Page 259 of 3573
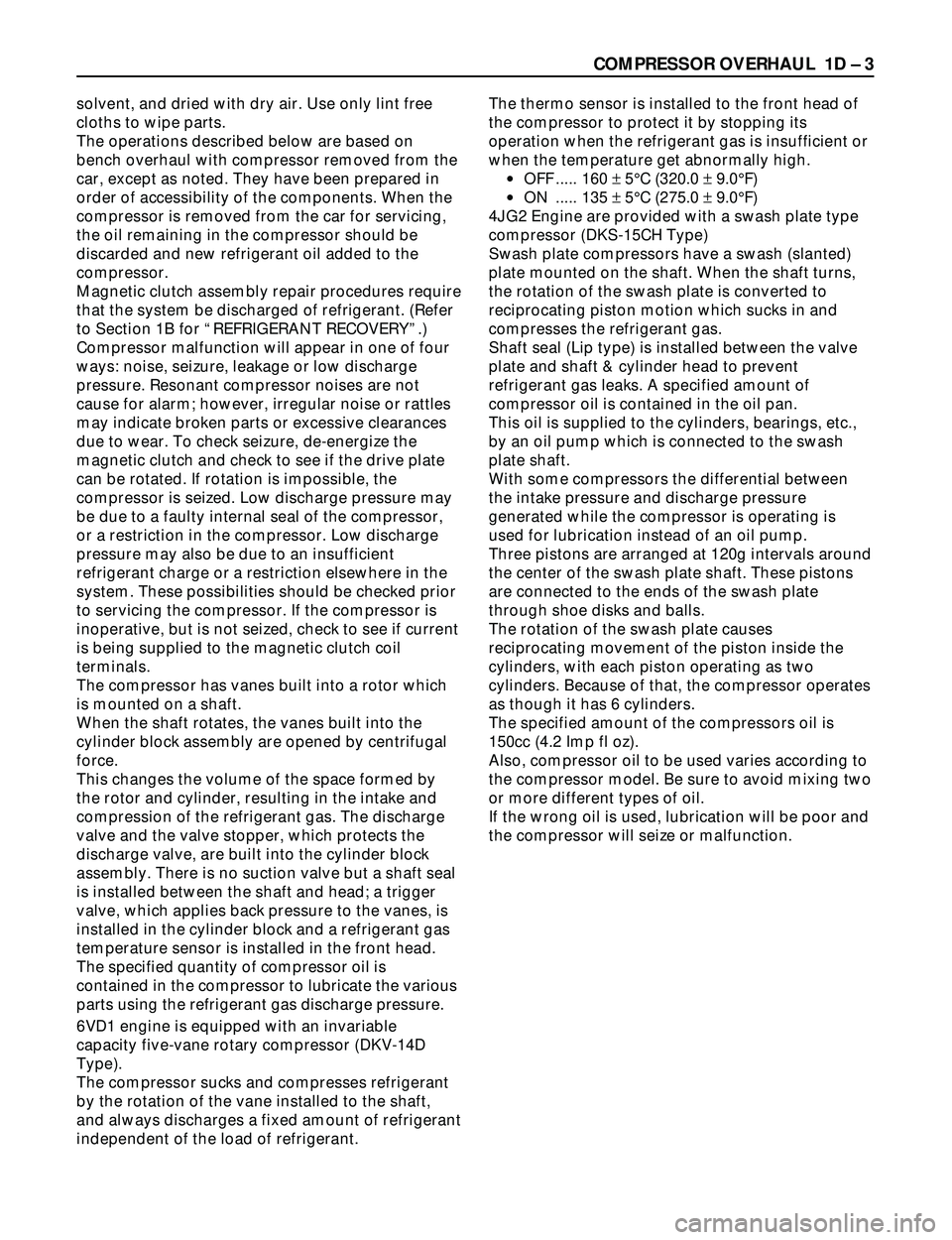
COMPRESSOR OVERHAUL 1D Ð 3
solvent, and dried with dry air. Use only lint free
cloths to wipe parts.
The operations described below are based on
bench overhaul with compressor removed from the
car, except as noted. They have been prepared in
order of accessibility of the components. When the
compressor is removed from the car for servicing,
the oil remaining in the compressor should be
discarded and new refrigerant oil added to the
compressor.
Magnetic clutch assembly repair procedures require
that the system be discharged of refrigerant. (Refer
to Section 1B for ÒREFRIGERANT RECOVERYÓ.)
