Page 27 of 873
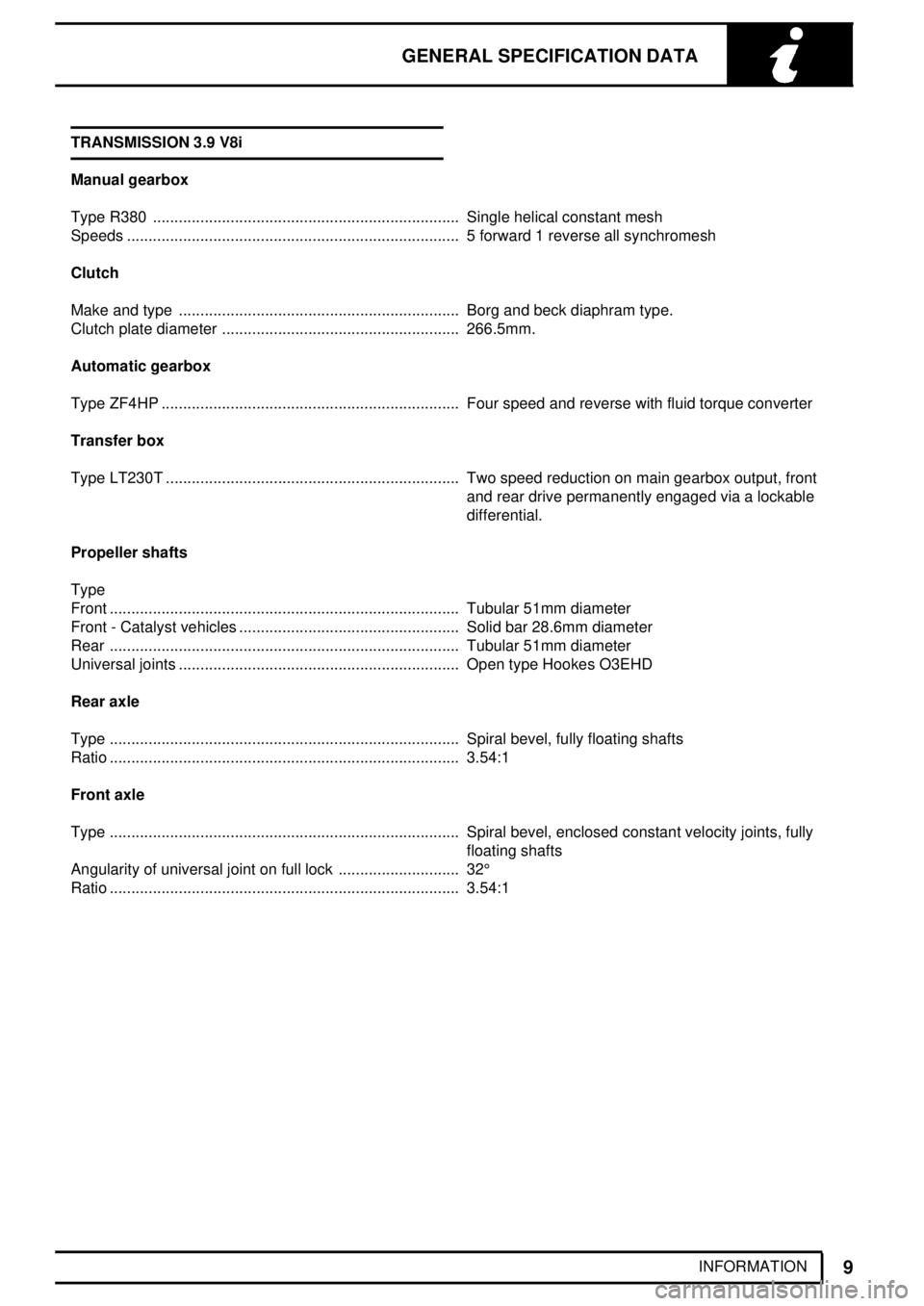
GENERAL SPECIFICATION DATA
9
INFORMATION TRANSMISSION 3.9 V8i
Manual gearbox
Type R380 Single helical constant mesh.......................................................................
Speeds 5 forward 1 reverse all synchromesh.............................................................................
Clutch
Make and type Borg and beck diaphram type..................................................................
Clutch plate diameter 266.5mm........................................................
Automatic gearbox
Type ZF4HP Four speed and reverse with fluid torque converter.....................................................................
Transfer box
Type LT230T Two speed reduction on main gearbox output, front....................................................................
and rear drive permanently engaged via a lockable
differential.
Propeller shafts
Type
Front Tubular 51mm diameter.................................................................................
