Page 837 of 1463
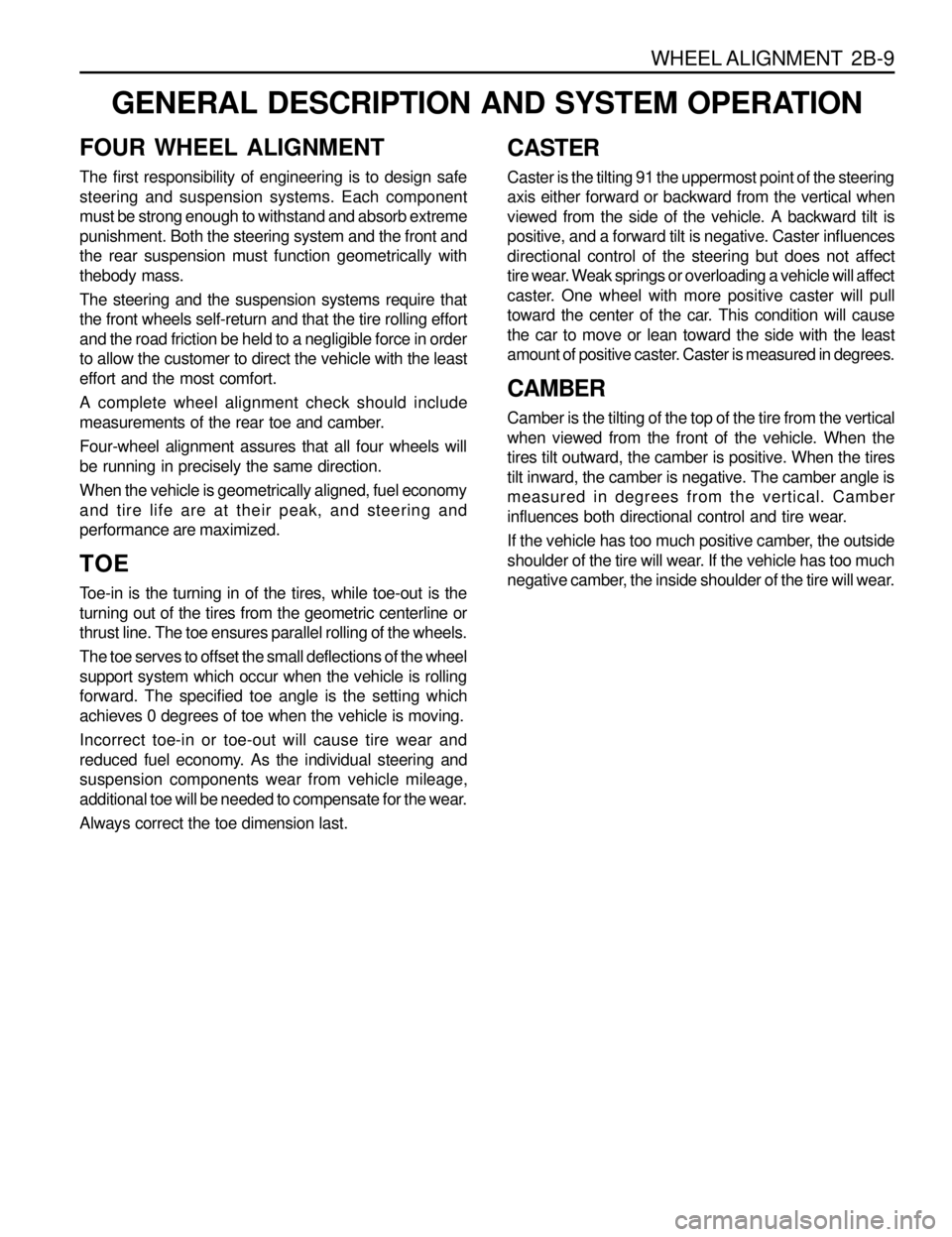
WHEEL ALIGNMENT 2B-9
GENERAL DESCRIPTION AND SYSTEM OPERATION
FOUR WHEEL ALIGNMENT
CASTER
Caster is the tilting 91 the uppermost point of the steering
axis either forward or backward from the vertical when
viewed from the side of the vehicle. A backward tilt is
positive, and a forward tilt is negative. Caster influences
directional control of the steering but does not affect
tire wear. Weak springs or overloading a vehicle will affect
caster. One wheel with more positive caster will pull
toward the center of the car. This condition will cause
the car to move or lean toward the side with the least
amount of positive caster. Caster is measured in degrees.
