Page 64 of 396
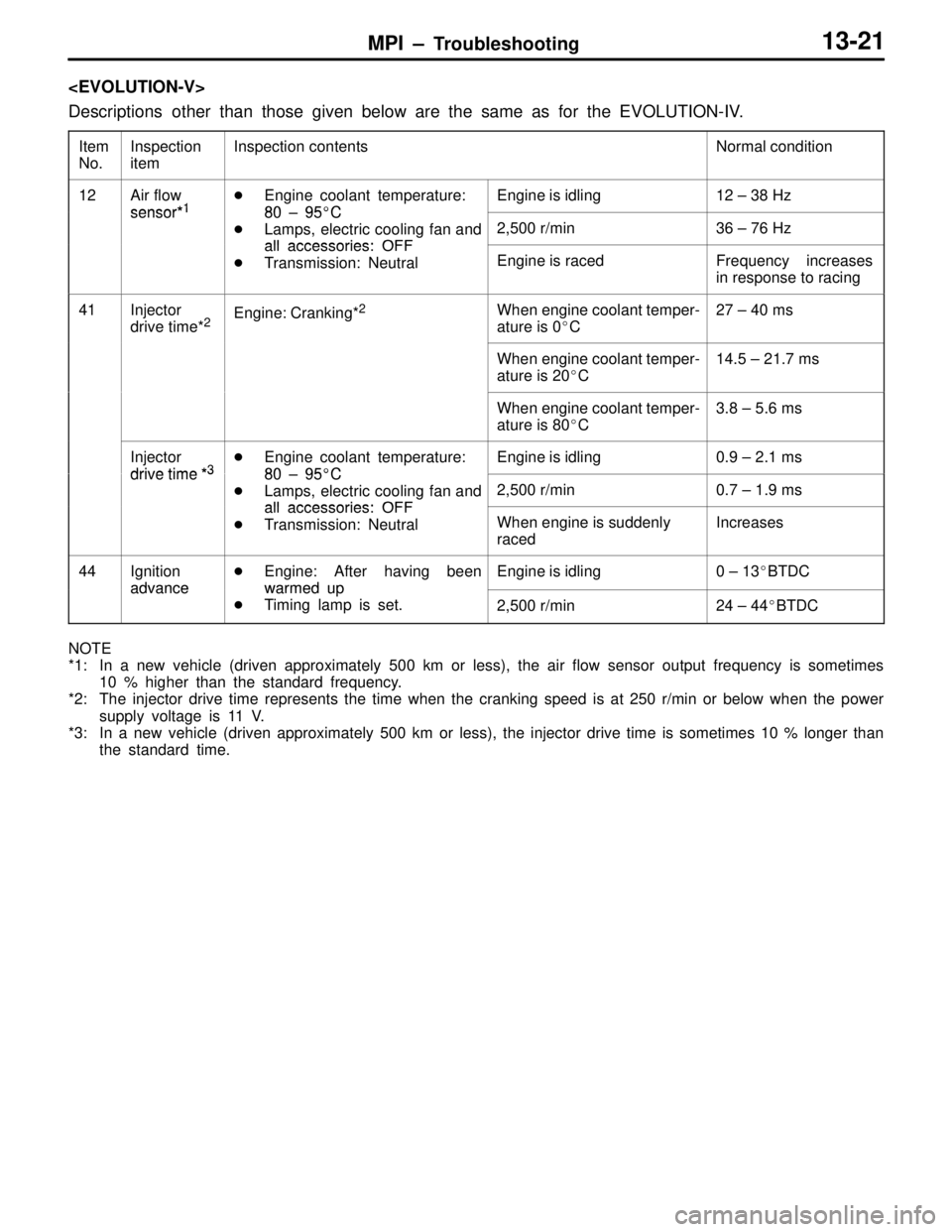
MPI – Troubleshooting13-21
Descriptions other than those given below are the same as for the EVOLUTION-IV.
Item
No.Inspection
itemInspection contentsNormal condition
12Air flow
sensor*1Engine coolant temperature:
80–95C
Engine is idling12 – 38 Hz
sensor*180 – 95C
Lamps, electric cooling fan and
all accessories: OFF
2,500 r/min36 – 76 Hz
all accessories: OFF
Transmission: NeutralEngine is racedFrequency increases
in response to racing
41Injector
drive time*2Engine: Cranking*2When engine coolant temper-
ature is 0C27 – 40 ms
When engine coolant temper-
ature is 20C14.5 – 21.7 ms
When engine coolant temper-
ature is 80C3.8 – 5.6 ms
Injector
drive time*3Engine coolant temperature:
8095C
Engine is idling0.9 – 2.1 ms
drive time *380 – 95C
Lamps, electric cooling fan and
all accessories: OFF
2,500 r/min0.7 – 1.9 ms
all accessories: OFF
Transmission: NeutralWhen engine is suddenly
racedIncreases
44Ignition
advance
Engine: After having been
warmed up
Engine is idling0 – 13BTDC
advancewarmed up
Timing lamp is set.2,500 r/min24 – 44BTDC
NOTE
*1: In a new vehicle (driven approximately 500 km or less), the air flow sensor output frequency is sometimes
10 % higher than the standard frequency.
