Page 8 of 64
8
Principles
The natural frequency of the bodywork
The vibrations are deÞned by the degree of
amplitude and its frequency. The natural
frequency of the bodywork is particularly
important during matching of the
suspension.
The natural frequency of unsprung parts is
between 10 Hz and 16 Hz for a medium-size
vehicle. Appropriate matching of the
suspension system reduces the natural
frequency of the bodywork (sprung mass) to
between 1 Hz and 1.5 Hz.
Vibration
If a mass on a spring is deßected from its rest
position by a force, a restoring force develops
in the spring which allows the mass to
rebound. The mass
oscillates
beyond its rest
position which results in a further restoring
force being exerted. This process is repeated
until air resistance and the internal friction of
the spring causes the vibration to cease.
242_021
Rest position Mass
Spring
Vibration
Rebound
Compression
1 cycleAmplitude
Page 14 of 64
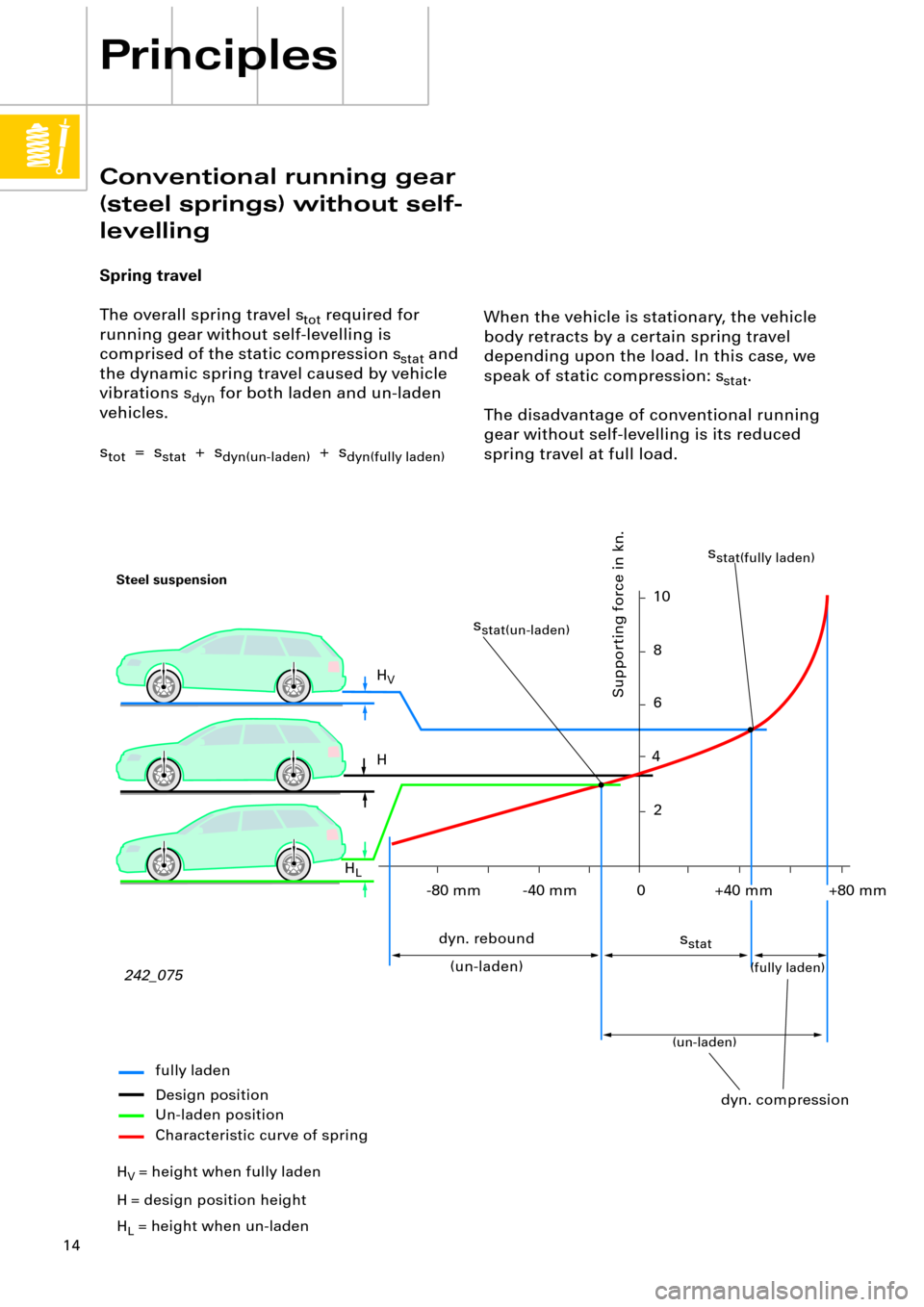
14
When the vehicle is stationary, the vehicle
body retracts by a certain spring travel
depending upon the load. In this case, we
speak of static compression: s
stat
.
The disadvantage of conventional running
gear without self-levelling is its reduced
spring travel at full load.
Conventional running gear
(steel springs) without self-
levelling
Spring travel
The overall spring travel s
tot
required for
running gear without self-levelling is
comprised of the static compression s
stat
and
the dynamic spring travel caused by vehicle
vibrations s
dyn
for both laden and un-laden
vehicles.
s
tot
= s
stat
+ s
dyn(un-laden)
+ s
dyn(fully laden)
Principles
242_075
Steel suspension
fully laden
Design position
Un-laden position
Supporting force in kn.
