Page 335 of 667
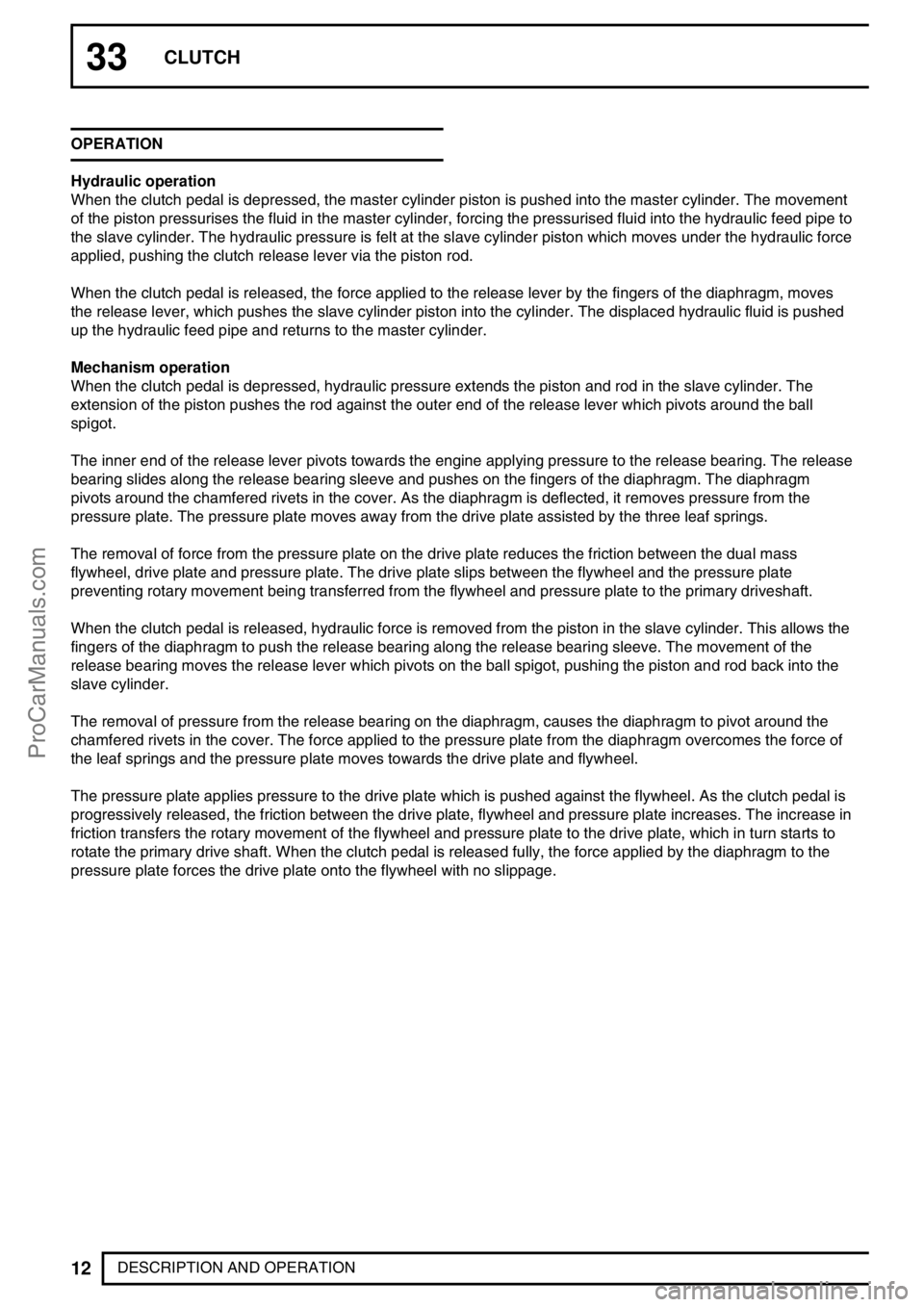
33CLUTCH
12
DESCRIPTION AND OPERATION OPERATION
Hydraulic operation
When the clutch pedal is depressed, the master cylinder piston is pushed into the master cylinder. The movement
of the piston pressurises the fluid in the master cylinder, forcing the pressurised fluid into the hydraulic feed pipe to
the slave cylinder. The hydraulic pressure is felt at the slave cylinder piston which moves under the hydraulic force
applied, pushing the clutch release lever via the piston rod.