CAMBER
Camber is the tilting of the top of the tire from the vertical
when viewed from the front of the vehicle. When the
tires tilt outward, the camber is positive. When the tires
tilt inward, the camber is negative. The camber angle is
measured in degrees from the vertical. Camber
influences both directional control and tire wear.
If the vehicle has too much positive camber, the outside
shoulder of the tire will wear. If the vehicle has too much
negative camber, the inside shoulder of the tire will wear. The first responsibility of engineering is to design safe
steering and suspension systems. Each component
must be strong enough to withstand and absorb extreme
punishment. Both the steering system and the front and
the rear suspension must function geometrically with
thebody mass.
The steering and the suspension systems require that
the front wheels self-return and that the tire rolling effort
and the road friction be held to a negligible force in order
to allow the customer to direct the vehicle with the least
effort and the most comfort.
A complete wheel alignment check should include
measurements of the rear toe and camber.
Four-wheel alignment assures that all four wheels will
be running in precisely the same direction.
When the vehicle is geometrically aligned, fuel economy
and tire life are at their peak, and steering and
performance are maximized.
TOE
Toe-in is the turning in of the tires, while toe-out is the
turning out of the tires from the geometric centerline or
thrust line. The toe ensures parallel rolling of the wheels.
The toe serves to offset the small deflections of the wheel
support system which occur when the vehicle is rolling
forward. The specified toe angle is the setting which
achieves 0 degrees of toe when the vehicle is moving.
Incorrect toe-in or toe-out will cause tire wear and
reduced fuel economy. As the individual steering and
suspension components wear from vehicle mileage,
additional toe will be needed to compensate for the wear.
Always correct the toe dimension last.
Page 873 of 1463
FRONT DRIVE AXLE 3A-5
VACUUM CIRCUIT
1 Engine
2 Vacuum Pump
3 3-way Connector
4 T-connector
5 Check Valve6 Auto locking Hub Solenoid Valve
7 T-connector Hose
8 Hub Hose (left)
9 Hub Hose (right)
Page 922 of 1463
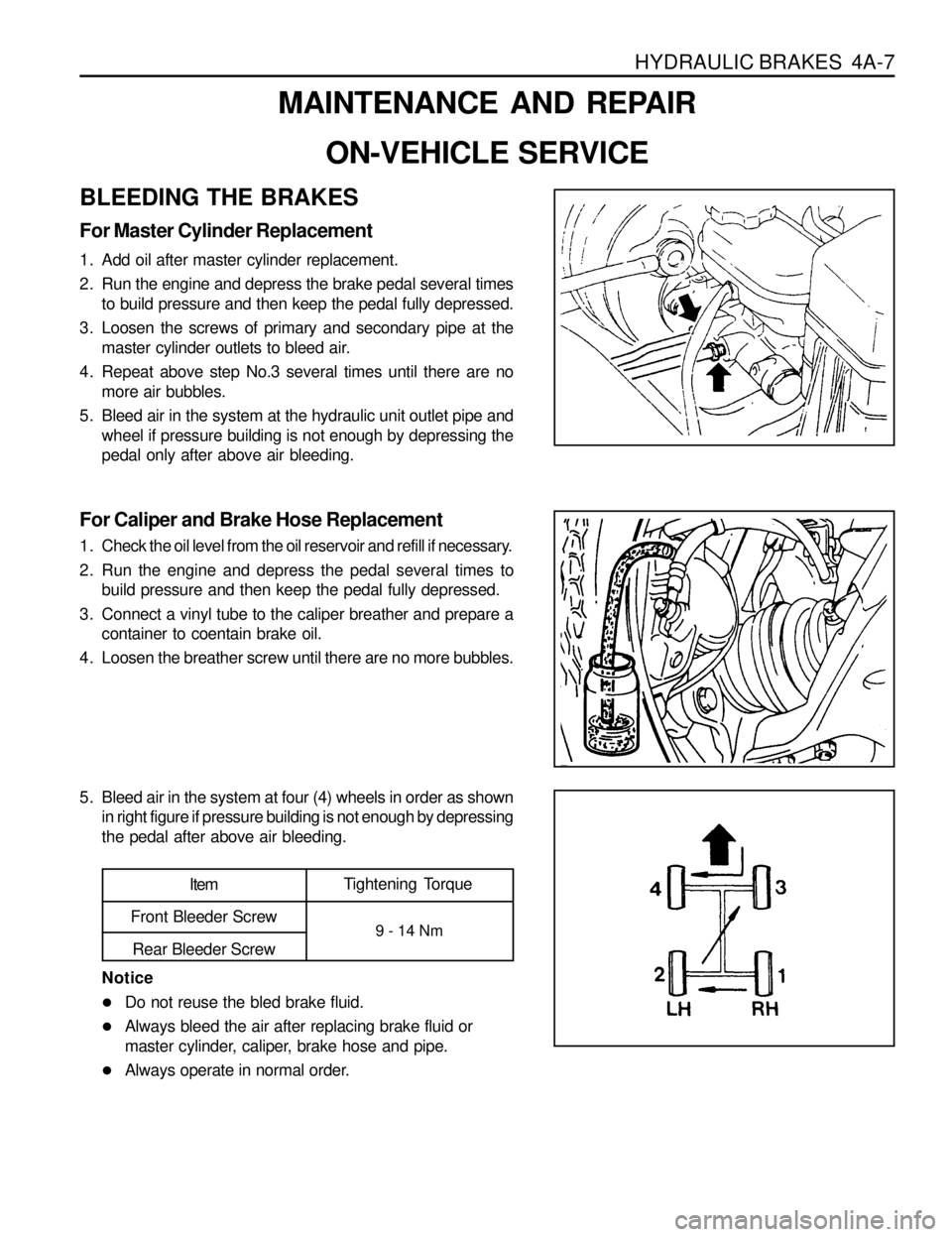
HYDRAULIC BRAKES 4A-7
MAINTENANCE AND REPAIR
ON-VEHICLE SERVICE
BLEEDING THE BRAKES
For Master Cylinder Replacement
1. Add oil after master cylinder replacement.