Front - Catalyst vehicles Solid bar 28.6mm diameter...................................................
Rear Tubular 51mm diameter.................................................................................
Universal joints Open type Hookes O3EHD.................................................................
Rear axle
Type Spiral bevel, fully floating shafts.................................................................................
Ratio 3.54:1.................................................................................
Front axle
Type Spiral bevel, enclosed constant velocity joints, fully.................................................................................
floating shafts
Angularity of universal joint on full lock 32° ............................
Ratio 3.54:1.................................................................................
Page 39 of 873
GENERAL SPECIFICATION DATA
21
INFORMATION TRANSMISSION - 300 Tdi
Manual gearbox
Type R380 Single helical constant mesh.......................................................................
Speeds 5 forward 1 reverse all synchromesh.............................................................................
Automatic gearbox
Type ZF4HP Four speed and reverse with fluid torque converter.....................................................................
Transfer box
Type LT230T Two speed reduction on main gearbox output. Front....................................................................
and rear drive permanently engaged via a lockable
differential
Page 71 of 873
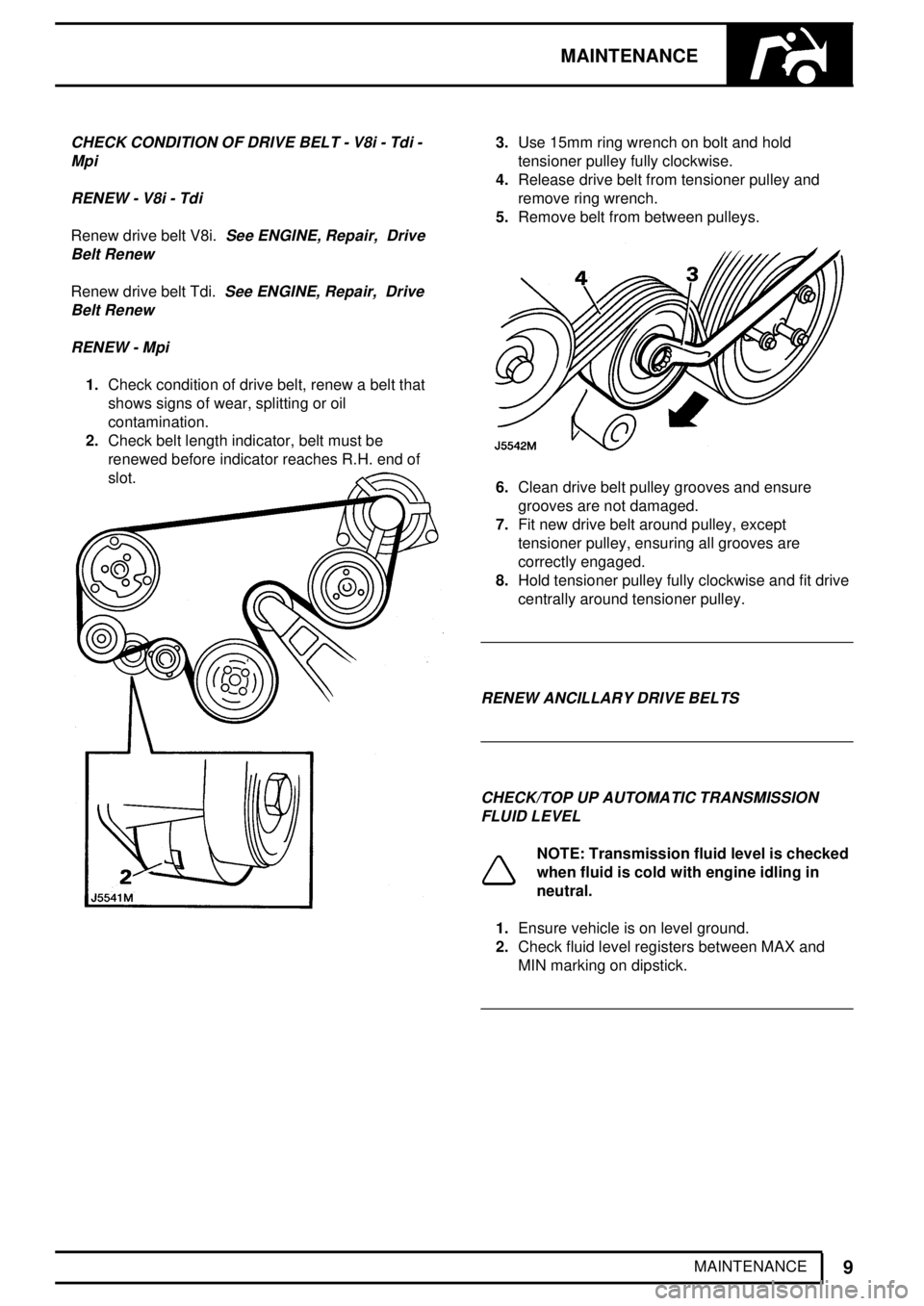
MAINTENANCE
9
MAINTENANCE
CHECK CONDITION OF DRIVE BELT - V8i - Tdi -
Mpi
RENEW - V8i - Tdi
Renew drive belt V8i.See ENGINE, Repair, Drive
Belt Renew
Renew drive belt Tdi.See ENGINE, Repair, Drive
Belt Renew
RENEW - Mpi
1.Check condition of drive belt, renew a belt that
shows signs of wear, splitting or oil
contamination.
