Page 581 of 667
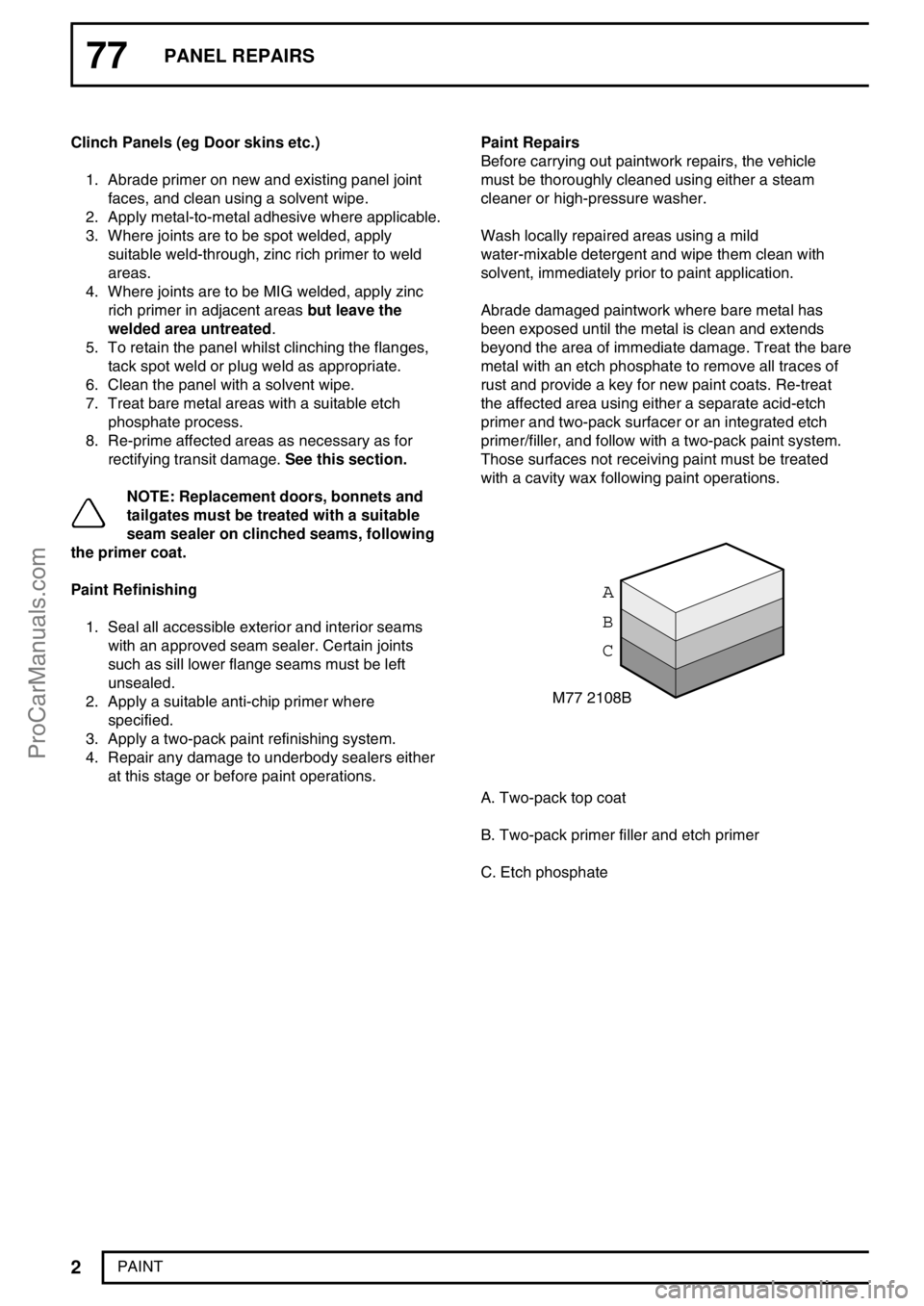
77PANEL REPAIRS
2
PAINT Clinch Panels (eg Door skins etc.)
1. Abrade primer on new and existing panel joint
faces, and clean using a solvent wipe.
2. Apply metal-to-metal adhesive where applicable.
3. Where joints are to be spot welded, apply
suitable weld-through, zinc rich primer to weld
areas.
4. Where joints are to be MIG welded, apply zinc
rich primer in adjacent areasbut leave the
welded area untreated.
5. To retain the panel whilst clinching the flanges,
tack spot weld or plug weld as appropriate.
6. Clean the panel with a solvent wipe.
7. Treat bare metal areas with a suitable etch
phosphate process.