2. Run the engine and depress the brake pedal several times
to build pressure and then keep the pedal fully depressed.
3. Loosen the screws of primary and secondary pipe at the
master cylinder outlets to bleed air.
4. Repeat above step No.3 several times until there are no
more air bubbles.
5. Bleed air in the system at the hydraulic unit outlet pipe and
wheel if pressure building is not enough by depressing the
pedal only after above air bleeding.
For Caliper and Brake Hose Replacement
1. Check the oil level from the oil reservoir and refill if necessary.
2. Run the engine and depress the pedal several times to
build pressure and then keep the pedal fully depressed.
3. Connect a vinyl tube to the caliper breather and prepare a
container to coentain brake oil.
4. Loosen the breather screw until there are no more bubbles.
5. Bleed air in the system at four (4) wheels in order as shown
in right figure if pressure building is not enough by depressing
the pedal after above air bleeding.
Tightening Torque
9 - 14 Nm
Item
Front Bleeder Screw
Rear Bleeder Screw
Notice
lDo not reuse the bled brake fluid.
lAlways bleed the air after replacing brake fluid or
master cylinder, caliper, brake hose and pipe.
lAlways operate in normal order.
Page 923 of 1463
4A-8 HYDRAULIC BRAKES
For Hydraulic Unit Replacement
1. Add oil after hydraulic unit replacement.
2. Run the engine and depress the pedal several times to
build pressure and then keep the pedal fully depressed.
3. Loosen hydraulic pipe screws at the hydraulic unit outlets
to bleed air.
4. Repeat above step No.3 several times until there are no
more air bubbles.
5. Bleed air in the system from the wheels if pressure building
is not enough by pressing the pedal only after above air
bleeding.
Page 938 of 1463
POWER BOOSTER 4C-5
PEDAL STROKE INSPECTION
1. Start the engine and stop it after one or two minutes.
Depress the brake pedal several times.
If the pedal goes down furthest the first time, but gradually
rises after the second or third time, brake booster is normal.
If there is no change in pedal stroke, the brake booster is
abnormal.
2. Depress the brake pedal several times with engine stopped,
and depress the brake pedal and start the engine. If the
pedal goes down slightly, the booster is normal.
3. Depress the brake pedal with engine running, and stop it
with the pedal depressed. If there is no change in pedal
height during 30 sec., the booster is normal.