*2: The injector drive time represents the time when the cranking speed is at 250 r/min or below when the power
supply voltage is 11 V.
*3: In a new vehicle (driven approximately 500 km or less), the injector drive time is sometimes 10 % longer than
the standard time.
Page 65 of 396
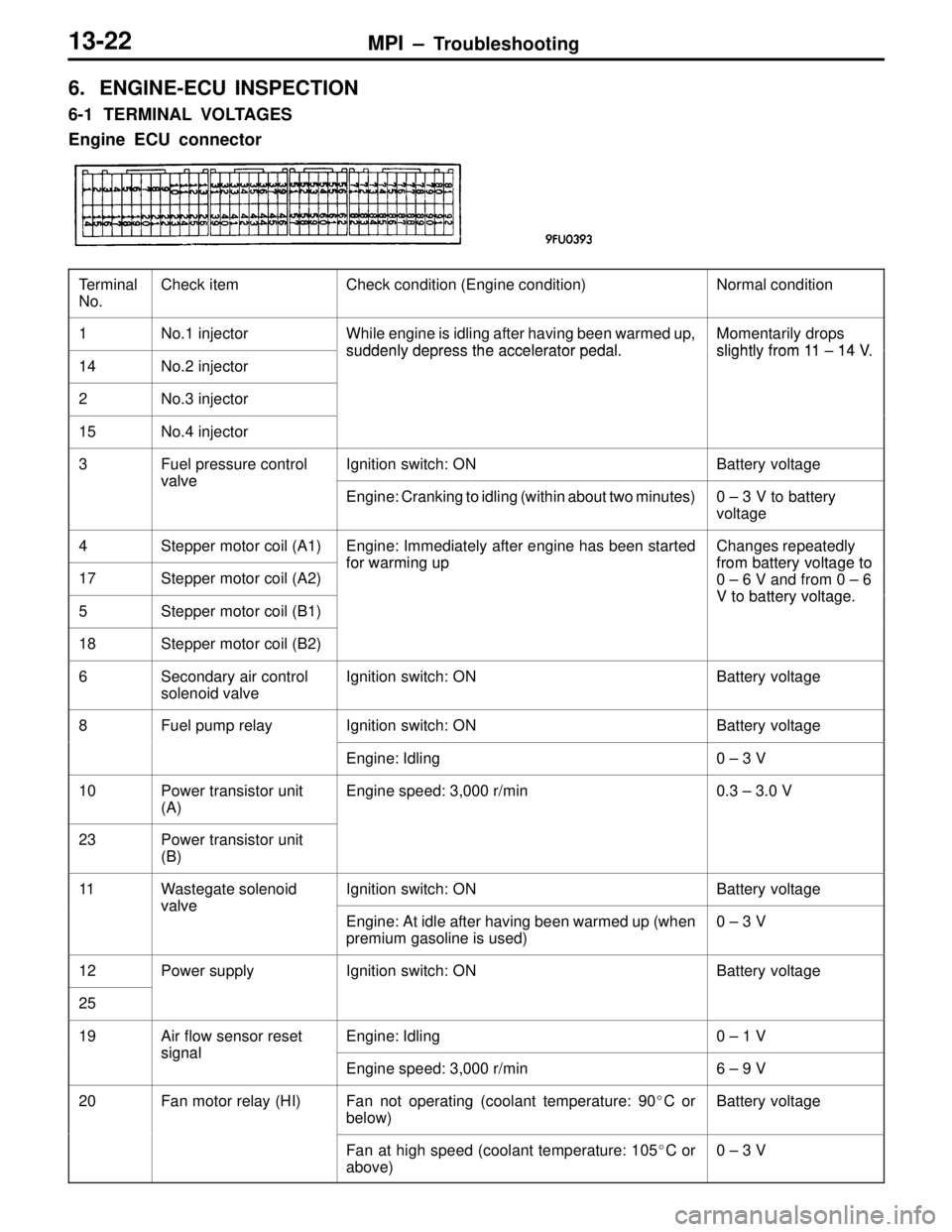
MPI – Troubleshooting13-22
6. ENGINE-ECU INSPECTION
6-1 TERMINAL VOLTAGES
Engine ECU connector
Terminal
No.Check itemCheck condition (Engine condition)Normal condition
1No.1 injectorWhile engine is idling after having been warmed up,
suddenly depress the accelerator pedal
Momentarily drops
slightlyfrom 1114V
14No.2 injector
suddenly depress the accelerator pedal.slightly from 11 – 14 V.
