Page 74 of 396
MPI – On-vehicle Service13-31
5. MPI SYSTEM COMPONENTS LAYOUT
NameSymbolNameSymbol
A/C switchQExhaust temperature warning lampS
A/C relayHFuel pressure control valveA
Air flow sensor (with a built-in intake air temperaturesensor and barometric pressure sensor)FIgnition coil and power transistor unitLsensor and barometric pressure sensor)InjectorB
Camshaft position sensorMISC servoD
Control relay and fuel pump relayPOxygen sensorK
Coolant temperature sensorEPower steering fluid pressure switchI
Crank angle sensorJSecondary air control solenoid valveN
Detonation sensorCThrottle position sensor (with a built-in idle switch)D
Diagnosis connectorR
Engine ECUOVehicle speed sensorT
Engine warning lampSWastegate solenoid valveG
Page 75 of 396
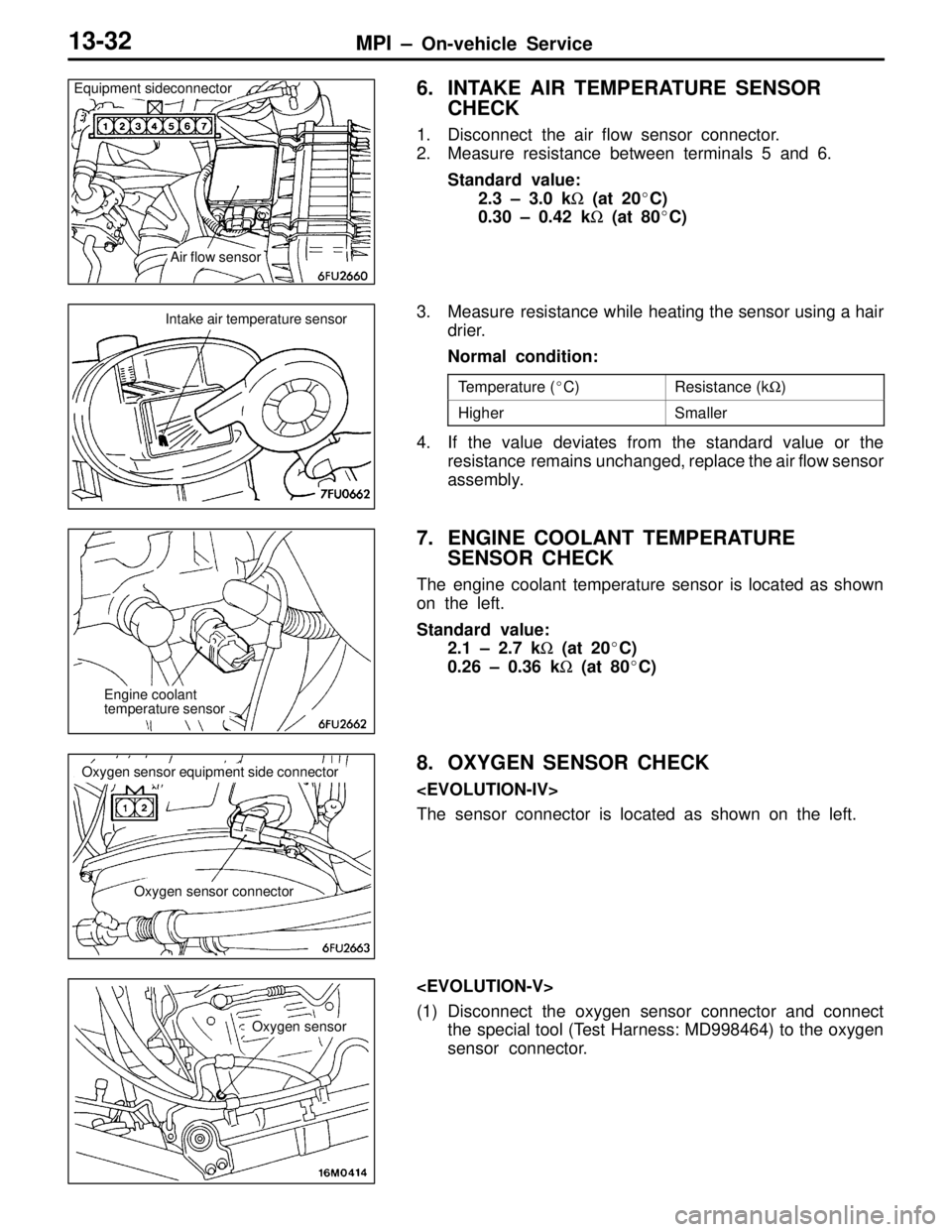
MPI – On-vehicle Service13-32
6. INTAKE AIR TEMPERATURE SENSOR
CHECK
1. Disconnect the air flow sensor connector.
2. Measure resistance between terminals 5 and 6.
Standard value:
2.3 – 3.0 kΩ (at 20C)
0.30 – 0.42 kΩ (at 80C)
3. Measure resistance while heating the sensor using a hair
drier.
Normal condition:
Temperature (C)Resistance (kΩ)
HigherSmaller
4. If the value deviates from the standard value or the
resistance remains unchanged, replace the air flow sensor
assembly.
7. ENGINE COOLANT TEMPERATURE
SENSOR CHECK