When the clutch pedal is released, the force applied to the release lever by the fingers of the diaphragm, moves
the release lever, which pushes the slave cylinder piston into the cylinder. The displaced hydraulic fluid is pushed
up the hydraulic feed pipe and returns to the master cylinder.
Mechanism operation
When the clutch pedal is depressed, hydraulic pressure extends the piston and rod in the slave cylinder. The
extension of the piston pushes the rod against the outer end of the release lever which pivots around the ball
spigot.
The inner end of the release lever pivots towards the engine applying pressure to the release bearing. The release
bearing slides along the release bearing sleeve and pushes on the fingers of the diaphragm. The diaphragm
pivots around the chamfered rivets in the cover. As the diaphragm is deflected, it removes pressure from the
pressure plate. The pressure plate moves away from the drive plate assisted by the three leaf springs.
The removal of force from the pressure plate on the drive plate reduces the friction between the dual mass
flywheel, drive plate and pressure plate. The drive plate slips between the flywheel and the pressure plate
preventing rotary movement being transferred from the flywheel and pressure plate to the primary driveshaft.
When the clutch pedal is released, hydraulic force is removed from the piston in the slave cylinder. This allows the
fingers of the diaphragm to push the release bearing along the release bearing sleeve. The movement of the
release bearing moves the release lever which pivots on the ball spigot, pushing the piston and rod back into the
slave cylinder.
The removal of pressure from the release bearing on the diaphragm, causes the diaphragm to pivot around the
chamfered rivets in the cover. The force applied to the pressure plate from the diaphragm overcomes the force of
the leaf springs and the pressure plate moves towards the drive plate and flywheel.
The pressure plate applies pressure to the drive plate which is pushed against the flywheel. As the clutch pedal is
progressively released, the friction between the drive plate, flywheel and pressure plate increases. The increase in
friction transfers the rotary movement of the flywheel and pressure plate to the drive plate, which in turn starts to
rotate the primary drive shaft. When the clutch pedal is released fully, the force applied by the diaphragm to the
pressure plate forces the drive plate onto the flywheel with no slippage.
ProCarManuals.com
Page 338 of 667
CLUTCH
1
REPAIR CLUTCH ASSEMBLY
Service repair no - 33.10.01.01
Remove
1.Remove gearbox assembly.See MANUAL
GEARBOX, Repair.
2.Restrain flywheel.
3.Working in sequence, loosen 6 nuts securing
clutch cover to flywheel.
4.Remove clutch cover and clutch plate.
Refit
5.Clean clutch cover and flywheel mating faces
and spigot bush in end of crankshaft.
6.Position clutch drive plate to flywheel with
’gearbox side’ facing towards gearbox.
7.PositionLRT-12-152alignment tool through
drive plate into spigot bearing in crankshaft.8.Fit clutch cover and locate on dowels.
9.Position clutch cover nuts and tighten in diagonal
sequence to25 Nm (18 lbf.ft).
10.Fit gearbox assembly.See MANUAL
GEARBOX, Repair.
