Page 70 of 1463
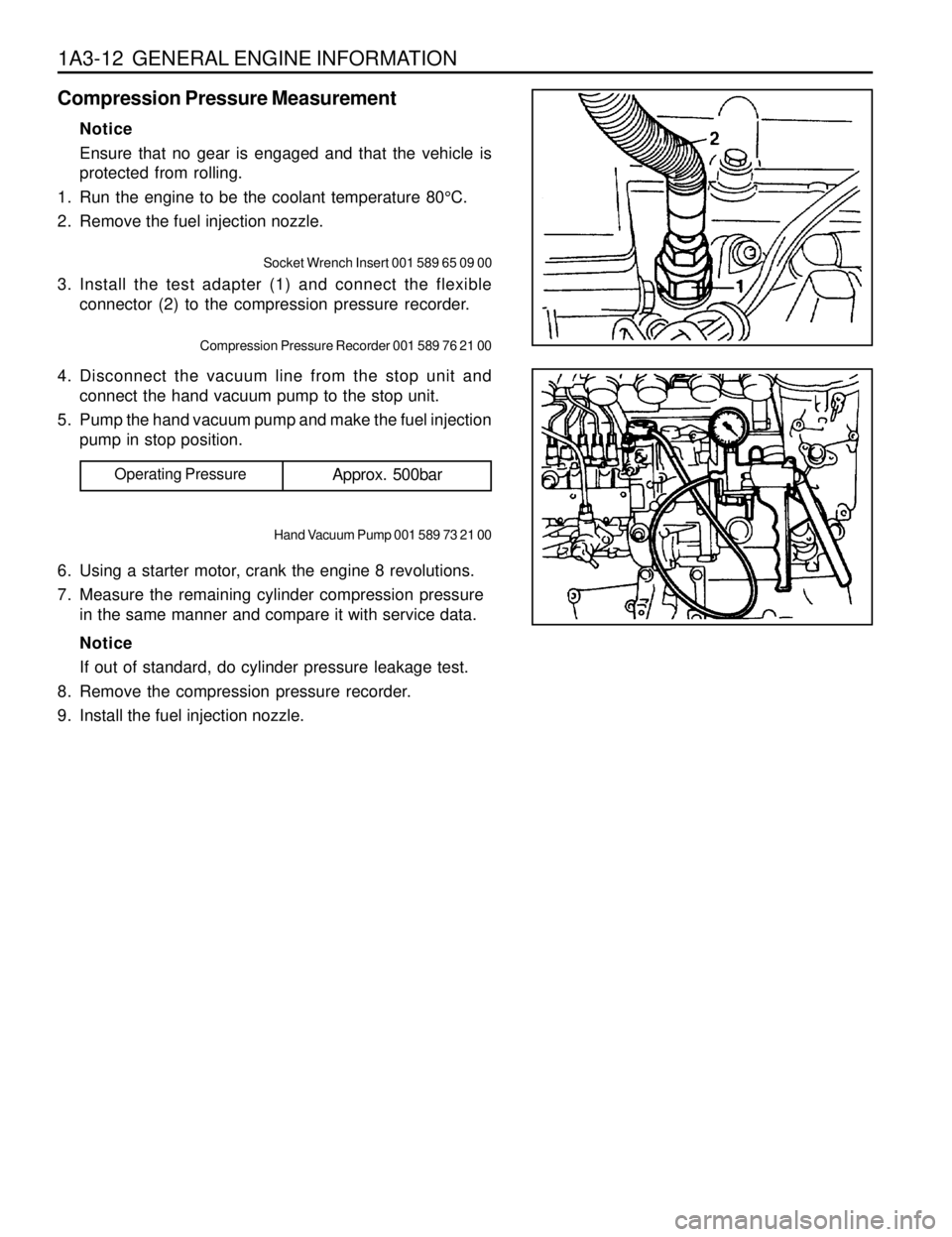
1A3-12 GENERAL ENGINE INFORMATION
Compression Pressure Measurement
Notice
Ensure that no gear is engaged and that the vehicle is
protected from rolling.
1. Run the engine to be the coolant temperature 80°C.
2. Remove the fuel injection nozzle.
Socket Wrench Insert 001 589 65 09 00
3. Install the test adapter (1) and connect the flexible
connector (2) to the compression pressure recorder.
Compression Pressure Recorder 001 589 76 21 00
4. Disconnect the vacuum line from the stop unit and
connect the hand vacuum pump to the stop unit.