8. Re-prime affected areas as necessary as for
rectifying transit damage.See this section.
NOTE: Replacement doors, bonnets and
tailgates must be treated with a suitable
seam sealer on clinched seams, following
the primer coat.
Paint Refinishing
1. Seal all accessible exterior and interior seams
with an approved seam sealer. Certain joints
such as sill lower flange seams must be left
unsealed.
2. Apply a suitable anti-chip primer where
specified.
3. Apply a two-pack paint refinishing system.
4. Repair any damage to underbody sealers either
at this stage or before paint operations.Paint Repairs
Before carrying out paintwork repairs, the vehicle
must be thoroughly cleaned using either a steam
cleaner or high-pressure washer.
Wash locally repaired areas using a mild
water-mixable detergent and wipe them clean with
solvent, immediately prior to paint application.
Abrade damaged paintwork where bare metal has
been exposed until the metal is clean and extends
beyond the area of immediate damage. Treat the bare
metal with an etch phosphate to remove all traces of
rust and provide a key for new paint coats. Re-treat
the affected area using either a separate acid-etch
primer and two-pack surfacer or an integrated etch
primer/filler, and follow with a two-pack paint system.
Those surfaces not receiving paint must be treated
with a cavity wax following paint operations.
M77 2108B
A
B
C
A. Two-pack top coat
B. Two-pack primer filler and etch primer
C. Etch phosphate
ProCarManuals.com
Page 592 of 667
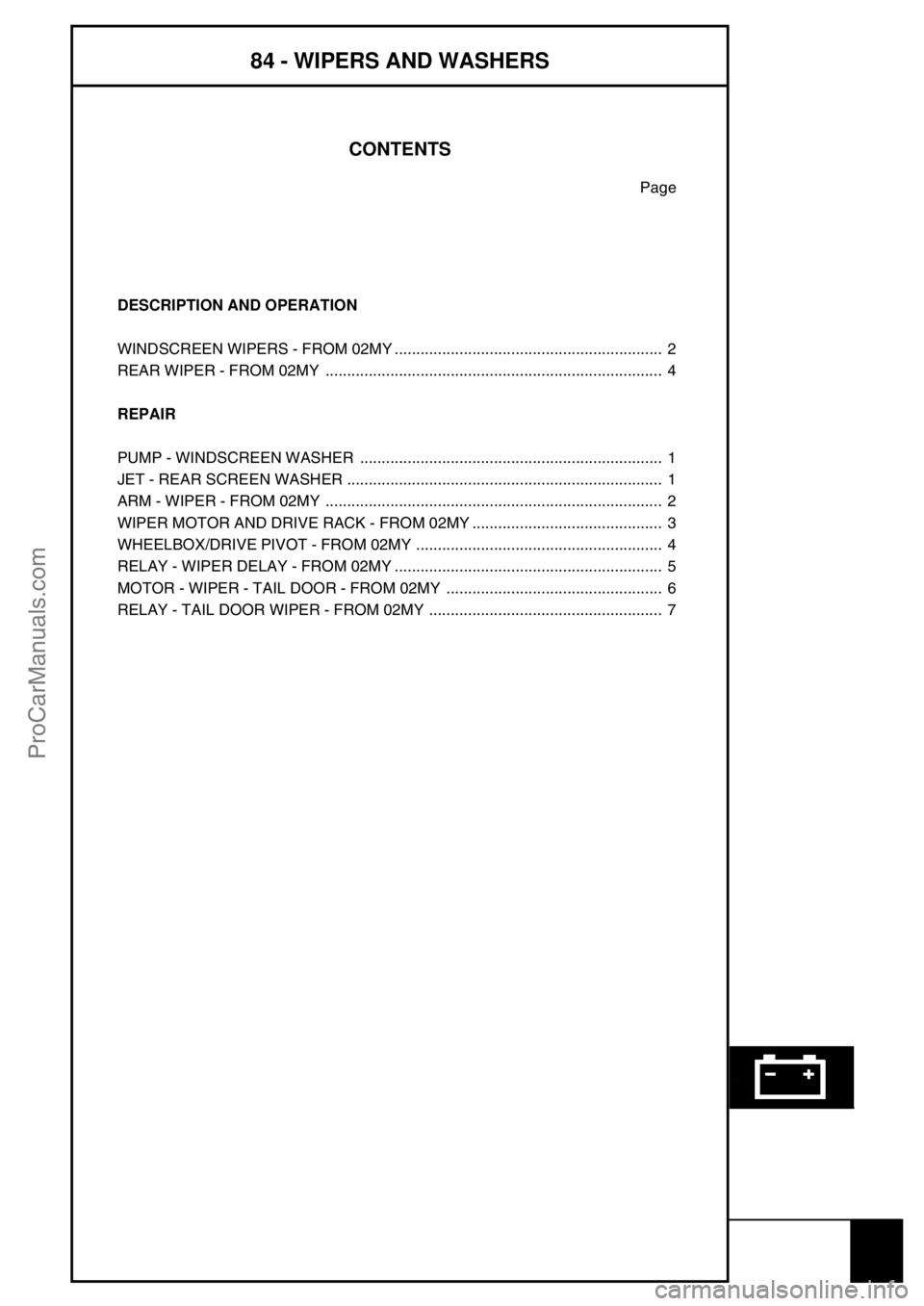
84 - WIPERS AND WASHERS
CONTENTS
Page
DESCRIPTION AND OPERATION
WINDSCREEN WIPERS - FROM 02MY 2..............................................................