2No.3 injector
15No.4 injector
3Fuel pressure control
valve
Ignition switch: ONBattery voltage
valve
Engine: Cranking to idling (within about two minutes)0 – 3 V to battery
voltage
4Stepper motor coil (A1)Engine: Immediately after engine has been started
f
or warming up
Changes repeatedly
f
rom battery voltage to
17Stepper motor coil (A2)
for warming upfrom battery voltage to
0 – 6 V and from 0 – 6
V to battery voltage5Stepper motor coil (B1)V to battery voltage.
18Stepper motor coil (B2)
6Secondary air control
solenoid valveIgnition switch: ONBattery voltage
8Fuel pump relayIgnition switch: ONBattery voltage
Engine: Idling0 – 3 V
10Power transistor unit
(A)Engine speed: 3,000 r/min0.3 – 3.0 V
23Power transistor unit
(B)
11Wastegate solenoid
valve
Ignition switch: ONBattery voltage
valve
Engine: At idle after having been warmed up (when
premium gasoline is used)0 – 3 V
12Power supplyIgnition switch: ONBattery voltage
25
19Air flow sensor reset
signal
Engine: Idling0 – 1 V
signal
Engine speed: 3,000 r/min6 – 9 V
20Fan motor relay (HI)Fan not operating (coolant temperature: 90C or
below)Battery voltage
Fan at high speed (coolant temperature: 105C or
above)0 – 3 V
Page 66 of 396
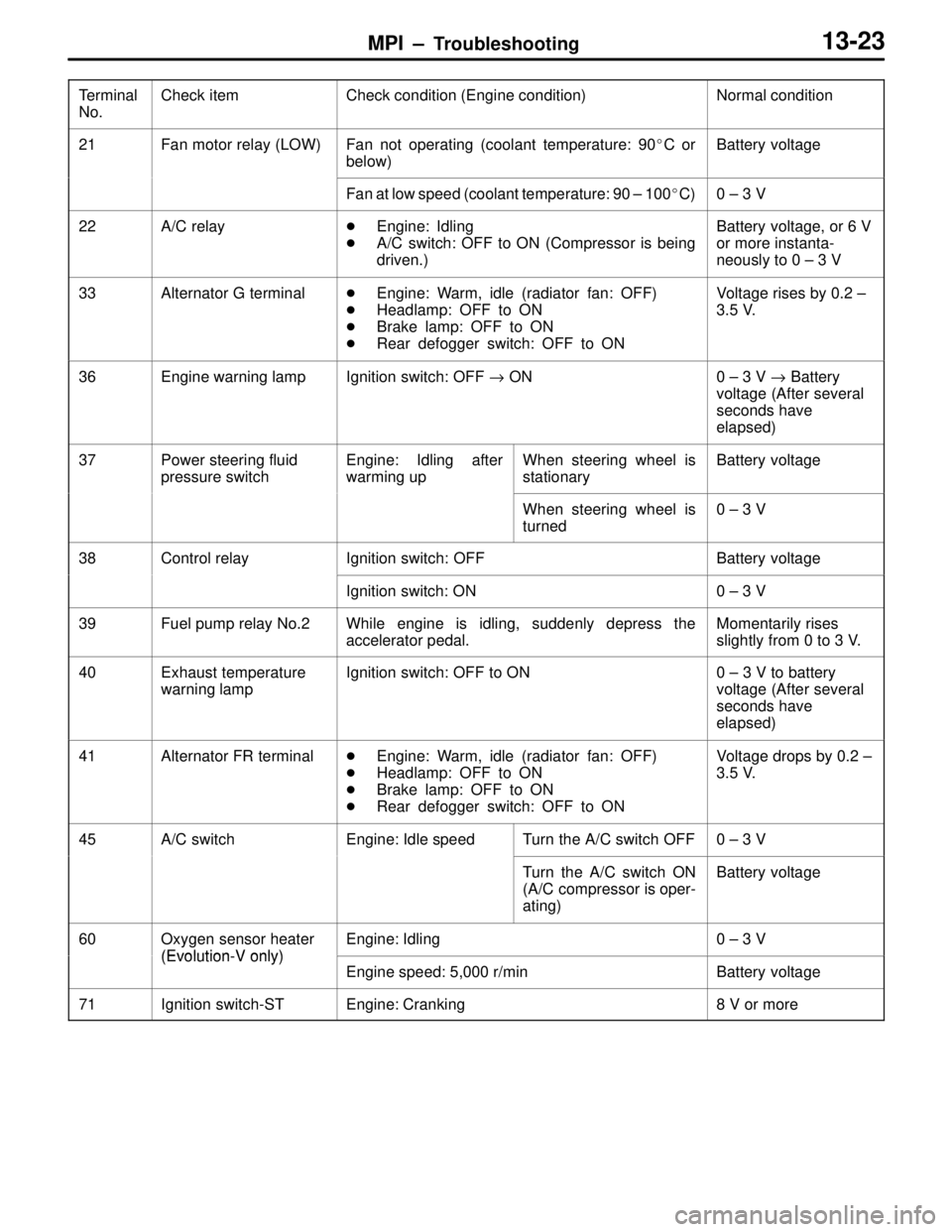
MPI – Troubleshooting13-23
Terminal
No.Normal condition Check condition (Engine condition) Check item
21Fan motor relay (LOW)Fan not operating (coolant temperature: 90C or
below)Battery voltage
Fan at low speed (coolant temperature: 90 – 100C)0 – 3 V
22A/C relayEngine: Idling
A/C switch: OFF to ON (Compressor is being
driven.)Battery voltage, or 6 V
or more instanta-
neously to 0 – 3 V
33Alternator G terminalEngine: Warm, idle (radiator fan: OFF)