5. Pump the hand vacuum pump and make the fuel injection
pump in stop position.
Operating PressureApprox. 500bar
Hand Vacuum Pump 001 589 73 21 00
6. Using a starter motor, crank the engine 8 revolutions.
7. Measure the remaining cylinder compression pressure
in the same manner and compare it with service data.
Notice
If out of standard, do cylinder pressure leakage test.
8. Remove the compression pressure recorder.
9. Install the fuel injection nozzle.
Page 72 of 1463
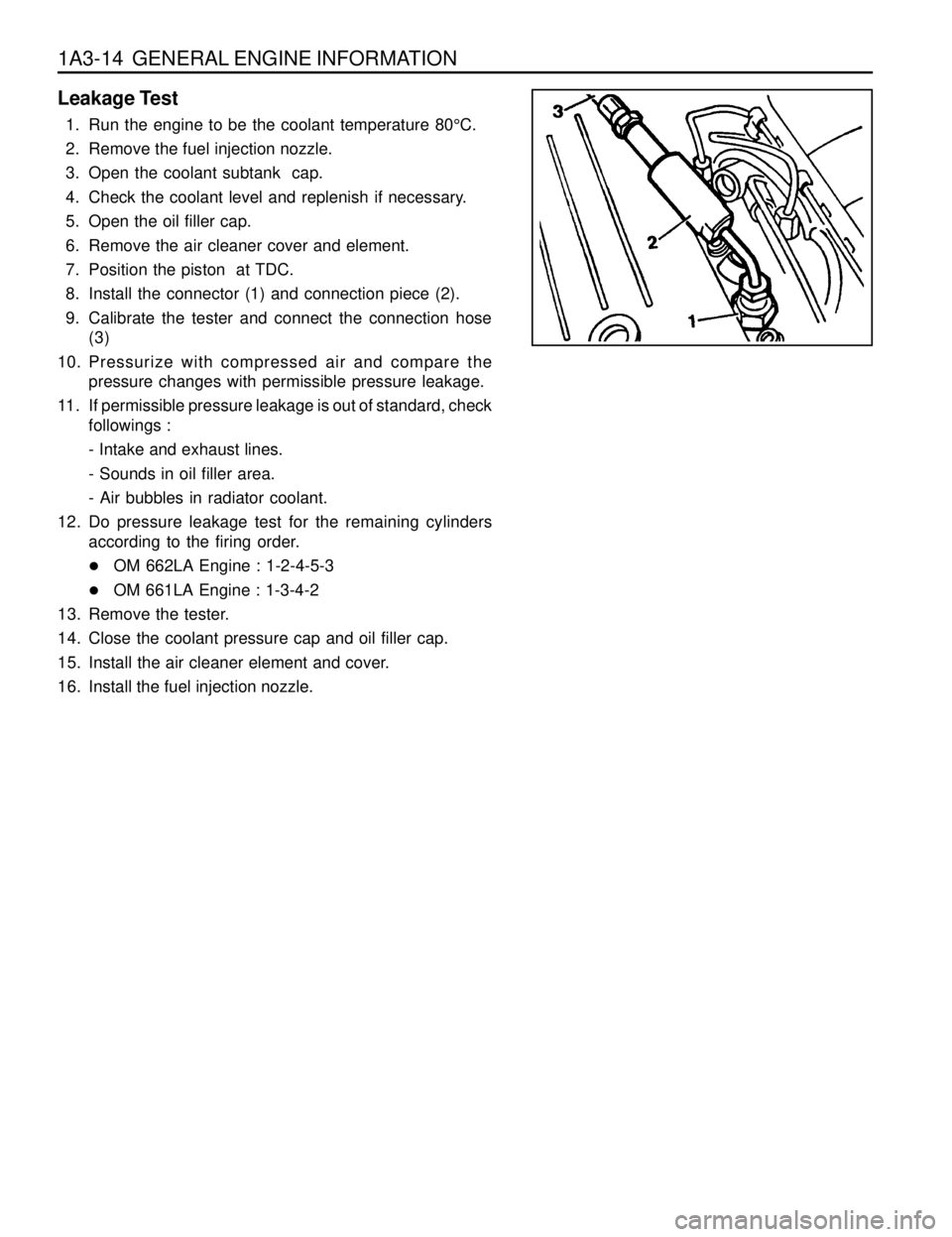
1A3-14 GENERAL ENGINE INFORMATION
Leakage Test
1. Run the engine to be the coolant temperature 80°C.
2. Remove the fuel injection nozzle.
3. Open the coolant subtank cap.
4. Check the coolant level and replenish if necessary.
5. Open the oil filler cap.
6. Remove the air cleaner cover and element.
7. Position the piston at TDC.
8. Install the connector (1) and connection piece (2).
9. Calibrate the tester and connect the connection hose
(3)
10. Pressurize with compressed air and compare the
pressure changes with permissible pressure leakage.
