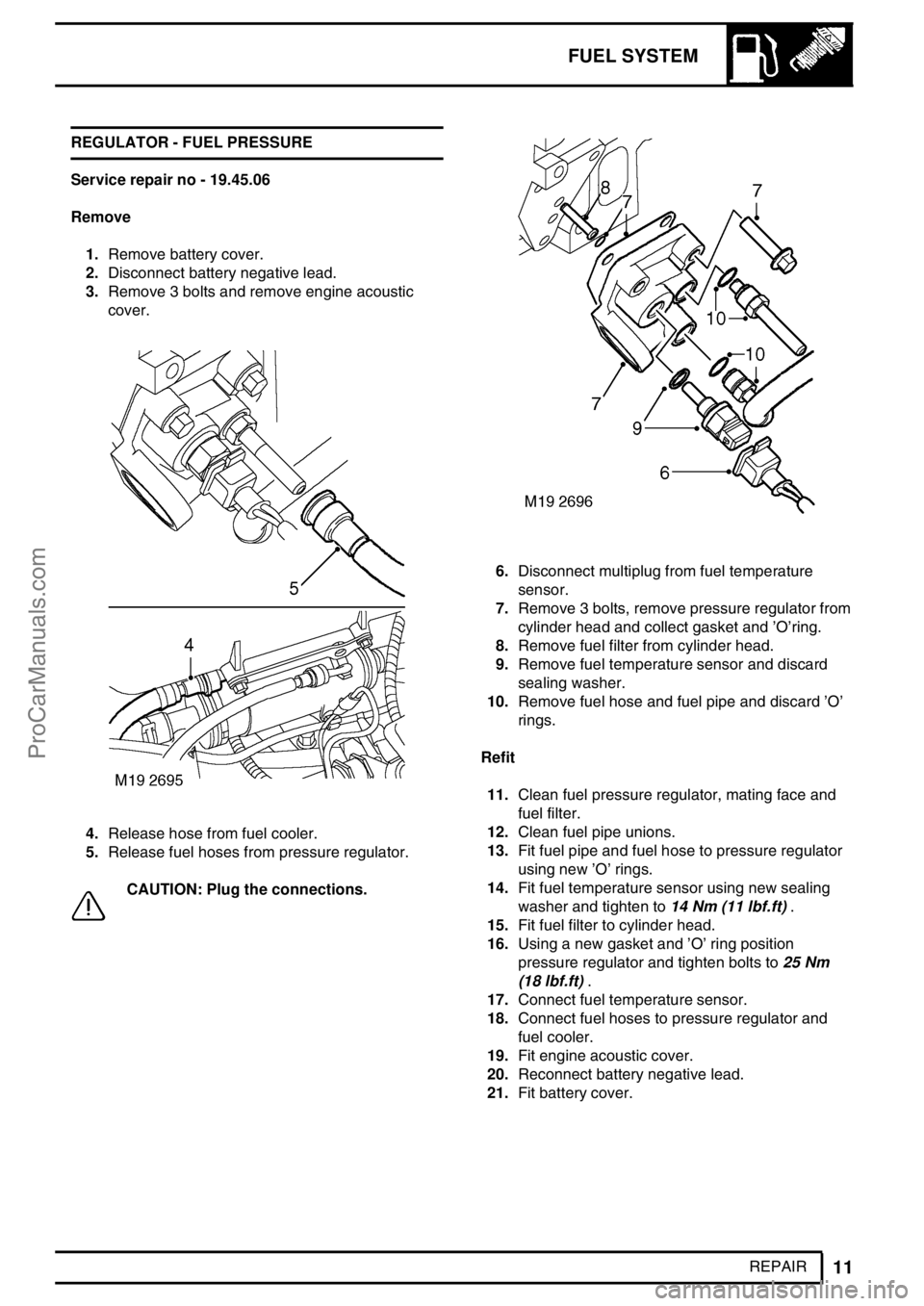
FUEL SYSTEM
11
REPAIR REGULATOR - FUEL PRESSURE
Service repair no - 19.45.06
Remove
1.Remove battery cover.
2.Disconnect battery negative lead.
3.Remove 3 bolts and remove engine acoustic
cover.
4.Release hose from fuel cooler.
5.Release fuel hoses from pressure regulator.
CAUTION: Plug the connections.
6.Disconnect multiplug from fuel temperature
sensor.
7.Remove 3 bolts, remove pressure regulator from
cylinder head and collect gasket and’O’ring.
8.Remove fuel filter from cylinder head.
9.Remove fuel temperature sensor and discard
sealing washer.
10.Remove fuel hose and fuel pipe and discard’O’
rings.
Refit
11.Clean fuel pressure regulator, mating face and
fuel filter.
12.Clean fuel pipe unions.
13.Fit fuel pipe and fuel hose to pressure regulator
using new’O’rings.
14.Fit fuel temperature sensor using new sealing
washer and tighten to14 Nm (11 lbf.ft).
15.Fit fuel filter to cylinder head.
16.Using a new gasket and’O’ring position
pressure regulator and tighten bolts to25 Nm
(18 lbf.ft).
17.Connect fuel temperature sensor.
18.Connect fuel hoses to pressure regulator and
fuel cooler.
19.Fit engine acoustic cover.
20.Reconnect battery negative lead.
21.Fit battery cover.
ProCarManuals.com
Page 326 of 667
CLUTCH
3
DESCRIPTION AND OPERATION 1.Brake/clutch reservoir
2.Connecting hose
3.Bolt - 2 off
4.Master cylinder
5.Clutch pedal
6.Gearbox housing
7.Primary driveshaft
8.Bolt - 2 off
9.Slave cylinder
10.Bleed nipple
11.Pressure plate
12.Drive plate
13.Dual mass flywheel
14.Metal hydraulic pipe
15.Ball spigot
16.Clutch release bearing sleeve
17.Bolt - 2 off
18.Pivot washer
19.Release lever
20.Release bearing
21.Retaining clip
22.Bolt
23.Plastic hydraulic pipe
ProCarManuals.com