Compressor malfunction will appear in one of four
ways: noise, seizure, leakage or low discharge
pressure. Resonant compressor noises are not
cause for alarm; however, irregular noise or rattles
may indicate broken parts or excessive clearances
due to wear. To check seizure, de-energize the
magnetic clutch and check to see if the drive plate
can be rotated. If rotation is impossible, the
compressor is seized. Low discharge pressure may
be due to a faulty internal seal of the compressor,
or a restriction in the compressor. Low discharge
pressure may also be due to an insufficient
refrigerant charge or a restriction elsewhere in the
system. These possibilities should be checked prior
to servicing the compressor. If the compressor is
inoperative, but is not seized, check to see if current
is being supplied to the magnetic clutch coil
terminals.
The compressor has vanes built into a rotor which
is mounted on a shaft.
When the shaft rotates, the vanes built into the
cylinder block assembly are opened by centrifugal
force.
This changes the volume of the space formed by
the rotor and cylinder, resulting in the intake and
compression of the refrigerant gas. The discharge
valve and the valve stopper, which protects the
discharge valve, are built into the cylinder block
assembly. There is no suction valve but a shaft seal
is installed between the shaft and head; a trigger
valve, which applies back pressure to the vanes, is
installed in the cylinder block and a refrigerant gas
temperature sensor is installed in the front head.
The specified quantity of compressor oil is
contained in the compressor to lubricate the various
parts using the refrigerant gas discharge pressure.
6VD1 engine is equipped with an invariable
capacity five-vane rotary compressor (DKV-14D
Type).
The compressor sucks and compresses refrigerant
by the rotation of the vane installed to the shaft,
and always discharges a fixed amount of refrigerant
independent of the load of refrigerant.The thermo sensor is installed to the front head of
the compressor to protect it by stopping its
operation when the refrigerant gas is insufficient or
when the temperature get abnormally high.
·OFF ..... 160 ±5¡C (320.0 ±9.0¡F)
·ON ..... 135 ±5¡C (275.0 ±9.0¡F)
4JG2 Engine are provided with a swash plate type
compressor (DKS-15CH Type)
Swash plate compressors have a swash (slanted)
plate mounted on the shaft. When the shaft turns,
the rotation of the swash plate is converted to
reciprocating piston motion which sucks in and
compresses the refrigerant gas.
Shaft seal (Lip type) is installed between the valve
plate and shaft & cylinder head to prevent
refrigerant gas leaks. A specified amount of
compressor oil is contained in the oil pan.
This oil is supplied to the cylinders, bearings, etc.,
by an oil pump which is connected to the swash
plate shaft.
With some compressors the differential between
the intake pressure and discharge pressure
generated while the compressor is operating is
used for lubrication instead of an oil pump.
Three pistons are arranged at 120g intervals around
the center of the swash plate shaft. These pistons
are connected to the ends of the swash plate
through shoe disks and balls.
The rotation of the swash plate causes
reciprocating movement of the piston inside the
cylinders, with each piston operating as two
cylinders. Because of that, the compressor operates
as though it has 6 cylinders.
The specified amount of the compressors oil is
150cc (4.2 Imp fl oz).
Also, compressor oil to be used varies according to
the compressor model. Be sure to avoid mixing two
or more different types of oil.
If the wrong oil is used, lubrication will be poor and
the compressor will seize or malfunction.
Page 398 of 3573
3C – 10 FRONT SUSPENSION
KNUCKLE
Removal Steps
1. Torsion bar
2. Wheel speed sensor
(if equipped with ABS)
3. Back plate
4. Lower ball joint
5. Upper ball joint
6. Knuckle assembly
7. Oil seal
8. Thrust washer
9. Needle bearing
10. Knuckle
Installation Steps
10. Knuckle
9. Needle bearing
8. Thrust washer
7. Oil seal
6. Knuckle assembly
5. Upper ball joint
4. Lower ball joint
3. Back plate
2. Wheel speed sensor
(if equipped with ABS)
1. Torsion bar
Page 399 of 3573
FRONT SUSPENSION 3C – 11
REMOVAL
Preparation:
1) Raise the vehicle and support the frame with suitable
safety stands.
2) Remove wheel and tire assembly. Refer to “Wheels
and Tires” in section 3E.
3) Remove the brake caliper. Refer to “Brakes” in section
5.
4) Remove the hub assembly. Refer to “Hub and Disk” in
section 4C.
5) Remove outer track rod from the knuckle. Refer to
“Steering Linkage” in section 2A.
1. Torsion Bar
Loosen torsion bar by height control arm adjust bolt.
