Page 200 of 391
/cY
REAR HUBREAR SUSPENSION
<2WD> - Rear Hub
Rl7FMA
17-7The rear hub has built-in unit ball bearing to secure
high bearing and hub accuracy. By simply tightening
the nut to specified torque, optimum preloading is
achieved for easier servicing.
Unit ball
a -\ Rear hub
/‘YLLY -Nut
12A0550
Page 216 of 391
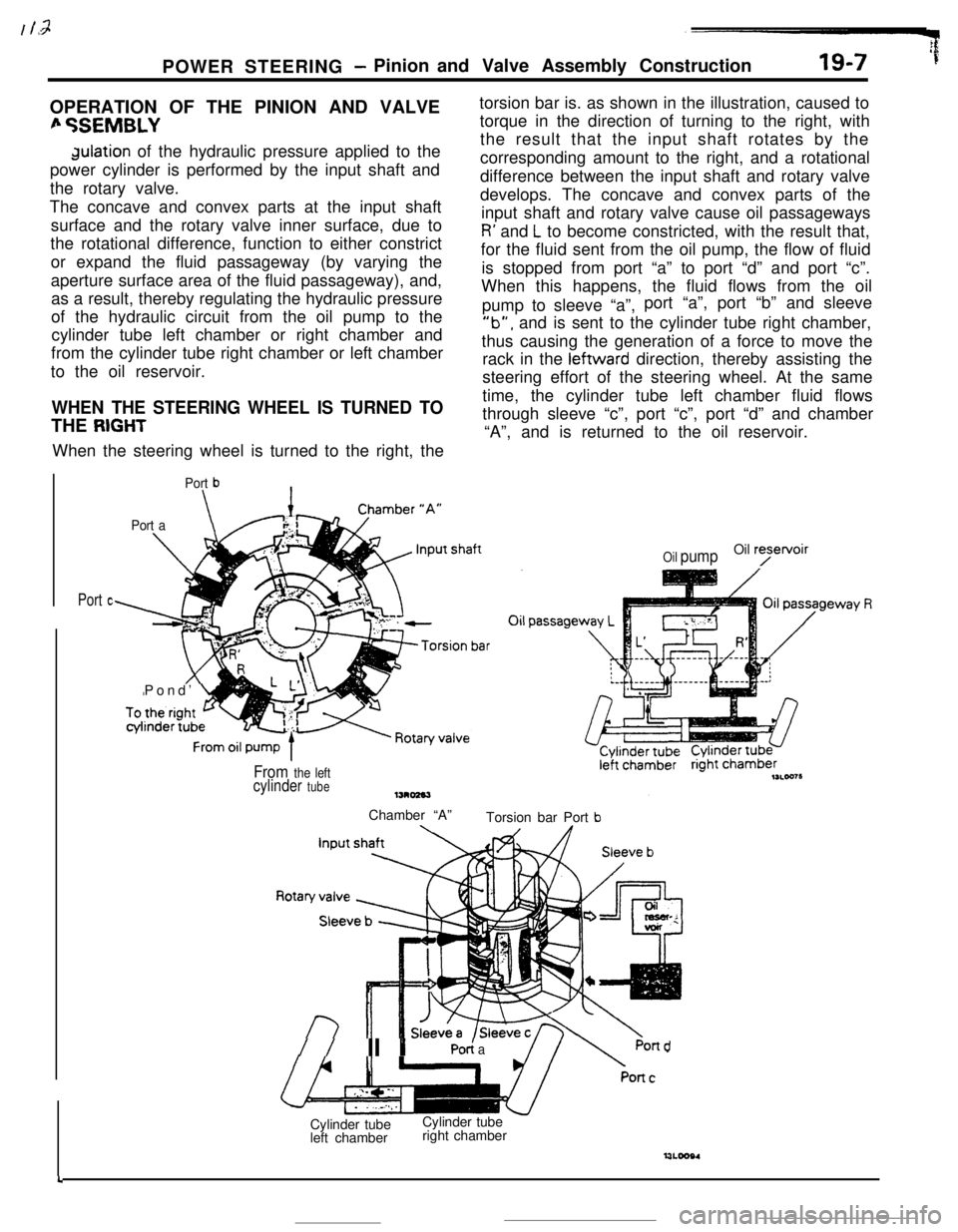
:POWER STEERING
- Pinion and Valve Assembly Construction19-7 ’fOPERATION OF THE PINION AND VALVE
fi %EMBLYdulation of the hydraulic pressure applied to the
power cylinder is performed by the input shaft and
the rotary valve.