Headlamp: OFF to ON
Brake lamp: OFF to ON
Rear defogger switch: OFF to ONVoltage rises by 0.2 –
3.5 V.
36Engine warning lampIgnition switch: OFF → ON0 – 3 V → Battery
voltage (After several
seconds have
elapsed)
37Power steering fluid
pressure switchEngine: Idling after
warming upWhen steering wheel is
stationaryBattery voltage
When steering wheel is
turned0 – 3 V
38Control relayIgnition switch: OFFBattery voltage
Ignition switch: ON0 – 3 V
39Fuel pump relay No.2While engine is idling, suddenly depress the
accelerator pedal.Momentarily rises
slightly from 0 to 3 V.
40Exhaust temperature
warning lampIgnition switch: OFF to ON0 – 3 V to battery
voltage (After several
seconds have
elapsed)
41Alternator FR terminalEngine: Warm, idle (radiator fan: OFF)
Headlamp: OFF to ON
Brake lamp: OFF to ON
Rear defogger switch: OFF to ONVoltage drops by 0.2 –
3.5 V.
45A/C switchEngine: Idle speedTurn the A/C switch OFF0 – 3 V
Turn the A/C switch ON
(A/C compressor is oper-
ating)Battery voltage
60Oxygen sensor heater
(Evolution V only)
Engine: Idling0 – 3 V
(Evolution-V only)
Engine speed: 5,000 r/minBattery voltage
71Ignition switch-STEngine: Cranking8 V or more
Page 67 of 396
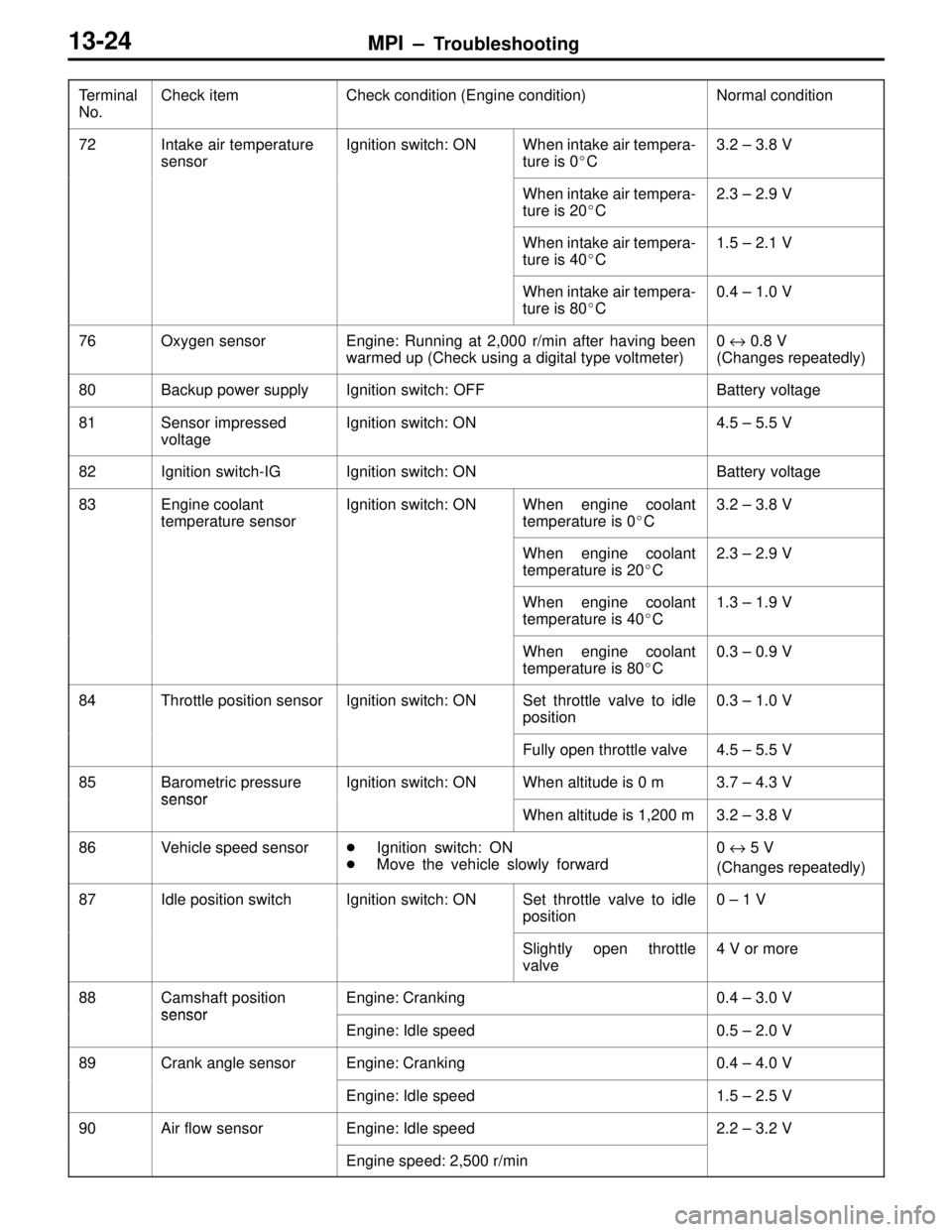
MPI – Troubleshooting13-24
Terminal
No.Normal condition Check condition (Engine condition) Check item
72Intake air temperature
sensorIgnition switch: ONWhen intake air tempera-
ture is 0C3.2 – 3.8 V
When intake air tempera-
ture is 20C2.3 – 2.9 V
When intake air tempera-
ture is 40C1.5 – 2.1 V
When intake air tempera-
ture is 80C0.4 – 1.0 V