11. If permissible pressure leakage is out of standard, check
followings :
- Intake and exhaust lines.
- Sounds in oil filler area.
- Air bubbles in radiator coolant.
12. Do pressure leakage test for the remaining cylinders
according to the firing order.
lOM 662LA Engine : 1-2-4-5-3
lOM 661LA Engine : 1-3-4-2
13. Remove the tester.
14. Close the coolant pressure cap and oil filler cap.
15. Install the air cleaner element and cover.
16. Install the fuel injection nozzle.
Page 82 of 1463
M162 ENGINE MECHANICAL 1B1-9
4. Disconnect the coupling of HFM sensor and remove the air
cleaner cross pipe.
6. Loosen the radiator drain cock and drain the coolant.
Notice
Open the coolant reservoir cap. 5. Remove the air cleaner cover. Remove the mounting bolts
and air cleaner housing and element assembly.
Removal & Installation Procedure
1. Disconnect the negative terminal of battery.
2. Remove the hood.
3. Remove the under cover.
Installation Notice
Tightening Torque 28 - 47 Nm
Page 83 of 1463
1B1-10 M162 ENGINE MECHANICAL
10. Remove the upper mounting bolts of radiator and then
remove the radiator.
7. Loosen the cylinder block drain plug and then drain the
coolant completely.
Installation Notice
Tightening Torque 30 Nm
Notice
Replace the seal before installation of the drain plug.
8. Remove the cooling fan shroud.
9. Disconnect the each hose from radiator.
Page 86 of 1463
M162 ENGINE MECHANICAL 1B1-13
20. Disconnect following sensors connector.
lHFM sensor.
lCoolant temperature sensor.
l2 knock sensors.
lCamshaft and crankshaft sensors.
21. After removing the ignition coil cover, disconnect the ignition
coil connector.
22. Remove the harness cover and disconnect the 6 injection
valve connectors. Disconnect the main harness
23. Separate the hose toward engine from canister purge
solenoid valve.
24. Remove the automatic transmission oil cooler line.
Page 106 of 1463
M162 ENGINE MECHANICAL 1B1-33
CYLINDER HEAD FRONT COVER
Preceding Work : Removal of cylinder head cover
Removal of coolant connection fitting
1 Camshaft Position Sensor
2 Magnet Assembly
3 Upper Guide Rail
4 Bolt (M6 x 60, 3 pieces).................22.5-27.5 Nm5 Bolt (M8 x 80, 3 pieces).................22.5-27.5 Nm
6 Front Cover
7 Rubber Gasket...................................... Replace
8 Bolt (M6 x 16, 3 pieces)......................... 9-11 Nm
Removal & Installation Procedure
1. Remove the magnet assembly.
Installation Notice
Tightening Torque 9 - 11 Nm
Page 109 of 1463
1B1-36 M162 ENGINE MECHANICAL
4. Remove the three flange bolts in the exhaust camshaft
sprocket.
Installation Notice
5. Separate the chain from the camshaft sprockrt.
Notice
Be careful not to drop the chain into the timing case. Do not reuse the removed bolts. Tools Required
000 589 01 10 00 Box Wrench Insert
116 589 02 34 00 Screw-fixed Pin
116 589 20 33 00 Sliding Hammer
Removal & Installation Procedure
1. Rotate the crankshaft so that the piston of number 1 cylinder
is at TDC.
Notice
Rotate the crankshaft in the normal engine direction.
2. Put the alignment marks (arrows) on the timing chain and
camshaft sprocket.
3. Drain the coolant from the crankcase.
Tightening Torque1st step 18 - 22 Nm
2nd step 90° ± 5°
Page 132 of 1463
M162 ENGINE MECHANICAL 1B1-59
CAMSHAFT
Preceding Work : Removal of cylinder head cover, removal of coolant connection fitting
1 Chain Tensioner Assembly..................72-88 Nm
2 Exhaust Camshaft Sprocket
3 Upper Guide Rail
4 Cylinder Head Front Cover5 Intake Camshaft Sprocket
6 Chain
7 Wrench (Special Tool)