Page 1049 of 1070
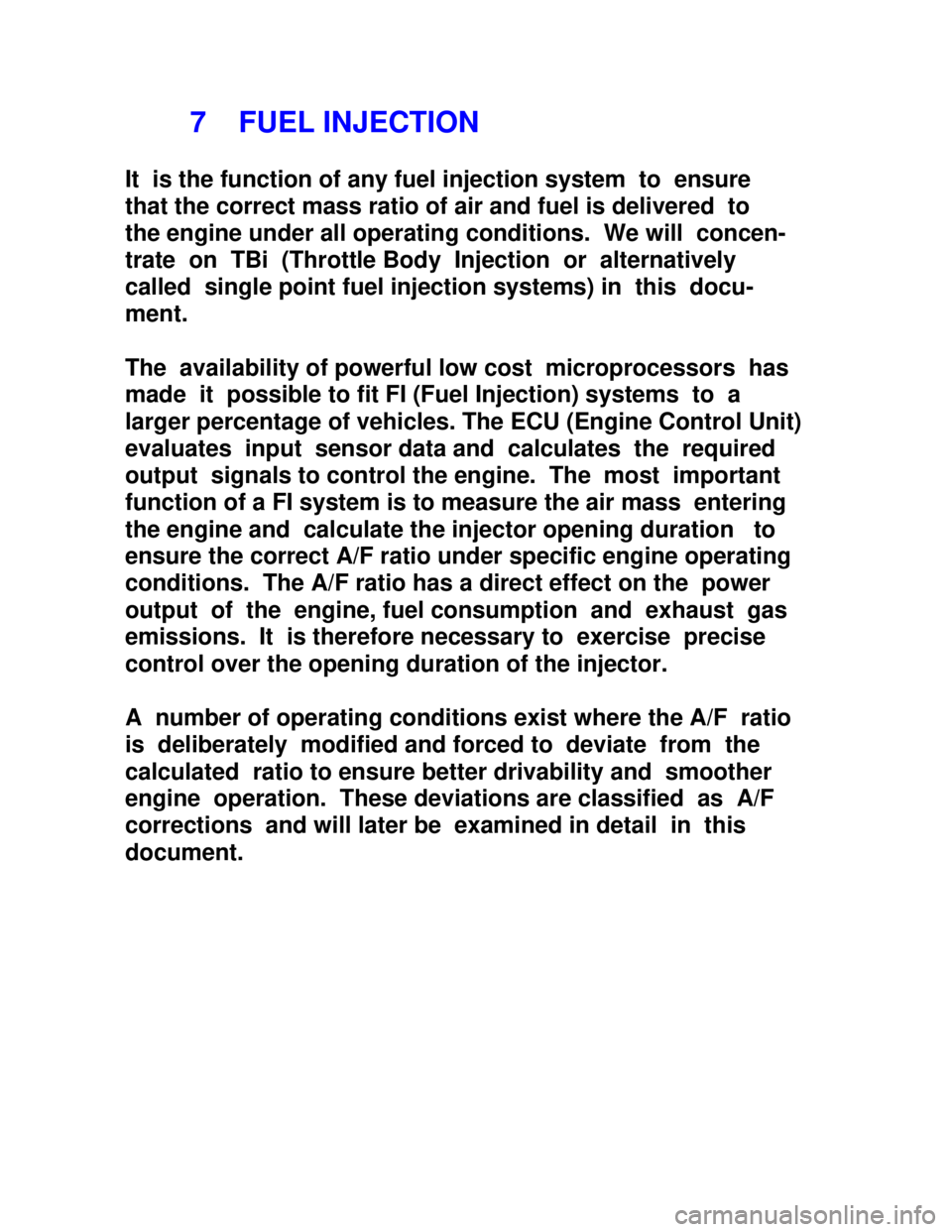
Downloaded from www.Manualslib.com manuals search engine 7 FUEL INJECTION
It is the function of any fuel injection system to ensure
that the correct mass ratio of air and fuel is delivered to
the engine under all operating conditions. We will concen-
trate on TBi (Throttle Body Injection or alternatively
called single point fuel injection systems) in this docu-
ment.