The engine coolant temperature sensor is located as shown
on the left.
Standard value:
2.1 – 2.7 kΩ (at 20C)
0.26 – 0.36 kΩ (at 80C)
8. OXYGEN SENSOR CHECK
The sensor connector is located as shown on the left.
(1) Disconnect the oxygen sensor connector and connect
the special tool (Test Harness: MD998464) to the oxygen
sensor connector.
Equipment sideconnector
Air flow sensor
Intake air temperature sensor
Engine coolant
temperature sensor
Oxygen sensor equipment side connector
Oxygen sensor connector
Oxygen sensor
Page 76 of 396
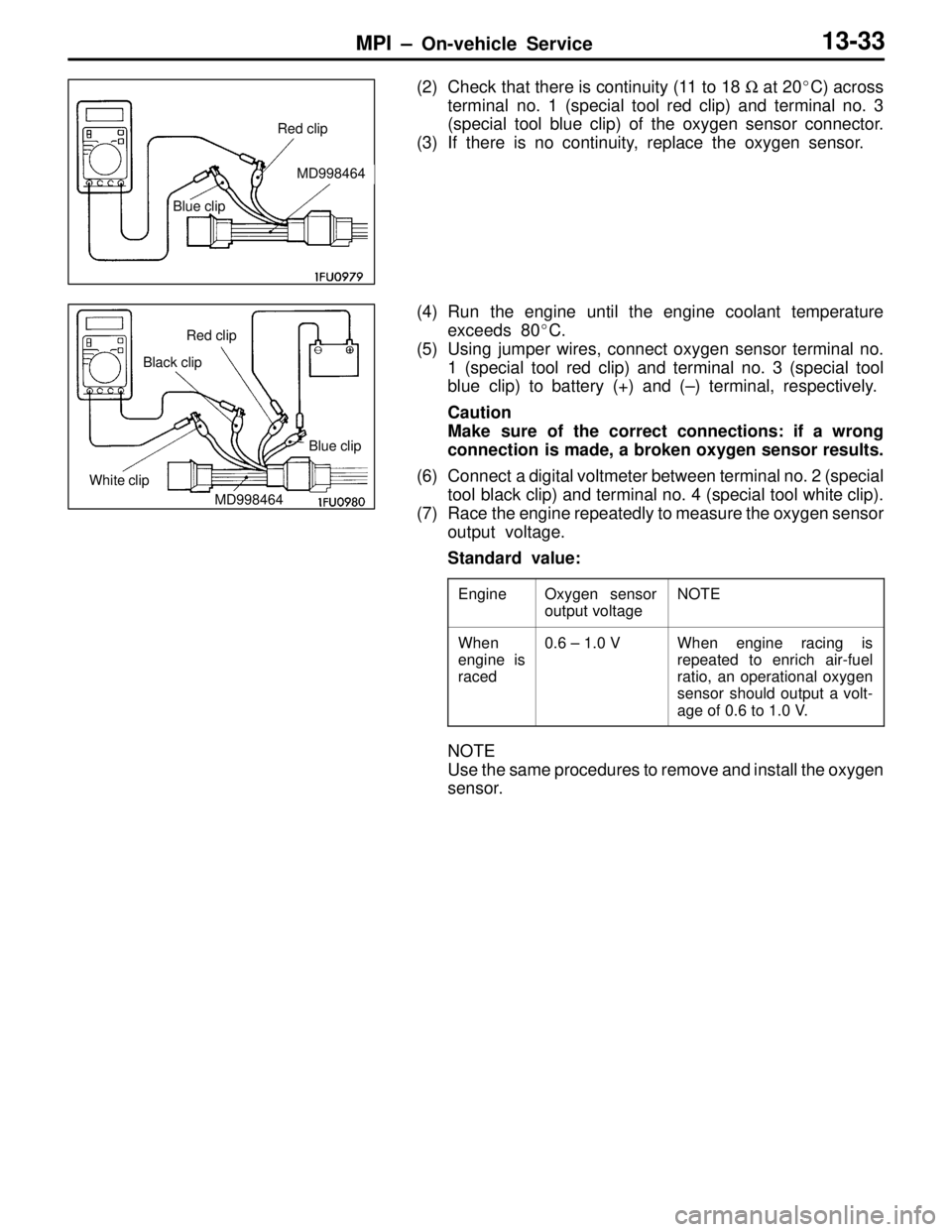
MPI – On-vehicle Service13-33
(2) Check that there is continuity (11 to 18 Ω at 20C) across
terminal no. 1 (special tool red clip) and terminal no. 3
(special tool blue clip) of the oxygen sensor connector.
(3) If there is no continuity, replace the oxygen sensor.
(4) Run the engine until the engine coolant temperature
exceeds 80C.
(5) Using jumper wires, connect oxygen sensor terminal no.
1 (special tool red clip) and terminal no. 3 (special tool
blue clip) to battery (+) and (–) terminal, respectively.
Caution
Make sure of the correct connections: if a wrong
connection is made, a broken oxygen sensor results.
(6) Connect a digital voltmeter between terminal no. 2 (special
tool black clip) and terminal no. 4 (special tool white clip).