The concave and convex parts at the input shaft
surface and the rotary valve inner surface, due to
the rotational difference, function to either constrict
or expand the fluid passageway (by varying the
aperture surface area of the fluid passageway), and,
as a result, thereby regulating the hydraulic pressure
of the hydraulic circuit from the oil pump to the
cylinder tube left chamber or right chamber and
from the cylinder tube right chamber or left chamber
to the oil reservoir.
WHEN THE STEERING WHEEL IS TURNED TOTHE
RIGHTWhen the steering wheel is turned to the right, the
Port b\
Port a\Pond’
Ltorsion bar is. as shown in the illustration, caused to
torque in the direction of turning to the right, with
the result that the input shaft rotates by the
corresponding amount to the right, and a rotational
difference between the input shaft and rotary valve
develops. The concave and convex parts of the
input shaft and rotary valve cause oil passageways
R’ and L to become constricted, with the result that,
for the fluid sent from the oil pump, the flow of fluid
is stopped from port “a” to port “d” and port “c”.
When this happens, the fluid flows from the oil
pump to sleeve “a”,port “a”, port “b” and sleeve
‘lb”, and is sent to the cylinder tube right chamber,
thus causing the generation of a force to move the
rack in the leftward direction, thereby assisting the
steering effort of the steering wheel. At the same
time, the cylinder tube left chamber fluid flows
through sleeve “c”, port “c”, port “d” and chamber
“A”, and is returned to the oil reservoir.
Port c
Oil pumpOil ryetvoir
From the leftcylinder tubeChamber “A”
Torsion bar Port
b
//II YPO< aPond
4Cylinder tube
left chamberCylinder tube
right chamber
Page 218 of 391
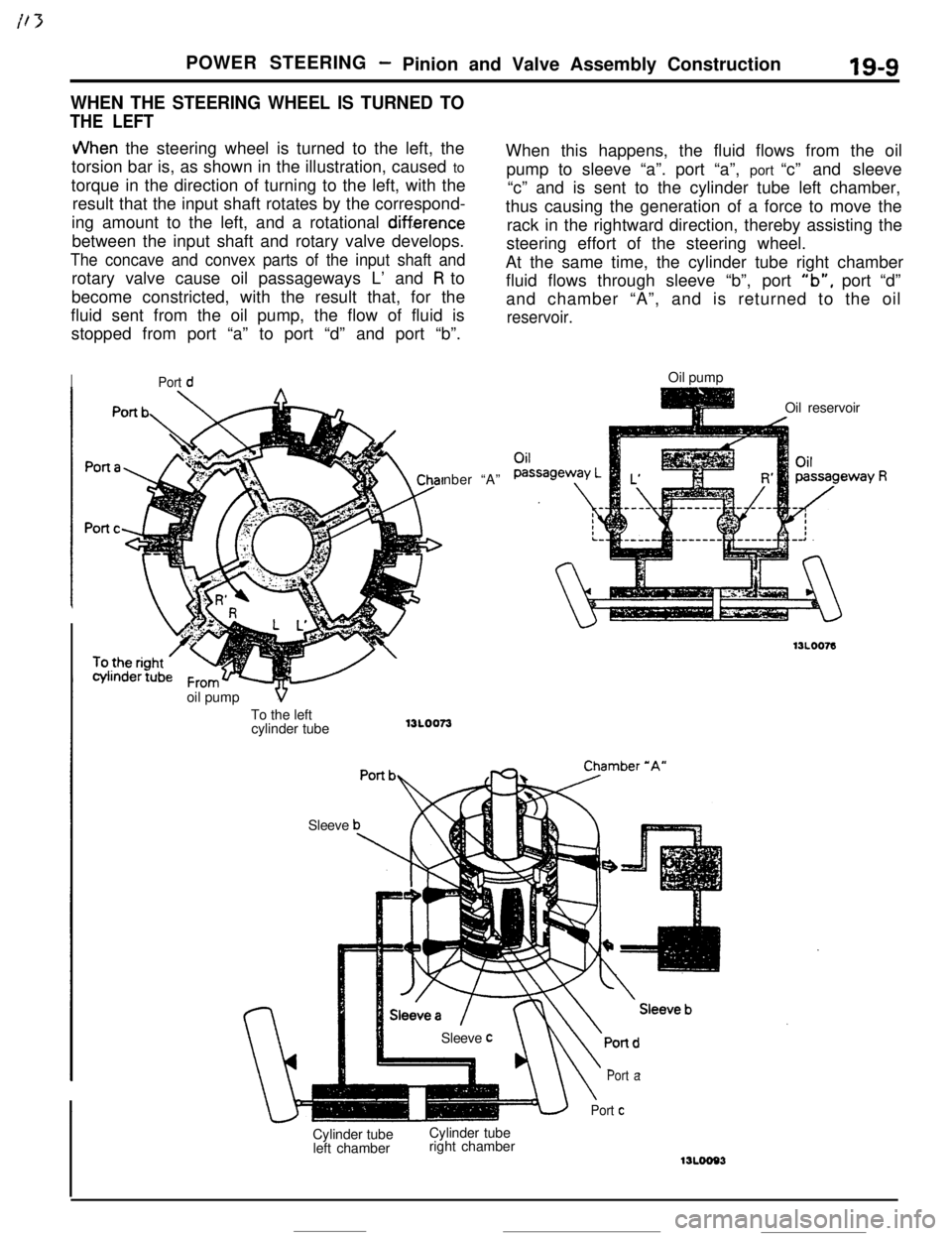
POWER STEERING -Pinion and Valve Assembly Construction
WHEN THE STEERING WHEEL IS TURNED TO
THE LEFT
IS-9
JVhen the steering wheel is turned to the left, the
torsion bar is, as shown in the illustration, caused to
torque in the direction of turning to the left, with the
result that the input shaft rotates by the correspond-
ing amount to the left, and a rotational
diff.erencebetween the input shaft and rotary valve develops.
The concave and convex parts of the input shaft androtary valve cause oil passageways L’ and
R to
become constricted, with the result that, for the
fluid sent from the oil pump, the flow of fluid is
stopped from port “a” to port “d” and port “b”.
IPort dnber “A”
SleeveWhen this happens, the fluid flows from the oil
pump to sleeve “a”. port “a”, port “c” and sleeve
“c” and is sent to the cylinder tube left chamber,
thus causing the generation of a force to move the
rack in the rightward direction, thereby assisting the
steering effort of the steering wheel.