2.Check belt length indicator, belt must be
renewed before indicator reaches R.H. end of
slot.
3.Use 15mm ring wrench on bolt and hold
tensioner pulley fully clockwise.
4.Release drive belt from tensioner pulley and
remove ring wrench.
5.Remove belt from between pulleys.
6.Clean drive belt pulley grooves and ensure
grooves are not damaged.
7.Fit new drive belt around pulley, except
tensioner pulley, ensuring all grooves are
correctly engaged.
8.Hold tensioner pulley fully clockwise and fit drive
centrally around tensioner pulley.
RENEW ANCILLARY DRIVE BELTS
CHECK/TOP UP AUTOMATIC TRANSMISSION
FLUID LEVEL
NOTE: Transmission fluid level is checked
when fluid is cold with engine idling in
neutral.
1.Ensure vehicle is on level ground.
2.Check fluid level registers between MAX and
MIN marking on dipstick.
Page 131 of 873
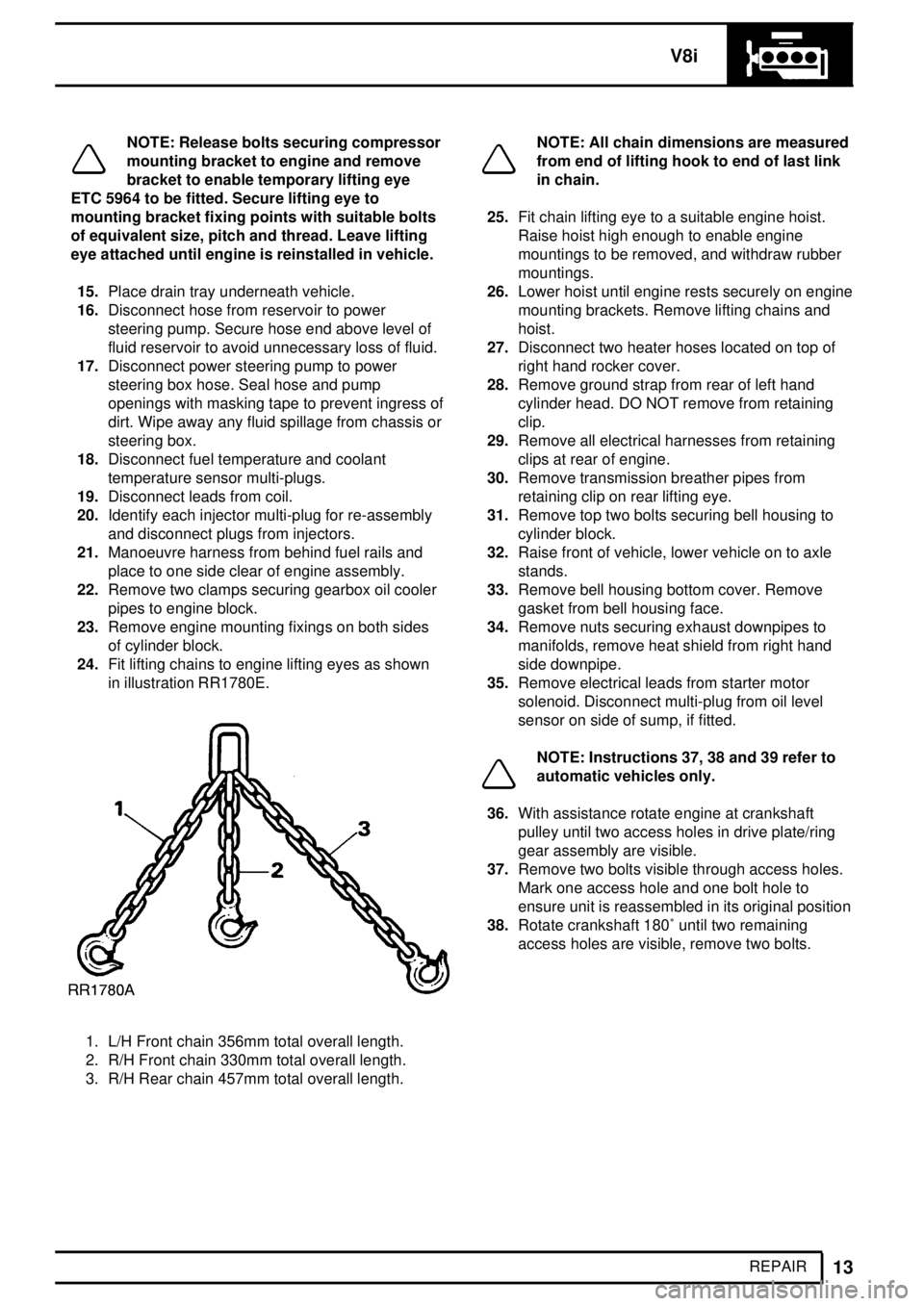
V8i
13
REPAIR
NOTE: Release bolts securing compressor
mounting bracket to engine and remove
bracket to enable temporary lifting eye
ETC 5964 to be fitted. Secure lifting eye to
mounting bracket fixing points with suitable bolts
of equivalent size, pitch and thread. Leave lifting
eye attached until engine is reinstalled in vehicle.
15.Place drain tray underneath vehicle.
16.Disconnect hose from reservoir to power
steering pump. Secure hose end above level of
fluid reservoir to avoid unnecessary loss of fluid.
17.Disconnect power steering pump to power
steering box hose. Seal hose and pump
openings with masking tape to prevent ingress of
dirt. Wipe away any fluid spillage from chassis or
steering box.
18.Disconnect fuel temperature and coolant
temperature sensor multi-plugs.
19.Disconnect leads from coil.
20.Identify each injector multi-plug for re-assembly
and disconnect plugs from injectors.
21.Manoeuvre harness from behind fuel rails and
place to one side clear of engine assembly.