Refer to “Torsion bar” in this section.
2. Wheel speed sensor (if equipped with ABS)
3. Back Plate
4. Lower Ball Joint
Remover: 5-8840-2005-0 (J-29107)
CAUTION:
Be careful not to break the ball joint boot.
5. Upper Ball Joint
Remover: 5-8840-2121-0 (J-36831)
CAUTION:
Be careful not to break the ball joint boot.
6. Knuckle Assembly
7. Oil Seal
8. Washer
9. Needle Bearing
Remover: 5-8840-0019-0 (J-23907)
Page 401 of 3573
FRONT SUSPENSION 3C – 13
4. Lower Ball Joint
Tighten the nut to the specified torque, with just
enough additional torque to align cotter pin holes.
Install new cotter pin.
Lower Ball Joint Nut Torque N·m (kg·m/lb·ft)
147 (15.0 / 108)
3. Back Plate
2. Wheel Speed Sensor (if equipped with ABS)
Tighten the bolt to the specified torque.
Wheel Speed Sensor Bolt Torque N·m (kg·m/lb·in)
8 (0.8 / 69)
1. Torsion Bar
Refer to “Torsion Bar” in this section.
NOTE:
Adjust the trim height. Refer to “Front End
Alignment” in section 2A.
Page 402 of 3573
3C – 14 FRONT SUSPENSION
UPPER CONTROL ARM
Removal Steps
1. Speed sensor cable (if equipped with
ABS)
2. Nut and cotter pin
3. Upper ball joint
4. Bolt and plate
5. Nut assembly
6. Camber shims
7. Caster shims
8. Upper control arm assembly
9. Nut
10. Plate
11. Bushing
12. Fulcrum pin
Installation Steps
12. Fulcrum pin
11. Bushing
10. Plate
9. Nut
8. Upper control arm assembly
7. Caster shims
6. Camber shims
5. Nut assembly
4. Bolt and plate
3. Upper ball joint
2. Nut and cotter pin
1. Speed sensor cable (if equipped with
ABS)
Page 403 of 3573
FRONT SUSPENSION 3C – 15
REMOVAL
Preparation:
1) Raise the vehicle and support the frame with suitable
safety stands.
2) Remove wheel and tire assembly. Refer to “Wheels
and Tires” in section 3E.
3) Remove the brake caliper and disconnect flexible hose.
Refer to “Brakes” in section 5.
4) Support lower control arm with a jack.
1. Speed Sensor Cable (if equipped with ABS)
2. Nut and Cotter Pin
Remove the upper ball joint from the knuckle.
Remover: 5-8840-2121-0 (J-36831)
CAUTION:
Be careful not to break the ball joint boot.
3. Upper Ball Joint
4. Bolt and Plate
5. Nut Assembly
6. Camber Shims
Note the positions and number of shims.
7. Caster Shims
Note the positions and number of shims.
8. Upper Control Arm Assembly
9. Nut
10. Plate
11. Bushing
Remover: 5-8840-0256-0 (J-29755)
12. Fulcrum Pin
Page 405 of 3573
FRONT SUSPENSION 3C – 17
8. Upper Control Arm Assembly
Install upper control arm assembly with the fulcrum
pin projections turned inward.
7. Caster Shims
Install the caster shims between the chassis frame and
fulcrum pin.
6. Camber Shims
Install the camber shims between the chassis frame
and fulcrum pin.
5. Nut Assembly
4. Bolt and Plate
Fulcrum Pin Bolt Torque N·m (kg·m/lb·ft)
152 (15.2 / 112)
3. Upper Ball Joint
Upper Ball Joint Nut Torque N·m (kg·m/lb·ft)
57 (5.8 / 42)
2. Nut and Cotter Pin
Tighten the nut to the specified torque, with just
enough additional torque to align cotter pin holes.
Install new cotter pin.
Upper Ball Joint Nut Torque N·m (kg·m/lb·ft)
98 (10.0 / 72)
1. Speed Sensor Cable (if equipped with ABS)
Page 410 of 3573
3C – 22 FRONT SUSPENSION
UPPER BALL JOINT
Removal Steps
1. Nut and cotter pin
2. Bolt, nut and washer
3. Upper ball joint
Installation Steps
3. Upper ball joint
2. Bolt, nut and washer
1. Nut and cotter pin
REMOVAL
Preparation:
1) Raise the vehicle and support the frame with suitable
safety stands.
2) Remove the speed sensor from the knuckle (If
equipped with ABS).