76Oxygen sensorEngine: Running at 2,000 r/min after having been
warmed up (Check using a digital type voltmeter)0 ↔ 0.8 V
(Changes repeatedly)
80Backup power supplyIgnition switch: OFFBattery voltage
81Sensor impressed
voltageIgnition switch: ON4.5 – 5.5 V
82Ignition switch-IGIgnition switch: ONBattery voltage
83Engine coolant
temperature sensorIgnition switch: ONWhen engine coolant
temperature is 0C3.2 – 3.8 V
When engine coolant
temperature is 20C2.3 – 2.9 V
When engine coolant
temperature is 40C1.3 – 1.9 V
When engine coolant
temperature is 80C0.3 – 0.9 V
84Throttle position sensorIgnition switch: ONSet throttle valve to idle
position0.3 – 1.0 V
Fully open throttle valve4.5 – 5.5 V
85Barometric pressure
sensor
Ignition switch: ONWhen altitude is 0 m3.7 – 4.3 V
sensor
When altitude is 1,200 m3.2 – 3.8 V
86Vehicle speed sensorIgnition switch: ON
Move the vehicle slowly forward0 ↔ 5 V
(Changes repeatedly)
87Idle position switchIgnition switch: ONSet throttle valve to idle
position0 – 1 V
Slightly open throttle
valve4 V or more
88Camshaft position
sensor
Engine: Cranking0.4 – 3.0 V
sensor
Engine: Idle speed0.5 – 2.0 V
89Crank angle sensorEngine: Cranking0.4 – 4.0 V
Engine: Idle speed1.5 – 2.5 V
90Air flow sensorEngine: Idle speed2.2 – 3.2 V
Engine speed: 2,500 r/min
Page 72 of 396
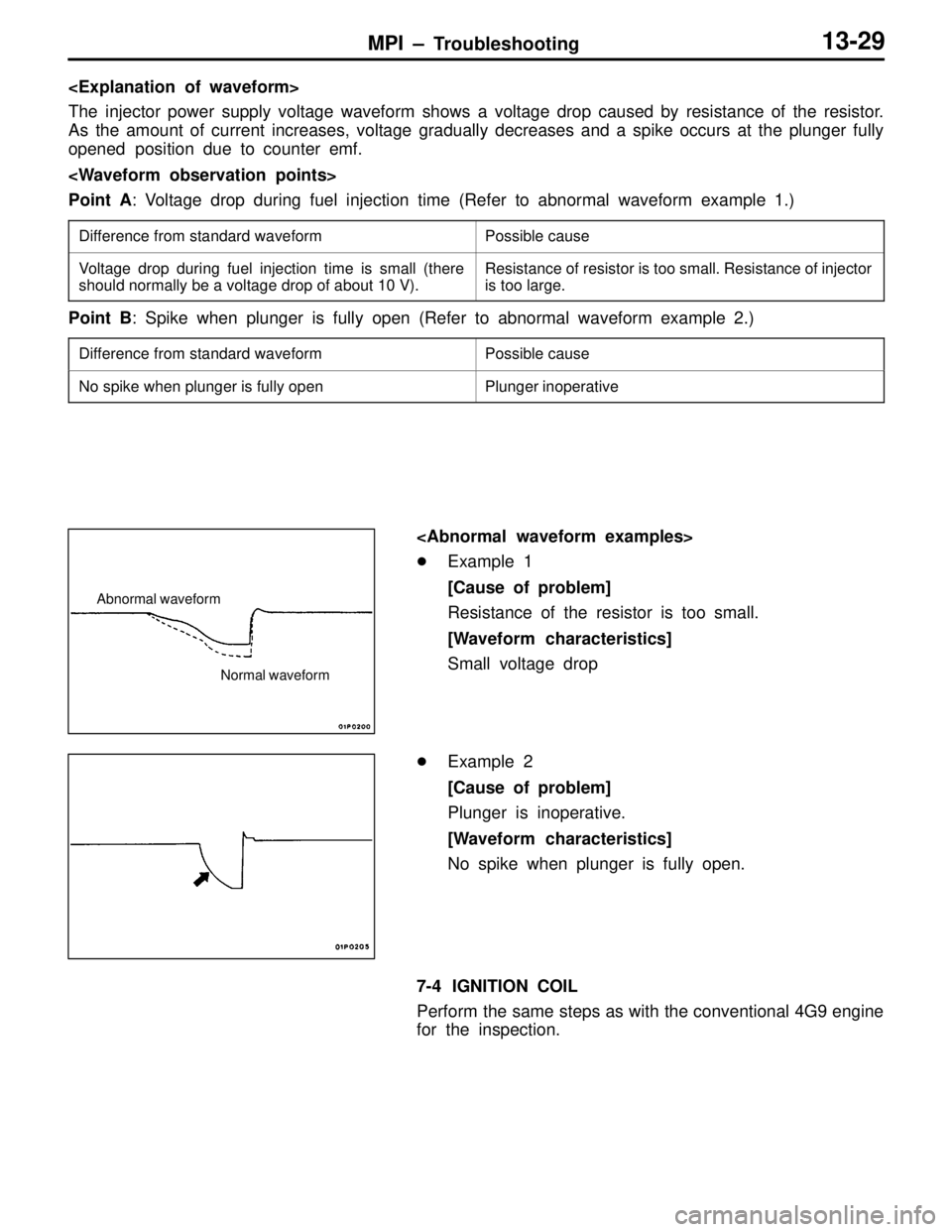
MPI – Troubleshooting13-29
The injector power supply voltage waveform shows a voltage drop caused by resistance of the resistor.
As the amount of current increases, voltage gradually decreases and a spike occurs at the plunger fully