Page 979 of 1463
5A-2 AUTOMATIC TRANSMISSION
SPECIFICATIONS
MODEL PART NUMBERS AND APPLICATIONS
Transmission
0574-000001 (9)
0574-000002 (8)
0574-000004 (10)
0574-000005 (7)Torque Converter
179K
160K
160K
179KEngine Version
661LA
E32
662LA(Turbo)
E23
MODEL SPECIFICATIONS
Application
Torque Converter
Mean diameter of fluid circuit
Maximum torque multiplication
Stall speed (rpm)
0574-000001 (D23LA)
0574-000002 (E32)
0574-000004 (D29LA)
0574-000005 (E23)
0574-000020
0574-000021
Gear Ratios
First
Second
Third
Fourth
Reverse
Lubricant
Type
Capacity
Dry System
Service Refill
Gear Train End Float
Gear Set Pinion End FloatDescriprtion
260
2.0 : 1
2100 - 2250
2050 - 2250
2100 - 2200
1800 - 2100
2.741 : 1
1.508 : 1
1.000 : 1
0.708 : 1
2.429 : 1
Castrol TQ95 or other approved fluid
9.0 Litres (approx)
4.5 Litres (approx)
0.50 - 0.65 mm
0.10 - 0.50 mm DWMC P/NO
36100-05420 (1)
36100-05430 (1)
36100-05410 (1)
36100-05440 (1)
Page 995 of 1463
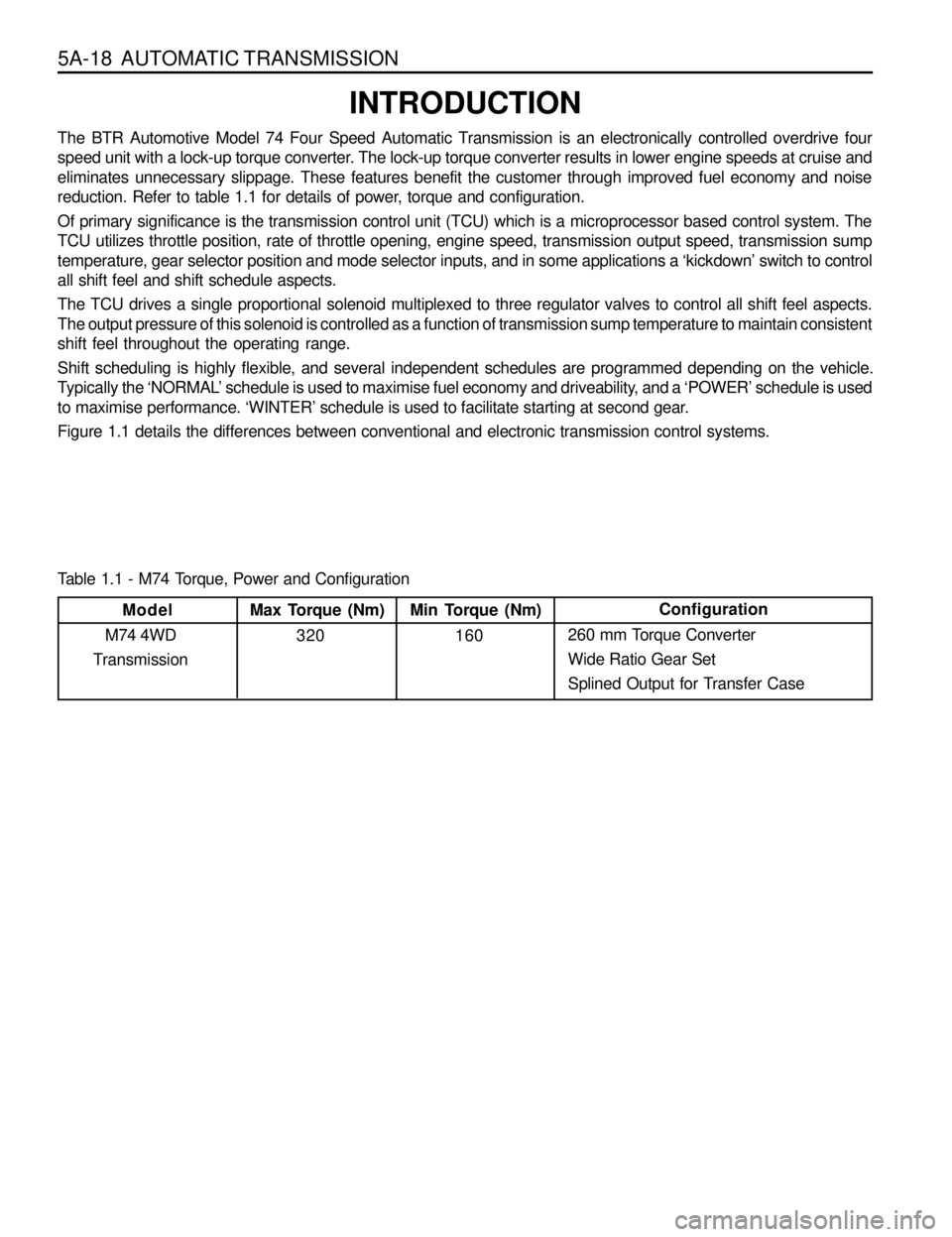
5A-18 AUTOMATIC TRANSMISSION
INTRODUCTION
The BTR Automotive Model 74 Four Speed Automatic Transmission is an electronically controlled overdrive four
speed unit with a lock-up torque converter. The lock-up torque converter results in lower engine speeds at cruise and
eliminates unnecessary slippage. These features benefit the customer through improved fuel economy and noise
reduction. Refer to table 1.1 for details of power, torque and configuration.