REAR WIPER - FROM 02MY 4..............................................................................
REPAIR
PUMP - WINDSCREEN WASHER 1......................................................................
JET - REAR SCREEN WASHER 1.........................................................................
ARM - WIPER - FROM 02MY 2..............................................................................
WIPER MOTOR AND DRIVE RACK - FROM 02MY 3............................................
WHEELBOX/DRIVE PIVOT - FROM 02MY 4.........................................................
RELAY - WIPER DELAY - FROM 02MY 5..............................................................
MOTOR - WIPER - TAIL DOOR - FROM 02MY 6..................................................
RELAY - TAIL DOOR WIPER - FROM 02MY 7......................................................
ProCarManuals.com
Page 594 of 667
WIPERS AND WASHERS
1
DESCRIPTION AND OPERATION This page is intentionally left blank
ProCarManuals.com
Page 595 of 667
84WIPERS AND WASHERS
2
DESCRIPTION AND OPERATION WINDSCREEN WIPERS - FROM 02MY
1.LH wheelbox
2.Cable
3.RH wheelbox
4.Wiper motor
5.Spindle with DIN taper arm attachment
6.Spacer
7.Locknut
8.Seal
9.Locknuts
ProCarManuals.com
Page 596 of 667
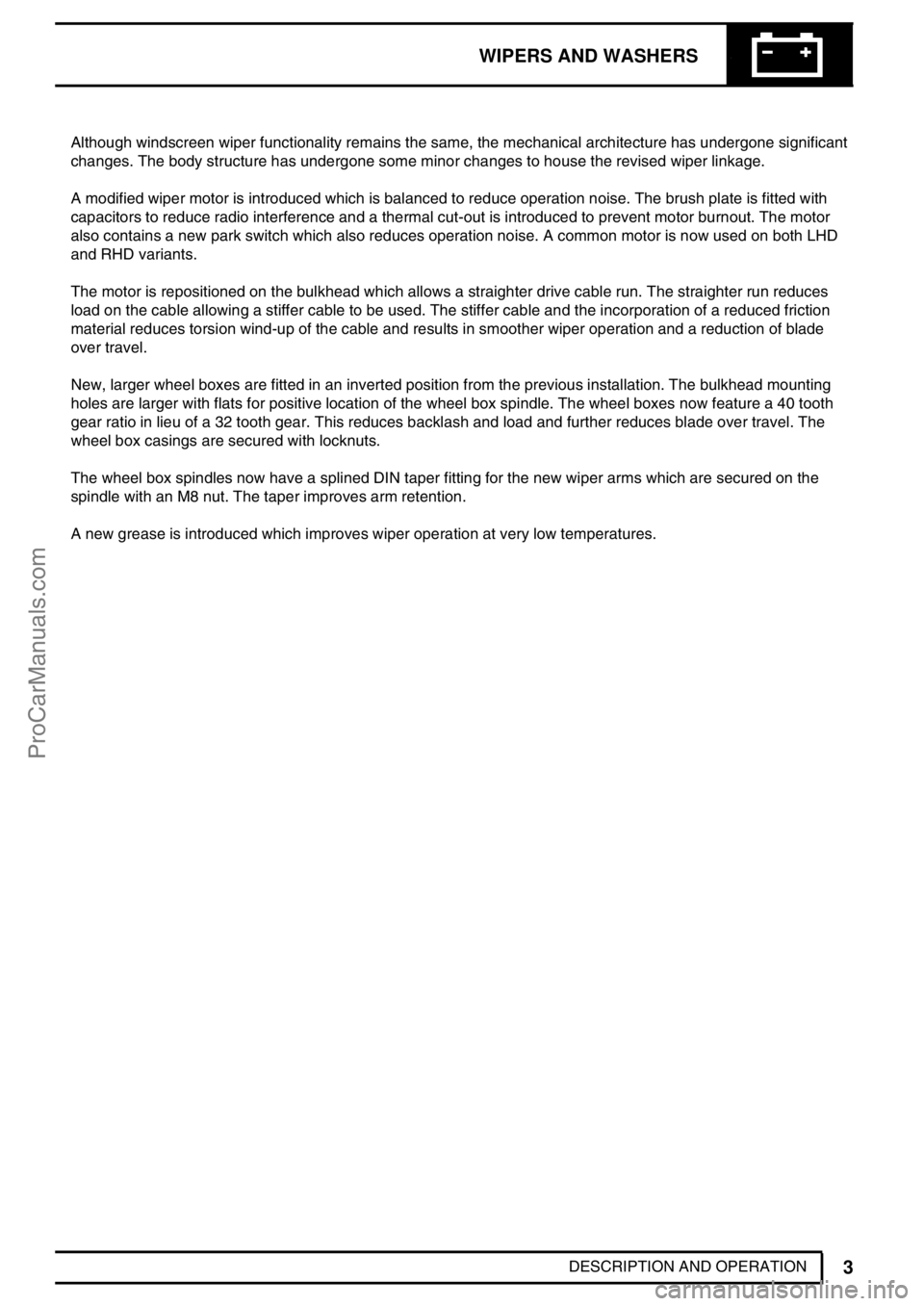
WIPERS AND WASHERS
3
DESCRIPTION AND OPERATION Although windscreen wiper functionality remains the same, the mechanical architecture has undergone significant
changes. The body structure has undergone some minor changes to house the revised wiper linkage.
A modified wiper motor is introduced which is balanced to reduce operation noise. The brush plate is fitted with
capacitors to reduce radio interference and a thermal cut-out is introduced to prevent motor burnout. The motor
also contains a new park switch which also reduces operation noise. A common motor is now used on both LHD
and RHD variants.
The motor is repositioned on the bulkhead which allows a straighter drive cable run. The straighter run reduces
load on the cable allowing a stiffer cable to be used. The stiffer cable and the incorporation of a reduced friction