opened position due to counter emf.
Point A: Voltage drop during fuel injection time (Refer to abnormal waveform example 1.)
Difference from standard waveformPossible cause
Voltage drop during fuel injection time is small (there
should normally be a voltage drop of about 10 V).Resistance of resistor is too small. Resistance of injector
is too large.
Point B: Spike when plunger is fully open (Refer to abnormal waveform example 2.)
Difference from standard waveformPossible cause
No spike when plunger is fully openPlunger inoperative
Example 1
[Cause of problem]
Resistance of the resistor is too small.
[Waveform characteristics]
Small voltage drop
Example 2
[Cause of problem]
Plunger is inoperative.
[Waveform characteristics]
No spike when plunger is fully open.
7-4 IGNITION COIL
Perform the same steps as with the conventional 4G9 engine
for the inspection.
Abnormal waveform
Normal waveform
Page 74 of 396
MPI – On-vehicle Service13-31
5. MPI SYSTEM COMPONENTS LAYOUT
NameSymbolNameSymbol
A/C switchQExhaust temperature warning lampS
A/C relayHFuel pressure control valveA
Air flow sensor (with a built-in intake air temperaturesensor and barometric pressure sensor)FIgnition coil and power transistor unitLsensor and barometric pressure sensor)InjectorB
Camshaft position sensorMISC servoD
Control relay and fuel pump relayPOxygen sensorK
Coolant temperature sensorEPower steering fluid pressure switchI
Crank angle sensorJSecondary air control solenoid valveN
Detonation sensorCThrottle position sensor (with a built-in idle switch)D