Of primary significance is the transmission control unit (TCU) which is a microprocessor based control system. The
TCU utilizes throttle position, rate of throttle opening, engine speed, transmission output speed, transmission sump
temperature, gear selector position and mode selector inputs, and in some applications a ‘kickdown’ switch to control
all shift feel and shift schedule aspects.
The TCU drives a single proportional solenoid multiplexed to three regulator valves to control all shift feel aspects.
The output pressure of this solenoid is controlled as a function of transmission sump temperature to maintain consistent
shift feel throughout the operating range.
Shift scheduling is highly flexible, and several independent schedules are programmed depending on the vehicle.
Typically the ‘NORMAL’ schedule is used to maximise fuel economy and driveability, and a ‘POWER’ schedule is used
to maximise performance. ‘WINTER’ schedule is used to facilitate starting at second gear.
Figure 1.1 details the differences between conventional and electronic transmission control systems.
Max Torque (Nm)
320Configuration
260 mm Torque Converter
Wide Ratio Gear Set
Splined Output for Transfer CaseMin Torque (Nm)
160 Model
M74 4WD
Transmission Table 1.1 - M74 Torque, Power and Configuration
Page 998 of 1463
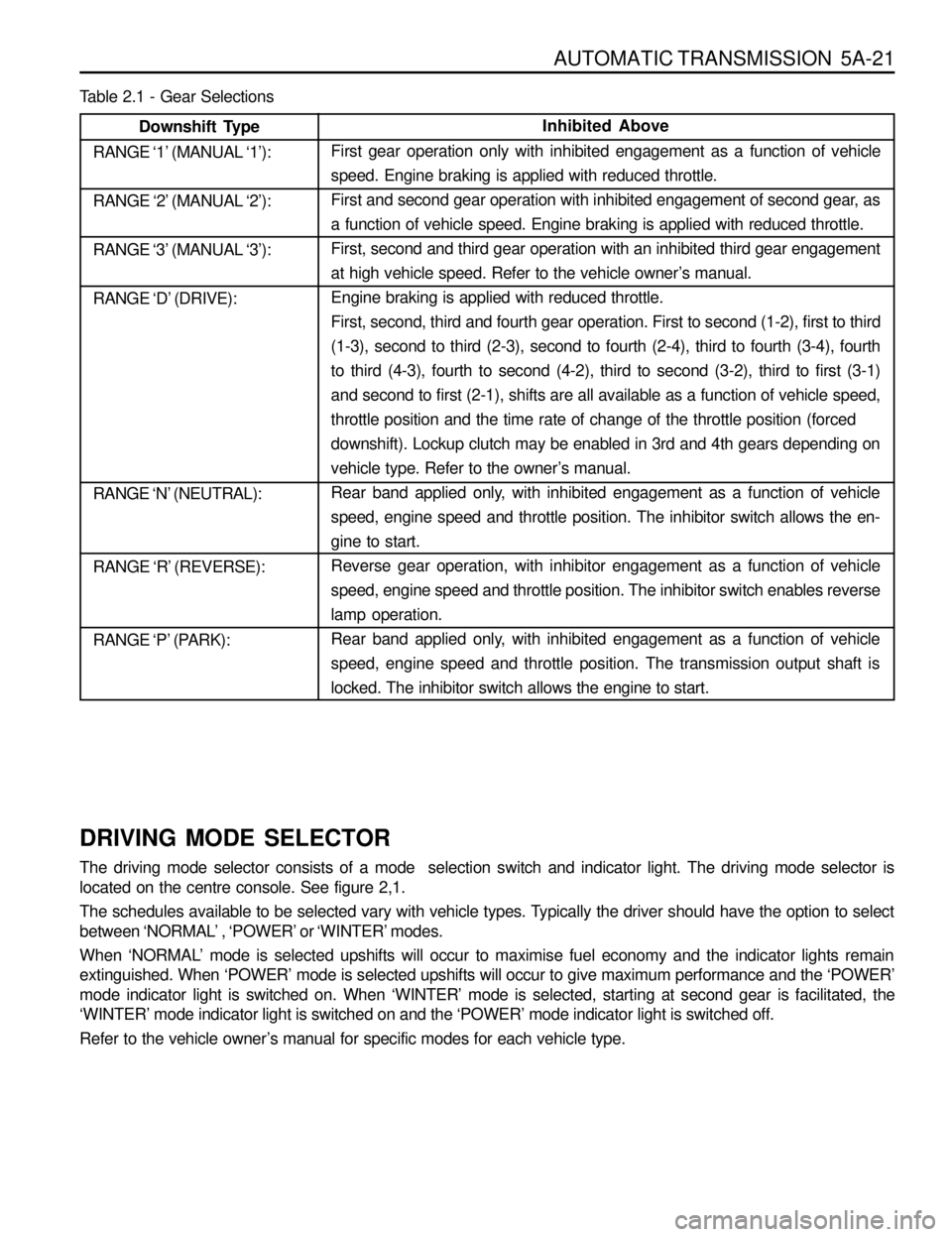
AUTOMATIC TRANSMISSION 5A-21
Downshift Type
RANGE ‘1’ (MANUAL ‘1’):
RANGE ‘2’ (MANUAL ‘2’):
RANGE ‘3’ (MANUAL ‘3’):
RANGE ‘D’ (DRIVE):
RANGE ‘N’ (NEUTRAL):
RANGE ‘R’ (REVERSE):
RANGE ‘P’ (PARK):Inhibited Above
First gear operation only with inhibited engagement as a function of vehicle
speed. Engine braking is applied with reduced throttle.
First and second gear operation with inhibited engagement of second gear, as
a function of vehicle speed. Engine braking is applied with reduced throttle.
First, second and third gear operation with an inhibited third gear engagement
at high vehicle speed. Refer to the vehicle owner’s manual.