At the same time, the cylinder tube right chamber
fluid flows through sleeve “b”, port
“b”, port “d”
and chamber “A”, and is returned to the oil
reservoir.Oil pump
Oil reservoir
Cylinder tube
left chamberCylinder tube
right chamber
\
Port a
Port cSleeve
coil pump
VTo the left
cylinder tube
13L0073
Page 220 of 391
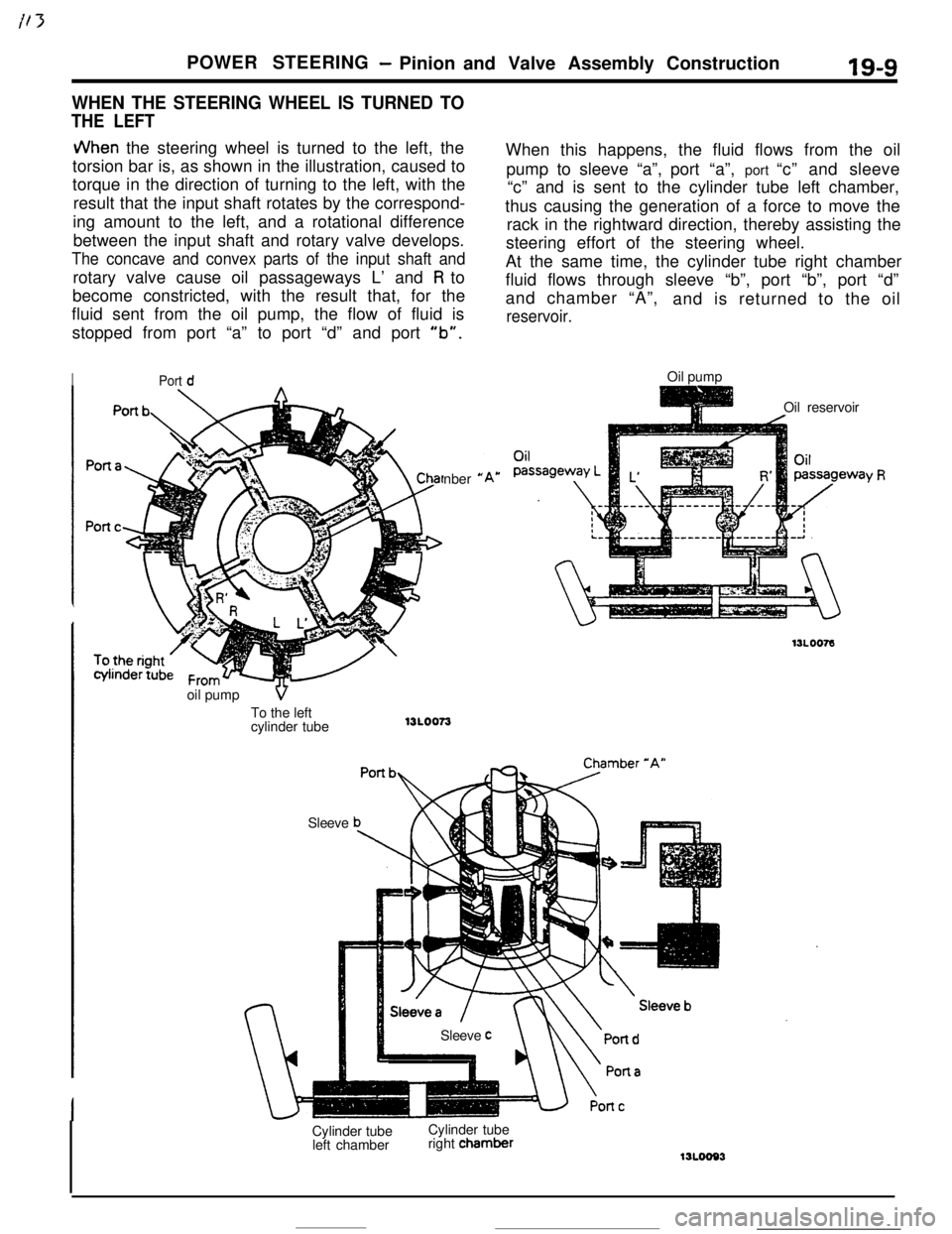
POWER STEERING- Pinion and Valve Assembly Construction19-9
WHEN THE STEERING WHEEL IS TURNED TO
THE LEFT
JVhen the steering wheel is turned to the left, the
torsion bar is, as shown in the illustration, caused to
torque in the direction of turning to the left, with the
result that the input shaft rotates by the correspond-
ing amount to the left, and a rotational difference
between the input shaft and rotary valve develops.
The concave and convex parts of the input shaft androtary valve cause oil passageways L’ and
R to
become constricted, with the result that, for the
fluid sent from the oil pump, the flow of fluid is
stopped from port “a” to port “d” and port
“b”.
IPort dnber
*oil pump
VTo the left
cylinder tube13LOO73
SleeveWhen this happens, the fluid flows from the oil
pump to sleeve “a”,port “a”, port “c” and sleeve
“c” and is sent to the cylinder tube left chamber,
thus causing the generation of a force to move the
rack in the rightward direction, thereby assisting the
steering effort of the steering wheel.