22.Remove two clamps securing gearbox oil cooler
pipes to engine block.
23.Remove engine mounting fixings on both sides
of cylinder block.
24.Fit lifting chains to engine lifting eyes as shown
in illustration RR1780E.
1. L/H Front chain 356mm total overall length.
2. R/H Front chain 330mm total overall length.
3. R/H Rear chain 457mm total overall length.
NOTE: All chain dimensions are measured
from end of lifting hook to end of last link
in chain.
25.Fit chain lifting eye to a suitable engine hoist.
Raise hoist high enough to enable engine
mountings to be removed, and withdraw rubber
mountings.
26.Lower hoist until engine rests securely on engine
mounting brackets. Remove lifting chains and
hoist.
27.Disconnect two heater hoses located on top of
right hand rocker cover.
28.Remove ground strap from rear of left hand
cylinder head. DO NOT remove from retaining
clip.
29.Remove all electrical harnesses from retaining
clips at rear of engine.
30.Remove transmission breather pipes from
retaining clip on rear lifting eye.
31.Remove top two bolts securing bell housing to
cylinder block.
32.Raise front of vehicle, lower vehicle on to axle
stands.
33.Remove bell housing bottom cover. Remove
gasket from bell housing face.
34.Remove nuts securing exhaust downpipes to
manifolds, remove heat shield from right hand
side downpipe.
35.Remove electrical leads from starter motor
solenoid. Disconnect multi-plug from oil level
sensor on side of sump, if fitted.
NOTE: Instructions 37, 38 and 39 refer to
automatic vehicles only.
36.With assistance rotate engine at crankshaft
pulley until two access holes in drive plate/ring
gear assembly are visible.
37.Remove two bolts visible through access holes.
Mark one access hole and one bolt hole to
ensure unit is reassembled in its original position
38.Rotate crankshaft 180Ê until two remaining
access holes are visible, remove two bolts.