Engine braking is applied with reduced throttle.
First, second, third and fourth gear operation. First to second (1-2), first to third
(1-3), second to third (2-3), second to fourth (2-4), third to fourth (3-4), fourth
to third (4-3), fourth to second (4-2), third to second (3-2), third to first (3-1)
and second to first (2-1), shifts are all available as a function of vehicle speed,
throttle position and the time rate of change of the throttle position (forced
downshift). Lockup clutch may be enabled in 3rd and 4th gears depending on
vehicle type. Refer to the owner’s manual.
Rear band applied only, with inhibited engagement as a function of vehicle
speed, engine speed and throttle position. The inhibitor switch allows the en-
gine to start.
Reverse gear operation, with inhibitor engagement as a function of vehicle
speed, engine speed and throttle position. The inhibitor switch enables reverse
lamp operation.
Rear band applied only, with inhibited engagement as a function of vehicle
speed, engine speed and throttle position. The transmission output shaft is
locked. The inhibitor switch allows the engine to start.
Table 2.1 - Gear Selections
DRIVING MODE SELECTOR
The driving mode selector consists of a mode selection switch and indicator light. The driving mode selector is
located on the centre console. See figure 2,1.
The schedules available to be selected vary with vehicle types. Typically the driver should have the option to select
between ‘NORMAL’ , ‘POWER’ or ‘WINTER’ modes.
When ‘NORMAL’ mode is selected upshifts will occur to maximise fuel economy and the indicator lights remain
extinguished. When ‘POWER’ mode is selected upshifts will occur to give maximum performance and the ‘POWER’
mode indicator light is switched on. When ‘WINTER’ mode is selected, starting at second gear is facilitated, the
‘WINTER’ mode indicator light is switched on and the ‘POWER’ mode indicator light is switched off.
Refer to the vehicle owner’s manual for specific modes for each vehicle type.