At the same time, the cylinder tube right chamber
fluid flows through sleeve “b”, port “b”, port “d”
and chamber “A”,
and is returned to the oil
reservoir.Oil pump
Oil reservoir
Sleeve
cCylinder tube
left chamberCylinder tube
right chamber
‘Y R
Page 225 of 391
21-l
k
TRANSAXLE
‘TORQUE CONVERTE R....................................22
TRANSAXLZ MECHANIS M............................ 23
EndClutch<.................................................. 27
Front Clutch’.................................................... 25
KickdownBrake............................................ 28
Low-reverse Brake........................................30
One-way Clutch............................................ 31
CObROL................................ 15I
VISCOUS COUPLING (VCU). . . . . . . . . . . . . . . . . . . . . . . . 12
Page 234 of 391
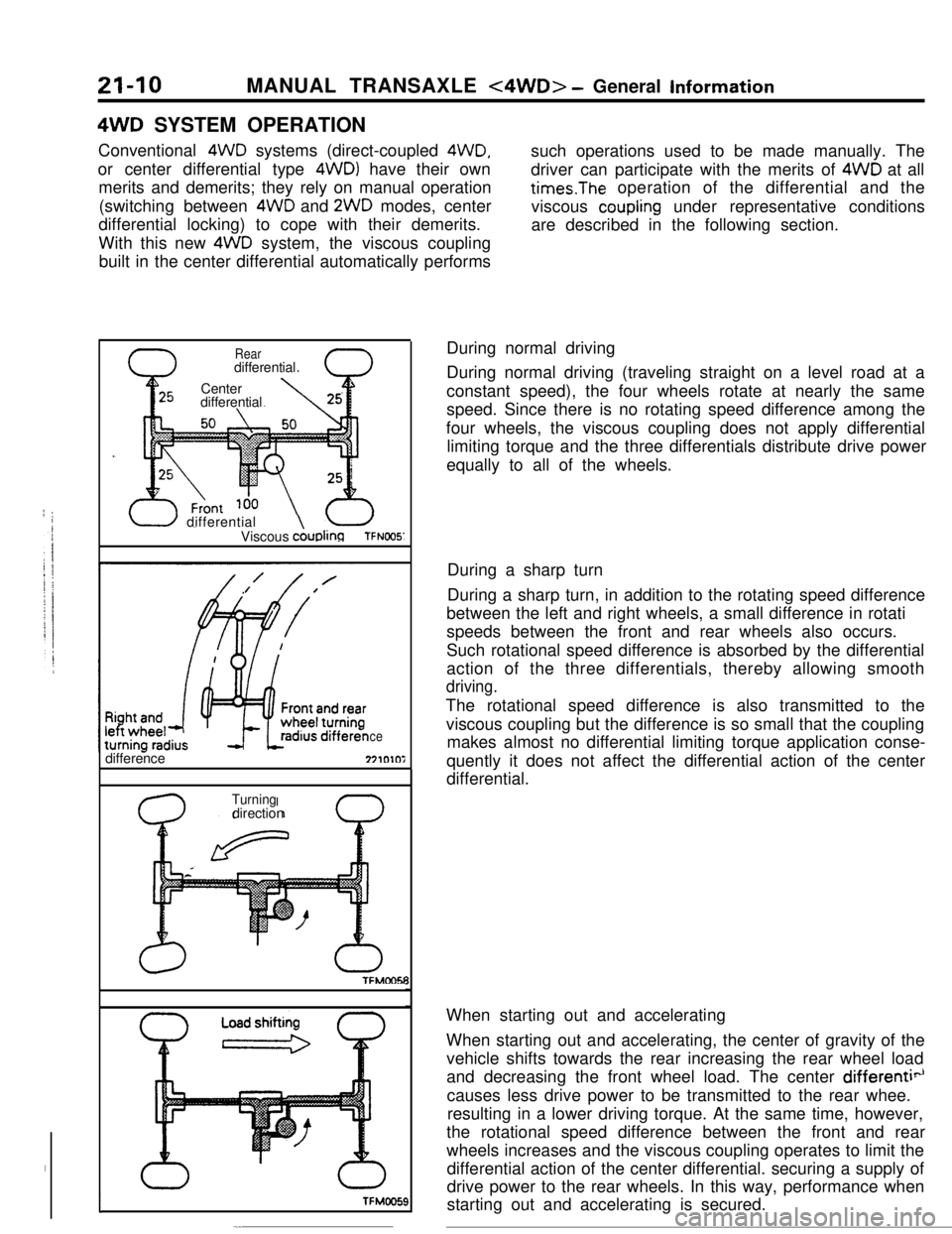
21-10MANUAL TRANSAXLE <4WD> - General Information4WD SYSTEM OPERATION
Conventional 4WD systems (direct-coupled
4WD,or center differential type 4WDl have their own
merits and demerits; they rely on manual operation
(switching between 4WD and 2WD modes, center
differential locking) to cope with their demerits.