The availability of powerful low cost microprocessors has
made it possible to fit FI (Fuel Injection) systems to a
larger percentage of vehicles. The ECU (Engine Control Unit)
evaluates input sensor data and calculates the required
output signals to control the engine. The most important
function of a FI system is to measure the air mass entering
the engine and calculate the injector opening duration to
ensure the correct A/F ratio under specific engine operating
conditions. The A/F ratio has a direct effect on the power
output of the engine, fuel consumption and exhaust gas
emissions. It is therefore necessary to exercise precise
control over the opening duration of the injector.
A number of operating conditions exist where the A/F ratio
is deliberately modified and forced to deviate from the
calculated ratio to ensure better drivability and smoother
engine operation. These deviations are classified as A/F
corrections and will later be examined in detail in this
document.
Page 1063 of 1070
Downloaded from www.Manualslib.com manuals search engine 10 DEFAULT MODE SELECTION
When the ECU detects a faulty signal from one of its sensors
it will substitute a default signal value to enable the
vehicle to be driven with degraded performance (see para-
graph 10.1).
Faulty sensor Substitute value/sensor
_____________________________________________________
______
EWT Warm engine - 100 øC
MAT 31 øC
Fuel map selector Zero percent enrichment
Timing map selector Map T1 - RON 87D
TPS Idle speed - 1,000 to
2,000 r.p.m.
MAP TPS and idle speed -
1,000 to 2,000 r.p.m.
Disable distributor
bypass operation and
fix spark timing at
10ø BTDC
CO potentiometer Zero percent
Page 1064 of 1070
Downloaded from www.Manualslib.com manuals search engine 11 DIAGNOSTICS
Various possible methods of fault finding are listed below
to reduce down-time of the vehicle.
11.1 Diagnostic codes
The CPU continuously monitors its own activities and sensor
inputs. If a fault is detected during operation the diagnos-
tic lamp is turned on and a default signal value is used to
allow the car to be driven with slightly reduced perform-
ance. The fault code is stored in RAM for later evaluation
by the Dealer. If the fault disappears the unit will immedi-
ately use the sensor data instead of the default data, thus
ensuring optimum performance. The fault will be erased from
RAM after 7 starts (ignition turned on 7 times) during which
no fault was detected.
The fault stored in RAM could be accessed by grounding the
diagnostic initialisation input terminal. The fault will
then be flashed out by the diagnostic lamp.
Page 1065 of 1070
Downloaded from www.Manualslib.com manuals search engine DIAGNOSTIC CODES
Code Cause
_____________________________________________________
14 Coolant temperature sensor voltage too low
15 Coolant temperature sensor voltage too high
21 TPS voltage too high
22 TPS voltage too low
25 MAT sensor voltage too low
26 MAT sensor voltage too high
33 MAP sensor voltage too high
34 MAP sensor voltage too low
35 Idle control stepper motor failure
36 Timing map selector error
42 Reference signal error/Engine stall
(Diagnostic lamp will not turn ON)
44 Fuel map selector error
48 Battery voltage too low
49 Battery voltage too high
65 CO potentiometer voltage out of range
Page 1067 of 1070
Downloaded from www.Manualslib.com manuals search engine 11.2.5 CO potentiometer supply voltage: The voltage
between
terminal 23B and signal ground should be between 4.7 and
5.2 volt.
11.2.6 MAP sensor supply voltage: The voltage between
terminal
24B and signal ground should be between 4.7 and 5.2 volt.
11.2.7 MAP sensor signal voltage: The voltage between
terminal
15B and signal ground with ignition on should be:
MAP signal voltage Manifold absolute pressure
_____________________________________________________
___
1.00 20 kPa
2.00 40 kPa
3.00 60 kPa
4.00 80 kPa
4.50 90 kPa
5.00 100 kPa
A general tolerance of +/- 5% exists on the above voltages.
Page 1069 of 1070
Downloaded from www.Manualslib.com manuals search engine 11.2.10 EWT sensor: The resistance between terminal 16B and
11A
on the harness connector with the ECU removed should be:
EWT øC Resistance (ohm)
-20 19,700
-0 5,640
+20 2,410
40 1,177
60 565
80 308
100 186
Page 1070 of 1070
Downloaded from www.Manualslib.com manuals search engine 11.2.11 MAT sensor: The resistance between terminal 17B and
11A on the harness with the ECU removed should be:
MAT øC Resistance (ohm)
-12 9,977
-5 6,540
0 5,627
18 2,290
33 1,241
48 782
62 485