ProCarManuals.com
Page 368 of 667
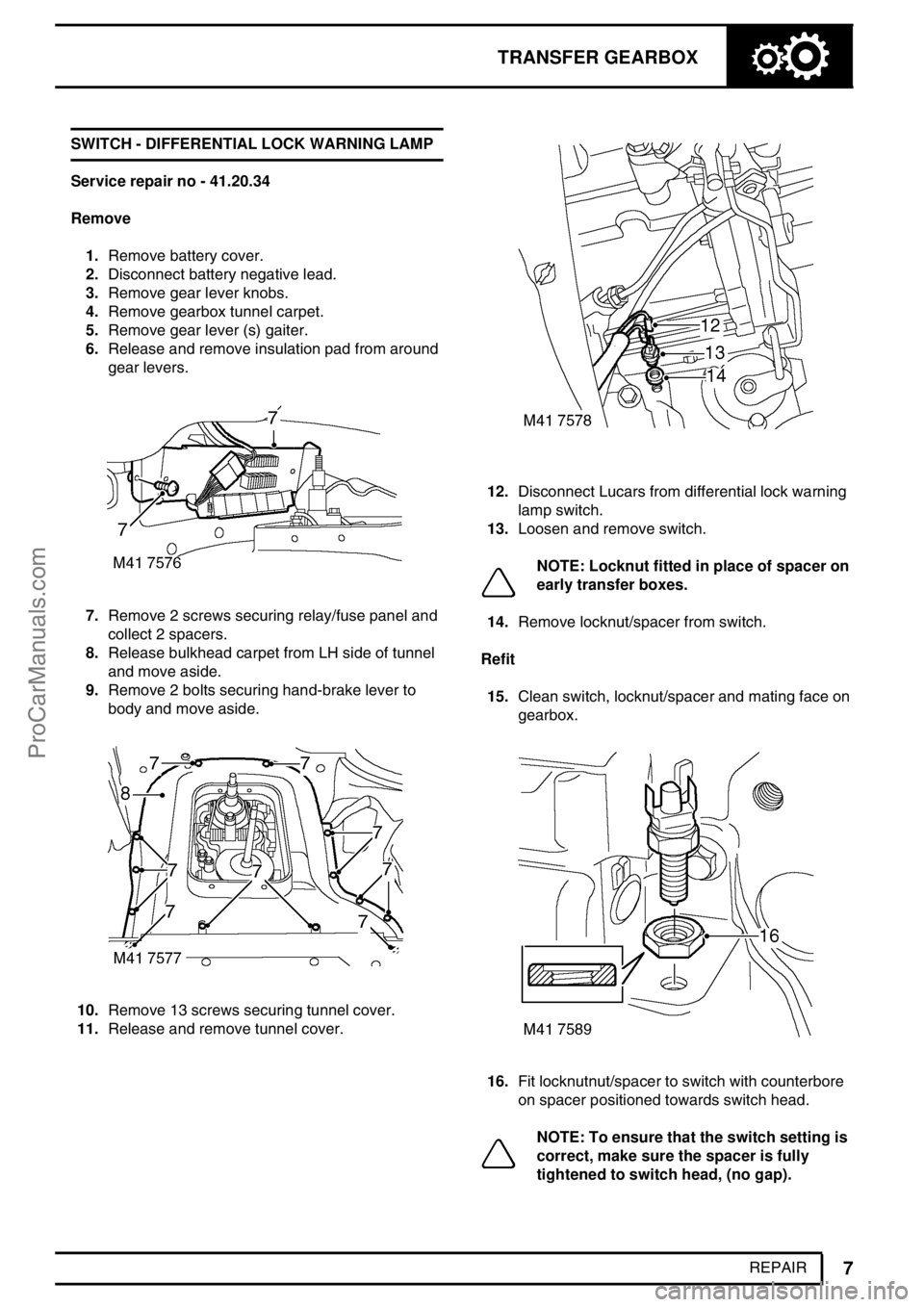
TRANSFER GEARBOX
7
REPAIR SWITCH - DIFFERENTIAL LOCK WARNING LAMP
Service repair no - 41.20.34
Remove
1.Remove battery cover.
2.Disconnect battery negative lead.
3.Remove gear lever knobs.
4.Remove gearbox tunnel carpet.
5.Remove gear lever (s) gaiter.
6.Release and remove insulation pad from around
gear levers.
7.Remove 2 screws securing relay/fuse panel and
collect 2 spacers.
8.Release bulkhead carpet from LH side of tunnel
and move aside.
9.Remove 2 bolts securing hand-brake lever to
body and move aside.
10.Remove 13 screws securing tunnel cover.