With this new 4WD system, the viscous coupling
built in the center differential automatically performssuch operations used to be made manually. The
driver can participate with the merits of 4WD at alltimes.The operation of the differential and the
viscous
coupling under representative conditions
are described in the following section.
I
Reardifferential
Center
differential
U differential
Viscous AuDk?TFNOO5’difference
ce271010i
TFMMYTFMMY
0
Turningdirection
ITFMOO!X
-.During normal driving
During normal driving (traveling straight on a level road at a
constant speed), the four wheels rotate at nearly the same
speed. Since there is no rotating speed difference among the
four wheels, the viscous coupling does not apply differential
limiting torque and the three differentials distribute drive power
equally to all of the wheels.
During a sharp turn
During a sharp turn, in addition to the rotating speed difference
between the left and right wheels, a small difference in rotati
speeds between the front and rear wheels also occurs.
Such rotational speed difference is absorbed by the differential
action of the three differentials, thereby allowing smooth
driving.The rotational speed difference is also transmitted to the
viscous coupling but the difference is so small that the coupling
makes almost no differential limiting torque application conse-
quently it does not affect the differential action of the center
differential.
When starting out and accelerating
When starting out and accelerating, the center of gravity of the
vehicle shifts towards the rear increasing the rear wheel load
and decreasing the front wheel load. The center
differenti”causes less drive power to be transmitted to the rear whee.
resulting in a lower driving torque. At the same time, however,
the rotational speed difference between the front and rear
wheels increases and the viscous coupling operates to limit the
differential action of the center differential. securing a supply of
drive power to the rear wheels. In this way, performance when
starting out and accelerating is secured.
Page 235 of 391
MANUAL TRANSAXLE <4WD> - General Information21-I 1When driving on rough roads. . .In case either a front or rear wheel starts spinning on a slippery
or muddy road or when the vehicle is stuck in mud and one tire
spins, the drive power will be decreased by differential action.