(7) Race the engine repeatedly to measure the oxygen sensor
output voltage.
Standard value:
EngineOxygen sensor
output voltageNOTE
When
engine is
raced0.6 – 1.0 VWhen engine racing is
repeated to enrich air-fuel
ratio, an operational oxygen
sensor should output a volt-
age of 0.6 to 1.0 V.
NOTE
Use the same procedures to remove and install the oxygen
sensor.
Red clip
Blue clip
MD998464
Red clip
Blue clip
MD998464 Black clip
White clip
Page 80 of 396
MPI – Throttle Body13-37
THROTTLE BODY
REMOVAL AND INSTALLATION
Pre-removal Operation
(1) Engine Coolant Draining
(2) Air Hose D Removal
(Refer to GROUP 15 – Intercooler.)
(3) Strut Tower Bar RemovalPost-installation Operation
(1) Strut Tower Bar Installation
(2) Air Hose D Installation
(Refer to GROUP 15 – Intercooler.)
(3) Engine Coolant Supplying
(4) Accelerator Cable Adjustment
34 2
61
7
19 {1.9}
5
Unit: Nm {kgfm}
5 {0.5}
Removal steps
1. Accelerator cable connection
2. Throttle position sensor connector
3. Idle speed control servo connector
4. Vacuum hose connection5. Water hose connection
6. Throttle body
A7. Throttle body gasket
INSTALLATION SERVICE POINT
ATHROTTLE BODY GASKET INSTALLATION
Place the gasket so that the projecting part is positioned
as shown in the illustration, and then install it between the
intake manifold and the throttle body.