Page 768 of 873
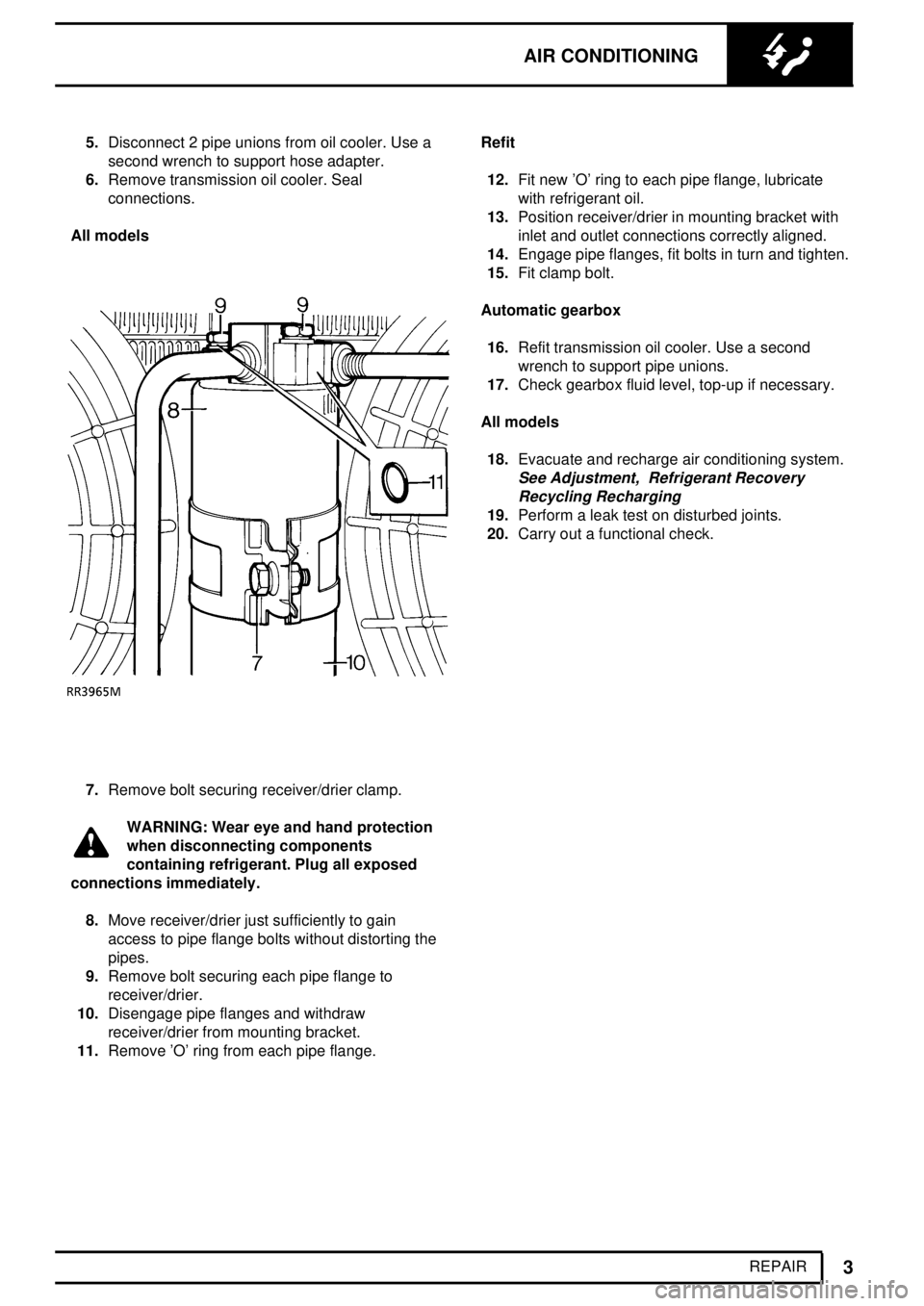
AIR CONDITIONING
3
REPAIR 5.Disconnect 2 pipe unions from oil cooler. Use a
second wrench to support hose adapter.
6.Remove transmission oil cooler. Seal
connections.
All models
7.Remove bolt securing receiver/drier clamp.
WARNING: Wear eye and hand protection
when disconnecting components
containing refrigerant. Plug all exposed
connections immediately.
8.Move receiver/drier just sufficiently to gain
access to pipe flange bolts without distorting the
pipes.
9.Remove bolt securing each pipe flange to
receiver/drier.
10.Disengage pipe flanges and withdraw
receiver/drier from mounting bracket.
11.Remove 'O' ring from each pipe flange.Refit
12.Fit new 'O' ring to each pipe flange, lubricate
with refrigerant oil.
13.Position receiver/drier in mounting bracket with
inlet and outlet connections correctly aligned.
14.Engage pipe flanges, fit bolts in turn and tighten.
15.Fit clamp bolt.
Automatic gearbox
16.Refit transmission oil cooler. Use a second
wrench to support pipe unions.
17.Check gearbox fluid level, top-up if necessary.
All models
18.Evacuate and recharge air conditioning system.
See Adjustment, Refrigerant Recovery
Recycling Recharging
19.Perform a leak test on disturbed joints.
20.Carry out a functional check.