However, as this also causes a sharp increase of speed
difference of the viscous coupling, a large differential limiting
torque is now applied, with more power transmitted to the tires
that are not spinning so that the vehicle can drive through or
getout of mud.A
Page 237 of 391
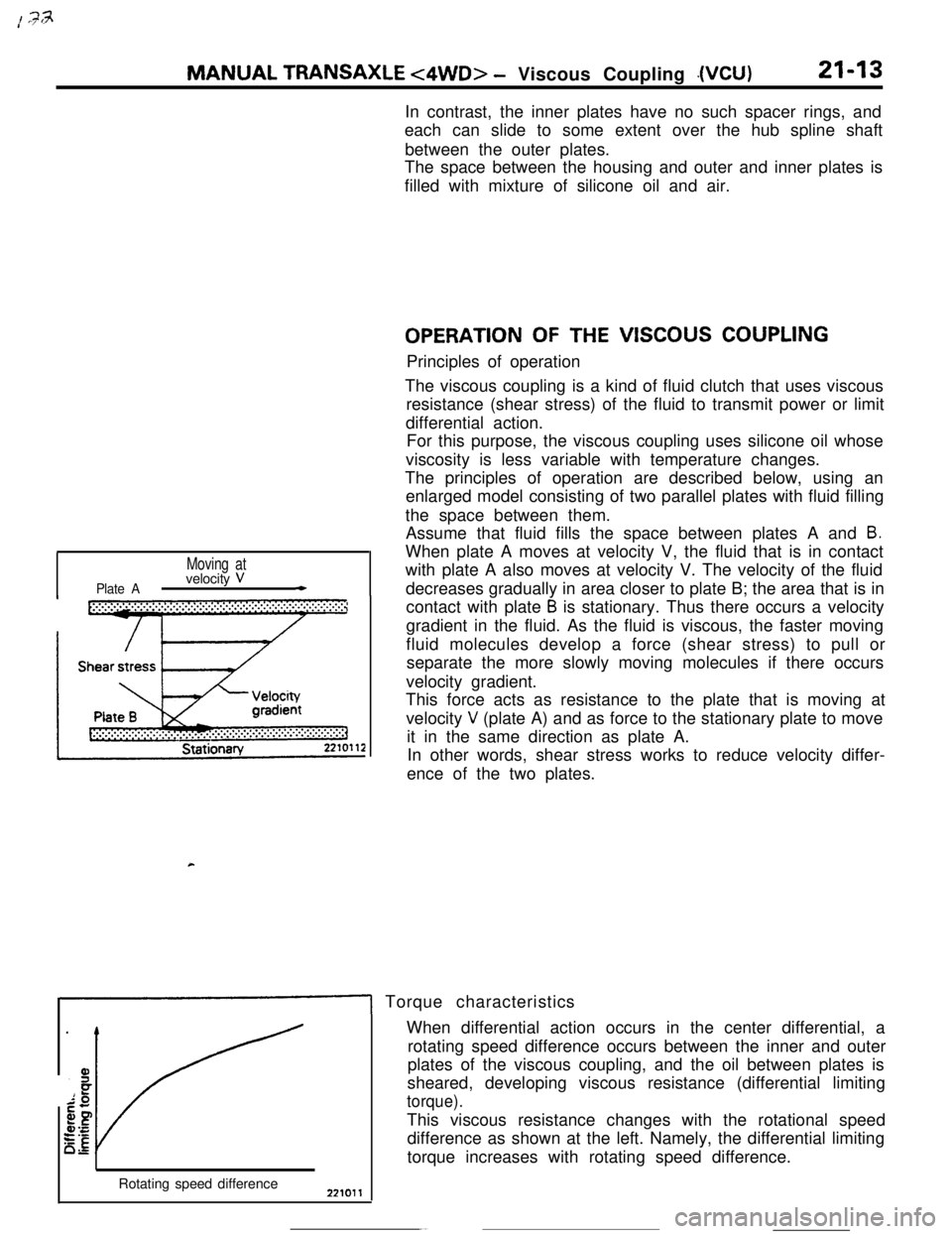
MANUAL TRANSAXLE <4WD> - Viscous Coupling .(VClJ)21-13In contrast, the inner plates have no such spacer rings, and
each can slide to some extent over the hub spline shaft
between the outer plates.
The space between the housing and outer and inner plates is
filled with mixture of silicone oil and air.
Plate A
Moving atvelocity V*
OPERATION OF THE VISCOUS COUPLINGPrinciples of operation
The viscous coupling is a kind of fluid clutch that uses viscous
resistance (shear stress) of the fluid to transmit power or limit
differential action.
For this purpose, the viscous coupling uses silicone oil whose
viscosity is less variable with temperature changes.
The principles of operation are described below, using an
enlarged model consisting of two parallel plates with fluid filling
the space between them.
Assume that fluid fills the space between plates A and
B.When plate A moves at velocity V, the fluid that is in contact
with plate A also moves at velocity V. The velocity of the fluid
decreases gradually in area closer to plate B; the area that is in
contact with plate
B is stationary. Thus there occurs a velocity
gradient in the fluid. As the fluid is viscous, the faster moving
fluid molecules develop a force (shear stress) to pull or
separate the more slowly moving molecules if there occurs
velocity gradient.
This force acts as resistance to the plate that is moving at
velocity
V (plate A) and as force to the stationary plate to move
it in the same direction as plate A.
In other words, shear stress works to reduce velocity differ-
ence of the two plates.
1 Torque characteristics
Rotating speed differenceWhen differential action occurs in the center differential, a
rotating speed difference occurs between the inner and outer
plates of the viscous coupling, and the oil between plates is
sheared, developing viscous resistance (differential limiting
torque).This viscous resistance changes with the rotational speed
difference as shown at the left. Namely, the differential limiting
torque increases with rotating speed difference.