material reduces torsion wind-up of the cable and results in smoother wiper operation and a reduction of blade
over travel.
New, larger wheel boxes are fitted in an inverted position from the previous installation. The bulkhead mounting
holes are larger with flats for positive location of the wheel box spindle. The wheel boxes now feature a 40 tooth
gear ratio in lieu of a 32 tooth gear. This reduces backlash and load and further reduces blade over travel. The
wheel box casings are secured with locknuts.
The wheel box spindles now have a splined DIN taper fitting for the new wiper arms which are secured on the
spindle with an M8 nut. The taper improves arm retention.
A new grease is introduced which improves wiper operation at very low temperatures.
ProCarManuals.com
Page 597 of 667
84WIPERS AND WASHERS
4
DESCRIPTION AND OPERATION REAR WIPER - FROM 02MY
1.Rear wiper relay
The rear wiper system is unchanged except for the addition of a wiper motor relay into the electrical circuit.
The new rear wiper relay is located in the tail door, below the wiper motor. The relay coil is energised by a feed
supplied from the rear wiper switch. When the relay contacts close, a feed is supplied via the ignition switch
(position II) and a fuse in the passenger compartment fuse box, through the relay contacts to the wiper motor.
ProCarManuals.com
Page 598 of 667
WIPERS AND WASHERS
5
DESCRIPTION AND OPERATION
ProCarManuals.com
Page 600 of 667
WIPERS AND WASHERS
1
REPAIR PUMP - WINDSCREEN WASHER
Service repair no - 84.10.21
Remove
1.Remove headlamp.See ELECTRICAL,
Repair.
2.Position drain tin to collect any fluid spillage.
3.Disconnect multiplug from washer pump.
4.Disconnect hose from washer pump.
5.Release washer pump from reservoir and
discard sealing washer.
Refit
6.Fit new sealing washer and secure pump to
reservoir.
7.Connect hose and multiplug to washer pump.
8.Fit headlamp.See ELECTRICAL, Repair.
9.Fill reservoir with screen cleaning fluid.JET - REAR SCREEN WASHER
Service repair no - 84.30.09
Remove
1.Release and remove both rear side window
finishers.
2.Remove 8 screws securing both rear grab
handles.
3.Remove both rear grab handles.
ProCarManuals.com