11.Release and remove tunnel cover.
12.Disconnect Lucars from differential lock warning
lamp switch.
13.Loosen and remove switch.
NOTE: Locknut fitted in place of spacer on
early transfer boxes.
14.Remove locknut/spacer from switch.
Refit
15.Clean switch, locknut/spacer and mating face on
gearbox.
16.Fit locknutnut/spacer to switch with counterbore
on spacer positioned towards switch head.
NOTE: To ensure that the switch setting is
correct, make sure the spacer is fully
tightened to switch head, (no gap).
ProCarManuals.com
Page 374 of 667
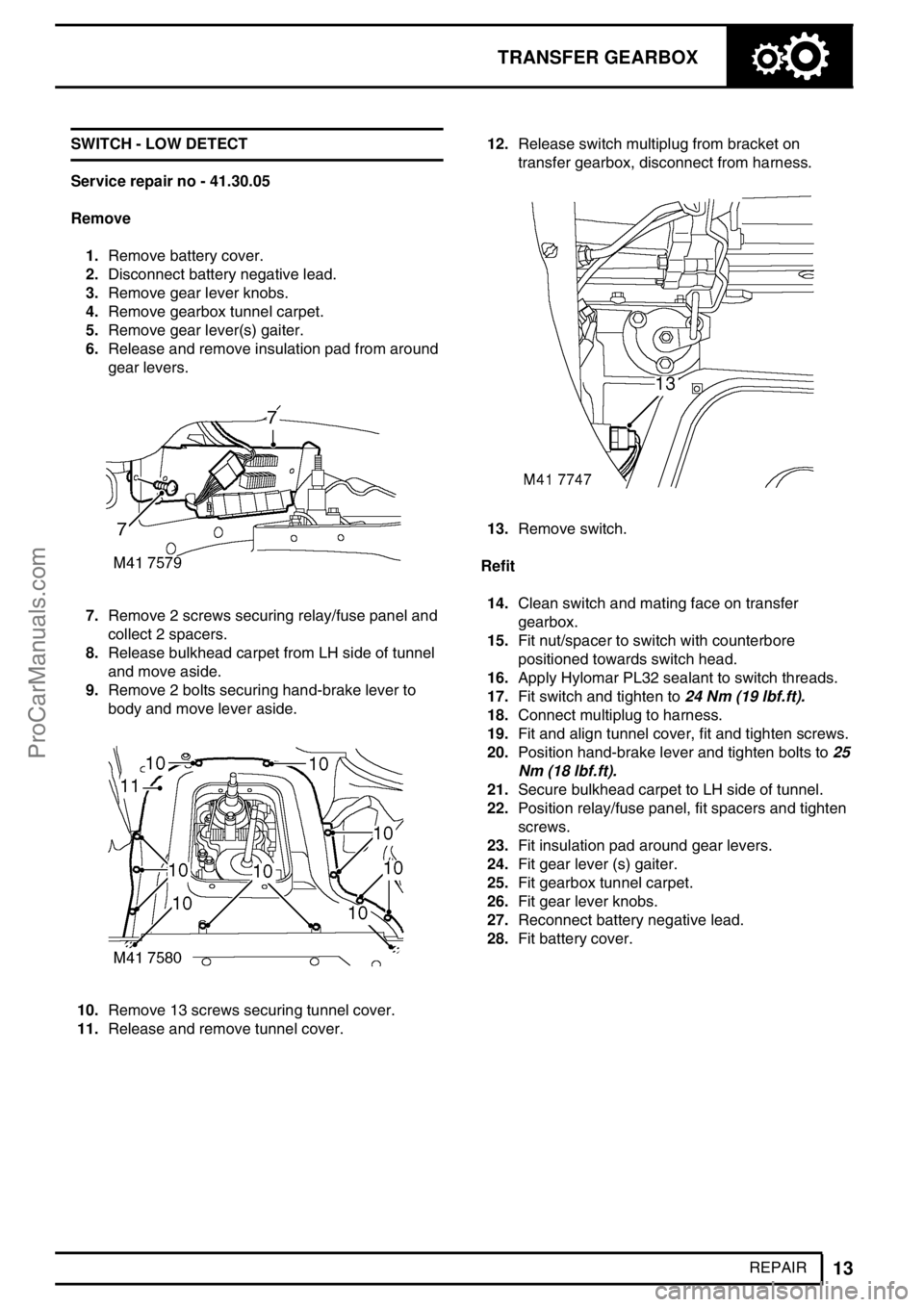
TRANSFER GEARBOX
13
REPAIR SWITCH - LOW DETECT
Service repair no - 41.30.05
Remove
1.Remove battery cover.