Towards front
of vehicle
Up
Page 91 of 396
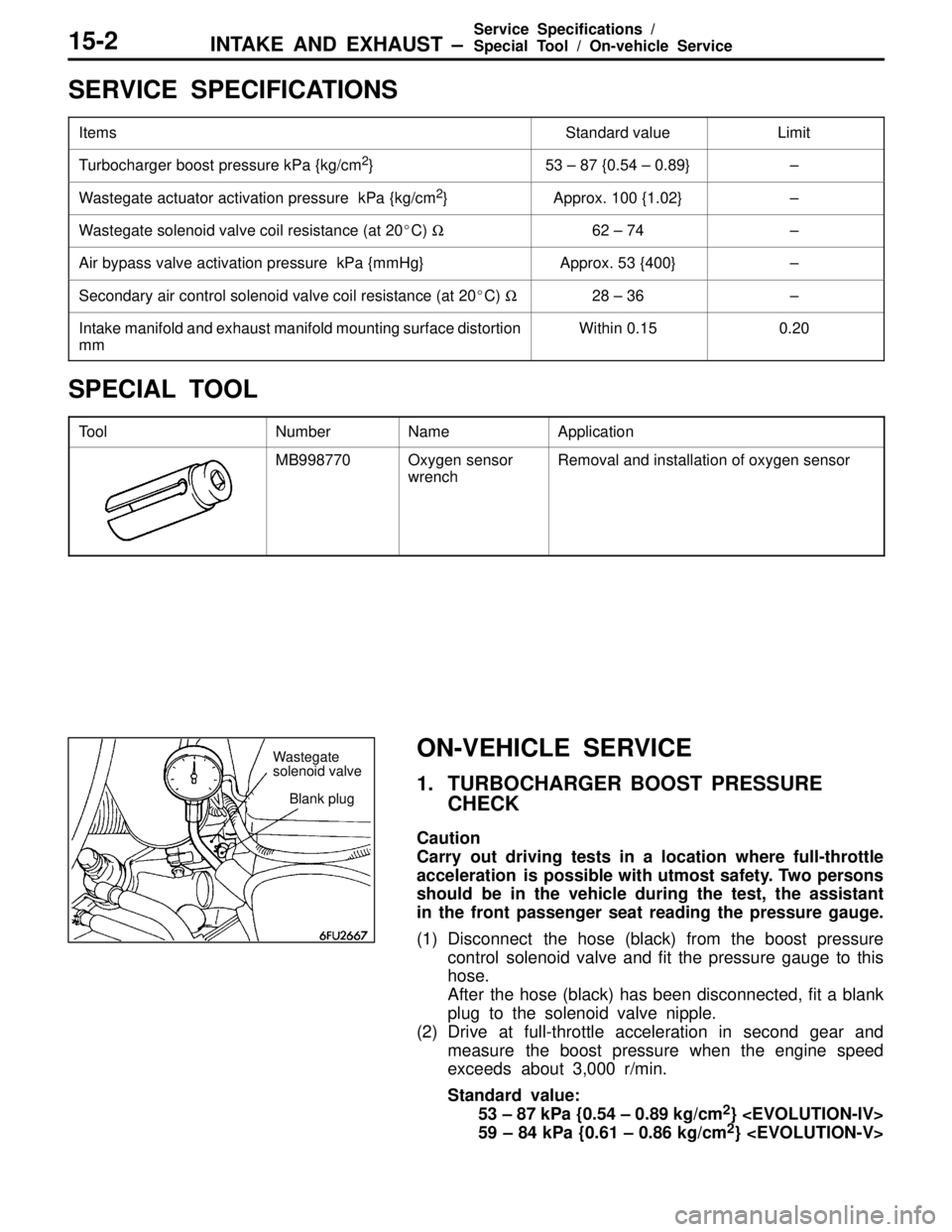
INTAKE AND EXHAUST –
Service Specifications /
Special Tool / On-vehicle Service15-2
SERVICE SPECIFICATIONS
ItemsStandard valueLimit
Turbocharger boost pressure kPa {kg/cm2}53 – 87 {0.54 – 0.89}–
Wastegate actuator activation pressure kPa {kg/cm2}Approx. 100 {1.02}–
Wastegate solenoid valve coil resistance (at 20C) Ω62 – 74–
Air bypass valve activation pressure kPa {mmHg}Approx. 53 {400}–
Secondary air control solenoid valve coil resistance (at 20C) Ω28 – 36–
Intake manifold and exhaust manifold mounting surface distortion
mmWithin 0.150.20
SPECIAL TOOL
ToolNumberNameApplication
MB998770Oxygen sensor
wrenchRemoval and installation of oxygen sensor
ON-VEHICLE SERVICE
1. TURBOCHARGER BOOST PRESSURE
CHECK
Caution
Carry out driving tests in a location where full-throttle
acceleration is possible with utmost safety. Two persons
should be in the vehicle during the test, the assistant
in the front passenger seat reading the pressure gauge.