H
V
H
H
L
dyn. rebound
s
stat
(un-laden)
dyn. compression
(un-laden)(fully laden)
10
8
6
4
2
+80 mm-40 mm -80 mm
H
V
= height when fully laden
H
= design position height
H
L
= height when un-ladenCharacteristic curve of spring
s
stat(un-laden)
s
stat(fully laden)
+40 mm
0
Page 27 of 64
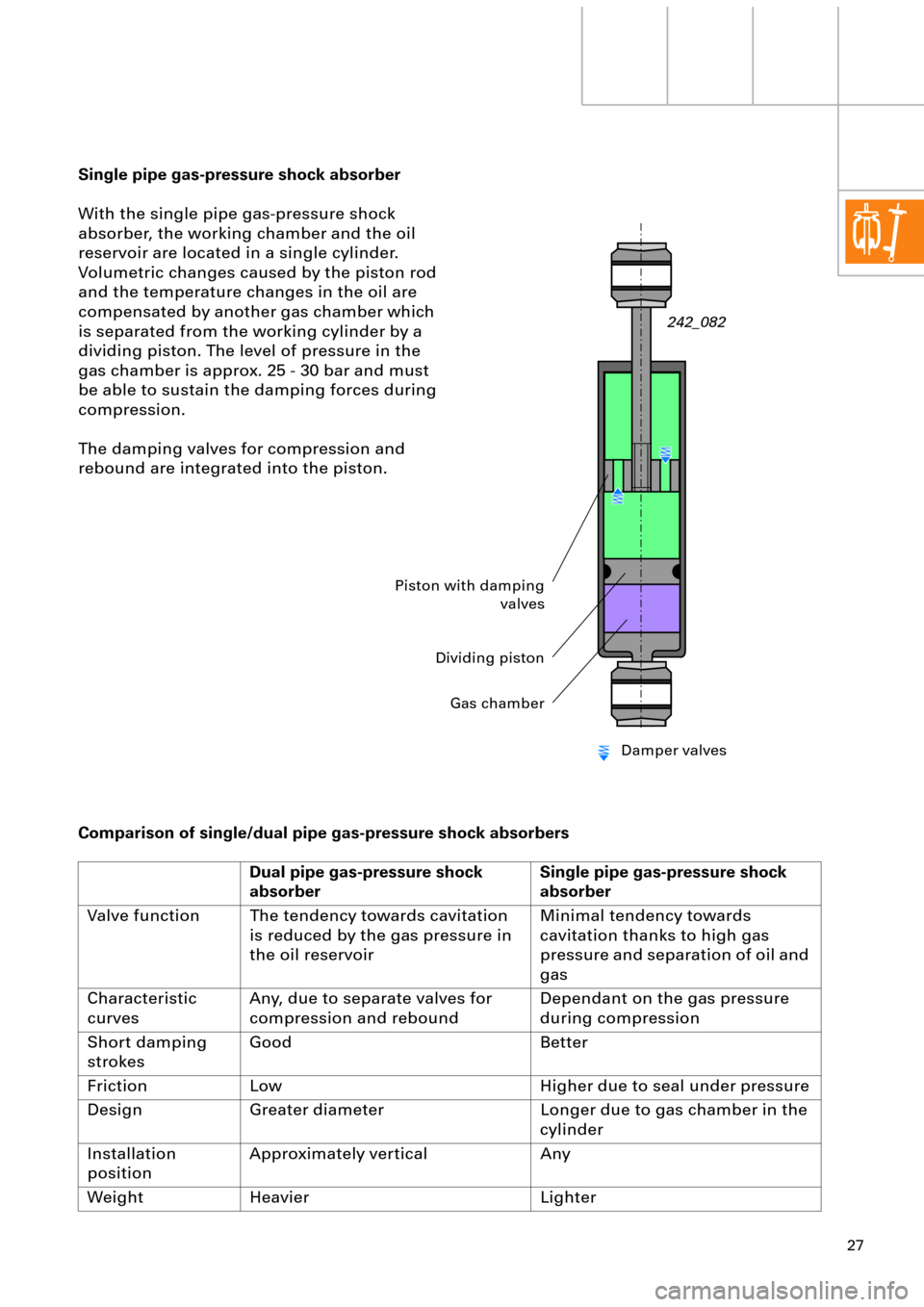
27
Single pipe gas-pressure shock absorber
With the single pipe gas-pressure shock
absorber, the working chamber and the oil
reservoir are located in a single cylinder.
Volumetric changes caused by the piston rod
and the temperature changes in the oil are
compensated by another gas chamber which
is separated from the working cylinder by a
dividing piston. The level of pressure in the
gas chamber is approx. 25 - 30 bar and must
be able to sustain the damping forces during
compression.
The damping valves for compression and
rebound are integrated into the piston.
Comparison of single/dual pipe gas-pressure shock absorbers
Dual pipe gas-pressure shock
absorberSingle pipe gas-pressure shock
absorber
Valve function The tendency towards cavitation
is reduced by the gas pressure in
the oil reservoirMinimal tendency towards
cavitation thanks to high gas
pressure and separation of oil and
gas
Characteristic
curvesAny, due to separate valves for
compression and reboundDependant on the gas pressure
during compression
Short damping
strokesGood Better
Friction Low Higher due to seal under pressure
Design Greater diameter Longer due to gas chamber in the
cylinder
Installation
positionApproximately vertical Any
Weight Heavier Lighter
242_082
Piston with damping
valves
Dividing piston
Gas chamber
Damper valves