Diagnosis connectorR
Engine ECUOVehicle speed sensorT
Engine warning lampSWastegate solenoid valveG
Page 92 of 396
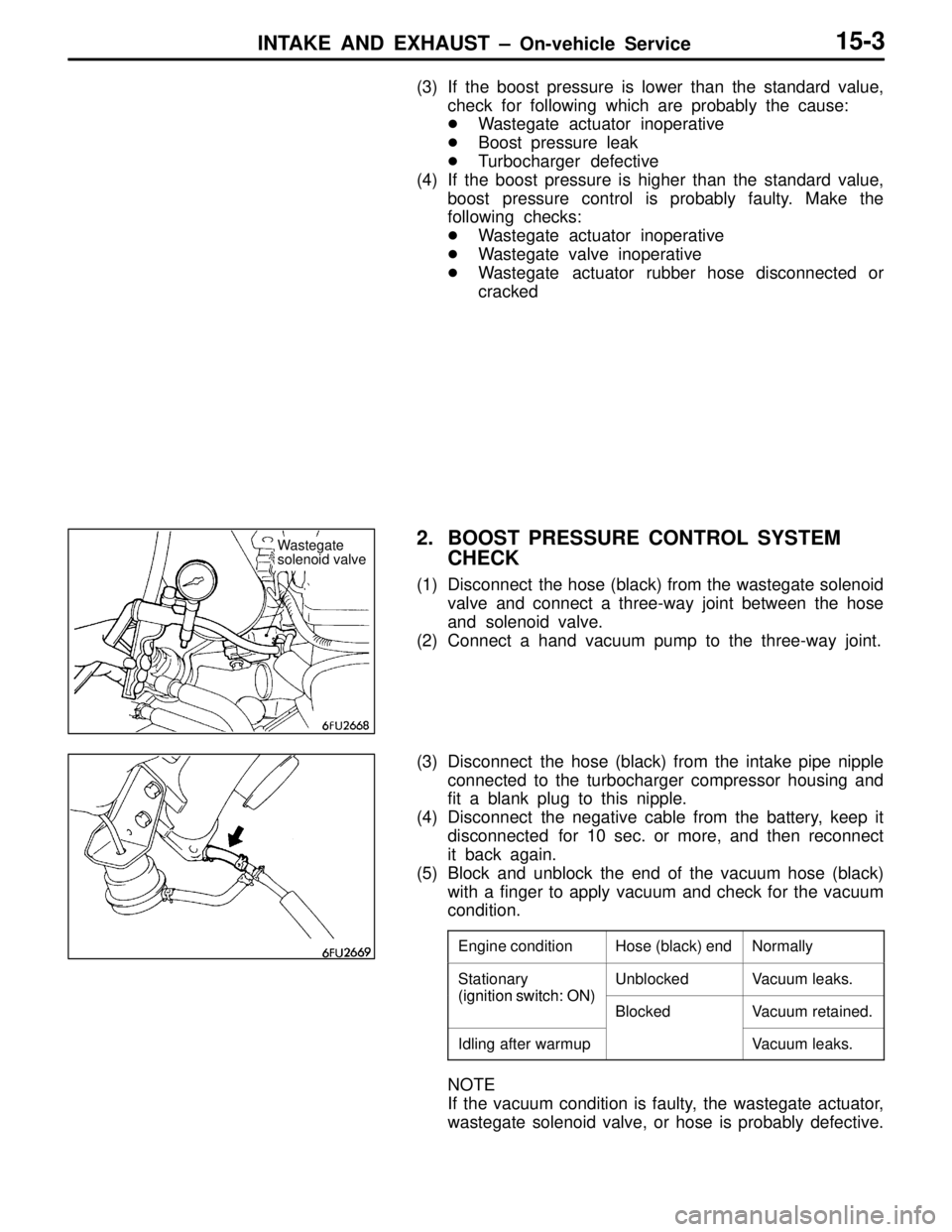
INTAKE AND EXHAUST – On-vehicle Service15-3
(3) If the boost pressure is lower than the standard value,
check for following which are probably the cause:
Wastegate actuator inoperative
Boost pressure leak
Turbocharger defective
(4) If the boost pressure is higher than the standard value,
boost pressure control is probably faulty. Make the
following checks:
Wastegate actuator inoperative
Wastegate valve inoperative
Wastegate actuator rubber hose disconnected or
cracked
2. BOOST PRESSURE CONTROL SYSTEM
CHECK
(1) Disconnect the hose (black) from the wastegate solenoid
valve and connect a three-way joint between the hose
and solenoid valve.
(2) Connect a hand vacuum pump to the three-way joint.
(3) Disconnect the hose (black) from the intake pipe nipple
connected to the turbocharger compressor housing and
fit a blank plug to this nipple.
(4) Disconnect the negative cable from the battery, keep it
disconnected for 10 sec. or more, and then reconnect
it back again.
(5) Block and unblock the end of the vacuum hose (black)
with a finger to apply vacuum and check for the vacuum
condition.
Engine conditionHose (black) endNormally
Stationary
(ignition switch: ON)
UnblockedVacuum leaks.
(ignition switch: ON)
BlockedVacuum retained.
Idling after warmupVacuum leaks.
NOTE
If the vacuum condition is faulty, the wastegate actuator,
wastegate solenoid valve, or hose is probably defective.