(1) Disconnect the hose (black) from the boost pressure
control solenoid valve and fit the pressure gauge to this
hose.
After the hose (black) has been disconnected, fit a blank
plug to the solenoid valve nipple.
(2) Drive at full-throttle acceleration in second gear and
measure the boost pressure when the engine speed
exceeds about 3,000 r/min.
Standard value:
53 – 87 kPa {0.54 – 0.89 kg/cm
2}
59 – 84 kPa {0.61 – 0.86 kg/cm2}
Wastegate
solenoid valve
Blank plug
Page 98 of 396
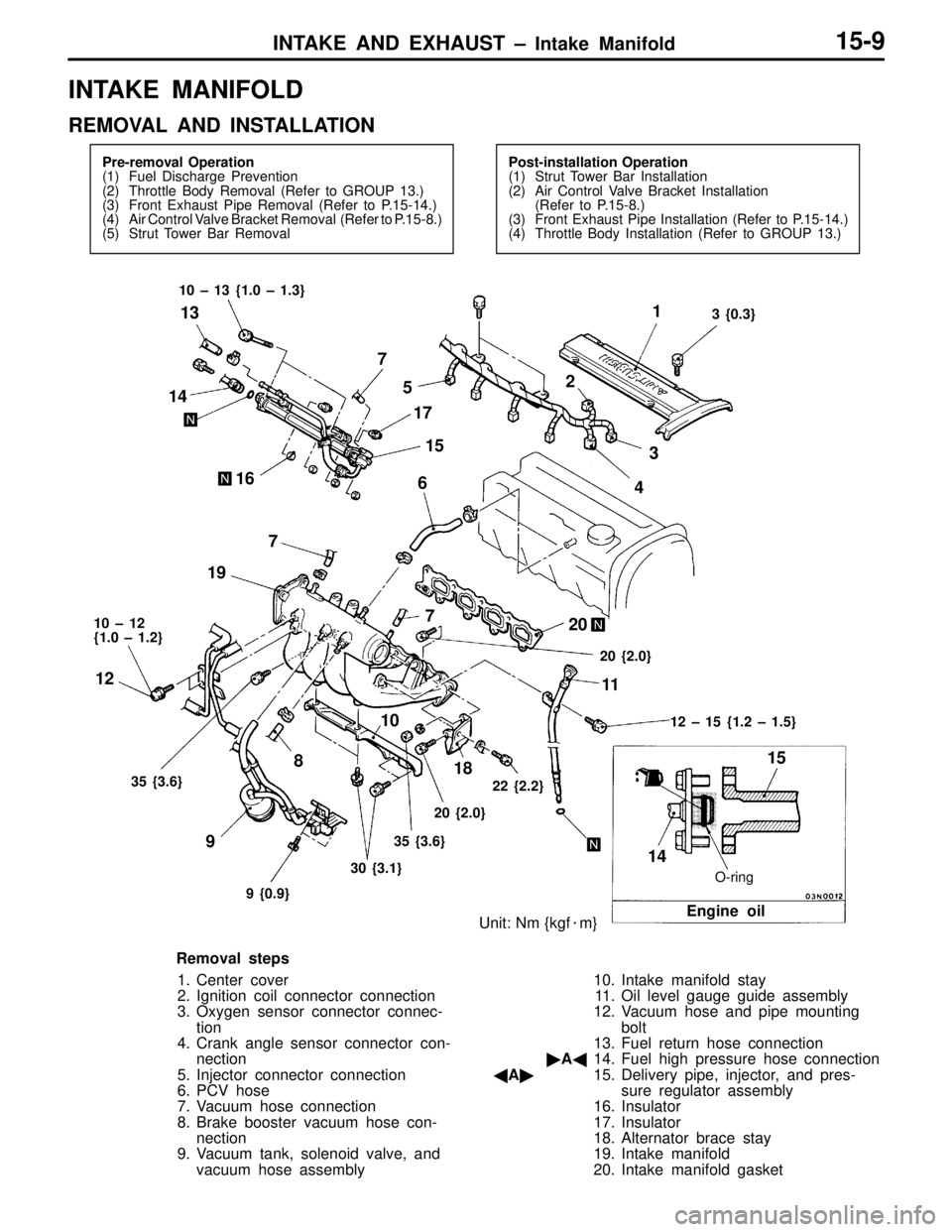
INTAKE AND EXHAUST – Intake Manifold15-9
INTAKE MANIFOLD
REMOVAL AND INSTALLATION
Pre-removal Operation
(1) Fuel Discharge Prevention
(2) Throttle Body Removal (Refer to GROUP 13.)