2.Disconnect battery negative lead.
3.Remove gear lever knobs.
4.Remove gearbox tunnel carpet.
5.Remove gear lever(s) gaiter.
6.Release and remove insulation pad from around
gear levers.
7.Remove 2 screws securing relay/fuse panel and
collect 2 spacers.
8.Release bulkhead carpet from LH side of tunnel
and move aside.
9.Remove 2 bolts securing hand-brake lever to
body and move lever aside.
10.Remove 13 screws securing tunnel cover.
11.Release and remove tunnel cover.12.Release switch multiplug from bracket on
transfer gearbox, disconnect from harness.
13.Remove switch.
Refit
14.Clean switch and mating face on transfer
gearbox.
15.Fit nut/spacer to switch with counterbore
positioned towards switch head.
16.Apply Hylomar PL32 sealant to switch threads.
17.Fit switch and tighten to24 Nm (19 lbf.ft).
18.Connect multiplug to harness.
19.Fit and align tunnel cover, fit and tighten screws.
20.Position hand-brake lever and tighten bolts to25
Nm (18 lbf.ft).
21.Secure bulkhead carpet to LH side of tunnel.
22.Position relay/fuse panel, fit spacers and tighten
screws.
23.Fit insulation pad around gear levers.
24.Fit gear lever (s) gaiter.
25.Fit gearbox tunnel carpet.
26.Fit gear lever knobs.
27.Reconnect battery negative lead.
28.Fit battery cover.
ProCarManuals.com
Page 532 of 667
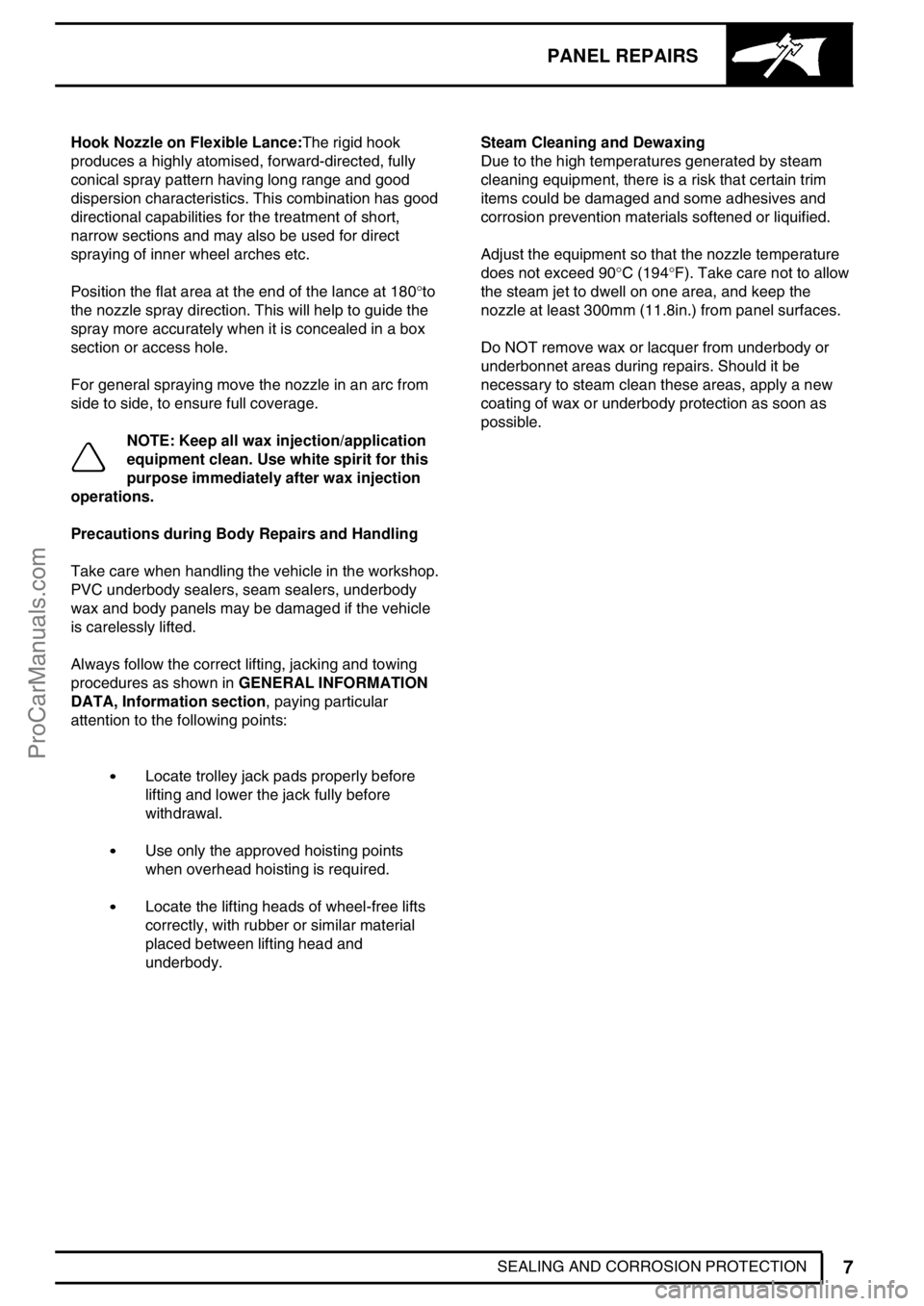
PANEL REPAIRS
7
SEALING AND CORROSION PROTECTION Hook Nozzle on Flexible Lance:The rigid hook
produces a highly atomised, forward-directed, fully
conical spray pattern having long range and good
dispersion characteristics. This combination has good
directional capabilities for the treatment of short,
narrow sections and may also be used for direct
spraying of inner wheel arches etc.
Position the flat area at the end of the lance at 180°to