Wastegate
solenoid valve
Page 98 of 396
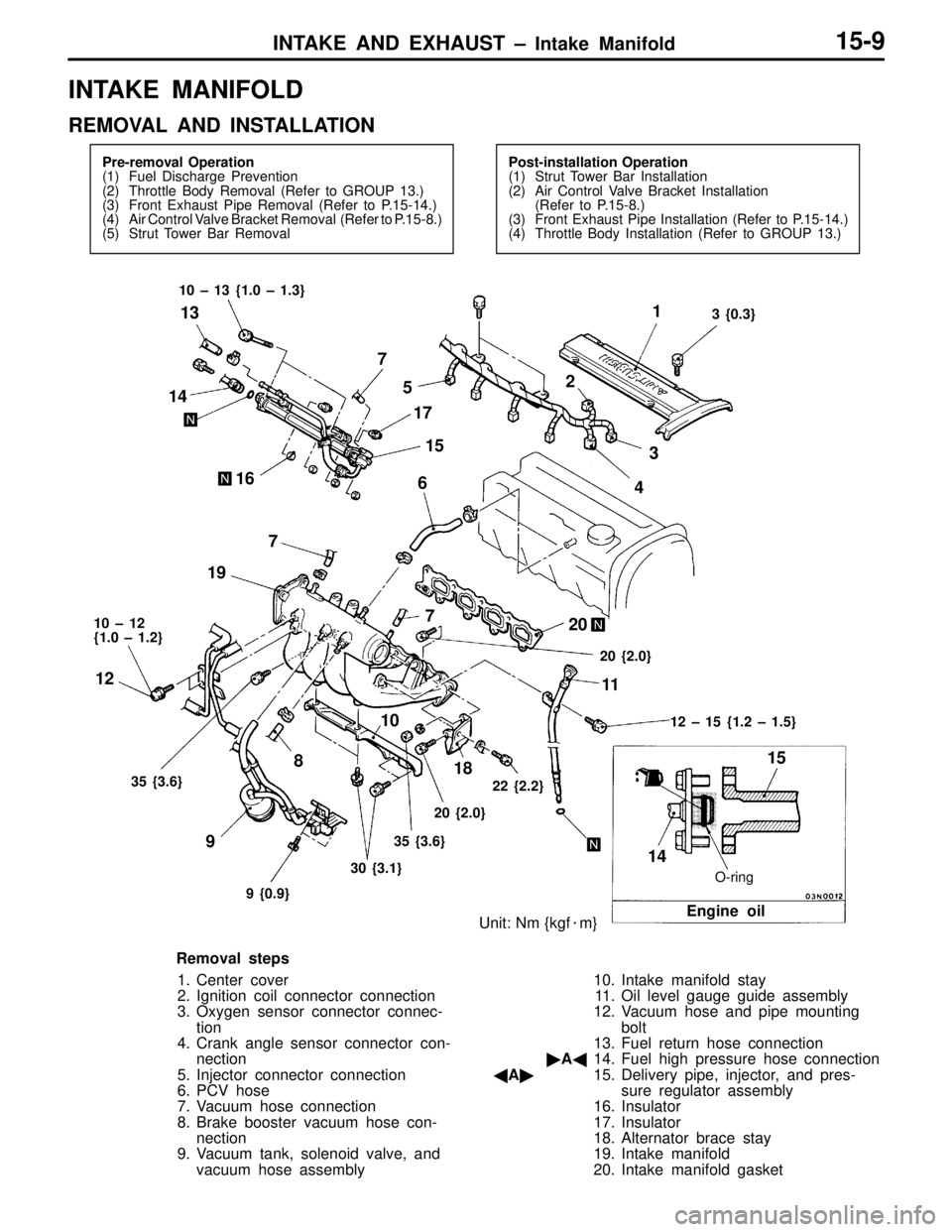
INTAKE AND EXHAUST – Intake Manifold15-9
INTAKE MANIFOLD
REMOVAL AND INSTALLATION
Pre-removal Operation
(1) Fuel Discharge Prevention
(2) Throttle Body Removal (Refer to GROUP 13.)
(3) Front Exhaust Pipe Removal (Refer to P.15-14.)
(4) Air Control Valve Bracket Removal (Refer to P.15-8.)
(5) Strut Tower Bar RemovalPost-installation Operation
(1) Strut Tower Bar Installation
(2) Air Control Valve Bracket Installation
(Refer to P.15-8.)
(3) Front Exhaust Pipe Installation (Refer to P.15-14.)
(4) Throttle Body Installation (Refer to GROUP 13.)
O-ring
Unit: Nm {kgfm}
15
Engine oil
3 {0.3} 10 – 13 {1.0 – 1.3}
10 – 12
{1.0 – 1.2}
12 – 15 {1.2 – 1.5}
35 {3.6}
9 {0.9}30 {3.1}35 {3.6}20 {2.0}22 {2.2}20 {2.0}
14 14
167
5
17
1521
3
4 6
7 7
19
20
18 8
9 12
1011
13
Removal steps
1. Center cover
2. Ignition coil connector connection
3. Oxygen sensor connector connec-
tion
4. Crank angle sensor connector con-
nection
5. Injector connector connection
6. PCV hose
7. Vacuum hose connection
8. Brake booster vacuum hose con-
nection
9. Vacuum tank, solenoid valve, and
vacuum hose assembly10. Intake manifold stay
11. Oil level gauge guide assembly
12. Vacuum hose and pipe mounting
bolt
13. Fuel return hose connection
A14. Fuel high pressure hose connection
A15. Delivery pipe, injector, and pres-
sure regulator assembly
16. Insulator
17. Insulator
18. Alternator brace stay
19. Intake manifold
20. Intake manifold gasket