(3) Front Exhaust Pipe Removal (Refer to P.15-14.)
(4) Air Control Valve Bracket Removal (Refer to P.15-8.)
(5) Strut Tower Bar RemovalPost-installation Operation
(1) Strut Tower Bar Installation
(2) Air Control Valve Bracket Installation
(Refer to P.15-8.)
(3) Front Exhaust Pipe Installation (Refer to P.15-14.)
(4) Throttle Body Installation (Refer to GROUP 13.)
O-ring
Unit: Nm {kgfm}
15
Engine oil
3 {0.3} 10 – 13 {1.0 – 1.3}
10 – 12
{1.0 – 1.2}
12 – 15 {1.2 – 1.5}
35 {3.6}
9 {0.9}30 {3.1}35 {3.6}20 {2.0}22 {2.2}20 {2.0}
14 14
167
5
17
1521
3
4 6
7 7
19
20
18 8
9 12
1011
13
Removal steps
1. Center cover
2. Ignition coil connector connection
3. Oxygen sensor connector connec-
tion
4. Crank angle sensor connector con-
nection
5. Injector connector connection
6. PCV hose
7. Vacuum hose connection
8. Brake booster vacuum hose con-
nection
9. Vacuum tank, solenoid valve, and
vacuum hose assembly10. Intake manifold stay
11. Oil level gauge guide assembly
12. Vacuum hose and pipe mounting
bolt
13. Fuel return hose connection
A14. Fuel high pressure hose connection
A15. Delivery pipe, injector, and pres-
sure regulator assembly
16. Insulator
17. Insulator
18. Alternator brace stay
19. Intake manifold
20. Intake manifold gasket
Page 100 of 396
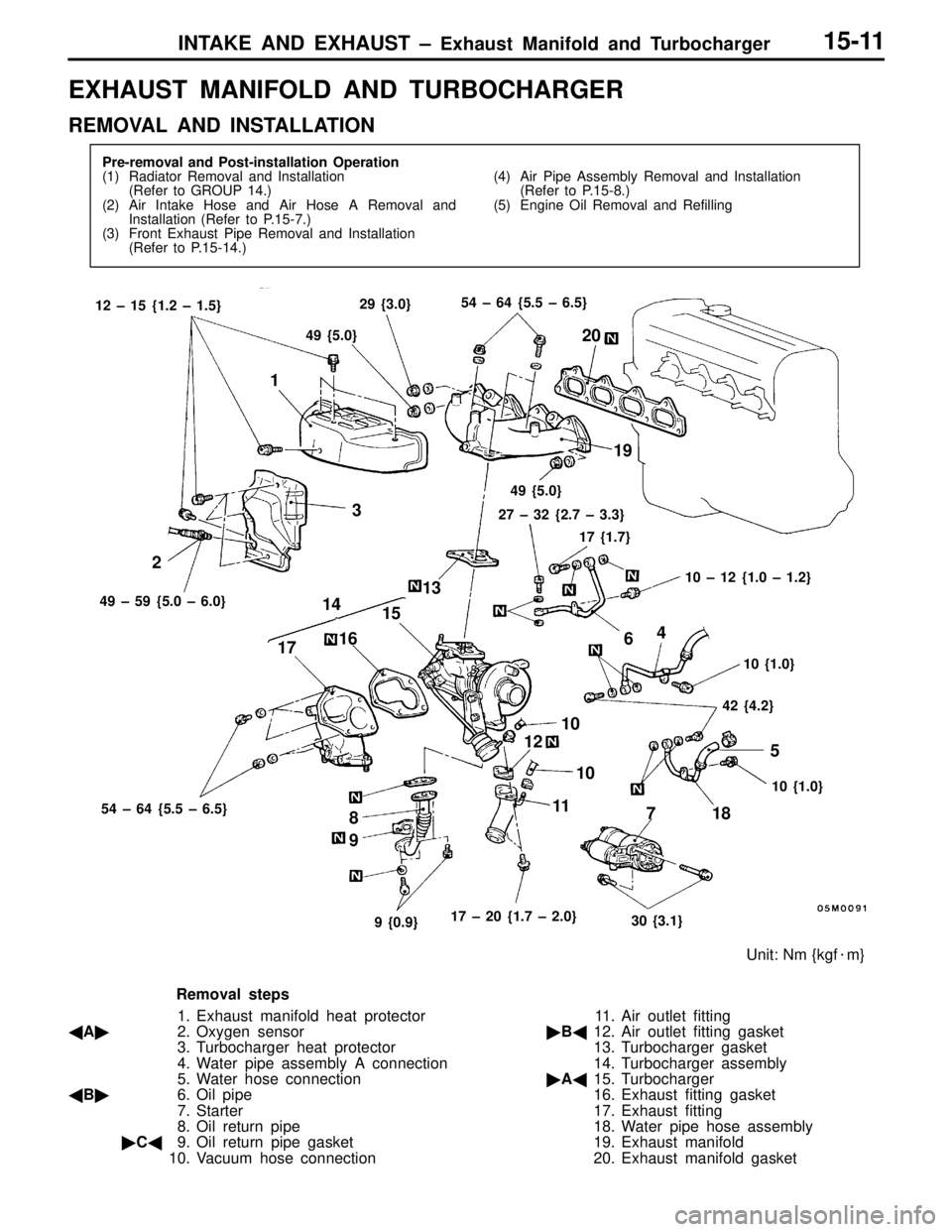
INTAKE AND EXHAUST – Exhaust Manifold and Turbocharger15-11
EXHAUST MANIFOLD AND TURBOCHARGER
REMOVAL AND INSTALLATION
Pre-removal and Post-installation Operation
(1) Radiator Removal and Installation
(Refer to GROUP 14.)
(2) Air Intake Hose and Air Hose A Removal and
Installation (Refer to P.15-7.)