the nozzle spray direction. This will help to guide the
spray more accurately when it is concealed in a box
section or access hole.
For general spraying move the nozzle in an arc from
side to side, to ensure full coverage.
NOTE: Keep all wax injection/application
equipment clean. Use white spirit for this
purpose immediately after wax injection
operations.
Precautions during Body Repairs and Handling
Take care when handling the vehicle in the workshop.
PVC underbody sealers, seam sealers, underbody
wax and body panels may be damaged if the vehicle
is carelessly lifted.
Always follow the correct lifting, jacking and towing
procedures as shown inGENERAL INFORMATION
DATA, Information section, paying particular
attention to the following points:
Locate trolley jack pads properly before
lifting and lower the jack fully before
withdrawal.
Use only the approved hoisting points
when overhead hoisting is required.
Locate the lifting heads of wheel-free lifts
correctly, with rubber or similar material
placed between lifting head and
underbody.Steam Cleaning and Dewaxing
Due to the high temperatures generated by steam
cleaning equipment, there is a risk that certain trim
items could be damaged and some adhesives and
corrosion prevention materials softened or liquified.
Adjust the equipment so that the nozzle temperature
does not exceed 90°C (194°F). Take care not to allow
the steam jet to dwell on one area, and keep the
nozzle at least 300mm (11.8in.) from panel surfaces.
Do NOT remove wax or lacquer from underbody or
underbonnet areas during repairs. Should it be
necessary to steam clean these areas, apply a new
coating of wax or underbody protection as soon as
possible.
ProCarManuals.com
Page:
< prev 1-8 9-16 17-24