(3) Front Exhaust Pipe Removal and Installation
(Refer to P.15-14.)(4) Air Pipe Assembly Removal and Installation
(Refer to P.15-8.)
(5) Engine Oil Removal and Refilling
1
Unit: Nm {kgfm}
49 {5.0}54 – 64 {5.5 – 6.5}
9 {0.9} 12 – 15 {1.2 – 1.5}
23
4
29 {3.0}
20
49 – 59 {5.0 – 6.0}
54 – 64 {5.5 – 6.5}
30 {3.1} 17 – 20 {1.7 – 2.0}10 {1.0} 42 {4.2}10 {1.0} 10 – 12 {1.0 – 1.2} 17 {1.7} 49 {5.0}
27 – 32 {2.7 – 3.3}
19
6
10
12
10
11
18 7
8
9 171615 1413
5
Removal steps
1. Exhaust manifold heat protector
A2. Oxygen sensor
3. Turbocharger heat protector
4. Water pipe assembly A connection
5. Water hose connection
B6. Oil pipe
7. Starter
8. Oil return pipe
C9. Oil return pipe gasket
10. Vacuum hose connection11. Air outlet fitting
B12. Air outlet fitting gasket
13. Turbocharger gasket
14. Turbocharger assembly
A15. Turbocharger
16. Exhaust fitting gasket
17. Exhaust fitting
18. Water pipe hose assembly
19. Exhaust manifold
20. Exhaust manifold gasket
Page 101 of 396
INTAKE AND EXHAUST – Exhaust Manifold and Turbocharger15-12
REMOVAL SERVICE POINTS
AOXYGEN SENSOR REMOVAL
BOIL PIPE REMOVAL
Caution
After the oil pipe has been removed, ensure that no foreign
matter will get into the oil passage holes in turbocharger.
INSTALLATION SERVICE POINTS
ATURBOCHARGER INSTALLATION
(1) Clean the connections between oil pipe, oil return pipe,
and water pipe.
Caution
Ensure that no foreign matter will get into the
turbocharger.
(2) Through the oil pipe mounting hole in the turbocharger,
add fresh engine oil.
BAIR OUTLET FITTING GASKET INSTALLATION
Install the gasket so that its tab is located as shown.
MB998770
Turbocharger
Ta b